全文HTML
--> --> -->氧化铟(In2O3)作为一种制备简单、成本低、长期稳定性良好的半导体材料, 目前在检测NO2方面已得到广泛的研究[5-8]. 研究发现, 增强In2O3材料传感特性的一种有效方法就是增大In2O3材料的比表面积[9,10], 例如Yang等[11]通过柯肯达尔效应和退火的方法制备了一种表面多孔的立方结构In2O3纳米材料. 也有科研工作者尝试通过改变In2O3的纳米结构来获取比晶体更大的比表面积, 如纳米棒、纳米线、纳米球等[12-15]. 另一种改善传感特性的方法是对In2O3进行掺杂[16], 如Sabry等[17]通过水热法制备了一种用于检测NO2气体的银掺杂In2O3传感材料, 但是文中没有报道银的最佳掺杂量也没有分析该传感器的气体选择性; Lee和Tseng[18]通过蒸汽输送和化学湿法沉积以及热处理的方法制备出一种NiO/In2O3复合纳米材料, 也能明显提升材料对NO2的气体灵敏度. 但大量研究同时表明, 仅仅通过增大半导体材料的比表面积或者掺杂会出现传感器稳定性较差、工作温度高或者响应、恢复时间慢等问题. 为有效解决此类问题, 本文提出在较大比表面积的多孔纳米材料的基础上对材料进一步掺杂处理, 以结合比表面积和掺杂这两方面优势.
本文采用水热法制备了Fe掺杂多孔In2O3纳米材料, 并基于该材料制备了传感器. 首先利用X射线衍射仪(X-ray diffraction, XRD)、扫描电子显微镜(scanning electron microscopy, SEM)、透射电子显微镜(transmission electron microscopy, TEM)和比表面积测试对所制备的纳米材料进行微观形貌表征与分析, 然后对该纳米材料制备的传感器进行性能研究, 包括温度特性、响应-恢复特性、选择性和稳定性.
2.1.材料与制备
实验采用的原材料包括分析纯In(NO3)3·4.5H2O, Fe(NO3)3·9H2O和Span-40, 购于国药集团化学试剂有限公司, 使用前未进一步纯化. 制备过程首先称取0.5729 g (1.5 mmol)的In(NO3)3·4.5H2O和0.6030 g (1.5 mmol)的Span-40混合溶于30.0 mL去离子水中, 室温下磁力搅拌. 溶解后, 加入不同质量的Fe(NO3)3·9H2O, 继续搅拌30 min. 然后将溶液转入不锈钢高压釜中, 利用水热炉进行加热, 反应温度为180 ℃, 反应时间为24 h. 自然冷却到室温, 得到灰色沉淀物. 用离心机将沉淀物分离后用无水乙醇清洗至pH值呈中性, 然后在80 ℃下烘干, 最后在马弗炉中500 ℃下煅烧2 h, 即可获得不同Fe掺杂的多孔In2O3材料. 根据Fe的掺杂量不同, 制备了6种样品, 每种样品的编号、组成及用量如表1所列.样品编号 | 组成及用量/g | In/Fe摩尔比 | ||
In(NO3)3·4.5H2O | Fe(NO3)3·9H2O | Span-40 | ||
样品1 (S1) | 0.5729 | 0 | 0.6030 | — |
样品2 (S2) | 0.5729 | 0.1212 | 0.6030 | 5∶1 |
样品3 (S3) | 0.5729 | 0.0866 | 0.6030 | 7∶1 |
样品4 (S4) | 0.5729 | 0.0673 | 0.6030 | 9∶1 |
样品5 (S5) | 0.5729 | 0.0505 | 0.6030 | 12∶1 |
样品6 (S6) | 0.5729 | 0.0404 | 0.6030 | 15∶1 |
表1样品原材料组成表
Table1.Composition of sample raw materials.
2
2.2.表 征
实验采用荷兰菲利普分析仪器公司的X’Pert PRO衍射仪做结构分析(衍射实验条件为Cu Kα, λ = 1.5406 ?, 加速电压40 kV, 电流35 mA, 扫描角度10° — 80°); 用日本电子公司的JSM-6701F型SEM对样品的表面形貌进行微观检测; 采用英国牛津公司生产的X-MaxN 80T型能量色散X射线光谱(energy dispersive X-ray spectroscopy, EDS)分析仪确定样品中的元素成分和含量; 采用美国 Hillsboro 公司的 Tecnai G2 F30型TEM观察样品的内部微观形貌; 采用北京金埃谱公司生产的 V-Sorb 2800P 型全自动物理吸附/化学吸附分析仪检测样品的比表面积, 然后采用 Brunauer-Emmett-Teller (BET)法[19]进行计算.2
2.3.传感器的制作和测量方法
实验过程首先将2.1节中得到的掺杂In2O3纳米粉体和α-松油醇混合并搅拌成糊状, 然后将其均匀涂覆在内径2 mm、外径4 mm、长度10 mm的氧化铝陶瓷管表面, 陶瓷管两端镀有金电极, 并由铂线引出作为传感器的两个电极引脚. 陶瓷管中穿入一根镍铬合金线, 用来对传感器进行加热. 传感器在60 ℃下干燥后, 放入马弗炉中500 ℃烧结2 h. 为了提高稳定性, 将传感器在300 ℃温度下老化240 h. 最终得到的传感器结构图如图1(a)所示.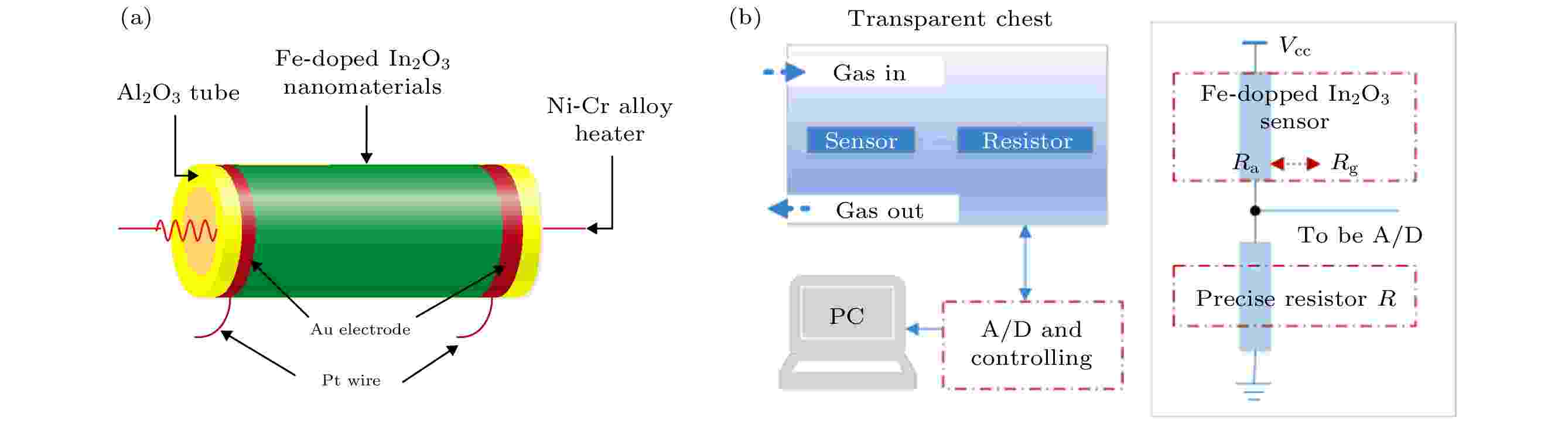
Figure1. Diagram used to measure the sensitivity of sensor: (a) Structure of sensor; (b) sensor test system.
传感测试系统的结构原理如图1(b)所示, 由一个透明测试箱、一个控制板和一台个人电脑(personal computer, PC)组成. 测试时传感器样品被置入测试箱中和精度为1%的金属膜电阻串联. 通过控制板设定、控制加热温度和对采样电压进行模数转换, PC用来接收由控制板发来的数据并进行处理和存储. 传感器的电阻值根据金属膜电阻上的电压间接计算得出. 当测试箱中通入待测气体后, 传感器阻值发生变化, 定义传感器的灵敏度值为Rg/Ra, 其中Rg和Ra分别为传感器在待测气体和空气中的阻值. 测试时同种样品制成3个元件进行3次测试以减少实验偏差.
3.1.微观形貌
图2为制备的6种样品的XRD 图谱. 通过与标准图谱(JCPDS No. 06-0416)对照, 发现所有In2O3衍射峰都与立方晶系结构的In2O3的XRD标准谱线相符合, 属于la-3(206)点群. 图谱中没有检测出任何In(NO3)3·4.5H2O和InOOH的衍射峰; 除样品2之外, 样品也不包含Fe或铁化合物的衍射峰. 与无掺Fe样品1比较, 其余掺杂样品的衍射峰角度随Fe含量的增加而有一定程度的增加, 图2中插图所示的是32°—34°之间衍射峰(321)放大后的图谱. 这表明Fe原子进入了In2O3的晶格. 因为当In原子被Fe原子所替代时, 晶格常数的变化会使得衍射峰发生移动[20].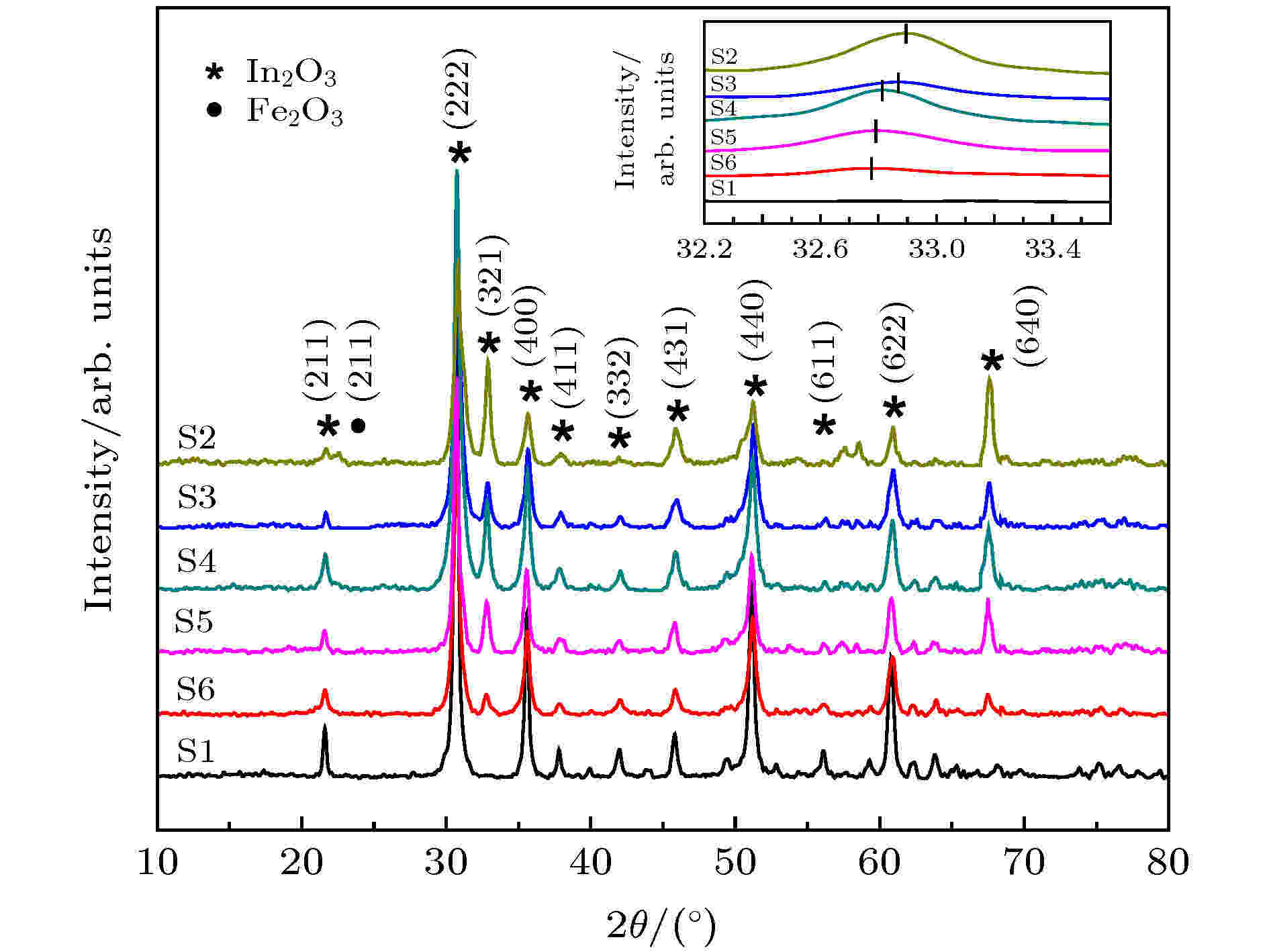
Figure2. XRD patterns of Fe-doped In2O3.
图3(a)—(f)是制备的6个In2O3样品的SEM形貌图. SEM形貌图清晰地显示出样品的微观结构由大量分散的不规则分布的立方体或长方体组成, 立方体边长约50—200 nm不等. 从图3还可以观察到这些立方体结构中间分布着大量细小的孔洞及不规则的裂纹.
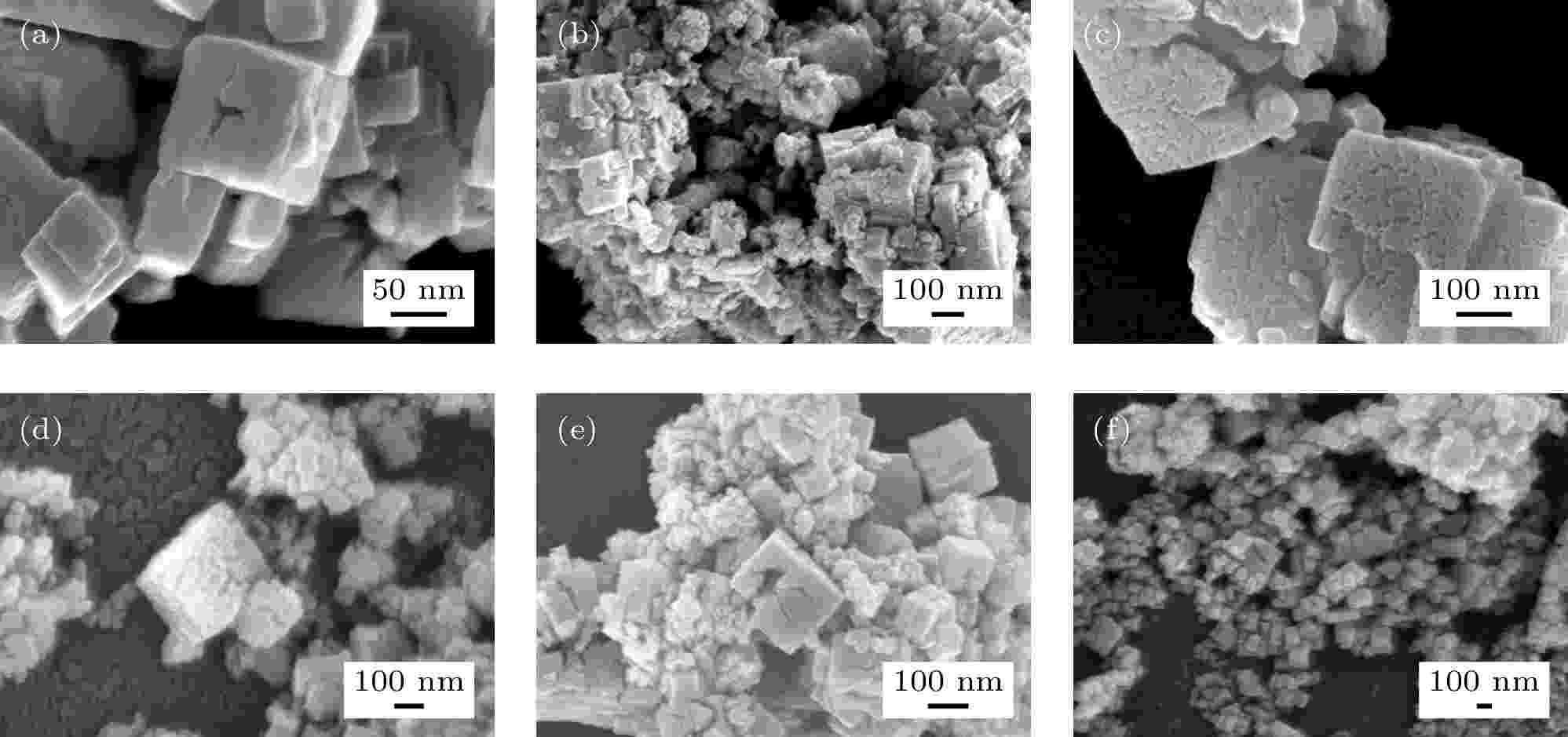
Figure3. SEM images: (a) S1; (b) S2; (c) S3; (d) S4; (e) S5; (f) S6.
图4(a)是样品4的TEM图, 清晰地表明观察到的立方体结构由均匀的更小的纳米颗粒堆砌生长而成. 对上述的同一区域进行EDS和选区电子衍射(selected area electron diffraction, SAED)图像分析, 结果见图4(b). 样品的EDS分析结果说明Fe掺杂 In2O3的元素组成包括In, Fe, O三种元素, 其摩尔比约是In∶Fe∶O=18.01∶2.1∶48.58, 这和样品4的原始化学组分一致. 图4(b)中插图为样品4的SAED光斑.
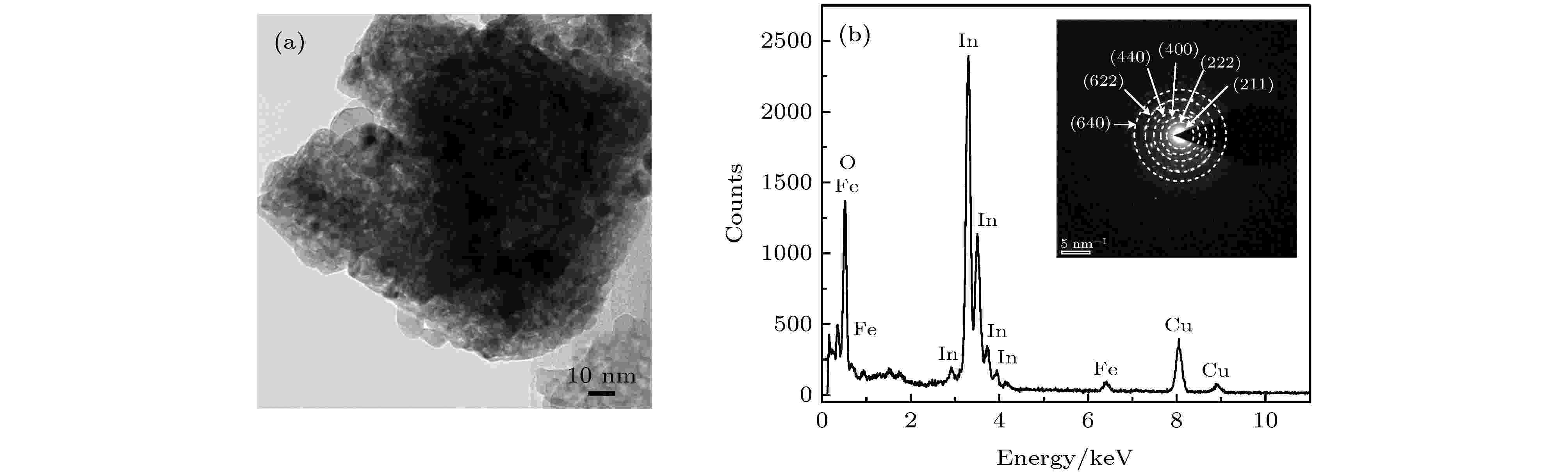
Figure4. (a) TEM image of S4; (b) EDS spectroscopy and SAED pattern taken from S4.
图5分别为样品1与样品4的N2吸附/脱附曲线和孔径分布图. 从图5(a)和图5(c)可以看出两种样品脱附所需的能量都高于吸附所需的能量, 根据IUPAC分类[21], 两种样品相似的N2吸附/脱附曲线表现出具有滞回效应的电流-电压型特征曲线, 表明这两种样品都是有孔结构, 这通过图3的SEM图像和图4的TEM图像也能观察到. 对比图5(a)和图5(c)可以看出, 在相对气压较高的情况下, 样品4的N2吸附量为81.58 cm3/g, 多于样品1的N2吸附量(39.61 cm3/g), 这说明样品4具有更大的比表面积.
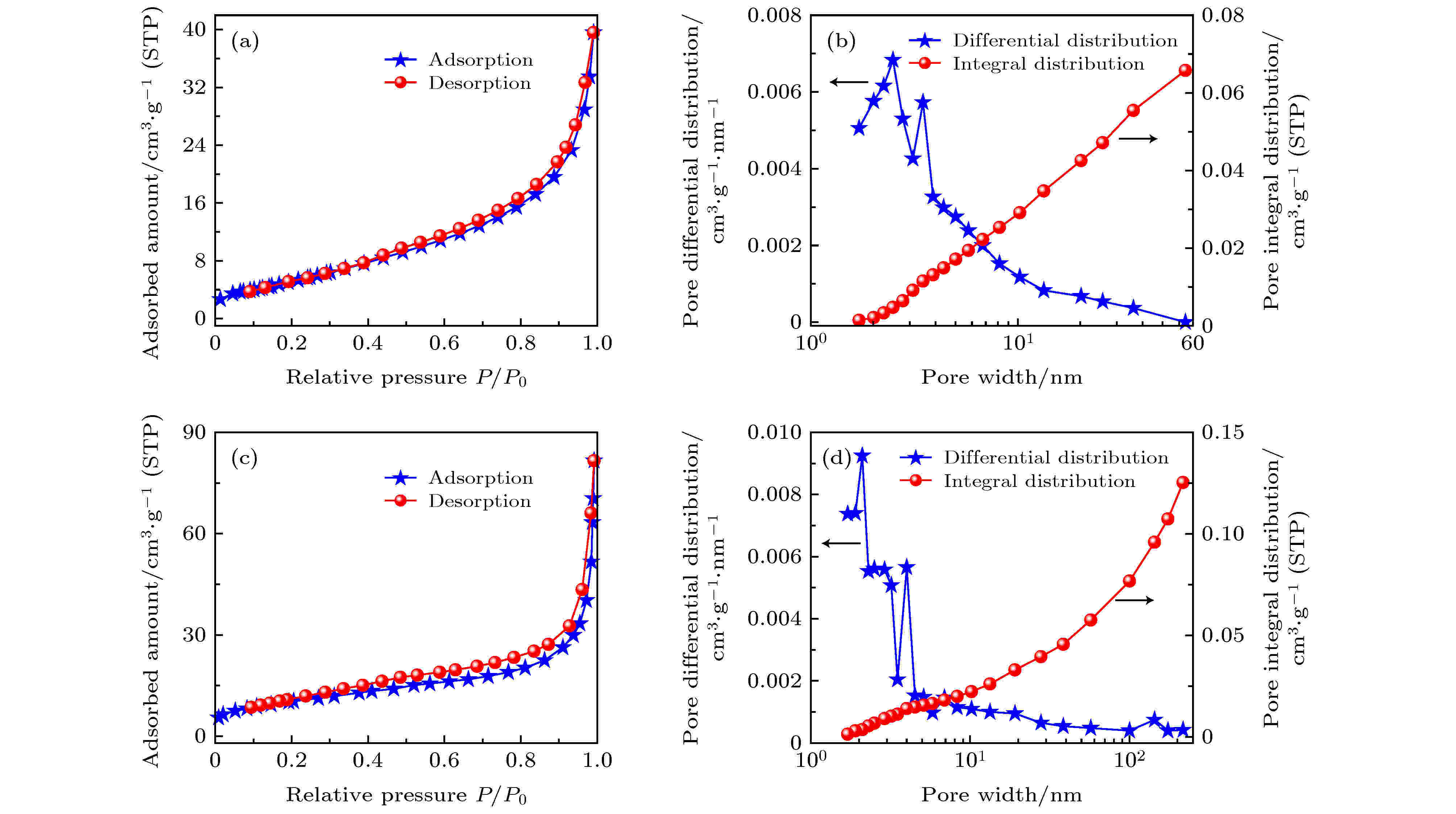
Figure5. N2 adsorption/desorption curves of (a) S1 and (c) S4; the pore size distribution of (b) S1 and (d) S4.
从图5(b)和图5(d)的孔径分布可以看出, 无Fe掺杂的In2O3样品1和Fe掺杂的In2O3样品4孔径分布都集中在2—10 nm, 均表现为介孔结构, 而且具有较小的孔径分布和均匀的孔结构. 根据Barrett-Joyner-Halenda (BJH)算法可得到, 无Fe掺杂的In2O3样品1和Fe掺杂的In2O3样品4的BJH累积孔体积分别为0.0667和0.0947 cm3/g, BJH累积孔面积分别为31.27和78.34 m2/g. 这充分说明了这两种样品材料分布着大量介孔.
2
3.2.形貌生成机理
在Fe掺杂多孔In2O3材料的制备过程中, In2O3由以下化学反应得到: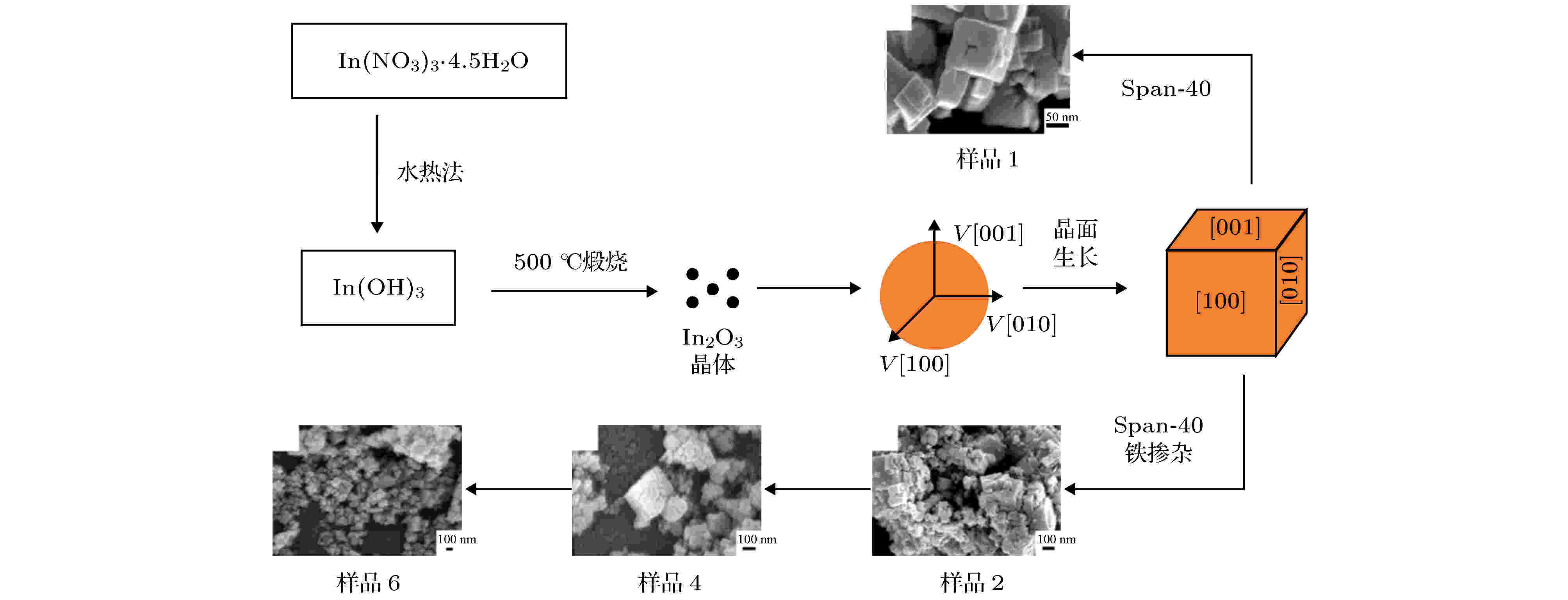
Figure6. Schematic illustrating the formation mechanism of the doped In2O3 structures.
由SEM和TEM图像及比表面积测试结果可以看出, 得到的Fe掺杂In2O3为多孔结构, 介孔的直径为2—10 nm. 此实验中, Span-40的加入是介孔结构形成的关键: Span-40是一种非离子表面活性剂, 能很好地溶解在水中或有机溶剂中. 此外, 与离子表面活性剂相比, Span-40不存在双电层, 因此具备很高的表面活性和稳定性, 常作为乳化剂、润滑剂、分散剂等使用. 本实验中, Span-40作为吸附剂使用, In2O3晶体生长过程中, Span-40作为非离子表面活性剂很容易就吸附在In2O3晶粒上一起生长, 经过煅烧之后, 吸附于In2O3的有机物Span-40分解成氧气和水蒸气从表面逸出, 因此在In2O3内部及表面原来Span-40占据的位置就变得疏松多孔, 多孔结构有效增大了Fe掺杂In2O3材料的比表面积, 增加了与气体的接触面也就提高对气体的灵敏度.
2
3.3.传感特性
图7(a)给出了6种样品制备的传感器灵敏度值在工作温度为260 ℃时随NO2气体浓度变化的关系曲线. 从图7(a)可以看出, 所有样品的灵敏度值都随着NO2气体浓度的增加而增大. 在所有样品中未进行Fe掺杂的样品1传感性最差, 样品4的传感性最佳, 样品4在5 ppm (1 ppm = 1 mg/L), 10 ppm, 30 ppm, 50 ppm, 100 ppm对应的灵敏度值分别为59.5, 118.2, 399.4, 960.5, 1144.6. 图7(b)所示的是6种样品的比表面积, 其中, 未进行Fe掺杂的样品1的比表面积最小, 为16.95 m2/g, 样品4的比表面积最大, 为50.03 m2/g. 对比图7(a)和图7(b)容易发现, 样品的比表面积越大, 气体灵敏度越高. 因此, 接下来选择样品4, 即In, Fe摩尔比为9∶1的样品作为研究对象, 对Fe掺杂多孔In2O3材料的传感性能进行研究.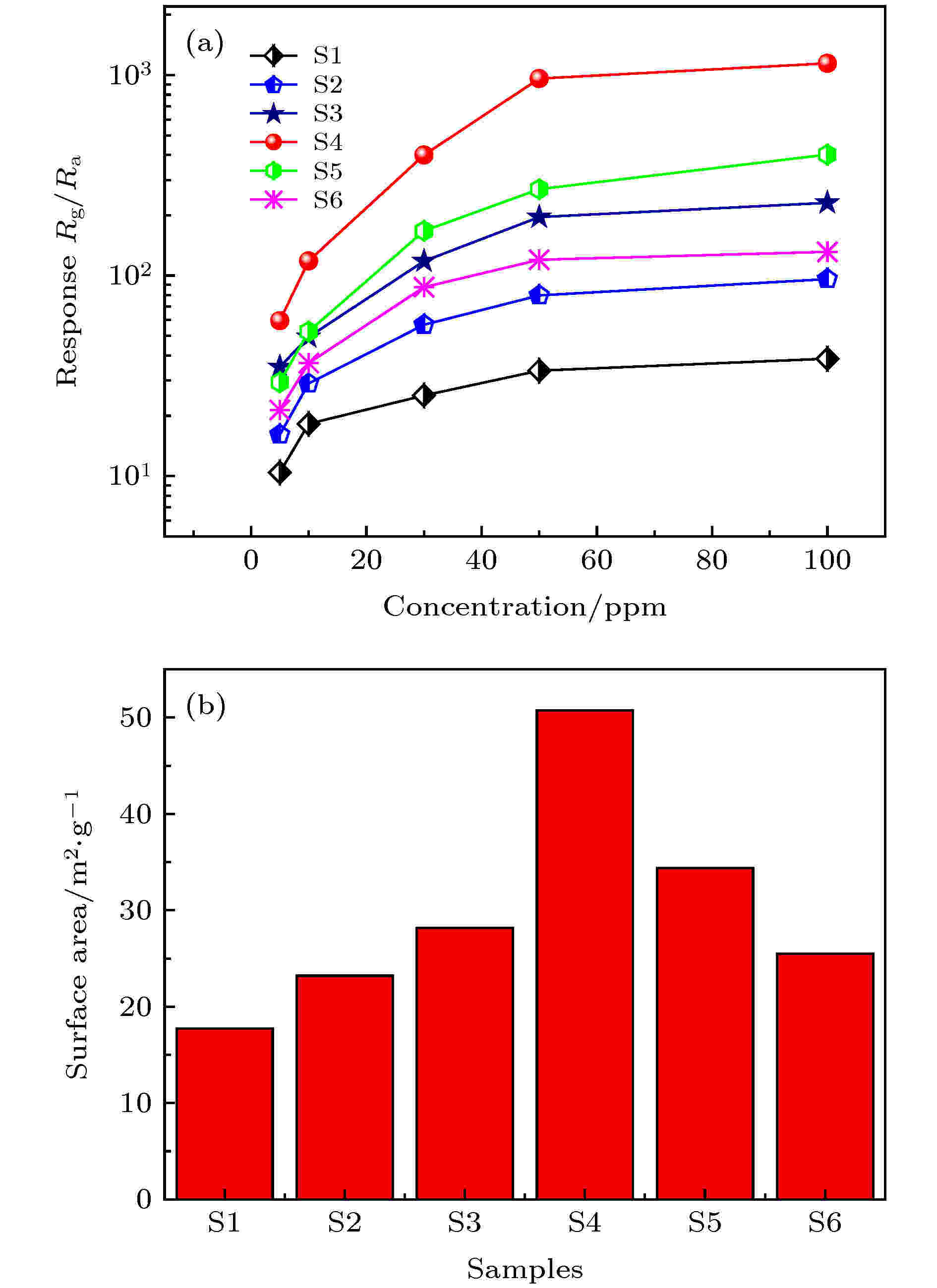
Figure7. (a) Gas response of the 6 sensors exposed to NO2 at concentrations ranging from 5 ppm to 100 ppm at 260 °C; (b) surface area of S1?S6.
图8为样品4制作的传感器在80—300 ℃的工作温度范围内对 50 ppm NO2气体的响应-恢复曲线和灵敏度值. 从图8(a)可以看出, 随着工作温度的升高, 传感器在空气中的电阻值Ra呈降低的趋势. 但是, 当传感器置于NO2气体中的时候, 其电阻值Rg随温度升高而增加. 从图8(b)可以更直观地看出, 随着工作温度的升高, 传感器对50 ppm浓度的NO2气体灵敏度值逐渐增大, 当温度升至260 ℃时, 灵敏度值达到最大值 960.5. 当温度进一步上升时, 灵敏度值有减小的趋势. 造成这种情况的原因可能是当温度逐渐升高时传感器的物理吸附逐渐转变为化学吸附, 而且吸附态的离子(如O–, O2–, OH–等)随着温度上升不断增加, 从而进一步改善了吸附反应. 但由于吸附反应是放热反应, 因此当温度不断升高时, 吸附与脱附反应会在某一温度(260 ℃左右)达到平衡[22,23]. 如果温度继续升高(如达到300 ℃), 气体的脱附反应将会强于吸附反应, 使得该传感器的气体响应降低. 因此, 对于Fe掺杂多孔In2O3 (样品4), 最佳工作温度为260 ℃, 后续所有的测试也都是在260 ℃工作温度下进行的.
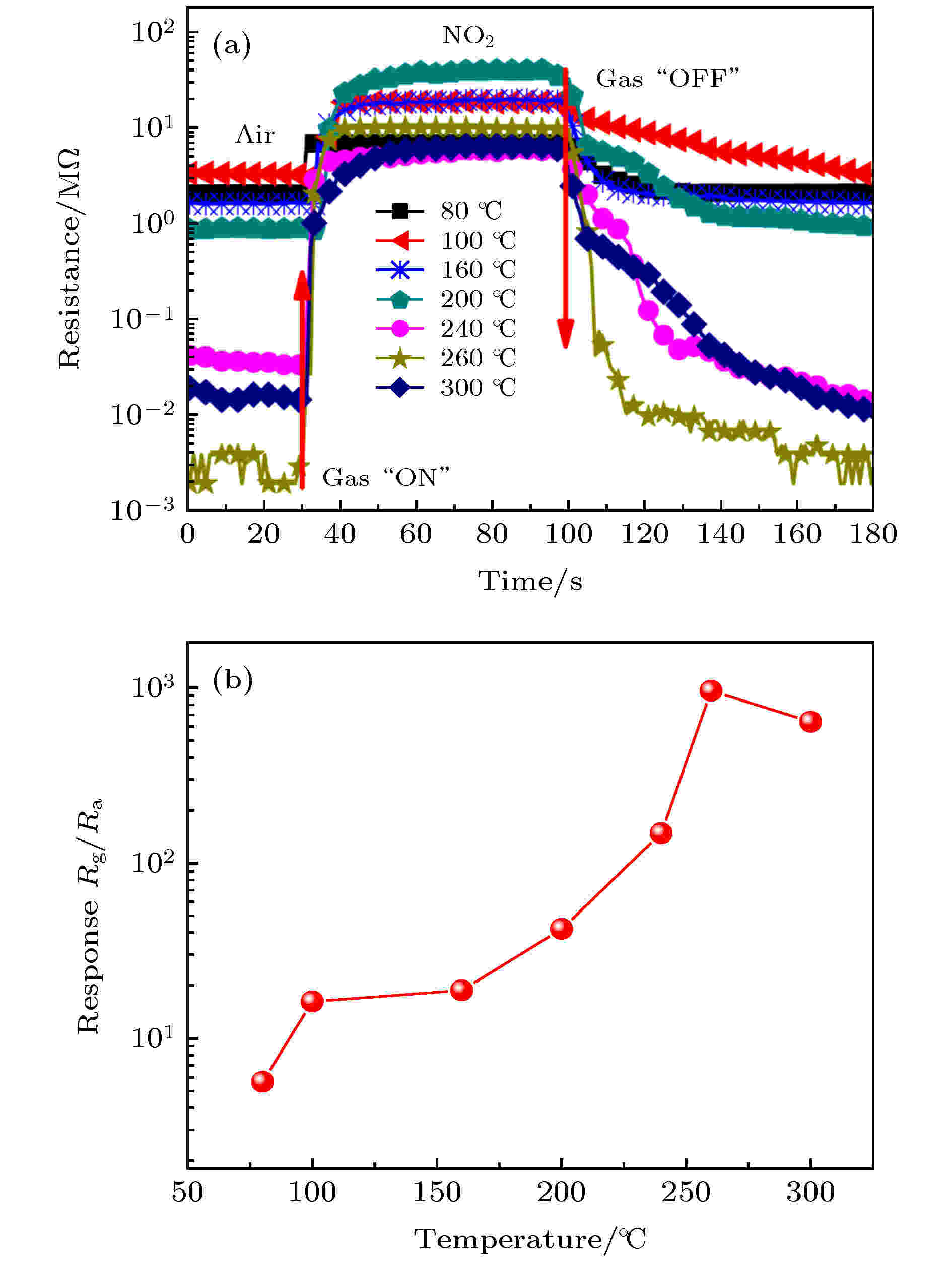
Figure8. Gas response of S4 as a function of temperature: (a) Typical response and recovery curves at different working temperatures; (b) gas response to 50 ppm NO2 at different working temperatures.
为测试Fe掺杂多孔In2O3传感器(样品4)在不同浓度NO2气体中的响应及恢复特性, 实验过程中往测试箱中通入不同浓度的NO2气体. 图9所示为传感器在260 ℃工作温度下对浓度分别为 5, 10, 30, 50 和 100 ppm的NO2气体的响应-恢复曲线. 将传感器上升或下降总阻值变化量的90%所需的时间分别定义为响应时间和恢复时间. 图9(a)给出了传感器随时间变化的响应-恢复特性, 可以看出元件在整个测试浓度范围内都有很好的响应, 说明该材料具有很大的浓度测试范围. 当 NO2气体浓度为5 ppm时, 传感器有较大响应, 说明制备的传感器可用于检测低浓度的 NO2气体. 图9(b)则更为清晰地反映了260 ℃时传感器在气体浓度为50 ppm环境中的响应和恢复特性. 在通入NO2气体时, 传感器的响应时间在5 s左右; 关断气体时, 传感器的恢复时间为6 s左右. 这说明该传感器的响应-恢复时间极短, 性能较好.
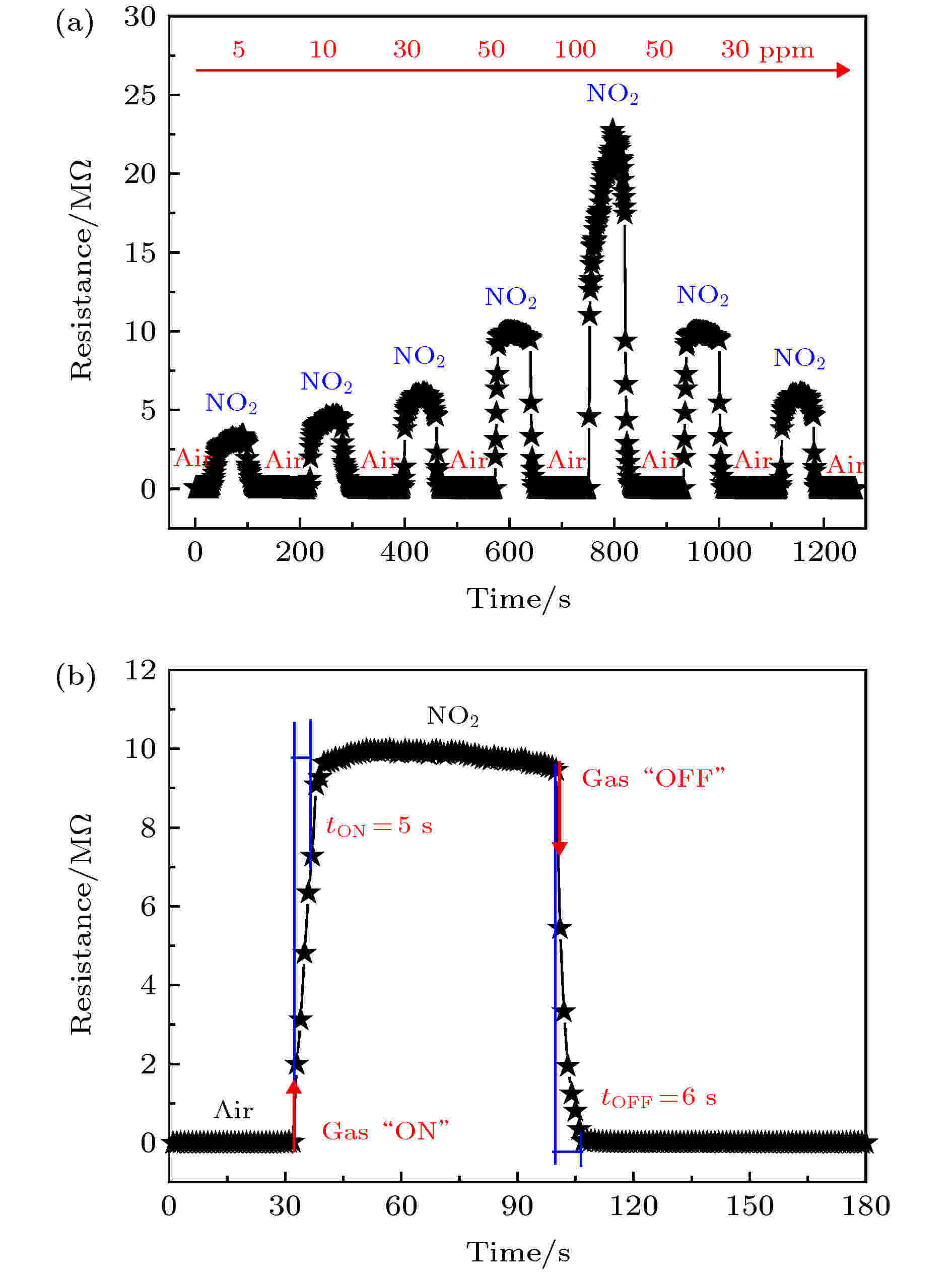
Figure9. Gas response-recovery of the sensor based on S4 exposed to NO2 at 260 °C: (a) Gas concentrations ranging from 5 ppm to 100 ppm; (b) gas concentration is 50 ppm.
一种实用的传感器必须具有显著的选择性, 即在多种气体中只对某一种气体具有相对很强的响应, 用以表现传感器的交叉干扰特性. 图10为Fe掺杂多孔In2O3 (样品4)传感器放置在浓度同为50 ppm的几种常见干扰气体中表现出来的响应情况, 被测气体包括汽油、甲醛、硫化氢、二氧化氮、氯气、氨气、丙酮和甲苯. 由图10可得该传感器对NO2气体的灵敏度值最高, 远远高于其他气体, 元件对氨、丙酮和甲苯三种气体几乎无响应, 可见制备的Fe掺杂In2O3 对NO2气体具备优秀的选择性.
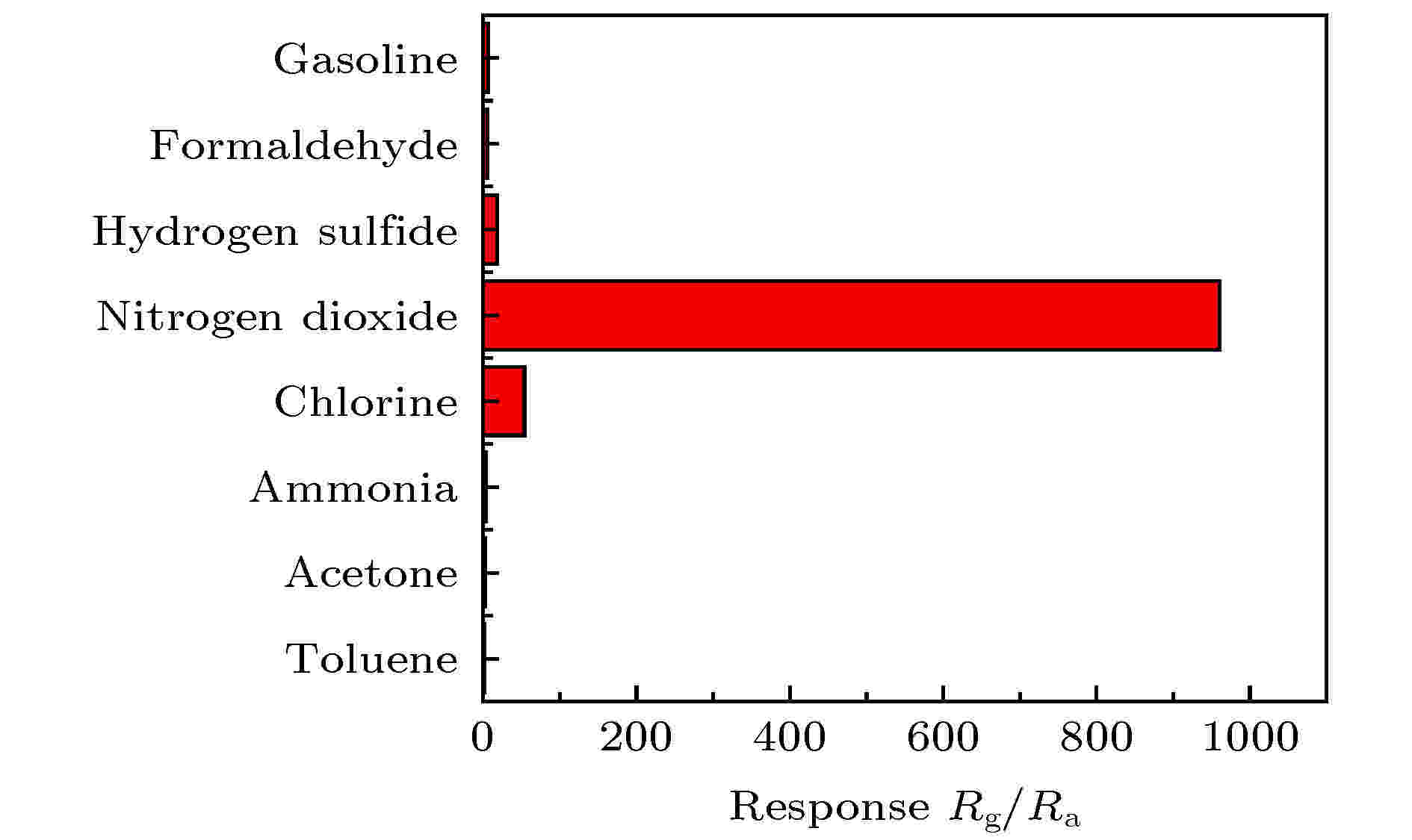
Figure10. Selectivity of S4 to different test gases with a concentration of 50 ppm at 260 °C.
最后, 对由Fe掺杂多孔In2O3制备的传感器(样品4)进行了为期90 d的稳定性测试, 分别在第1, 3, 7, 15, 30, 60和90 d时进行了多次测试, 所得结果如图11所示. 测试过程中发现传感器的灵敏度随时间有降低的趋势, 可以看出, 即使在90 d之后, 该传感器对NO2气体仍保持很高的灵敏度值, 表明该传感器具有良好的稳定性.
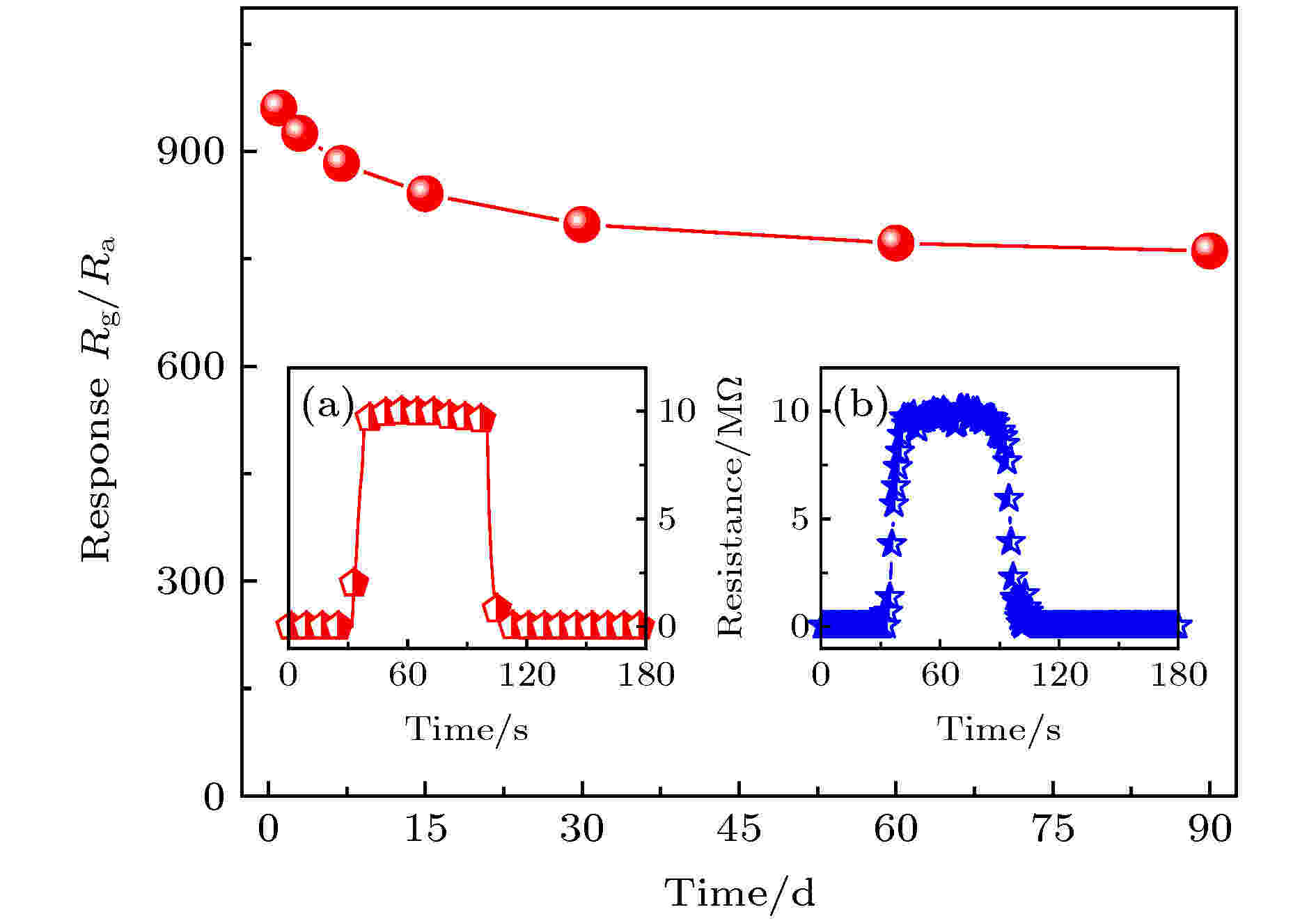
Figure11. Stability of the Fe-doped In2O3 structures (S4) sensor to NO2 with a concentration of 50 ppm at 260 °C (inset: gas response of S4 for (a) the first day and (b) the 90th day).
2
3.4.传感机理
In2O3的传感机理通常认为和材料表面的化学反应相关[24,25]. 作为N型半导体材料的In2O3, 掺铁后会导致其内部有更多的氧空位和金属原子等点缺陷, 从而增加了能导电的自由电子. 传感器在待测气体中电阻值发生变化是传感的基本机理, 而其阻值变化主要是由气体分子在传感器表面的吸附/脱附反应引起的. 当掺铁In2O3纳米晶粒刚开始暴露于空气之中时, 空气中的氧分子和传感器材料表面的自由电子结合形成氧离子[5,26], 如图12(a)和图12(b)所示, 这些带负电离子在晶粒表面形成一层薄的耗尽层, 增加了势垒高度, 进而增加了传感器的表面电阻. 当传感器表面暴露在测试箱中的NO2气体环境中时, 亲电子的NO2分子附着在样品表面并俘获更多In2O3导带中的电子从而在靠近表面区域形成更厚的耗尽层, 这使得样品表面的电阻率进一步增加, 这一机理的具体反应式如下[27-29]: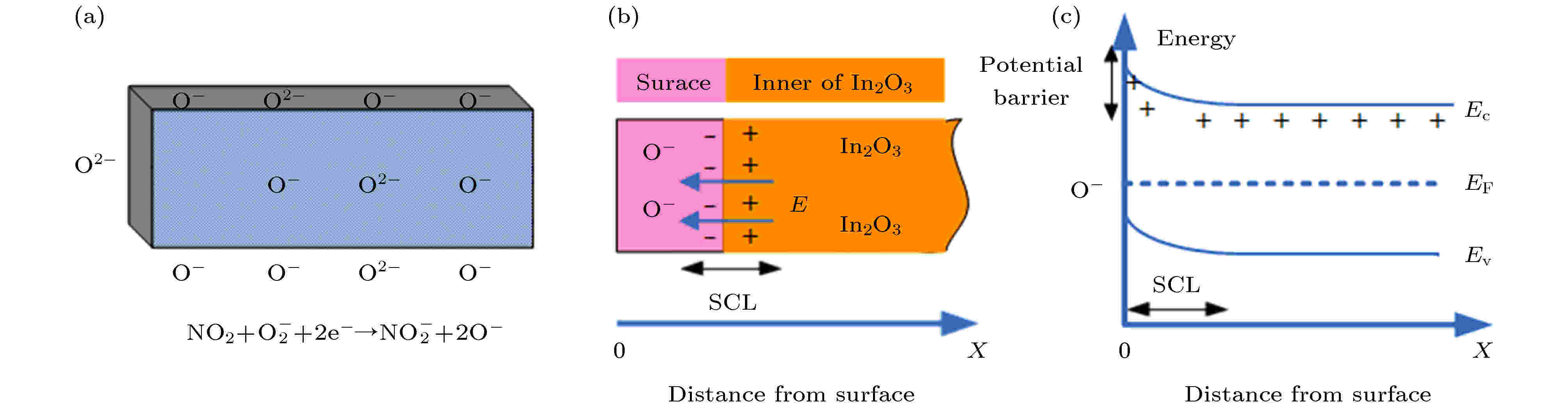
Figure12. (a) Schematic diagram; (b) gas sensing mechanism; (c) the band diagram.
除样品的表面积之外, 另外一个影响传感特性的主要因素是Fe掺杂. Fe的加入除了引起缺陷外还可能会导致In2O3禁带宽度变化, 继而影响自由电子数量, 最终引起表面电阻值变化. Fahed等[30]通过Fe掺杂得到的In1.95Fe0.05O3和In1.78Fe0.22O3的禁带宽度分别为0.44和0.5 eV, 远小于In2O3的禁带宽度2.8 eV, 这表明Fe的掺杂导致In2O3的能隙禁带宽度降低. 而较小的禁带宽度意味着电子更容易从价带跃迁到导带成为自由电子. 在测量时, NO2气体和更多的自由电子结合的概率增加并引起材料阻值发生更大变化, 从而使得传感器灵敏度增强.