全文HTML
--> --> -->近年来的研究指出石墨烯的表面摩擦力具有厚度依赖性[3,4], 这是因为石墨烯具有极低的面外刚度, 在摩擦过程中易产生面外变形从而导致摩擦力增大[3]. 基底的不同会导致这一过程产生差异, 与基底结合得更牢固会抑制褶皱的产生从而使摩擦力减小. 如将基底换成与石墨烯黏附力更大的云母, 或者对SiO2基底进行等离子体处理以增强石墨烯与基底的黏附力, 都可以降低褶皱效应达到减少摩擦力的目的[5]. 另外, 刚度越小的基底由于变形越大导致石墨烯表面摩擦力也越大[6]. 因此, 基底会影响石墨烯等二维材料的面外变形, 从而影响摩擦力[7]. 对比研究有基底的支撑石墨烯和悬浮石墨烯的摩擦特性, 可以探讨面外变形对石墨烯的影响[8].
将石墨烯悬浮是一种测量石墨烯本征性能的常用方法[9,10]. 近年的研究发现, 悬浮状态的石墨烯受到的面内拉伸强度高于支撑石墨烯[11]. Zhang等[12]发现应力拉伸可以显著减少石墨烯的面外变形. 可见, 通过拉伸可以调节石墨烯的面外变形强度, 进而调节石墨烯的表面摩擦. 因此, 研究悬浮石墨烯的摩擦特性可以排除基底的影响[13,14], 拉伸应力对石墨烯表面摩擦力的影响也对石墨烯的摩擦力调控提供了新的思路. 另外, 在微/纳米机电系统的实际应用中, 石墨烯可能以悬浮状态存在, 如石墨烯机械谐振器等[15,16], 因此研究悬浮石墨烯的摩擦性能是十分必要的, 对石墨烯在MEMS/NEMS中的应用具有很大帮助.
原子力显微镜(atomic force microscope, AFM)作为研究纳米摩擦的重要工具, 其极高的分辨率与灵敏度可以帮助我们研究石墨烯在不同状态下摩擦力的微小差异. 本文通过使用AFM的侧向力模块研究了不同厚度石墨烯在悬浮状态与支撑状态的摩擦特性, 对比两种状态下摩擦特性上的异同, 并分析造成差异的原因. 此外, 研究了不同针尖半径下悬浮与支撑石墨烯的摩擦力变化情况, 深入探讨了石墨烯的面外变形与接触面积对摩擦力的影响.
2.1.悬浮石墨烯的制备
实验所用基底为SiO2/Si基底(覆盖有300 nm厚SiO2氧化层的Si晶片). 采用接触式光刻与湿法刻蚀在SiO2表面刻蚀出均匀分布的圆孔阵列, 圆孔的直径为3 μm, 圆孔间距为10 μm, 深度为150 nm. 刻蚀所用溶液为BOE (buffered oxide etch)溶液, 以49% HF水溶液∶40% NH4F水溶液 = 1∶6 (体积比)的比例配置而成. 溶液用量根据需要配置, 本文用量为NH4F 32 g, 去离子水48 mL, 49% HF水溶液9.8 mL. 样品制备过程中所使用的试剂的规格纯度等信息由表1列出. 刻蚀速度与孔径大小有关, 当孔径小于5 μm时由于刻蚀液的流动速度等原因刻蚀速度会下降, 因此刻蚀深度的准确值需要使用AFM测量, 保证石墨烯薄膜能够悬浮即可. 刻蚀后的基底表面残留有光刻胶, 在实验前需要进行超声清洗, 依次使用丙酮、异丙醇、去离子水超声清洗30 min, 并用氮气吹干.序号 | 名称 | 型号/规格 | 生产公司 |
1 | 光刻胶 | AZ5214 | 苏州锐材半导体有限公司 |
2 | 显影剂 | NMD- 3/2.38% | 长春应化(常熟)有限公司 |
3 | 氟化铵(NH4F) | 优级纯 | 国药化试 |
4 | 氢氟酸(HF) | 化学纯 | 国药化试 |
5 | 乙醇 | 分析纯 | 国药化试 |
6 | 丙酮 | 分析纯 | 国药化试 |
7 | 异丙醇 | 分析纯 | 国药化试 |
表1实验所用的试剂信息
Table1.The reagent information used in the experiment.
圆孔阵列刻蚀完成后, 采用机械剥离法制备石墨烯薄膜. 先用胶带剥离出石墨烯, 剥离好后将胶带上的石墨烯样品转移到已清洗干净的带有微孔的基底上, 形成悬浮石墨烯结构.
2
2.2.实验方法
实验用原子力显微镜购自Asylum Research公司(美国), 型号为MFP-3D型. 实验前首先在光学显微镜下找到适合的样品, 确定位置后使用AFM的轻敲模式(tapping)表征样品的形貌, 样品形貌如图1所示, 图中所示石墨烯高度为7.9 nm. 使用侧向力模式测量样品的摩擦力, 实验所用探针为multi75AI-G硅探针, 其标称力常数为3 N/m. 采用扫描电子显微镜(scanning electron microscope, SEM)表征针尖的大小. 使用非接触法标定探针的法向和侧向力弹性系数, 结合悬臂长度(225 μm)和宽度(28 μm)在不接触样品的条件下即可测得. 新针、预磨损针尖的侧向灵敏系数分别为479 nN/V和796 nN/V. 实验时湿度保持在50%—60%, 温度保持在(25 ± 2) ℃. 为研究悬浮与支撑石墨烯的差异, 对比实验在同一样品的不同区域进行, 在同一组试验中先后测试悬浮区域与支撑区域的摩擦特性, 避免其他因素的影响. 摩擦力测试的主要步骤如下: 1) 在轻敲模式下扫描样品, 找到合适的试验区域; 2) 确定位置后转换侧向力模式, 标定探针的法向与侧向灵敏系数, 测试区域为500 nm × 500 nm的正方形区域. 分别在悬浮区域与支撑区域进行黏附力、摩擦力-载荷关系特性以及黏滑(stick-slip)特性测试; 3) 重复在悬浮与支撑区域转换位置实验, 每次实验重复3次以上.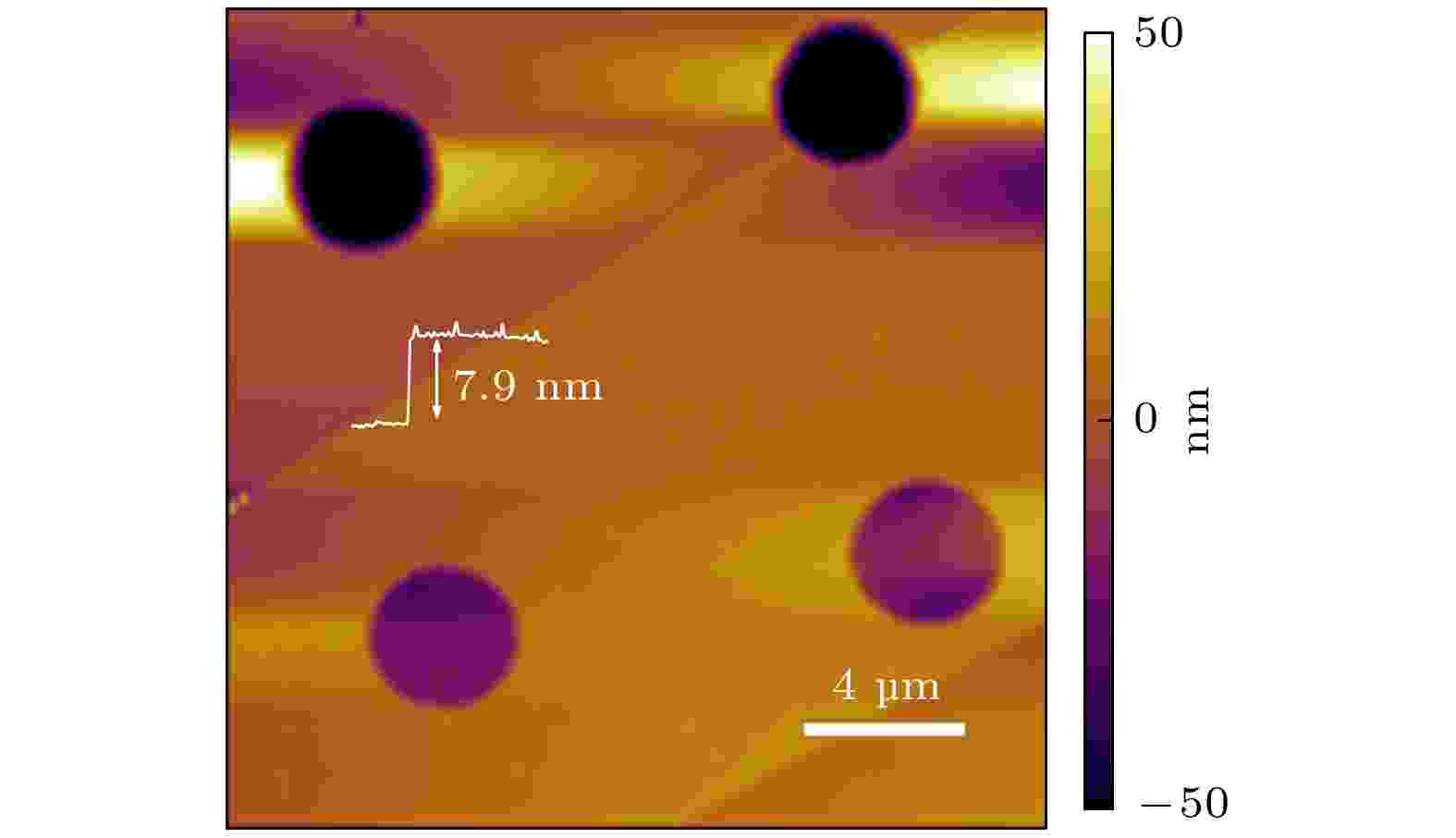
Figure1. AFM topographic image with height of graphene.
3.1.悬浮石墨烯与支撑石墨烯的摩擦特性
图2(a)为悬浮石墨烯的AFM形貌图, 孔中央白框为悬浮石墨烯摩擦力测量区域, 黑框为支撑石墨烯摩擦力测量区域. 悬浮与支撑石墨烯是在同一样品上测量的, AFM实验记录了实验区域的粗糙度数据, 悬浮区域的粗糙度轮廓算数平均偏差Ra为42.505 pm, 支撑区域Ra为45.093 pm. 可见悬浮区域与支撑区域的粗糙度差异很小, 几皮米的差异可能是仪器误差导致的, 对于摩擦力没有影响. 分别在这两片区域进行摩擦力-载荷特性的实验, 实验结果如图2(b)所示, 其中蓝色线是支撑石墨烯实验结果, 黑色线是悬浮石墨烯实验结果. 可见, 悬浮区域的摩擦力明显小于支撑区域. 此外, 为了进一步研究悬浮对石墨烯摩擦力的影响, 进行了原子尺度的摩擦力测量. 在原子尺度下, 针尖的摩擦是“跳跃”的, 即从一个势能最小位置“跳跃”到下一个势能最小位置, 这种非连续的滑动跃迁被称为“黏滑”, 表现为侧向力曲线的锯齿状变化[17,18]. 图2(c)和图2(d)分别为支撑区域与悬浮区域在5 nm范围测量的侧向力曲线, 载荷为150 nN. 红色和蓝色曲线分别代表针尖在石墨烯表面来回滑动过程中的侧向力大小. 可见, 针尖在石墨烯表面产生了明显的黏滑运动. 对比支撑与悬浮区域的黏滑图像可以看出, 支撑石墨烯出现了明显的“摩擦增强效应”[5], 即在摩擦的起始阶段侧向力逐渐增大, 表现为整体侧向力曲线的向上倾斜; 而悬浮石墨烯则没有出现摩擦增强效应.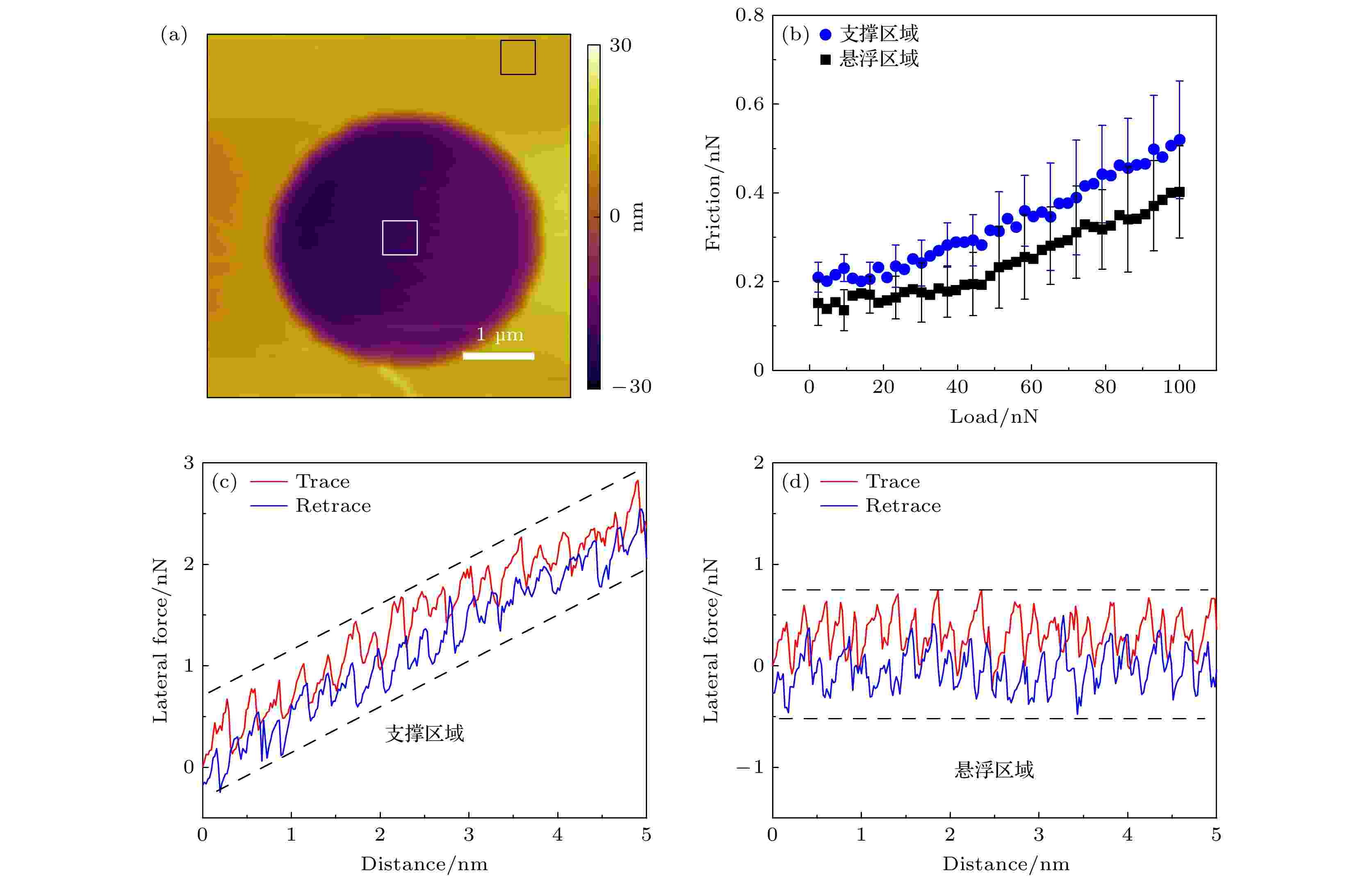
Figure2. (a) Topography of suspended graphene, the white box is the test area for suspended graphene, the white box is the test area for supported graphene; (b) friction versus load data measured on the suspended graphene and supported graphene; (c) lateral force curves (load of 150 nN) measured on supported graphene and (d) suspended graphene.
图3(a)分别为7.9, 12.0, 39.0和68.0 nm厚的石墨烯在悬浮与支撑状态下的摩擦-载荷关系比较. 从图3(a)可以看到, 随着载荷的增加, 支撑石墨烯与悬浮石墨烯摩擦力差异变大, 因此提取100 nN载荷下不同厚度支撑与悬浮石墨烯样品的摩擦力作为对比, 结果如图3(b)所示. 当厚度逐渐增大时, 支撑石墨烯的摩擦力逐渐减小. 另外, 当厚度增大时悬浮与支撑石墨烯的摩擦力逐渐接近. 可以看出在石墨烯厚度达到68 nm时悬浮与支撑石墨烯的摩擦力已经相差无几, 这表明厚层石墨烯表面受悬浮的影响很小.
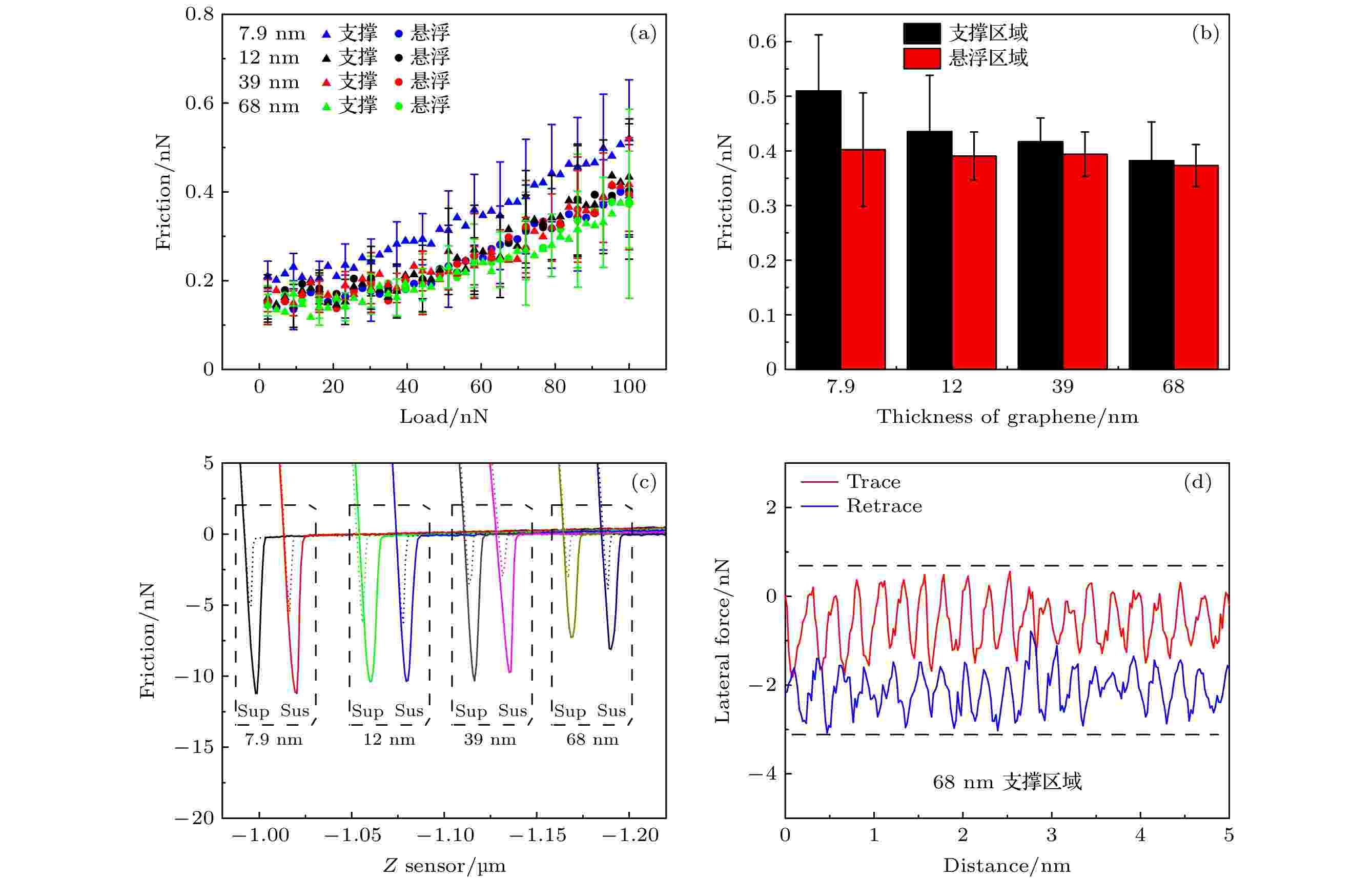
Figure3. (a) Friction versus load data measured on the suspended graphene and supported graphene of different thickness; (b) the friction of supported and suspended graphene of different thickness (load of 100 nN); (c) force-distance curves measured on suspended and supported graphene of different thickness; (d) lateral force curves (load of 150 nN) measured on supported thick grapheme (68 nm).
由于摩擦力受到界面间黏附力的影响, 首先对比不同厚度石墨烯的黏附力大小. 如图3(c)所示, 分别在同一石墨烯样品的悬浮区域与支撑区域进行法向力-位移曲线的测量. 在法向力-位移曲线测量中, 针尖首先接近石墨烯表面直到接触, 达到设定的力后针尖抬起与样品表面分离, 黏附力是通过测量针尖从样品表面分离所需的力得到. 虚线表示针尖接近石墨烯时针尖与石墨烯的相互作用, 实线表示针尖从石墨烯表面缩回时针尖与石墨烯的相互作用. 最低点代表针尖与石墨烯脱离时的黏附力. 考虑到不同样品测量时的环境影响, 不同厚度石墨烯与针尖的黏附力并没有明显的差别. 悬浮石墨烯与支撑石墨烯的黏附力也无明显区别. 这说明不同厚度悬浮石墨烯与支撑石墨烯摩擦力的巨大差异与黏附力无关, 摩擦力的差异主要来自于摩擦过程中的面外变形.
当石墨烯有基底支撑时, 针尖与石墨烯接触后, 石墨烯被夹在针尖与基底之间, 由于几何约束, 石墨烯不能自由的变形. 如图4(a)所示, 当针尖向前滑动时, 带动针尖周围区域松散的石墨烯, 逐渐推动石墨烯在接触区域产生面外变形, 即形成面外的褶皱, 阻碍针尖的运动, 导致摩擦力在起始阶段出现增强效应[19]. 褶皱在摩擦的阶段始终阻碍针尖的运动造成摩擦力的增大. 然而, 石墨烯薄膜在悬浮状态下处于可自由变形的状态. 一方面, 悬浮石墨烯由于受到重力与针尖的载荷, 会产生拉伸应力, 拉伸应力将会使褶皱在整个平面上得到舒展, 如图4(b)所示. 另一方面, 悬浮石墨烯可以自由地上下变形, 受到针尖的压力时接触点会迅速达到稳定状态, 摩擦过程中石墨烯始终保持较为平坦的状态, 摩擦力主要来自于针尖与表面作用时产生的能量耗散[20,21], 因此没有增强效应的出现, 导致悬浮石墨烯的摩擦力比支撑石墨烯明显减小. 厚层石墨烯本身的面外刚度大, 即使在支撑状态也难以产生褶皱, 因此悬浮与支撑区域的摩擦力并无明显区别. 图3(d)是68 nm厚支撑石墨烯150 nN载荷时的侧向力曲线, 没有摩擦增强效应的出现. 增大石墨烯的厚度抑制了摩擦过程中的面外变形, 这说明褶皱是影响石墨烯摩擦力大小的重要因素.
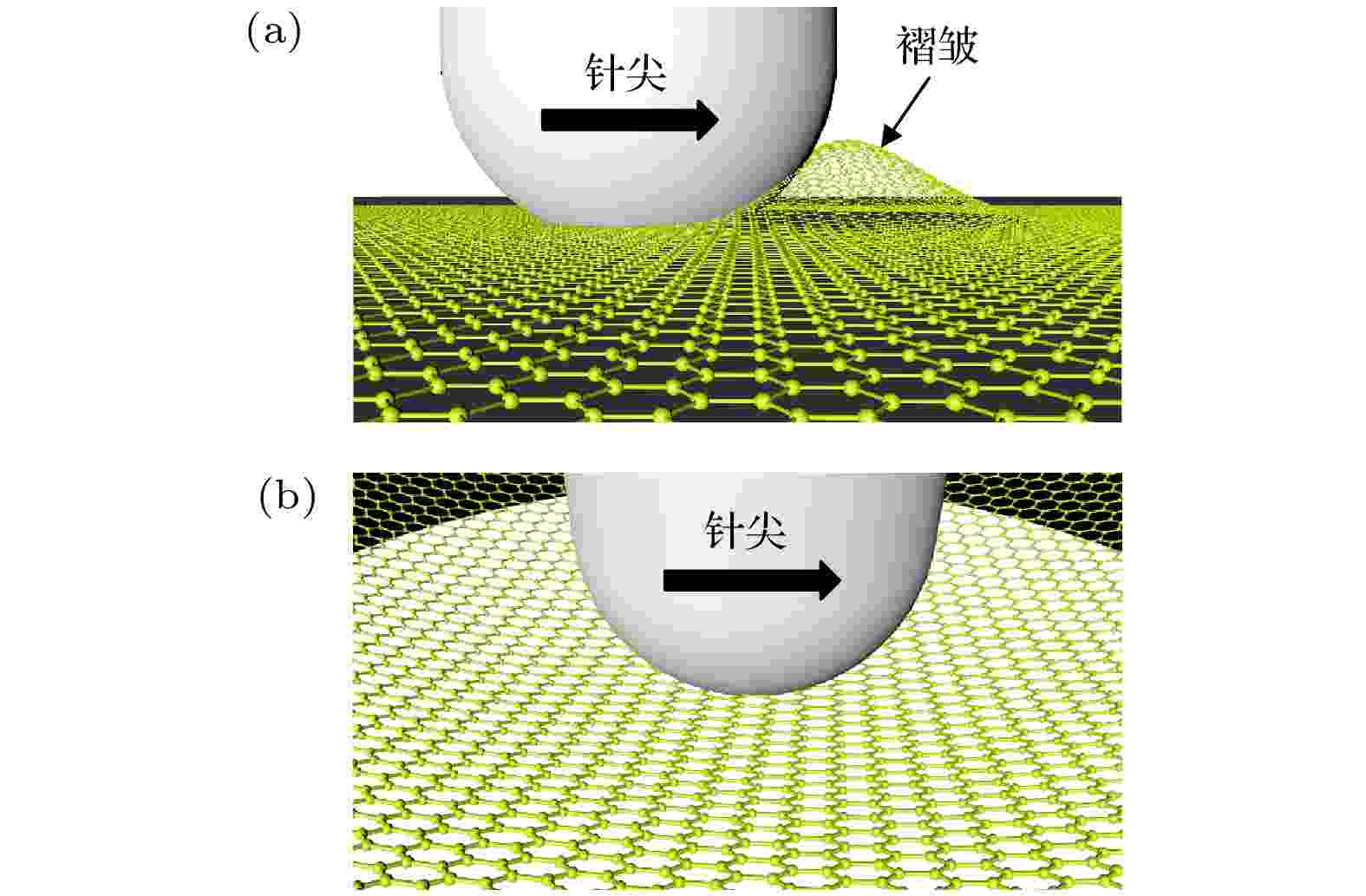
Figure4. Schematic diagram of the friction process between the tip and graphene under (a) supported and (b) suspended states.
2
3.2.针尖大小对于石墨烯摩擦力的影响
在微纳尺度下, 褶皱是石墨烯摩擦力大小的重要影响因素. 一方面是石墨烯薄膜的自身褶皱, 在SiO2基底上由于基底与石墨烯的结合并不十分紧密, 石墨烯本身会有一定的起伏; 另一方面是在摩擦的动态过程中产生的, 石墨烯在针尖与基底的挤压下产生面外变形. 此外, 界面间实际接触面积是微纳尺度下摩擦力最主要影响因素, 通过改变针尖大小可以探讨接触面积对石墨烯摩擦力的影响.图5(a)和图5(b)分别为新探针与预磨损探针针尖的SEM图像. 预磨损探针是使用过超过一万次摩擦循环的探针, 针尖严重磨损, 可以看出预磨损探针的针尖半径明显增大.
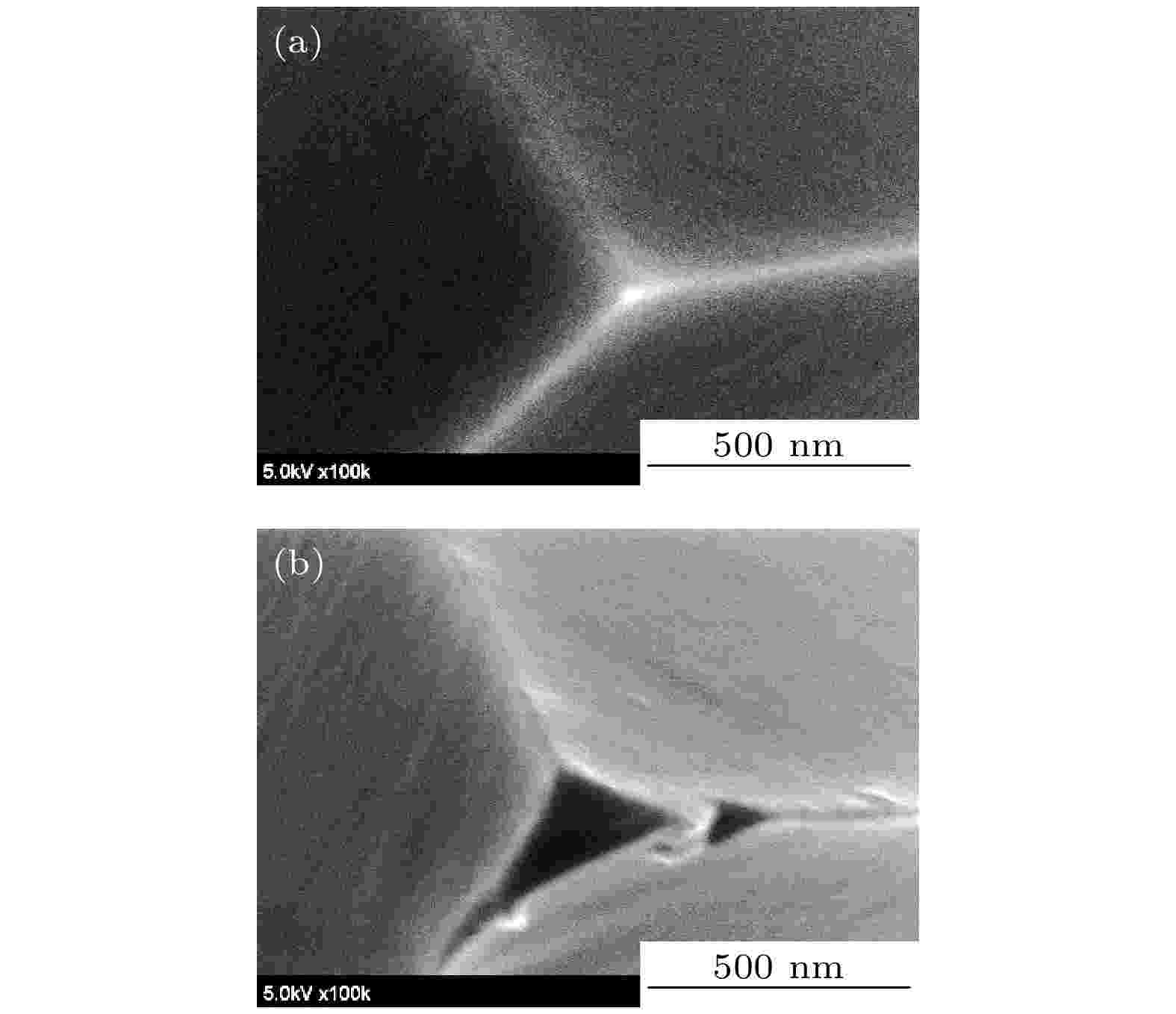
Figure5. AFM tip (a) without and (b) with pre-wearing process before measurements obtained by scanning electron microscope (SEM).
图6(a)为新针尖和预磨损针尖与悬浮石墨烯和支撑石墨烯的法向力-位移曲线. 可见, 使用预磨损针尖时, 石墨烯表面的黏附力显著大于新针尖, 而悬浮区域与支撑区域的黏附力均没有明显差异.
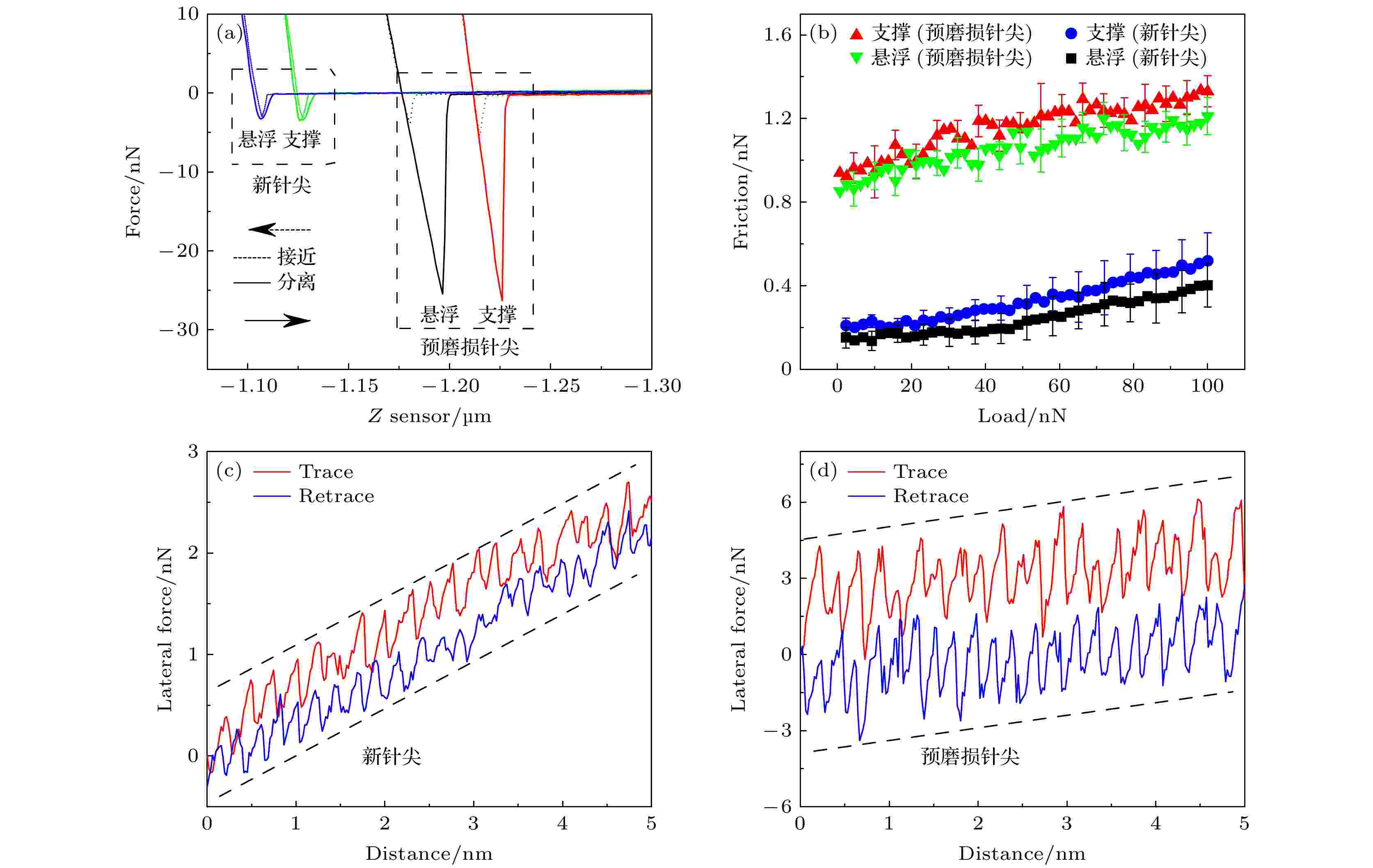
Figure6. (a) Force-distance curves measured on suspended and supported graphene under new tip and pretreated tip; (b) friction-load image of the new probe tip and pretreated tip on the supported graphene and suspended graphene; (c) and (d) lateral force curves measured on supported graphene measured by different tips (load of 150 nN).
黏附力主要来自于范德瓦耳斯力、静电力、毛细作用力以及化学键作用力等力的总和. 本实验中, 预磨损针尖黏附力的增大主要是因为针尖面积增大导致范德瓦耳斯力的增大. 由于黏附力对摩擦力有重要影响, 黏附力增大摩擦力也会随之增大. 如图6(b)所示, 使用预磨损针尖时, 石墨烯表面的摩擦力显著大于新针尖, 这与黏附力的变化一致. 另一方面, 与黏附力变化不同的是, 使用新针尖与预磨损针尖测量悬浮区域的摩擦力都小于支撑区域, 这来自于褶皱的影响. 预磨损针尖与石墨烯的接触面积比新针尖大, 在载荷相同的情况下接触应力减小, 因此褶皱效应更弱. 褶皱产生的额外摩擦力也在总摩擦力中占据更小的比例, 总摩擦力更多取决于针尖与石墨烯表面黏滑运动产生的能量耗散以及克服黏附所需的力[22]. 图6(c)和图6(d)分别为新针尖与预磨损针尖在支撑石墨烯表面测量的侧向力曲线, 载荷相同, 都为150 nN, 针尖与石墨烯表面均产生了明显的黏滑运动. 预磨损针尖与石墨烯之间黏滑运动的强度显著加强, 表明能量耗散的增加. 同时, 预磨损针尖与支撑石墨烯表面也出现摩擦增强效应, 说明针尖与石墨烯表面接触区域产生了褶皱, 引起摩擦力的增大.
由上述研究可以得出, 石墨烯的总摩擦力可以由以下三个主要力来源相加得出:
通过以上实验可以发现, 除了改善接触面积与接触质量以外, 褶皱是影响石墨烯摩擦的重要因素, 在作为减摩材料时, 考虑如何减少褶皱的产生可以明显地提高减摩效果. 如减少应力的集中, 可以减少褶皱的产生; 或是采用如悬浮等方法对材料进行拉伸, 可以尽量避免因为面外变形导致的额外摩擦, 减少能量损耗.
1) 悬浮状态下石墨烯的摩擦力显著小于支撑状态下石墨烯的摩擦力, 并且随着载荷的增大减摩效果更明显; 黏滑实验显示支撑石墨烯产生了明显的摩擦增强现象, 而悬浮石墨烯没有出现此现象.
2) 厚度的增加会导致石墨烯褶皱效应的减弱, 随着厚度的增加, 悬浮石墨烯的减摩效果逐渐消失, 并且厚层石墨烯也无摩擦增强效应.
3) 使用预磨损探针时, 悬浮石墨烯和支撑石墨烯的摩擦力都显著增大, 且悬浮石墨烯的摩擦力依然比支撑石墨烯小, 但摩擦力减少比例小于新针尖.
上述结果表明, 悬浮石墨烯与支撑石墨烯摩擦力的巨大差异是由石墨烯的褶皱造成的. 在将石墨烯等二维材料应用到微纳米器件上时, 对褶皱的控制将显著影响摩擦力的大小, 也会很大程度上影响器件的功耗. 本文通过对悬浮石墨烯摩擦特性的研究揭示了石墨烯摩擦力的产生机理, 对于石墨烯应用到微纳器件中提供了帮助.