全文HTML
--> --> -->FeAl/Al2O3阻氚涂层的制备可分为两步: 第一步是在一定条件下使基体与铝相互扩散, 获得Fe-Al合金渗层; 另一步是氧化, 即对基体表面Fe-Al合金层进行氧化, 获得致密的Al2O3膜层. 由于氧化过程是在Fe-Al合金渗层上进行的, 因此渗层的表面形貌及组织结构对Al2O3膜层的质量有重要的影响. 研究表明, 渗层的制备过程受多种因素影响. 袁晓明等[11]采用粉末包埋法在RAFM钢基体上制备Fe-Al渗层, 发现在750 ℃时钢表面出现渗铝剂颗粒烧结现象, 在650 ℃时, 渗层生长不完整且存在较多孔洞, 而在700 ℃下可获得致密完整的Fe-Al渗层. Parushothman等[12]研究了热浸铝中熔融态铝内的Si元素含量及浸泡温度对渗层的影响, 发现Fe-Al合金渗层的厚度随铝熔液中Si元素含量的增大而减小, 同时Si含量为1%, 6%和11%铝溶液中获得的涂层中平均缺陷密度分别为21%, 11%和3%. Chen等[13]也发现了在CLAM钢基体表面热浸铝过程中, 外层Al涂层的厚度随着浸泡温度和时间的变化不明显, 而内层Fe-Al合金层厚度随浸泡温度和时间的提升显著增大. 可见, 合理的互扩散条件(温度、时间、铝源成分及状态等)是获得均匀致密的Fe-Al合金渗层的关键.
离子液体电镀具有镀层厚度可控、绕镀性好、工艺简单和经济安全等优点, 近年来在制备FeAl/Al2O3阻氚涂层上备受关注[4,10,14-16]. 中国工程物理研究院Zhang等[15,16]采用“离子液体电镀铝+热处理+选择氧化”技术路线, 经过系统的工艺优化研究在奥氏体钢表面制备阻氚性能良好的FeAl/Al2O3涂层, 600—727 ℃涂层的氘渗透率降低了2—3个数量级. Krauss等[4]分别采用有机质子惰性电解质和离子液体两种电镀体系在Eurofer钢表面镀铝, 发现离子液体体系下获得的铝涂层晶粒更细小, 表面更加光滑. 热处理后的样品在液态Pb-15.7Li (550 ℃, 0.1 m/s)中暴露12000 h仍能保护基体免受腐蚀, 径向腐蚀速率为10—20 μm/a. 本文采用离子液体电镀法在CLAM钢基体上制备铝镀层, 再通过热处理使基体中的Fe原子与镀层中的Al原子相互扩散反应, 获得均匀致密的Fe-Al合金渗层, 重点探讨了不同热处理温度和时间对Fe-Al合金层形貌和组织结构的影响.
2.1.铝镀层制备
电镀在氮气保护气氛的手套箱内进行. 电镀阳极采用纯度为99.999%的铝丝, 螺旋放置于电镀槽内, 经磷酸、无水乙醇超声清洗并干燥后移入手套箱内. 阴极材料为CLAM钢试样, 尺寸为Φ20 × 1 mm. CLAM钢的化学成分如表1所列. CLAM钢试样经砂纸打磨, 丙酮、无水乙醇超声清洗后干燥, 移入手套箱内待用. 采用摩尔比为AlCl3∶EMIC=2∶1混合溶液作为电镀液.Cr | W | V | Ta | Mn | C | Si | Fe |
9.00 | 1.50 | 0.20 | 0.07 | 0.45 | 0.10 | 0.01 | Bal |
表1CLAM钢的化学成分(wt%)
Table1.Chemical composition of CLAM steel (wt%).
在电镀前对CLAM钢试样进行电化学前处理, 去除试样表面的钝化层, 使镀层与基体直接接触, 保障良好的镀层质量. 前处理电流密度为15 mA/cm2, 时间15 min. 电镀参数如下: 电流密度为10 mA/cm2, 时间96 min, 此参数下的铝镀层理论厚度为20 μm. 为消除浓度差极化, 电镀过程使用恒温磁力搅拌器搅拌离子液体.
2
2.2.热处理
镀铝后的CLAM钢试样转移至快速升温管式电炉内在空气气氛中进行热处理, 制备Fe-Al合金渗层. 具体热处理参数列于表2中. 试样经30 min升温至所需温度并保温相应时间, 后随炉冷却.1 | 2 | 3 | 4 | 5 | 6 | 7 | 8 | |
Temperature/℃ | 640 | 640 | 640 | 700 | 700 | 760 | 760 | 760 |
Annealing time/h | 4 | 20 | 50 | 4 | 10 | 4 | 10 | 20 |
表2热处理条件
Table2.Annealing condition.
热处理完毕, 通过扫描电子显微镜(SEM)观察试样表面和截面形貌, 利用能量散射谱仪(EDS)获取Fe-Al合金渗层元素浓度分布信息. 使用X射线衍射谱仪(XRD)分析试样表面的物相结构. 通过对比EDS和XRD的测试结果, 结合Fe-Al合金二元相图分析样品截面的相组成.
3.1.铝镀层的形貌
在铝镀层理论厚度均为20 μm的情况下, 电镀电流密度分别为10 mA/cm2和15 mA/cm2获得的镀层表面及截面形貌如图1所示. 图1(b)中界面处形成了白色线条是由于SEM扫描时发生了二次电子边缘效应. 该现象可能是因为样品膜基结合力较差或镀层与基体硬度差异较大所导致. 由SEM结果分析, 不同电镀电流密度下的试样均无漏镀现象, 表面铝晶粒呈柱状生长. 借助Image J软件对不同电镀电流密度下的镀层在放大500倍的SEM图像中进行了统计分析. 当电镀电流密度为15 mA/cm2时, 铝镀层平均颗粒尺寸为6.4 μm, 明显小于电镀电流密度为10 mA/cm2条件下铝镀层的平均颗粒尺寸(12.8 μm). 这是由于在一定电镀电流密度范围内, 电流密度越大, 基体表面生长点多, 吸附原子扩散距离短, 形核更快; 同时大电流使基体表面吸附原子浓度增大, 易聚集使得晶核形成概率更大, 晶核生长速度快, 因此晶体尺寸小.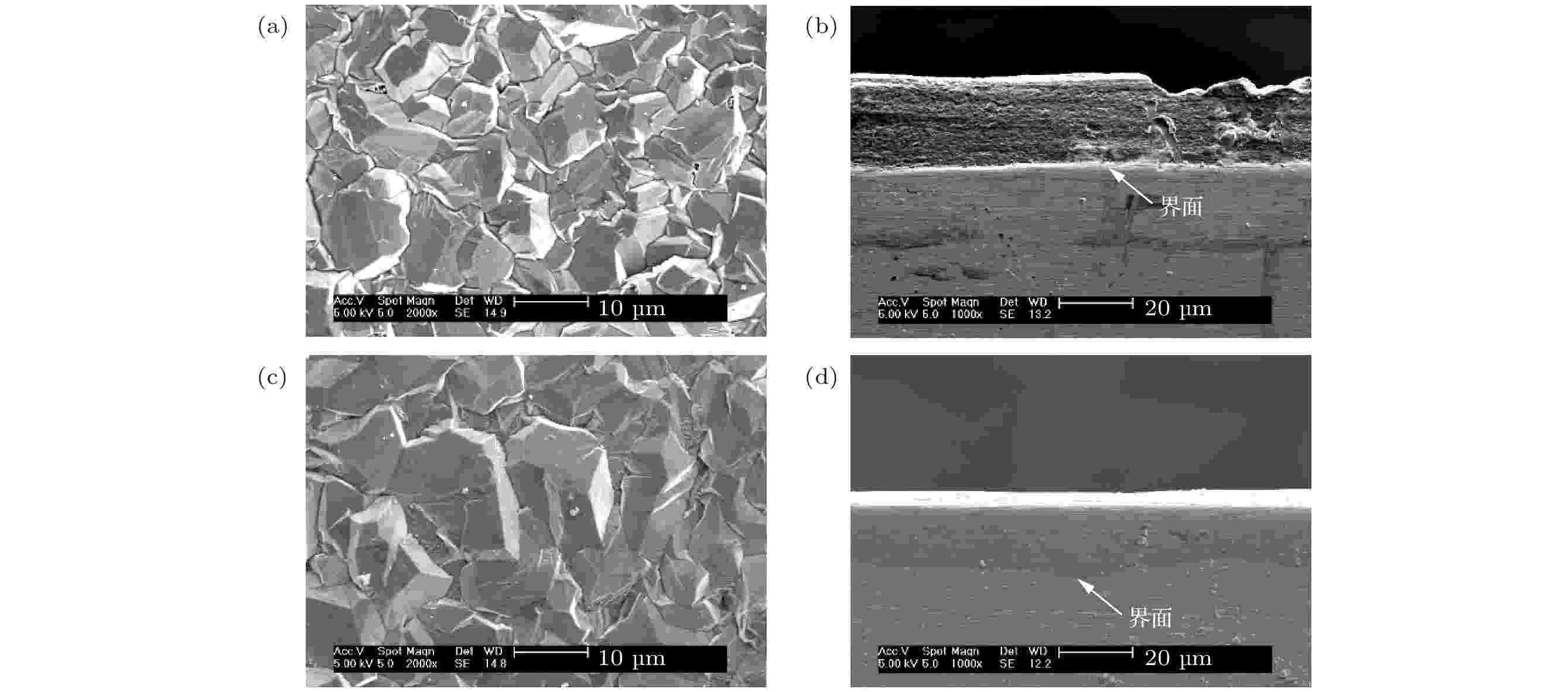
Figure1. Surface (a), (c) and cross-sectional (b), (d) SEM micrographs of aluminum coatings under different electroplating parameters: (a), (b) Current density is 15 mA/cm2, 68 min; (c), (d) current density is 10 mA/cm2, 96 min.
电化学前处理后, 一方面去除了试样表面的钝化层, 使铝镀层与基体直接接触, 保障镀层的结合质量. 另一方面, 从镀层的截面形貌上看, 前处理后的基体表面呈起伏状, 使得铝镀层与基体接触面积增大, 也有利于增强膜基结合力[17]. 电镀电流密度为10 mA/cm2下的镀层与基体界面间无缺陷, 结合更紧密.
图2所示的XRD分析结果表明, 在基体表面形成了纯铝涂层, 其中(200)面衍射峰(2θ = 44.801)强度显著, 说明了电镀过程中, 铝涂层具有(200)面择优生长的特性. 张桂凯等[18]曾对电镀铝镀层的织构和形貌进行了系统的研究, 认为镀层的(200)面对离子液体中的Al2

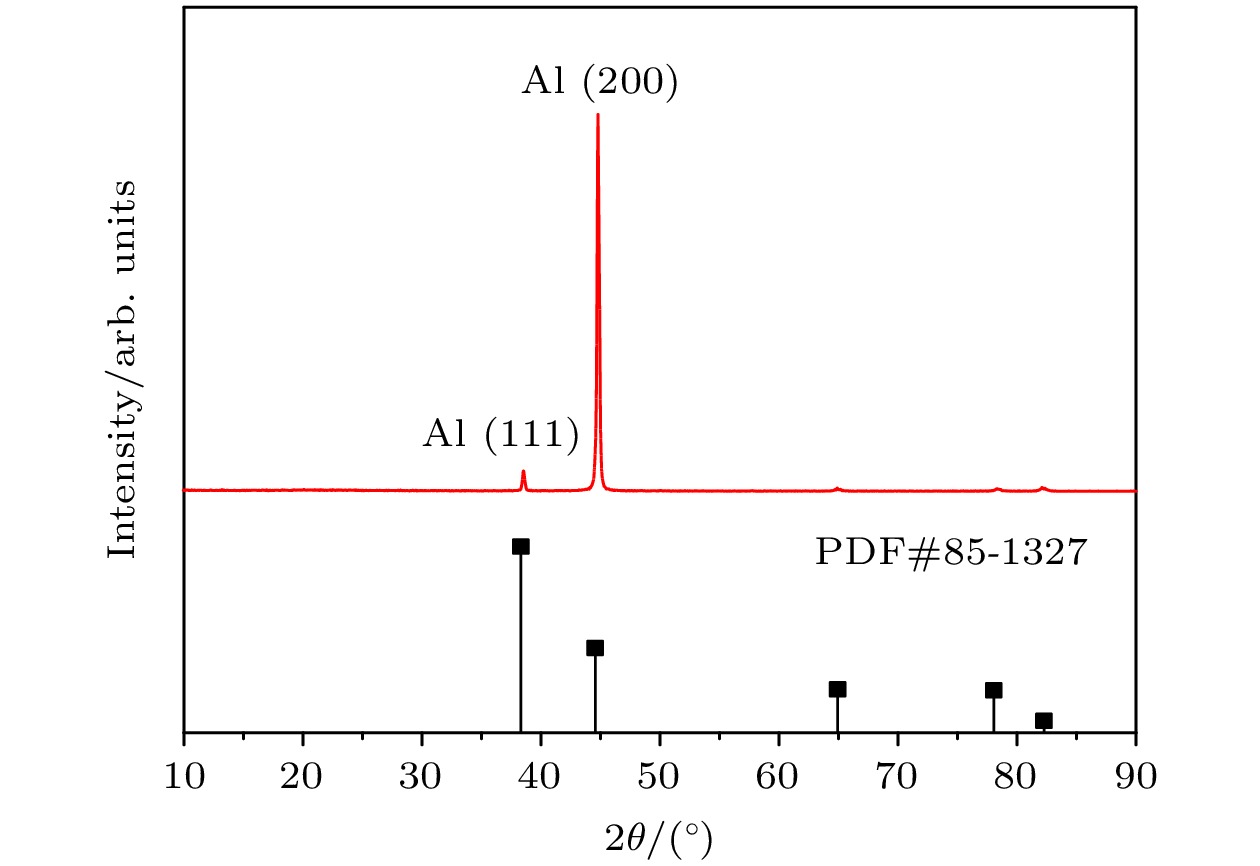
Figure2. XRD patterns of Al coating at 10 mA/cm2.
2
3.2.热处理温度对渗层组织结构的影响
选择在640 ℃, 700 ℃和760 ℃三个温度下分别对试样进行4 h的热处理实验. 640 ℃下试样表面形貌如图3(a)所示, 表面为棱形颗粒状疏松物质, 局部出现脱落. 表3列出了图3(b)中各点的EDS能谱分析结果, 可以看出试样表面棱形颗粒状物质为Al及Al2O3, 剥落处裸露部分为Fe-Al合金, 这说明了基体与铝镀层间已发生扩散. 此温度下Al为固态(Al熔点为660 ℃), 其与基体间的扩散相对缓慢, 因此试样表面存在未参与扩散的Al. 而760 ℃下铝镀层熔化为液态, 试样表面也呈现出明显的熔融状态, 如图3(c)所示.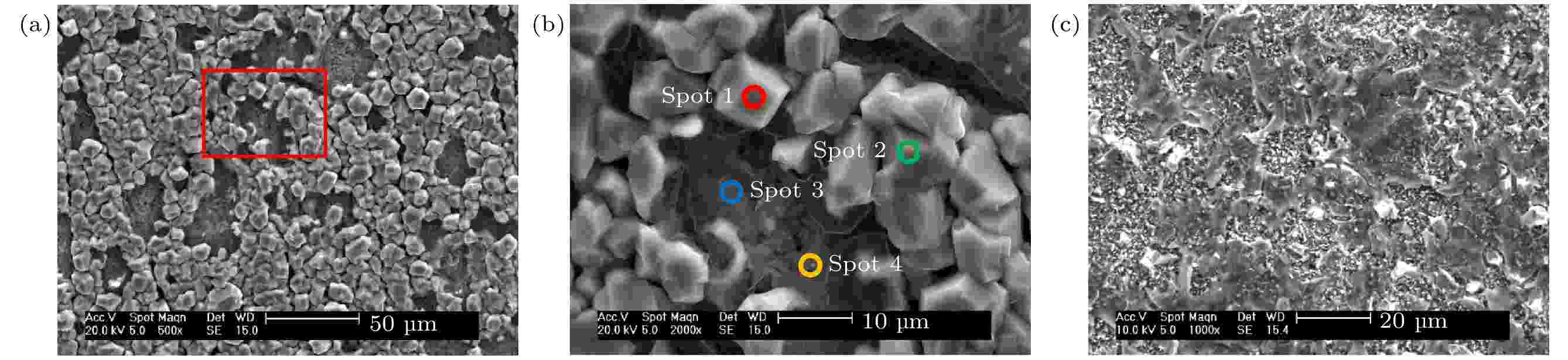
Figure3. SEM micrographs (surface) of samples after annealing for 4 h at different temperatures: (a) 640 ℃; (b) magnification of the red box area in (a); (c) 760 ℃.
Spot | Al K | Fe K | Cr K | O K | Possible |
1 | 95.74 | — | — | 4.26 | Al, Al2O3 |
2 | 89.82 | — | — | 10.18 | Al, Al2O3 |
3 | 58.81 | 16.72 | 1.56 | 22.92 | — |
4 | 57.38 | 16.69 | — | 25.93 | — |
表3640 ℃/20 h下试样表面EDS能谱分析(at%)
Table3.EDS elemental analysis of sample surface at 640 ℃ for 4 h (at%).
图4为厚度为20 μm铝镀层的试样在640 ℃, 700 ℃和760 ℃温度下经过4 h热处理后的截面SEM形貌. 可以看到渗层与基体间无孔洞或间隙, 结合紧密. 结合图4中各试样截面EDS线扫描结果, 发现从表面至基体中心, 渗层中Al原子含量随扫描深度逐渐降低, 而Fe原子含量逐渐增大.
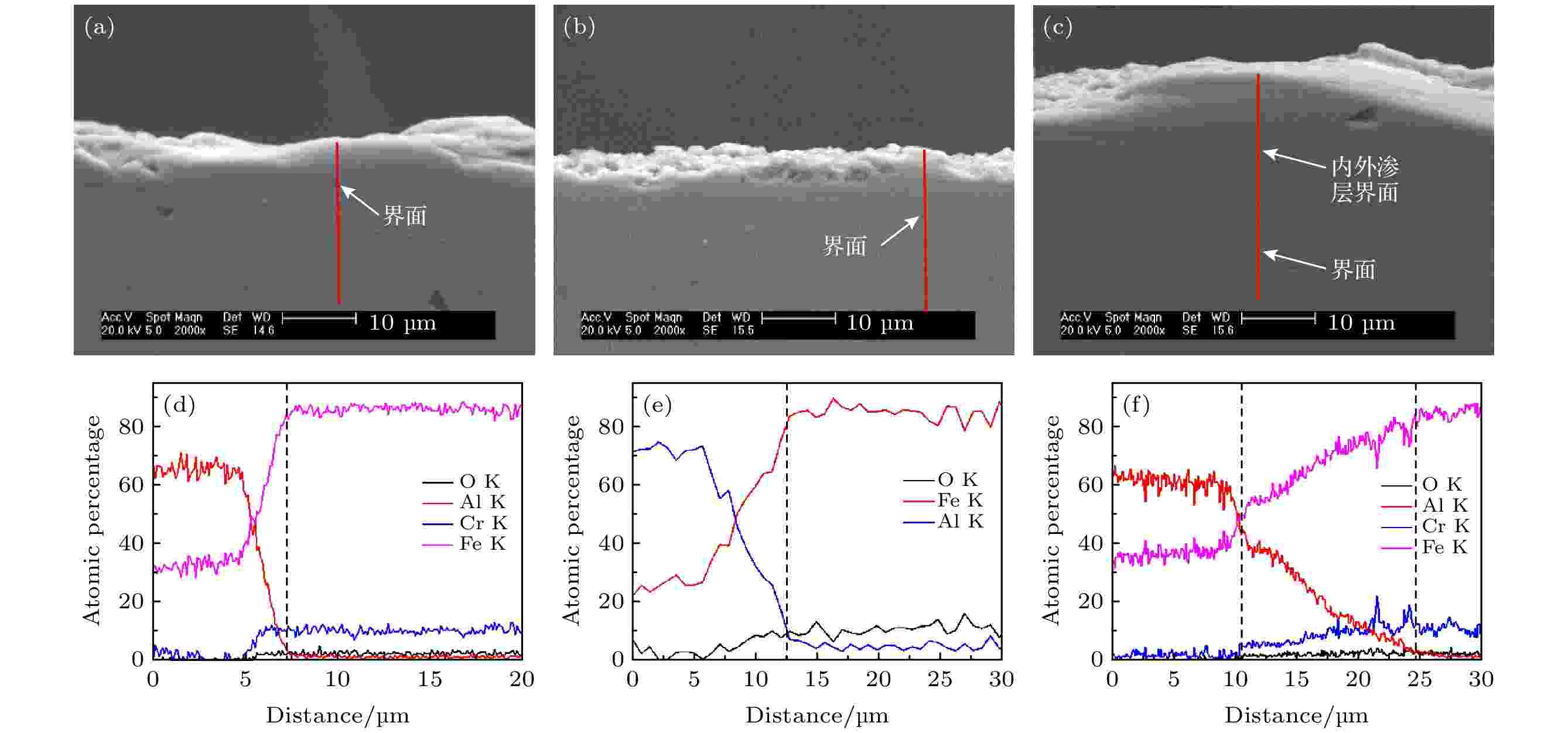
Figure4. Cross-sectional SEM micrographs and EDS element analysis of samples after annealing for 4 h at different temperature. The red lines in the cross-sectional SEM micrographs are scanning lines, and the white arrows indicate the position of the dotted line in the corresponding EDS graphs. (a), (d) The temperature is 640 ℃; (b), (e) the temperature is 700 ℃; (c), (f) the temperature is 760 ℃
同时为了确定渗层表面的相组成, 对试样进行了XRD测试, 结果如图5所示. 从EDS线扫描结果可以看出, 640 ℃下渗层厚度约为7 μm, Al原子含量在65%左右, 从XRD图谱上看出其表面的合金相主要是Al和Fe2Al5相, 这也进一步印证了试样表面存在未能参与扩散的Al. 700 ℃下, 由于温度已高于铝的熔点, 此时试样表面铝镀层为液态. Fe在固体铝中的溶解度为0.02%, 而在液态Al中的溶解度达44%, 因此液态铝下扩散进行得更快[19]. 此时获得的渗层厚度约为12.5 μm, 表面形成了Fe2Al5和FeAl2混合相. 而在760 ℃下试样截面呈现较为明显的内外两层结构, 内外两层界面约在距表面10 μm处. 此时渗层总厚度达24 μm左右. 可见, 温度越高, Fe, Al原子扩散越快, 渗层厚度更大, 表面获得的Fe-Al合金相种类也不同, 并逐渐由富铝相向贫铝相转变.
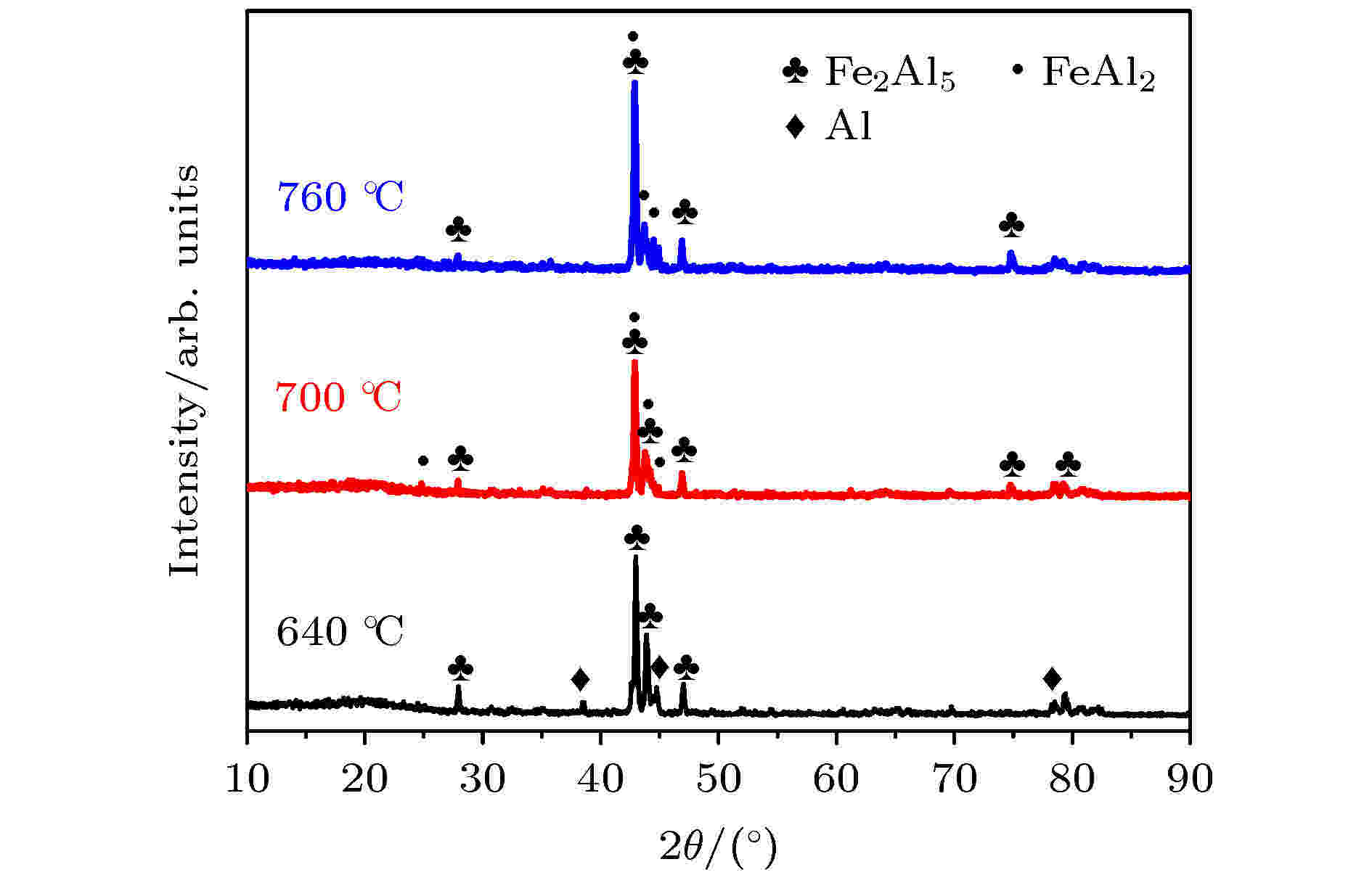
Figure5. XRD patterns of samples after annealing for 4 h.
将渗层厚度L的对数与1/T进行拟合, 结果如图6所示. 两者呈线性关系, 表明热处理温度对渗层生长速率的影响符合Arrhenius关系, 可以用下面公式表示[20-23]:
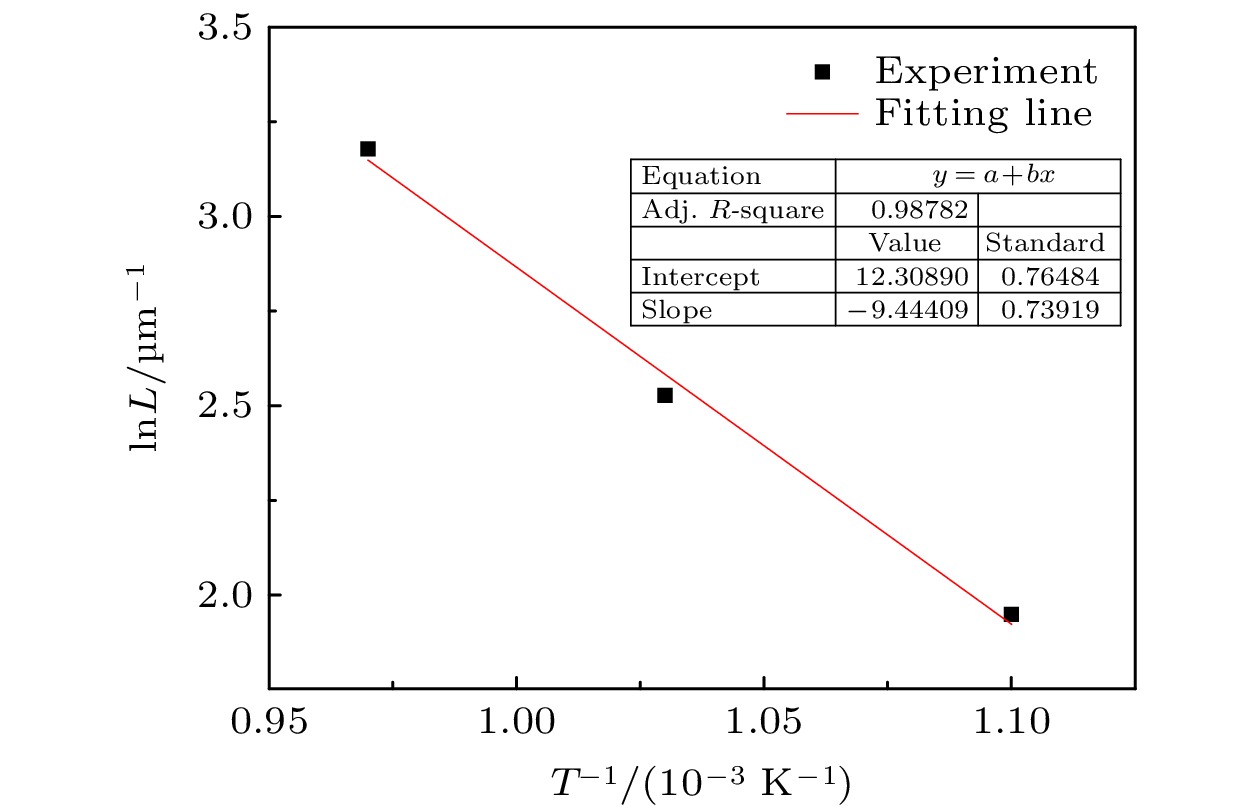
Figure6. Relationship between Fe-Al alloy’s thickness and annealing temperature.
2
3.3.热处理时间对试样组织结构的影响
Fe-Al合金渗层的形成过程包含着复杂的物理化学反应. 扩散初期, 原子在位错、晶界附近发生富铝相形核、生长和转变. 在基体表面形成Fe-Al合金, 此阶段主要形成无序状态的FeAl3和Fe2Al5. 随着Fe, Al原子互扩散的进行, 当Fe2Al5晶粒铺满基体表面后, Al原子由于浓度差异开始向基体中心扩散, 涂层厚度也开始增大. 沿中心方向, Al原子浓度逐渐降低[23].为了考查热处理时间对渗层形成的影响, 选择在640 ℃和760 ℃两个温度下进行实验. 试样在640 ℃下分别处理4 h, 20 h和50 h后的截面形貌及EDS线扫描结果如图7所示. 其中, 图7(c)中最外层为未完全渗透的铝及其在热处理过程中与空气反应生成的氧化铝, 呈疏松状, 约为7 μm. 渗层分内外两层, 内层为成分渐变的过渡层, 内外层界面明显, 该处Fe和Al原子百分比相等. 而渗层与基体间无明显界面(图中白色箭头处), 结合紧密. 4 h, 20 h和50 h下渗层总厚度分别约为7 μm, 14 μm和16 μm. 可见, 在640 ℃下, 随着热处理时间延长到一定程度后, 渗层厚度增大幅度并不显著. XRD测试结果如图8所示, 经过4 h, 20 h和50 h热处理后, 试样表面均存在未参与扩散的Al和Fe2Al5相. 此时, 获得的Fe-Al合金渗层均比较薄, 而且此温度下获取更厚的渗层, 花费的时间成本成倍增加.

Figure7. Cross-sectional SEM micrographs and EDS element analysis of samples after annealing at 640 ℃ for different time. The red lines in the cross-sectional SEM micrographs are scanning lines, and the white arrows indicate the position of the dotted line in the corresponding EDS graphs: (a), (d) Heating time is 4 h; (b), (e) heating time is 20 h; (c), (f) heating time is 50 h.
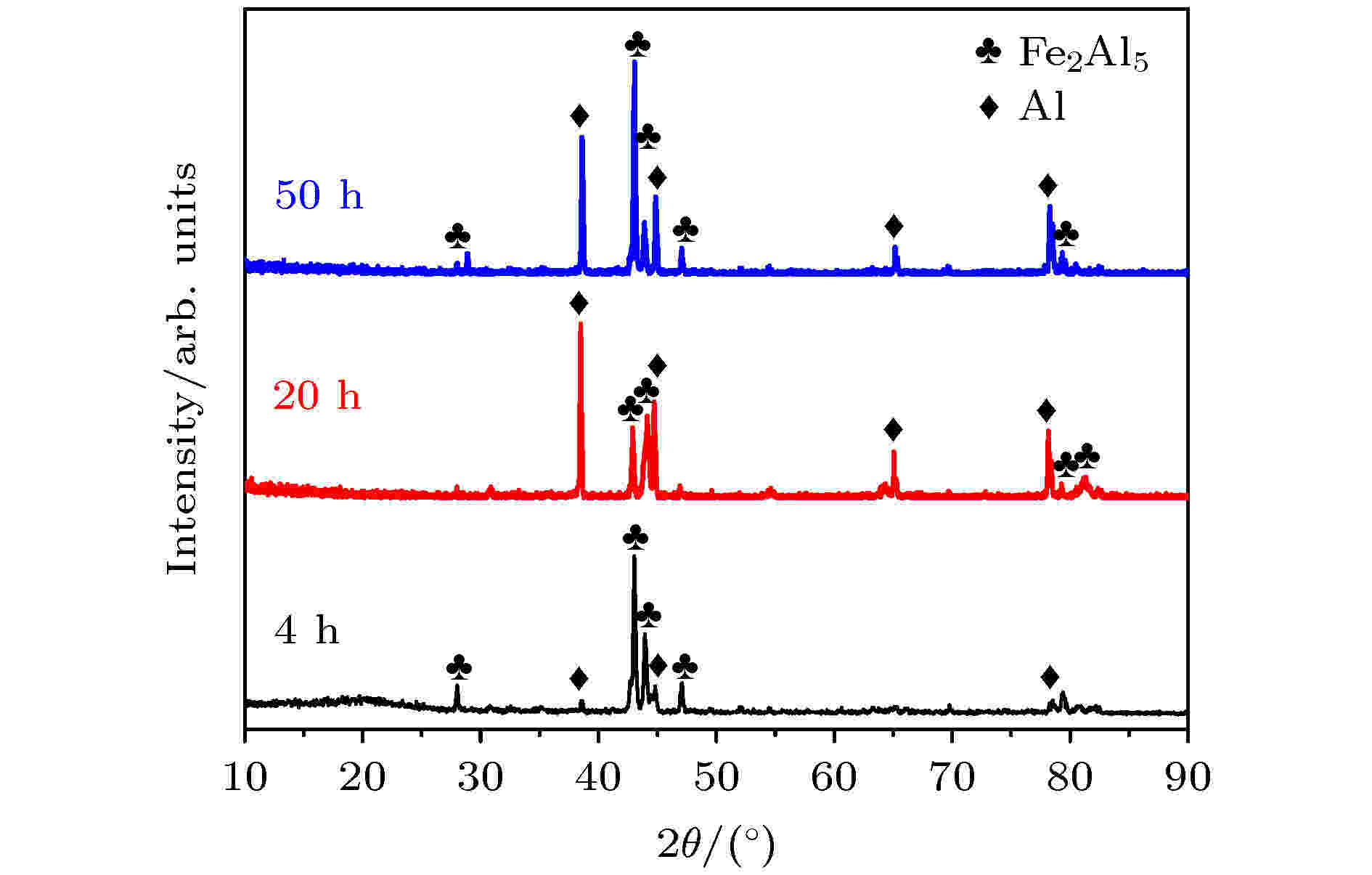
Figure8. XRD patterns of samples after annealing at 640 ℃.
760 ℃下对试样分别进行4 h, 10 h和20 h的热处理. 各条件下试样形貌及EDS线扫描结果如图9所示. 760 ℃/4 h热处理条件下的试样渗层总厚度达24 μm左右. 760 ℃/10 h下, 结合Fe-Al合金二元相图, 从Fe和Al随扫描深度的原子比例变化来推测, 渗层从表面至基体可分为Fe2Al5层、FeAl2层及混合相形成的过渡层, 总厚度约为35 μm. 760 ℃/20 h试样的渗层总厚度约为45 μm, 由于热处理时间足够长, Fe与Al之间扩散反应更加充分, 试样表面已经由富铝相Fe2Al5或FeAl2向FeAl相转变. 图10所示的XRD分析结果也说明了这一点. 760 ℃/4 h热处理条件下可观察到Fe2Al5和FeAl2混合相. 760 ℃/10 h时Fe2Al5相主要衍射峰强度减弱, FeAl2相部分衍射峰开始出现. 到760 ℃/20 h时, FeAl2相已经逐渐向FeAl相转变. 由Fe-Al二元相图推测出热处理过程中最先生成的应该是FeAl3, 但该相不稳定, 易转化为Fe2Al5相, 因此在XRD谱图上未检测出FeAl3相的存在. 可见, 随着热处理时间的增加, Fe与Al原子间持续进行扩散, 渗层表面逐步由富铝相向贫铝相生长, 即FeAl3 → Fe2Al5 → FeAl2 → FeAl.
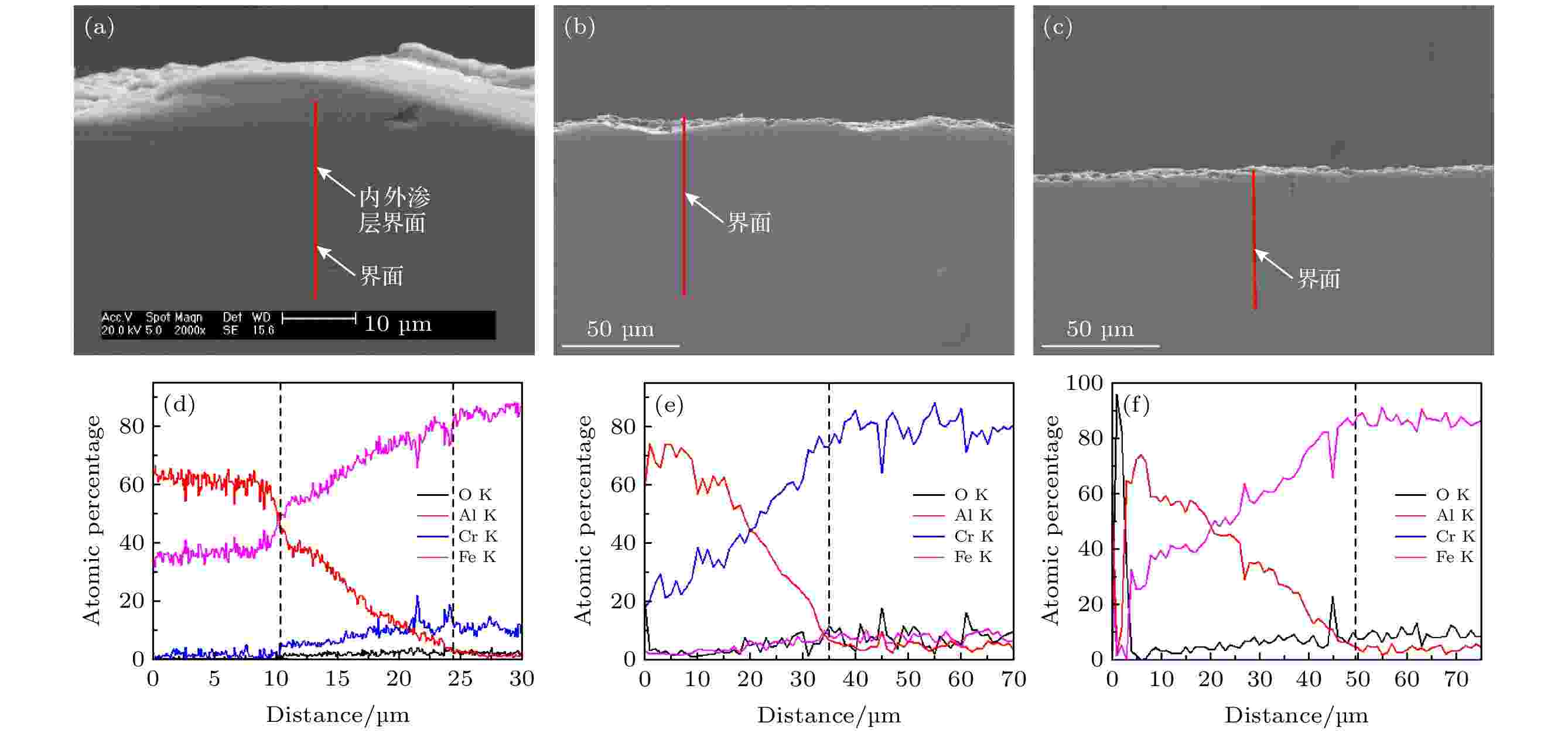
Figure9. Cross-sectional SEM micrographs and EDS element analysis of samples after annealing at 760 ℃ for different time. The red lines in the cross-sectional SEM micrographs are scanning lines, and the white arrows indicate the position of the dotted line in the corresponding EDS graphs. (a), (d) Heating time is 4 h; (b), (e) heating time is 10 h; (c), (f) heating time is 20 h.
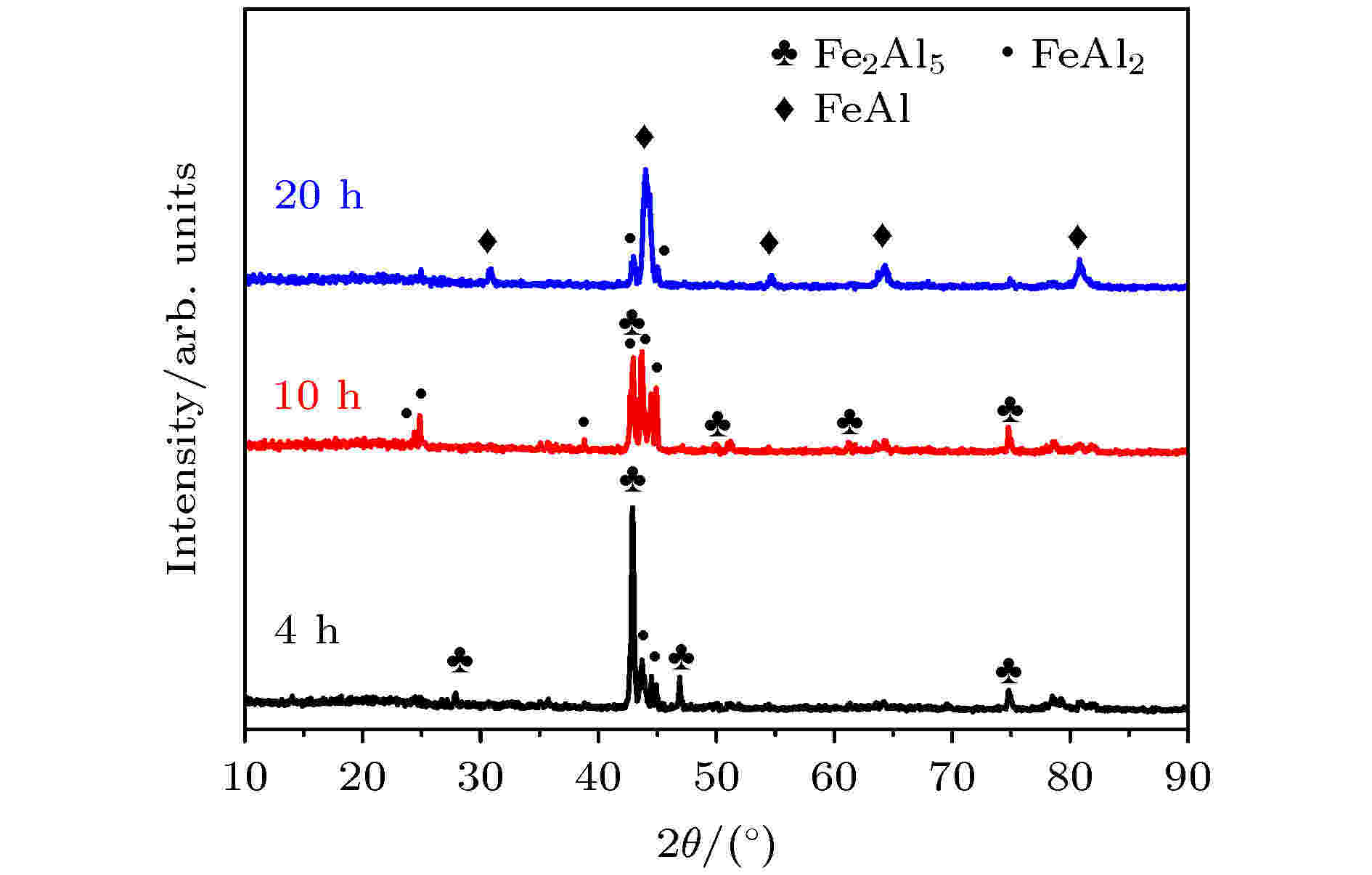
Figure10. XRD patterns of samples after annealing at 760 ℃.
在640 ℃下热处理后的截面形貌中均观察到渗层中分布着不规律的白点. 760 ℃/4 h下也能观察到少许白点, 但却未在760 ℃/10 h和760 ℃/20 h的试样中观察到此现象. 选取图7(b)中的3个位置进行EDS扫描, 结果如表4所列. 从EDS扫描结果来看, 白点主要由 Fe, Al, Cr元素组成, 其中Cr原子含量为4.33%, 而其附近渗层中Cr原子含量为1.26%. 可见白点为Cr富集的Fe-Al合金. 张桂凯等[24]在对HR-2不锈钢镀铝样品进行700 ℃/2 h热处理后, 发现约5 μm的外层渗层中弥散着相当数量的白点, 但并未对该现象作进一步的解释. 李亚江等[25]研究Fe3Al合金与Q235和Cr18-Ni8钢之间的扩散焊时发现, 在扩散焊界面过渡区均观察到了白色的第二相, Fe3Al/ Q235形成的白点C, Cr含量较基体高, 而Fe3Al/ Cr18-Ni8钢样品的白点Cr, Ni含量较高. 形成此现象的原因有可能是: 在热处理过程中, 基体中Cr, Si, Mn等元素在迁移过程中容易富集于缺陷处, 引起Cr的偏聚. 在与铝镀层相互扩散过程中, 由于Cr在Al内的溶解度很小, Fe原子与铝原子的互扩散要比Cr原子更快, 导致富集点中的Cr未能完全扩散, 形成了无规则分布的白色第二相. 随着扩散的进行, 白点中的Cr持续往四周的低浓度区域扩散. 当热处理条件足够使其完全扩散后, 白点也随之消失[26].
Spot | Al K | Fe K | Cr K | O K |
1 (白点) | 62.81 | 32.87 | 4.33 | — |
2 (基体) | — | 79.68 | 8.32 | 2.35 |
3 (渗层) | 67.53 | 24.26 | 1.26 | 6.95 |
表4640 ℃/20 h下试样截面EDS能谱分析(at%)
Table4.EDS elemental analysis of sample cross section at 640 ℃ for 20 h (at%).
通常来说, 扩散反应形成的金属间化合物厚度L与时间t之间的关系可以用幂函数表示:
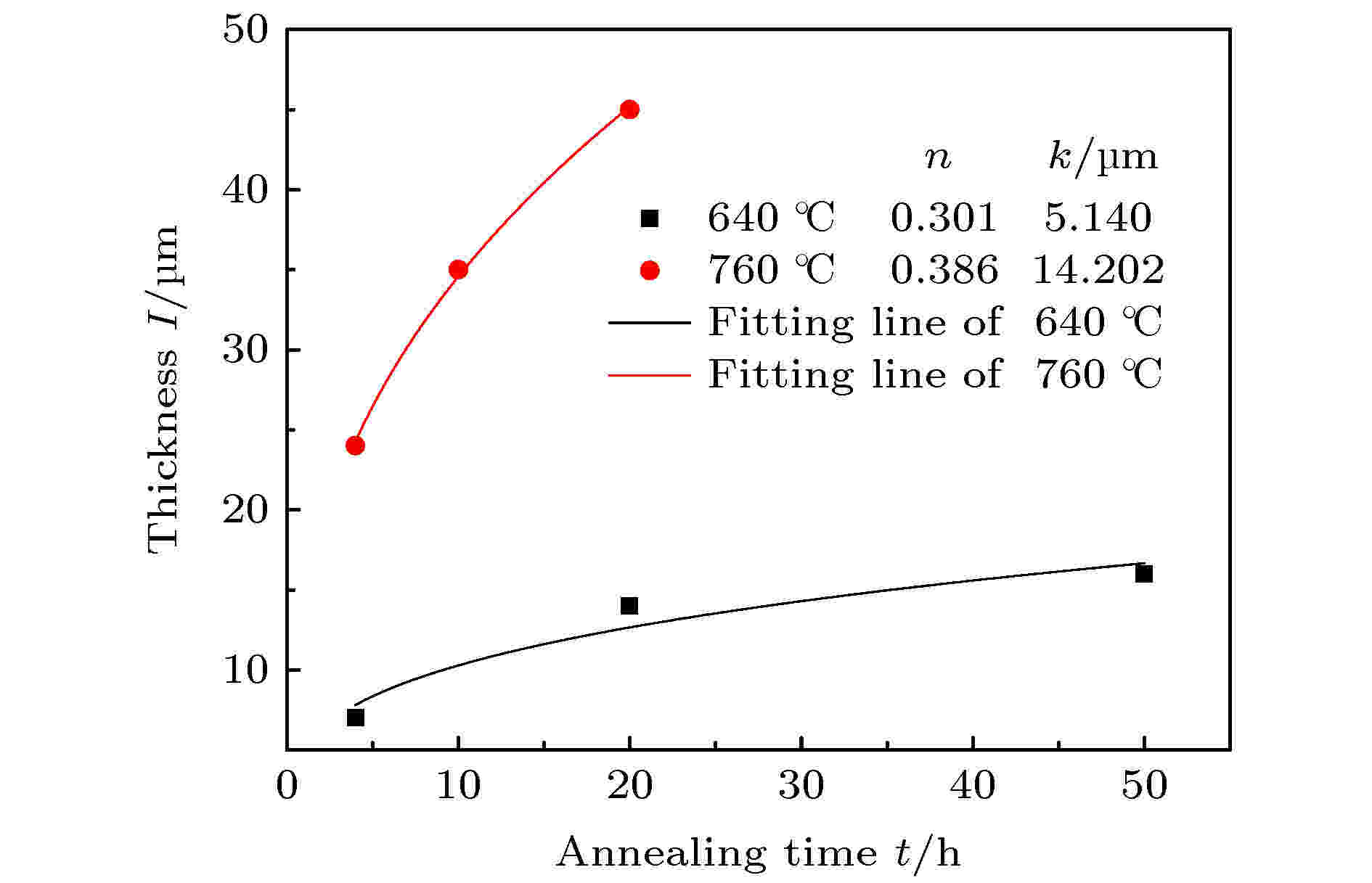
Figure11. Curves of Fe-Al alloy’s thickness vs. the annealing time.
2
3.4.最优热处理条件的确定
热处理获得的渗层厚度应存在一个最佳数值, 太薄则在后续氧化表面预处理过程中易将渗层消耗尽而使基体裸露, 无法获得均匀致密的氧化膜; 太厚则要求更高的热处理温度或时间, 进一步增加制备成本. 同时, 当表面合金为富铝相时更加有利于Al2O3膜的形成[28]. 因此, 通过控制热处理条件可以在镀铝的基体表面获得一定厚度的富铝相Fe-Al合金层.一方面热处理温度越高, 尤其是高于铝熔点时, 渗层生长速率较快; 但另一方面, 过高的温度可能会导致RAFM钢基体的高温强度和抗蠕变性能下降, 影响基体的力学性能[29,30]. 为了尽可能降低对基体性能的影响, 热处理温度越低越好. 因此, 热处理温度较优的选择为700 ℃, 参照700 ℃/4 h的结果, 适当延长了热处理时间至10 h, 所得试样表面和截面形貌如图12(a)和图12(b)所示. 热处理后试样表面呈黑褐色, 打磨去除氧化层后获得亮银色金属光泽的表面. 从图12(a)可观察到少量白色物质分布于渗层上, 取所标识的三处位置进行了EDS点扫描, 其结果如表4所列. 据此可以推断出白色物质为基体Fe元素扩散至表面被氧化后形成的氧化物, 同时也说明了试样表面已生成了Fe-A1合金渗层. 渗层与基体间结合良好, 未观察到孔洞、缝隙等缺陷, 也无明显界面. 从EDS线扫描结果来看, 渗层总厚度约为25 μm, 包括厚度约为15 μm的富铝相Fe-Al合金层以及约10 μm成分渐变的过渡层.
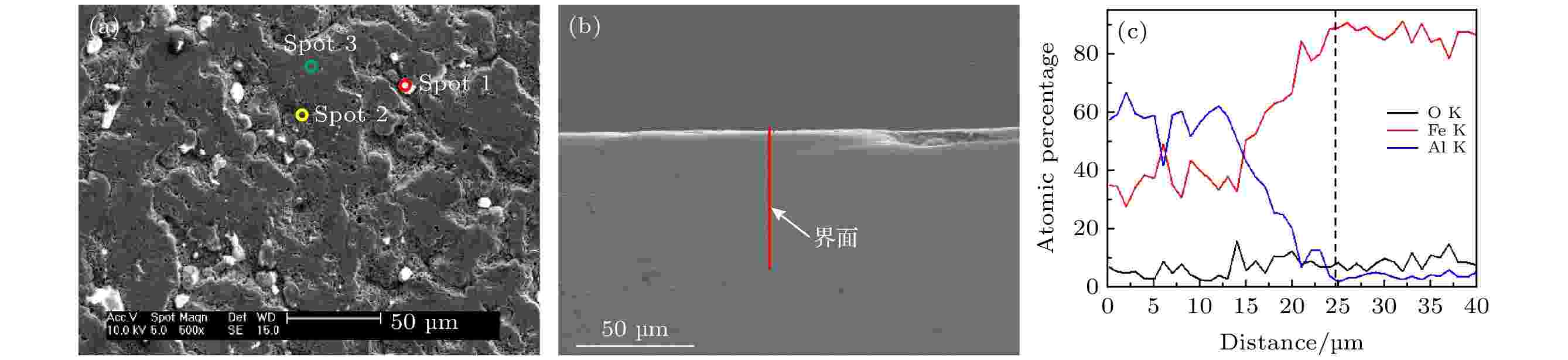
Figure12. Surface (a), cross-sectional (b) SEM micrographs and EDS element analysis (c) of samples after annealing at 700 ℃ for 10 h.
试样的XRD测试结果如图13所示, 渗层表面主要由Fe2Al5和FeAl2相组成, 同时也检测到了Fe2O3的存在, 结合表面EDS结果可以确定分布于表面的白色物质为Fe2O3. 不论是渗层厚度还是其Fe-Al合金相结构, 该试样均满足后续氧化的基本要求, 因此较优的热处理工艺为700 ℃/10 h.
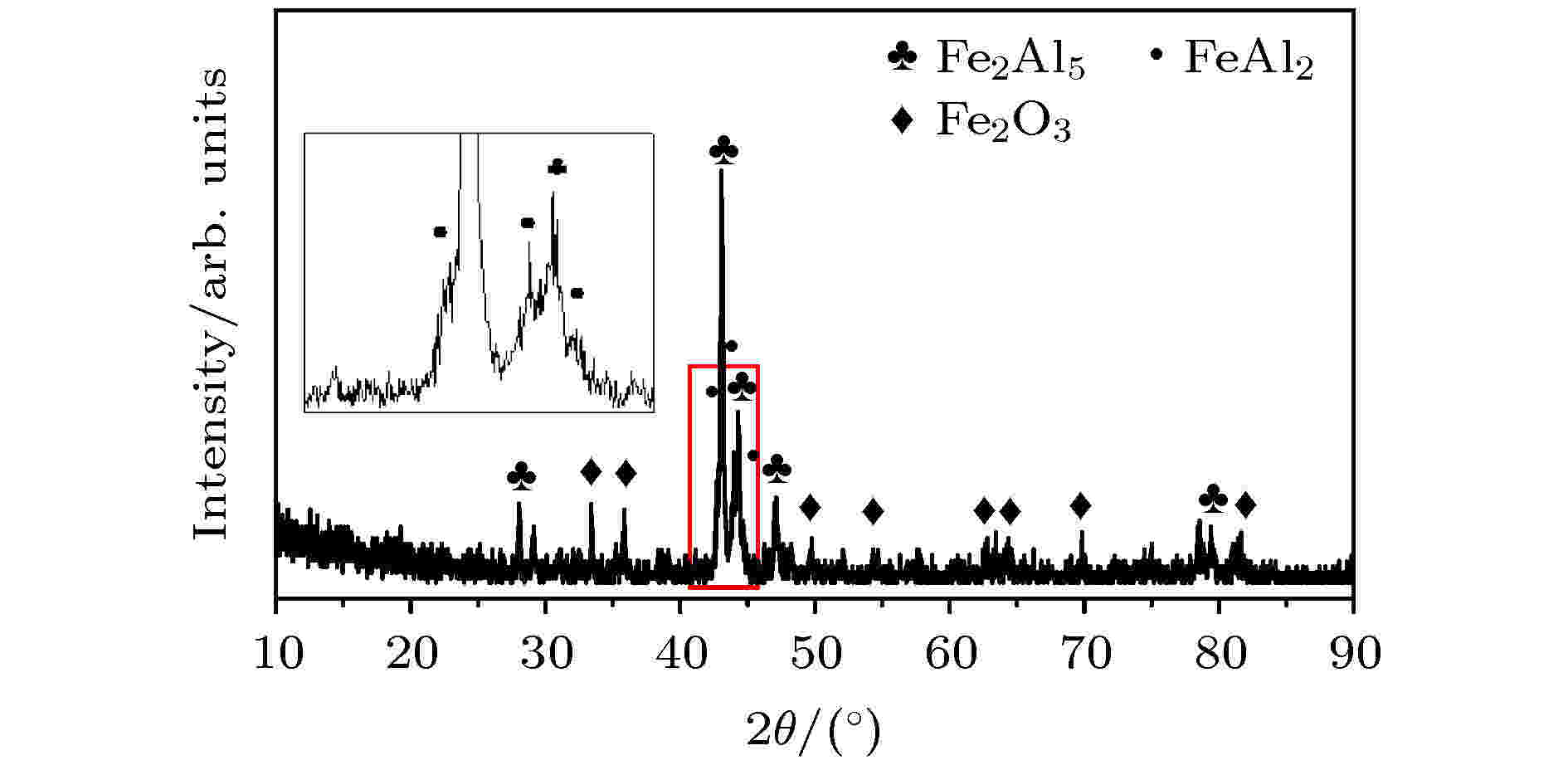
Figure13. XRD patterns of samples after annealing at 700 ℃ for 10 h.
Spot | Al K | Fe L | O K |
1 | — | 25.16 | 74.84 |
2 | 20.37 | 12.46 | 67.17 |
3 | 71.45 | 14.00 | 14.55 |
表5700 ℃/10 h试样表面EDS结果
Table5.EDS elemental analysis of sample surface at 700 ℃ for 10 h (at%).
