全文HTML
--> --> -->由于等离子体被看成是一种多成份 (电子、离子和中性粒子) 的流体, 通过求解各种粒子相应的流体力学方程组, 并耦合质量守恒方程、电子能量守恒方程及泊松方程, 得到等离子体的一些宏观和微观特性. 因此近年来, 许多国内外****和专家提出了基于流体模型的静电场和低温等离子体仿真方法, 用于传感器结构和电极间粒子的运动分析. Govardhan等[13]基于COMSOL有限元仿真对金属氧化物半导体气体传感器的结构优化进行了建模, 完成了传感器气体敏感室的结构优化. Wilde和Lai[14]采用COMSOL软件建立了涡流传感器监测系统模型, 优化了涡流传感器的结构参数. Atieh[15]基于流体模型, 针对两电极击穿型电离式碳纳米管气体传感器做了结构优化, 通过减小电极间距和生长直立碳纳米管, 降低了击穿电压. Chivu等[16]基于COMSOL软件, 对两电极击穿型电离式纳米线气体传感器做了结构优化, 主要分析纳米线结构形貌对击穿电压的影响. 以上研究均证明了采用流体模型及COMSOL仿真软件进行传感器结构优化的可行性. 因此, 本文也选用COMSOL Multiphysics多物理场直接耦合分析软件, 对传感器的静电场及极间放电进行仿真建模, 通过分析不同结构下的静电场分布、场域空间放电过程 (离子密度、电子密度等) 及收集电流的大小, 来获得引出电流大、灵敏度高的传感器优化结构, 为确定及制作何种结构的电离式传感器提供了科学依据.
2.1.传感器的工作原理
传感器结构示意图如图1所示 (1#传感器), 传感器由3个电极构成, 分别为碳纳米管阴极、引出极和收集极. 3个电极尺寸相同, 阴极具有两个圆形扩散孔, 引出极中心具有1个圆形引出孔, 收集极中心有1个长方形盲孔. 3个电极之间由绝缘层隔离, 不同厚度的绝缘层可用来调节传感器的极间距, 传感器的阴极-引出极间距d与引出极-收集极间距d相同.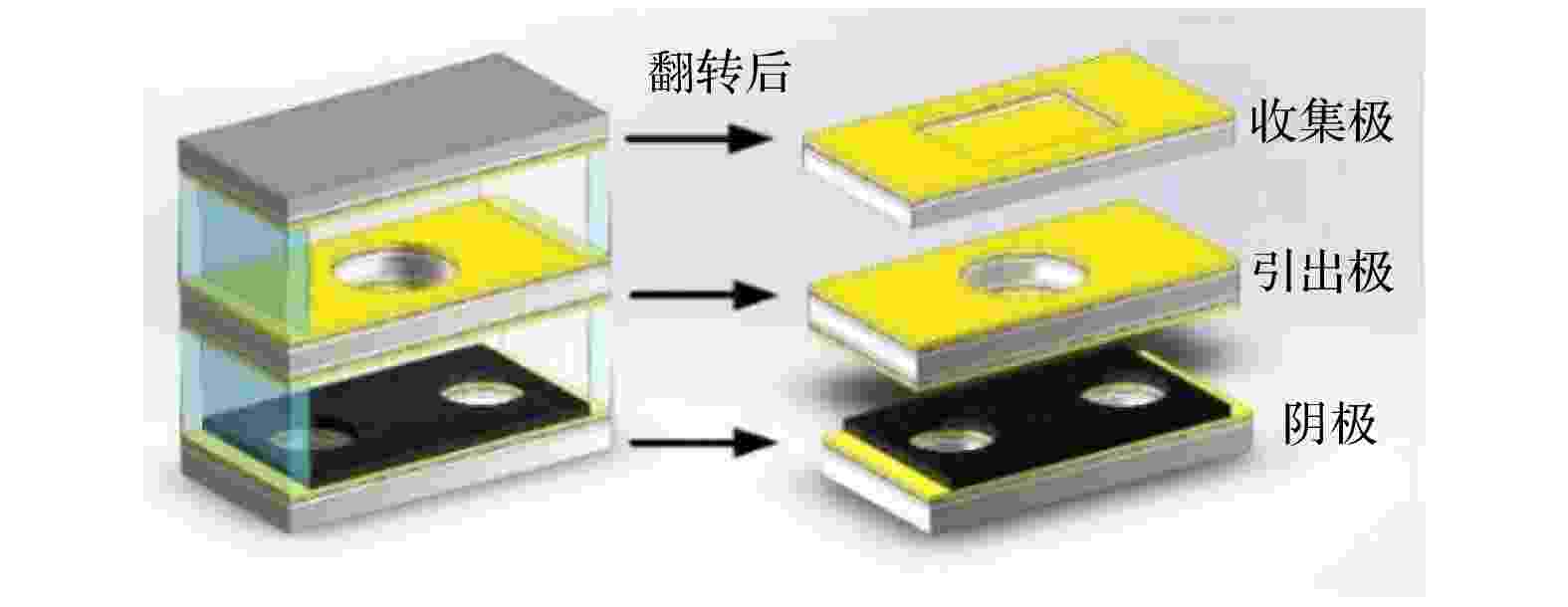
Figure1. Schematic diagram of the carbon nanotube triple electrode sensor.
三电极传感器测量电路如图2所示, 工作时阴极接地、引出极-阴极间加直流电压Ue、阴极-收集极加直流电压Uc, Ue > Uc. 通过电极电压控制方式在传感器的极间产生两个反向电场E1和E2. 由于碳管具有纳米尖端形貌, 因此在碳纳米管尖端附近有较高的电场强度, 气体分子通过碰撞电离产生电子和正离子, 大多数的正离子会向引出极扩散. 通过引出孔后, 在反向电场E2的作用下, 正离子会加速运动到收集极, 作为传感器的输出电流Ic输出.
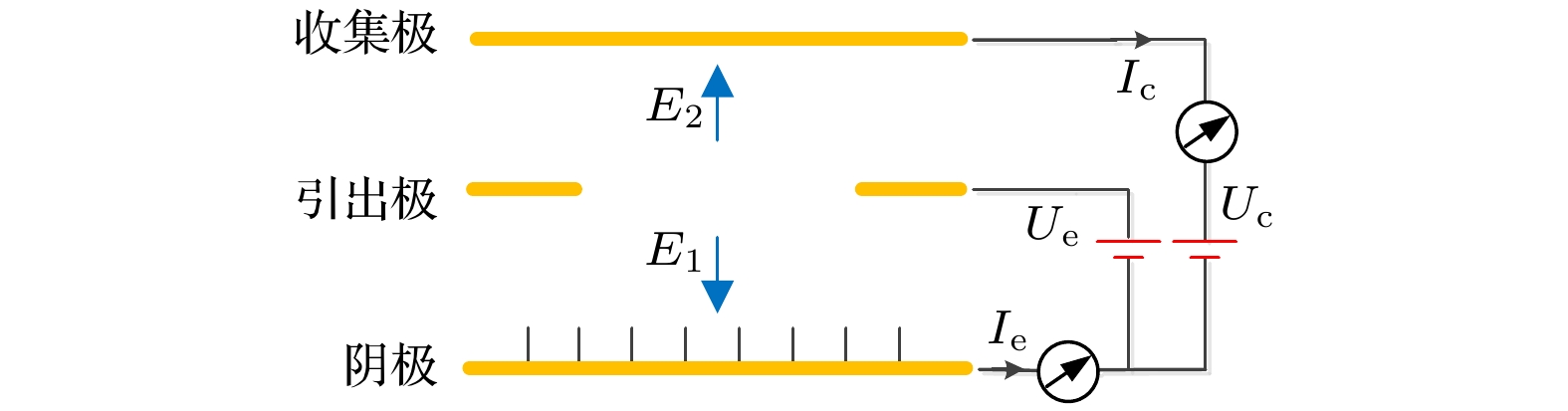
Figure2. Schematic diagram of the measuring circuit.
三电极传感器工作在非自持放电状态, 基于气体放电理论, 气体第一电离系数α和场强E及压力P存在指数关系[17], 即

同时, 收集电流Ic为总放电电流I的一部分[17],

传感器内部电场分布将根据传感器结构的变化而发生改变, 正向电场E1的分布变化会影响电子发射及电子能量的分布, 进而影响到正离子的生成; 反向电场E2的分布变化会影响收集极对正离子的收集, 最终影响收集电流Ic的大小. 因此, 对传感器结构的优化能够提升传感器收集电流的大小, 提高传感器的检测性能.
2
2.2.传感器静电场仿真模型的建立
选择COMSOL软件中的静电模块建立传感器静电场仿真模型. 由于电极结构和电极电压是电场分布的决定因素, 所以建立三电极电离式碳纳米管传感器极间电场的二维仿真模型时, 需要在简化模型时尽可能多包含传感器电极的几何结构特点, 便于求解计算. 沿图3(a)左一图虚线所示截面, 依次截取获得图3(a)右二、右一图所示截面, 用来建立传感器的二维轴对称模型, 并在阴极上均匀设置碳纳米管阵列(图3(b)). 图3的建模参数如表1所列 (该结构为1#传感器).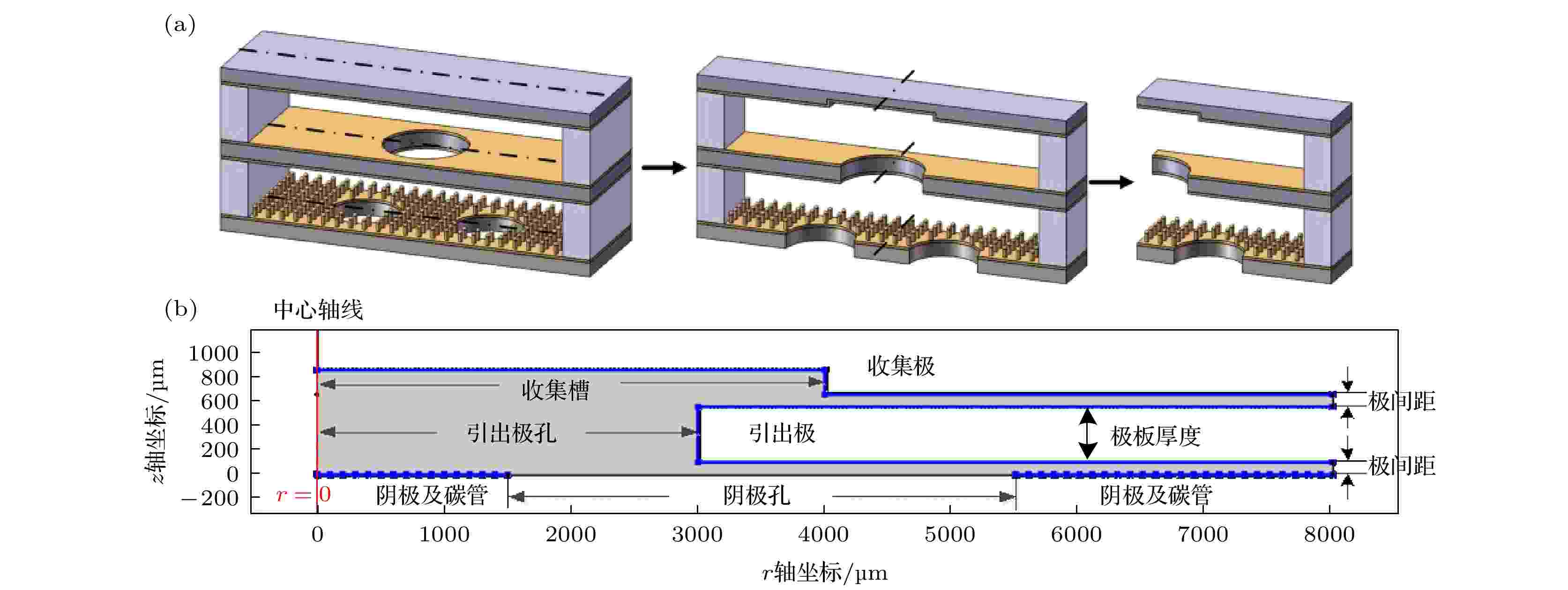
Figure3. Simulation model: (a) Longitudinal section diagram of the two-dimensional model; (b) two-dimensional axisymmetric field simulation model of the electrostatic field.
d/μm | Ue/V | Uc/V | 极板厚度/μm | 收集极槽参数 | 引出极孔半径/mm | 阴极孔半径/mm | 碳纳米管参数 | |
数值 | 100 | 100 | 1 | 450 | 6 mm × 8 mm, 200 μm深 | 3 | 2 | 长: 5 μm, 尖端半径: 10 nm, 间距: 200 nm |
表1仿真建模参数
Table1.Parameters of the simulation model.
1) 仿真模型静电特性的控制方程及边界条件
对于静电场模型, 采用拉普拉斯方程描述空间场域电场分布, 控制方程如下:
模型边界条件如下:
根据传感器电路测量示意图可知: 对于阴极边界, V0 = 0 V; 对于引出极边界, V0 = 100 V; 对于收集极边界, V0 = 1 V. 模型添加的边界条件如图4所示 (图中长度单位是μm).
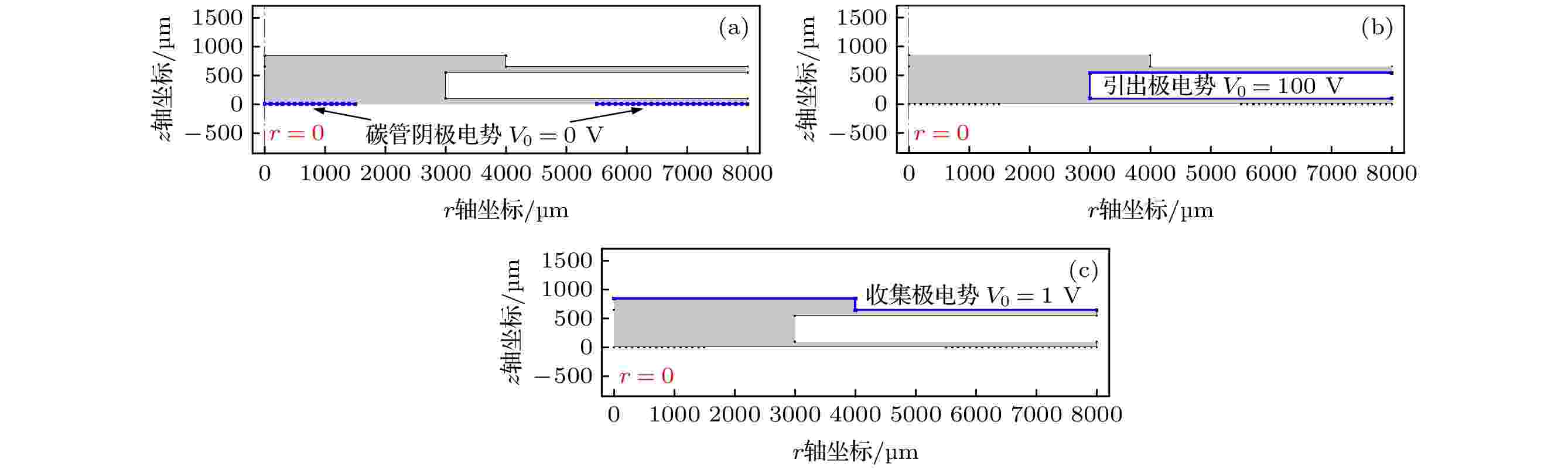
Figure4. Boundary conditions: (a) The cathode; (b) extracting electrode; (c) collecting electrode.
2) 网格剖分
模型采用自由三角剖分, 网格剖分尺寸设置如表2所列.
整体区域 | 阴极碳纳米管边界 | 阴极非碳纳米管边界 | 引出极、收集极边界 | |
最大单元尺寸/μm | 40 | 0.5 | 20 | 30 |
最小单元尺寸/μm | 10 | 0.001 | 20 | 30 |
最大单元生长率 | 1.25 | 1.25 | — | — |
曲率解析度 | 0.25 | 0.2 | — | — |
狭窄区域解析度 | 1 | 1 | — | — |
表2网格剖分尺寸
Table2.Mesh size of the model.
剖分后获得传感器模型的网格剖分如图5所示, 图中长度单位是μm.
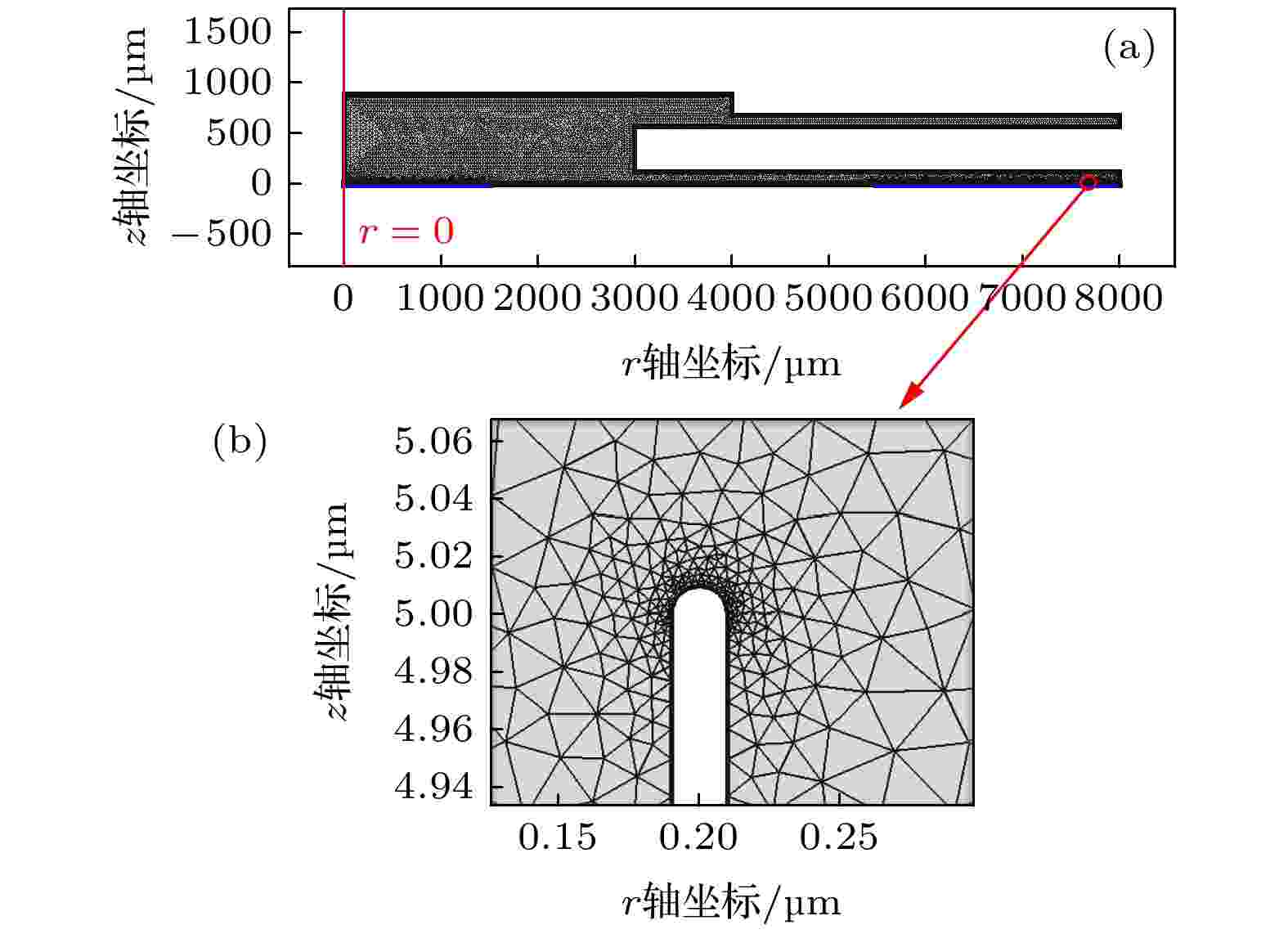
Figure5. Grid mesh of sensor model in the half region of interelectrode: (a) Mesh in the half region of interelectrode; (b) mesh in the local region around carbon nanotube.
3) 求解以及结果处理
选择COMSOL的稳态求解器, 采用有限元方法对静电场模型进行直接迭代计算, 即可获得仿真结果. 通过对仿真结果中正向电场与反向电场分布分析, 为电极结构的优化提供科学依据.
2
2.3.传感器极间放电仿真模型的建立
采用2.2节静电场建模中介绍的二维轴对称模型, 基于以下流程建立传感器极间放电模型.1) 气体基本粒子及其化学反应的添加
碳纳米管电离式传感器的检测背景是氮气, 主要的活性粒子包括电子、正离子(




类型 | 序号 | 反应式 | 反应率系数k/(m3·s–1) | 参考文献 |
电子碰撞 | R1 | e + N2 → e + N2 | f(Te) | [18] |
R2 | e + N2 → e + $ {\rm{N}}_{2}\left({\rm{A}}^{3}\Sigma _{\rm{u}}^{+}\right) $ | f(Te) | [18] | |
R3 | e + N2 → e + $ {\rm{N}}_{2}\left({\rm{a'}}^{1}\Sigma _{\rm{u}}^{-}\right) $ | f(Te) | [18] | |
R4 | e + N2 → 2e +$ {\rm{N}}_{2}^{+} $ | f(Te) | [18] | |
R5 | e +$ {\rm{N}}_{4}^{+} $ → N2 + N2 | 4.73 × 10–11/(Te0.53) | [18] | |
R6 | e + N2 + $ {\rm{N}}_{2}^{+} $ → 2N2 | 3.12 × 10–35/Te1.5 | [18] | |
R7 | e + e +$ {\rm{N}}_{2}^{+} $ → N2 | 1 × 10–31 × (Tg/Te)4.5 | [18] | |
重粒子反应 | R8 | $ {\rm{N}}_{2}\left({\rm{A}}^{3}\Sigma _{\rm{u}}^{+}\right) $ + $ {\rm{N}}_{2}\left({\rm{a'}}^{1}\Sigma _{\rm{u}}^{-}\right) $ → e + N2 +$ {\rm{N}}_{2}^{+} $ | 5.0 × 10–17 | [19] |
R9 | $ {\rm{N}}_{2}\left({\rm{a'}}^{1}\Sigma _{\rm{u}}^{-}\right) $ + $ {\rm{N}}_{2}\left({\rm{a'}}^{1}\Sigma _{\rm{u}}^{-}\right) $ → e + N2 +$ {\rm{N}}_{2}^{+} $ | 2.0 × 10–16 | [19] | |
R10 | $ {\rm{N}}_{2}\left({\rm{A}}^{3}\Sigma _{\rm{u}}^{+}\right) $ + $ {\rm{N}}_{2}\left({\rm{a'}}^{1}\Sigma _{\rm{u}}^{-}\right) $ → e + $ {\rm{N}}_{4}^{+} $ | 5.0 × 10–17 | [20] | |
R11 | $ {\rm{N}}_{2}\left({\rm{a'}}^{1}\Sigma _{\rm{u}}^{-}\right) $ + $ {\rm{N}}_{2}\left({\rm{a'}}^{1}\Sigma _{\rm{u}}^{-}\right) $ → e + $ {\rm{N}}_{4}^{+} $ | 2.0 × 10–16 | [20] | |
R12 | $ {\rm{N}}_{2}\left({\rm{A}}^{3}\Sigma _{\rm{u}}^{+}\right) $ + N2 → N2 + N2 | 3.0 × 10–22 | [19] | |
R13 | $ {\rm{N}}_{2}\left({\rm{a'}}^{1}\Sigma _{\rm{u}}^{-}\right) $+ N2 → N2 + N2 | 2.3 × 10–19 | [21] | |
R14 | $ {\rm{N}}_{2}^{+} $ + N2 + N2 → $ {\rm{N}}_{4}^{+} $ + N2 | 1 × 10–41 × (300/Te) | [18] | |
R15 | $ {\rm{N}}_{4}^{+} $ + N2 → $ {\rm{N}}_{2}^{+} $ + N2 + N2 | 2.1 × 10–16exp(Tg/121) | [18] |
表3气体电离流体仿真模型的区域反应
Table3.Regional reactions of the fluid simulation model on gas ionization.
在传感器电极表面, 各种粒子都会跟电极作用, 发生表面化学反应, 反应生成物有的在电极上消失, 有的回馈到等离子体中, 还需要在模型中添加表面化学反应, 参数如表4所列. 其中γe为二次电子发射系数, εr为二次电子平均能量.
序号 | 表面化学反应 | 碳纳米管 材料边界 | 其他电 极边界 | |||
γe | εr/eV | γe | εr/eV | |||
1 | ${\rm{N} }_{2}\big({\rm{A} }^{3}\Sigma _{\rm{u} }^{+}\big)$ + 电极 → N2 | 0 | 0 | 0 | 0 | |
2 | ${\rm{N} }_{2}\big({\rm{a'} }^{1}\Sigma _{\rm{u} }^{-}\big)$ + 电极 → N2 | 0 | 0 | 0 | 0 | |
3 | $ {\rm{N}}_{2}^{+} $ + 电极 → N2 | 0.2 | 2 | 0 | 0 | |
4 | $ {\rm{N}}_{4}^{+} $+ 电极 → 2N2 | 0.2 | 2 | 0 | 0 |
表4电极表面化学反应
Table4.Chemical reactions on the electrode surface
2) 场域模型的控制方程
流体模型通过求解质量守恒方程、能量守恒方程和泊松方程来求解等离子体内部各种粒子密度[22].
3) 场域模型的边界条件
(1) 粒子质量守恒方程边界条件
电子、离子会在电场和热运动下轰击传感器电极, 被电极完全吸收, 同时正离子轰击电极还可能发生二次电子发射. 对于电子, 边界通量是电场迁移形成的通量、热运动形成的通量和正离子轰击阴极发射二次电子形成的通量之和, 如(5)式; 而对于正离子和负离子的边界条件分别如(6)式和(7)式所示:
对于中性粒子, 电极边界条件主要取决于中性粒子的热运动. 因此, 中性粒子的电极边界条件为
(2) 电子能量守恒方程边界条件
电子能量在边界的通量由热运动电子能量的通量和二次发射电子的能量通量之差构成, 所以电子温度守恒方程的边界条件为
(3) 泊松方程边界条件
阴极一端接地, 引出极一端接100 V电压, 收集极接1 V电压.
4) 传感器放电模型的求解
模型依旧采用自由三角剖分, 剖分参数与2.2节相同. 由于有限体积法具有很好的守恒性, 可以克服泰勒展开离散的缺点, 对网格的适应性也很好, 因此采用有限体积法进行数值求解. 计算时通过逐步调节空间网格和时间步长来实现结果收敛, 当相对误差小于0.001时, 结束本次迭代, 进行下一步迭代计算. 设置的时间步长: 从10–11 s开始, 以100.06 s为步长, 计算到0.1 s结束.
求解过程中, 根据表3和表4中的反应式, 耦合(5)—(9)式, 可以计算获得电子浓度ne、正离子浓度n+等参量, 在结果中查看这些参量并了解其分布情况, 进而可以计算得到电流密度jc:
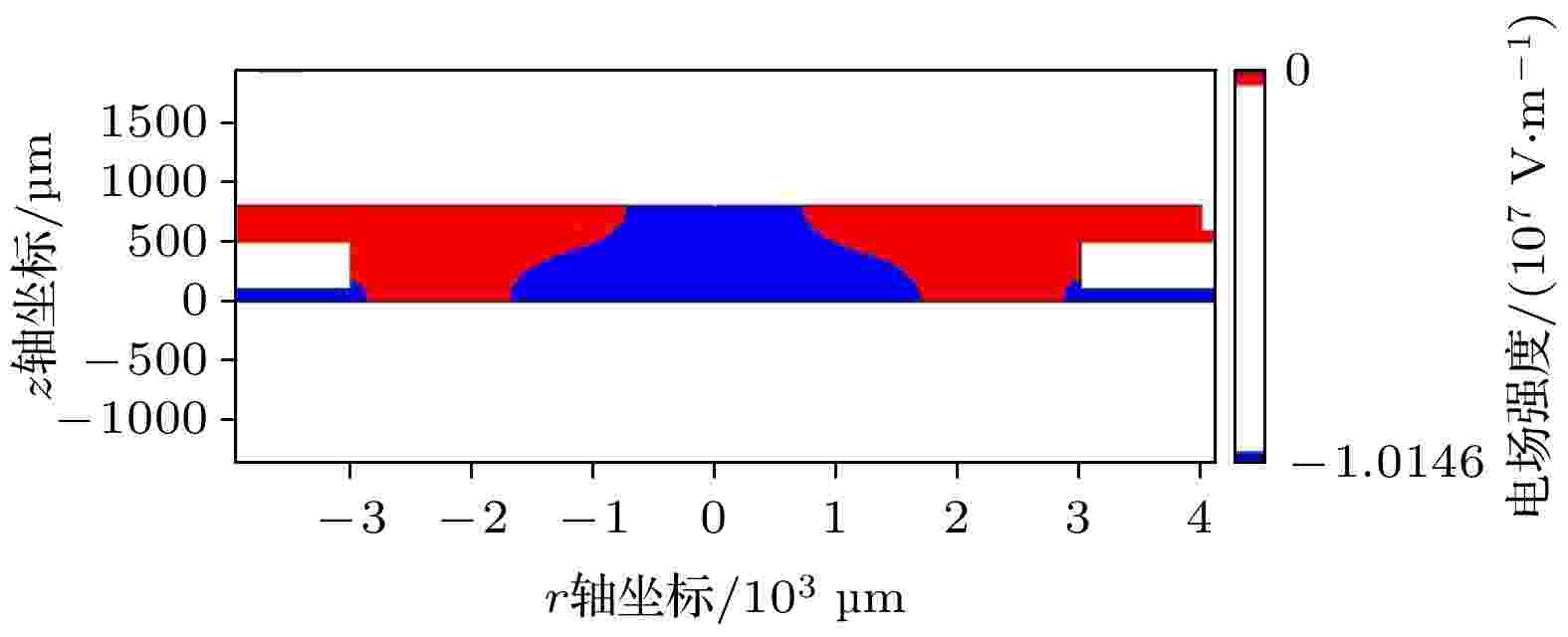
Figure6. Longitudinal electric field distribution of the sensor.
2
3.1.收集极结构对传感器放电过程的影响
收集极用于收集正离子, 形成传感器的输出电流Ic. 设计研究4种不同形貌的收集极电极结构, 保持引出极和阴极结构不变, 即引出极中心有一个直径为6 mm的引出孔, 阴极有两个直径为4 mm的透气孔, 如图7所示. 图7(a) 1#传感器收集极中心有一个尺寸为6 mm × 8 mm深度为200 μm的矩形盲孔 (考虑硅片面积只有14 mm × 10 mm, 而且硅片两边还需要粘接绝缘条和导线, 所以, 收集极盲孔面积取6 mm × 8 mm). 图7(b) 2#传感器是平板收集极, 用于研究中心矩形盲孔是否对传感器收集电流有作用. 图7(c) 3#传感器是在图7(a)基础上, 将收集极中心矩形盲孔深度200 μm减小为50 μm, 用于矩形盲孔深度对传感器性能的研究. 图7(d) 4#传感器是将图7(a)中的一个中心矩形盲孔设计为12个1.2 mm × 1.2 mm深度为200 μm的小矩形盲孔, 研究这种分散矩形盲孔对传感器收集正离子是否有帮助.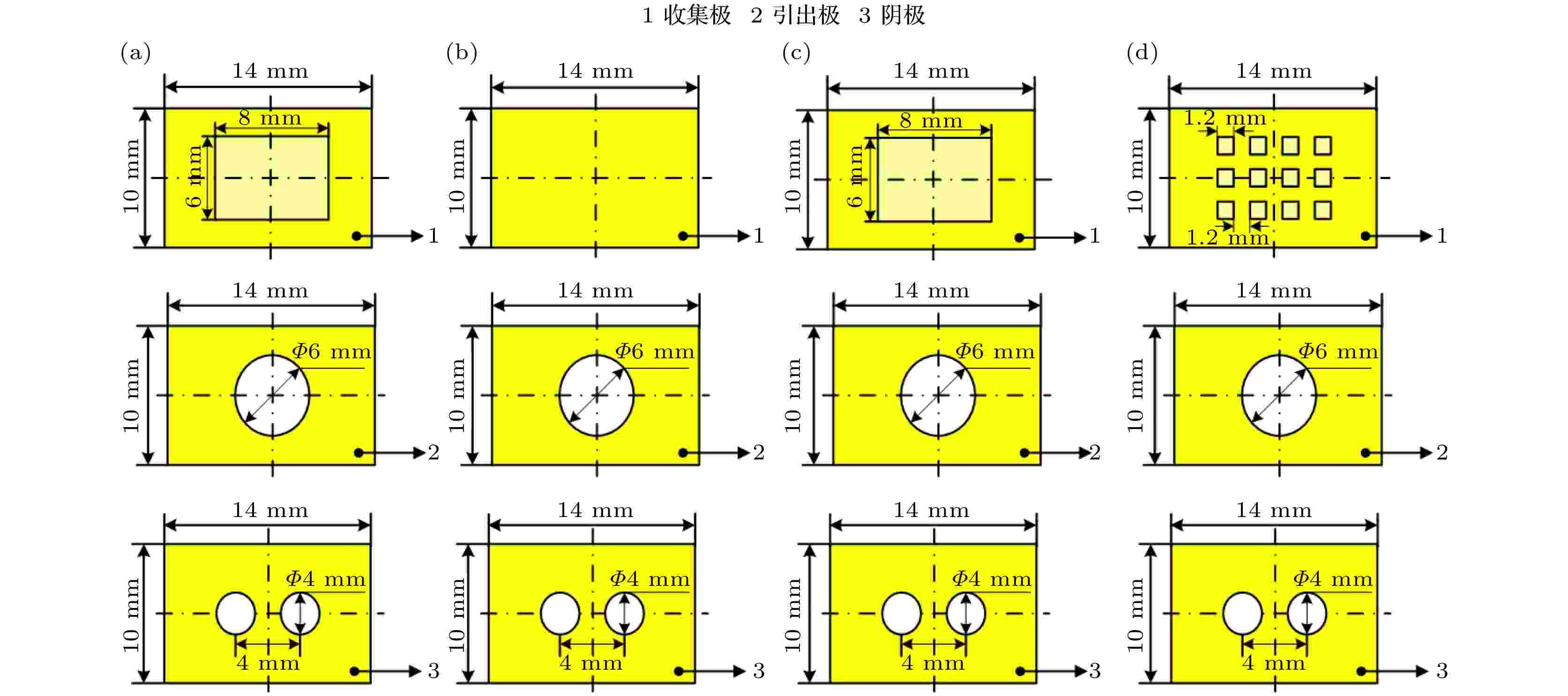
Figure7. Schematic diagram of the electrodes with four different collecting structures: (a) 1# sensor; (b) 2# sensor; (c) 3# sensor; (d) 4# sensor.
建立这4种结构传感器的放电流体模型, 其中, 传感器极间距均为100 μm, 放电环境为氮气, 气压为1个标准大气压, 温度为30 ℃, 在Ue = 100 V 和Uc = 1 V条件下, 仿真获得4种不同结构的传感器放电参数, 如表5所列.
传感器 型号 | 电子浓 度/m–3 | 正离子 浓度/m–3 | 平均收集电流 密度/(A·m–2) |
1 | 4.88 × 1011 | 9.30 × 1013 | 6.50 × 10-4 |
2 | 3.32 × 1011 | 4.85 × 1013 | 4.09 × 10-4 |
3 | 4.36 × 1011 | 6.10 × 1013 | 4.67 × 10-4 |
4 | 4.61 × 1011 | 6.29 × 1013 | 4.96 × 10-4 |
表54种不同收集极结构的传感器的仿真放电参数
Table5.Simulation discharge parameters of the four sensors with different collecting electrode structures.
由表5可知, 对比1#和2#传感器, 当传感器收集极有盲孔时, 仿真电子浓度、正离子浓度、平均收集电流密度, 比没有盲孔的收集极更大, 这说明盲孔有助于传感器收集更多正离子. 对比1#和3#传感器, 当盲孔深度由200 μm减小为50 μm时, 传感器放电参数均有所减小, 放电强度减弱, 这说明盲孔深度越深, 产生和收集的正离子越多. 考虑硅片厚度只有450 μm, 因此, 收集极盲孔深度取200 μm. 1#和4#传感器相比, 中心有一个尺寸为6 mm × 8 mm、深度为200 μm的矩形盲孔的电极, 相比4#传感器收集极的多个小矩形盲孔, 具有较大的平均收集电流密度. 因此, 收集极中心有一个尺寸为6 mm × 8 mm, 深度为200 μm矩形盲孔的1#传感器结构, 是4种收集极结构中的最优结构(图7(a)).
2
3.2.引出极结构对传感器放电过程的影响
在3.1节中获得的1#传感器收集极为优化结构的基础上, 保持收集极和阴极结构不变, 即收集极中心有1个尺寸为6 mm × 8 mm、深度为200 μm的矩形盲孔, 阴极有两个直径为4 mm的透气孔, 建立引出极引出孔直径分别为4, 3, 2, 1.2和1 mm的传感器静电场仿真模型 (图8), 研究不同引出极结构的影响.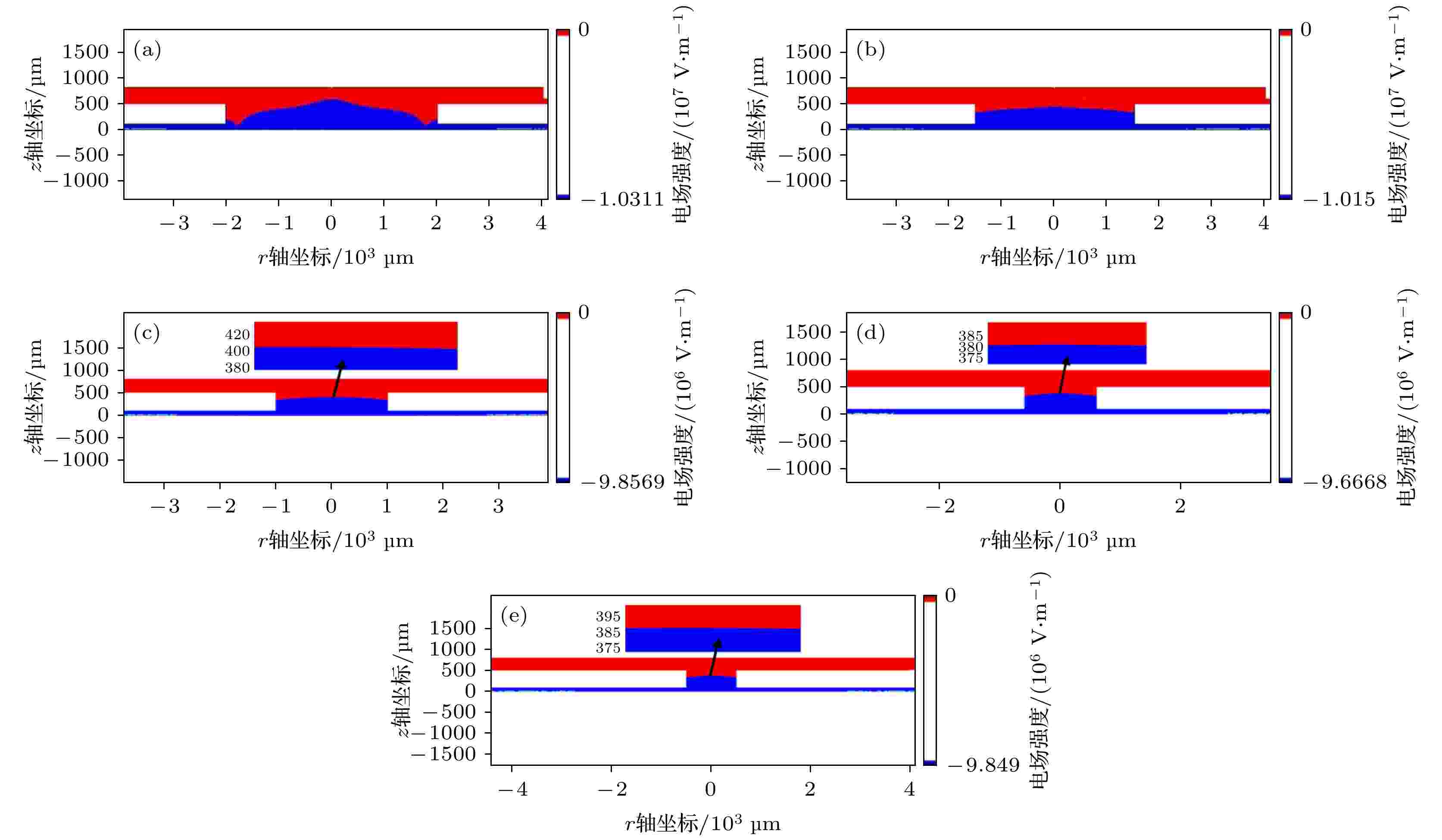
Figure8. Electrostatic field simulation of the sensors with different outlet diameters of (a) 4 mm, (b) 3 mm, (c) 2 mm, (d) 1.2 mm, and (e) 1 mm.
由图6和图8可知, 随着引出孔的孔径由6 mm逐渐减小到1 mm, 反向电场红色场域先增大后减小, 当引出孔孔径为1.2 mm时, 反向电场场域面积最大. 根据传感器不同孔径引出极静电场仿真结果, 建立了3种结构传感器(图9)的放电流体模型. 图9(a) 1#传感器引出极有1个直径为6 mm的引出孔, 图9(b) 5#传感器引出极有6个直径为2 mm的引出孔, 图9(c) 6#传感器引出极有9个直径为1.2 mm的引出孔. 仿真获得了3种不同引出极结构的传感器仿真放电参数, 如表6所列.
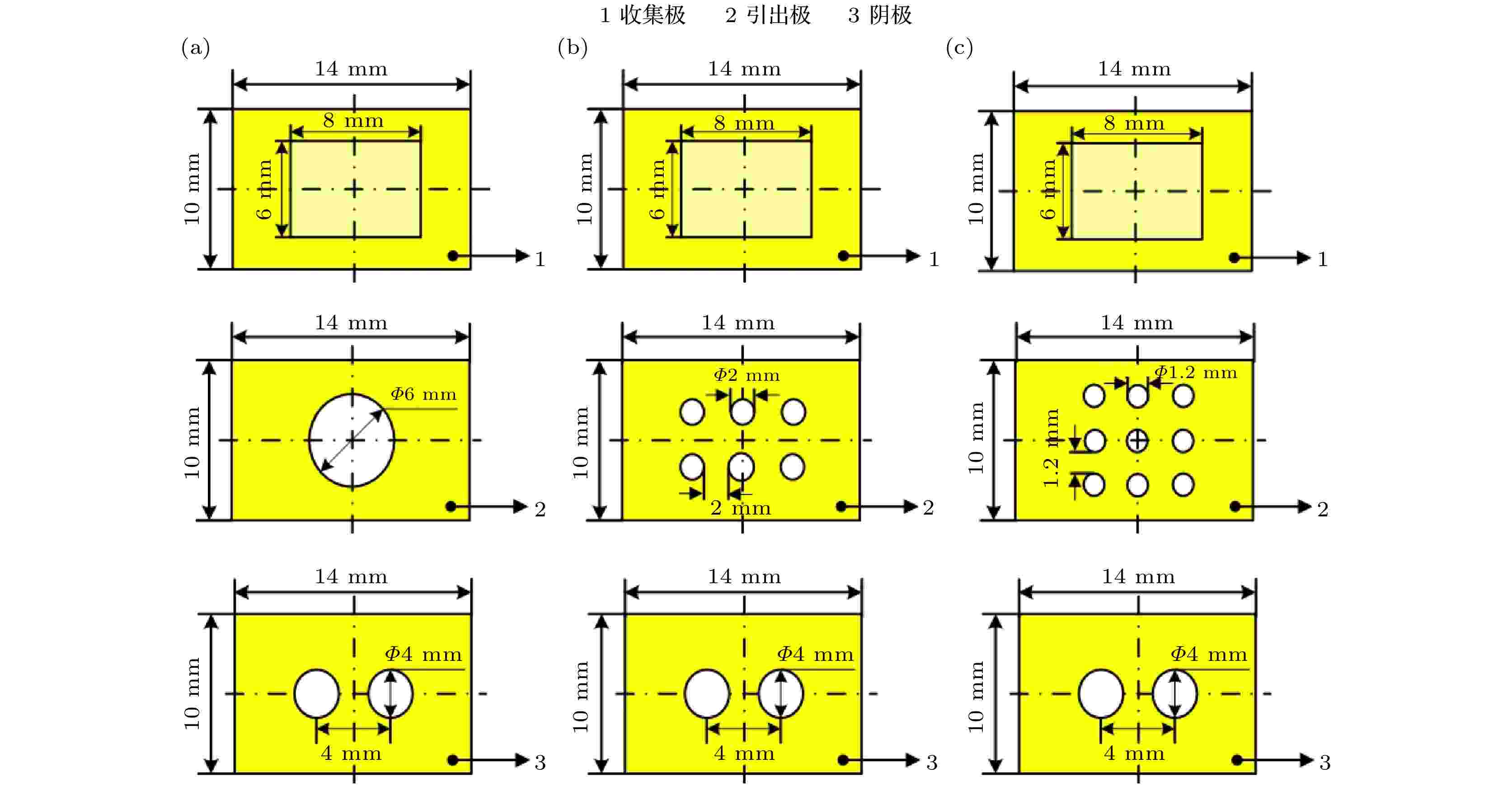
Figure9. Schematic diagram of the electrodes with three different extracting electrode structures: (a) 1# sensor; (b) 5# sensor; (c) 6# sensor.
传感器 型号 | 电子浓 度/m–3 | 正离子 浓度/m–3 | 平均收集电流 密度/(A·m–2) |
1 | 4.88 × 1011 | 9.30 × 1013 | 6.50 × 10–4 |
5 | 6.87 × 1011 | 1.12 × 1014 | 7.77 × 10–4 |
6 | 2.15 × 1012 | 3.25 × 1014 | 9.99 × 10–4 |
表63种不同引出极结构的传感器的仿真放电参数
Table6.Simulation discharge parameters of the three sensors with different extracting electrode structures.
1#, 5#和6#传感器的放电参数仿真对比(表6)说明, 引出极具有9个直径为1.2 mm引出孔的6#传感器放电参数仿真结果最大. 因此, 6#传感器所具有的9个直径为1.2 mm的引出孔结构, 是最佳引出极结构.
2
3.3.阴极结构对传感器放电过程的影响
原有传感器阴极有两个直径为4 mm的扩散孔, 有利于气体的扩散及热量的散失. 保持收集极和引出极结构不变, 即收集极中心有一个尺寸为6 mm × 8 mm深度为200 μm的矩形盲孔 (基于1#传感器优化结果), 引出极有9个直径为1.2 mm的引出孔 (基于6#传感器优化结果), 分别设计研究3种不同孔径的阴极电极结构, 如图10所示. 其中, 图10(a) 6#传感器阴极结构设计了两个直径为4 mm的扩散孔, 图10(b) 7#传感器阴极结构设计了两个直径为3 mm的扩散孔, 图10(c) 8#传感器阴极结构设计了两个直径为2 mm的扩散孔. 建立了这3种结构传感器的放电流体模型, 仿真获得了3种不同阴极结构的传感器放电参数(表7).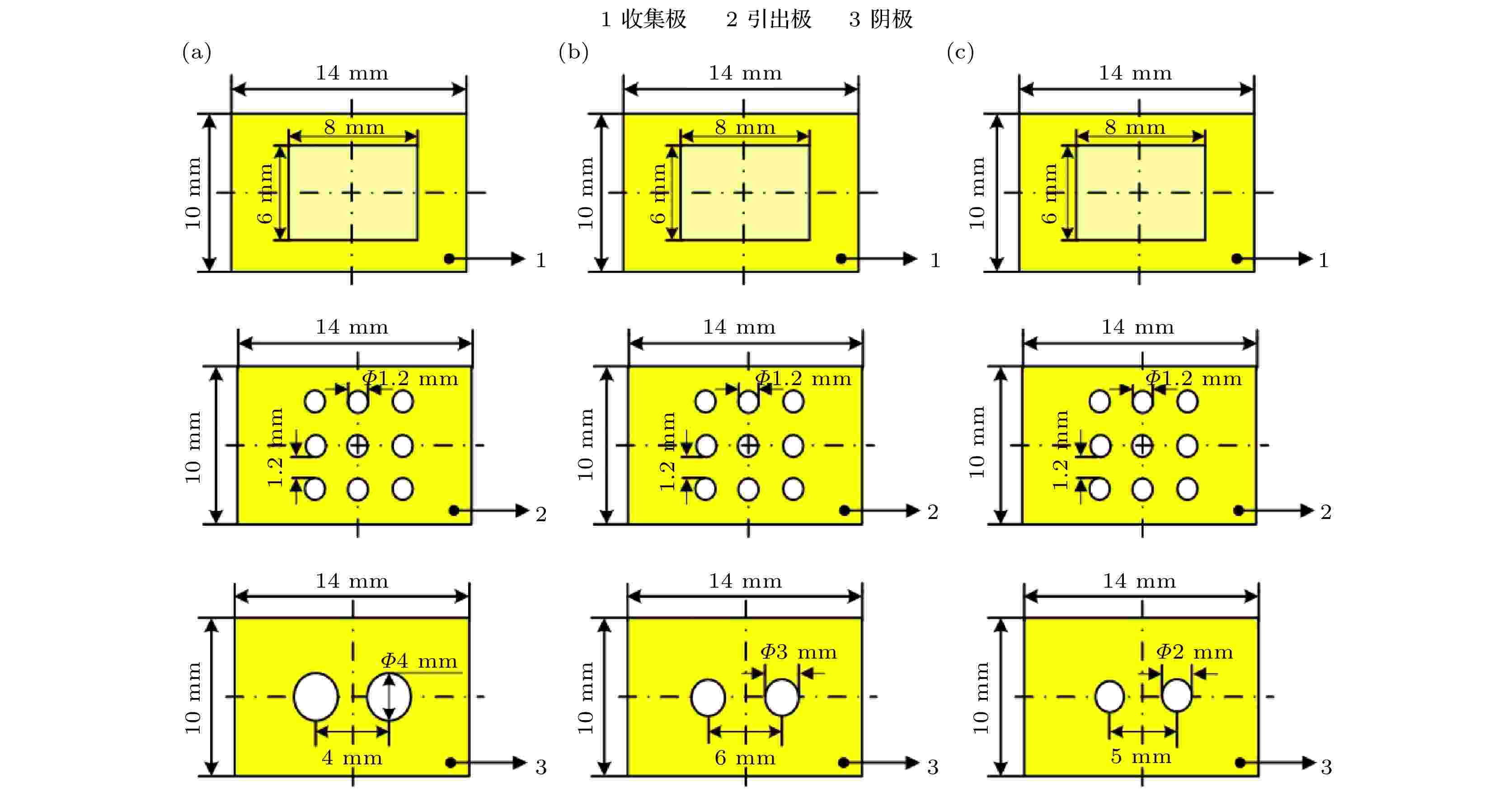
Figure10. Schematic diagram of the electrodes with three different cathode structures: (a) 6# sensor; (b) 7# sensor; (c) 8# sensor.
传感器 型号 | 电子浓 度/m–3 | 正离子浓 度/m–3 | 平均收集电流 密度/(A·m–2) |
6 | 2.15 × 1012 | 3.25 × 1014 | 9.99 × 10–4 |
7 | 2.28 × 1012 | 3.67 × 1014 | 1.00 × 10–3 |
8 | 1.99 × 1012 | 3.09 × 1014 | 9.93 × 10–4 |
表73种不同阴极结构的传感器的仿真放电参数
Table7.Simulation discharge parameters of the sensors with three different cathode structures.
由表7可知, 6#和7#传感器相比, 当传感器阴极孔径由4 mm减小到3 mm时, 仿真放电参数均变大. 但是, 当8#传感器阴极孔径减为2 mm时, 传感器放电参数反而减小, 说明阴极孔径太小, 不利于传感器收集更多正离子. 因此, 6#, 7#和8#传感器的对比说明, 7#传感器所具有的有2个直径为3 mm通孔的阴极, 是最佳阴极结构.
通过传感器收集极、引出极和阴极结构的优化, 仿真获得7#传感器为最优电极结构, 即收集极中心有1个尺寸为6 mm × 8 mm、深度为200 μm的矩形盲孔, 引出极有9个直径为1.2 mm的引出孔, 阴极有2个直径为3 mm的阴极孔.
2
3.4.传感器结构优化的实验验证
为了验证传感器结构优化仿真结果的正确性以及仿真优化方法的可行性, 按照图7、图9和图10所示的1#—8#传感器结构, 分别制作了极间距均为100 μm的1#—8#八只传感器.在与仿真相同条件下, 实验测量了8个不同结构传感器的收集电流Ic. 已知传感器收集极极板面积Se为140 mm2 (14 mm × 10 mm), 实验收集电流密度jc等于收集电流Ic除以收集极极板面积Se, 由此计算出实验收集电流密度, 与仿真平均收集电流密度进行对比(图11). 虽然仿真和实验所获得的收集电流密度有些差异, 但气体放电流体模型仿真的收集电流密度变化趋势与实验结果相近, 说明建立的气体电离流体模型可以在一定程度上反映传感器结构变化的真实情况, 因此采用仿真方法来优化传感器结构不仅是可行的, 而且可以降低传感器的设计成本. 图11说明, 7#传感器具有最大的收集电流密度, 为最优结构, 与仿真结果一致.
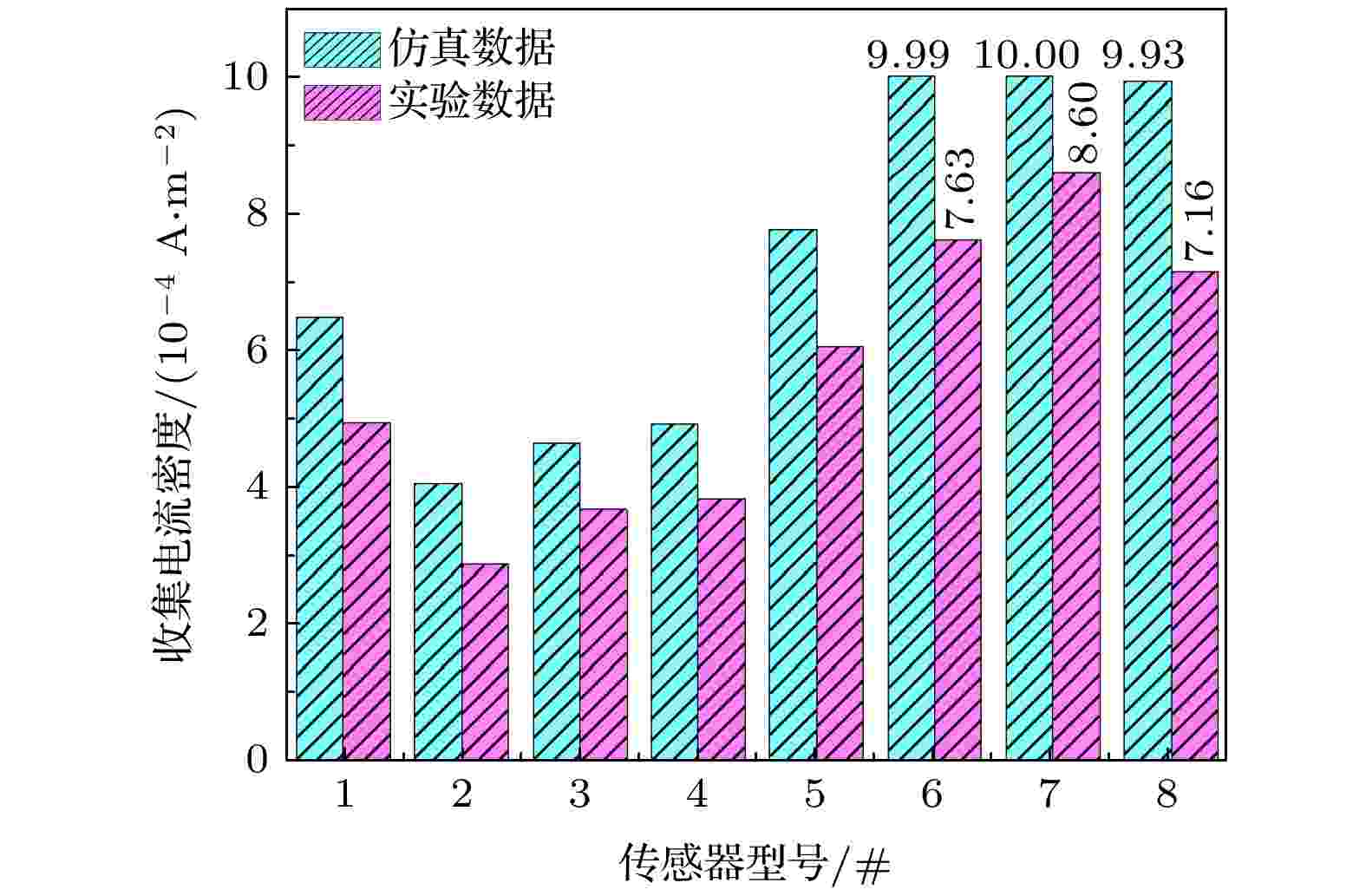
Figure11. Comparison of current densities obtained through simulation and experiment.
实验条件 | NO传感器 | SO2传感器 |
极间距/μm | 100 | 120 |
阴极电压/V | 0 | |
引出极电压/V | 150 | |
收集极电压/V | 10 | |
NO体积分数 | 0—1114 × 10–6 | |
SO2体积分数 | 0—735 × 10–6 |
表8传感器阵列测量NO和SO2两组分混合气体的实验条件
Table8.Experimental conditions of NO and SO2 mixtures detection with a sensor array.
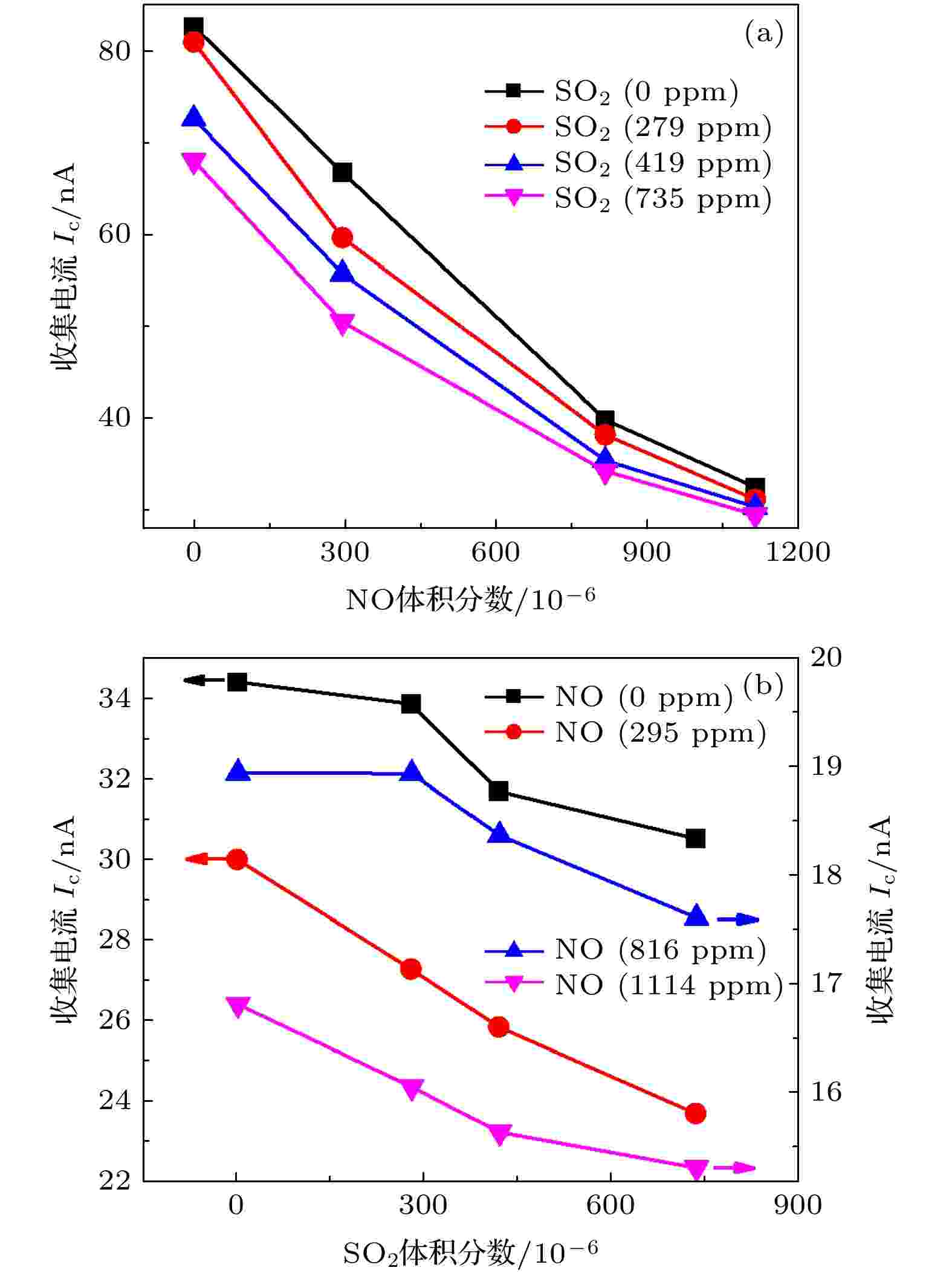
Figure12. Sensitivity characteristic curves of the sensor array for measuring NO and SO2 mixture in nitrogen: (a) Collecting currents of the NO sensor with the electrode spacing of 100 μm versus volume fraction of NO under different volume fractions of SO2; (b) collecting currents of the SO2 sensor with the electrode spacing of 120 μm versus volume fraction of SO2 under different volume fractions of NO.
灵敏度数值是衡量传感器性能的一个重要指标, 灵敏度越高, 表示相同的输入改变量引起的输出变化量越大, 性能越好. 为了与其他不同原理的传感器对比, 灵敏度计算时输出量采用相对变化量形式:
传感器型号 | 量程/10–6 | 灵敏度SN/106 |
三电极碳纳米管NO传感器 | 0—1114 | –1.6 × 10–2 |
三电极碳纳米管SO2传感器 | 0—735 | –1.0 × 10–2 |
NO-B1 NO传感器[23] | 0—250 | 4.0 × 10–3 |
NX1 CiTiceL NO传感器[24] | 0—5000 | 2.0 × 10–4 |
3SF CiTiceL SO2传感器[25] | 0—2000 | 5.0 × 10–3 |
5SF CiTiceL SO2传感器[26] | 0—2000 | 5.0 × 10–3 |
GS+7SO2 SO2传感器[27] | 0—1000 | 1.0 × 10–3 |
表9碳纳米管三电极传感器与现有NO, SO2传感器的性能对比
Table9.Performance comparison of carbon nanotube based triple electrode sensors with the existing NO and SO2 sensors.