现代发动机多采用对流冷却、冲击冷却、肋壁强化换热和扰流柱强化换热等冷却方式。在涡轮导向叶片中,冲击冷却技术应用较多。导管是导向叶片实现冲击冷却的重要结构件,嵌在叶片内腔,一般由管身、冲击孔构成,某些叶片还创建有定位突起[2-3]。冲击冷却气流示意图见图 1,冲击冷却结构及导管示意图见图 2。
![]() |
图 1 冲击冷却气流示意图 Fig. 1 Schematic diagram of cooling flow of impingement cooling in blade |
图选项 |
![]() |
图 2 冲击冷却结构及导管示意图 Fig. 2 Schematic diagram of impingement cooling structure and pipe |
图选项 |
随着发动机燃气温度的不断提升,根据叶片冷却结构的发展趋势,气膜孔、扰流柱、弯扭隔肋和扰流肋等冷却结构均有可能应用于导向叶片中。基于预研考虑,有设计人员提出,导管建模应当将上述现有的冷却结构均纳入考虑范畴,以尽可能增加建模适应性与准确性。这给导管的快速建模带来了如下困难:①叶片内腔表面的连续性被冷却结构破坏,管身需要适应形状复杂的叶片内腔;②为了保证导管与叶片内腔的精确配合,导管上需要创建定位突起,突起与叶片内壁贴合,手动建模时需要进行大量测算;③导管上冲击孔及突起成组分布,数量较大;④导管位于叶片内部,操作不便。以上困难使得手动创建导管人机交互繁杂,效率低下。
为提高建模效率,许多研究者对涡轮叶片及其冷却结构的快速建模技术进行了探讨:北京航空航天大学席平课题组利用特征造型和参数化建模技术开发了涡轮叶片的快速建模系统,并分别就涡轮叶片的叶身、伸根、转接段、扰流肋、尾缝等特征的造型方法进行了研究[4-7]。迟重然[8]和王松涛[9]等提出了单元设计法,实现了面向管网计算的涡轮动叶冷却结构的参数化设计。曹率等[10]针对涡轮叶片气膜孔参数化进行了研究。迟重然[8]和王松涛[9]等还针对叶片的传热设计进行了研究,其中涉及导管快速建模,但其建模方法具有以下缺点:①不涉及定位突起建模;②主要针对冲击孔建模,大量数据直接导入,缺少交互,模型用于计算机辅助工程(Computer Aided Engineering,CAE)分析,不适用于设计。
以上研究或不涉及涡轮叶片导管的建模研究,或不曾解决预定精度要求下的建模效率问题,因此本文提出涡轮叶片导管快速建模方法,首先对导管的几何特点及设计特征进行分析,归纳导管建模的要求,提出导管建模的整体方案并就导管快速建模方法中的细节问题进行讨论,最后在Unigraphis (UG)平台上开发了涡轮叶片导管快速建模程序,验证了本文所提出方法的有效性。
2 导管建模方案分析 根据导管位于叶片流道的位置,可将导管分为前缘导管、后缘导管和单腔导管等。其创建方法基本相同,本文以前缘导管为例,进行建模方案分析。
以往手动导管建模时,一般直接以叶片内腔表面为操作对象,进行曲面组合,生成管身,以适应叶片内腔形状变化,然后在管身上创建冲击孔及突起。然而随着叶片内腔冷却结构日趋复杂,叶片内腔表面的连续性遭到破坏,管身无法由内腔曲面直接创建,需采用截面线积叠的方式创建。因而,如何构建截面线,使得管身曲面可以高度适应叶片内腔中叶片内型曲面与隔肋曲面的变化,是管身创建的重点。为使管身截面线适应叶片内腔,可以在叶身内腔曲面指定位置处创建截线,以此截线作为叶身曲面几何信息载体,并作为管身截面线的原始参考,完成管身截面线的设计。
同时,选取合适的截面线积叠方案,也是一个重要的考虑因素。管身积叠可以选用截面线整体造型法、曲面缝合法以及曲线网格法。截面线整体造型法在截面线拼接处容易出现参数扭曲的情况,需要对截面曲线进行多次优化。曲面缝合法能够有效避免叶身曲面在截面线拼接处出现参数扭曲的情况,但是缝合法不能保证型面的一阶连续性。曲线网格法是对缝合法的改进,克服了其曲面拼合处一阶不连续的缺点[11]。就导管曲面而言,当导管截面线拼接处达G1连续时,截面线整体造型法创建效果与曲线网格法基本等同。但是,曲线网格法步骤相对繁琐,参数化建模难度较大。而且,在边界表示(B-Rep)模型中,曲线网格法生成的曲面数量要远高于截面线整体造型法,如图 3所示,截面线组数相同时,2种方法创建的叶片,其线框模型截然不同。管身曲面数量众多,会影响后文截交包络裁剪法与曲线阵列方法的实现,也会增加后续有限元网格剖分的难度[12],因而管身建模采用截面线整体造型法。
![]() |
图 3 造型方法与曲面数量 Fig. 3 Modeling method and number of surfaces |
图选项 |
冲击孔的位置分布与几何参数是影响冲击冷却效果的关键因素,因而其建模需要设计人员反复修改。定位突起是将球体经多次裁剪而成,余留的突出部分与叶片内腔按照预定精度切触。由于叶片内腔及管身曲面均是自由曲面,且叶片存在气膜孔、扰流柱等冷却结构,这使得球心定位困难,需要进行大量测算。因而冲击孔与突起建模,需要设计人员承担较大的工作量。
另外,由于管身是管道状,所以冲击孔与突起实质上属于管壁附属特征。管壁附属特征快速建模的一大要点是:在管壁上执行布尔运算时,必须对布尔运算的工具体进行自动自适应性裁剪,否则会发生建模错误。例如,在创建冲击孔时一般采用管身(布尔目标体)与圆柱(布尔工具体)布尔求差的方式。但是为了避免出现如图 4(a)所示打不穿的情况,一般会将圆柱长度设置足够大,再适当裁剪圆柱以避免如图 4(b)所示错误[4, 10]。因此,在管壁执行布尔运算时,必须解决布尔工具体的自适应裁剪问题,否则建模算法将不具备稳定性。冲击孔与定位突起的建模同样面临这个问题。
![]() |
图 4 打孔易出现的问题 Fig. 4 Possible errors in creation of holes |
图选项 |
根据这些特点,导管的建模要求归纳如下:
1) 管身曲面由截面线整体放样生成,必须与叶片叶型、隔肋曲面相适应,并且具有一定光顺性,满足冷气流通的气动需求。
2) 设计突起球心的定位算法,使突起与叶片内腔的贴合达到预定精度。
3) 实现冲击孔或突起的沿曲面按某种规则阵列,减轻设计人员负担。
4) 设计裁剪算法使冲击孔与突起建模具有稳定性。
为实现上述要求,本文设计了涡轮叶片导管的快速建模方法,其总体方案如图 5所示。
![]() |
图 5 导管整体建模方案 Fig. 5 Project design of pipe modeling |
图选项 |
在叶身内型曲面及隔肋面上创建截线作为叶片内腔几何形状的原始依据,截取的曲线称之为截形曲线。对截形曲线进行偏置、桥接等一系列处理,获取连续的管身外型截面线,进而放样生成管身外型,使得生成的管身符合要求1);通过设计突起定位迭代公式解决了要求2);通过识别管身外曲面构造阵列曲线,设计了针对孔和突起的曲线阵列方法,满足了要求3);在冲击孔和突起建模时应用截交包络裁剪法,解决了要求4)。
第3节将详细介绍建模方法及相关算法。
3 导管快速建模方法 根据第2节所归纳的建模要求以及建模整体方案,本节将分别介绍导管建模方法中的管身快速建模方法、截交包络裁剪法、特征等弧长阵列方法以及突起建模方法。
3.1 管身快速建模方法 管身由截面线整体放样生成,管身创建的核心是构建管身内、外型截面线。管身截面线的设计依据是叶片内型盆背曲面以及隔肋曲面的几何形状信息,通过截形的方式获取。依据截形曲线的位置,本文将截形曲线称为叶盆曲线、叶背曲线和隔肋曲线。
如图 6所示的管身外型截面线,曲线SP、SB和SL分别由截取的叶背曲线、叶盆曲线和隔肋截线偏置而得,然后依次用圆弧过渡连接。内型截面线可由外型截面线直接偏置获得。由此内、外型截面线创建方案,提取管身创建参数见表 1。
![]() |
图 6 管身外型截面线 Fig. 6 Section curves of body of pipe |
图选项 |
表 1 管身参数 Table 1 Parameters of body of pipe
参数名 | 参数几何意义 |
D1 | 截形曲线向内偏置距离 |
C1 | 管身外型前缘处桥接圆弧半径 |
C2 | 管身外型叶背处桥接圆弧半径 |
C3 | 管身外型叶盆处桥接圆弧半径 |
D2 | 管身厚度 |
表选项
由管身参数可知,在构建管身外型截面线时需要创建多个桥接圆弧。在传统的建模机制中,对两条曲线做桥接圆弧,需要通过交互有序选取2条曲线,给定圆弧半径,再交互指定圆心的大致位置,才能获得预期的圆弧曲线。以2条相交曲线为例,如图 7所示,曲线S1与S2有交点P1,P2,欲在P1处获得圆弧d,仅输入2条曲线及圆弧半径,若不通过交互指定圆心大略位置,有可能得到图中a~h这8种桥接圆弧(部分桥接圆弧弧长较短,以虚线整圆示意),这显然不符合要求。因此,创建桥接圆弧时需要判断桥接曲线的交点状况,并且自动计算桥接圆弧圆心参考点。
![]() |
图 7 8种可能出现的桥接圆弧 Fig. 7 Eight possible bridge curves |
图选项 |
桥接圆弧圆心粗测算算法如下。
对于2条相交曲线,如图 7中S1与S2,若以交点P1及2条曲线作为平面分割基准,则P1点附近被曲线分割为4个区域。桥接圆弧a、b、c、d分别位于4个不同区域,且彼此无交叉,则可以在不同的区域内取点以指定桥接圆弧究竟创建于哪一个区域。以桥接圆弧d为例,取参考点算法如下:
1) 求交点P1,并将距离P1点较近的曲线端点视为曲线始点Ps,较远的点视为曲线终点Pe。
2) 计算P1在曲线S1上的参数u1,在S2上的参数t1。并计算曲线S1在参数u1处的切矢T1和曲线S2在t1处的切矢T2,由于S1、S2参数化方向未知,T1、T2指向不可确定,暂按图 8所示方向。
![]() |
图 8 参考向量的获取 Fig. 8 Creation of reference vector |
图选项 |
3) 分别求曲线S1与S2在始点处的参数u0和t0。
4) 曲线S1设置标识λ,若u0=0,λ=-1;若u0=1,λ=1。S2标识类推。
5) 设置参数步移δ=0.01;取 u2=u1+λ·δ, 并计算曲线S1在参数u2处的点P3 。类推在曲线S2上得到P4,创建参考向量
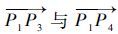
6) 若
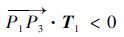

7) 令T=T1+T2,将T单位化,将点P1沿T平移距离r(桥接圆弧半径),得点P,则P必位于图 7中d所在区域,可以作为圆弧d的圆心参考。
在以上诸步骤中,第3)步~第6)步是创建参考向量,以保证P1点处所求切矢由Ps指向Pe。若在第7)步中将T1或T2反向,可以对应获取其他区域圆弧的圆心参考点。如图 8所示,获取的参考向量符合要求。
3.2 截交包络裁剪法 要解决管壁特征创建时布尔工具体的裁剪问题,关键在于适应性的获取裁剪曲面,使得布尔工具体位于布尔目标体任意位置时,构建的裁剪曲面边缘均完全位于裁剪工具体外部,或称裁剪曲面可以包络裁剪工具体,可以进行有效裁剪,使裁剪后的工具体尾端悬空于管道状模型内腔。本文设计了一种通过截交获取裁剪面的方法,称之为截交包络裁剪法,如图 9所示。下面介绍其步骤,并在图 9按照此方法创建空气冷却孔,解决第2节中图 4所述的问题。
![]() |
图 9 截交包络裁剪法 Fig. 9 Intersect-envelope trimming method |
图选项 |
1) 在目标体外表面上选取一点P,作为创建工具体的参考点;创建工具体,使其尺寸足以完成特征正常创建,见图 9(a)。
2) 工具体与目标体求交得一个或多个实体,从中选取P点所在实体,记为B。此处需要注意的是,做布尔交运算时管身实体和圆柱实体都必须保留。
3) 查询实体B所有面,存于链表中,从中删除P点所在曲面F0以及与F0相连的所有面,将链表中剩余的面缝合为一个片体T,见图 9(b)。
4) 延展片体T裁剪工具体,见图 9(c)。
截交片体T与管身内表面贴合,且T的边缘必然与工具体外表面重合,片体T自然延展后必然可以作为裁剪面,而且裁剪后的工具体也必然符合要求。应用此方法,可以在管身任意位置处稳定实现冲击孔与突起的建模,不会出现图 4所示的类似问题,图 9(d)中可见孔最终创建效果,仅打穿一侧管壁而不伤及管身其余部分。
3.3 特征等弧长阵列方法 当前主流的CAD软件主要支持线性阵列与圆弧阵列,而对于曲面上的特征阵列化支持稍显不足。针对曲面曲率变化较大的管身曲面,现有阵列功能不能适应冲击孔与突起的建模要求。本文设计曲线等弧长阵列,是在指定曲面内的指定曲线上,按照指定弧长创建一系列特征参考点,进而以这些参考点为基准创建相应特征。事实证明,该功能在进行初步设计时可以有效减少设计人员的工作量,提高设计效率,但无法应用于细节设计。该方法的实现可分为阵列曲线的获取与阵列参考点计算2大步骤。
总体来说,阵列参考点数目不多,计算成本不高,可以直接采用CAD系统等弧长函数,结合文献[13-14]采用列表的方式进行并不明显,因此无需进行额外的算法优化。
阵列曲线获取如下。
本文根据衬套冷却孔、突起的建模特点,提供投影法与交线法来获取位于套身外曲面上的阵列曲线。投影法是在套身外曲面上选取型值点,插值生成曲线并投影到套身外曲面上,特点是设计自由度大,可以设计形状复杂的阵列曲线。交线法是构建基准面与套身外曲面进行截交生成曲线,特点是操作简洁。以下给出交线法实现方法。①在套身外曲面F1上取被阵列的原始特征的定位点P0,计算曲面A在P0处的法向量n;②根据方向要求在曲面F1上选取阵列方向参考点P1;③计算向量
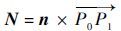
![]() |
图 10 阵列曲线的获取 Fig. 10 Creation of array-curve |
图选项 |
3.4 突起创建方法 在截交包络裁剪法与曲线阵列方法的基础上,突起快速建模只需解决突起球心的定位问题,以保证突起与叶片的切触精度。
为了定位突起球的球心,需要用户给定突起球直径D,同时在管身外曲面F1上给定参考点 p0(x0,y0,z0) ,参考点可以交互选定,也可以是曲线阵列计算得出。以 p0 作为初始输入,经过迭代,可以获取球心 pk(xk,yk,zk) 。迭代公式如下:
![]() |
式中: g(pk) 为pk点同叶片实体Bb的最小距离; r 为曲面F1在 p0 处单位法矢(指向实体内部),迭代终止条件为 yk+1∈[-ξ,ξ] , pk 点即为球心。
图 11给定了突起的创建流程,其中虚线框部分为突起球心定位迭代流程。
![]() |
图 11 突起建模方法流程图 Fig. 11 Flowchart of hump modeling procedure |
图选项 |
4 参数化建模实现 在以上研究的基础上,本文在Siemens NX7.5平台上,采用UG Open API开发完成导管快速建模程序,建模实例如图 12所示,必须声明的是此实例仅用于演示建模效果,无实际设计意义。程序被嵌入到“涡轮叶片快速建模系统”中,系统界面如图 13所示,可以实现叶身内、外型,隔肋,扰流肋,扰流柱和尾缝等十余种结构特征的快速建模和快速修改,并已在某发动机设计所应用。曲线阵列功能亦应设计人员要求,作为独立工具,嵌入该系统。
![]() |
图 12 导管建模结果 Fig. 12 Result of modeling of impingement pipe |
图选项 |
![]() |
图 13 涡轮叶片快速建模系统与导管建模程序 Fig. 13 Turbine blade rapid modeling system and impingement pipe modeling module |
图选项 |
5 结 论 本文针对涡轮导向叶片导管的结构特点进行了分析,提出导管快速建模方法,该方法解决了以下问题:
1) 提出了基于截形方法的管身创建方法。
2) 解决了参数化建模中桥接圆弧圆心参考点选取问题。
3) 通过设计截交包络裁剪法,解决了叶片或导管等管道状模型参数化设计易出现的裁剪问题。
4) 构建了定位突起的球心迭代公式,解决了管身突起的创建问题。
5) 设计了针对突起和冲击孔的等弧长阵列方法,有效提高了突起和冲击孔的建模效率。
根据以上研究工作,开发了导管快速建模程序,验证了本文所提方法的有效性。同时,该快速建模方法也为其他嵌入套管式零件的创建提供了参考。
参考文献
[1] | 冯国泰, 顾中华, 温风波, 等. 燃气涡轮机气冷涡轮气动设计体系设计思想及其应用[J]. 工程热物理学报,2009, 30(11): 1841–1848.FENG G T, GU Z H, WEN F B, et al. Aerodynamic design system & ideology of air-cooled turbine and its application to gas turbines[J]. Journal of Engineering Thermophysics,2009, 30(11): 1841–1848.(in Chinese). |
Cited By in Cnki (0) | Click to display the text | |
[2] | 陈凯.燃气涡轮冷却结构设计与气热弹多场耦合的数值研究[D].哈尔滨:哈尔滨工业大学,2010:6-9. CHEN K.Numerical research of gas turbine cooling structure design with aerodynamic thermal mechanical conjugate methods[D].Harbin:Harbin Institute of Technology,2010:6-9(in Chinese).(in Chinese). |
Cited By in Cnki (0) | Click to display the text | |
[3] | 谷振鹏, 王开. 冲击加气膜组合式换热效果的试验研究[J]. 航空发动机,2010, 36(5): 52–55.GU Z P, WANG K. Experiments invetisgation on heat transfer effectiveness of combined implingment and film[J]. Aeroengine,2010, 36(5): 52–55.(in Chinese). |
Cited By in Cnki (0) | Click to display the text | |
[4] | 宋玉旺, 席平. 基于特征造型技术的涡轮叶片参数化设计[J]. 北京航空航天大学学报,2004, 30(4): 321–324.SONG Y W, XI P. Parametric design of turbine blade based onfeature modeling[J]. Journal of Beijing University of Aeronautics and Astronautics,2004, 30(4): 321–324.(in Chinese). |
Cited By in Cnki (0) | Click to display the text | |
[5] | 朱谦, 宁涛, 席平. 基于引导线的涡轮气冷叶片伸根建模方法[J]. 北京航空航天大学学报,2012, 38(8): 1085–1089.ZHU Q, NING T, XI P. Root extending section of turbine blade modeling method based on guide curves[J]. Journal of Beijing University of Aeronautics and Astronautics,2012, 38(8): 1085–1089.(in Chinese). |
Cited By in Cnki (0) | Click to display the text | |
[6] | 张宝源, 席平, 杨炯. 复合弯扭涡轮叶片尾缝的快速建模[J]. 北京航空航天大学学报,2014, 40(1): 48–53.ZHANG B Y, XI P, YANG J. Rapid modeling of trailing edge slots in bowed-twisted turbine blade[J]. Journal of Beijing University of Aeronautics and Astronautics,2014, 40(1): 48–53.(in Chinese). |
Cited By in Cnki (0) | Click to display the text | |
[7] | 杨炯, 席平, 胡毕富, 等. 适应弯扭隔肋的涡轮叶片多种扰流肋造型方法[J]. 北京航空航天大学学报,2014, 40(6): 775–781.YANG J, XI P, HU B F, et al. Multi-type ribs of turbine blade modeling method fitting bowed-twist wall[J]. Journal of Beijing University of Aeronautics and Astronautics,2014, 40(6): 775–781.(in Chinese). |
Cited By in Cnki (0) | Click to display the text | |
[8] | 迟重然.气冷涡轮叶片的传热设计[D].哈尔滨:哈尔滨工业大学,2011:45-56. CHI C R.Heat transferring design for air-cooling turbine blades[D].Harbin:Harbin Institute of Technology,2011:45-56(in Chinese).(in Chinese). |
Cited By in Cnki (0) | Click to display the text | |
[9] | 王松涛, 迟重然, 温风波, 等. 涡轮动叶冷却结构设计方法Ⅰ:参数化设计[J]. 工程热物理学报,2011, 32(4): 581–584.WANG S T, CHI C R, WEN F B, et al. Cooling structures design for turbine blade I:Parametric design[J]. Journal of Engineering Thermophysics,2011, 32(4): 581–584.(in Chinese). |
Cited By in Cnki (0) | Click to display the text | |
[10] | 曹率, 莫蓉, 宫中伟. 航空涡轮叶片气膜孔参数化建模研究[J]. 航空计算技术,2011, 41(3): 77–81.CAO S, MO R, GONG Z W. Research on parametric modeling of aeronautic turbine blade film hole[J]. Aeronautical Computing Technique,2011, 41(3): 77–81.(in Chinese). |
Cited By in Cnki (0) | Click to display the text | |
[11] | XIA Y.The research of turbine blade modeling CAD system[D].Xi'an:Northwestern Polytechnical University,2004:19-22(in Chinese). |
Cited By in Cnki (0) | |
[12] | CHEN R Z,XI P.Analysis-oriented parametric modeling technology[C]//20122nd International Conference on IEEE Computer Science and Network Technology (ICCSNT).Piscataway,NJ:IEEE Press,2012:1208-1211. |
Click to display the text | |
[13] | LIU Y,FENG X,JIANG Z,et al.High-precision modeling of turbine blade from cross-section data[C]//2010 International Conference on IEEE Measuring Technology and Mechatronics Automation(ICMTMA).Piscataway,NJ:IEEE Press,2010,2:390-393. |
Click to display the text | |
[14] | KORAKIANITIS T, PANTAZOPOULOS G I. Improved turbine-blade design techniques using 4th-order parametric-spline segments[J]. Computer Aided Design,1993, 25(5): 289–299. |
Click to display the text | |