全文HTML
--> --> -->针对微通道内气体流动行为, 研究者通过机理分析获得了不同微通道下压力、速度或流量的解析解. 2007年, Dongari等[14]采用二阶滑移边界求解了长微通道内气体滑移流动N-S方程, 结果表明采用高阶滑移边界条件可以提高N-S方程对稀薄气体流动的有效性. Stevanovic[15]对变截面微通道内的可压缩亚音速气体流动进行了分析研究, 模型为微通道内气体流动的设计分析提供了支撑. 2015年, Das和Tahmouresi[16]应用积分变换分析了椭圆微通道内充分发展的气体滑移流动, 所建立的模型可用于计算椭圆微通道内滑移流的质量流量与压力分布. 2017年, Kurkin等[17]研究了等截面通道内进口段的滑移流, 给出了克努森数0—1间的解析公式, 并与模拟结果进行比较, 二者吻合较好. 2018年, 鉴于前人所得解析解存在繁琐复杂的问题, Simlandi[18]利用积分技术求解了矩形微通道内的气体流动, 所得结果与文献符合得很好.
关于微通道稀薄气体流动模拟, 研究者对不同形状微通道内的流动性为进行了研究. 2015年, 在前人对不同形状微通道内气体流动行为研究的基础上, Yovanovich等[19]指出了椭圆型微通道与矩形微通道内稀薄气体流动的相似性, 给出了两种截面下的滑移流模型. 2016年, Rovenskaya[20]利用耦合一阶滑移边界条件的N-S方程, 对90o三维弯通道内可压缩气体流动进行模拟, 讨论了几何、气体稀薄度与可压缩性对流场的影响. 2018年, Taassob等[21]用直接模拟蒙特卡罗法, 模拟了含弯管微通道中的稀薄气体流, 提出了弯管的最佳适用曲率半径. 2019年, Ahangara等[22-23]利用具有双弛豫时间的格子玻尔兹曼法, 模拟了瞬态滑移条件下具有多喉部或后向台阶的微通道内的稀薄气体流, 与直接模拟蒙特卡罗法所得结果吻合较好.
但是, 尚无文献报道封闭微小器件通过微通道充放气的气体流动行为, 也无文献从效率的角度对抽空所使用的微米级通道管型进行研究. 本文在推导靶丸内残余气体分压的基础上, 分析了低温靶靶丸内残余气体分压的影响因素, 为微直径管道内杂质气体抽空流洗建立分压上限值. 在充分考虑不同压力气体在微直径管道内流动机理的基础上, 选定滑移流模型, 利用COMSOL软件开展数值模拟, 为流洗过程中毛细管选型与最佳中间抽洗压力提供了方法指导. 在此基础上, 还讨论了流洗温度对流洗效率的影响, 证明了低温下进行气体流洗的优势和必要性.
2.1.靶内杂质气体分压上限分析
靶物理设计要求靶内杂质的原子数量百分比不超过0.003%, 由于实际上无法测量原子百分比, 故需将该指标转换成杂质气体分压. 同时为便于分析, 对如图1所示的低温靶靶丸作冰层完全光滑, 呈球壳形的假设.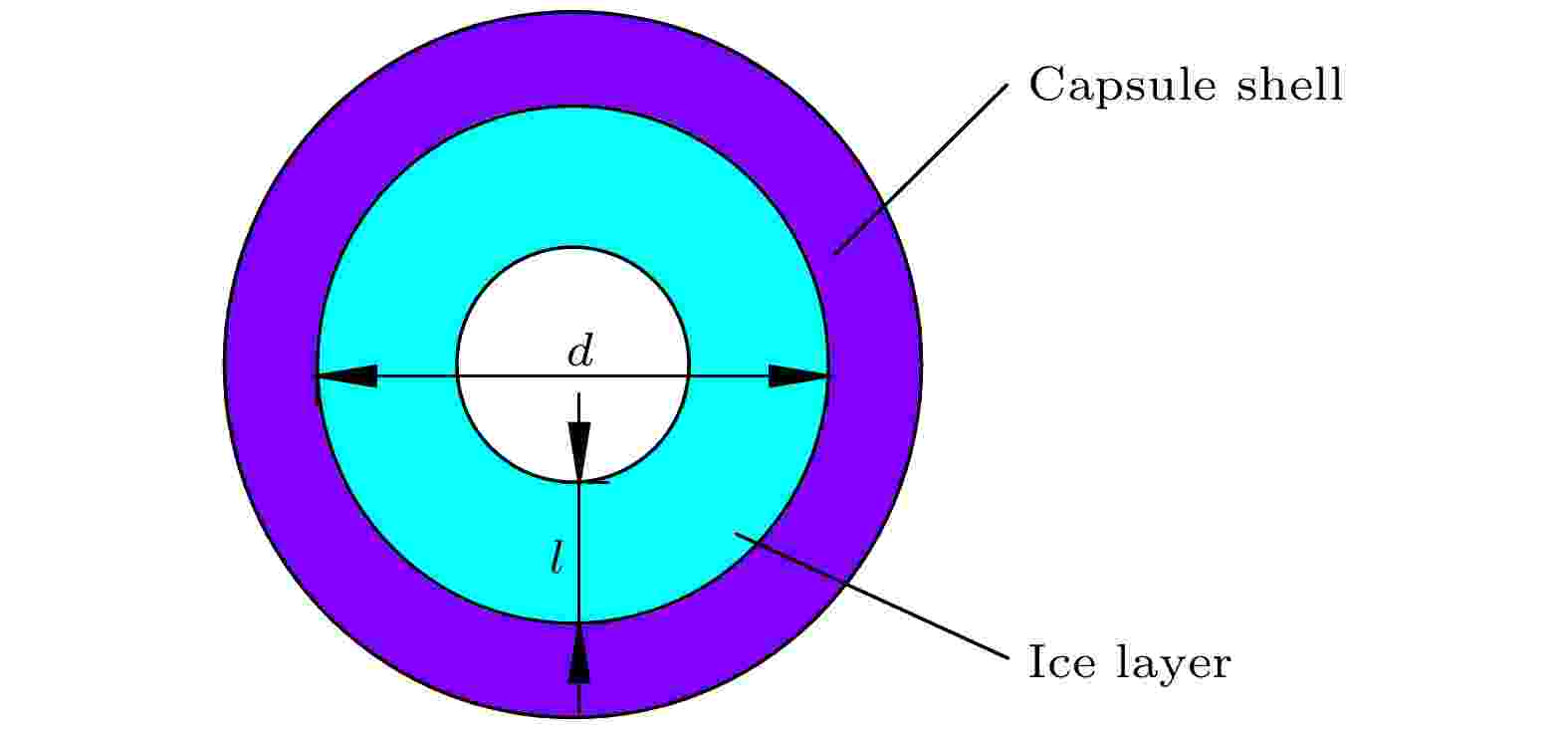
Figure1. Schematic of cryogenic target capsule.
根据靶物理设计要求, 分别计算杂质气体与燃料气体的原子个数, 获得靶内杂质气体原子数量百分比β:
考虑杂质冰层体积占比α, 分别计算燃料与杂质质量, 并代入(1)式得:
由此计算杂质冰层质量, 并将杂质气体考虑为理想气体, 可得杂质气体分压上限pr计算式为
根据式(3)可知, 对于内径d和冰层厚度l一定的低温靶, 影响杂质气体分压上限的因素主要是杂质原子数量百分比上限β与靶内温度T. 显然, β值越小, 杂质气体分压上限值pr越小; 靶内温度T越低, 杂质气体分压上限值pr也越低.
下面以NIF (National Ignition Facility) 基准靶为参照[24], 分析靶内温度对pr的影响程度. NIF基准靶内径d = 2 mm, 冰层厚度l = 70 μm; 氘燃料冰层密度取ρ1 = 206 kg/m3, 杂质气体冰层密度取ρ2 = 1160 kg/m3. 由于靶内气体杂质不限于空气, 故将杂质原子百分比上限再取小一个量级, 即β = 0.0003%. 作出该典型工况下, 温度T对杂质气体分压上限pr的函数关系图, 如图2所示.
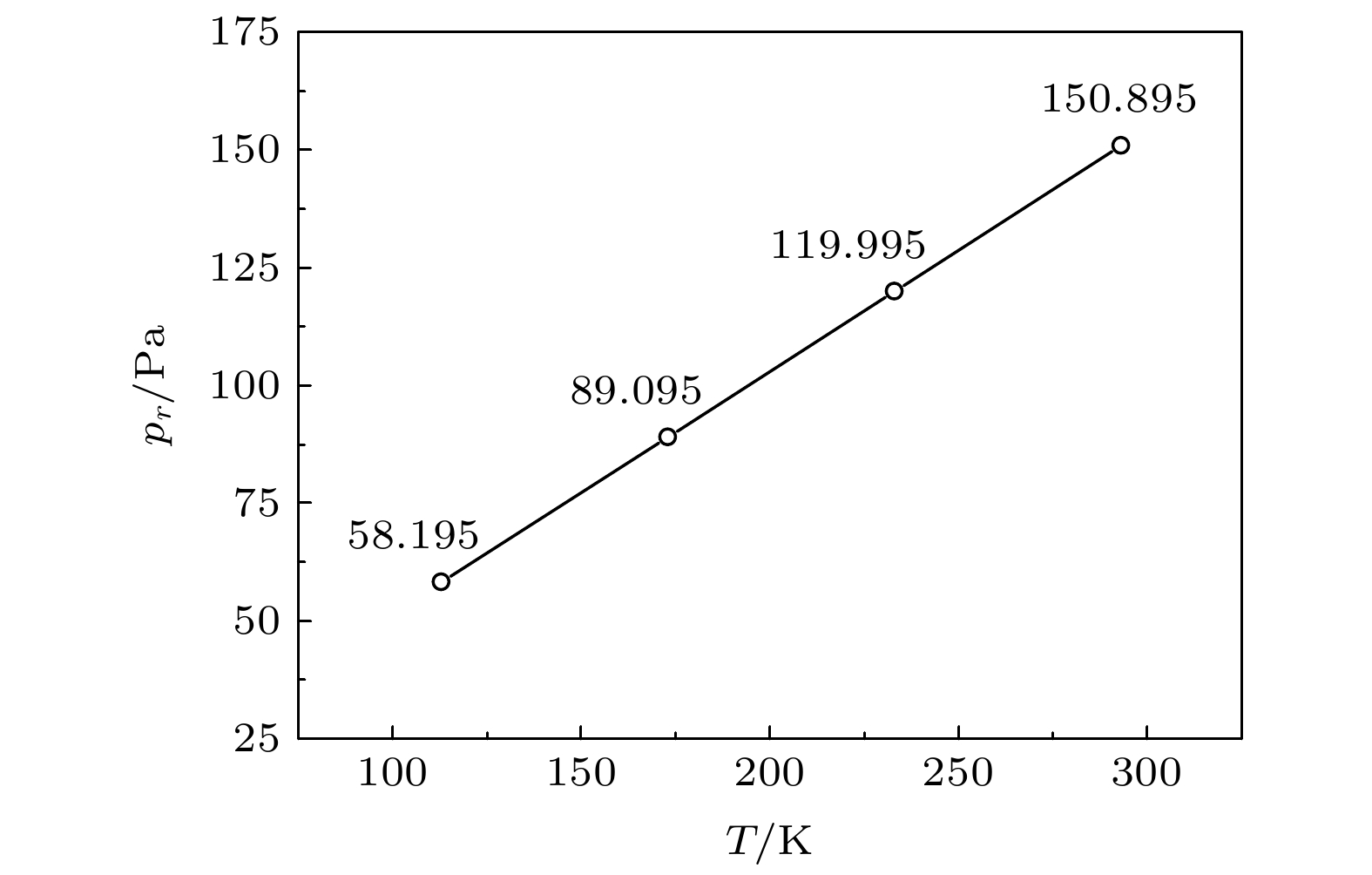
Figure2. Influence of temperature in target on upper limit of impurity gas pressure.
由图2可知, 当靶内温度值取29, 233, 173与113 K时, 其杂质气体残余压力上限分别为151, 120, 90与60 Pa, 也就是说, 低温引起的杂质气压上限变化分别为20.5%, 40.4%与60.3%. 但是, 由于温度降低, 气体黏度减小, 导致流洗阻力减小, 可提高流洗效率. 所以, 可以考虑通过低温流洗策略进行杂质气体的抽空, 影响最终流洗时间长短的关键在于杂质气压上限降低所增加时间与气体黏度降低所减少时间的相对大小.
2
2.2.微通道气体流域分析
实际上, 与低温靶黏接的部分微管直径较小, 而远离靶丸后, 使用直径较大的铜管与微管黏接. 这里以2—10 μm直径的微管为基础, 讨论低温靶气体流洗问题.因为靶丸抽空流洗所用毛细管为微米级微管, 在该尺寸影响下, 微通道内的气体流动行为与常见连续流体有所差别. 通常依据气体分子自由程与特征尺寸的相对大小, 作出气体流动领域划分, 以反映不同领域内分子运动机理. Karniadakis等[25]利用克努森数Kn作出以下划分, 即当Kn < 0.001, 连续流流域; 当0.001 < Kn < 0.1, 滑移流流域; 0.1 < Kn < 10, 过渡流流域; Kn > 10, 分子流流域. 依据克努森数的定义与气体分子平均自由程计算式, 求得气体临界压力:
据式(4)作出T = 293 K时空气与氢气在微米级管道中流域的转换图, 如图3所示. 由该图可知, 2—10 μm直径的微管内空气与氢气的连续流与滑移流转变压力均在101.325 kPa以上. 因此, 考虑抽空端压力为100 Pa时, 将靶内空气压力抽空至较低中间压力p1(过渡流压力下限以上), 再充注氢气至101.325 kPa, 并在100 Pa低压下继续反复流洗, 以达到降低杂质气体含量的效果. 其具体流程如图4所示. 需要注意的是, 由于充注燃料气体过程所需时间与流洗所需时间相比较短, 计算过程不予考虑.
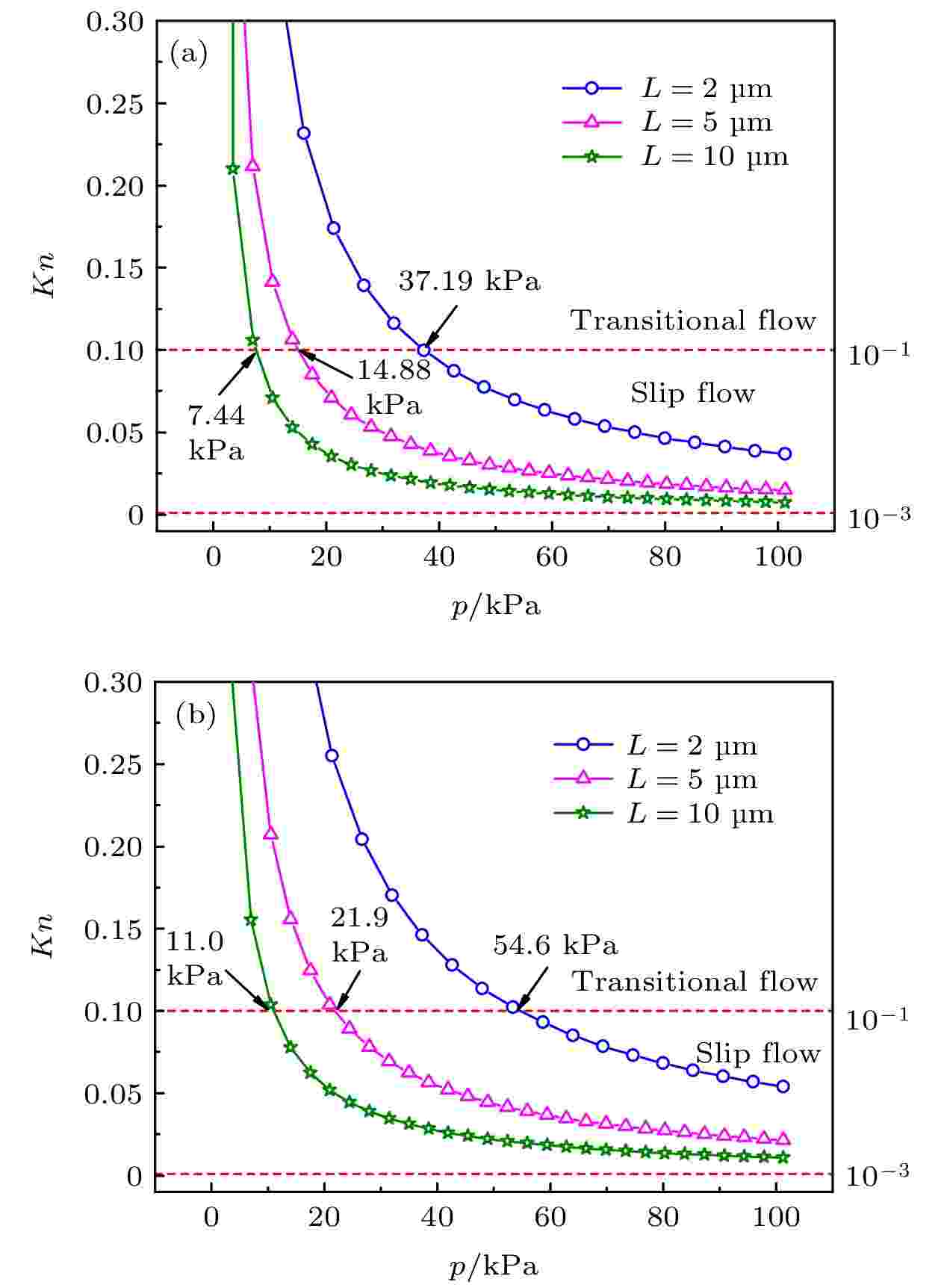
Figure3. Conversion chart of gas flow field: (a) Conversion chart of air flow field; (b) conversion chart of hydrogen flow field.

Figure4. Flow chart of target filling and evacuating.
2
2.3.模型有效性验证
建立如图5所示的低温靶抽空流洗物理模型, 使用低温胶将靶丸与微管一端黏接, 微管另一端连接低压端与燃料端; 靶丸内径为d, 微管长度为L1, 直径为D. 模拟过程中, 认为流洗过程中气体温度不变, 且不考虑靶壳厚度与微管壁厚度.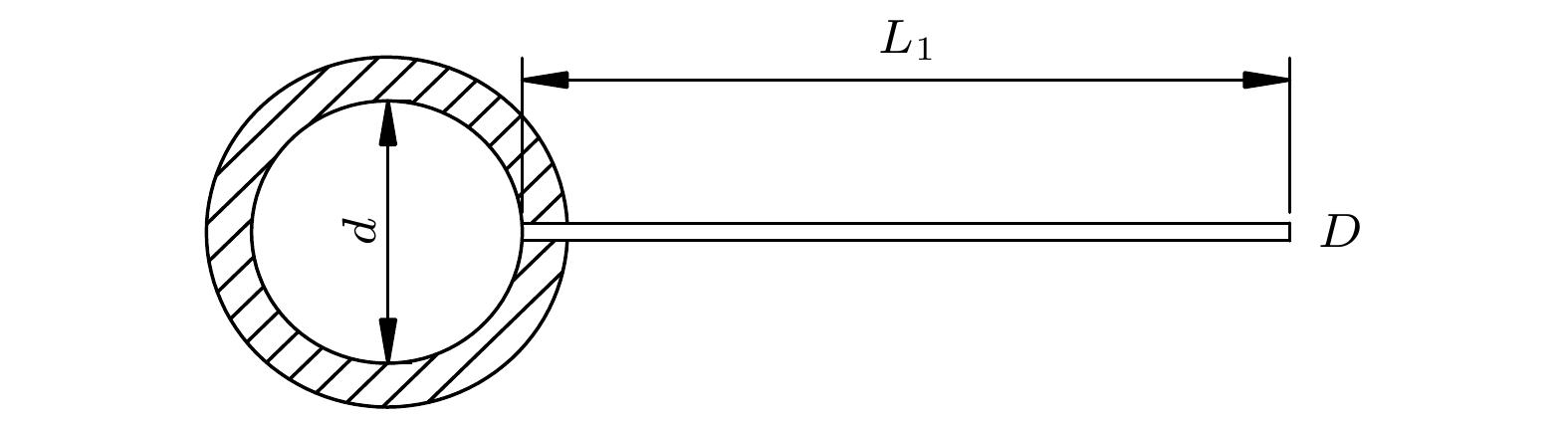
Figure5. The physical model of target filling and evacuating.
在数值计算中, 考虑气体滑移、气体密度与黏度变化、气体比例输入, 添加了滑移流场、化学场与浓物质传递场. 基本控制方程为连续性方程、动量守恒方程与传质方程.
建立低温靶在100 Pa低压下的流洗模型, 以靶内压力降至某中间压力的时间t作为判断物理量, 进行了网格无关性验证; 同时为保证所建立物理模型的有效性, 以直径5 μm、长度20 mm微管为例(低压端95 kPa、中间压力96 kPa), 将模拟结果与计算模型比较. 计算模型是小压差条件下, 考虑气体可压缩与速度滑移的Hagen-Poiseuille方程[26-27]





图6是模拟结果与计算结果的误差比较图. 由图可知, 靶内气压从101.325 kPa降至96 kPa, 模拟结果与模型结果偏差均在5.9%以内, 且随着靶内压力降低(微管两端压差越小, 越满足小压差条件), 偏差越小. 因此, 所建立的滑移流模型基本与实际情况相符, 可用于模拟计算.
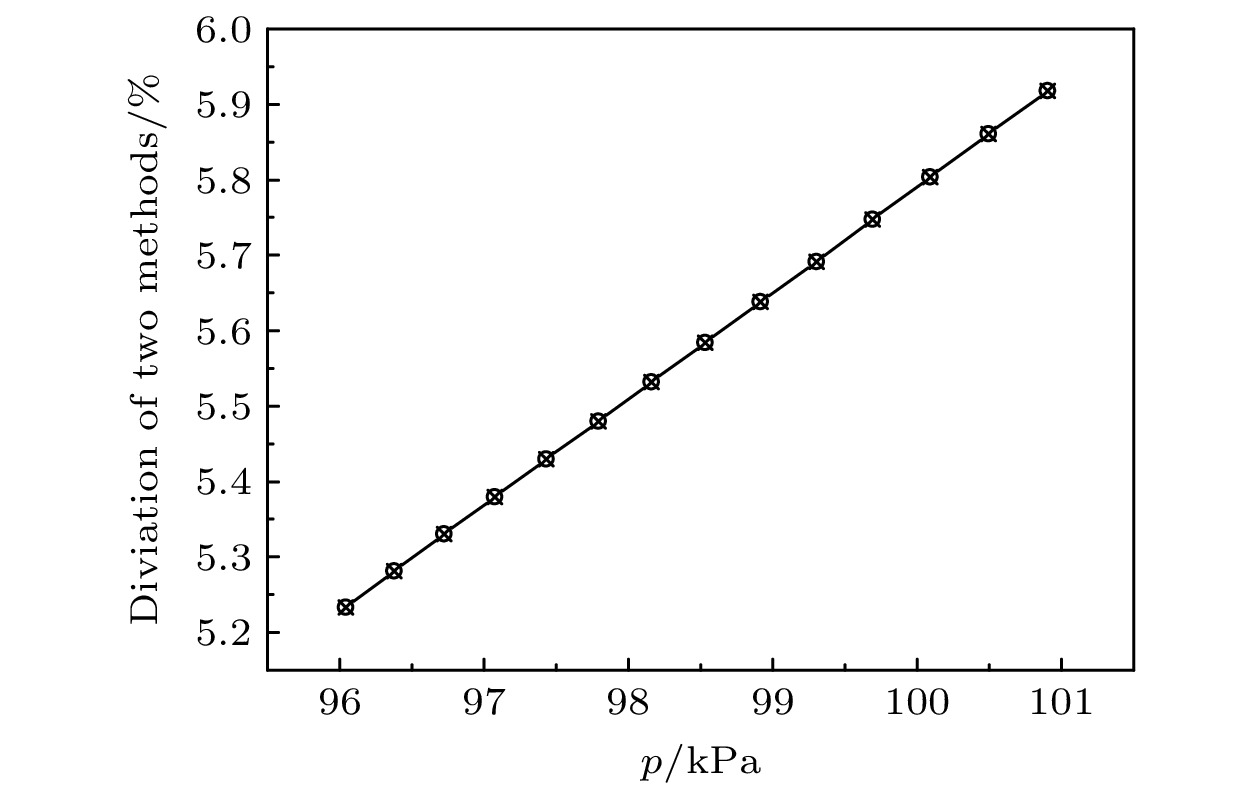
Figure6. Deviation between simulation and formula.
2
3.1.微管长度对流洗时间的影响
取p1 = 56 kPa, D = 5 μm, L1分别为5, 20, 35与50 mm的微管, 对低温靶内气体总压与残余杂质气体分压变化进行了计算. 典型结果如图7所示, 其微管长度50 mm. 图中总压p(实线)每升高一次, 即表示完成一次杂质气体抽空流洗, 并进入下一次流洗阶段. 该图表明, 随着流洗次数增加, 靶内分压pr(虚线)随之减小, 当流洗次数到达11次时, 靶内分压pr降低到0.15 kPa, 达到流洗要求. 但计算表明, 对于更短的管长(5—35 mm), 其流洗次数基本都为11次; 这是因为滑移流流域内, 气体不发生分馏效应, 只要初始压力与中间压力一致, 流洗完成时各组分分压相同.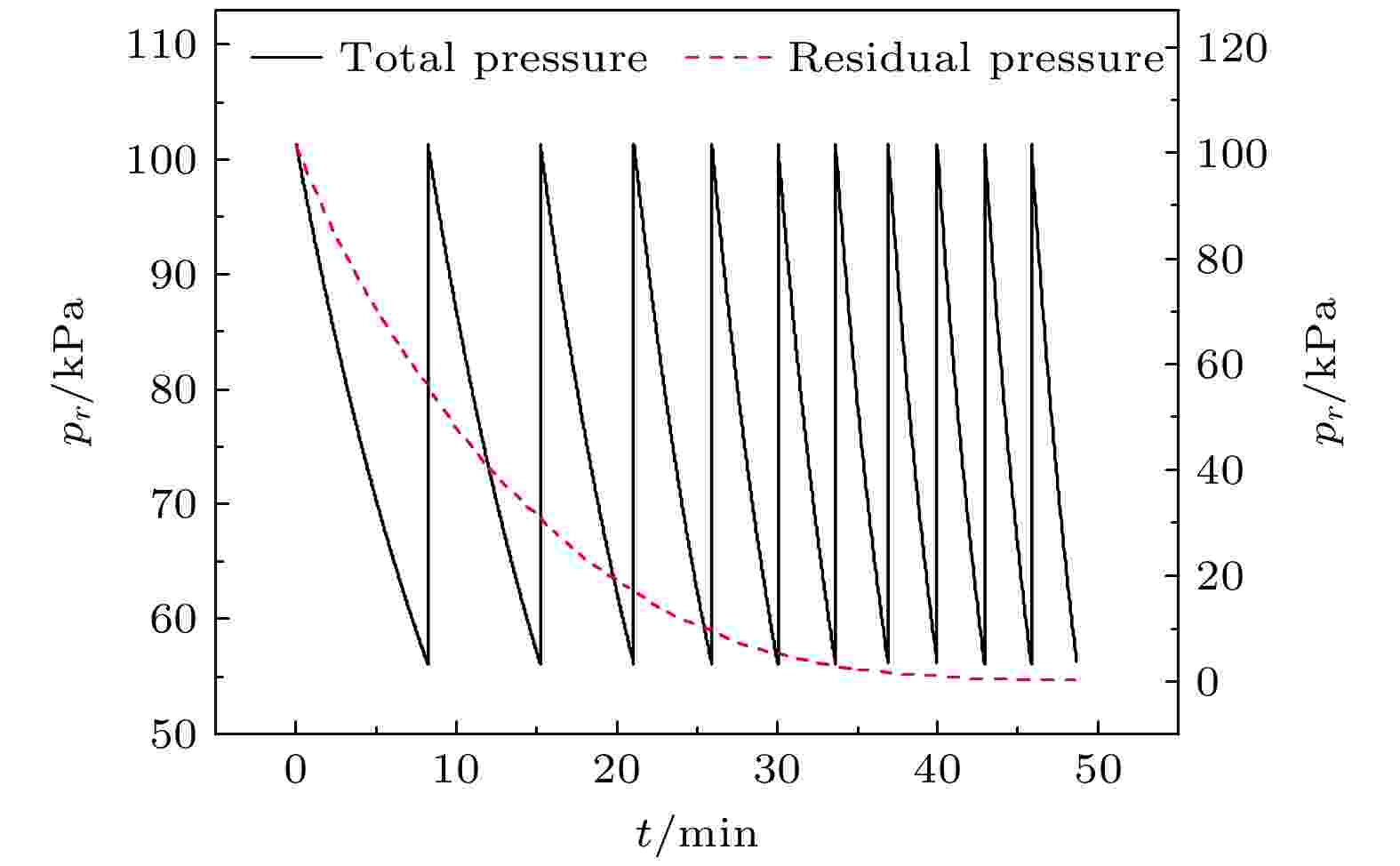
Figure7. Variation of total pressure and residual pressure in cryogenic target capsule.
虽然不同管长的流洗次数基本相同, 但流洗时间是不一样的, 这种影响见图8. 该图是不同微管长度下, 靶丸内残余杂质气体分压随时间的变化曲线. 结合计算结果, 4种微管长度下(5, 20, 35与50 mm)的总流洗时间分别为585, 1752, 2447与2919 s. 也就是说, 以L1 = 50 mm微管的流洗时间为基准, 采用35, 20和5 mm长的微管流洗时, 将节省约16%, 40%与80%的流洗时间. 其原因是微管长度减小引起管道阻力降低, 进而造成抽气速率增大.
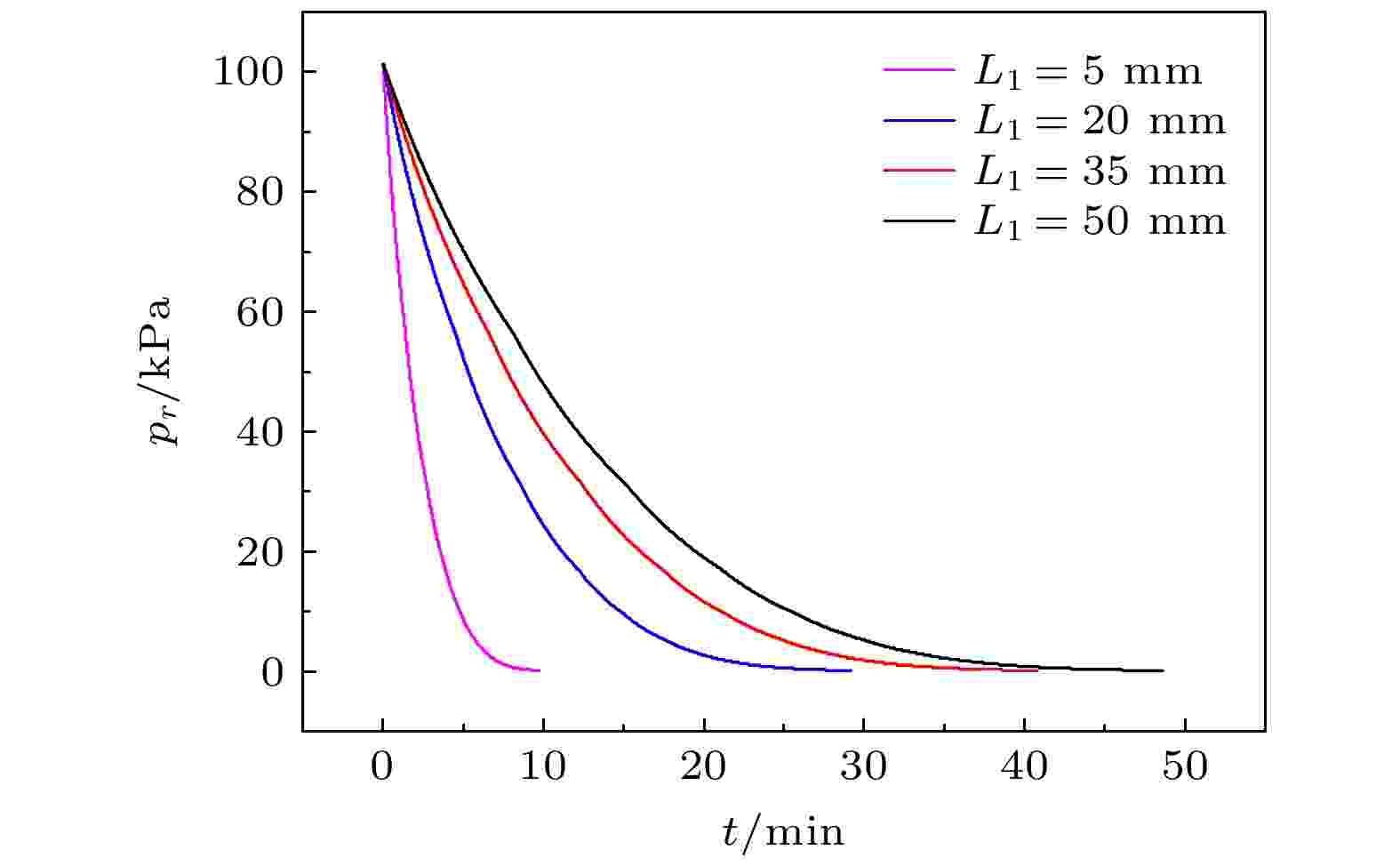
Figure8. Variation of residual pressure at different capillary length.
图9是不同微管长度下, 单次抽空流洗时间的变化曲线. 由图可知, 流洗次数相同时, 管长越长, 该次流洗时间也将增长, 其原因亦为管道阻力的影响. 同时, 对同一管长, 单次流洗时间随着抽空流洗次数的增加而降低, 最终趋于平稳. 这是由于空气与氢气相比, 黏度更大, 流动阻力也相应增大, 导致流洗时间更长; 随着氢气比例的增大, 气体黏度将逐渐向氢气黏度靠近, 流洗时间降低, 最终因氢气成为靶内气体主导成分, 单次流洗时间基本不变.
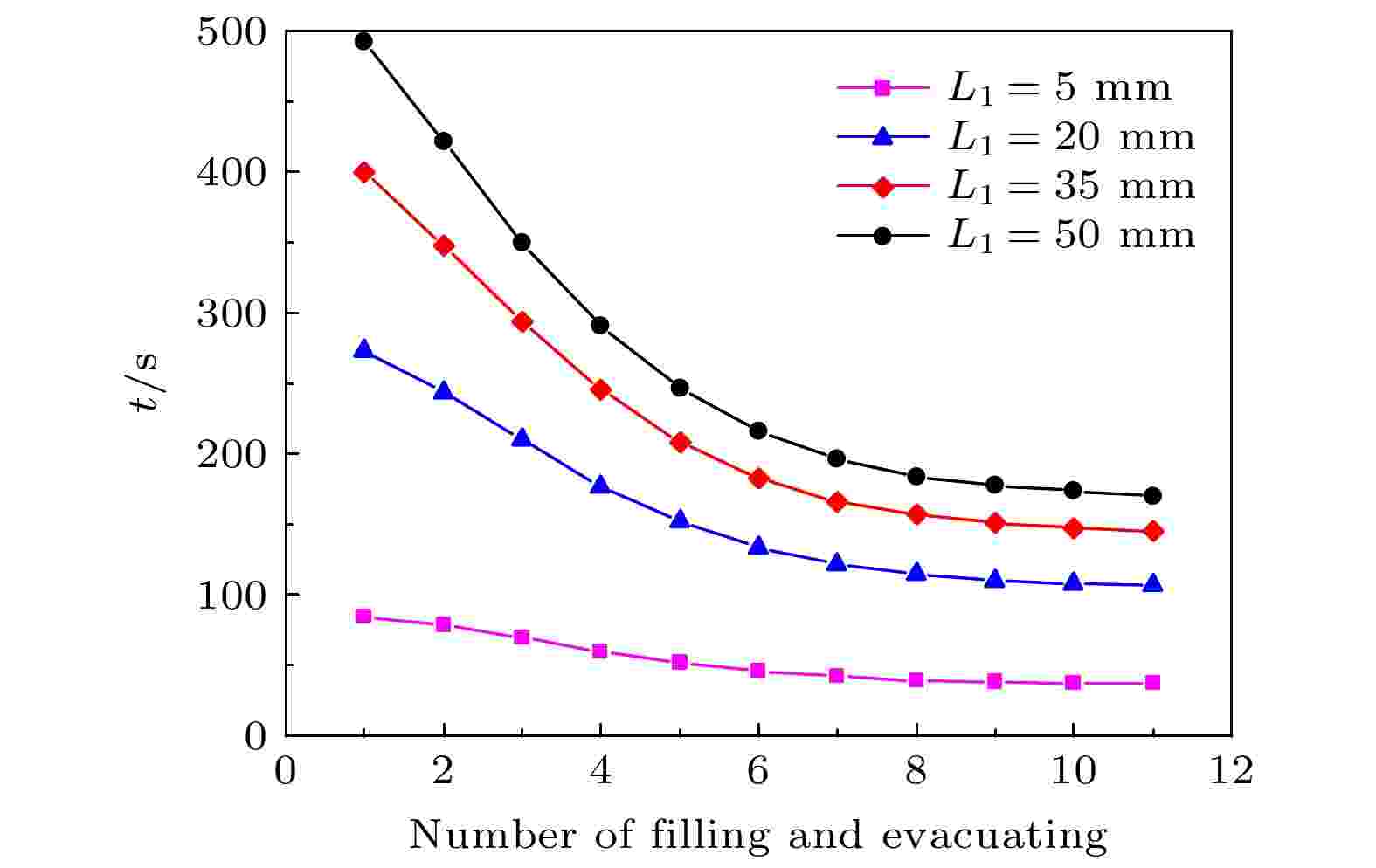
Figure9. Variation of single filling and evacuating time at different capillary length.
2
3.2.微管直径对流洗时间的影响
由对微管长度影响的讨论可知, 在保证低温靶靶体强度的情况下, 为提高低温靶抽空流洗效率, 小直径微管应尽量短. 因此, 取p1 = 56000 Pa, L1 = 20 mm, 直径D分别为2, 4, 6与8 μm的微管, 研究微管直径对流洗时间的影响.图10是不同微管直径下, 靶内杂质残余压力随时间的变化曲线. 当直径为2, 4, 6和8 μm时, 流洗总时间分别为5478, 2925, 1061和397 s. 以D = 2 μm的流洗时间为基准, 采用4, 6和8 μm直径微管流洗时, 将节省约46%, 80%和93%的流洗时间. 其原因是, 微管直径增大引起管道阻力减小, 流洗速率变快. 图11是不同微管直径下, 单次流洗时间的变化曲线. 显然, 单次流洗时间随抽空流洗次数的增加而减小, 最终趋于平稳. 其原因与不同微管长度下, 单次流洗时间变化的原因一致.
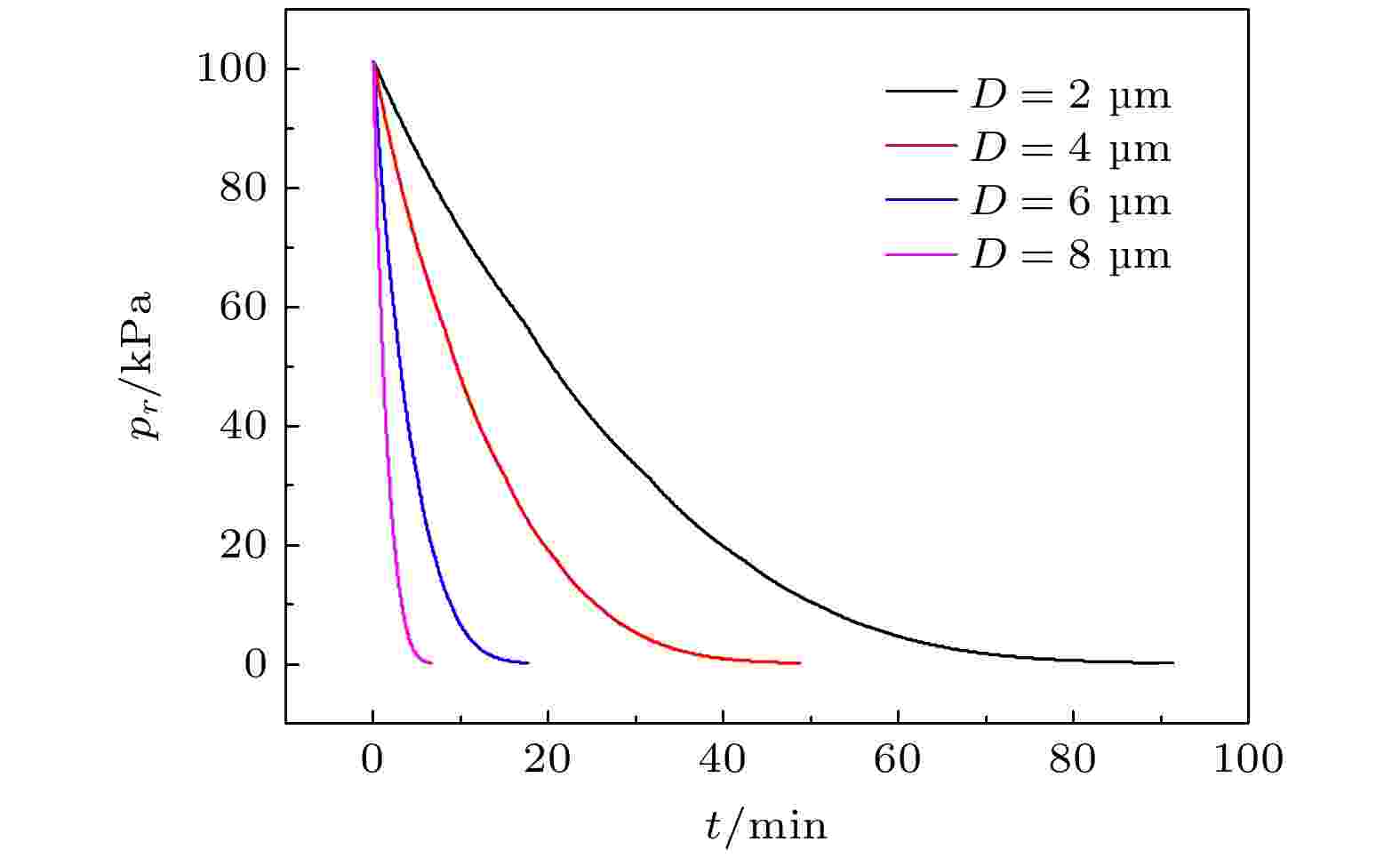
Figure10. Variation of residual pressure at different capillary diameter.
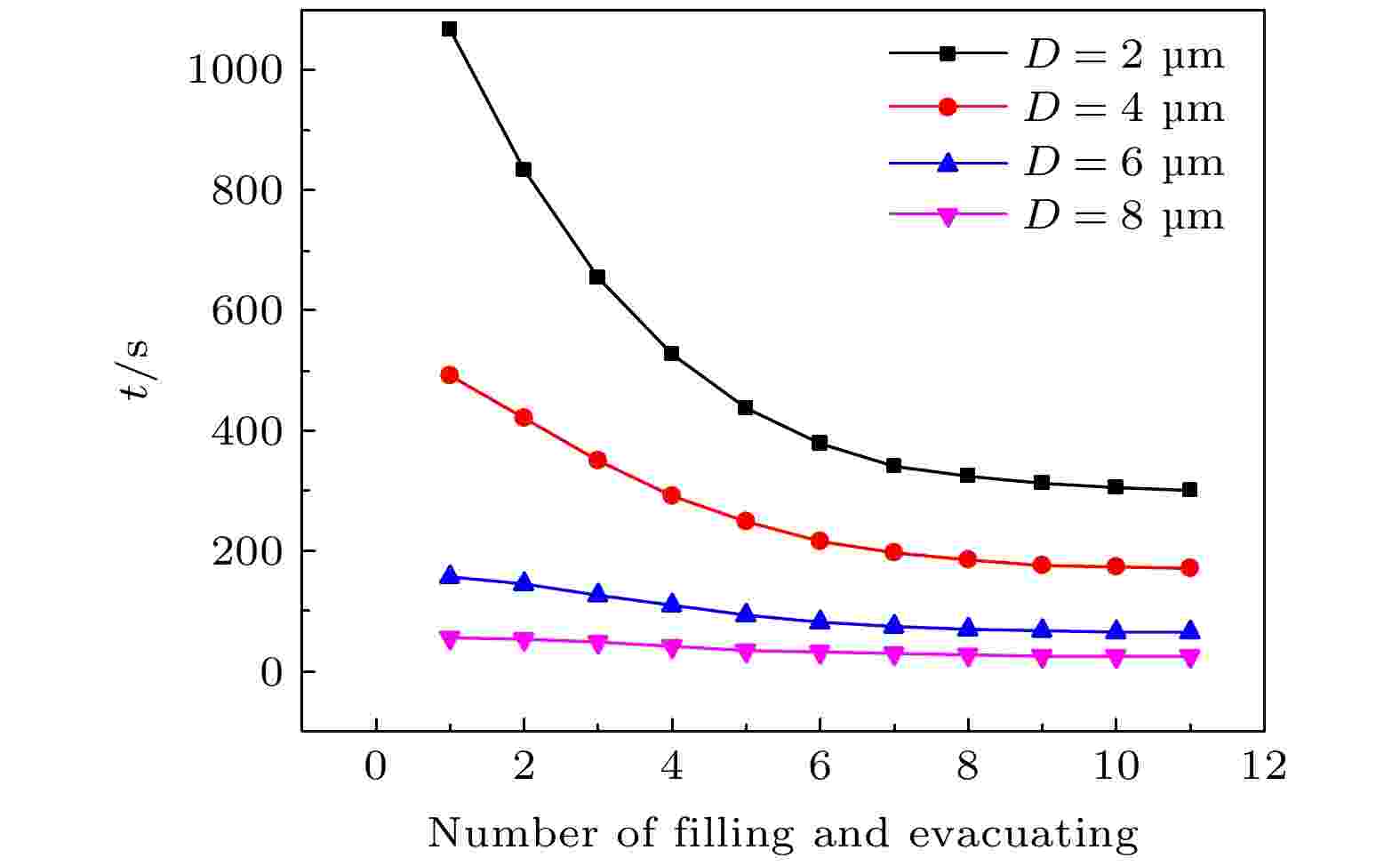
Figure11. Variation of single filling and evacuating at different capillary diameter.
2
3.3.微管管型对流洗时间的影响
依据微管尺度对流洗效率的影响, 结合聚变动力学稳定性的要求, 提出以下几类管型进行模拟, 其纵截面形式如图12所示, 其中间压力均为p1 = 56 kPa. ①内径为4 μm、长度20 mm的均直圆管; ②前半段为内径4 μm、长度5 mm的均直圆管, 后半段为内径8 μm、长度为15 mm的均直圆管; ③第一段是内径4 μm、长度2 mm的均直圆管, 第二段是入口直径4 μm、出口内径8 μm、长度为3 mm的圆锥管, 第三段是内径为8 μm, 长度是15 mm的均直圆管; ④前半段是入口内径为4 μm、出口内径8 μm、长度为5 mm的圆锥管, 后半段为内径8 μm、长度为15 mm的均直圆管.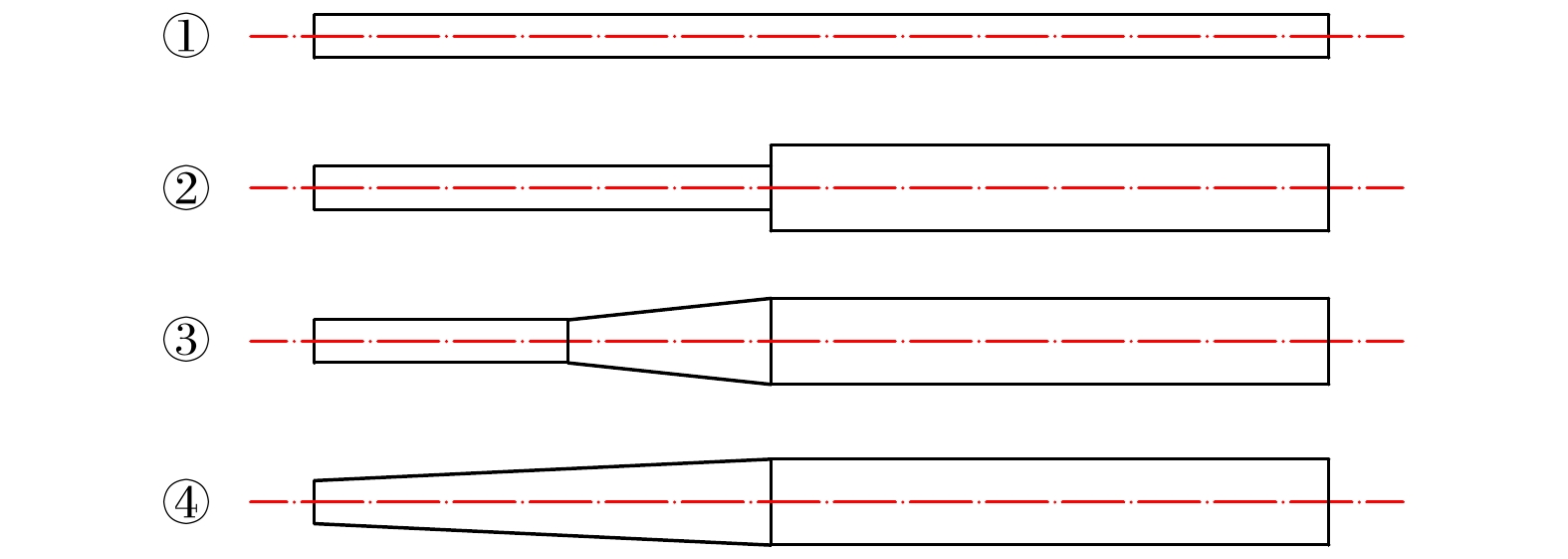
Figure12. Schematic of capillary form.
图13是不同管型下, 残余气体压力随时间的变化图. 根据计算结果, 管型①②③④的抽空流洗时间分别为2925 s, 1608 s, 1020 s与738 s. 管型④既考虑了内爆稳定性要求, 又将抽空流洗时间在4 μm均直管基础上降低了75%. 因此, 可使用管型④作为低温靶微管的最佳形式.
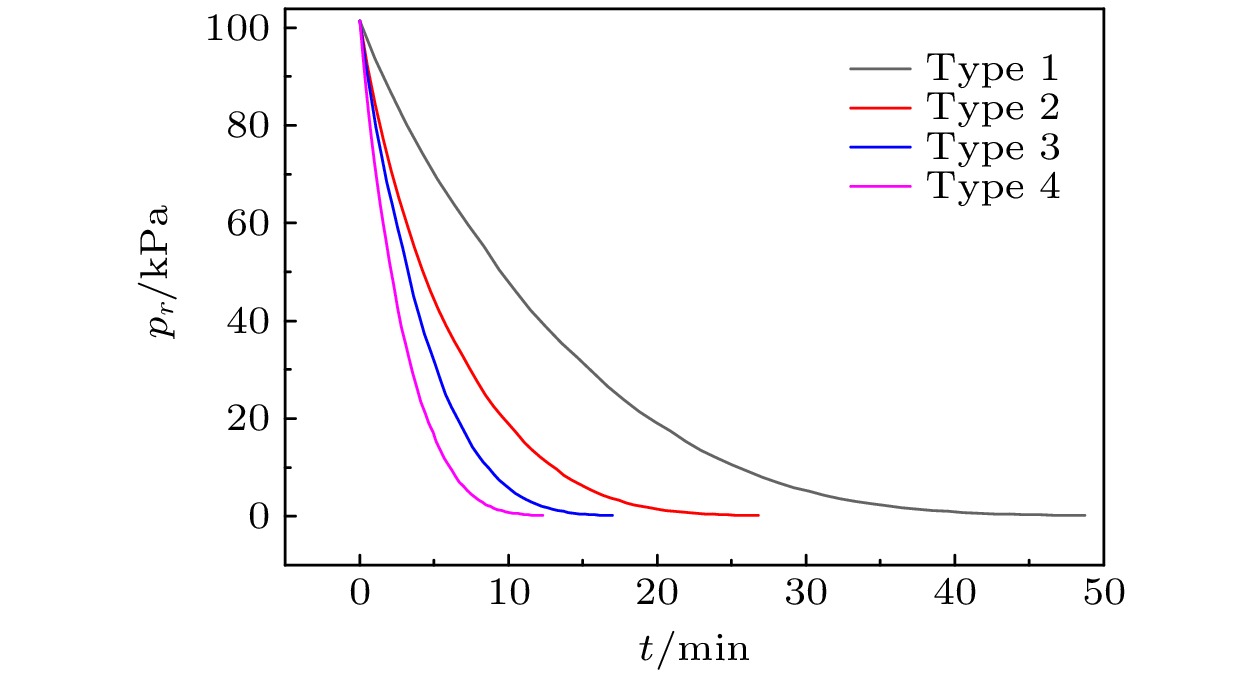
Figure13. Variation of residual pressure at different tube type.
此外, 从本质上说, 管型对流洗效率的影响仍然可以归结到直径对流洗效率的影响. 均直管型①直径为4 μm, 相比较于后半段直径为8 μm的管型, 阻力较大, 因而效率较低. 同时由于圆锥管又可以等效为半径为R的均直圆管[12], 其计算式为
因此, 据式(6)可知, 管型②的阻力必然大于管型③与管型④的阻力, 而管型④的阻力最小, 流洗效率也较大.
2
3.4.最佳流洗中间压力的确定
当微管低压端保持100 Pa时, 低温靶内气压不断下降至中间压力p1. 当中间压力越小时, 气体驱动力也将越小, 而单次流洗时间越长, 次数越少. 若中间压力较高, 其流洗次数必将越多, 真空泵与充气腔间的切换也将增多, 但总时间可能降低. 为解决抽空流洗时间与流洗次数之间的矛盾, 对NIF基准靶在不同中间压力下的流洗进行了计算, 得到了图14的最佳流洗中间压力优化图.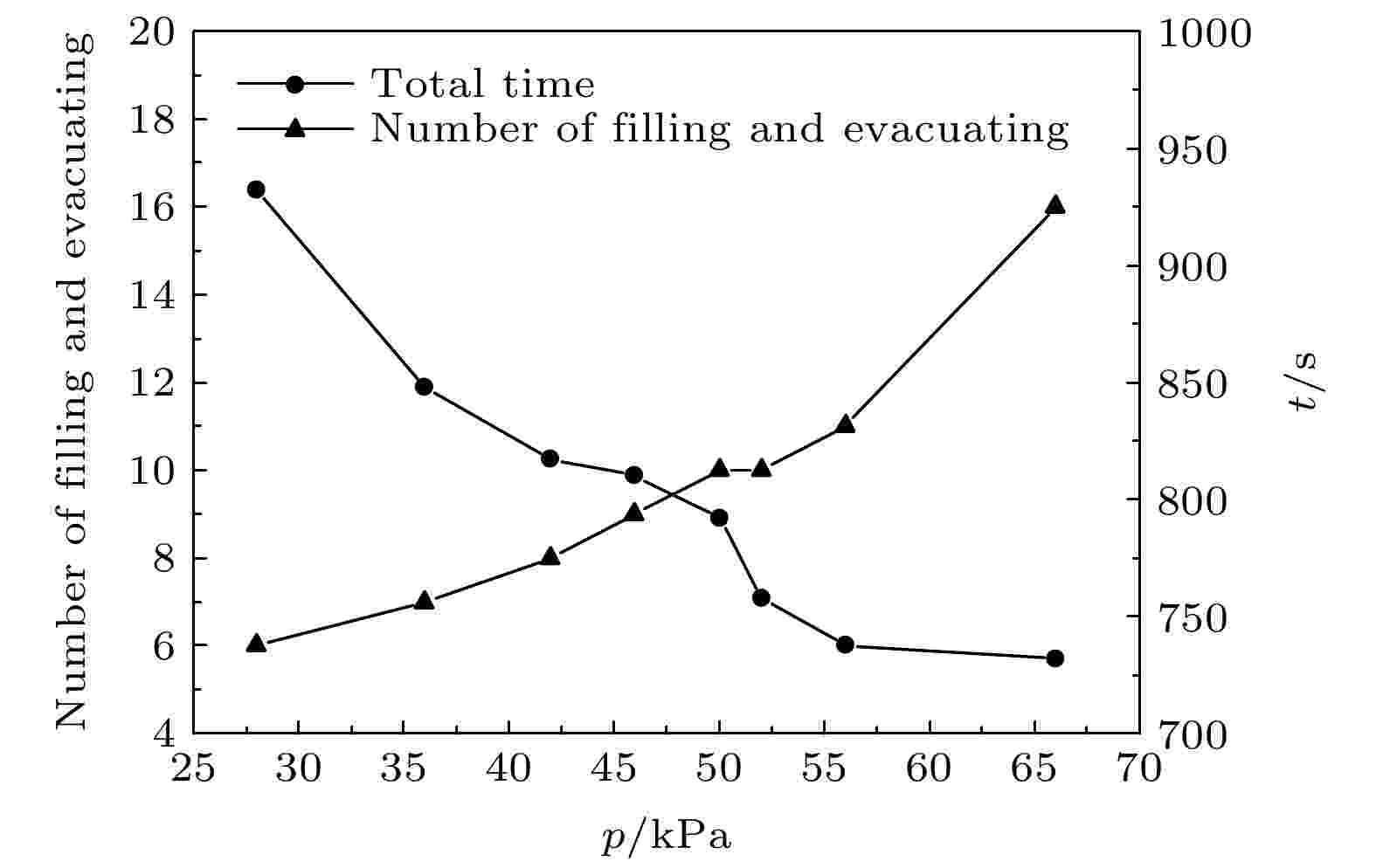
Figure14. Optimization of the optimal intermediate pressure of washing.
从图14可以看出, 当中间压力为52 kPa时, 其流洗次数为10次, 流洗总时间约758 s. 在该中间压力下, 流洗总时间不太长, 且流洗次数也相对较少. 故在常温下, 兼顾流洗效率与流洗次数, 选择最佳流洗中间压力为52 kPa.
2
3.5.温度对流洗时间的影响
如前所述, 低温下气体黏度有所降低, 而残余气体目标压力降低幅度不大, 可以考虑低温流洗提高流洗效率. 这里对低温靶在293, 233, 173及113 K下的杂质气体流洗进行模拟. 注意, 由于温度降低, 低温靶内气压也将降低, 在233, 173与113 K下初始靶内气压分别为80535, 59797, 39058 Pa; 且4种情形下, 抽空流洗次数均为10次.图15是使用管型④进行流洗时, 不同温度对流洗时间的影响变化趋势图. 由该图可以看出, T = 293 K时, 所需流洗时间为758 s. 在233, 173与113 K温度下流洗时, 其流洗总时间分别较293 K时下降13.98%, 32.72%与48.02%. 这表明, 低温下的流洗将极大地提高流洗效率. 实际流洗操作时, 可通过降低燃料气体充注温度和靶丸温度的方式来提高去除杂质气体的效率. 同时, 考虑到实际情况下低温流洗的温度可能低于某些组分(如水蒸气)的三相点, 使其形成冰霜附着在低温靶内壁. 可采取的策略是, 从常温逐步降低至该低温进行流洗, 这样可相对减少水蒸气等组分吸附在低温靶内表面引起的较难抽空的问题.
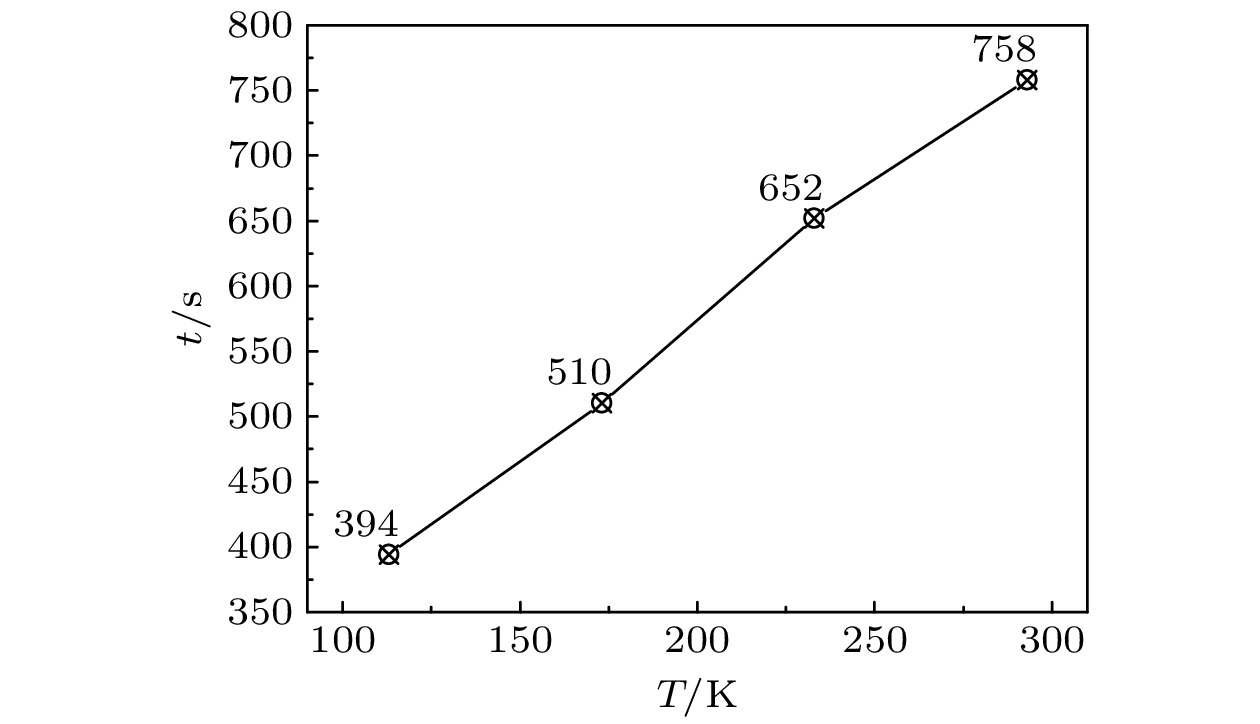
Figure15. Influence of temperature on total filling and evacuating time.