全文HTML
--> --> -->为此, 本文从背电极材料选取、结构设计及厚度优化出发, 采用COMSOL软件仿真研究了钙钛矿太阳能电池背电极电阻的变化, 并与实验结果对比, 分析得出优化的背电极属性.
图1(a)和图1(b)是文献[20](图1(a))及本文(图1(b))构建的背电极结构在COMSOL中的网格剖分图, 图1(c)是文献与本文计算的背电极电阻-厚度变化趋势. 从图1(c)可以看出, 文献中提取获得的阻值与本文仿真所得阻值虽然在部分厚度上有所区别, 但是总体符合很好. 它们平均相对误差小于0.6%, 误差基本可以忽略不记, 并且变化趋势两者一致, 由此验证本文模型构建及计算是对的.
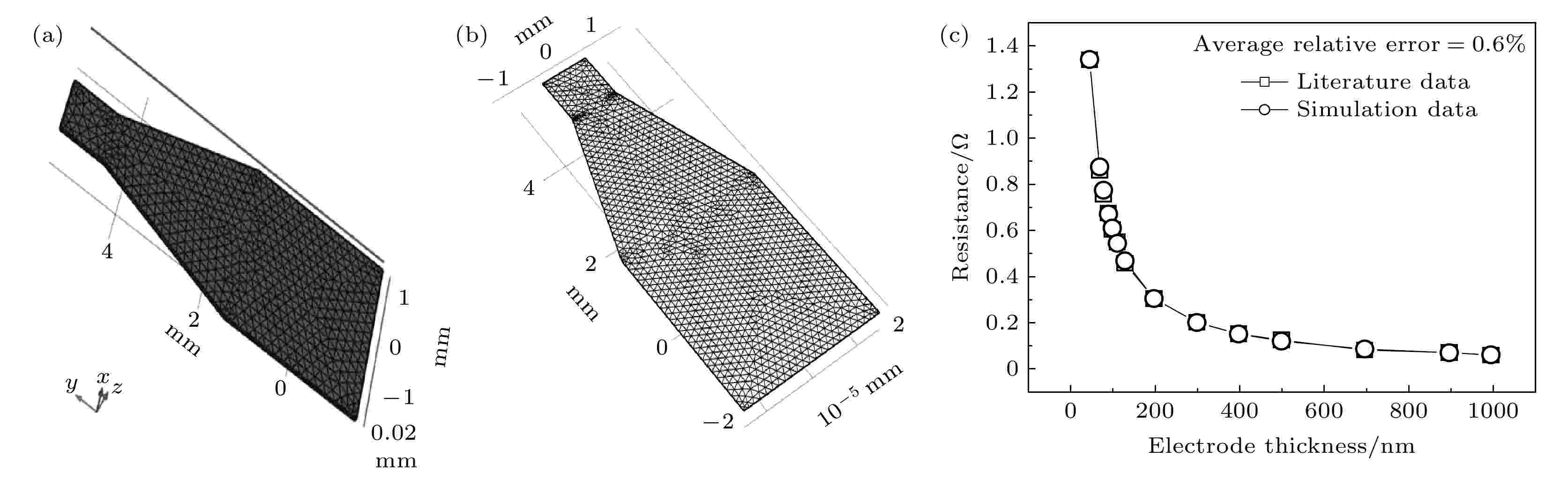
Figure1. The grid diagram of the back electrode structure constructed in literature (a) and this paper (b) in COMSOL; (c) back electrode resistance changing with its thickness.
3.1.背电极材料的影响
研究文献[21]中厚度为150 nm的铝(Al)、锡(Sn)、Ag、铁(Fe)、铜(Cu)、Au 6种八边形结构金属背电极的阻值. 图2(a)和图2(b)分别是6种金属背电极功函数、PCE及其电阻.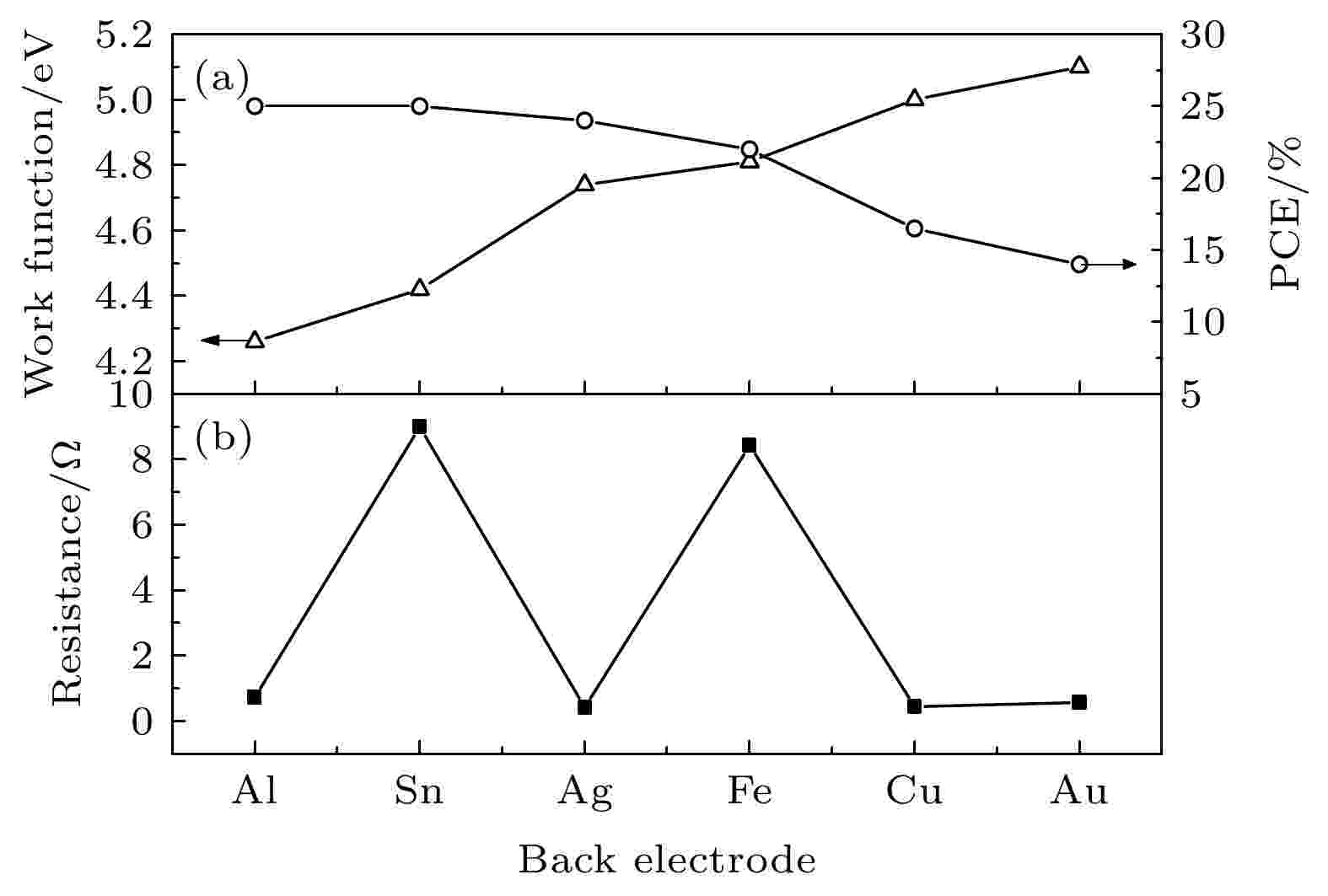
Figure2. Back electrode work function, cell conversion efficiency (a) and electrode resistance (b) of six metals.
由图2可知, 上述6种材料中Ag的阻值是最小的, 只有0.41881Ω, Au和Al则次之; 而Sn和Fe的电阻阻值最大, 远大于其他材料的阻值. 因此, 若只考虑金属材料自身电阻对钙钛矿太阳能电池的影响时, 使用Ag作为背电极材料制备的钙钛矿太阳能电池性能最好, 而使用Sn作为背电极材料制备的钙钛矿太阳能电池性能最差. 将上面金属电阻值分别和金属材料功函数以及文献中的PCE对比, 发现金属电阻小的其功函数和PCE不一定大, 而电阻大的其功函数和PCE也不一定小. 但可以看出金属功函数与电池PCE的大小成反比. 由此可知, 金属材料的阻值对电池性能影响没有功函数大. 采用上述方法进一步研究了八边形结构碳基背电极, 电阻值为8596 Ω. 尽管碳基背电极的阻值是Au电极的数千倍, 但其PCE仍然可以超过10%[11]. 因此, 背电极电阻值对电池效率的影响相对其他因素来说较小. 此外, 与文献[21]中三种空穴传输层NiO, Cu2O, P3HT下的钙钛矿电池PCE对比研究, 发现三种空穴传输层下, 金属性质对电池PCE影响规律一样, 即与金属电阻值相比, 金属功函数对电池PCE的影响更大.
2
3.2.背电极结构影响
33.2.1.蜂窝结构S-HQIDE和L-HQIDE背电极的比较
文献[22]分别设计了两种暴露面积的背电极结构: 一种是暴露面积较小的蜂窝结构(S-HQIDE), 它的背电极圆形直径约为2.7 μm, 边缘间距约为1.3 μm. 另一种是暴露面积较大的蜂窝结构(L-HQIDE), 它的圆形直径约为8.0 μm, 边缘间距约为1.5 μm. 图3是厚度2.5 μm的S-HQIDE(图3(a)和图3(c))和L-HQIDE(图3(b)和图3(d))的结构以及仿真图.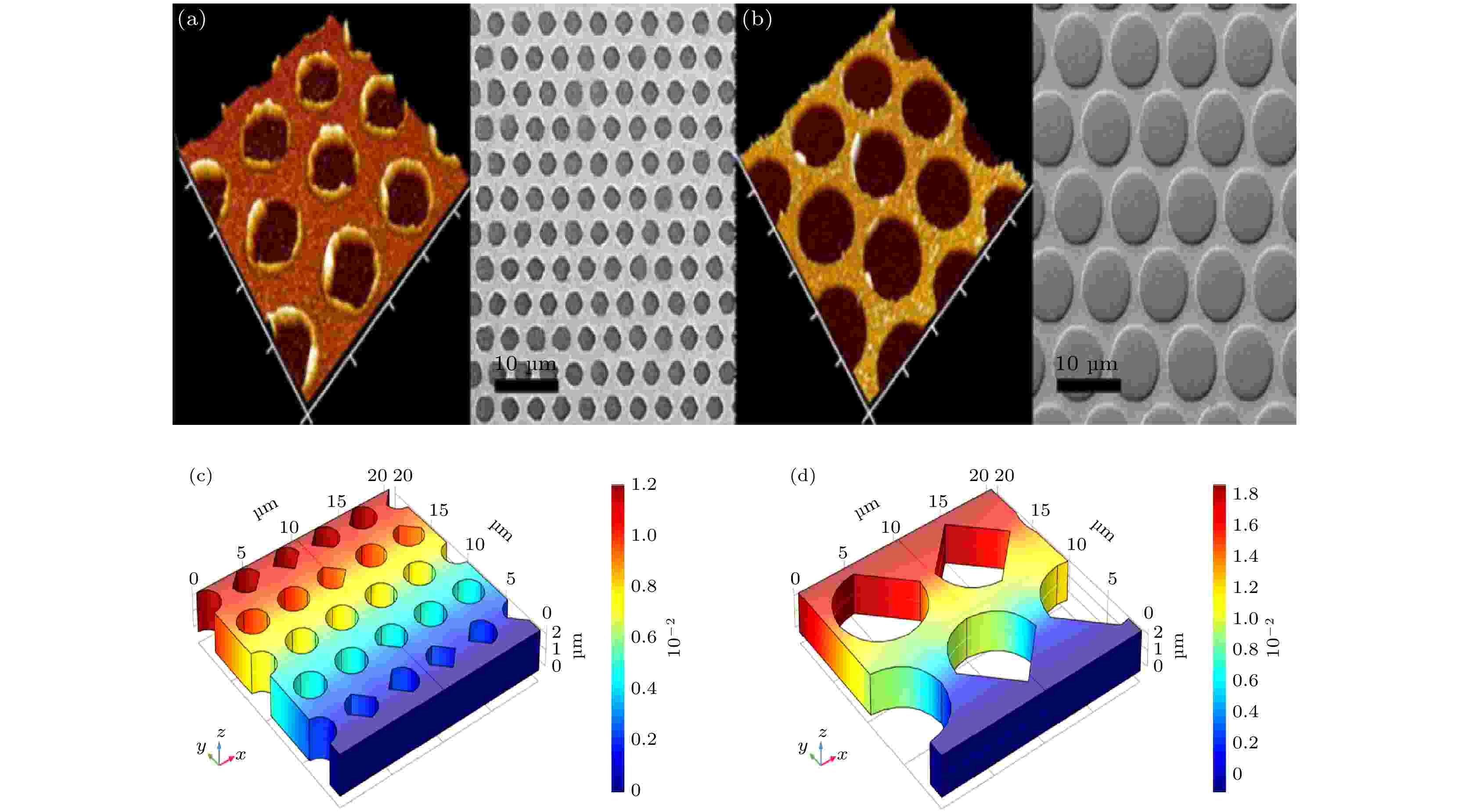
Figure3. Back electrode structure and simulation diagram of S-HQIDE ((a), (c)) and L-HQIDE ((b), (d)).
由图3知S-HQIDE结构的电阻为0.012249 Ω, 而L-HQIDE结构的电阻为0.017534 Ω. 两种结构电势相似, 都在水平方向上相等, 在竖直方向上均匀下降直至为零. 比较可知, L-HQIDE结构的阻值约为S-HQIDE结构的1.4倍. 若只考虑电阻的影响, 则使用S-HQIDE结构作为背电极的太阳能电池效率约为L-HQIDE结构背电极效率的1.4倍. 实验结果证明它们的PCE之比约为4倍. 因此, 蜂窝型结构背电极除了在阻值方面上影响效率外, 还在其他方面, 例如接触面积上影响了电池的效率.
3
3.2.2.蜂窝结构中圆形半径对背电极的影响
研究厚度为150 nm Ag薄膜蜂窝结构, 边缘间距分别为1和2 μm时, 圆形半径依次为0.5, 1, 1.5, 2, 2.5和3 μm的背电极电阻, 结果如图4所示.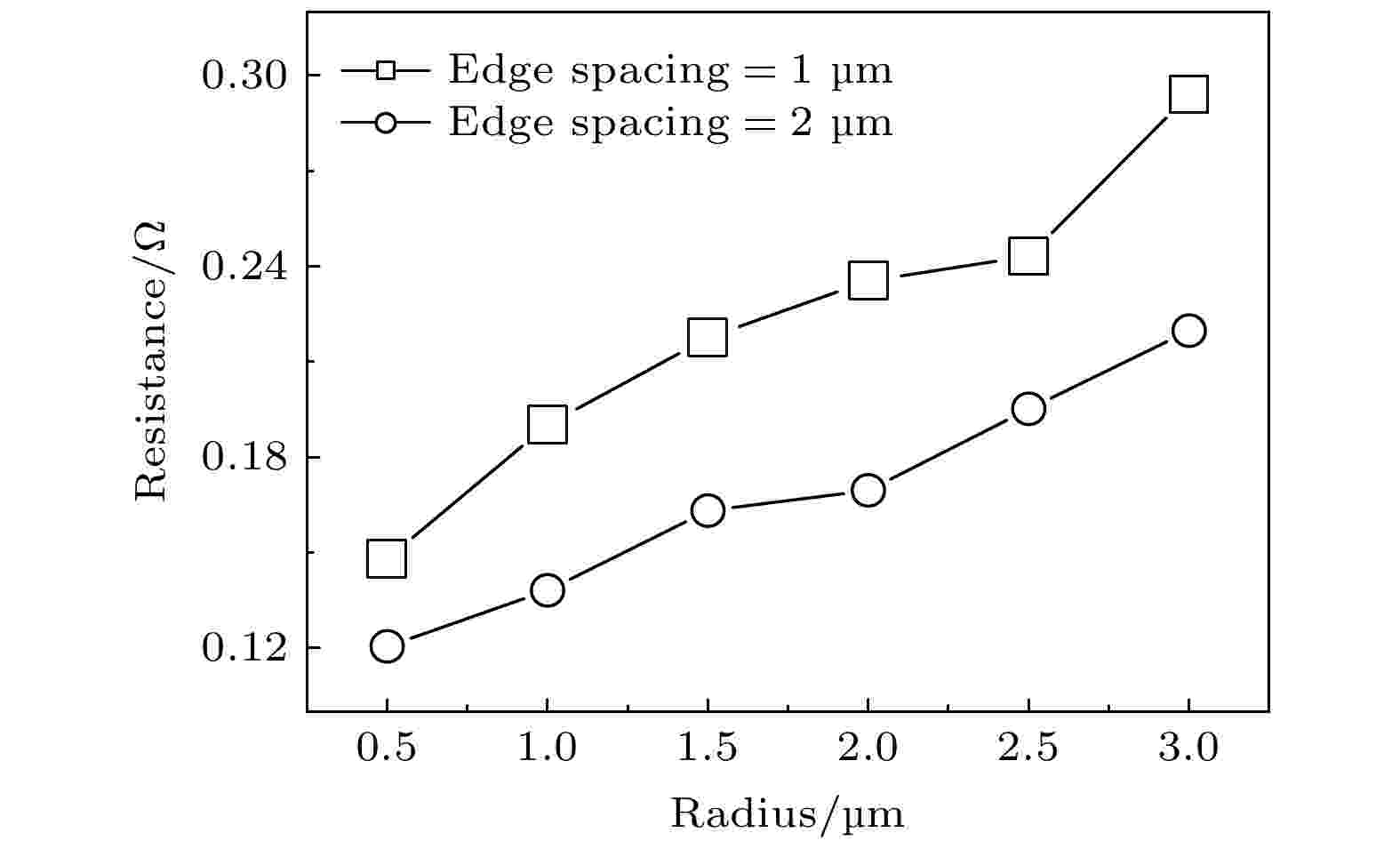
Figure4. The resistance of the back electrode with honeycomb structure varies with the radius of the circle.
由图4可知, 圆形半径为0.5 μm时, 边缘间距分别为1和2 μm的背电极阻值都最小, 半径为3 μm时电极阻值最大. 并且随着圆形半径的增加, 电阻是在逐渐增加的, 但是增大的趋势不是线性的. 同时发现, 在半径相同时, 边缘间距为2 μm的背电极阻值更小, 这可能是由于当边缘间距为2 μm时, 在相同的面积上, 该结构的圆形间隙个数更少, 占比面积较小, 因此使得它的电阻比边缘间距为1 μm时的小.
由此, 理论上来说蜂窝结构背电极的圆形半径是越小越好, 边缘间距越大越好. 但是圆形半径越小其制作就越复杂, 制作时间也要越长, 且边缘间距越大可能会使得整个电极的面积越大, 性价比低. 因此认为蜂窝结构的圆形半径约等于边缘间距时性价比最高.
3
3.2.3.多孔孔隙的占比对背电极的影响
最近基于多孔隙金背电极的钙钛矿太阳电池研究中, 发现孔隙中CH3NH3PbI3填充效果是影响器件性能的重要因素[23,24]. 为此, 研究了厚度为150 nm正方形Ag 背电极(面积 100 μm × 100 μm)中, 1—10 μm孔隙占比对其电阻影响的规律. 图5是无孔隙及10%随机孔隙时背电极仿真图及其电阻(图5(a)), 以及占比变化对其电阻值的影响(图5(b)).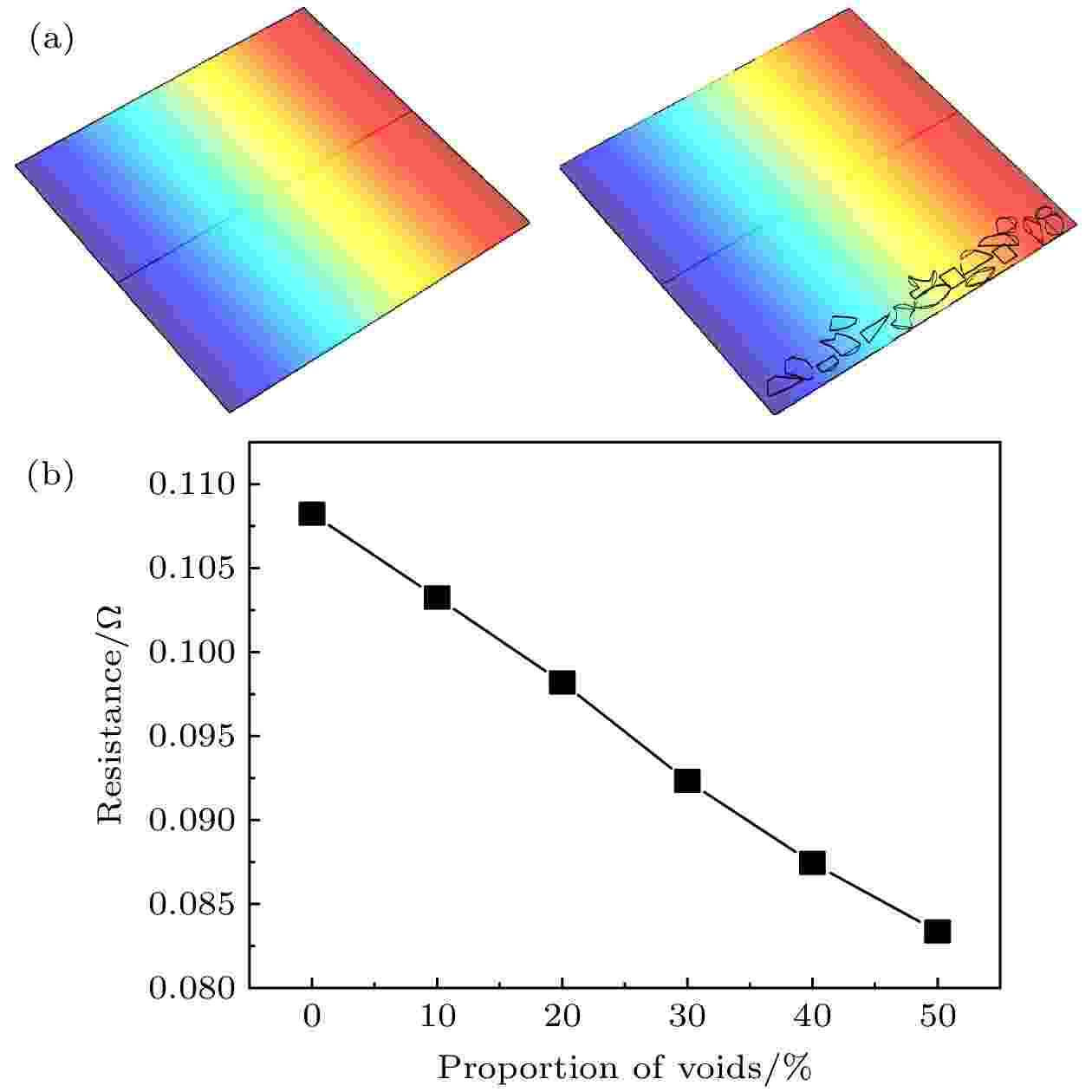
Figure5. Simulation diagram of back electrode without and with 10% random pores and its resistance (a), and the influence of proportion change on its resistance (b).
由图5(a)可知, 添加孔隙后的背电极电阻比无孔隙时要小. 原因是孔隙的加入导致电流通过的横截面积增加. 由图5(b)可知, 随着孔隙占比的增加, 其阻值几乎线性减小, 且每增加10%的孔隙, 其阻值大约减少0.005 Ω左右, 减少比例大约为5%. 因此, 预测每增加10%的孔隙, 提升电池PCE大约5%.
进一步分析上述最优结构的相对性能. 由于多孔孔隙结构背电极中占空比的差别, 导致不能通过阻值大小比较来直接判断结构的优劣. 为此, 需要计算出上述结构补充为矩形时的电阻, 然后通过各个结构阻值与该矩形结构的比值来判断结构的相对性能. 得出边缘间距为1 μm、圆形半径为0.5 μm的蜂窝结构的比值为1.3157, 边缘间距为2 μm、圆形半径为0.5 μm蜂窝结构的比值为1.1141, 50%多孔隙结构的比值为1.5440, 八边形结构的比值为1.5871. 由此可知, 边缘间距为2 μm、圆形间隙半径为0.5 μm的蜂窝结构比值最小, 性能最好.
2
3.3.厚度对背电极影响
研究边缘间距为2 μm圆形半径为0.5 μm的Ag薄膜蜂窝结构背电极. 图6是仿真蜂窝结构(图6(a))及背电极电阻-厚度变化趋势图(图6(b)).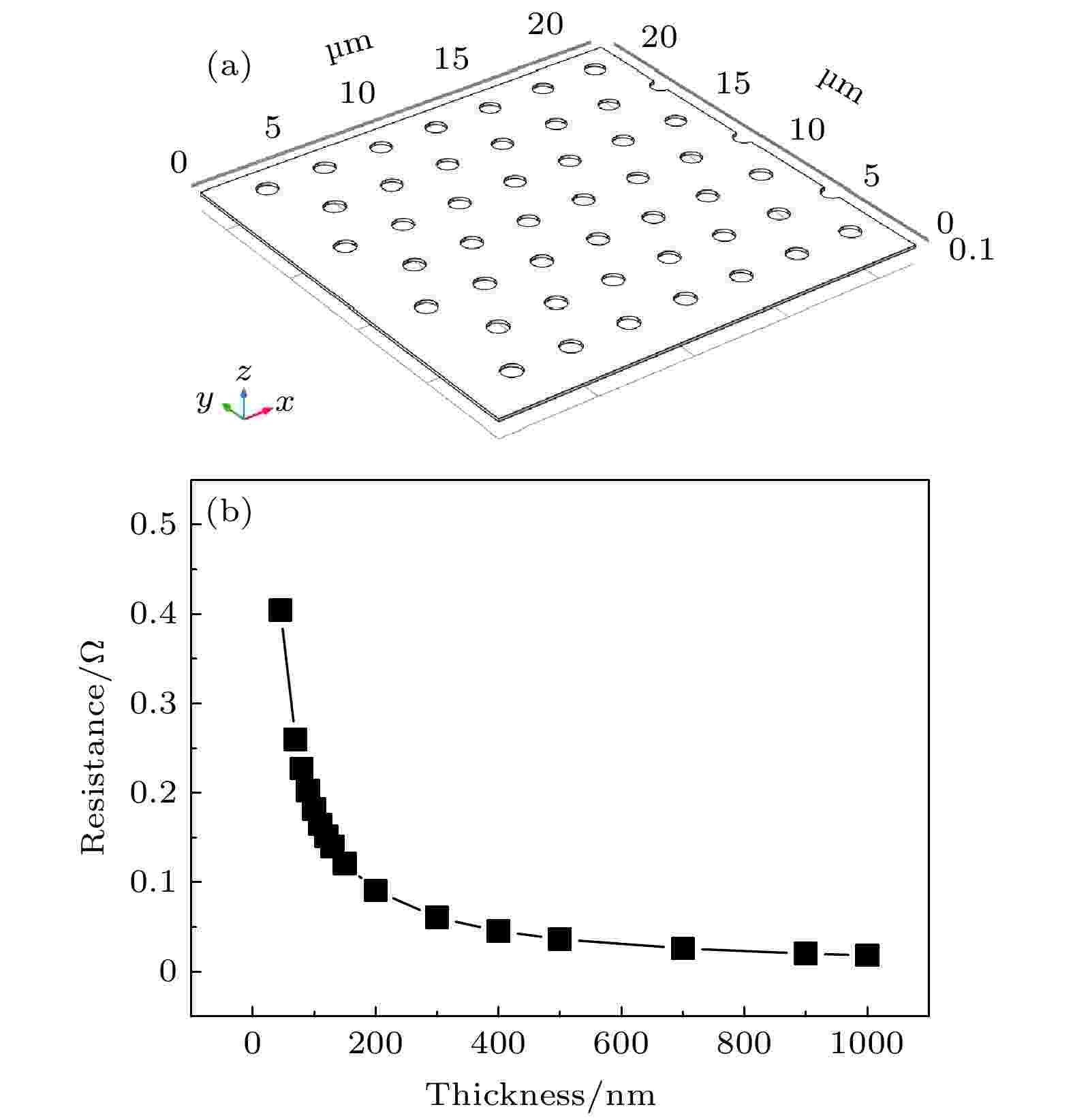
Figure6. Simulated honeycomb structure (a) and back electrode resistance changing with its thickness (b).
由图6可知, 背电极厚度为45 nm时电阻最大, 1000 nm厚度的背电极电阻最小; 且随着背电极厚度的增加, 电极电阻是在逐渐减小的. 在厚度为45—200 nm之间的电阻变化趋势最大, 下降得最为迅速, 而在500—1000 nm之间的电阻变化趋势最小, 下降得不明显.
实际上, 对于钙钛矿太阳能电池来说背电极的电阻越小越好, 因此理论上来说背电极的厚度是越大越好. 但在考虑制作成本及制作效率的条件下, 当背电极厚度达到200 nm以上时, 电阻的变化程度不明显, 性价比低; 而背电极厚度低于100 nm时, 电阻的变化幅度比较大, 很难精确地控制. 因此蜂窝结构的背电极厚度在为100—150 nm时其性能最优, 效果最佳, 此时电极的制备成本等较合适.