全文HTML
--> --> -->已有的研究表明, 氮掺杂在某些热处理条件下可以有效地抑制CZ硅单晶中位错的滑移[12-17]. Mezhennyi等[16,17]通过在500—800 ℃条件下进行的四点弯曲测试, 揭示了CZ硅单晶中浓度超过1.6 × 1014 cm–3的氮掺杂可以提高位错滑移的临界切应力, 并认为掺入的氮杂质促进了氧沉淀的形成从而抑制位错的滑移. Yonenaga[12]则通过三点弯曲测试, 证明了浓度为6 × 1015 cm–3的氮掺杂在650—900 ℃均能导致CZ硅单晶中的位错被有效地钉扎, 并将之归因于氧、氮原子在位错核心处相互作用而形成作为钉扎中心的氮-氧(N-O)复合体. 然而, 他们发现当温度超过900 ℃时, 氮掺杂导致的位错钉扎效应显著减弱.
人们对锗掺杂抑制CZ硅单晶中的位错滑移也进行了研究. Fukuda和Ohsawa[18]报道了在锗浓度低于3 × 1020 cm–3的硅外延层(不含氧杂质)中的位错在900 ℃下的滑移行为几乎不受锗浓度的影响; 而在衬底硅片中, 位错滑移长度随锗浓度从6 × 1019 cm–3上升至3.7 × 1020 cm–3而有所减小, 他们认为这是锗原子与近邻位置的氧原子相互作用, 产生了对位错的钉扎效应. Yonenaga[19]发现: 在800 ℃, 锗掺杂浓度在6—9 × 1019 cm–3时不能有效钉扎CZ硅中的位错, 仅当锗浓度进一步提升至1 × 1020 cm–3以上时, 位错滑移的临界应力略有增加. Chen等[20]发现1018 cm–3以上的锗掺杂就能够降低CZ硅中位错在1100 ℃的滑移长度. Taishi等[21]通过使用含有9 × 1019 cm–3锗杂质的籽晶成功实现了CZ硅单晶的无缩颈生长, 表明锗掺杂在接近硅熔点(约1420 ℃)的温度可以显著抑制位错的产生和滑移.
总之, 氮掺杂和锗掺杂在各自特定的温度范围内能抑制CZ硅单晶中位错的滑移, 从而提高硅片的机械强度. 为了满足ICs的发展对硅片机械强度提出的更高要求, 本文提出在CZ硅单晶中同时掺入锗和氮两种杂质来改善机械强度的思路. 通过对比研究普通的、单一掺氮的、单一掺锗的、锗和氮共掺的直拉硅片在室温和650—1200 ℃温度范围内的位错行为, 探明锗和氮共掺对硅片机械强度的影响. 基于实验结果, 阐述了锗和氮掺杂对位错滑移行为影响的相关机制.

硅片 | 杂质 | ||
[Ge]/(1019 cm–3) | [N]/(1014 cm–3) | [Oi]/(1017 cm–3) | |
CZ | — | — | 7.9 |
GCZ | 2.8 | — | 8.1 |
NCZ | — | 9.0 | 8.1 |
GNCZ | 2.0 | 8.1 | 8.0 |
表1实验所采用的硅片中的杂质浓度
Table1.Concentrations of impurities in the silicon wafers used.
分别从上述4种硅片切下若干1.5 cm × 1.5 cm的方形样品, 在Struers TegraForce-5抛光机上进行单面化学机械抛光. 随后采用Agilent Nano Indenter? G200纳米压痕系统对各样品进行测试. 这里, 采用三棱锥型Berkovich压针, 并保证压针的一面与样品表面的某一

为探究在600—750 ℃的位错滑移行为, 先从4种硅片上取下长宽沿

通过压痕诱生位错滑移的方法探究位错在900—1200 ℃下的滑移行为. 从上述4种硅片取下的样品经化学机械抛光后, 分别在如上所述的维氏硬度仪上进行载荷为100 g的压载, 以形成微米压痕. 如此, 在每个样品上施加30个微米压痕, 随后将样品置于石英管热处理炉中, 分别进行氩气氛下的900 ℃/2 h, 1000 ℃/1 h, 1100 ℃/1 h和1200 ℃/1 h热处理. 最后, 经过上述热处理的样品在Yang 1腐蚀液择优腐蚀10 min后, 采用OM观察位错的滑移并进行拍照.
3.1.常温硬度
图1(a)给出了4种样品经纳米压痕测试所得的一组典型载荷-位移(P-h)曲线. 可以看到, CZ, GCZ, NCZ和GNCZ样品的P-h曲线几乎是相同的. 各样品的P-h曲线均出现了加载突进(pop-in)和卸载突退(pop-out)的特征, 如图1(b)所示. 其中, 加载段曲线中显著的pop-in是由Si-I相转变为亚稳的Si-II相引起的, 而轻微的pop-in则被认为与加载过程中位错滑移系的开动有关[22]. Pop-out则由Si-II 相进一步转变为Si-III/Si-XII相引起[23], 图1(a)中的pop-out还带有扭结型(kink)特征, 这与部分Si-II 相在卸载过程中转变为非晶α-Si相有关[24]. 以往的透射电子显微镜观察证实: 在纳米压痕下方不仅存在上述几种硅亚稳相, 而且在相变区域的下方存在含有高密度滑移位错的塑性变形区[25,26]. 本工作所采用的载荷较大(约500 mN), 因此压痕下方的塑性变形应该是显著的. 图1中各样品的P-h曲线均存在很相似的pop-in和pop-out的特征, 因此可以认为各样品中形成的亚稳相几乎不存在差异, 它们对基体塑性变形的影响可视为相同. 值得注意的是, 4种样品的压针位移随载荷的变化行为几乎相同, 意味着它们的相变和塑性变形的行为几乎相同. 总之, 上述结果表明: 单一的锗掺杂或氮掺杂以及锗和氮两种杂质的共掺几乎不会对CZ硅片在室温纳米压痕过程中的相变和位错滑移产生影响.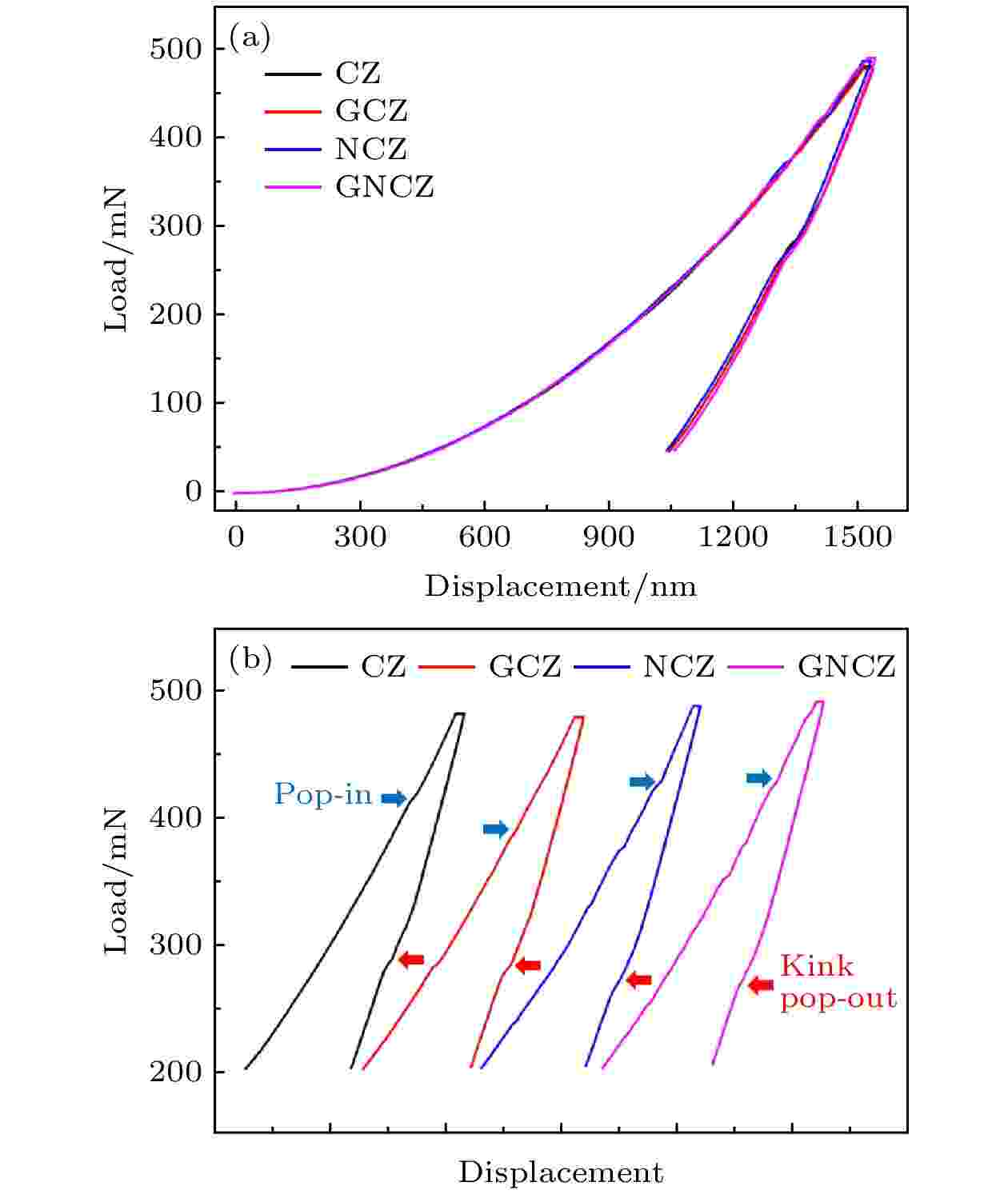
Figure1. (a) Representative P-h curves of CZ, GCZ, NCZ, GNCZ silicon specimens under nanoindentation; (b) segments of the P-h curves with features of phase transformation for CZ, GCZ, NCZ, GNCZ silicon specimens (the curves are deliberately shifted for visual discrimination).
对图1中所示的P-h曲线中的卸载段进行幂函数拟合可得样品的纳米压痕硬度值[27]. 图2给出了各样品的纳米压痕硬度的平均值及其标准差. 这里需要说明的是, 对每个样品而言, 从5条P-h曲线中的卸载段拟合推导出5个纳米压痕硬度值, 然后作统计分析. 从图2可以看到, GCZ样品的硬度值最低, 为10.98 GPa; GNCZ样品的硬度值最高, 为11.34 GPa, 但仅比GCZ样品的大3.3%. 考虑到纳米压痕测试的系统误差和偶然误差, 上述差异被认为可以忽略. 进一步地, 对各样品进行了维氏硬度的测试, 在每个样品上施加50个维氏压痕, 得到相应的维氏硬度. 图2(b)为各样品的维氏硬度平均值及其标准差. 可以看出, GNCZ样品的硬度值为11.41 GPa, 仅比CZ样品的11.17 GPa大2.1%, 这样的差异在测量的误差范围之内. 需要指出的是, 维氏硬度的计算是基于压痕卸载后经弹性恢复后的残余变形量, 而纳米压痕硬度的计算则是基于玻氏压针在最大压载深度处的变形量, 这可能是导致维氏硬度比纳米压痕硬度稍大的原因. 总之, 纳米压痕硬度和维氏硬度的测试结果表明: 单一的锗掺杂或氮掺杂以及锗和氮两种杂质的共掺对直拉硅片的常温机械强度几乎没有影响.
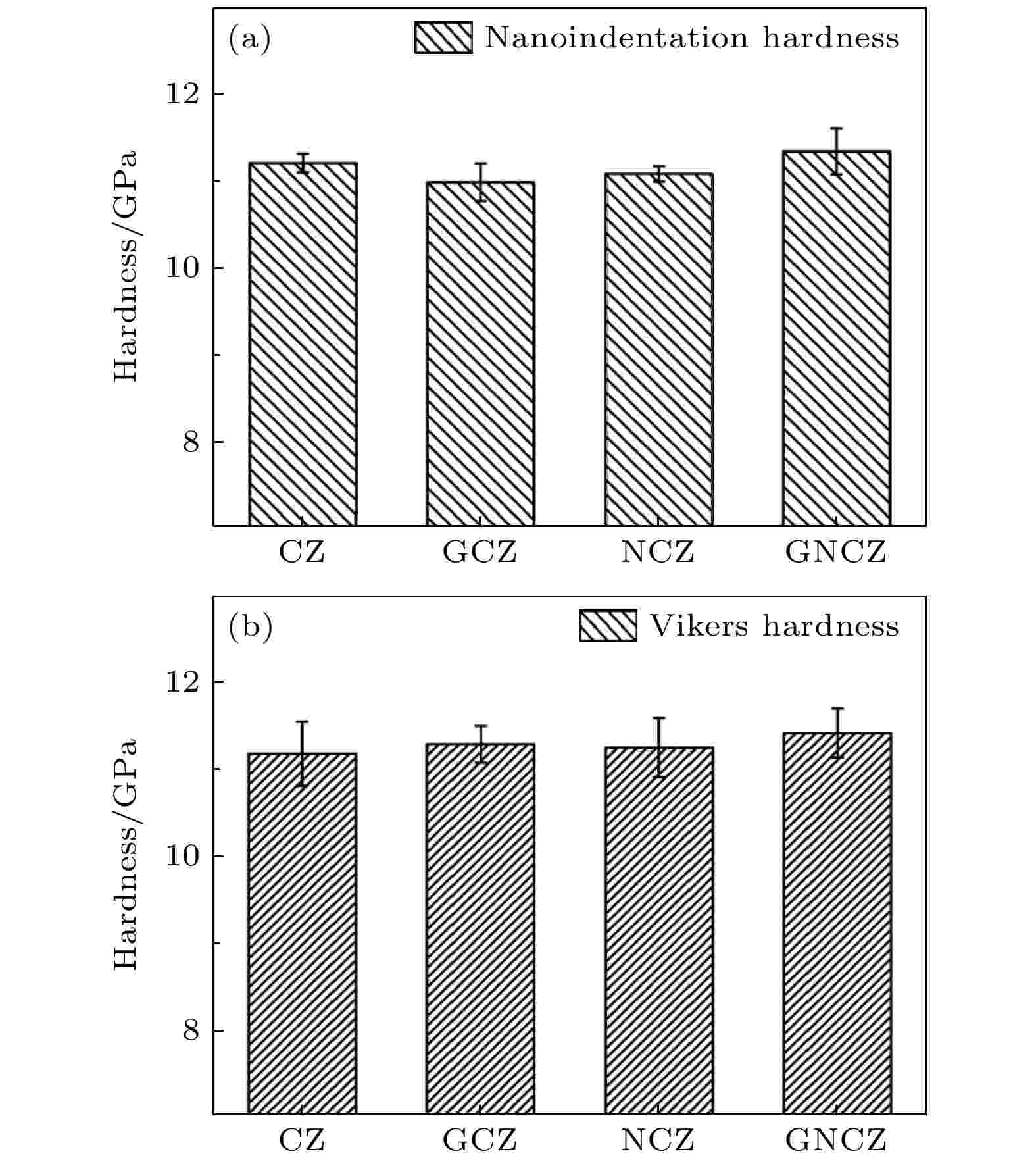
Figure2. Average values and standard deviations of the (a) nanoindentation hardness and (b) Vikers hardness of CZ, GCZ, NCZ and GNCZ silicon specimens.
2
3.2.三点弯曲加载下的位错滑移
考察了带有划痕的CZ, GCZ, NCZ和GNCZ样品在600, 650, 700和750 ℃施加三点弯曲时的位错滑移行为. 在三点弯曲加载状态下, 位错从划痕损伤处产生, 继而在硅片近表面区域沿着
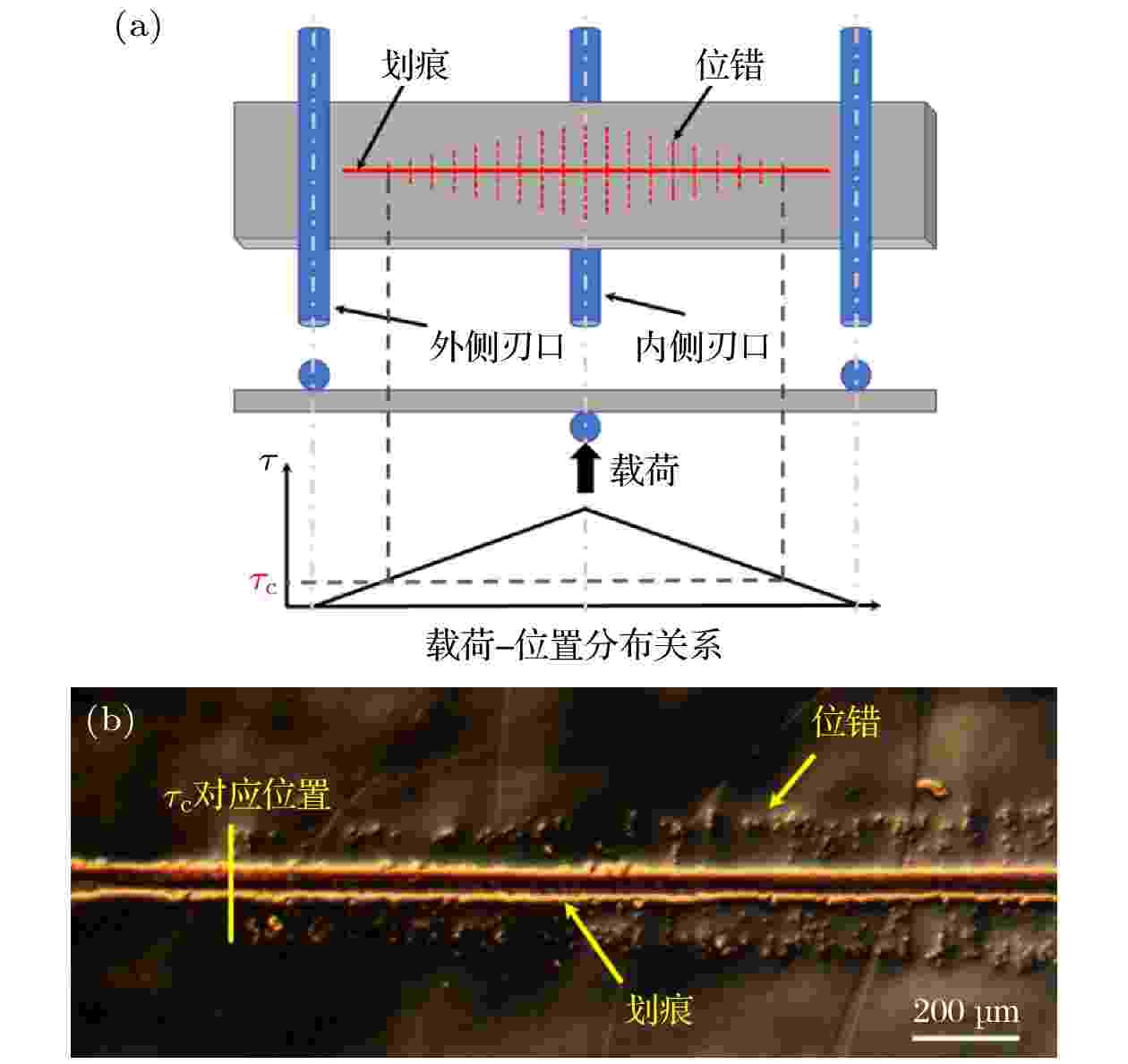
Figure3. (a) Schematic diagram of three-point bending unit and the dependence of load on the position under a given loading; (b) regional OM image of the conventional CZ silicon specimen subjected to three-point bending at 650 ℃ for 25 min and subsequent preferential etching.


由于位错滑移是热激活过程, 滑移速率(Vg)和外加的分切应力τ的关系可以表示为
CZ | GCZ | NCZ | GNCZ | |
Q /eV | 2.12 | 2.10 | 2.07 | 2.00 |
表2CZ, NCZ, GCZ, GNCZ样品的位错滑移激活能
Table2.Activation energy of dislocation gliding in CZ, NCZ, GCZ and GNCZ silicon specimens.
由(2)式可知, 位错滑移速率与施加的分切应力成正比. 然而, 位错开始滑移实际上存在一个临界切应力(τc). 仅当外加切应力大于τc时, 位错才会在划痕损伤处脱离钉扎而发生滑移[32]. 图3(b)为普通CZ样品在650 ℃三点弯曲加载25 min并经择优腐蚀后的OM照片. 该照片显示的是样品某一长度内的位错自刃口处出发的滑移情况. 位错滑移的终止处就是外加切应力对应于τc的位置, 测出该位置与外侧刃口的距离x, 根据(1)式即可以算得到τc值.
对4种样品在600—750 ℃三点弯曲加载时位错滑移的终止位置进行测量, 根据(1)式计算所得的位错滑移临界切应力τc如图4所示. 可以看到, 在600—700 ℃的温度范围内, 各样品的τc随着温度的升高而明显下降; 继续升高至750 ℃, CZ和GCZ样品的τc进一步下降, 而NCZ和GNCZ样品的τc变化则很小. 总体上, NCZ和GNCZ样品的τc值接近, 且明显高于CZ和GCZ样品的τc值. 特别是在750 ℃, CZ和GCZ样品的τc值(分别是3.9和3.3 MPa)只有NCZ和GNCZ样品τc值(分别是7.1和7.8 MPa)的50%左右.
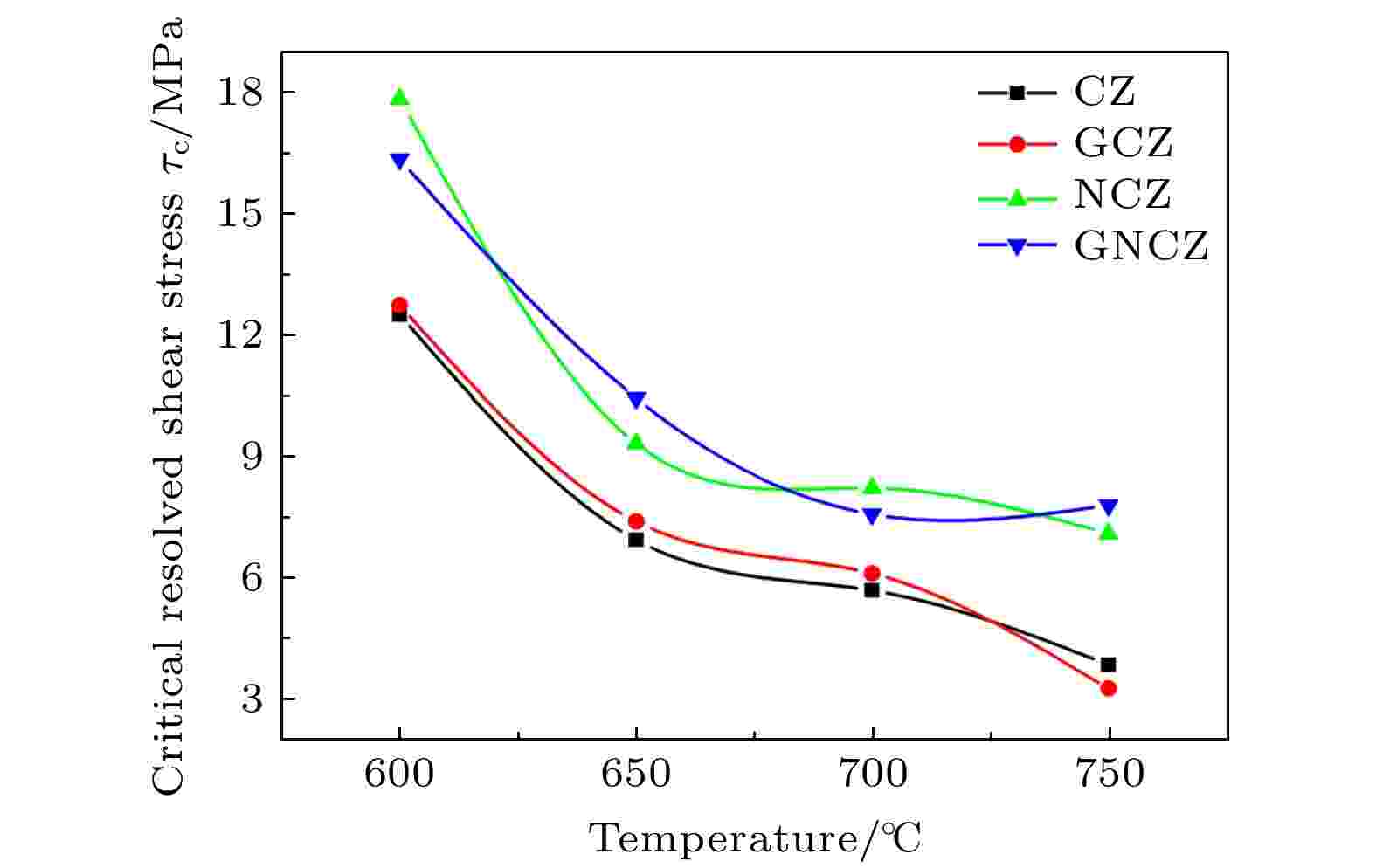
Figure4. Critical shear stresses of dislocation gliding in CZ, GCZ, NCZ and GNCZ silicon specimens at temperature in the range of 600?750 ℃.
通常而言, 位错滑移的临界切应力τc由两部分组成, 即晶格势垒阻碍位错运动造成的应力(τSi); 杂质或与杂质相关的钉扎中心与位错发生交互作用而产生的钉扎应力(τimpurity)[19]. 因此, τc = τSi + τimpurity. 对于CZ, GCZ, NCZ和GNCZ样品而言, 由于位错滑移的运动方式没有差异, τSi可视作相同, 因而上述样品τc间的差异主要取决于由杂质或其衍生缺陷形成的钉扎中心所引起的τimpurity的大小差异. 从图4给出的结果来看, 氮掺杂促进了位错钉扎中心在600—750 ℃的形成, 因而显著提高τimpurity; 而锗掺杂在该温度范围内对位错滑移几乎没有钉扎效应.
由于氮在硅中的浓度很低, 且单一的氮原子和位错的交互作用能较小, 因此孤立的氮原子无法有效钉扎位错. 但是, 硅中的位错可以有效吸收扩散进来的杂质, 并为不同杂质间的反应或相互作用提供位点. 已有研究表明: 氮和氧杂质经扩散被位错吸收后, 可以发生相互作用形成所谓的N-O复合体, 这些复合体可作为位错的“钉扎中心”[12-14]. 此外, N-O复合体可以在650—1100 ℃这一较宽的温度范围内形成[33,34]. 就本文实施的三点弯曲加载而言, 在样品表面会预先引入划痕损伤作为位错源, 随后进入炉管升温至目标温度(650—750 ℃)并保温一段时间(约20 min), 然后实施加载. 在这一前置的热过程中, N-O复合体在NCZ和GNCZ样品的划痕损伤位错处得以形成. 尽管退火时间较短, 但以N-O复合体为异质形核中心而形成极小氧沉淀也是有可能的[35]. 在后续的三点弯曲加载过程中, N-O复合体及可能衍生出的极小氧沉淀可以有效地钉扎位错. 因此, 与CZ和GCZ样品相比, NCZ和GNCZ样品的τc得到显著的提高. 需要特别说明的是, 当温度从700 ℃升高至750 ℃时, 一方面氮和氧杂质扩散速率的增大使得位错核心处N-O复合体的形成更加显著, 从而增强位错的钉扎效应; 另一方面热激活所导致的位错脱钉也得到增强. 上述两方面相反的效应使得NCZ和GNCZ样品在700和750 ℃时的τc没有显著的差异.
2
3.3.压痕位错的滑移
当温度在800 ℃及以上时, 硅单晶的塑性特征已十分显著. 在这种情况下, 无法采用三点弯曲加载的方法研究位错滑移. 为研究位错在800 ℃及以上温度的滑移行为, 我们采用微米压痕、热处理和择优腐蚀相结合的手段, 即: 首先在室温下利用维氏硬度仪在硅片表面引入压痕, 然后在某温度(800—1200 ℃)下热处理一定的时间, 经择优腐蚀后显微观察始于压痕的位错滑移情况. 在微米压痕卸载后, 压痕对角线尖端处会产生径向裂纹, 其中的残余应力超过某一温度的位错滑移临界切应力时, 将驱动位错沿着



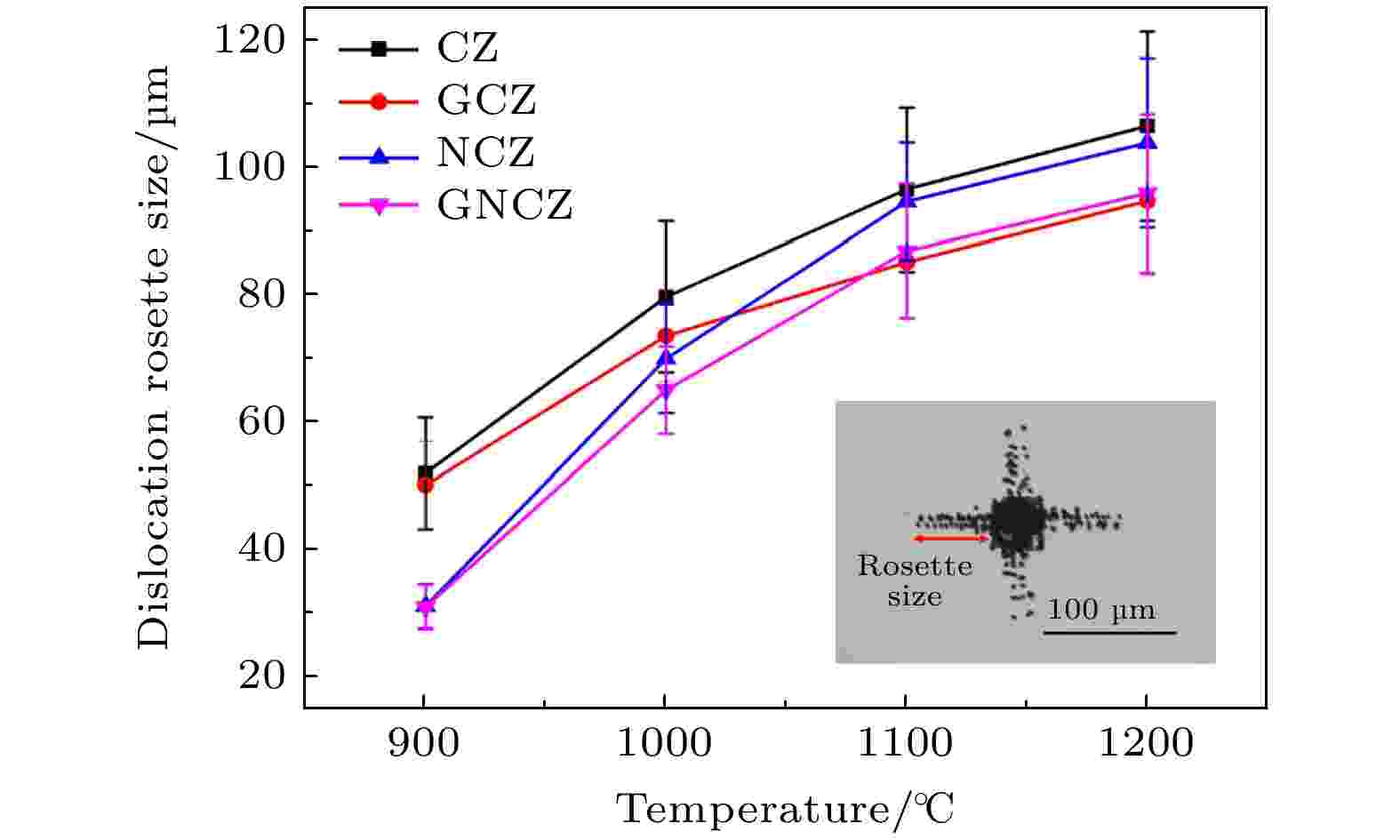
Figure5. Statistical results for the dislocation rosette sizes in the indented CZ, GCZ, NCZ and GNCZ silicon specimens annealed at 900?1200 ℃
对4种样品分别经900 ℃/2 h, 1000 ℃/1 h, 1100 ℃/1 h和1200 ℃/1 h热处理后形成的30个rosette的尺寸进行统计分析, 结果如图5所示. 可以看到, 各样品的rosette尺寸随着退火温度的升高而增大, 表明位错滑移的临界切应力τc随着温度的升高而降低. 在各个温度, CZ样品的rosette尺寸均为最大. 在900 ℃, GCZ样品的rosette尺寸与CZ样品的几乎相等, 表明锗掺杂几乎没有抑制位错滑移的作用; 而NCZ和GNCZ样品的rosette尺寸接近, 均明显小于CZ和GCZ样品的rosette尺寸, 表明氮掺杂具有显著抑制位错滑移的作用. 当温度为1000 ℃时, GCZ样品的rosette尺寸相比于CZ样品的有明显减小, 表明锗掺杂显示出抑制位错滑移的效应; NCZ样品的rosette尺寸仍然比CZ样品的小得多, 表明氮掺杂抑制位错滑移的效应依然显著; 相比之下, GNCZ样品的rosette尺寸最小, 表明锗掺杂和氮掺杂共同发挥了抑制位错滑移的作用. 在1100和1200 ℃, 氮掺杂对位错滑移的影响情况出现了明显的转折, NCZ样品的rosette尺寸仅略小于CZ样品的, 表明氮掺杂在高温下抑制位错滑移的效应已不再显著; 相反地, GCZ样品的rosette尺寸远小于CZ样品的, 且与GNCZ样品的相近, 这表明锗掺杂在高温下表现出显著的抑制位错滑移的作用. 很显然, 在900—1200 ℃范围内, GNCZ样品中的位错滑移均受到了显著的抑制, 表明锗掺杂和氮杂质抑制位错滑移的效应得到了很好的结合.
当温度为800—1000 ℃时, 在位错处形成的N-O复合体等相关缺陷仍将作为钉扎中心, 抑制位错的滑移. 然而, 从图5可以看到, 在1000 ℃氮掺杂对位错滑移的抑制效应已不如900 ℃时那样显著. 这一方面是由于氮杂质的扩散速率显著增加[36], 导致被位错捕获的氮原子减少; 另一方面, 间隙氧杂质的过饱和度随着温度的上升而减小. 这两方面因素都不利于N-O复合体在位错处的形成, 因而氮掺杂抑制位错滑移的效应有所减弱. 以往的研究表明, 在1000 ℃以上, N-O复合体的形成比较微弱[33]. 因而, 在本文中可以认为位错处N-O复合体的形成在1100和1200 ℃时是很困难的. 这样, 就可理解NCZ样品的rosette尺寸在1100和1200 ℃仅略微小于CZ样品的rosette尺寸, 如图5所示.
对于硅中的锗掺杂, 处在晶格替代位上的锗原子的共价半径比基体硅原子的大约4%, 这将造成晶格弹性畸变而产生应力场. 原则上, 位错与锗原子可以通过弹性应力场发生交互作用. 然而, 这一交互作用的能量很低. 理论计算结果表明, 在730 ℃下锗原子与位错间的交互作用仅能达到0.25 eV[37]. 还有计算表明, 对于硅中的替位原子, 即使引起很大的晶格畸变, 单个原子与位错的交互作用能一般也不会超过0.5 eV[38]. 显然, 锗原子本身与位错间的交互作用能很小, 不会引起显著的位错钉扎效应. 另一方面, 本文中GCZ样品的锗浓度低于0.2% (原子百分比), 再者, 即使在高温下替位锗原子的扩散速率也很小, 因此在GCZ样品中难以形成与锗相关的固溶气团来钉扎位错[39]. 因此, 可以理解锗掺杂在较低的温度(600—900 ℃)不能有效钉扎位错. 但是, 在1000 ℃及以上温度时, 如图5所示, 锗掺杂显著抑制了位错滑移. 我们初步认为这是由于在位错运动路径上形成了可以作为位错钉扎中心的锗-氧(Ge-O)复合体. 为解释方便起见, 从刃位错滑移的角度来阐述: 在正常晶格中, Ge-O复合体较难形成, 这是由于氧原子偏聚在锗原子周围将引起晶格畸变, 造成自由能上升[40]. 但在有位错的晶格中, 刃位错引入的多余半原子面将在位错的前沿造成拉应力区域, 在此形成Ge-O复合体将使体系的自由能降低. 在1000—1200 ℃下, 间隙氧原子可快速向处在位错前沿拉应力区域附近的锗原子扩散, 并与锗原子发生相互作用形成Ge-O复合体, 成为阻碍位错滑移的中心. 在900 ℃及更低的温度下, 间隙氧原子的扩散速率要小得多, 在位错前沿附近不能有效地形成Ge-O复合体, 因而没有显现抑制位错滑移的效应.