![]() |
图 1 复合材料开孔层板开孔压缩试验夹持及加载系统 Fig. 1 Clamping and loading system of open-hole compressional experiment on open-hole composite laminates |
图选项 |
2 试验结果共进行3组试验,表 1所示为开孔压缩试验结果.标准差及离散系数表明试验具有较好的重复性.以1号试验件为例进行试验结果分析.压缩试验过程中复合材料开孔层板的载荷-位移曲线如图 2所示,载荷随位移线性增加,到达承载极限时突降,试件损坏.表 1 开孔压缩试验结果 Table 1 Experimental results of open-hole compression
试件编号 | 破坏载荷/kN | 标准差 | 离散系数 |
1 | 47.068 | 1.358 | 0.028 |
2 | 49.761 | ||
3 | 48.713 |
表选项
![]() |
图 2 复合材料开孔层板的压缩试验载荷-位移曲线 Fig. 2 Load-displacement curve of compressional experiment on open-hole composite laminates |
图选项 |
2.1 孔边渐进损伤结果图 3所示为复合材料开孔层板压缩加载过程孔边渐进损伤现象,与图 2曲线上各点分别对应.图中显示了开孔截面应力(σ)状态以及当前载荷占承载极限载荷的百分比(p).
![]() |
图 3 复合材料开孔层板压缩加载过程孔边渐进损伤现象 Fig. 3 Phenomenon of progressive damage at edge of hole during loading procedure of compressional experiment on open-hole composite laminates |
图选项 |
首先发生如图 3(b)所示的纤维挤出损伤.随压缩载荷增大,出现纤维挤出损伤的位置数量增多且损伤更为严重,孔边开始有分层损伤出现.接近破坏时,孔边有显著的纤维挤出现象,且分层位置已十分明显.选取一试件在纤维挤出现象出现后停止加载,对孔边进行X光扫描,检测到孔边小范围纤维微屈曲的存在.继续加载至破坏,制备孔边断口处切片,并进行SEM观测,观测结果显示了纤维由于微屈曲而产生的断裂.复合材料开孔层板孔边X光扫描及断口SEM观测结果如图 4所示.以上结果表明,纤维挤出与孔边纤维微屈曲直接相关.结合渐进损伤过程可以看出,孔边纤维微屈曲现象先于分层现象发生,少量的纤维微屈曲损伤对开孔层板承载能力影响不大.
![]() |
图 4 复合材料开孔层板孔边X光扫描及断口SEM观测结果 Fig. 4 Results of X-scan at edge of hole and SEM-scan at fracture of open-hole composite laminates |
图选项 |
图 5所示为临近破坏时复合材料开孔层板孔边分层损伤位置的细节放大图.结合铺层方式和单层厚度,可看出压缩载荷作用下分层位置为45°和90°铺层层间,结合文献[10]的研究成果可以看出,在拉伸及压缩载荷作用下45°和90°铺层间均易发生分层现象.开孔板产生明显分层及分层扩展对应图 2载荷-位移曲线中的D、E、F点,此时层板已临近破坏.
![]() |
图 5 复合材料开孔层板孔边分层损伤位置的细节放大图 Fig. 5 Detail amplification image of delamination location at hole edge of open-hole composite laminates |
图选项 |
2.2 破坏结果图 6所示为复合材料开孔压缩层板最终破坏形式以及破坏试件侧面的X光扫描.可以看出,载荷达到承载极限时,分层现象进一步加剧并出现显著的层间开裂,孔边发生明显的层板压入和折断,承载能力丧失.
![]() |
图 6 复合材料开孔压缩层板最终破坏形式及破坏试件侧面的X光扫描 Fig. 6 Ultimte failure mode of open-hole compressional composite laminates and X-scan of failure specimen |
图选项 |
3 有限元数值模拟3.1 有限元模型使用有限元软件ABAQUS对开孔结构进行数值模拟,模型所需复合材料开孔层板材料性能见表 2.表中:复合材料各方向弹性模量E11、E22、E33,剪切模量G12、G13、G23和泊松比ν12、ν13、ν23为材料制造方提供的实测数据;Tf为纤维拉伸强度;Cf为纤维压缩强度;Tm为基体拉伸强度;Cm为基体压缩强度;Sm为基体剪切强度;t0i(i=n,s,t)为胶层在法向和2个切向上的强度;Kii(i=n,s,t)为3个方向上的刚度;Gci(i=n,s,t)为3个方向上的临界能量释放率.
表 2 复合材料开孔层板材料性能Table 2 Material properties of open-hole composite laminates
性能 | 参数 | 数值 |
复合材料铺层性能 | E11/GPa | 123.91 |
E22=E33/GPa | 9.72 | |
ν12=ν13 | 0.288 | |
ν23 | 0.347 | |
G12=G13/GPa | 4.53 | |
G23/GPa | 2.56 | |
Tf/MPa | 3091.8 | |
Cf/MPa | 2440.6 | |
Tm/MPa | 138.7 | |
Cm/MPa | 353.3 | |
Sm/MPa | 145.1 | |
层间性能 | Knn=Ktt=Kss | 106 |
t0n=t0t=t0s/MPa | 70 | |
Gcn/(N·mm-1) | 0.3 | |
Gcs=Gct/(N·mm-1) | 1.2 |
表选项
开孔层板有限元模型如图 7所示,考虑到距离开孔处较远区域层板并未损伤及计算成本,对含开孔部分54mm长范围内的层板进行建模.复合材料铺层采用8节点减缩积分实体单元C3D8R模拟,单元个数为20800.各铺层间的界面采用8节点胶层单元COH3D8模拟,界面厚度为0.001mm,单元个数为4550.参考图 2所示夹持系统施加有限元模型的边界条件,为避免在计算过程中出现收敛问题,对有限元模型采用非线性显式动力学分析.模型长度方向为纵向,宽度方向为横向,沿纵向进行加载.
![]() |
图 7 开孔层板有限元模型 Fig. 7 Finite element (FE) model of open-hole laminate |
图选项 |
3.2 复合材料损伤准则采用基于MMF3理论的跨尺度失效准则模拟压缩载荷情况下复合材料的损伤.该方法由Tsai[11]提出,从细观层面分析纤维和基体的应力状态,并分别定义纤维和基体的失效行为,可以真实反映纤维和基体的材料性能.基于纤维和基体的细观应力分析首先需要将宏观应力转化为细观应力.为此,参考文献[12]的方法建立了正方形和六边形代表体积单元并在单元截面上选取参考点,对代表体积单元施加边界条件,计算输出各参考点的应力值以获得宏观应力到各参考点的细观应力的应力放大系数矩阵,实现宏观应力到细观应力的转化.MMF3理论定义纤维和基体的失效判定准则如下.1) 纤维失效:Tf≤σ11 纤维拉伸失效
σ11≤-Cf 纤维压缩失效2) 基体失效:
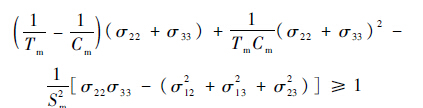
式中:σij(i,j=1,2,3)为单层平板宏观应力经应力放大系数矩阵转换获得的细观应力.对于纤维和基体规定了5个细观强度参数,即Tf、Cf、Tm、Cm、Sm.各细观强度参数均参考文献[12]方法通过单向层合板的纵向拉伸及压缩强度、横向拉伸及压缩强度、面内剪切强度结合基于代表体积单元获得的应力放大矩阵最终确定.各复合材料铺层的损伤判定及演化通过编写ABAQUS用户自定义场变量子程序VUSDFLD[13]实现.对宏观有限元模型施加载荷增量,获得各单元的宏观应力,计算代表体积单元各参考点的细观应力值,判断是否满足纤维和基体的失效准则.若不满足,表明材料并未失效,进入下一轮载荷增量计算;若满足,根据破坏模式对材料性能进行衰减.经试算并对比试验结果,最终确定纤维损伤折减系数Df取0.01,基体损伤折减系数Dm取0.05.模型的计算载荷急剧下降时,认为结构损坏,计算结束.3.3 胶层单元及损伤判据对分层损伤起始和扩展现象的模拟通过界面胶层单元实现.胶层单元使用基于连续损伤力学的牵引力-相对位移关系,本构模型为图 8所示线弹性-线性软化本构模型,作用是连接可能发生分层的2个相邻复合材料铺层界面.图中:δ0为胶层损伤起始发生时的位移;δf为胶层完全破坏时的位移;t0为胶层材料破坏强度;GC为临界损伤能量;材料初始刚度和折减后刚度以斜率形式体现,分别为K1和K2,K1=K,K2=(1-D)K,K为胶层材料刚度,D为胶层材料刚度折减系数;单元允许有法向正应力tn、切向剪应力ts和tt 3个方向的作用力,各作用力定义为

式中:εi(i=n,s,t)为3个方向上的应变,εi=δi/T0,δi为胶层单元各节点在3个方向上的相对位移,T0为胶层厚度,取值0.001mm.
![]() |
图 8 胶层材料线弹性-线性软化本构模型 Fig. 8 Linear elastic-linear softening constitutive model of cohesive material |
图选项 |
使用二次应力准则判定胶层单元损伤的起始:

式中:麦考林符号〈·〉表示单纯的压缩状态不引起胶层损伤.胶层3方向应力使式(2)大于1时,胶层出现损伤,胶层刚度折减方式为
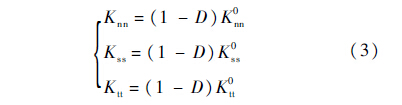
式中:
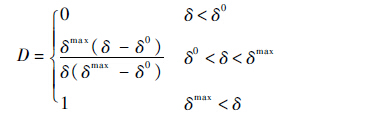
其中:K0nn、K0ss、K0tt为胶层在3个方向上的初始刚度.胶层单元最终破坏采用基于能量的BK-Law混合模式线性刚度衰减模型[14]:

式中:η为与总临界应变能释放率Gequiv和比例

相关的材料参数,由试验材料制造方提供,取值1.45.各界面参数是试验材料制造方参考文献[15]根据目前常用的工程方法结合复合材料高温固化工艺和树脂性能经过试算对比给出的经验参数,数值详见表 2.4 计算结果分析4.1 损伤起始与扩展预测计算模型通过细观强度参数定义了纤维和基体2种损伤.纤维损伤先于基体损伤出现,于孔边0°层起始,随后沿层板厚度方向扩展至除90°铺层外其他铺层.随压缩载荷进一步增大,各铺层纤维损伤沿层板横向扩展,90°铺层始终未出现纤维损伤.图 9输出了加载过程中各单层纤维损伤云图计算结果及当前载荷占承载极限载荷百分比.图 10输出了纤维损伤发生前0°层的σ11应力分布情况,0°层孔边中间位置较大、σ11应力集中是该位置产生纤维损伤起始的原因.纤维损伤的出现和扩展在整个加载过程中跨度较大,少量的纤维损伤并未引起载荷-位移曲线的可见波动,与第2节试验结果一致.
![]() |
图 9 有限元模型纤维损伤计算结果 Fig. 9 Numeric results of fiber damage of FE model |
图选项 |
![]() |
图 10 有限元模型纤维损伤前0°层σ11应力分布 Fig. 10 σ11 stress distribution at 0° ply of FE model before occurrence of fiber damage |
图选项 |
图 11输出了加载过程中基体损伤云图计算结果及当前载荷占承载极限载荷百分比.基体损伤起始于45°、-45°、90°铺层孔边位置.图 12给出了各铺层基体损伤前的不同应力集中情况:在孔边中间位置,90°铺层存在σ22应力集中,45°和-45°铺层存在σ12应力集中.基体损伤的起始与以上应力集中直接相关.随载荷增大,损伤沿层板横向扩展并沿厚度方向扩展至0°层.
![]() |
图 11 有限元基体损伤计算结果 Fig. 11 Numeric results of matrix damage of FE model |
图选项 |
![]() |
图 12 各铺层有限元模型应力集中情况计算结果 Fig. 12 Numeric results of stress concentration at plies of FE model |
图选项 |
基体和纤维损伤程度较高时,有显著的分层现象出现.如图 13所示,分层集中发生在45°和90°铺层之间,与图 6所示试验结果一致.分层现象起始于孔边,随后沿孔边扩展,最后沿层板横向扩展.分层的横向大范围扩展伴随有较大的孔边变形,与计算所得载荷-位移曲线中的载荷突降点相对应.
![]() |
图 13 层板模型分层位置及分层扩展过程有限元模型计算结果 Fig. 13 Numeric results of delamination location and extension procedure of FE laminate model |
图选项 |
4.2 破坏强度及模式预测计算所得载荷-位移曲线如图 14所示,计算所得最终破坏载荷49.862kN与表 1所示各试验结果最大误差为5.93%.图 15所示为有限元层板模型的最终破坏结果,结合图 6的试验结果可以看出有限元计算较准确地反映了复合材料开孔层板最终破坏时的分层及压入等现象,计算结果与试验结果吻合良好.
![]() |
图 14 计算所得载荷-位移曲线 Fig. 14 Numeric result of load-displacement curve |
图选项 |
![]() |
图 15 计算所得有限元层板模型最终破坏结果 Fig. 15 Numeric result of failure mode of FE laminate model |
图选项 |
5 结 论1) 损伤起始于孔边并沿层板厚度方向及横向扩展.0°层孔边σ11应力集中导致该处出现纤维损伤起始.90°层孔边存在σ22应力集中以及45°和-45°层孔边存在σ12应力集中是以上3区域产生基体损伤的原因.2) 分层现象伴随大范围的纤维和基体损伤出现在45°和90°铺层之间,首先沿孔边扩展,随后沿层板横向扩展.层板破坏与分层损伤沿层板横向的大范围扩展直接相关,最终破坏模式为中部断裂、大范围分层和压入.3) 本文提出的基于跨尺度MMF3失效理论和界面单元方法的计算模型在纤维和基体的损伤起始与扩展、分层位置、承载能力和最终破坏模式等方面计算结果均与试验结果相吻合,该模型适用于分析复合材料开孔结构压缩破坏问题.
参考文献
[1] | 杜善义, 关志东.我国大型客机先进复合材料技术应对策略思考[J].复合材料学报, 2008, 25(1):1-10. Du S Y, Guan Z D.Strategic considerations for development of advanced composite technology for large commercial aircraft in China[J].Acta Materiae Compositae Sinica, 2008, 25(1):1-10(in Chinese). |
Cited By in Cnki (94) | |
[2] | Suemasu H, Takahashi H, Ishikawa T.On failure mechanisms of composite laminates with an open hole subjected to compressive load[J].Composites Science and Technology, 2006, 66(5):634-641. |
Click to display the text | |
[3] | Berbinau P, Scoutis C, Guz I A.Compressive failure of 0°unidirectional carbon-fibre-reinforced plastic(CFRP)laminates by fibre microbuckling[J].Composites Science and Technology, 1999, 59(9):1451-1455. |
Click to display the text | |
[4] | Soutis C.Damage tolerance of open-hole CFRP laminates loaded in compression[J].Composite Engineering, 1994, 4(3):317-327. |
Click to display the text | |
[5] | Soutis C, Curtisb P T.A method for predicting the fracture toughness of CFRP laminates failing by fiber microbuckling[J].Composites Part A:Applied Science and Manufacturing, 2000, 31(7):733-740. |
Click to display the text | |
[6] | Lee J, Soutis C.Thickness effect on the compressive strength of T800/924C carbon fibre-epoxy laminates[J].Composites, 2006, 36(2):213-227. |
Click to display the text | |
[7] | 关志东, 黎增山, 刘德博, 等.复合材料层板开孔压缩损伤分析[J].复合材料学报, 2012, 29(3):167-172. Guan Z D, Li Z S, Liu D B, et al.Damage analysis of open-hole compression laminates[J].Acta Materiae Compositae Sinica, 2012, 29(3):167-172(in Chinese). |
Cited By in Cnki (8) | |
[8] | Lee H K, Kim B R.Numerical characterization of compressive response and damage evolution in laminated plates containing a cutout[J].Composites Science and Technology, 2007, 67(11):2221-2230. |
Click to display the text | |
[9] | American Society for Testing and Materials International.ASTM D6484/D6484M-09 Standard test method for open-hole compressive strength of polymer matrix composite laminates[S].West Conshohocken:ASTM International, 2009. |
Click to display the text | |
[10] | Wisnom M R, Hallett S R.The role of delamination in strength, failure mechanism and hole size effect in open hole tensile tests on quasi-isotropic laminates[J].Composites Part A:Applied Science and Manufacturing, 2009, 40(4):335-342. |
Click to display the text | |
[11] | Tsai S W.Strength & life of composites[M].Stanford:Stanford University, 2008:6-29-6-51. |
Click to display the text | |
[12] | Sun X S, Tan V B C, Tay T E.Micromechanics-based progressive failure analysis of fibre-reinforced composites with non-iterative element-failure method[J].Computers & Structures, 2011, 89(11):1103-1116. |
Click to display the text | |
[13] | Anon.ABAQUS user's manual[CP/CD].Version 6.10.Pawtucket:Hibbitt Karlsson and Sorensen, 2010. |
[14] | Benzeggagh M L, Kenane M.Measurement of mixed-mode delamination fracture toughness of unidirectional glass/epoxy composites with mixed-mode bending apparatus[J].Composites Science and Technology, 1996, 56(4):439-449. |
Click to display the text | |
[15] | Turon A, Davila C G, Camanho P P, et al.An engineering solution for mesh size effects in the simulation of delamination using cohesive zone models[J].Engineering Fracture Mechanics, 2007, 74(10):1665-1682. |
Click to display the text |