全文HTML
--> --> -->为解决上述问题, 前人进行了大量研究工作, 如调控电解液中锂离子的溶剂化[12-19], 设计人工界面层[20-27], 构筑三维复合负极[28-35], 应用准固态[36-40]和固态电解质[41-47]等. 这些研究既涉及固液界面膜形成机制和金属锂沉积规律等基础层面, 也包含策略优化和材料体系创新等面向实用化的应用层面, 对于加深对金属锂负极的认识具有重要意义, 同时也为实用化金属锂负极的发展奠定了基础.
然而, 以上工作主要采用温和的实验条件以研究和评测金属锂负极, 如厚锂负极(> 200 μm)、高负极/正极面容量比(N/P > 10.0)、高电解液量(> 30.0 g·Ah–1)等. 但高比能金属锂电池的实现要基于实用化条件, 如超薄锂负极(< 50 μm)、低N/P比(< 3.0)、低电解液量(< 3.0 g·Ah–1)等. 现有的一些策略在温和条件下可以提升金属锂电池的循环性能, 但其结果一般难以在实用化条件下的电池中完全复现[48]. 因此, 为了实现稳定循环的高比能金属锂二次电池, 需要深入认识温和以及实用化条件下金属锂负极的差异, 并分析差异产生的原因, 进而为实用化金属锂负极的发展提供参考.
本文详细探究了金属锂厚度、N/P比、电解液量及循环倍率等条件对金属锂负极循环性能、极化电压和表面形貌的影响, 着重分析了差异产生的原因. 在实用化条件下, 应用超薄锂负极和低N/P比时, 活性锂极大减少, 金属锂负极的利用深度(即参与充放电的锂与负极所有活性锂的比例)大幅提高, 愈加不均匀的沉积锂和巨大的体积形变加剧了固液界面膜的破坏和再生; 少量电解液的快速耗尽和大量死锂的急剧生成使得电池极化迅速增加. 在高循环倍率条件下, 金属锂表面电化学反应加快, 不均匀锂沉积与电解液的消耗加剧, 导致锂利用率(脱出锂量/沉积锂量)进一步降低, 电池加速失效. 而在温和条件下, 应用厚锂负极和高N/P比时, 电池的循环容量小、利用深度低, 固液界面膜破坏程度小, 在电解液严重过量的条件下, 极化电压增加较小, 电池循环稳定. 本文揭示了金属锂负极在实用化条件下面临的挑战, 以望促进高能量密度金属锂电池的发展.
2.1.材料制备
金属锂购自天津中能锂业有限公司. 正极极片(镍钴锰酸锂, LiNi0.5Co0.2Mn0.3O2, NCM523)购自广东烛光新能源科技有限公司. 六氟磷酸锂(LiPF6, > 99.9%)购自苏州多多化学科技有限公司. 氟代碳酸乙烯酯(FEC, 98%)和碳酸二甲酯(DMC, 99%)购自阿法埃莎(中国)化学有限公司. 聚丙烯(PP)隔膜型号为Celgard 2400. 所有的材料都置于水氧值均低于0.1 ppm的氩气环境的手套箱中, 并于其中进行电池组装、电解液配制和表征测试样品制备.2
2.2.电池测试
以金属锂为负极, NCM523为正极(Li | NCM523)的全电池组装为CR2032型纽扣电池, 并在蓝电充放电测试仪(武汉蓝电电子股份有限公司)上进行充放电性能测试. 金属锂负极厚度、正极面容量及电解液添加量见下面文中说明.实验中所采用的电解液体系为1.0 mol·L–1 LiPF6溶解于FEC/DMC溶剂中(FEC/DMC体积比为1∶4). 该电解液组成简单并可显著提升锂负极的循环性能, 更能突显出金属锂负极在温和及实用化条件下的区别.
电池测试电压范围为2.8—4.3 V, 在0.1 C (1 C = 180 mA·g–1)下预循环2圈后以0.4 C进行循环(在探究倍率影响的实验中, 部分电池在0.2 C条件下进行循环).
2
2.3.材料表征
在5.0 kV下使用扫描电子显微镜(SEM, 日本电子株式会社, JEOL)对负极表面的沉积形貌进行表征. 表征前用DMC纯溶剂对金属锂负极表面进行冲洗, 之后将其置于手套箱内晾干. 在转移到SEM的腔室过程中, 样品置于充满氩气的盒子中, 避免与空气的接触.2
3.1.金属锂负极厚度
金属锂作为电池的负极材料, 直接影响着电池的循环性能. 过量的金属锂可显著提升电池循环性能, 但会导致电池能量密度下降, 尤其是体积能量密度, 同时也会增加电池的安全风险, 与实用化金属锂电池的要求不符[49]. 目前, 大多数纽扣电池中采用厚锂负极(> 200 μm, 40 mA·h·cm–2). 对于实用化金属锂电池, 采用超薄锂负极(< 50 μm, 10 mA·h·cm–2)才有望获得高能量密度的新体系电池. 因此, 分析锂负极厚度对电池循环性能的影响, 解析薄锂条件下电池失效原因非常重要.本文分别采用33, 50, 600 μm金属锂作为电池负极以探究锂负极厚度对电池循环的影响(图1(a)). 在电池其他参数一致的情况下, 电池循环性能随着金属锂负极厚度的降低显著下降, 600 μm锂负极可稳定循环130圈, 50 μm锂负极可稳定循环82圈, 33 μm锂负极仅循环65圈(以初始容量的80%保持率为基准, 下同, 图1(b)). 随循环进行, 应用33 μm锂负极电池的极化电压增长迅速, 循环60圈后, 其放电中值电压比应用600 μm锂负极电池的放电中值电压低68 mV (图1(c)), 表明薄锂负极电池内阻增加迅速.
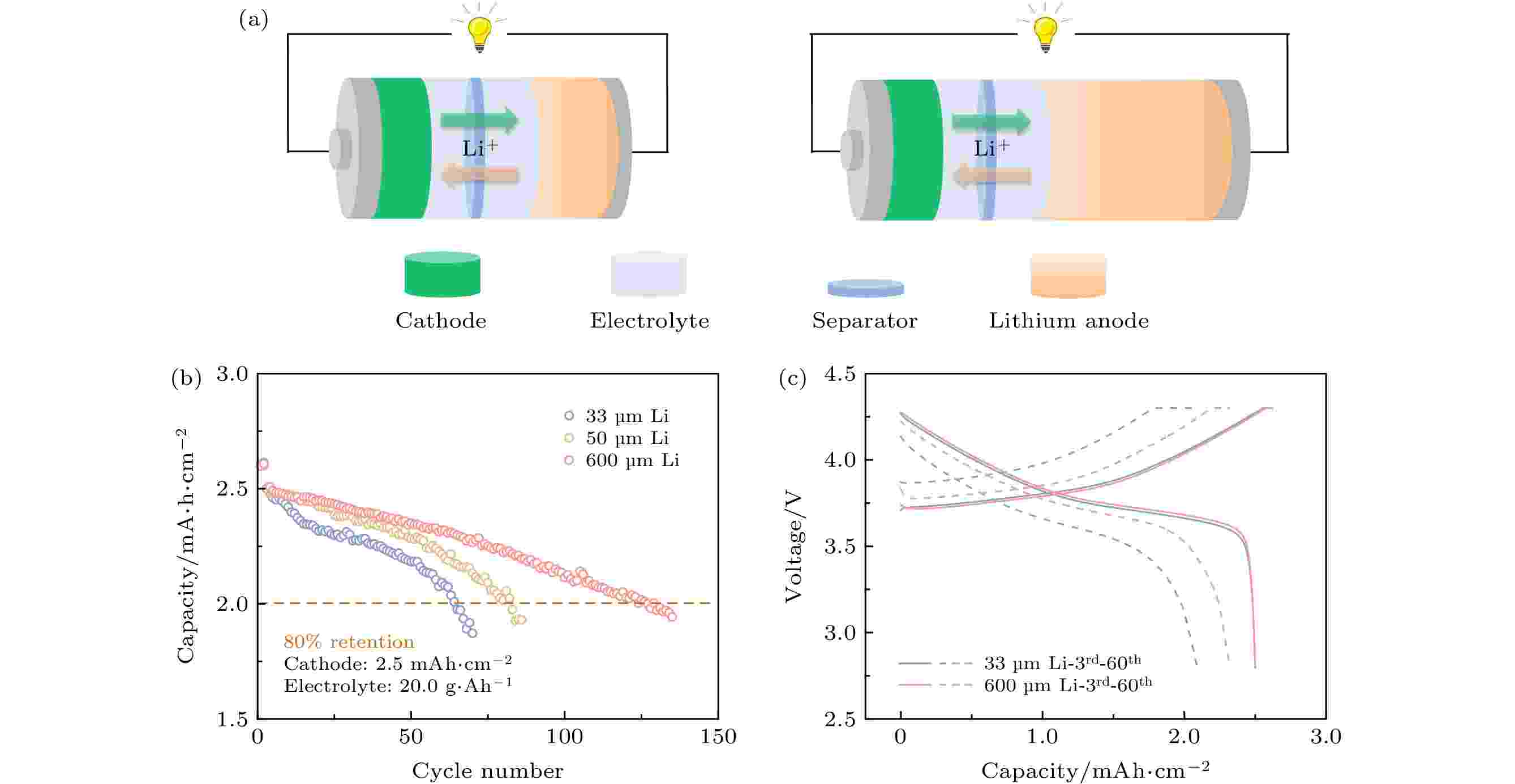
Figure1. The effect of the thickness of Li metal anode on the cycling of batteries: (a) The schematics of batteries with Li metal anode in different thicknesses; (b) the cycling performance of Li | NCM523 batteries; (c) the corresponding charge and discharge curves of Li | NCM523 batteries at the 3rd and 60th cycle.
为了探究负极厚度对金属锂沉积行为的影响, 本文采用扫描电子显微镜(SEM)对循环后的金属锂表面形貌进行分析. 循环5次后, 薄锂表面有枝晶状沉积锂出现, 且金属锂部分粉化, 而厚锂表面沉积锂形貌平整光滑(图2(a)和图2(b)). 当循环容量增加到3.0 mA·h·cm–2, 薄锂表面沉积锂的枝晶行为明显, 而厚锂负极表面沉积锂仍然致密, 两者表现出的沉积形貌差异更加显著(图2 (c),(d)).

Figure2. The effect of the thickness of Li metal anode on the morphology of Li deposition: The morphology of the deposited Li in Li | Li symmetrical cells at (a, b) a current density of 1.0 mA·cm–2 and a capacity of 1.0 mA·h·cm–2, and (c, d) a current density of 3.0 mA·cm–2 and a capacity of 3.0 mA·h·cm–2. The thickness of the Li anode is 600 μm in (a, c) and 50 μm in (b, d).
金属锂厚度不同造成的主要区别为活性锂的剩余量不同[49,50]. 在相同且过量的电解液和相同的循环容量条件下, 单次循环锂的利用率差别较小. 在超薄锂负极的活性锂耗尽时, 厚锂负极仍存在有大量活性锂. 因此, 超薄锂负极失效的主要原因为活性锂的耗尽, 而厚锂负极电池失效的主要原因是死锂积累造成的电池极化增加. 另外, 在有限体积内, 电池施加在厚、薄锂负极表面的压力不同, 厚锂的应用使得施加在负极表面的压力增大. 近期研究表明, 增大电池施加在锂负极表面上的压力有助于锂的均匀沉积, 从而进一步提升电池循环性能[51,52]. 因此, 薄锂负极失效的真实原因不同于厚锂负极, 采用薄锂评测负极保护策略的可行性符合实用化金属锂电池的发展要求.
2
3.2.N/P比
N/P比是电池设计和能量密度计算中的一个重要的参数, 在金属锂电池中, N/P比过大会损失电池的能量密度[53,54]. 本文设计N/P比分别为1.6(负极面容量为6.6 mAh·cm–2, 正极面容量为4.0 mAh/cm2)和120(负极面容量为120 mAh/cm2, 正极面容量为mAh/cm2)两种构型的电池(图3(a)). 当N/P比由120缩减到1.6时, 电池的循环性能由稳定循环350圈锐减至60圈(图3(b)), 电池的循环性能与N/P比成正相关. 此外, 循环50圈后, 低N/P比电池的放电中值电压比高N/P比电池的放电中值电压低290 mV (图3(c)), 在低N/P比条件下, 电池内阻的增加更为迅速.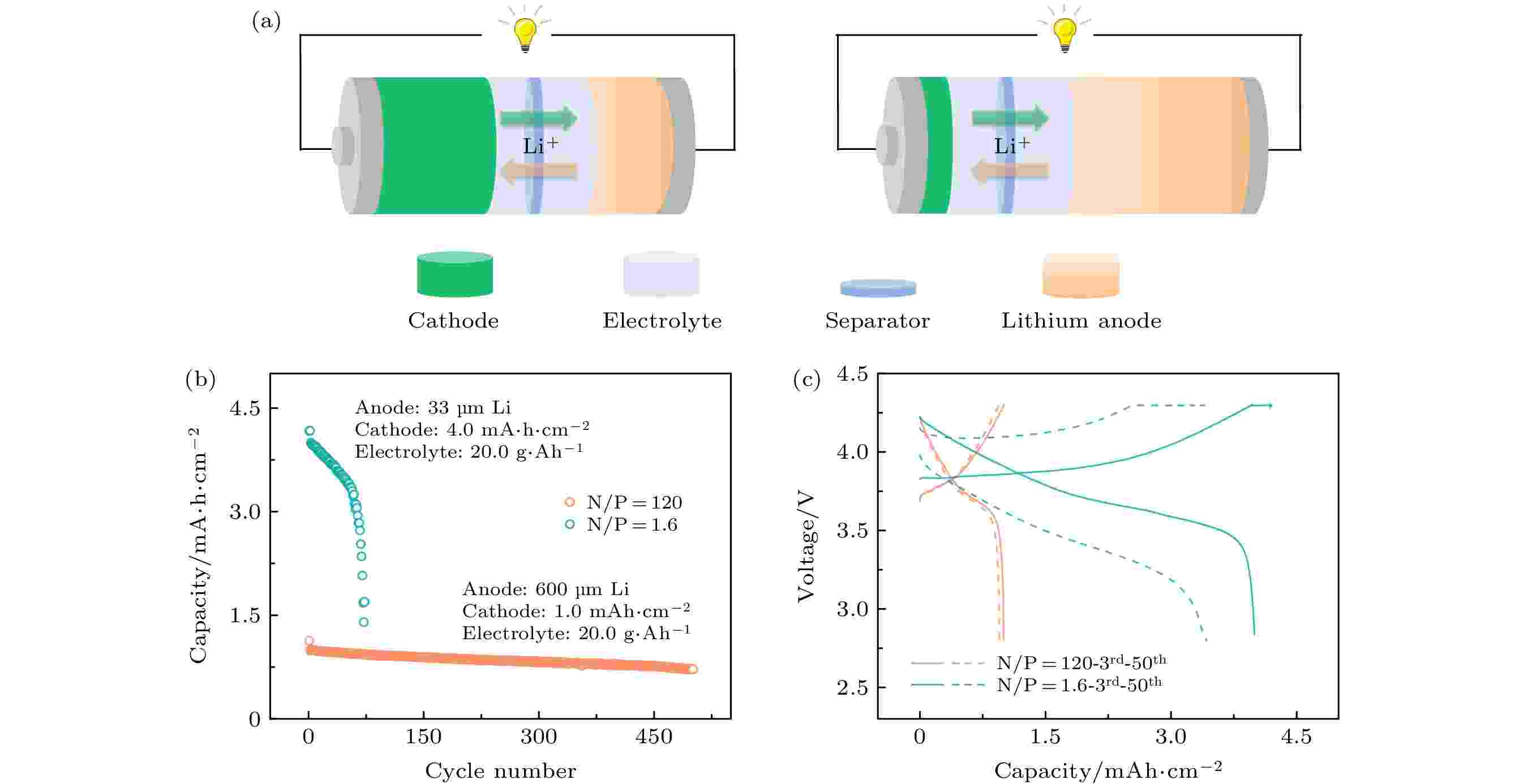
Figure3. The effect of the N/P ratio on the cycling of batteries: (a) The schematics of batteries with different N/P ratios; (b) the cycling performance of Li | NCM523 batteries; (c) the corresponding charge and discharge curves of Li | NCM523 batteries at the 3rd and 50th cycle.
因循环容量的巨大差异(4.0 vs. 1.0 mAh/cm2), 在低N/P比下, 负极的利用深度为61%, 远高于高N/P比电池负极0.8%的利用深度. 在高利用深度下, 金属锂负极承受着巨大的体积形变. 在此过程中, 固液界面膜不断破裂重组, 持续消耗电解液和活性锂. 此外, 高循环容量也会导致锂沉积的不均匀性加剧, 从而造成大量死锂累积, 因而极化电压迅速增长, 容量快速衰减.
综上所述, 厚锂负极及高N/P比条件下, 可参与循环的活性锂多, 金属锂利用深度低, 体积形变小, 枝晶行为弱, 金属锂保护策略在此条件下可有效地增加电池的循环稳定性. 然而, 这些策略难以在金属锂利用深度增加、体积形变加剧的苛刻条件下继续发挥原有的作用. 因此, 在薄锂负极及低N/P比条件下进行锂负极保护研究更具实用价值.
2
3.3.电解液量
电解液在电池中扮演着十分重要的角色, 其搭建了正负极之间的离子通路, 除此之外, 电解液与金属锂反应在锂表面分解形成的固液界面膜, 对锂沉积的均匀性具有显著调节作用[55,56]. 在循环过程中, 伴随着金属锂沉积脱出, 负极持续的体积形变使固液界面膜发生破裂, 裸露的金属锂与电解液接触形成新的固液界面膜, 不断消耗电解液[8]. 为了排除或降低电解液消耗的影响, 电池测试过程中往往加入大量的电解液(>30.0 g·Ah-1). 但电解液质量在电池总质量中的占比不容忽视, 为了实现高比能电池, 必须要对电解液量加以限制(<3.0 g·Ah-1, 图4(a)).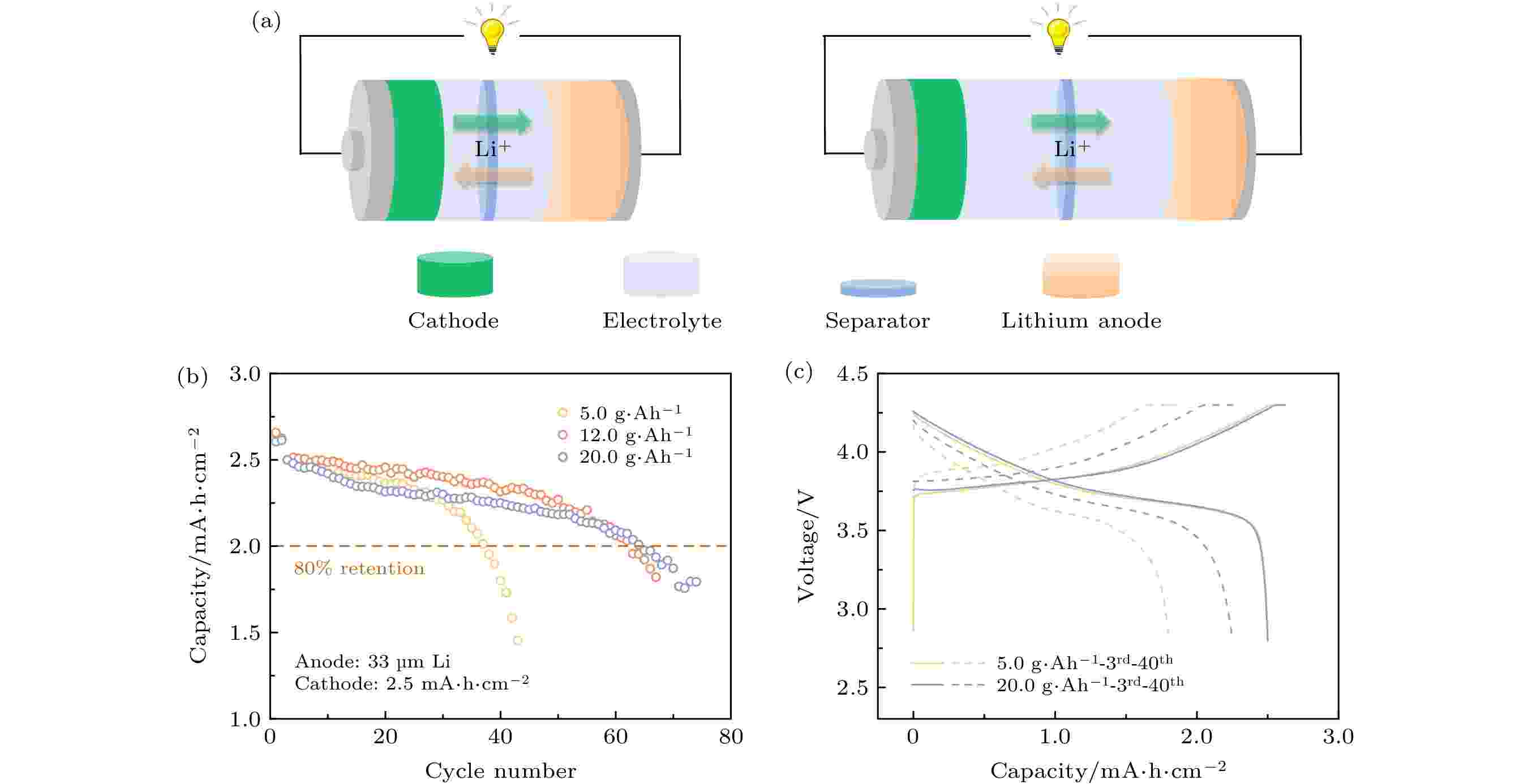
Figure4. The effect of the amount of electrolyte on the cycling of batteries: (a) The schematics of batteries with different amounts of electrolyte; (b) the cycling performance of Li | NCM523 batteries; (c) the corresponding charge and discharge curves of Li | NCM523 batteries at the 3rd and 40th cycle.
本文设置3个梯度来探究电解液量对电池循环影响. 由于纽扣电池存在大量的无效体积(相比于软包电池而言, 纽扣电池内部空间利用率低, 存在更多的无效空间), 所以最低电解液用量设置为5.0 g·Ah–1以保证正常循环. 经过实验发现, 电池的循环性能(37, 60, 65圈)与电解液量(5.0, 12.0, 20.0 g·Ah–1)呈正相关(图4(b)). 这表明电解液量直接影响着电池的循环性能. 循环40圈后, 少量电解液(5.0 g·Ah–1)条件下的电池放电中值电压明显低于添加大量电解液(20.0 g·Ah–1)电池的放电中值电压, 两者相差76 mV (图4(c)). 这表明在电解液量较低的情况下, 随着循环的进行, 电池界面阻力增加较大. 在相同的电流密度和循环容量条件下, 少量电解液更容易被耗尽, 从而导致电池内部离子传输受阻, 因此极化电压增加迅速, 电池容量衰减加快.
此外, 当电解液量大于一定量时, 如本文实验条件下的12.0 g·Ah–1, 进一步增加电解液量不能有效提升电池循环性能, 这主要是由于此时薄锂负极先于电解液耗尽, 从而导致电池循环容量衰减. 电解液对固液界面膜和锂沉积均匀性具有较大影响, 电解液设计有助于提升电池的循环性能, 但其有效性需要在实用化添加量下的电池中进行评测.
2
3.4.循环倍率
优异的快速充电性能是快节奏的现代社会对储能电池的要求之一[57]. 结合前人所做电流密度对于金属锂形核及枝晶生长影响的研究工作, 本文进一步揭示了实用化条件下, 高倍率测试时金属锂负极面临的挑战.本文采用相同构型的电池, 分别在0.2 C和0.4 C条件下进行测试以探究不同倍率对电池循环的影响(图5(a)). 实验发现, 在高倍率条件下, 电池的循环性能明显下降(91 vs. 65圈, 图5(b)), 极化电压迅速增长, 电池的放电平台缩短, 放电中值电压降低(图5(c)). 同时, 根据SEM图像分析负极表面发现, 高倍率下金属锂沉积更加不均匀, 枝晶生长和粉化行为更加严重(图2).
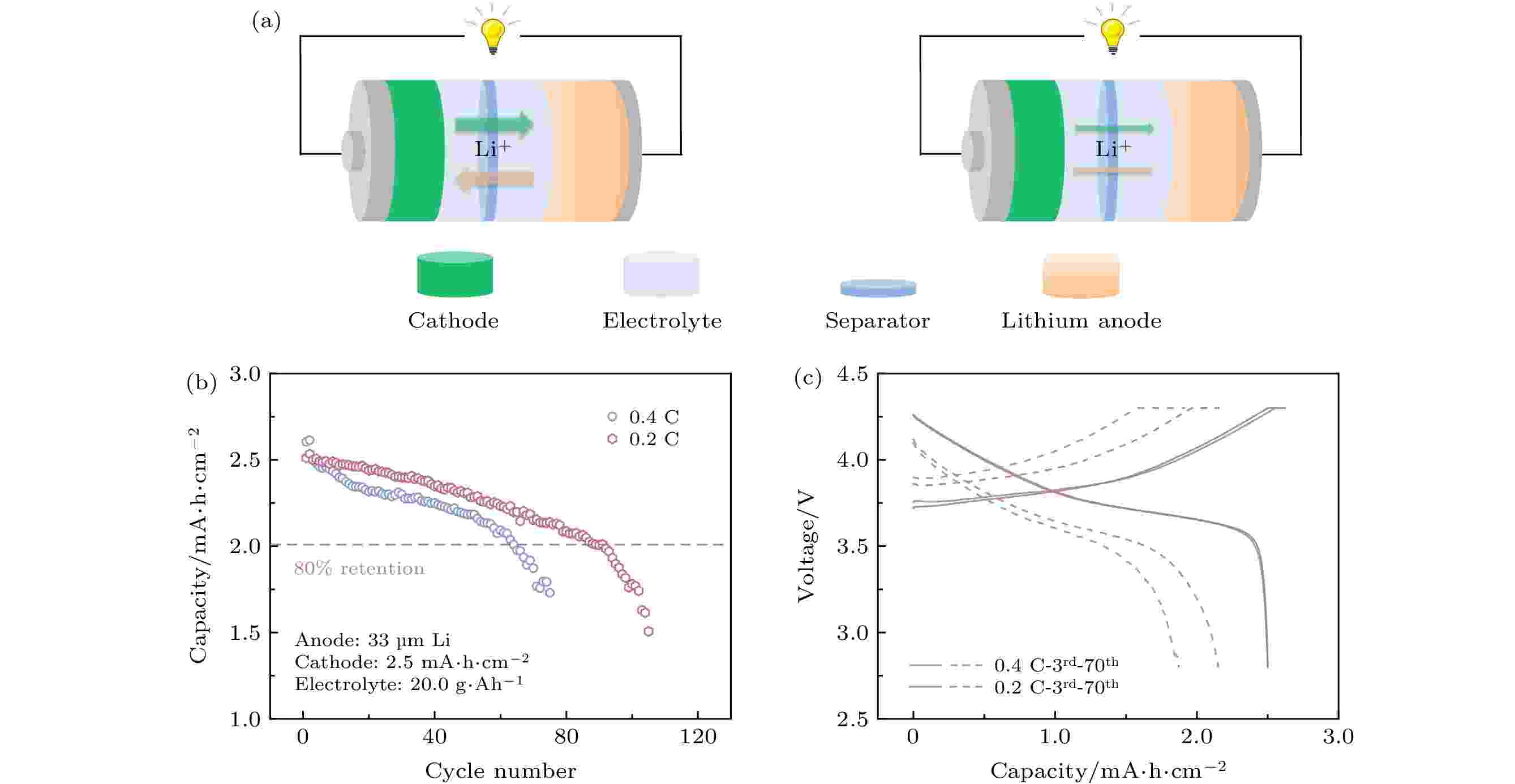
Figure5. The effect of the rate on the cycling of batteries: (a) The schematics of batteries with different rates; (b) the cycling performance of Li | NCM523 batteries; (c) the corresponding charge and discharge curves of Li | NCM523 batteries at the 3rd and 70th cycle.
根据经典成核理论, 高电流密度条件下, 金属锂沉积初始阶段会产生较多的形核位点, 金属锂沉积松散, 更易促进锂枝晶的生长[58,59]. 同时, 电极表面反应加快, 锂离子浓度降低, 与主体相之间形成较大的浓度梯度, 导致浓差极化进一步加大[60]. 因此, 高倍率条件下电池的极化电压显著增加, 循环容量快速衰减. 而在低倍率条件下, 金属锂形核位点较少, 枝晶生长缓慢, 电极表面浓差极化低, 电池的循环稳定性得以提高.
在高倍率条件下, 为了提高电池的循环性能, 可采用合适的手段降低有效电流密度, 例如在金属锂负极中引入导电三维骨架. 此外, 三维导电骨架与锂离子间的相互作用可降低金属锂电极表面的浓度梯度, 继而降低离子传输阻力[29]. 三维骨架的引入为今后进一步推进金属锂电池快速充点的研究提供了一种新的思路.
金属锂负极的研究由温和迈向实用化条件对于后续的基础和应用研究均有重要意义. 在基础研究方面, 实用化条件的测试可进一步揭示金属锂负极在实用化条件下的失效机理, 为提升金属锂负极循环稳定性提供指导. 在应用研究方面, 金属锂负极保护策略的实用化潜力, 在实用化条件下测试能更好地体现出来. 在实用化条件下, 调控电解液中锂离子的溶剂化层[13,14,61]、构筑三维复合负极[29,30]、设计人工界面层[62]等措施对提升金属锂负极循环稳定性具有显著作用, 需要进一步的研究. 此外, 实用化条件下的测试可在纽扣或软包电池中完成, 但也应注意纽扣和软包电池的差异. 实用化条件下锂负极的研究将极大促进金属锂电池的发展.