

2Department of Mathematics,
3Department of Mathematics, College of Sciences AlZulfi,
4Department of Mathematics,
5Department of Mathematics,
First author contact:
Received:2020-12-02Revised:2021-02-23Accepted:2021-02-24Online:2021-04-09

Abstract
Keywords:
PDF (0KB)MetadataMetricsRelated articlesExportEndNote|Ris|BibtexFavorite
Cite this article
Ammarah Raees, Umer Farooq, Muzamil Hussain, Waseem Asghar Khan, Fozia Bashir Farooq. Non-similar mixed convection analysis for magnetic flow of second-grade nanofluid over a vertically stretching sheet. Communications in Theoretical Physics, 2021, 73(6): 065801- doi:10.1088/1572-9494/abe932
1. Introduction
Study of the flows induced by the stretching of the surfaces is of significant importance in view of its use in technical manufacturing, such as aerodynamics, the cooling process of metal sheets, extrusion of plastic sheets, the condensation process of fluid films, chemical processing equipment, glass and polymer industries, crystal growth and several heat exchanger projects. In such situations, the outputs with the required attributes depend on the rate of cooling and stretching in the process. Sakiadis [1] was the pioneer in this field who theoretically explored the moving solid structures. He addressed the problem by applying similarity transformation via a numerical technique. Moreover, Erickson et al [2] continued the exploration by assuming a moving surface with nonzero transverse velocity. The 2D steady flow was investigated by Crane [3] over a stretching surface. He attempted to concentrate on a stretching sheet as he realized that this case was a pivotal subject in the polymer industry. Gupta and Gupta [4] utilized that that was introduced by Crane [3] and extended those examinations. They explored heat and mass transfer by incorporating suction effects over an expanding surface. Rajagopal et al [5] inspected the flow of viscoelastic fluid in the absence of heat transfer and discussed its applications in the polymer industry. Using the momentum integral method, Bujurke et al [6] performed convection studies for second-grade fluid flow. Magyari and Keller [7] examined steady flow using both analytical and numerical solutions. They also compared heat and mass transfer features of the considered problem with already proven results of earlier authors. Elbashbeshy [8] introduced a new dimension in the analysis of an exponentially stretching surface. He examined the effects of suction in a surface which is expanding at exponential rate. Partha et al [9] studied mixed convection flow with viscous dissipation consequences over a vertical surface expanding at exponential rate. Khan et al [10] studied viscoelastic fluid over an exponentially expanding surface. Xu et al [11] analytically examined the unsteady electrically conductive incompressible viscous fluid in which flow is initiated by the expansion of the surface in two lateral directions. Latterly Khan [12] and Bataller [13] analytically reviewed convection equations for viscoelastic fluid flow persuaded by a stretchable sheet. Tan and Liao [14] analytically examined the 3D unsteady incompressible viscous rotating fluid flow over an impulsive surface. Sajid and Hayat [15] surveyed thermal radiation effects in an exponentially expanding sheet. Sekhar and Chethan [16] examined heat transfer using Boussinesq-Stokes suspension numerically in the fluid flow, which is started by the exponentially expanding surface. Siddheshwar et al [17] expanded this research by considering the magnetic field in a transversal direction. Ramzan et al [18], with the help of surface heat flux, examined the effects of thermal radiation and mixed convection on 3D second-grade nanofluid. Rasheed and Anwar [19] studied magnetohydrodynamic (MHD) viscoelastic fluid flow with homogeneous-heterogeneous reactions in the flow domain. By utilizing the time-dependent magnetic field, Muhammad [20] analyzed the impact of heat absorption/generation effects over a curved surface. Ahmad et al [21] inspected 3D unsteady flow with thermophoresis and Brownian motion effects. Jamil et al [22] examined heat transfer of viscoelastic incompressible unsteady flow generated by a stretching surface with heat radiation and chemical reaction effects. Irfan et al [23] examined 3D MHD nonlinear radiated flow of mixed convection Carreau nanofluid over a stretching surface.In accordance with industrial and technical applications, flow models based on non-Newtonian fluids are more acceptable than Newtonian fluids. Non-Newtonian fluids show a nonlinear stress and strain rate relationship at any point of flow. Mathematically, compared to the Newtonian the constitutive equations of non-Newtonian fluids are much more complex because of the nonlinear relation of the stress and strain rate. Constitutive equations are more complex, containing a number of parameters, and the solutions of the resulting equations are more complicated to find in general. Numerous variable viscous fluid models have been suggested which demonstrate the complexity of their governing equations. Now, several researchers are engaged in the study of analytical or numerical solutions to fluid flow problems that generate from the use of various non-Newtonian fluid models. Viscoelastic fluids are common types of non-Newtonian fluids. However, the most widely used basic type of viscoelastic fluid is the second-order fluid, which may address problems that are far from trivial. The fluid property visco-elasticity refers to the rise in the order of differential equations that describe the flow. Nevertheless, flow equations are typically more nonlinear compared to Newtonian fluid equations. Among these reasons, the field of research on non-Newtonian fluids poses some fascinating and impressive tasks for computer scientists, physicists and mathematicians alike.
Mathematical simulations of physical processes in fields such as fluid dynamics, diffusion, wave dynamics, chemical kinetics and general transport problems are governed by nonlinear partial differential equations whose solutions are difficult to find analytically. Consequently, the conversion technique for analyzing nonlinear partial differential system (PDEs) into ordinary differential equations (ODEs) has been very influential in the study of various convection equations. Ames [24] presented many types of these reduction approaches and thought about the developments in fluid dynamics, wave propagation and nonlinear diffusion from the use of PDEs to the reduction approach to ODEs. Although a similar approach has frequently been used in the literature [25-29], the approach cannot be used to a significant extent because of a limitation clarified underneath. Success of this approach depends vigorously on the achievement of a reduced ODEs solution. For a few cases, the reduced ODEs may be integrated in the form of elementary functions, but it is not an easy matter in most cases, so it was proposed that numerical methods be used to solve the converted ODEs. Generally, the given system is not fully converted to ODEs using a local similar method; to overcome this drawback Sparrow and Yu [30] introduced a method of local non-similarity. Hayat et al [31] numerically examined magnetic viscous fluid in nonlinear curved expansion. Zhang et al [32] investigated 3D pressure drop through a spherically coordinated helically coiled tube. Ray et al [33] utilized local non-similarity via a homotopy analysis scheme for mixed convection in the vertical flow of Eyring-Powell fluid with variable velocity. Farooq et al [34] employed local non-similarity via bvp4c for Darcy-Forchheimer-Brinkman flow in non-Darcy porous media.
The purpose of this work is to provide a realistic means of dealing with these circumstances in which governing equations cannot be reduced into ordinary differential systems. The laminar incompressible flow of magnetic second-grade fluid over an exponentially expanding surface in the presence of buoyancy forces in terms of temperature and concentration with surface heat flux is considered. Under these premises, the governing convection differential equations are formulated. The appropriate non-similarity transformations are proposed. The governing equations are reduced into a dimensionless nonlinear partial differential system. The transformed system is solved numerically using local non-similarity via bvp4c, which is valid for a system of PDEs. Finally, tabular representations regarding the impact of concerning parameters on the friction coefficient ${C}_{f},$ Nusselt number $Nu,$ and Sherwood number $Sh$ are disclosed, and demonstrated graphically the effects of involved dimensionless parameters on the non-dimensional velocity, temperature and mass concentration profiles.
2. Formulation of convection equations
Consider mixed convection in a second-grade laminar, incompressible, steady, 2D, magnetized second-grade fluid flow over a sheet positioned along the $x$-axis in the vertical direction, although fluid in the domain $y\gt 0$ is constrained. It is also presumed that the sheet is stretched at an exponential rate $u={U}_{0}\exp \left(\tfrac{x}{l}\right)$, where ${U}_{0}$ is the reference velocity. Figure 1 demonstrates the geometrical configuration of the present flow.Figure 1.
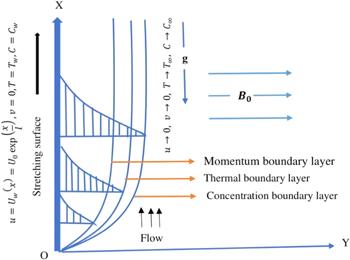
Figure 1.Flow over a hot vertical plate at temperature ${T}_{w}$ immersed in a fluid at temperature ${T}_{\infty }.$
The governing equations for
are as follows:
continuity equation
equation of motion
energy equation
nanoparticle volume fraction equation
In the governing system $u$ and $v$ are the velocity components along the $x$- and $y$-directions, while $T$ and $C$ represent temperature and concentration variables, respectively, ${\rho }_{f}$ is the fluid density, $\sigma $ represents the electrical conductivity, $\vartheta $ is the kinematic viscosity, ${B}_{0}$ indicates the applied magnetic field, ${\alpha }_{1}$ is the second-grade fluid material parameter, $g$ is the gravitational acceleration, ${\beta }_{{\rm{T}}}$ and ${\beta }_{{\rm{c}}}$ are the thermal and concentration enlargement coefficients, respectively, $\tau $ describes the ratio between the nanoparticle’s heat capacity and the original fluid heat capacity, ${D}_{{\rm{B}}}$ represents the coefficient of Brownian diffusion, ${D}_{T}$ indicates the thermophoresis diffusion coefficient, ${C}_{\infty }$ and ${T}_{\infty }$ are upstream concentration and temperature, respectively, and $\alpha $ is thermal diffusivity.
The suitable boundary conditions for the considered flow problems are
3. Non-similar analysis
We propose the following non-similarity transformationsThese transformations identically satisfy the continuity equation (
In the above equations, the magnetic parameter $\left(M\right),$ second-grade fluid parameter $(\alpha ),\,$ Richardson number $(\lambda ),$ ratio of mass and heat transfer Grashof numbers $(N),$ Brownian motion $\left(\,{N}_{b}\right),$ Prandtl number $(Pr),\,$ thermophoresis $({N}_{t}),$ and Schmidt number $({S}_{c})$, respectively, are defined as
4. First truncation system
By using a local similarity technique the terms containing a partial derivative with respect to $\xi $ are treated as approximately small and considered equal to zero. Therefore, equations (The boundary conditions are
5. Second truncation system
For the second truncation system we consideredEquations (
The boundary conditions are
The parameters of physical interest, such as the friction coefficient ${C}_{{\rm{f}}},$ the local Nusselt number $Nu$ and the Sherwood number $Sh$ are defined as,
where the wall skin friction ${\tau }_{wx},$ ${\rm{heat}}\,\mathrm{flux}\,{q}_{w}$ and mass flux ${j}_{w}$ are expressed as
Using (
6. Results and discussion
The interpretation of solutions regarding the impacts of the different dimensionless quantities on ${f}^{{\prime} }\left(\eta \right),$ $\theta \left(\eta \right)$ and $\phi \left(\eta \right)$ are presented in this section. The variation in the numerical data of the friction coefficient $(\,{C}_{{\rm{f}}}),$ Nusselt number ($Nu$) and Sherwood number ($Sh$) for numerous values of involved quantities are depicted in this tabular form. The Nusselt number is the ratio of convective to conductive heat transfer, and the Sherwood number is defined as the ratio of the convective mass transfer to the mass diffusivity at a boundary in a fluid. Large values of the Nusselt number show pre-eminence of convection of heat transfer over conduction and small values of the Nusselt number indicate that poor convection occurs. So the Nusselt number indicates the dominant heat transfer phenomenon of the system. Graphical analysis of the velocity, temperature and concentration fields are conferred to explain the current non-similar model.Table 1 shows the range of governing parameters in which graphical solutions of velocity, temperature and concentration profiles reveal stable behavior. Table 2 depicts the impacts of the magnetic parameter $\left(M\right),$ Richardson number $(\lambda ),$ second-grade fluid parameter $(\alpha )$ and ratio of mass and heat transfer Grashof numbers $(N)$ on the local skin friction. We perceive that the friction coefficient decreases marginally as $M$ increases, while the coefficient of skin friction increases due to increases in the values of $\alpha ,\,\lambda $ and $N.$
Table 1.
Table 1.The range of defined parameters for a stable solution.
$M$ | $\alpha $ | $\lambda $ | $N$ | $Pr$ | $Nb$ | $Nt$ | $Sc$ |
1-20 | 1 | 0.1 | 0.1 | 10 | 0.1 | 0.1 | 0.1 |
2 | 1-8 | 5 | 0.1 | 10 | 0.1 | 0.1 | 0.1 |
2 | 1 | 0-20 | 0.1 | 10 | 0.1 | 0.1 | 0.1 |
2 | 1 | 2 | 0-16 | 10 | 0.1 | 0.1 | 0.1 |
2 | 2 | 7 | 1 | 1-35 | 1 | 1 | 1 |
4 | 4 | 4 | 2 | 7 | 0.1-2 | 0.5 | 1 |
4 | 4 | 5 | 1 | 7 | 0.4 | 0-1 | 1 |
1 | 2 | 5 | 1 | 7 | 0.4 | 0.4 | 0.3-50 |
New window|CSV
Table 2.
Table 2.Numerical data for the skin friction coefficient $R{e}_{x}^{\tfrac{1}{2}}{C}_{{\rm{f}}}$ for various parameters.
$M$ | $\alpha $ | $\xi $ | $\lambda $ | $N$ | ${N}_{b}$ | ${N}_{t}$ | ${S}_{c}$ | $Pr$ | $-R{e}_{x}^{\tfrac{1}{2}}{C}_{{\rm{f}}}$ |
1 | 1.5 | 2.5 | 0.1 | 0.1 | 0.1 | 0.1 | 0.1 | 10 | 0.663 583 4713 |
2 | 1.5 | 2.5 | 0.1 | 0.1 | 0.1 | 0.1 | 0.1 | 10 | 0.856 293 1308 |
3 | 1.5 | 2.5 | 0.1 | 0.1 | 0.1 | 0.1 | 0.1 | 10 | 1.225 811 0306 |
4 | 1.5 | 2.5 | 0.1 | 0.1 | 0.1 | 0.1 | 0.1 | 10 | 1.574 931 1745 |
2 | 1 | 1.5 | 1.5 | 0.1 | 0.1 | 0.1 | 0.1 | 10 | 1.830 895 0187 |
2 | 2 | 1.5 | 1.5 | 0.1 | 0.1 | 0.1 | 0.1 | 10 | 1.444 299 1125 |
2 | 3 | 1.5 | 1.5 | 0.1 | 0.1 | 0.1 | 0.1 | 10 | 1.210 097 2603 |
2 | 4 | 1.5 | 1.5 | 0.1 | 0.1 | 0.1 | 0.1 | 10 | 1.060 750 1270 |
2 | 1 | 1.5 | 1 | 0.1 | 0.1 | 0.1 | 0.1 | 10 | 1.029 614 1067 |
2 | 1 | 1.5 | 2 | 0.1 | 0.1 | 0.1 | 0.1 | 10 | 0.989 847 5139 |
2 | 1 | 1.5 | 3 | 0.1 | 0.1 | 0.1 | 0.1 | 10 | 0.924 498 0245 |
2 | 1 | 1.5 | 4 | 0.1 | 0.1 | 0.1 | 0.1 | 10 | 0.874 504 9428 |
2 | 1 | 2 | 2 | 0.1 | 0.1 | 0.1 | 0.1 | 10 | 1.265 880 9749 |
2 | 1 | 2 | 2 | 0.2 | 0.1 | 0.1 | 0.1 | 10 | 1.216 799 9095 |
2 | 1 | 2 | 2 | 0.3 | 0.1 | 0.1 | 0.1 | 10 | 1.164 759 5975 |
2 | 1 | 2 | 2 | 0.4 | 0.1 | 0.1 | 0.1 | 10 | 1.125 926 6318 |
New window|CSV
Table 3 displays the local Nusselt number values for the various governing parameter values. It is established that the rate of heat transfer on the wall increases due to the increase in ${N}_{b}.$ It is also shown that uplifting the values of the parameters $Pr\,$ and ${N}_{t}$ resulted in a decline in the numeric values of the local Nusselt number.
Table 3.
Table 3.The local Nusselt number $R{e}_{x}^{-\tfrac{1}{2}}N{u}_{x}$ for various parameters.
$M$ | $\alpha $ | $\xi $ | $\lambda $ | $N$ | ${N}_{b}$ | ${N}_{t}$ | ${S}_{c}$ | $Pr$ | $-R{e}_{x}^{-\tfrac{1}{2}}N{u}_{x}$ |
4 | 2 | 0.01 | 5 | 0.1 | 0.1 | 0.1 | 0.1 | 8 | 0.264 954 9335 |
4 | 2 | 0.01 | 5 | 0.1 | 0.1 | 0.1 | 0.1 | 10 | 0.312 707 1600 |
4 | 2 | 0.01 | 5 | 0.1 | 0.1 | 0.1 | 0.1 | 12 | 0.362 955 6961 |
4 | 2 | 0.01 | 5 | 0.1 | 0.1 | 0.1 | 0.1 | 15 | 0.438 384 2125 |
4 | 4 | 0.01 | 5 | 2 | 0.2 | 0.5 | 1 | 7 | 0.235 524 6848 |
4 | 4 | 0.01 | 5 | 2 | 0.3 | 0.5 | 1 | 7 | 0.206 545 0969 |
4 | 4 | 0.01 | 5 | 2 | 0.4 | 0.5 | 1 | 7 | 0.191 251 8247 |
4 | 4 | 0.01 | 5 | 2 | 0.6 | 0.5 | 1 | 7 | 0.165 460 3569 |
4 | 4 | 0.01 | 5 | 1 | 0.1 | 0.2 | 0.1 | 10 | 0.255 267 7573 |
4 | 4 | 0.01 | 5 | 1 | 4 | 0.4 | 0.1 | 10 | 0.293 119 1975 |
4 | 4 | 0.01 | 5 | 1 | 4 | 0.6 | 0.1 | 10 | 0.302 495 9839 |
4 | 4 | 0.01 | 5 | 1 | 4 | 0.8 | 0.1 | 10 | 0.308 375 4409 |
New window|CSV
Table 4 describes the impact of governing parameters on the local Sherwood number. The table shows that for increasing ${N}_{t}\,{\rm{and}}\,{S}_{c}$ values, the local Sherwood coefficient decreases.
Table 4.
Table 4.Numerical data for the local Sherwood number $R{e}_{x}^{-\tfrac{1}{2}}Sh$ for various parameters.
$M$ | $\alpha $ | $\xi $ | $\lambda $ | $N$ | ${N}_{b}$ | ${N}_{t}$ | ${S}_{c}$ | $Pr$ | $-R{e}_{x}^{-\tfrac{1}{2}}Sh$ |
2 | 2 | 0.01 | 5 | 1 | 0.4 | 0.4 | 0.2 | 7 | 0.127 830 7934 |
2 | 2 | 0.01 | 5 | 1 | 0.4 | 0.4 | 0.4 | 7 | 0.141 073 9103 |
2 | 2 | 0.01 | 5 | 1 | 0.4 | 0.4 | 0.6 | 7 | 0.294 137 7066 |
2 | 2 | 0.01 | 5 | 1 | 0.4 | 0.4 | 0.8 | 7 | 0.307 232 1177 |
2 | 2 | 0.01 | 5 | 1 | 0.2 | 0.4 | 0.1 | 7 | 0.102 663 3317 |
2 | 2 | 0.01 | 5 | 1 | 0.3 | 0.4 | 0.1 | 7 | 0.101 851 7903 |
2 | 2 | 0.01 | 5 | 1 | 0.4 | 0.4 | 0.1 | 7 | 0.093 584 0243 |
2 | 2 | 0.01 | 5 | 1 | 0.5 | 0.4 | 0.1 | 7 | 0.095 747 2218 |
2 | 2 | 0.01 | 5 | 1 | 0.4 | 0.1 | 0.1 | 7 | 0.075 010 4120 |
2 | 2 | 0.01 | 5 | 1 | 0.4 | 0.2 | 0.1 | 7 | 0.084 432 5427 |
2 | 2 | 0.01 | 5 | 1 | 0.4 | 0.3 | 0.1 | 7 | 0.087 396 3154 |
2 | 2 | 0.01 | 5 | 1 | 0.4 | 0.4 | 0.1 | 7 | 0.093 584 0243 |
New window|CSV
Whereas the local Sherwood number increases with the increasing values of ${N}_{b}.$
Figures 2-5 demonstrate the velocity profiles for different parameters like $M,$ $\alpha ,$ $\delta$and $N.$ The consequence of an applied magnetic field $M$ in the transverse direction on flow over a stretching sheet is shown in figure 2. It is observed that the increase in magnetic field reduces the fluid velocity. In general, an increase in the applied magnetic field in the transverse direction produces the Lorentz force which opposes the flow. We observed that the Lorentz force effect reduces the flow of the velocity profile. Figure 3 indicates that the fluid flow increases with increasing $\alpha$, thus thickening the boundary velocity layer. Figures 4 and 5 give an insight into the effect of ${\rm{\lambda }}$ and $N$ on velocity. From figure 4 it is conspicuous that the velocity profile increases with increasing values of ${\rm{\lambda }}.$ Figure 5 indicates that the velocity profile increases with the increasing values of $N$ (ratio of mass and heat transfer Grashof numbers) due to the buoyancy effect.
Figure 2.
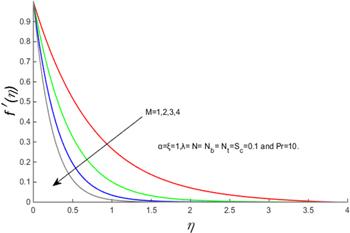
Figure 2.$f^{\prime} \left(\eta \right)$ for several values of $ \mbox{``} M\mbox{''}.$
Figure 3.
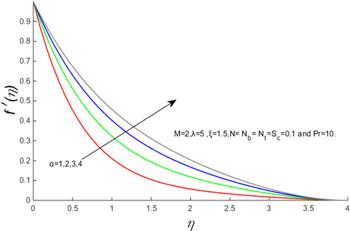
Figure 3.$f^{\prime} \left(\eta \right)$ for several values of '$\alpha$’.
Figure 4.
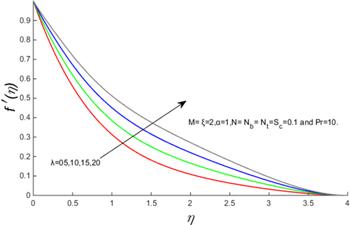
Figure 4.$f^{\prime} \left(\eta \right)$ for several values of 'λ’.
Figure 5.
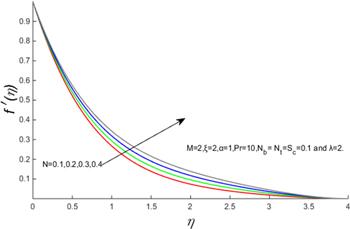
Figure 5.$f^{\prime} \left(\eta \right)$ for several values of 'N’.
Figure 6 reveals that the effect of increasing the $Pr$ is a decrease in the temperature profile. The ratio of momentum diffusivity and thermal diffusivity is specified by the Prandtl number. So, it is clear that the rise in $Pr$ decreases the thickness of the thermal boundary layer. Figure 7 expresses the dimensionless temperature for several values of ${N}_{b}.$ It shows that due to a rise in the values of ${N}_{b},$ the temperature profile decreases. From figure 8 it is seen that the temperature profile rises with the increasing values of the thermophoresis parameter ${N}_{t}.$
Figure 6.
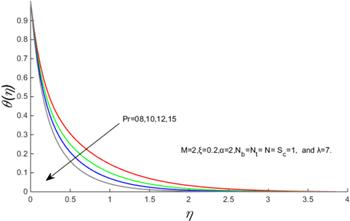
Figure 6.$\theta \left(\eta \right)$ for several values of '$Pr$’.
Figure 7.
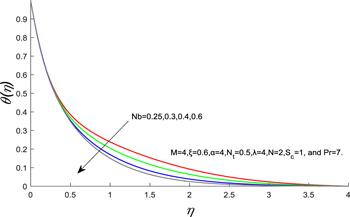
Figure 7.$\theta \left(\eta \right)$ for several values of '${N}_{b}$’.
Figure 8.
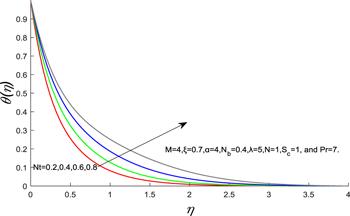
Figure 8.$\theta \left(\eta \right)$ for several values of '${N}_{t}$’.
Figure 9 shows the influence of the Schmidt number ${S}_{c}$ on the mass concentration profile. It is seen that a rise in ${S}_{c}$ leads to a reduction in the concentration boundary layer thickness. Figure 10 explains the impact of the Brownian motion parameter ${N}_{b}$ on the mass concentration profile. It is evident from the figure that the concentration profile rises with the upsurge in the values of ${N}_{b}.$ The influence of the thermophoresis parameter ${N}_{t}$ on the concentration profile is illustrated in figure 11. It is perceived that the concentration profile decreases with the increase in ${N}_{t}.$
Figure 9.
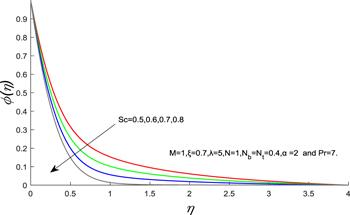
Figure 9.$\phi \left(\eta \right)$ for several values of '${S}_{c}$’.
Figure 10.
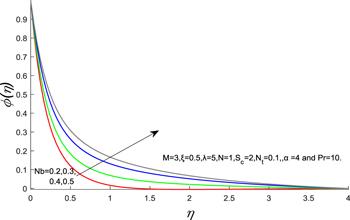
Figure 10.$\phi \left(\eta \right)$ for several values of '${N}_{b}$’.
Figure 11.
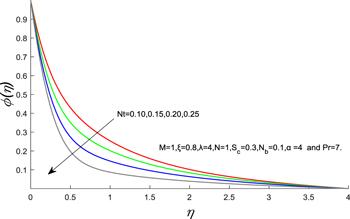
Figure 11.$\phi \left(\eta \right)$ for several values of '${N}_{t}$’.
7. Conclusions
In this research non-similar modeling is performed for second-grade magnetic nanofluid flow over a vertical surface which is stretching at an exponential rate. Non-similar solutions are obtained through local non-similarity via bvp4c. The important results are mentioned below. The velocity profile is increased by the increase in $N,$ $\delta$and $\alpha$, while the velocity profile decreases as a result of the increase in $M.$The temperature profile is increased due to the increase in ${N}_{t}$, although the temperature profile decreases due to the increase in ${N}_{b}$ and ${\rm{\Pr }}.$
The increase in the value ${N}_{b}$ leads to the rise in the volumetric concentration profile, while the opposite is true for ${S}_{c}$ and ${N}_{t}.$
Local skin friction increases due to the increase in the values of $\alpha ,\,\lambda $ and $N$ and slightly decreases as the values of the $M$ increase.
It is observed that the local Nusselt number upsurges against the ${N}_{b}$, whereas it declines by uplifting the ${\rm{\Pr }}$ and ${N}_{t}$ parameters.
The local Sherwood number decreases with the increase in ${N}_{t}\,{\rm{and}}\,{S}_{c}$, but the effect is the reverse for ${N}_{b}.$
Reference By original order
By published year
By cited within times
By Impact factor
DOI:10.1002/aic.690070211 [Cited within: 1]
DOI:10.1021/i160017a004 [Cited within: 1]
DOI:10.1007/BF01587695 [Cited within: 2]
DOI:10.1002/cjce.5450550619 [Cited within: 1]
DOI:10.1007/BF01332078 [Cited within: 1]
DOI:10.1007/BF00946345 [Cited within: 1]
DOI:10.1088/0022-3727/32/5/012 [Cited within: 1]
[Cited within: 1]
DOI:10.1007/s00231-004-0552-2 [Cited within: 1]
DOI:10.1016/j.ijheatmasstransfer.2004.10.032 [Cited within: 1]
DOI:10.1016/j.euromechflu.2005.12.003 [Cited within: 1]
DOI:10.1016/j.ijheatmasstransfer.2005.07.049 [Cited within: 1]
DOI:10.1016/j.ijheatmasstransfer.2007.01.003 [Cited within: 1]
DOI:10.1115/1.2723816 [Cited within: 1]
DOI:10.1016/j.icheatmasstransfer.2007.08.006 [Cited within: 1]
DOI:10.36884/jafm.7.01.19473 [Cited within: 1]
DOI:10.36884/jafm.7.01.19473 [Cited within: 1]
DOI:10.1016/j.rinp.2016.10.011 [Cited within: 1]
DOI:10.1016/j.molliq.2018.10.028 [Cited within: 1]
DOI:10.1108/MMMS-11-2019-0203 [Cited within: 1]
DOI:10.1016/j.physa.2019.124004 [Cited within: 1]
DOI:10.1016/j.cjph.2020.08.012 [Cited within: 1]
DOI:10.1007/s13204-020-01498-5 [Cited within: 1]
[Cited within: 1]
DOI:10.1090/qam/427829 [Cited within: 1]
DOI:10.1016/j.amc.2009.12.016
DOI:10.1007/s11075-014-9934-9 [Cited within: 1]
DOI:10.1115/1.3449827 [Cited within: 1]
DOI:10.1016/j.rinp.2017.07.023 [Cited within: 1]
DOI:10.1016/j.ijheatmasstransfer.2017.05.108 [Cited within: 1]
DOI:10.1007/s40819-019-0765-1 [Cited within: 1]
DOI:10.1016/j.icheatmasstransfer.2020.104955 [Cited within: 1]