全文HTML
--> --> -->
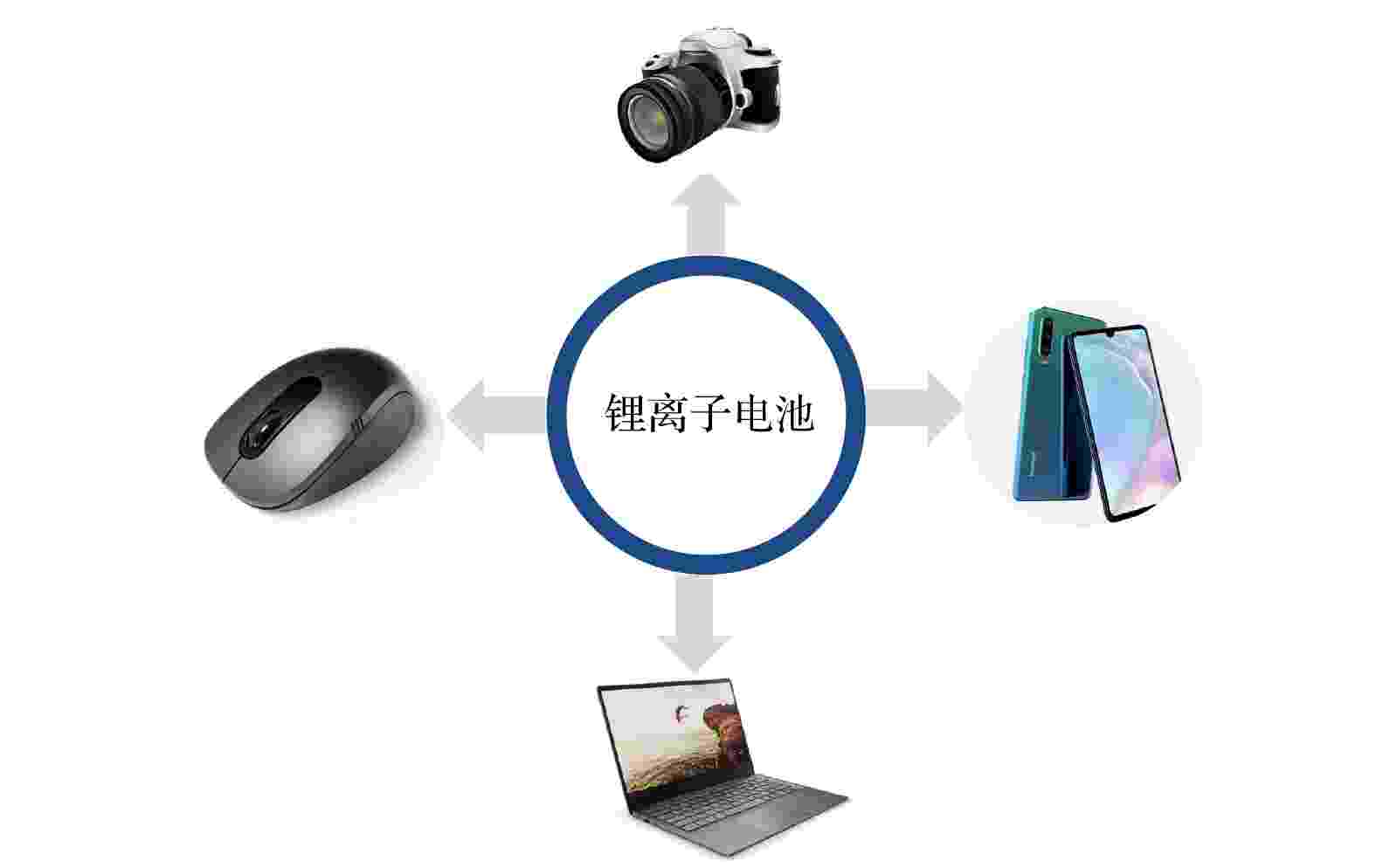
Figure1. Usage of lithium-ion batteries.
造成锂离子电池容量衰减甚至失效的原因是多方面的, 其中最主要的是电池内部产生的扩散诱导应力. 锂离子电池的工作原理是锂离子在正负极之间的移动来完成充电、放电过程. 在充电过程中, 锂离子在外加电场的驱动下从正极材料脱嵌后透过电解质嵌入到负极中, 放电时则相反. 由于锂离子电池频繁地循环充放电, 锂不断嵌入和脱出, 使得电极颗粒发生(晶格大小、晶格结构和晶相转变等)变化, 产生扩散诱导应力. 在其作用下电极颗粒可能发生破碎、粉化, 最终造成电池内阻增加, 循环性能下降, 容量衰减, 电池失效. 由此可见, 研究电极颗粒中扩散诱导应力的分布与演化, 有助于认识锂离子电池的失效机理.
锂离子电池的充放电过程, 涉及到锂离子的扩散、电极结构的变形与内部应力场演化, 是一个物理扩散、电化学与力学的多物理场强耦合问题. 锂离子在电极中的嵌入和脱嵌会产生应力; 反之, 应力也会影响锂离子的扩散过程. Prussin[9]首次类比于温度应力推导扩散应力, 从此热应力类比法广泛应用于锂离子电池的模拟分析中 (图2). 基于Prussin[9]的热应力类比法, Zhang等[10]通过建立数学模型研究了球形颗粒和椭球颗粒的扩散诱导应力的产生与演变, 在线弹性、小变形的情况下确定了颗粒的扩散诱导应力表达式, 而且对椭球粒子的模拟结果表明, 较大的长宽比有利于减小扩散诱导应力. Song等[11]通过研究由于浓度不均匀引起的扩散诱导应力, 得到了圆柱形多层电极中的扩散诱导应力的解析解.
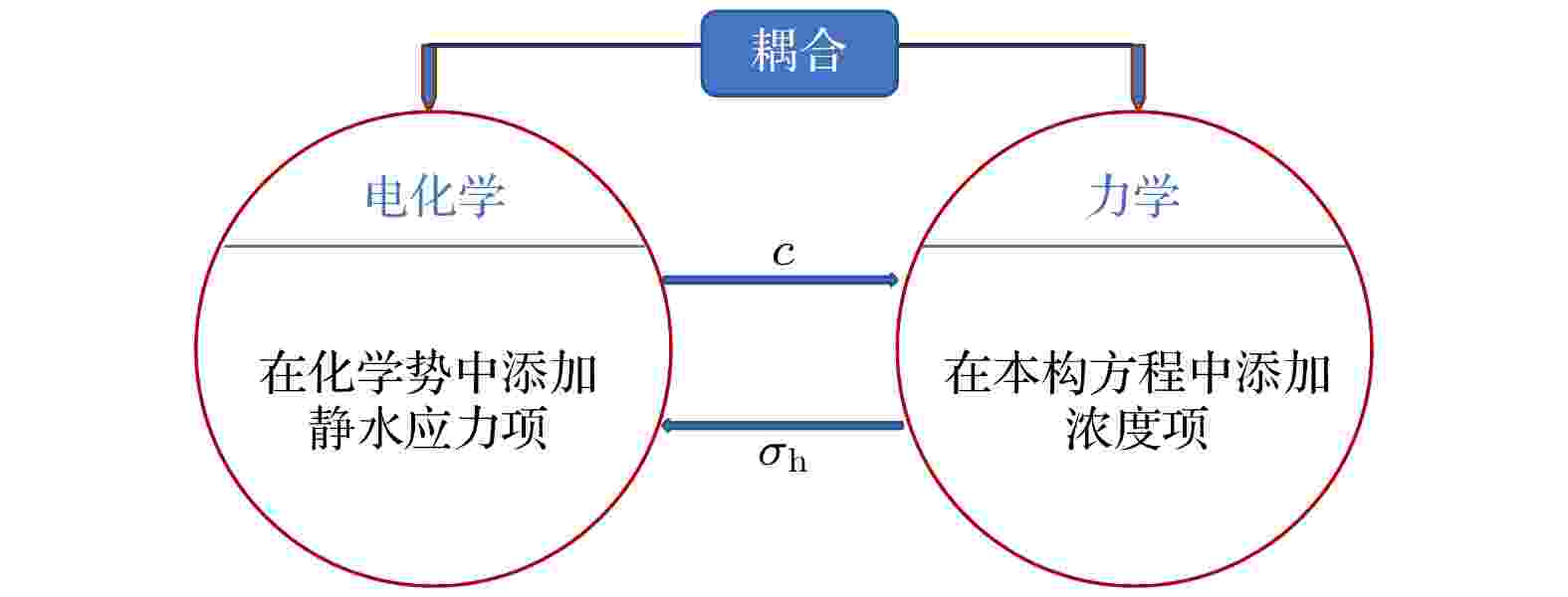
Figure2. Electrochemistry-mechanics coupling mechanism.
由于耦合作用, 扩散诱导应力与扩散过程之间相互影响, 众多研究表明, 拉应力会促进锂离子的快速扩散, 而压应力则在一定程度上抑制扩散过程. 如Bagheri等[12]研究了静水应力对锂离子电池球形活性颗粒中锂离子扩散动力学的影响, 结果表明, 静水应力可以加快锂离子的扩散, 并且在恒电流状态下静水应力会导致浓度梯度减小, 从而降低应力. Lu等[13]也研究了表面张力对纳米球形颗粒中力学与电化学的作用, 数值结果表明, 在嵌入过程中电极颗粒表面的压应力抑制了锂离子的吸收.
由于扩散诱导应力直接关系到电极颗粒的膨胀与破裂、粉化, 研究其影响因素以有效降低应力水平, 从而提高电极的机械性能就成为一个重要研究课题. Christensen[14]阐明了体积膨胀因子、非线性晶格膨胀和压力扩散对扩散诱导应力的作用, 发现压力扩散和非线性晶格膨胀在决定大体积膨胀材料的电压和应力响应方面扮演着重要的角色. Zhang等[15]建立了恒电流作用下横向各向同性圆柱状电极的扩散诱导应力分析模型, 结果表明径向和切向应力基本不依赖于杨氏模量比和扩散膨胀系数比, 而轴向应力在很大程度上取决于杨氏模量比和扩散膨胀系数比. Cheng等[16]研究了表面张力对球形纳米颗粒内扩散诱导应力的影响. 结果表明, 当颗粒直径在纳米范围内时, 应力的大小及分布对颗粒表面的断裂行为具有重要影响, 随着颗粒半径的减小, 拉伸应力的大小显著降低, 甚至可以恢复到压缩应力状态. Deluca等[17]使用电化学-力学耦合模型研究了锂离子嵌入硅颗粒过程中颗粒形态(空心颗粒与实心颗粒)和尺寸对应力产生的影响, 发现产生的应力随着颗粒尺寸减小而减小, 在纳米级时达到最小值, 并且结果表明在相同的几何尺度下, 空心球形颗粒中的扩散应力水平远小于实心球形颗粒, 表现出更好的力学性能. Li等[18]为了研究复合梯度球状电极颗粒中的力学机制, 采用了有限变形理论和可逆化学反应, 得出可逆的电化学反应导致了容量的衰退和力学性能的下降, 并提出3种非均匀梯度材料参数有利于减轻扩散诱导应力带来的负面影响. Hu等[19]建立了电极颗粒的二维电化学-力-热耦合模型, 研究了电极颗粒的形状对颗粒锂的浓度和应力的影响, 结果表明电极的几何形状在锂离子的扩散动力学中起着重要的作用. Zhao等[20]考虑到在晶界处的锂离子偏析, 建立了用于锂离子在多晶膜电极的晶界和晶界中扩散的二维解析解. 通过有限元模拟表明晶界可以帮助锂离子快速扩散并有效地降低应力.
另一方面, 针对锂离子电池充放电过程中伴随的巨大体积变化和容量衰减问题, 研究者们提出了核壳结构的设计. 核壳结构的核心为电极材料, 壳层为起辅助改善作用的包覆层材料. 包覆层材料的作用主要有以下几个方面: 包覆层可以降低电极材料被电解液腐蚀的可能性、强化或者是带来新的物理化学性能、限制体积膨胀保持结构稳定性等. 其中碳材料具有成本较低、良好的导电性和力学性能等优点, 是目前最常用的包覆材料之一[21]. Hao等[22]建立了碳包覆正极材料锰酸锂的模型来研究核壳纳米结构的扩散应力, 结果表明, 碳层能够有效缓冲材料的体积膨胀, 降低核活性材料的拉应力. Zhao等[23]研究了包覆硅纳米管颗粒的氧化铝外壳中的扩散应力, 发现对于厚壳颗粒, 核壳界面容易发生脱黏, 而对于核较大、壳相对较薄的颗粒, 则更容易发生壳破裂. 并且借助能量释放率量化了应力和破坏模式之间的关系. 基于Zhao等[23]关于核壳结构中能量释放率的研究, Wu和Lu[24]建立了核为LiNi0.8Mn0.1Co0.1O2、包覆层为LiNi0.4Mn0.4Co0.2O2的核壳结构, 研究发现嵌锂过程中, 在壳内产生了拉伸切向应力, 可能导致壳体断裂, 而在脱锂过程中, 在核壳界面处产生了拉伸径向应力, 可能导致核心和外壳之间的脱黏, 从力学的角度解释了可能发生的两种失效模式, 并且采用能量释放率量化了核半径、壳层厚度、外加电流密度对壳层断裂和核壳界面处脱黏两种失效模式的影响, 构建了设计图用于指导核壳结构的设计. Zhang等[25]研究了恒压充放电条件下锂离子初始浓度和电极尺寸对空心碳纳米球壳电极中扩散诱导应力大小的影响, 结果表明, 初始锂离子浓度越低, 电极尺寸越小, 电极颗粒中的扩散诱导应力越小.
核壳结构在缓释应力的同时有效地限制了电极颗粒的膨胀, 是电极材料设计的一个发展方向. 为了进一步深化对于核壳结构的认识, 本文针对电极颗粒在充放电过程中的几何大变形问题, 采用有限变形假设建立了核壳颗粒模型来描述锂离子的扩散过程和由此产生的应力, 分析研究锂离子电池的失效机理, 进而重点研究核壳结构对硅负极材料的改善作用. 对于可能出现的失效情况, 计算了目前电极材料设计领域采用的两种方案, 探索了单、双层核壳结构对应力的缓冲效果, 为锂离子电池核壳结构电极的设计提供了理论依据和优化策略.
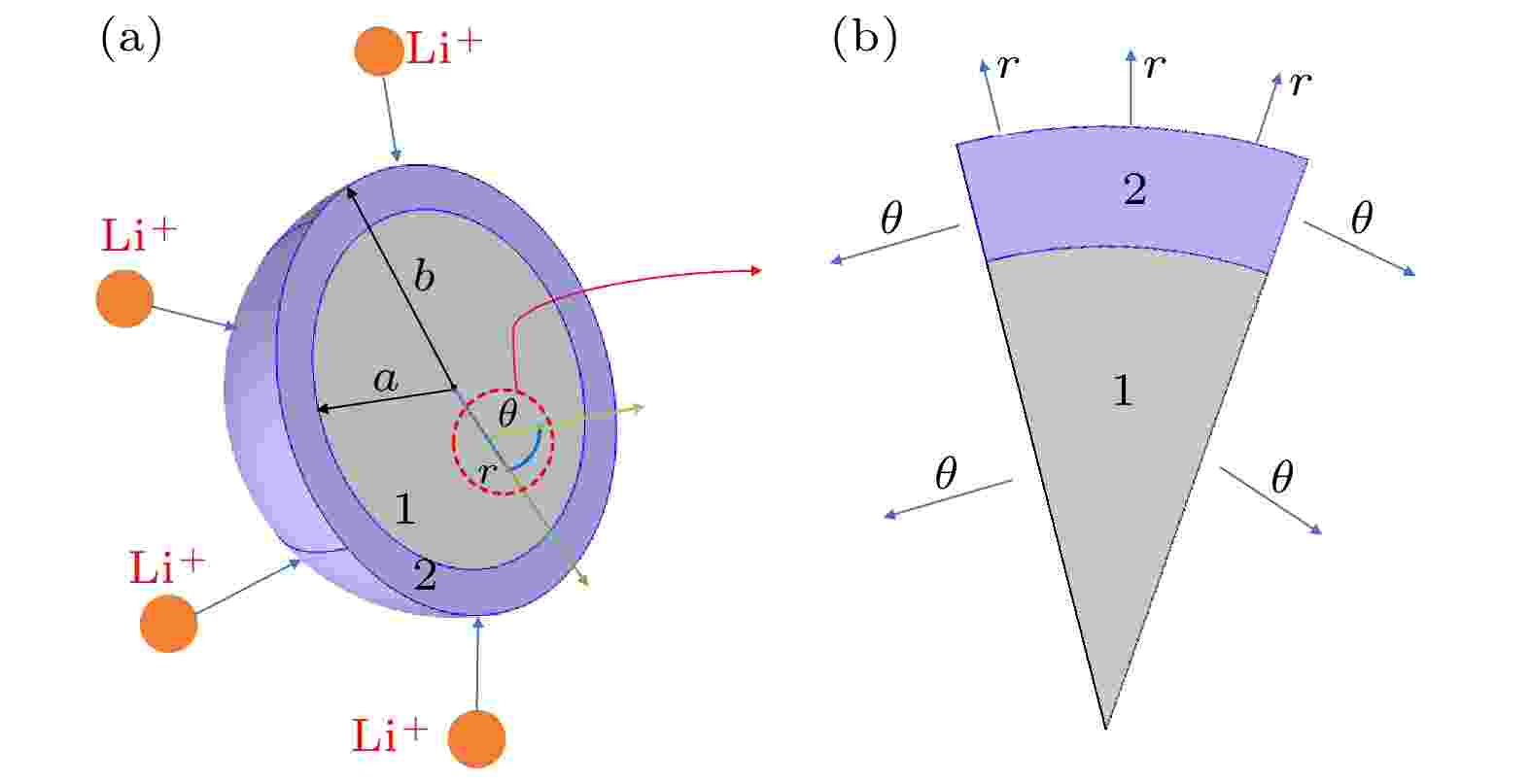
Figure3. (a) Schematic diagram of core-shell structure of lithium-ion battery; (b) radial and tangential schematic diagram.
2
2.1.电化学过程
核壳结构中锂离子的扩散用Fick第二定律[26]来描述. 根据动力学理论, 活性粒子在化学势μ的梯度的驱动下扩散[27], 表达式为
在化学势μ包含静水应力项




将方程(2)代入(1)式中, 可以得到:

2
2.2.力学过程
首先认为力学平衡过程远快于扩散过程, 因而是一个静态问题. 考虑锂化过程发生的几何大变形, 控制方程组表述如下.1)几何方程: 对于球对称的各向同性球形颗粒, 若球体的径向位移为u, 应变分量与径向位移u有关[29]. 在有限变形问题中, 区分参考构型与当前构型, 以下方程都在当前构型中建立. 基于连续介质力学大变形理论, 应变-位移关系可以表示为


本文考虑球形颗粒不受外在束缚的理想状态. 则有如下的边界条件:
2
2.3.材料参数
将具有高导电性、充放电过程中体积变形小等优良特点的碳作为硅负极电极颗粒的包覆层材料, 核与壳的材料参数如表1所列. 其中对于硅电极颗粒, 完全锂化状态的体积膨胀约300%, 因此其在有限变形条件下的偏摩尔体积是通过
参数 | 核 | 壳 |
饱和浓度 Cmax/(mol·m–3) | 2.95 × 105 | 2.4 × 104 |
初始浓度C0/(mol·m–3) | 0 | 0 |
扩散系数 D/(m2·s–1) | 1.0 × 10–16 | 1.45 × 10–13 |
内径/外径 R/m | 4 × 10–8 | 5 × 10–8 |
泊松比 ν | 0.23 | 0.30 |
杨氏模量E/Pa | 8 × 1010 | 6 × 1010 |
偏摩尔体积 Ω/(m3·mol–1) | 3/Cmax | 3.497 × 10–6 |
室温 T/K | 298 |
表1核壳结构材料参数[16,32,33]
Table1.Material parameters of core-shell structure[16,32,33]
2
3.1.有限变形效应
针对高能量密度所带来的体积膨胀, 计算了小变形理论的径向应力与切向应力, 与有限变形理论的数值结果进行了对比, 如图4所示. 随后模拟计算得到浓度场和应力场, 结果如图5所示.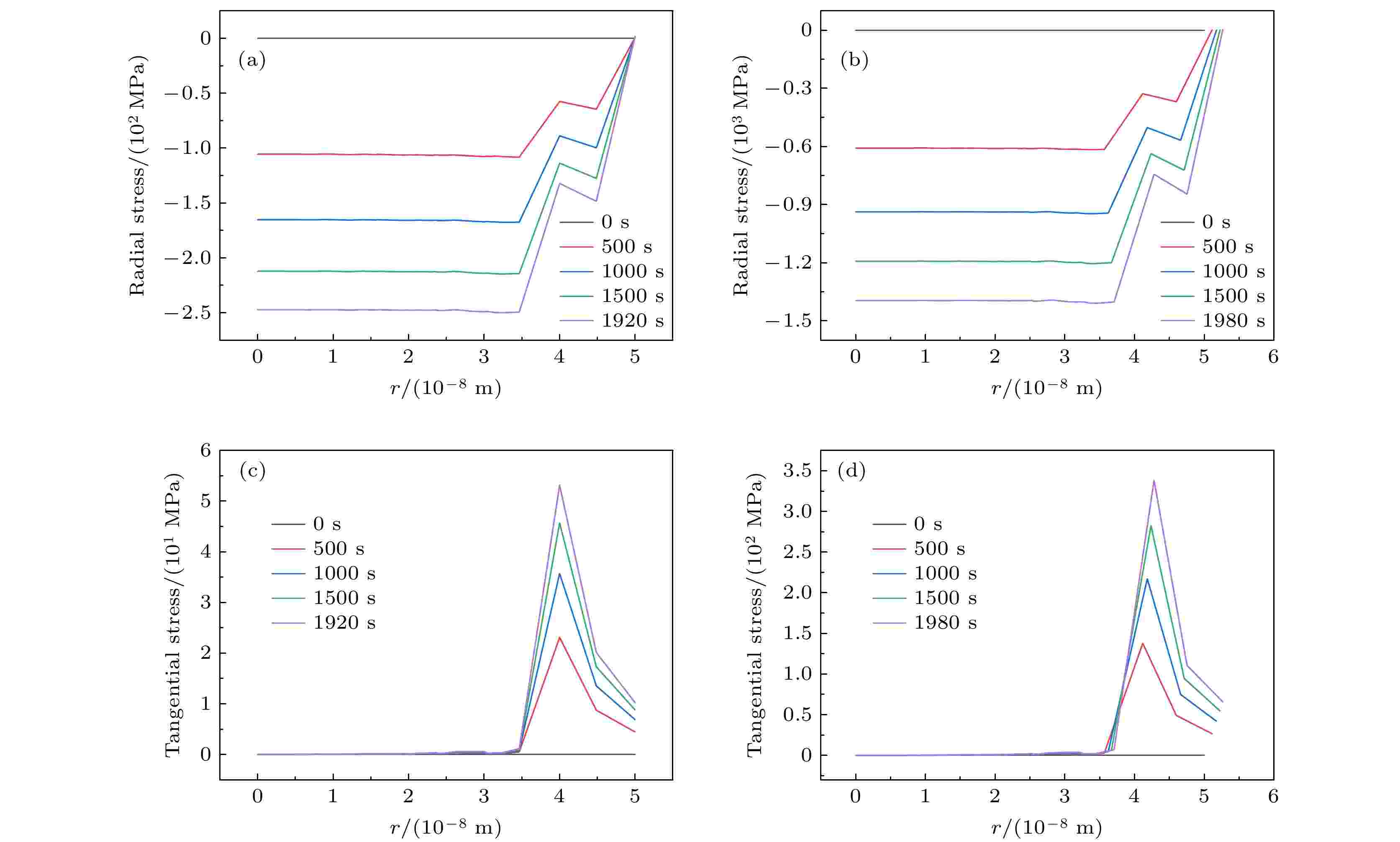
Figure4. Radial stress and tangential stress along the radial direction during charging under different hypothesis: (a) Radial stress under small deformation; (b) radial stress under finite deformation; (c) tangential stress under small deformation; (d) tangential stress under finite deformation.
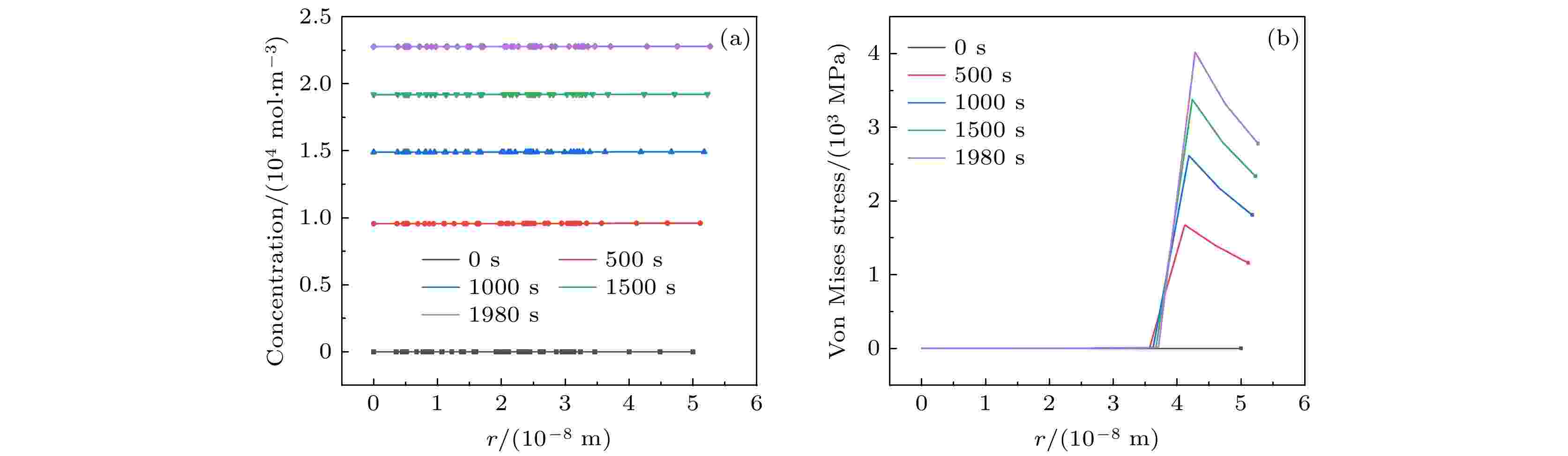
Figure5. Schematic diagram of (a) concentration; (b) von Mises stress along the radius during lithium insertion.
对比图4(a)和图4(b), 可以看出, 有限变形假设下的应力在各个时刻均大于小变形假设下的应力, 而且小变形条件下的半径随着锂化的进行, 并没有表现出增大的趋势, 而在有限变形的基础下, 核壳结构的半径随着充电过程的进行越来越大, 表明有限变形假设能正确地描述材料的膨胀. 在颗粒的外表面, 径向应力为0, 这是由方程(13)所定义的. 外表面不受约束的情况下, 在锂化过程中随着锂原子的扩散, 硅颗粒开始膨胀, 内部承受拉应力. 然而, 在图4(a)和图4(b)中核壳结构表现出径向压缩应力, 这是由于包覆层材料对硅体积膨胀的限制.
图4(c)和图4(d)为材料半径方向的切向应力分布图, 可以看出, 不同时刻下, 锂浓度的变化对切向应力的影响较大, 有限变形条件下的应力水平明显大于小变形. 为了限制硅核心的膨胀, 在核壳界面处产生了较大的切向应力, 这种切向拉伸应力可能会导致壳层材料的断裂.
锂离子电池有限变形理论下的浓度场与von Mises应力场结果如图5所示.
图5(a)给出了核壳结构在锂化过程中, 锂离子浓度沿径向的分布图. 嵌锂开始前, 整个核壳结构的浓度为0, 随着锂不断嵌入至外部的碳壳层饱和(停止条件), 硅核心材料与壳层的锂离子浓度均在增大, 而且注意到核壳结构趋向于均匀分布, 这是因为在核壳结构中的扩散应力会促进锂离子的快速扩散. 图5(b)为不同时刻碳包覆硅电极内的von Mises应力沿着径向的分布云图. 随着锂离子的不断嵌入, 颗粒会发生膨胀而产生应力, 可以看出核壳两相之间的von Mises应力差异较大, 核心材料相比于壳包覆层材料应力水平明显很低, 壳层为了保持结构稳定性以及限制硅颗粒的膨胀, 承受着巨大的应力.
针对有限变形条件下核壳结构中可能出现的失效情形, 考虑材料和结构效应带来的影响, 模拟了以下两种结构的优化: 1)单层核壳结构, 2)双层核壳结构. 模拟所使用的参数如表2所示.
参数 | 杨氏模量E/Pa | 饱和浓度Cmax/(mol·m–3) | 偏摩尔体积Ω/(m3·mol–1) | 泊松比ν | 扩散系数D/(m2·s–1) |
碳层[34] | 1 × 1010 | 24161 | 3.497 × 10–6 | 0.3 | 1.0 × 10–14 |
外包覆层[35] | 3 × 1010 | 2.5 × 104 | 3.497 × 10–6 | 0.3 | 1.0 × 10–14 |
表2包覆层碳的材料参数
Table2.Material parameters of the outer shell.
2
3.2.单层核壳结构
为了降低核壳结构有限变形模型下的应力, 本文数值模拟了不同的包覆层碳, 以比较包覆层材料对活性颗粒结构的电化学和力学性能的影响. 图6所示为嵌锂过程中浓度、von Mises应力、径向应力和切向应力随着时间的分布示意.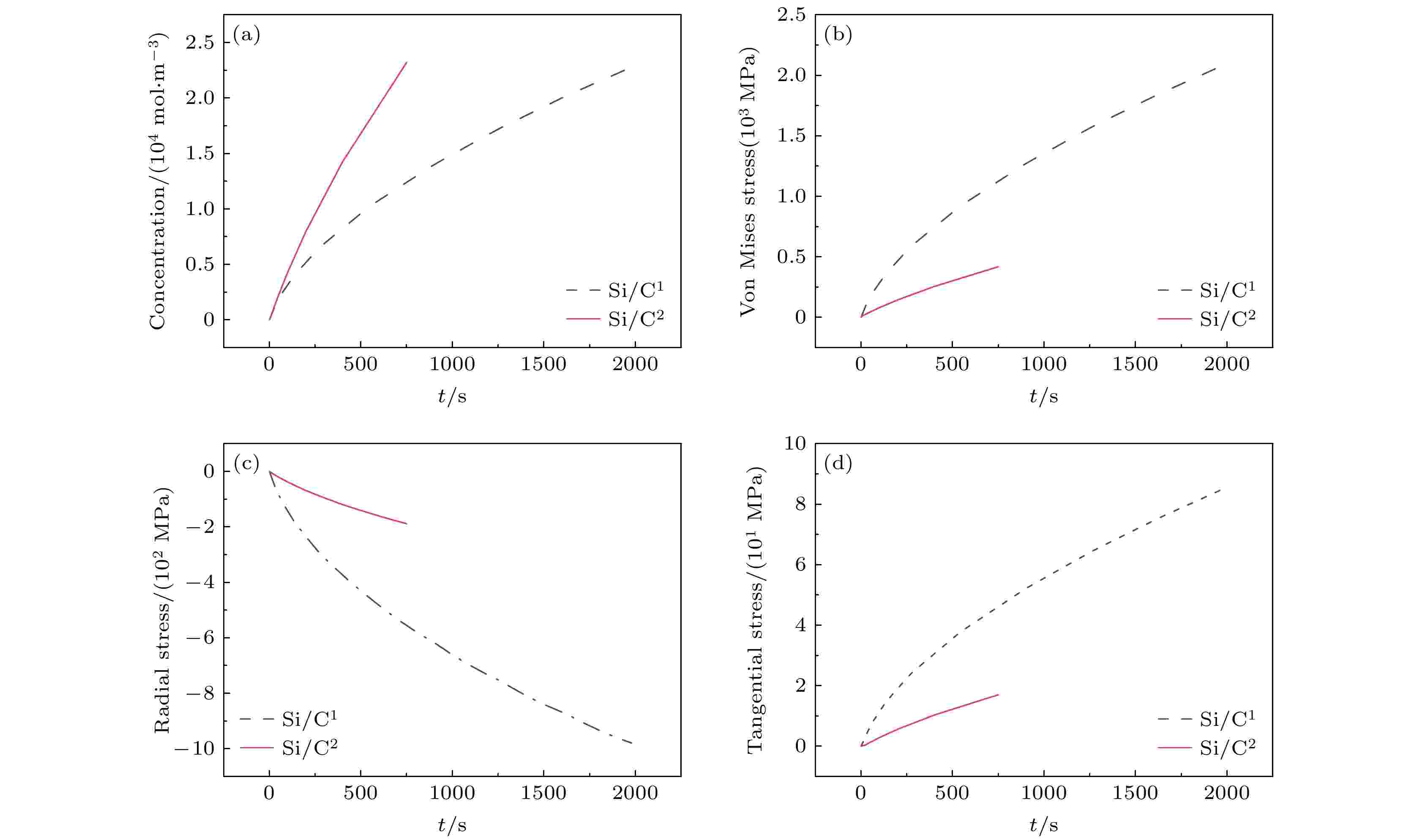
Figure6. Schematic diagram of the distribution of (a) concentration, (b) von Mises stress, (c) radial stress, and (d) tangential stress over time during lithium insertion.
由于锂离子浓度沿着颗粒径向基本保持均匀而且核壳界面处的应力数值最大, 因此选取了核壳界面处的一点作为随时间变化曲线图的基点. 图中黑线代表了3.1节讨论部分的核壳结构, 表示为Si/C1, 红线代表使用了不同碳包覆材料之后的结果图, 用Si/C2来表示.
由图6(a)可看出在达到相同的饱和浓度时, 使用表2参数的包覆层所用的时间更少, 表明选取合适的包覆材料可以更快地传输锂离子, 提高锂离子电池的倍率性能.
从图6(b)—图6(d)可以看出: 随着时间的延长, Si/C2在核壳界面处的Von Mises应力、径向应力、切向应力都明显降低. 应力水平的整体降低体现了使用更软的包覆层材料对于减少活性颗粒的力学损伤、限制硅核心的体积变化、提高结构的稳定性有着重要的作用.
因此, 使用更软的包覆层材料, 可以有效地提高核壳结构的电化学与力学性能, 从而实现锂离子电池更长的循环寿命.
2
3.3.双层核壳结构
另一种抑制体积膨胀、提高电极机械性能的结构是双层壳结构, 该结构既可以缓解电极颗粒的体积膨胀, 也可以维持内部核壳结构的稳定性.本文在Si/C1核壳结构的外表面, 再包覆一层机械和导电性能良好的纳米级别的碳材料, 形成Si/C1/C3双层核壳结构, 在下图中用Si/C1/C3表示. 最外层碳的厚度与第一层碳的厚度一致, 均为10 nm.
对表2与表1参数下构建的核壳结构和双层核壳结构进行多物理场仿真计算, 得到结果如图7所示. 图7(a)是Si/C1与Si/C1/C3双层核壳结构的浓度随着时间的分布图, 可以看出, Si/C1/C3双层核壳结构更快地达到了壳的饱和浓度, 这表明双层核壳结构有着更加优秀的扩散性能, 加快了锂离子嵌入核壳结构, 是改善负极颗粒电化学性能的有效方法.
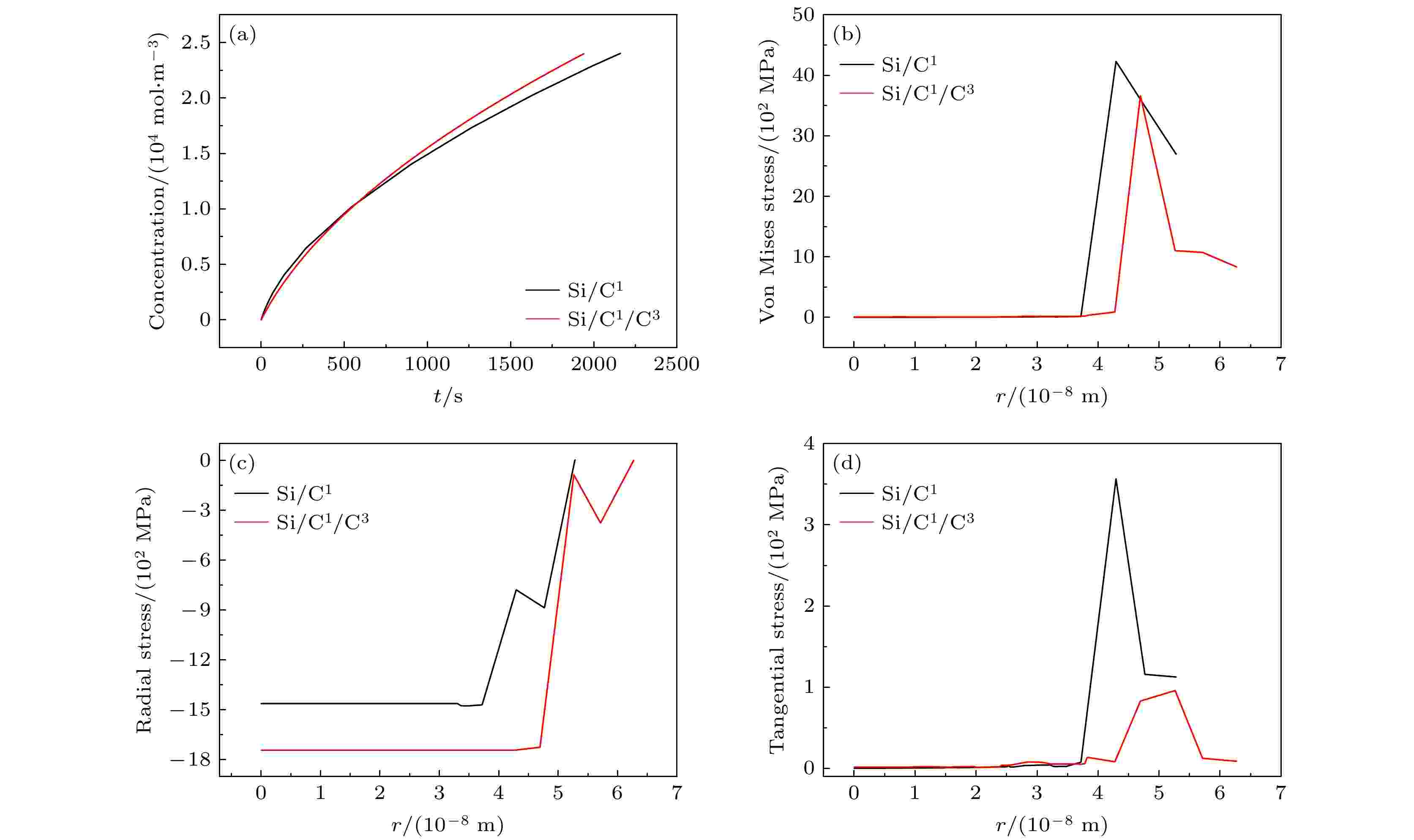
Figure7. Schematic diagram of the distribution of the double-layer core-shell structure during lithium insertion process: (a) concentration; (b) von Mises stress; (c) radial stress; and (d) tangential stress.
图7(b)为达到停止条件时单、双层核壳的von Mises应力沿着径向的分布图. 对比显示, 双层核壳的应力水平整体低于只有一层碳包覆的核壳结构, 这是内层壳与外层壳之间, 壳与核之间相互制约和相互作用所致.
图7(c)是Si/C1核壳结构与Si/C1/C3双层核壳结构的径向应力沿着半径方向的分布图, 在有限变形的情况下, 双层核壳结构表现出了更大的径向压缩应力. 这种径向应力是核壳脱黏的原因, 这也导致了双层核壳结构相较于核壳结构有更大的脱黏风险.
图7(d)为达到停止条件时单、双层核壳的切向应力沿着径向的分布图. 相对于单层核壳结构, 双层核壳结构的切向应力则大幅降低, 且在核壳界面处变化较为平缓, 显示了更好的结构稳定性. 根据Wu和Lu[24]的发现, 切向拉伸应力可能导致壳结构的断裂, 因此双层核壳结构有效地避免了切向应力过大而造成的包覆硅结构的碳材料的失效, 进而提高了电池的循环稳定性.
从以上分析可以看出, 双层核壳结构有着更加优越的电化学性能, 有利于避免包覆硅材料的碳结构的断裂, 随之而来的是增加了核与壳之间的脱黏概率.
2
3.4.双层核壳结构的优化
双层壳为电极设计提供了一个新的自由度: 壳层材料的选取与组合. 本文考虑两层壳之间杨氏模量的影响, 将内外层壳的材料互换, 即形成Si/C3/C1双层核壳结构, 来比较对于硅电极材料的包覆效果, 结果如图8所示. 其中两种双层核壳结构分别用Si/C1/C3和Si/C3/C1来表示.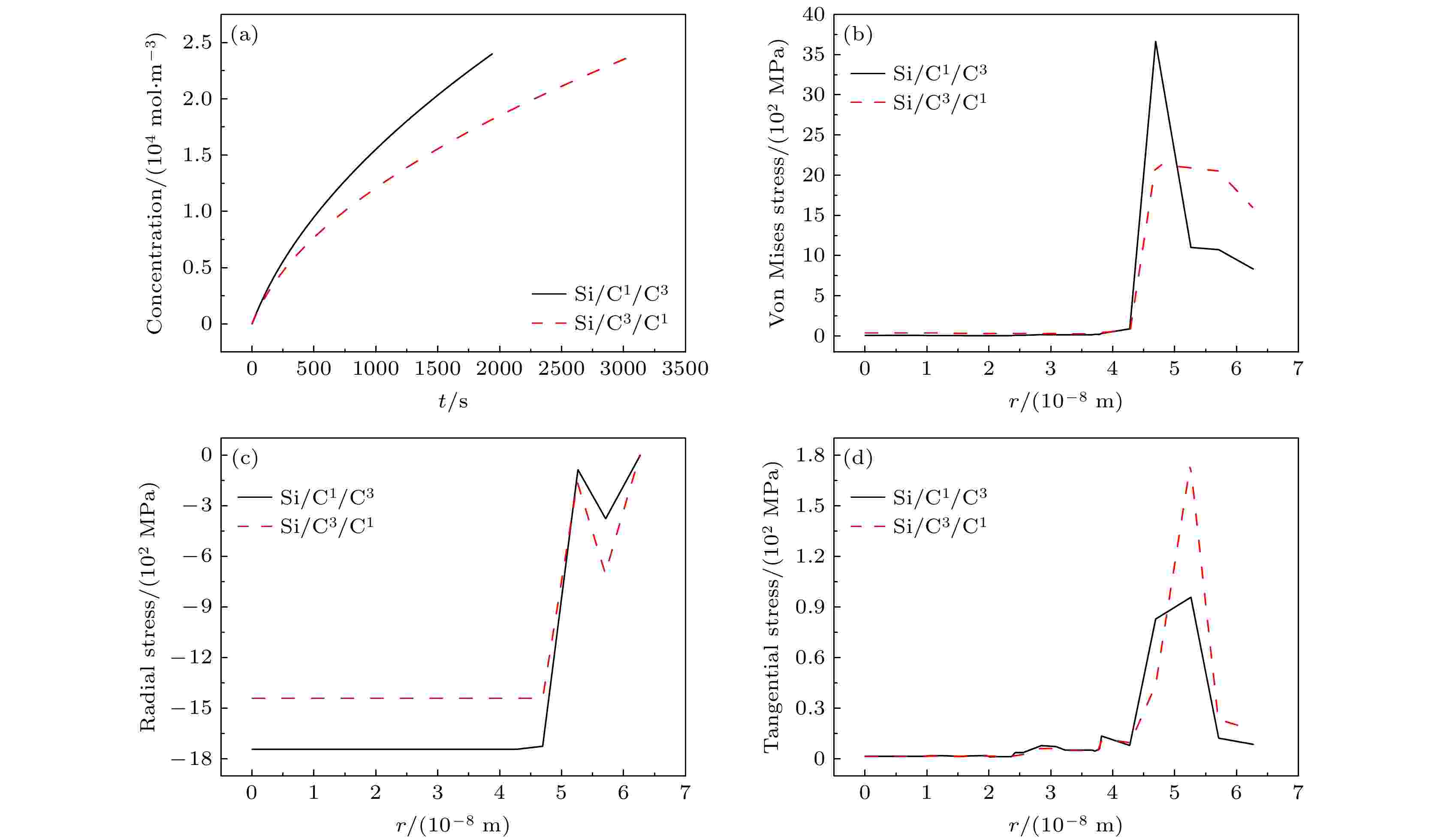
Figure8. (a) Concentration, (b) von Mises stress, (c) radial stress, and (d) tangential stress distribution schematic diagram of Si/C1/C3 double-layer core-shell structure and Si/C3/C1 double-layer core-shell structure.
图8(a)以核壳界面处的一点为研究对象, 对比了Si/C1/C3双层核壳结构和Si/C3/C1双层核壳结构对于嵌锂过程中锂离子浓度扩散的影响. 由图8可以看出, Si/C1/C3双层核壳结构更快地达到了结构中锂离子的饱和状态. 与图7(a)对比, 这表明了内外层壳材料的不同, 影响锂离子扩散的反应动力学, 从而影响倍率性能.
双层碳包覆层不仅防止了硅颗粒与电解液之间的直接接触, 也充当了硅颗粒在充电过程中体积膨胀的缓冲介质. 图8(b)和图8(c)分别显示了当达到饱和浓度时, Si/C1/C3双层核壳结构和Si/C3/C1双层核壳结构的von Mises应力、径向应力沿着径向的分布. 由图可得, 双层核壳的应力在嵌锂过程中不断增加, 沿着径向Si/C3/C1双层核壳结构的von Mises应力、径向应力均低于Si/C1/C3双层核壳结构. 而且对比von Mises应力可以发现, 互换壳层材料之后的von Mises应力在核壳界面处更加平缓. 结合图7可以看出, Si/C3/C1双层核壳结构的稳定性更加优越, 因此内软外硬的双层核壳结构有利于缓解结构中的von Mises应力和径向应力. 图8(d)为当达到饱和浓度时, 内外层壳材料不同的双层核壳结构的切向应力沿着径向的分布示意图. 虽然Si/C3/C1双层核壳结构的切向应力大于Si/C1/C3双层核壳结构的切向应力, 但是对比图7(d), 仍然低于核壳结构的应力水平.
在本文的理论框架范围内, 为了探究双层核壳结构优化, 对内外碳层材料的杨氏模量进行了进一步讨论. 图中E1和E2分别表示内层壳、外层壳的杨氏模量, 且E1 = 60 GPa与E2 = 30 GPa代表了Si/C1/C3双层核壳结构. 图9(a)表示了4组不同杨氏模量下, 核与内层壳界面处一点的锂离子浓度随时间分布图.
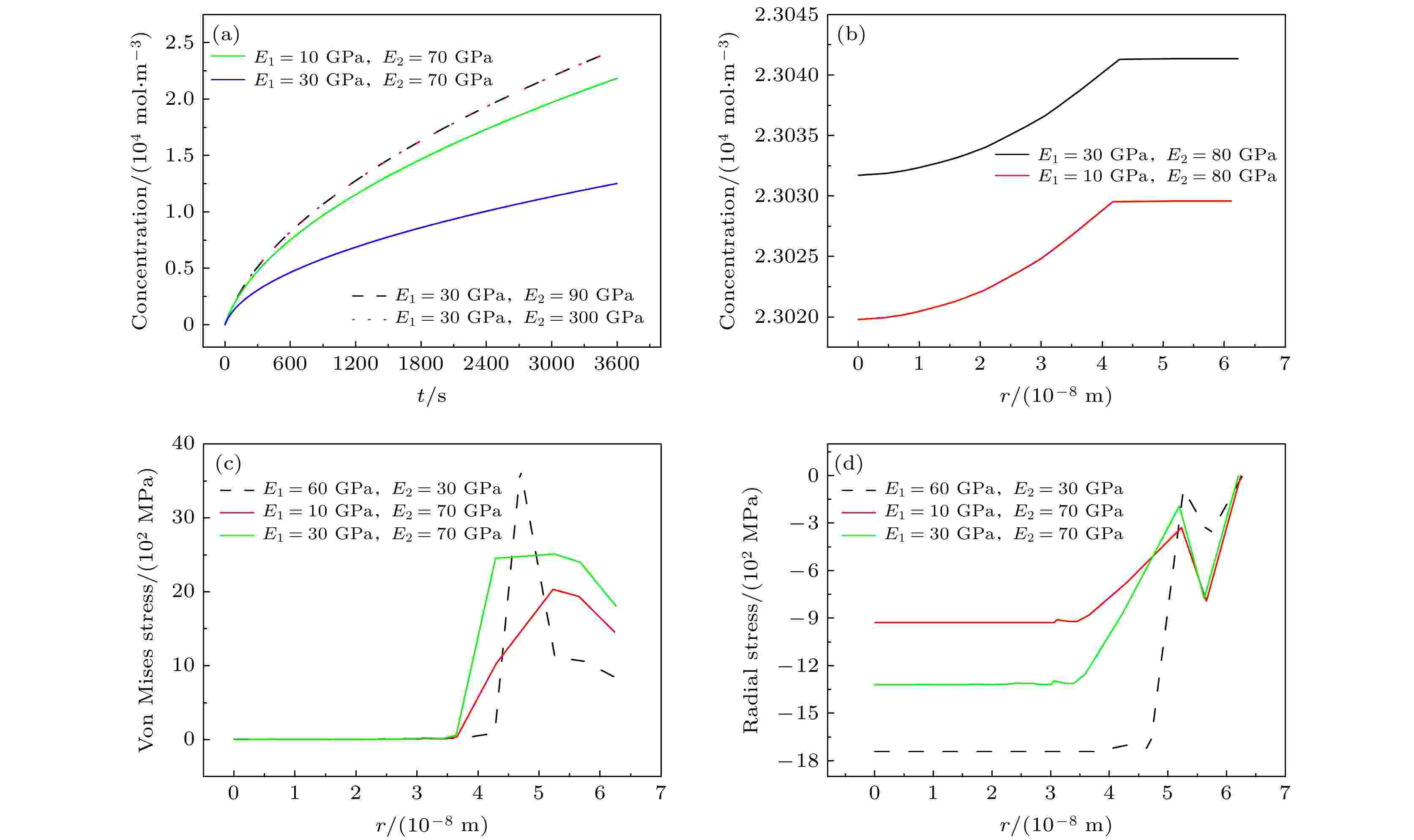
Figure9. (a) Concentration, (b) concentration, (c) von Mises stress, (d) schematic diagram of radial stress distribution under different Young's modulus of inner and outer shells.
图9结果表明, E2 = 70 GPa时, E1 = 10 GPa与E1 = 30 GPa锂离子浓度均在3600 s内达到饱和浓度. 而当E2 = 90 GPa时, 锂离子浓度在3600 s内并没有到规定的饱和浓度(2.4 × 104 mol/m3), 说明活性颗粒的电化学性能变弱. 随着外层杨氏模量增大到300 GPa时, 双层核壳结构的嵌锂能力更差. 进一步缩小外层壳杨氏模量的范围, 以E2 = 80 GPa为研究对象, 由图9(b)可得3600 s时仍未达到壳层的饱和浓度. 因此综合图9(a)与图9(b), 从锂离子的电化学性能考虑外层的硬度不能高于70 GPa, 而内层壳的杨氏模量最小可到10 GPa(文献中可查到的碳最小杨氏模量).
本文将此优化范围内的扩散应力与Si/C1/C3双层核壳结构中的应力水平进行了对比, 得图9(c)与图9(d). 图9(c)和图9(d)分别显示了结构中的von Mises应力、径向应力沿着径向的变化规律, 其中红线与绿线代表了内软外硬的双层核壳结构. 数据显示在合理范围内的内软外硬双层壳结构应力水平显著低于Si/C1/C3双层核壳结构.
综上所述, E1不低于10 GPa, E2不高于70 GPa的内软外硬的双层壳, 可对硅基双层壳结构中的应力起到很好的缓解作用.
针对这种失效情况, 研究了两种解决方案: 1)单层核壳结构, 2)双层核壳结构. 通过分析可以得出, 使用不同的包覆层材料, 能有效地改善材料内部的应力水平, 从而提高核壳结构的循环性能. 使用两种不同的材料包覆硅电极材料, 得到双层核壳结构, 可以有效降低充电过程中的扩散诱导应力. 进一步对双层核壳结构的硬度进行优化, 发现在锂化过程中内软外硬的双层壳的应力水平更低, 有助于更好地减少活性材料的失效, 并且经过计算发现优化范围为: 内层壳杨氏模量不低于10 GPa, 外层壳杨氏模量不高于70 GPa.