全文HTML
--> --> -->此外, 电池的p型发射层作为构成SHJ电池的重要组成部分之一, 必须具有足够的导电性与透光性, 以及满足能带匹配等方面的要求; 更重要的是, p型的沉积不能影响i-a-Si:H的微结构特性, 确保a-Si:H/c-Si界面的钝化效果不会受到影响[13-16]. 2018年, Boccard等[17]在i-a-Si:H和p-nc-Si:H界面处加入CO2等离子体处理, 从而提高p-nc-Si:H的晶化率, 经过该处理的电池得到了21.5%的效率. 同年, 德国于利希研究中心的Richter等[18]探究了不同生长条件下n, p掺杂硅氧材料的折射率与光学带隙等特性, 并且分别使用n型纳米晶硅氧(n-nc-SiOx :H)和p型纳米晶硅氧(p-nc-SiOx :H)作为前后掺杂层, 获得效率为21.4%的SHJ电池. 2020年, 中国科学院上海微系统与信息技术研究所通过三步后掺杂法提高催化化学气相沉积生长的p型掺杂层的掺杂浓度, 观察到氢原子的扩散有利于下方本征层的氢含量增加, 并且提高了p型掺杂层的掺杂浓度, 增加了场效应钝化的效果, 电池效率提升到22.18%[19].
本文首先研究在c-Si与常规钝化层之间引入超薄的i-a-Si:H缓冲层, 用于提高钝化效果, 同时扩展钝化的工艺窗口; 然后提出一种双层结构的发射极, 即在p-nc-Si:H薄膜的上面再沉积一层重掺杂的p型掺杂层, 用于降低掺杂层与透明导电玻璃(ITO)之间的接触电阻, 提高SHJ电池的整体性能.
2.1.双层钝化层的制备
超薄缓冲层的制备. 实验采用n型(100)晶向直拉(Cz)切割硅片为衬底, 电阻率为1.5—7.0 Ω·cm, 厚度为180 μm. 通过等离子体化学气相沉积(plasma enhanced chemical vapor deposition, PECVD)系统制备薄膜, 具体参数为: 氢稀释比(H2∶SiH4)RH = 140∶20, 功率为1 W, 衬底温度为160 ℃, 极板间距为20 mm.常规钝化层的制备. 在缓冲层上沉积常规钝化层, 工艺参数为: 氢稀释比RH = 110∶20, 功率为4 W, 衬底温度为160 ℃, 极板间距为20 mm. 含双层钝化层的SHJ电池结构如图1(a)所示.
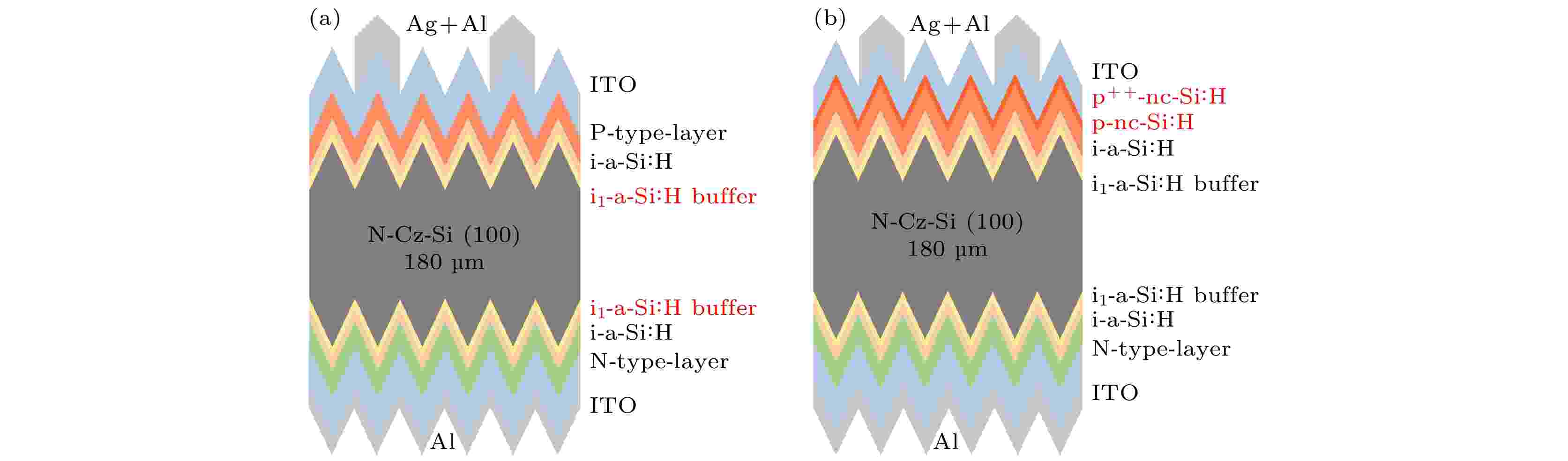
Figure1. (a) Schematic diagram of the SHJ solar cell with the double passivation layer; (b) schematic diagram of the SHJ solar cell with the double emitting layer.
2
2.2.双层p型发射极的制备
前掺杂层的制备. 采用PECVD, 硅烷∶氢气∶三甲基硼(SiH4∶H2∶TMB) = 4∶400∶1.2, 沉积功率为10 W, 极板间距为20 mm, 沉积厚度为13 nm.后掺杂层的制备. 采用PECVD, 硅烷∶氢气∶三甲基硼(SiH4∶H2∶TMB) = 4∶200∶4.8, 沉积功率为10 W, 极板间距为20 mm, 沉积厚度为5 nm. 含双层发射极的SHJ电池结构如图1(b)所示.
2
2.3.性能测试与表征
不同硅薄膜生长厚度由ET200台阶仪获得. 原子力显微镜测试薄膜表面粗糙度. 拉曼光谱仪用来测试所制备硅薄膜的结晶程度. 硅薄膜电导率由共面光暗电导率测试获得. 硅薄膜载流子浓度由霍尔测试获得. 硅薄膜激活能由激活能自动测试系统获得. 样品少数载流子寿命由WCT-120型少数载流子寿命测试仪获得. 硅薄膜材料微结构特性由傅里叶变换红外光谱测试(Fourier transform infra-red, FTIR)获得. SHJ电池外量子效率(external quantum efficiency, EQE)由QEX10型太阳电池量子效率测试系统获得. 所有电池样品由双光源太阳模拟器(WXS-156S-L2, AM1.5GMM)在室温25 ℃、功率密度为100 mW/cm2的条件下进行测试.3.1.双层钝化层对SHJ太阳电池的影响
对单层钝化层改变氢稀释比进行实验, 图2为不同氢稀释比的单层钝化层在inip结构上的少子寿命与隐含开路电压(implied-VOC, iVOC)的变化情况.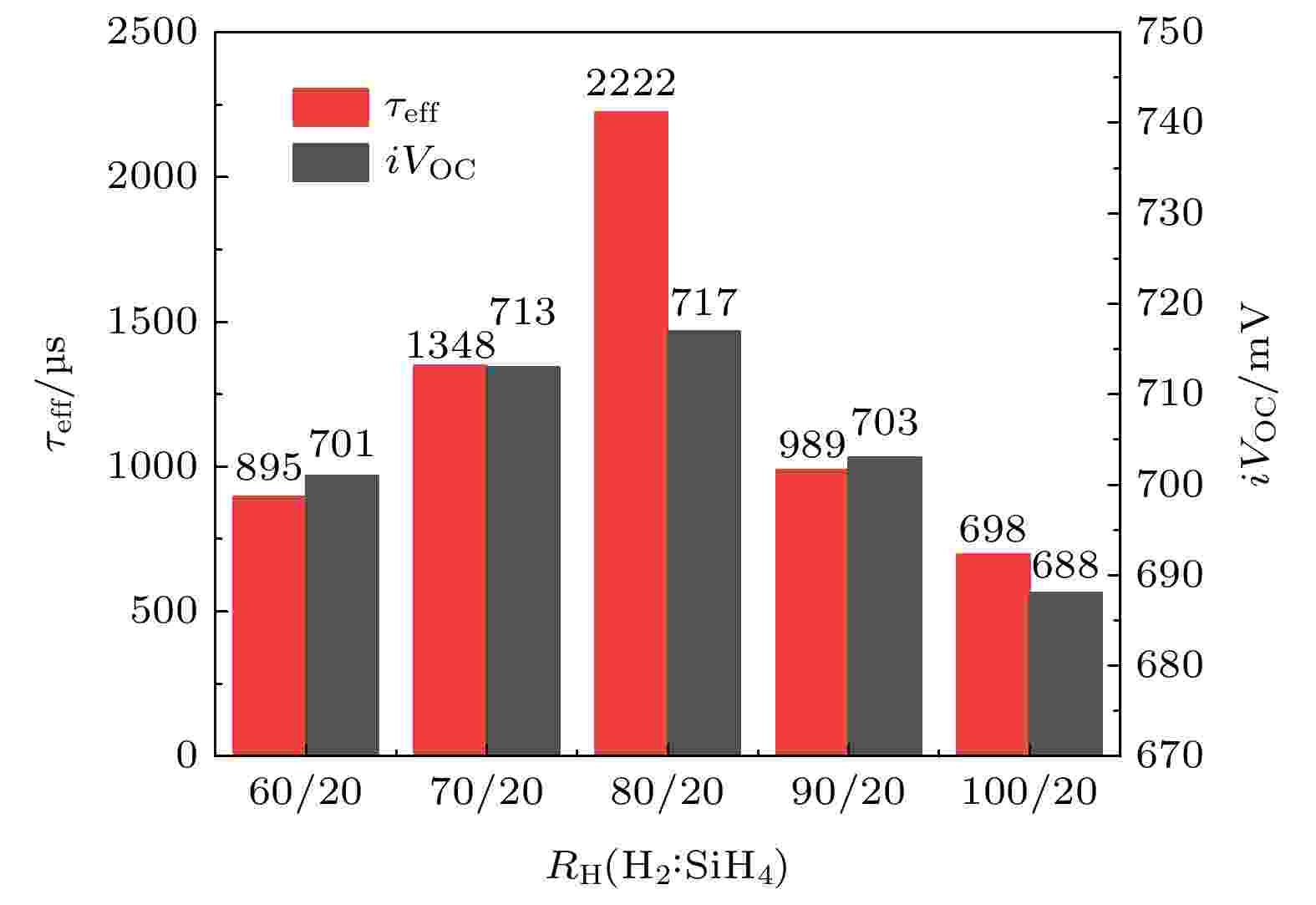
Figure2. Minority carrier lifetime and variation trend of iVOC in single passivation layer with different hydrogen dilution ratio.
由图2可知, 单层钝化层最佳少子寿命为2.2 ms, 但是当氢稀释比高于4时, 少子寿命下降明显, 这是由于钝化层发生外延导致钝化质量恶化, 因为外延硅中的氢含量是非晶硅中的1/100—1/30, 较低的氢含量导致无法获得好的钝化结果, 另外, 外延硅中含有较多的与团簇氢相关的缺陷, 这对电池性能造成不利影响.
由于单层钝化层沉积过程中容易发生外延现象, 导致所能调节的实验窗口过窄, 很大程度上限制了硅异质结太阳电池性能的提高[20,21], 为了有效防止外延, 提高钝化层性能, 拓宽实验窗口, 在钝化层与c-Si之间插入一层超薄的缓冲层, 研究了双层钝化层对钝化效果的影响.
3
3.1.1.缓冲层对钝化效果的影响
将低功率高氢稀释比(1 W, RH = 140∶20)的缓冲层与常规钝化层做了FTIR图谱测试, 并对图谱进行了分峰处理, 如图3所示.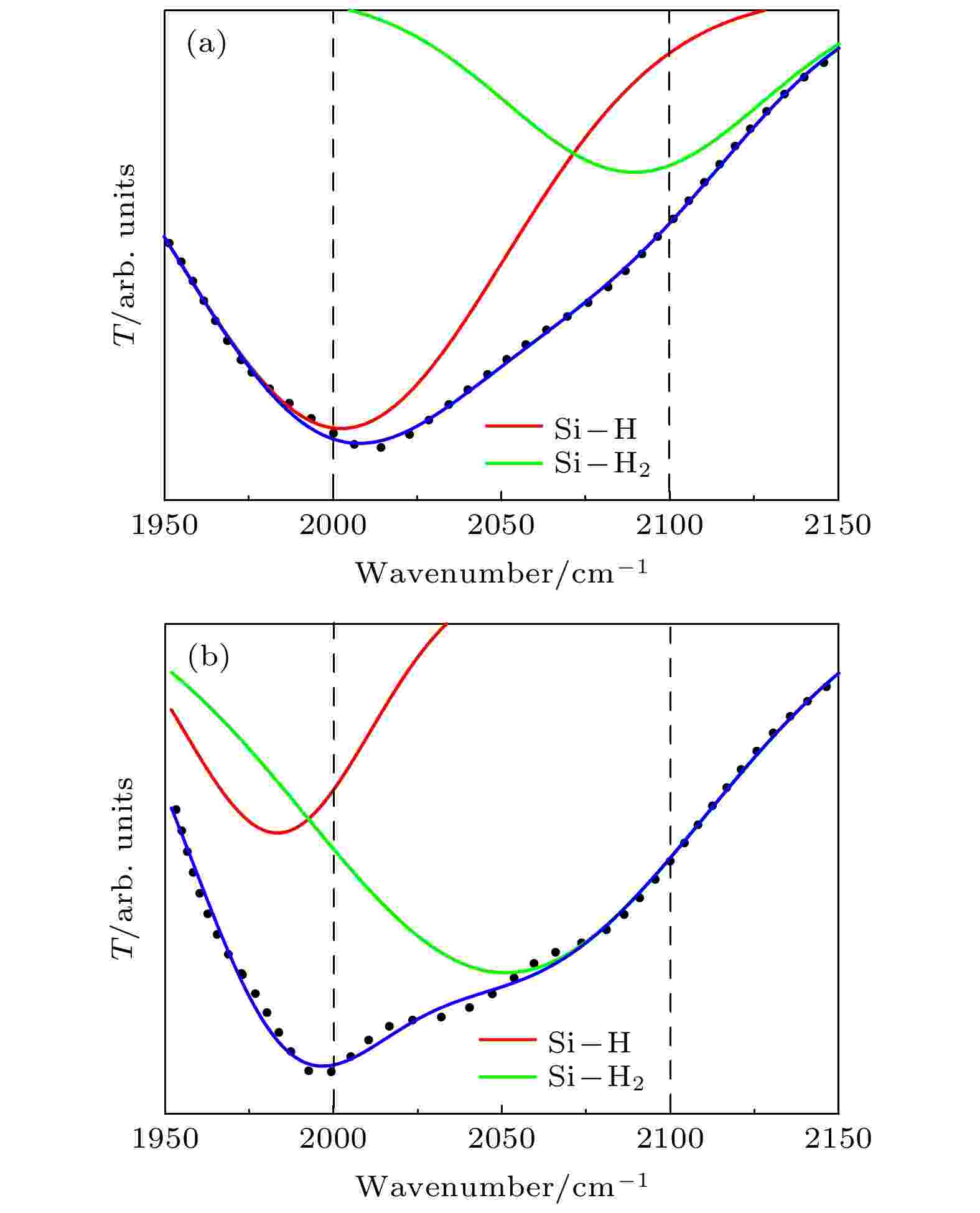
Figure3. FTIR spectra of (a) conventional passivation layers and (b) buffer passivation layers.
从图3可以看出, 低功率高氢稀释比的缓冲层中, 二氢化物(Si—H2)键的占比明显比常规钝化层多. 一般来说, 具有较低微观结构因子(R)的高质量i-a-Si:H材料有利于SHJ太阳电池的性能, 然而, 在PECVD过程中, a-Si:H/c-Si界面的外延生长不利于表面钝化[9,22]. 尽管存在缺陷, 但是富氢的缓冲层仍有希望通过形成突变的a-Si:H/c-Si界面来改善钝化, 其原因为在 PECVD工艺中, 在低沉积速率条件下, 可以更有效地饱和硅悬挂键, 并尽可能减缓界面外延生长. 同时由于缓冲层具有很高的氢稀释比, 而且结构疏松, 所以Si—H2键占据了主导地位. 尽管这与以往对钝化层最佳效果的认知有很大不同, 但是因为缓冲层的超薄特性, 以及在后续钝化层的沉积过程中, Si—H2键断裂, 从而释放出更多的氢来饱和界面的悬挂键, 从而达到了提高少数载流子寿命、增强钝化效果的目的.
低功率高氢稀释比的缓冲层中Si—H2键过多, 当缓冲层厚度增加时, 过多的缺陷会使得钝化效果无法得到优化, 因此缓冲层的厚度至关重要, 图4给出了不同厚度缓冲层对少子寿命和iVOC的影响. 可以看出, 缓冲层厚度在0.4—1 nm之间时, 少子寿命稳定在3 ms左右, 说明缓冲层对钝化性能起到改善作用, 当缓冲层厚度超过1 nm后, 少子寿命与iVOC有很大的下降, 这表明疏松的缓冲层已经影响到整体钝化层的性能, 而因为低功率缓冲层的存在, 后续沉积的钝化层的外延性大大降低, 钝化层优化的条件相较之前有了扩宽.
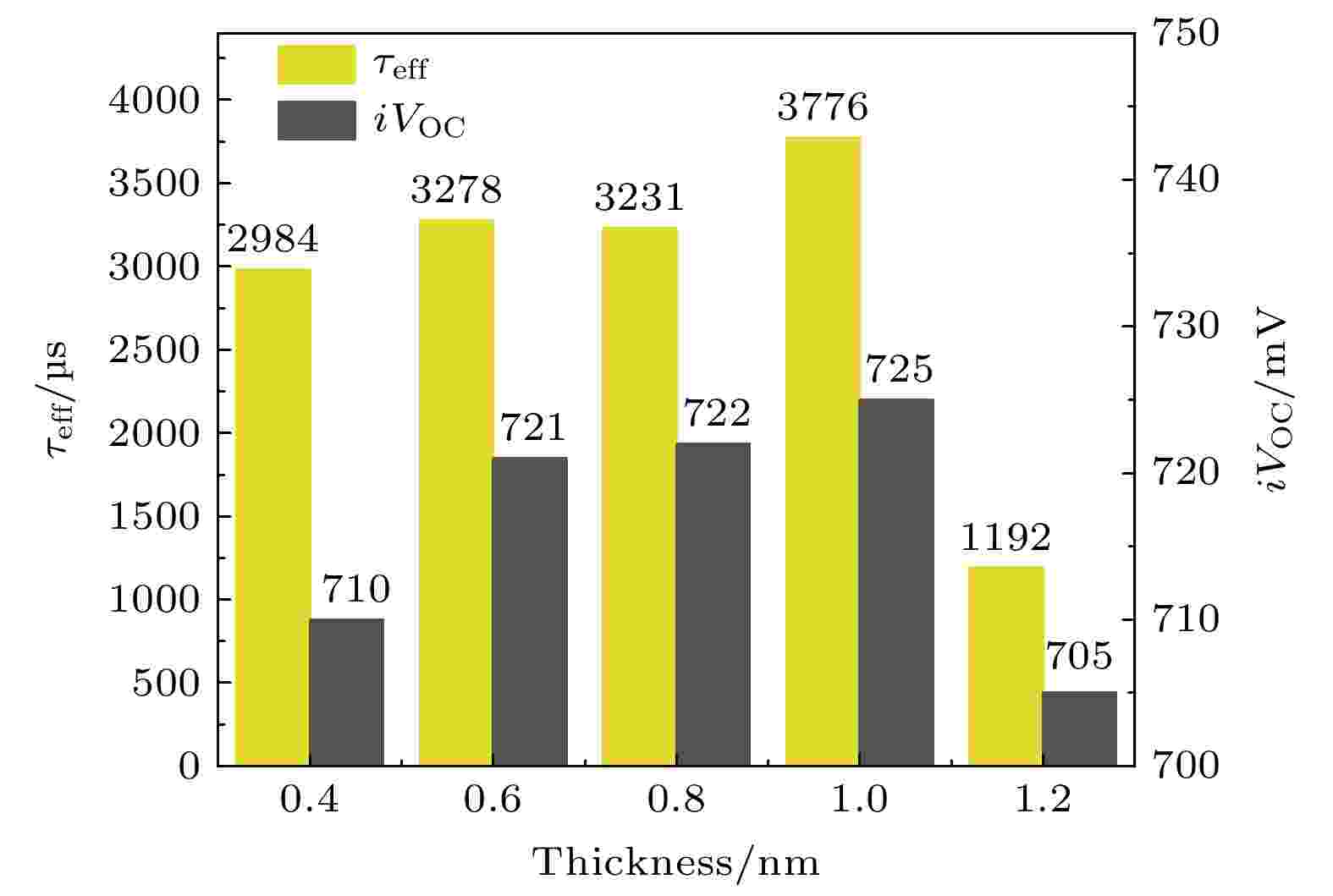
Figure4. Minority carrier lifetime and iVOC of samples with different thicknesses of buffer layer.
3
3.1.2.常规钝化层对钝化效果的影响
为了获得更好的钝化性能, 在缓冲层厚度为1 nm的基础上对常规钝化层氢稀释比进行了进一步优化, 氢稀释比从RH = 80∶20增加到RH = 120∶20, 整体钝化层厚度保持一致, 为5 nm[23]. 图5为增加常规钝化层氢稀释比对少子寿命与iVOC的影响. 可以看出, 氢稀释比在RH = 80∶20—110∶20范围内均有良好的钝化效果, 因为低功率缓冲层的加入为i-a-Si:H提供了保护层, 同时由于缓冲层是低功率的, 可以有效地饱和悬挂键, 所以与c-Si接触的地方很难形成外延, 并且低功率的缓冲层对c-Si衬底的轰击更小, 对于常规钝化层来说, 双层钝化层能够拓宽钝化工艺的窗口.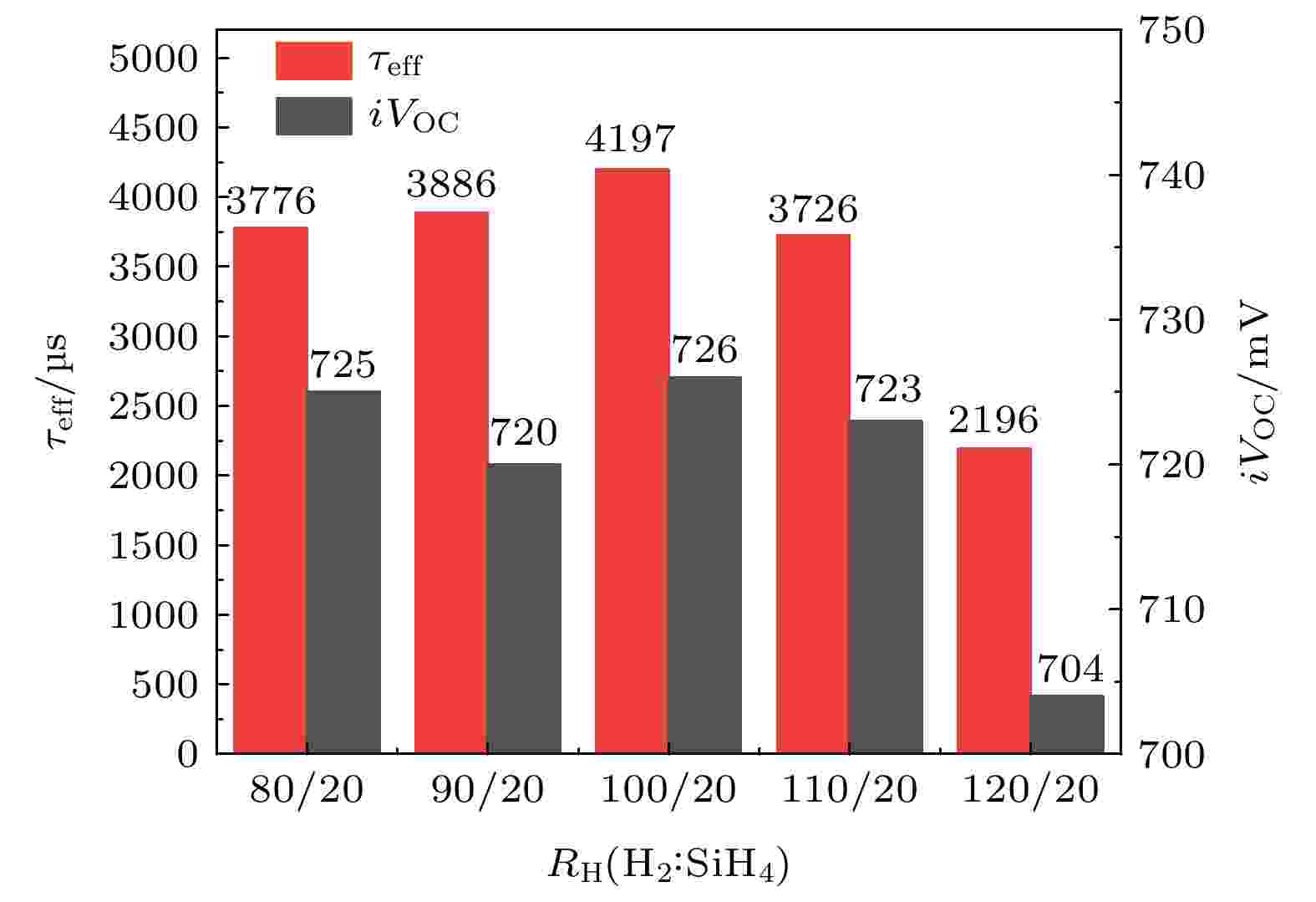
Figure5. Minority carrier lifetimes and iVOC of samples of double passivation layer for different hydrogen dilution ratio.
为了验证双层钝化层的可重复性, 同时与常规钝化层进行对比, 采用常规单层钝化层与双层钝化层在inip结构上各做了10组实验进行统计学分析. 图6为两种不同钝化层的少子寿命的箱线图, 可以明显地看出, 采用单钝化层时的样品钝化寿命多数不超过2.5 ms, 而采用双钝化层的样品钝化寿命多数超过3.5 ms, 这说明低功率缓冲层可以很好地抑制外延的发生, 而且该低功率缓冲层对钝化层实验的可重复性也起到重要的作用. 当常规钝化层的氢稀释比RH = 110∶20时, 钝化效果最好, 并且具有很好的可重复性.
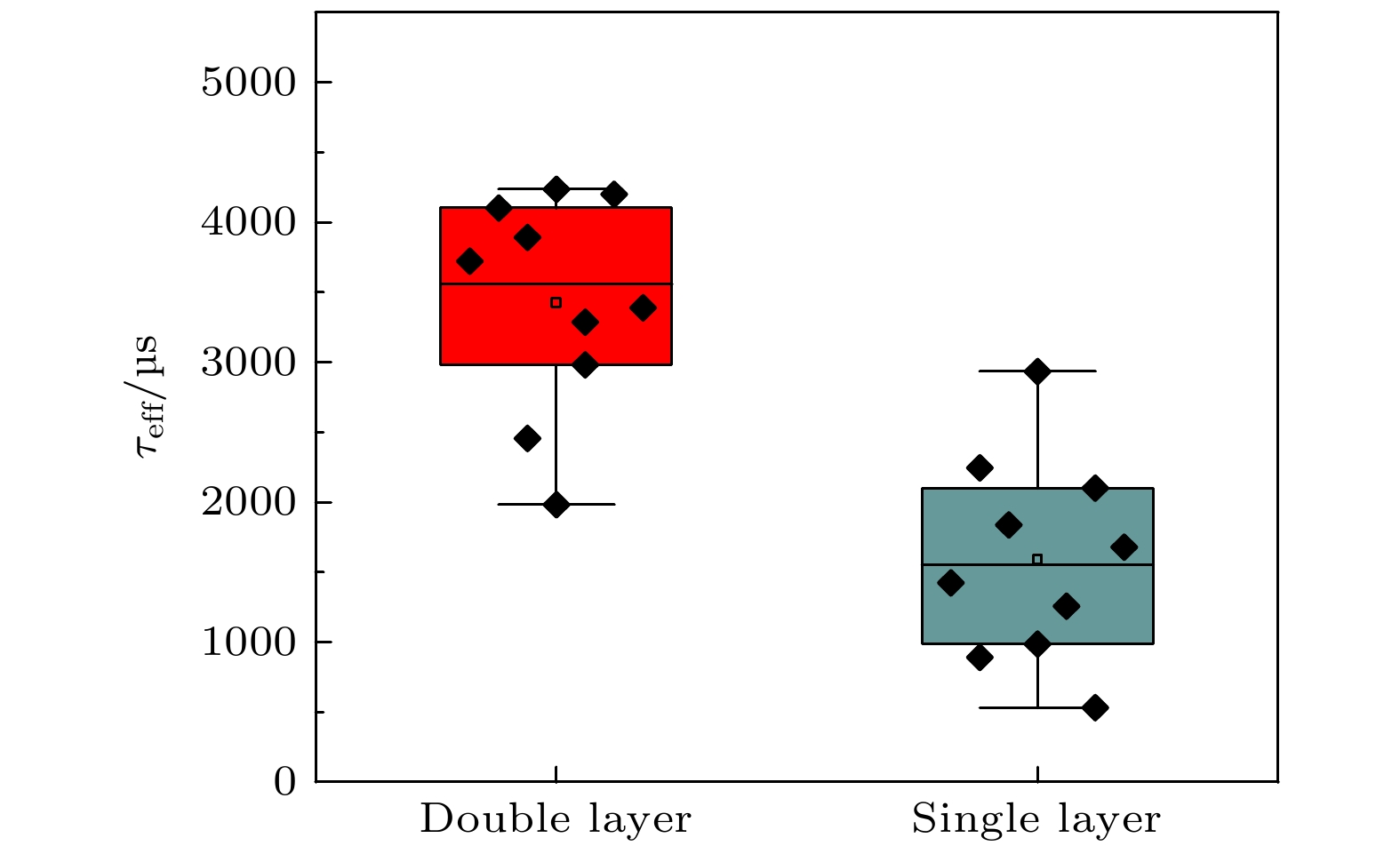
Figure6. Minority carrier lifetimes of samples with double passivation layers or single passivation layers.
2
3.2.双层发射层对SHJ太阳电池的影响
33.2.1.前掺杂层对SHJ太阳电池的影响
发射极过高的掺杂会带来更多的缺陷, 使悬挂键数量与自由载流子浓度增加[24-26], 因此我们采用轻掺杂的p-nc-Si:H作为发射极的前掺杂层. 首先为了获得更接近实际SHJ电池中发射极的电学性能, 在玻璃上沉积厚度5 nm的 i-a-Si:H, 再沉积15 nm的p型掺杂层, 然后进行相应的电学测试. 图7所示为p型掺杂层载流子浓度、电导率与激活能随掺杂量的变化.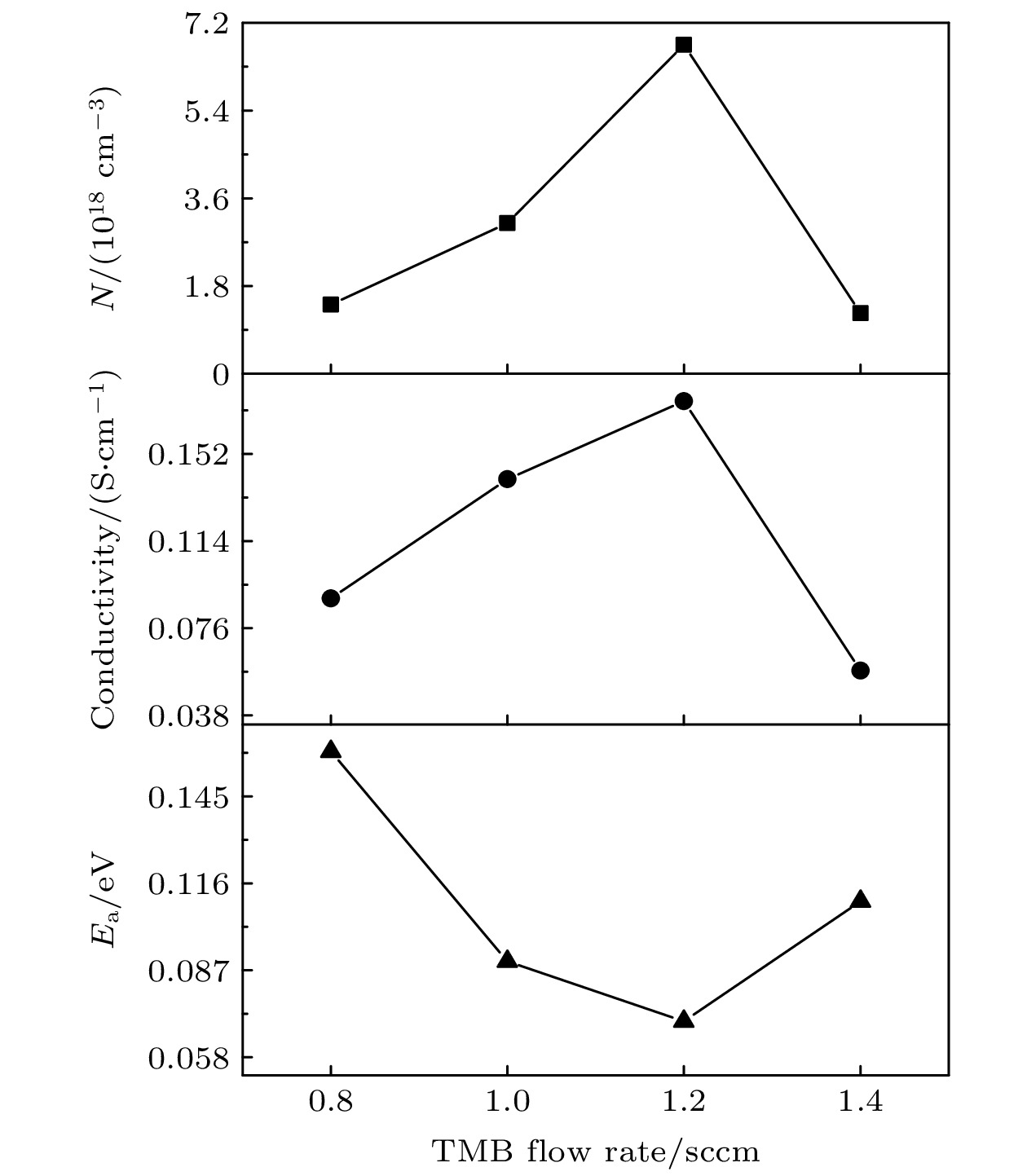
Figure7. Carrier density, conductivity and activation energy of p-type layers with different TMB flow rate.
从图7可以看出, 当TMB的流量从0.8 sccm (1 sccm = 1 mL/min)增至1.2 sccm时, 电导率从0.089 S/cm上升至0.175 S/cm, 激活能从0.16 eV 下降至0.07 eV, 载流子浓度从1.42 × 1018 cm–3上升至6.75 × 1018 cm–3, 而当TMB流量继续增加时, 电导率出现明显下降, 激活能上升至0.11 eV, 载流子浓度下降至1.24 × 1018 cm–3. 为进一步验证, 对不同掺杂量的p型掺杂层进行了拉曼测试, 如图8所示.
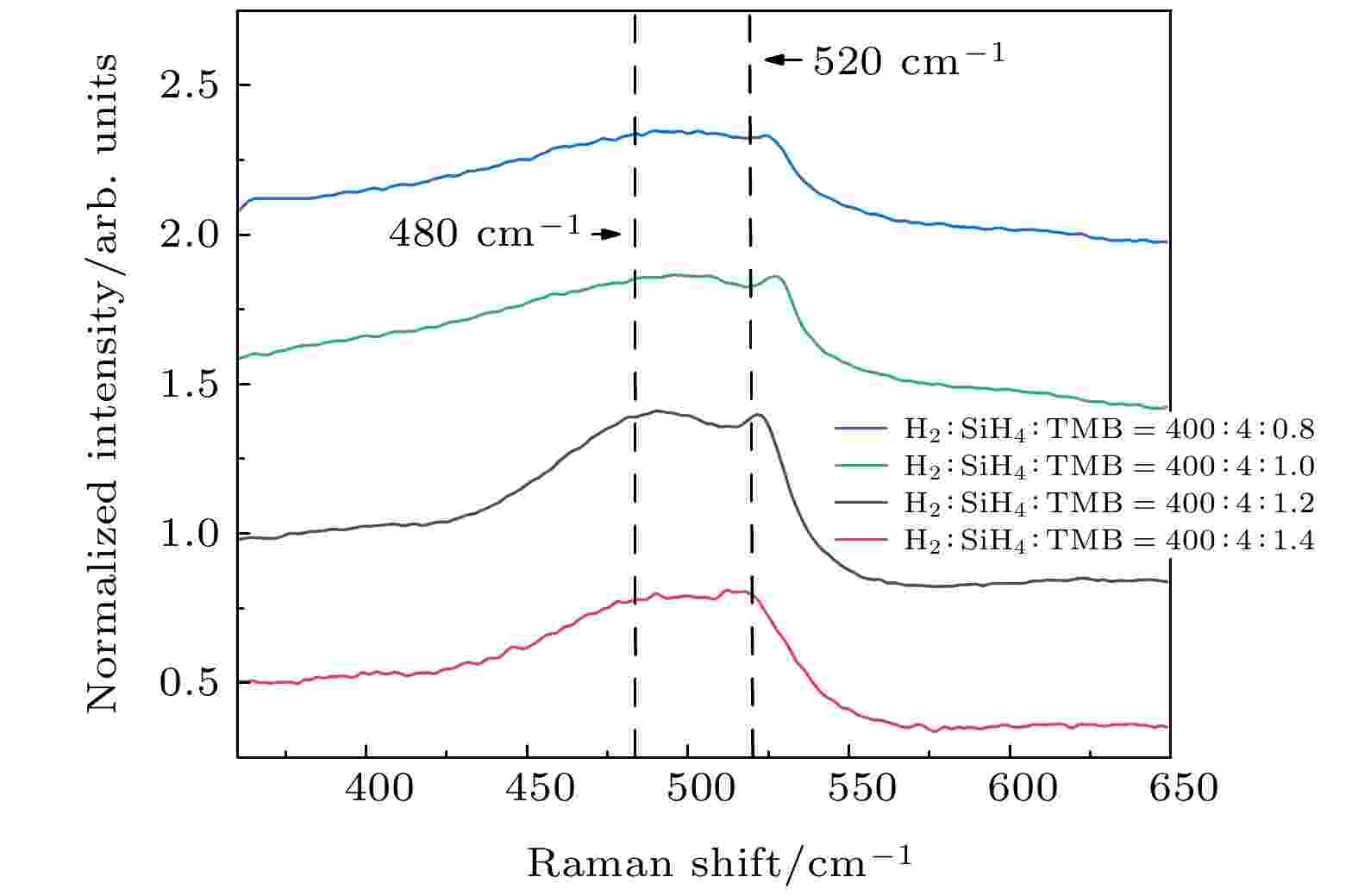
Figure8. Raman spectra of p-type layers with different TMB flow rate.
从图8可以看出, TMB掺杂流量在1.2 sccm之前, 结晶率基本持平, 而当超过1.2 sccm时, 薄膜结晶度下降明显, 原因是掺杂量的增加使得缺陷增加, 同时硼抑制晶化作用进一步加强, 结晶度下降从而导致电导率、载流子浓度下降以及激活能上升[27].
将上述不同掺杂量的p型掺杂层作为SHJ电池的发射极, 并对相应电池的各个参数进行比较, 结果如图9所示. 从图9可以看出, 当p型掺杂层的掺杂流量从0.8 sccm提升至1.2 sccm时, 开路电压(VOC)从705 mV提升至710 mV, 说明掺杂量的提高使得掺杂层与衬底之间的能带弯曲增加, 而填充因子(FF )从62.07%提升至64.35%, 这归因于掺杂量的提高减小了接触电阻[28,29]. 而当掺杂流量继续上升时, 电池性能出现下降, 尤其是VOC, 这是因为过高的掺杂流量使得p型掺杂层出现过多的缺陷, 掺杂效率降低, 导致电导率下降, 发射极无法在c-Si表面产生足够的能带弯曲, 同时过高的掺杂会增加悬挂键密度, 从而降低了钝化效果[16,30]. 得到的最佳条件为H2∶SiH4∶TMB = 400∶4∶1.2, 此时电池效率达到最高.
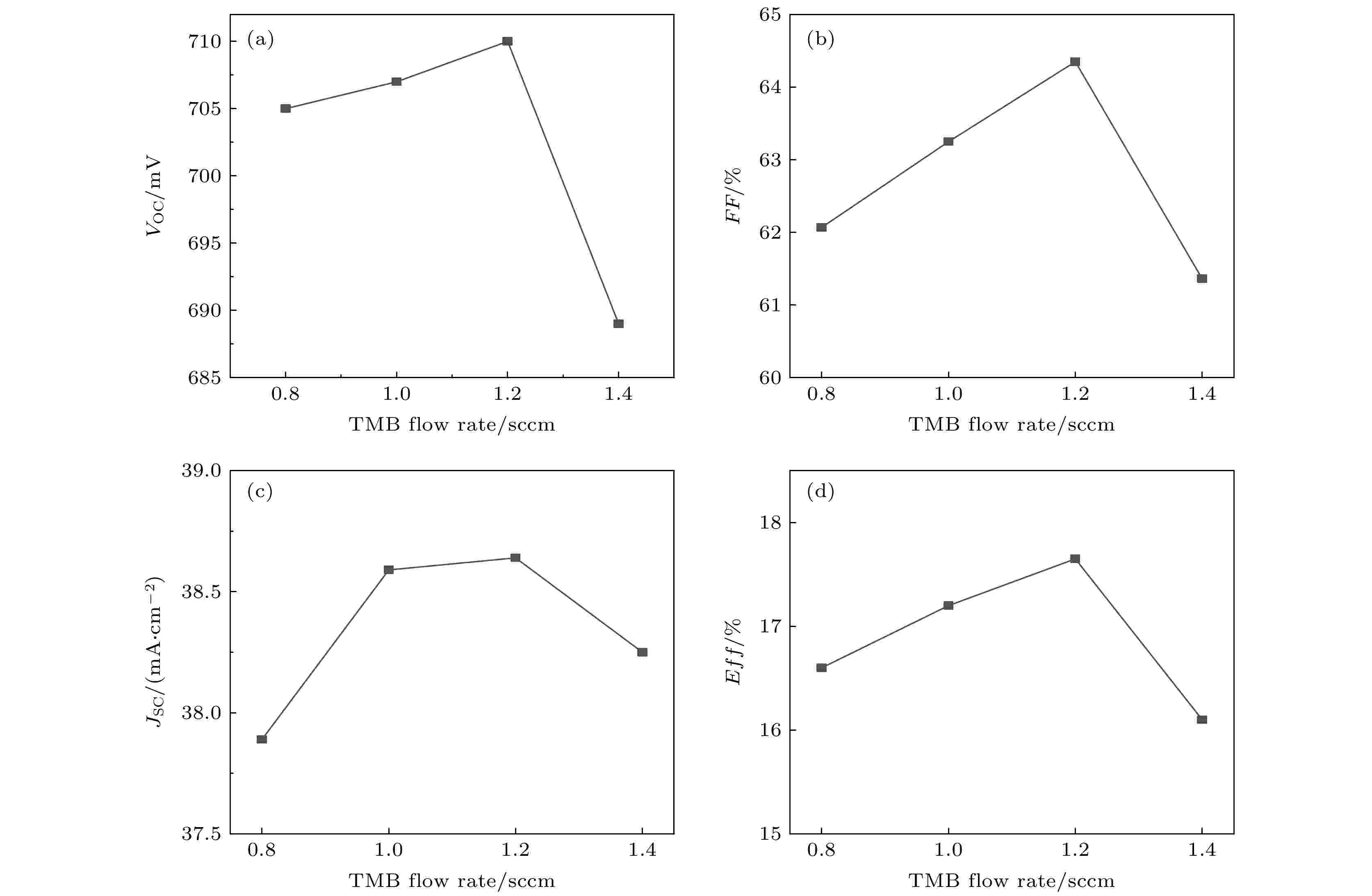
Figure9. J -V parameters of SHJ solar cells with different TMB flow rates in p-type layers: (a) VOC; (b) FF; (c) Jsc; (d) Eff.
3
3.2.2.后掺杂层对SHJ太阳电池的影响
通过前面对前掺杂层的优化, 获得了初始效率(Eff )达到17.65%的SHJ太阳电池, 为了进一步获得更大的内建电势以实现有效的电子-空穴分离, 且与ITO有良好的接触, 使得FF与电池效率得到提升[13], 在前述前掺杂层的基础上, 提出如图1(b)所示的双层发射极, 也就是在p/ITO之间加入一层重掺杂的p型掺杂层(p++-nc-Si:H).为了保证p++-nc-Si:H的掺杂效率, 从氢稀释比与掺杂量两方面来进行优化. 重掺杂层采用不同氢稀释比时相应的器件性能参数见表1. 在最优氢稀释比下不同掺杂量相应的器件性能参数如表2所列. 由表1可知, 氢稀释比的增加使得电池的效率先增后减, 其中VOC基本没有变化, JSC略有上升, 而FF提升明显, 说明氢稀释比的增加使得掺杂效率上升, 重掺杂改善了ITO与p型掺杂层的接触, 载流子传输特性增强, 因此FF显著增加, 但是过高的氢稀释比使得重掺杂层生长速度减慢, 大量的氢气流量会对前掺杂层造成刻蚀, 这是当氢稀释比RH > 60以后, FF下降的原因. 表2是在最佳氢稀释比的基础上增加掺杂量, 可以看出, TMB流量增加至4.8 sccm时, FF与JSC都有小幅度提升, 这是因为掺杂量的增加使得能带进一步弯曲, 增加了少数载流子的隧穿, 同时增大了内建电场, 降低了p/ITO之间的接触电阻, 而当流量增加至5.6 sccm以上时, FF从71.86%下降至63.20%, 说明过高的掺杂使掺杂效率降低, 过多的缺陷使得接触电阻增加, 从而导致FF的大幅度下降[31,32].
H2∶SiH4∶TMB | JSC/mA·cm–2 | VOC/V | FF/% | Eff /% |
120∶4∶4 | 38.7 | 0.709 | 66.57 | 18.26 |
160∶4∶4 | 38.91 | 0.710 | 69.08 | 19.08 |
200∶4∶4 | 39.15 | 0.709 | 70.84 | 19.66 |
240∶4∶4 | 38.4 | 0.708 | 65.56 | 17.8 |
表1重掺杂层不同氢稀释比的电池具体参数
Table1.J -V parameters of SHJ solar cells with different hydrogen dilution ratio in the p++-nc-Si:H layer.
H2∶SiH4∶TMB | JSC/mA·cm–2 | VOC/V | FF/% | Eff/% |
200∶4∶4 | 39.15 | 0.709 | 70.84 | 19.66 |
200∶4∶4.8 | 39.37 | 0.708 | 71.86 | 20.03 |
200∶4∶5.6 | 38.79 | 0.709 | 69.71 | 19.17 |
200∶4∶6.4 | 38.7 | 0.710 | 63.20 | 17.3 |
表2重掺杂层不同掺杂量的电池具体参数
Table2.J -V parameters of SHJ solar cells with different TMB flow rate in the p++-nc-Si:H layer.
为了研究双层p型发射极有效提升电池性能的原因, 制备出p-nc-Si:H和 p-nc-Si:H/p++-nc-Si:H (重掺杂)两种发射极材料作为对比, 两种材料的厚度均控制为15 nm, 测试了两种不同材料的电导率以及载流子浓度, 测得单层发射极的电导率为0.175 S/cm, 载流子浓度为6.75 × 1018 /cm3, 略低于双层发射极的电导率0.402 S/cm, 载流子浓度2.91 × 1019 /cm3, 说明重掺杂层对材料的电学性能起到了有益的效果, 同时因为沉积p++-nc-Si:H的氢稀释比较低, 为确保整体材料的结晶度, 对两种材料的结晶度进行了Raman图谱的测试, 结果如图10所示. 可以看出, 双层p型发射极的结晶度要略高于单层p型发射极的结晶度, 说明在p-nc-Si:H上沉积的p++-nc-Si:H虽然氢稀释比较低, 但是由于生长在p-nc-Si:H上, 使得薄膜更易结晶.
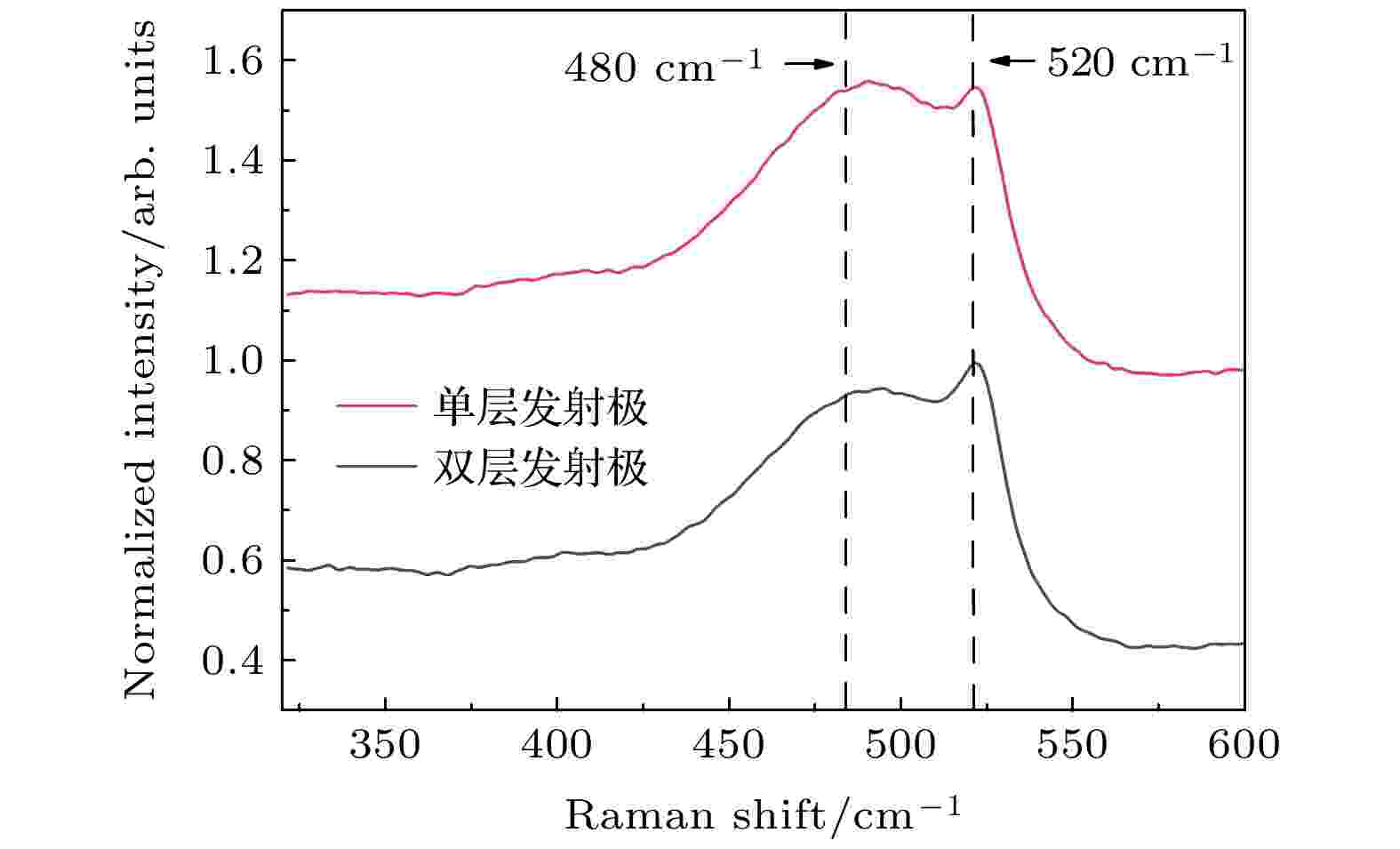
Figure10. Raman spectra of single-layer emitter and double-layer emitter.
将这两种不同的发射极应用在SHJ电池, 结果见图11. 可以看出, 双层p型发射极的JSC和FF都要高于单层p型发射极, 填充因子从64.35%提升至71.86%, 原因在于双层的p型发射极改善了与ITO的接触, 增强了内建电场对载流子的迁移能力, 并且重掺杂的p型掺杂层具有较高的掺杂浓度和较高的费米能级, 改善了ITO/p的接触特性. 同时EQE小幅度上升, 且在短波段最为明显, 因为光伏器件对短波的吸收主要集中在窗口层, 而对长波的吸收则集中在硅片上, 当表面窗口层的掺杂浓度为梯度掺杂时, 通过表面的短波光越多, 短波光被c-Si硅片层吸收, 导致光子被转换成更多的载流子[33]. 光吸收的增强提高了载流子的利用效率, 从而有利于提高电池的电流密度.
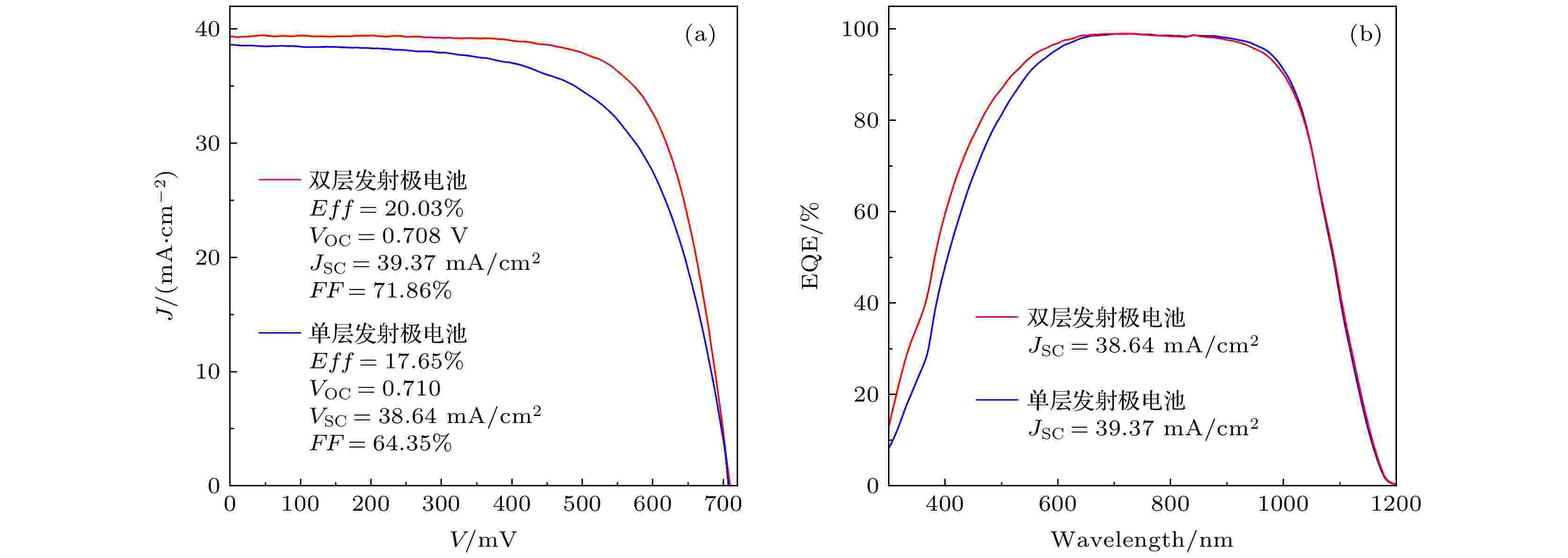
Figure11. (a) J -V curves and (b) EQE curves of SHJ solar cells with different p-type emitters.
采用本文提出的双层钝化层来提高钝化性能, 双层发射极来提高接触效果, 最终获得了最高效率为20.96%的SHJ太阳电池, 其中VOC为710 mV, JSC为39.88 mA/cm2, FF为74.02%.
为了验证双层发射极优化器件性能的可重复性, 对双层发射极电池与单层发射极电池进行了统计学分析, 图12为10组不同发射极结构的SHJ太阳电池的光伏参数. 可以看出, 双层发射极结构太阳电池JSC平均值在39.25 mA/cm2左右, VOC平均值在708 mV左右, FF平均值在73%左右, 均高于单层结构的SHJ电池.
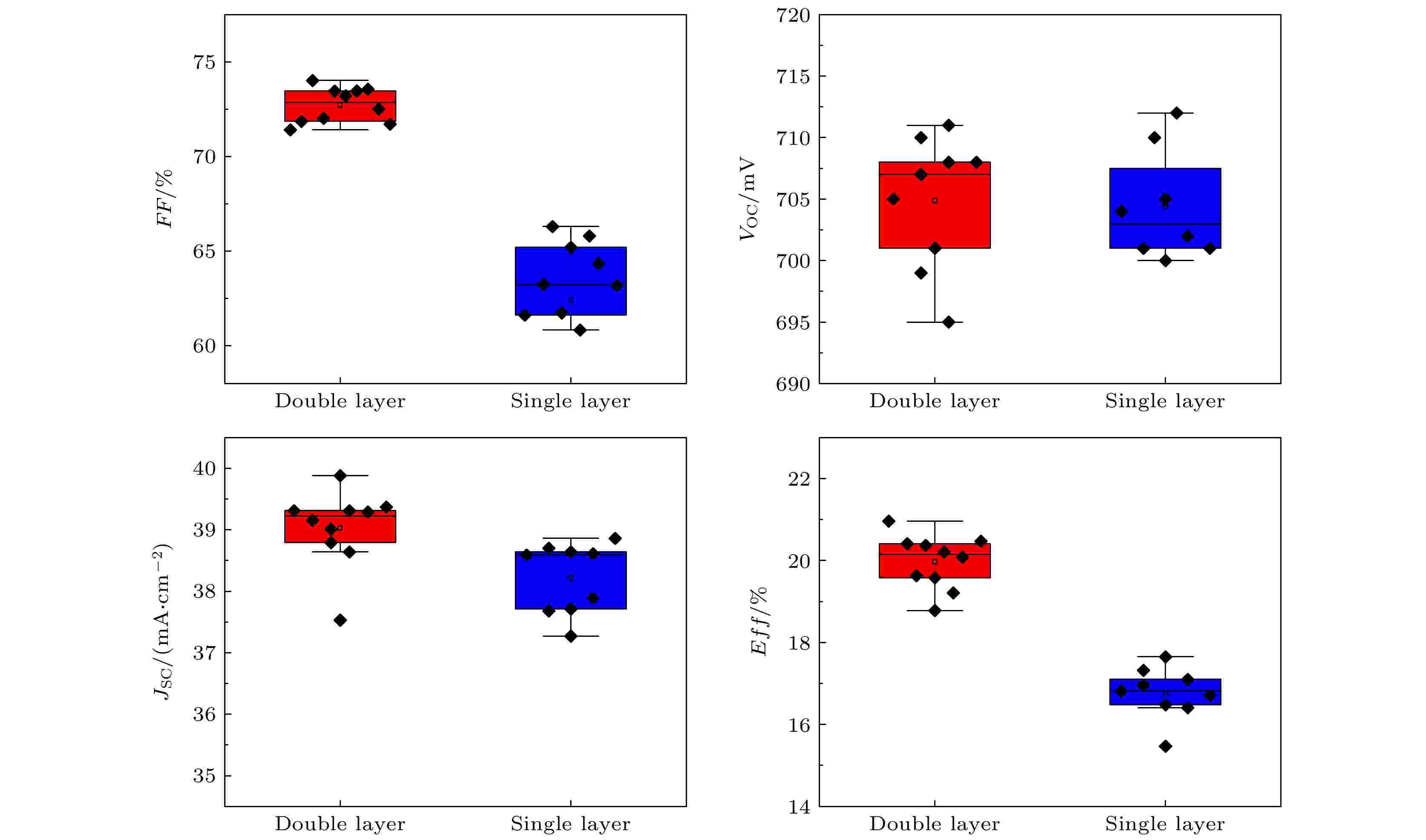
Figure12. Illuminate J -V parameters of SHJ solar cells with double emitter layer and single layer emitter.