全文HTML
--> --> -->石墨烯作为一种新型材料, 自从2004年被Geim和Novoselov[11]用胶带对粘的方法获得以来, 持续受到科学界和工业界的广泛关注. 石墨烯是最薄的二维材料, 由碳原子以sp2杂化连接成单层二维蜂窝状晶格. 因其自身出色的化学惰性和抗渗透性, 致密的石墨烯晶格可以在金属表面形成一层腐蚀防护罩. 除此之外, 石墨烯的高透光率和良好的柔韧性也可以保留金属的光学外观和表面粗糙度[12-14]. 这些特性使石墨烯材料在一众防腐材料中脱颖而出. 在石墨烯逐步实现工业化的进程中, 石墨烯的制造成本逐渐降低, 这使得石墨烯在防腐领域的应用也成为可能. 与已有的关于石墨烯在防腐领域的综述相比[15,16], 本文结合最新的研究成果, 对包括石墨烯薄膜及石墨烯粉体在防腐领域的应用进行更加全面的讨论, 从石墨烯防腐作用机理和其相应的涂层制备方法开始, 进而探讨不同因素对石墨烯防腐效果的影响, 最后对各种方法进行综合比较, 并对未来的发展进行展望. 本综述通过对已有工作的回顾, 为今后制备防腐性能更加优良的石墨烯材料提供重要的参考.
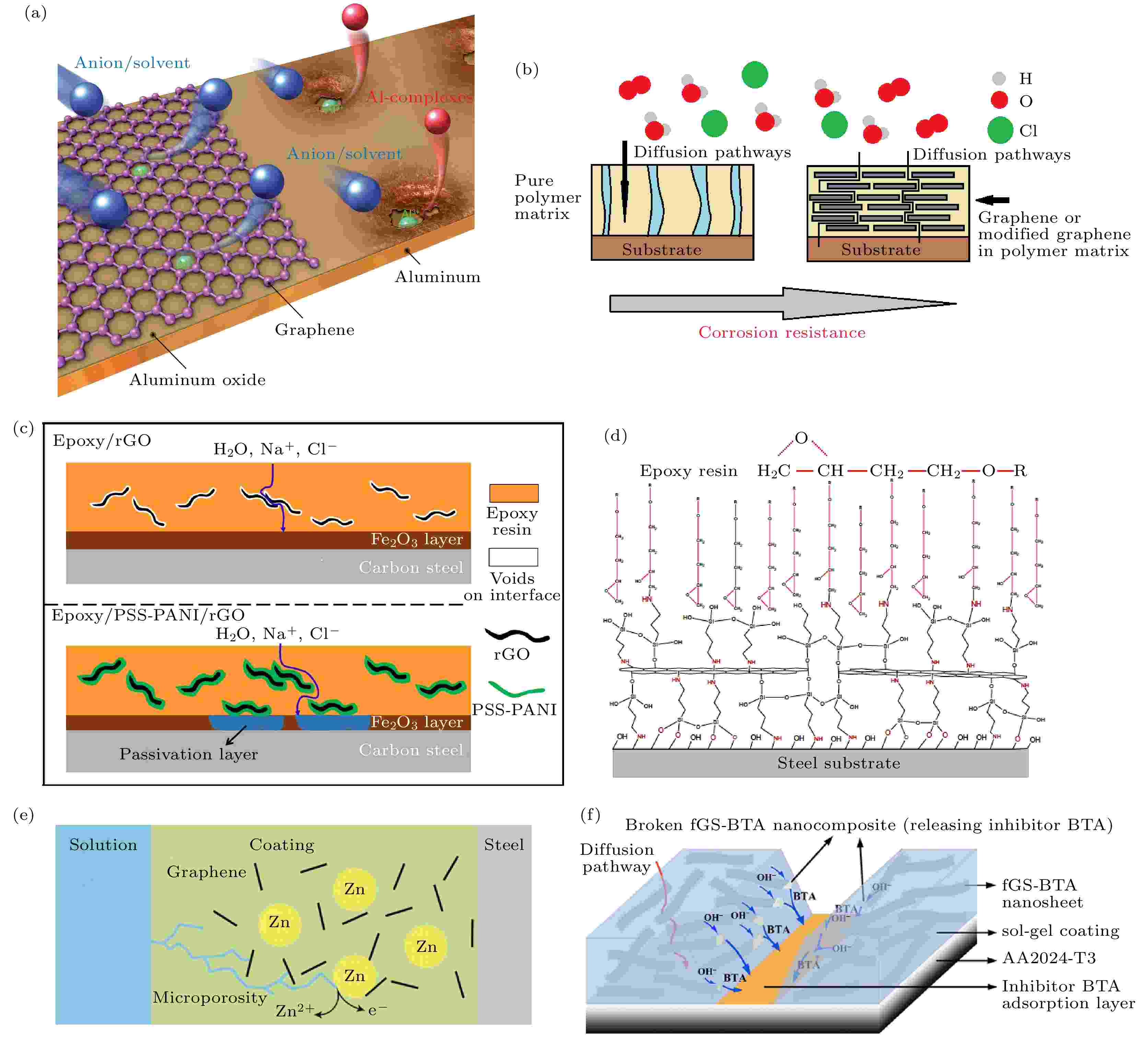
Figure1. Anticorrosion mechanism of graphene: (a) Barrier effect[13]; (b) shielding effect[17]; (c) corrosion inhibition synergy[18]; (d) enhancement of coating adhesion[19]; (e) cathodic protection[20]; (f) self-healing effect[21].
3.1.连续石墨烯薄膜防腐层
由于石墨烯致密的晶格结构可以有效地阻隔氧、水、盐离子等腐蚀性物质, 因此, 在金属表面上覆盖一层完美结构的石墨烯薄膜可以防止金属被腐蚀. 可以通过化学气相沉积(CVD)法在金属表面直接生长连续的大面积石墨烯薄膜[22], 尤其是基于Cu基底的CVD法, 是当前大面积石墨烯薄膜制备最普遍的方法, 该方法由Li等[23]于2009年发明. 该课题组于2011年最先报道了CVD石墨烯薄膜在金属防腐领域的应用[24], 如图2所示. 研究发现, 通过CVD法在Cu和Cu/Ni基底上生长石墨烯薄膜, 即使在200 ℃时也可以很好地防止金属被氧化. Kirkland等[25]通过电化学测试证明通过CVD法在Cu和Ni上生长的石墨烯薄膜可以降低金属的短期腐蚀速率. Pu等[26]在SUS304不锈钢上镀了一层5 μm的Ni层来控制碳扩散过程, 并通过CVD法使石墨烯直接生长在其表面. 比较纯SUS304不锈钢和覆盖了石墨烯和镍层的SUS304不锈钢(Gr/Ni/SUS304)的腐蚀电流测试结果发现, Gr/Ni/SUS304表面并未体现出类似于纯SUS304不锈钢样品的钝化或点蚀极化曲线, 说明石墨烯作为涂层成功阻隔了氯离子与金属表面的相互作用, 从而抑制腐蚀发生. Zhu等[27]将聚苯乙烯(PS)作为碳源, 通过低温CVD法使石墨烯生长在钢板表面. 与裸钢相比, 表面覆盖有石墨烯层的钢板腐蚀速率降低了9倍. 对于无法直接生长石墨烯的金属, 通过将CVD石墨烯转移到目标基底上[28], 理论上可以起到同样的效果. Zheng等[29]在Cu基底上生长石墨烯薄膜后, 采用湿法转移工艺将石墨烯转移到铝合金基材上. 通过阻抗和极化测试发现, 覆盖有石墨烯的铝合金表面测到了更大的阻抗数值和较小的电流密度, 证明了转移的石墨烯薄膜发挥了防腐作用. 需要指出的是, 上述工作中所用的石墨烯薄膜, 拉曼光谱表征均显示出可见的甚至较高的D峰, 表明石墨烯薄膜较高的缺陷密度[25-27,29].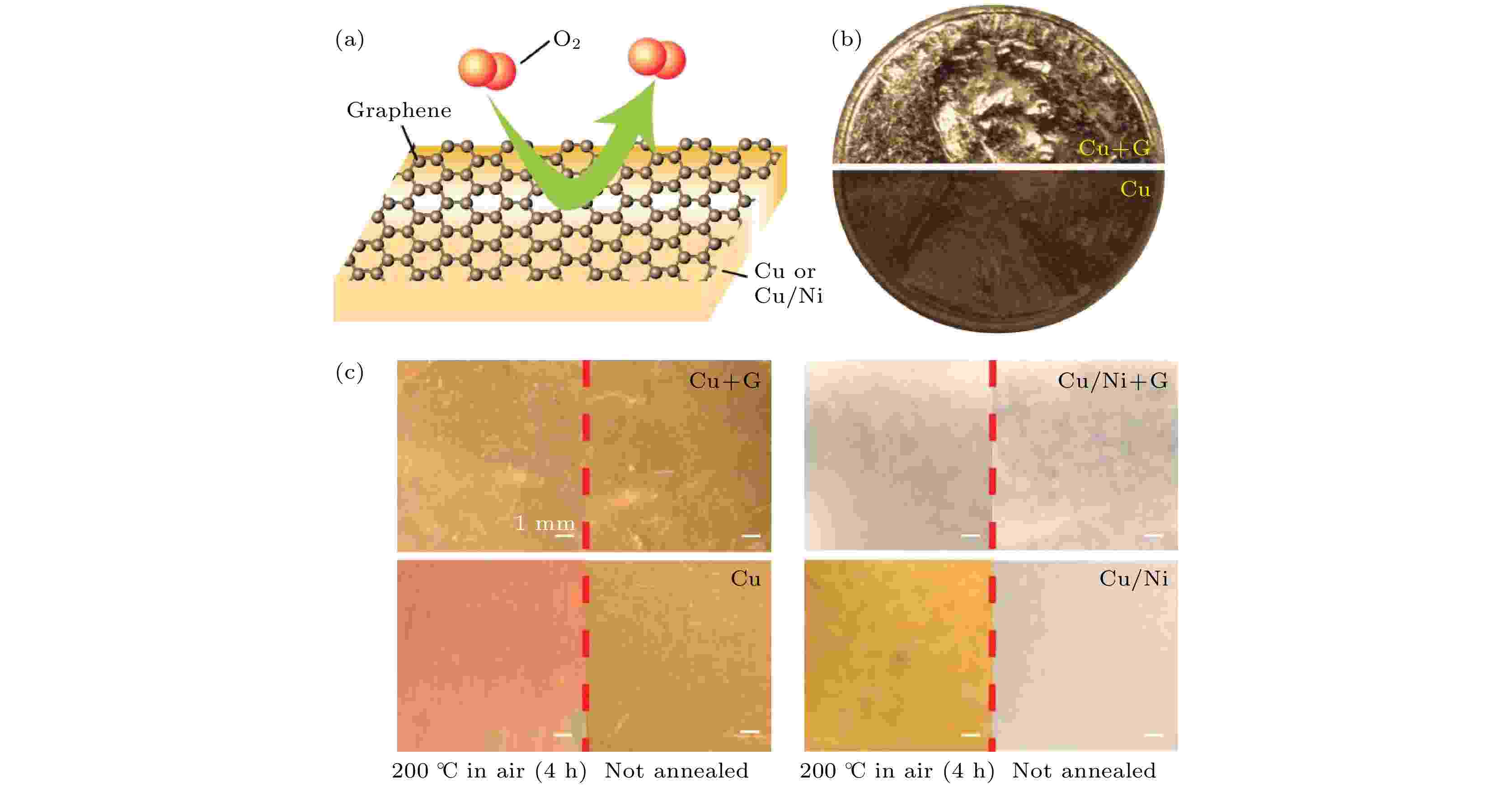
Figure2. Performance of CVD graphene as an anticorrosion layer[24]: (a) Schematics of graphene as a chemically inert diffusion barrier; (b) photograph showing graphene coated (upper) and uncoated (lower) penny after H2O2 treatment (30%, 2 min); (c) photographs of Cu and Cu/Ni foils with and without graphene coating taken before and after annealing in air (200 °C, 4 h).
2
3.2.石墨烯防腐涂料
与石墨烯薄膜的制备与应用相比, 石墨烯粉体的制备与应用更加广泛, 其中一个比较成功的应用是将石墨烯粉体作为功能性填料加入防腐涂料中, 以提高现有涂料的性能, 或者降低成本.Yang等[30]开发了一种原位聚合方法来制备氧化石墨烯/聚苯胺(GO/PANI)纳米复合材料, 将所制备的复合材料分散在环氧树脂中, 然后涂覆在钢表面. 通过电化学阻抗(EIS)测试发现, 当频率为0.01 Hz时, 与GO/PANI混合后的环氧树脂涂料测得的阻抗值是纯环氧树脂涂料所测数值的55.22倍, 是环氧树脂/PANI所测数值的12.4倍, 表明氧化石墨烯的加入使该复合材料获得了更好的缓蚀效果. 这一防腐性能的提高, 被归结于氧化石墨烯对PANI团聚现象的抑制作用, 并通过填充在环氧树脂与金属表面形成的空隙, 进一步阻隔腐蚀介质的干扰, 发挥了屏蔽防腐的作用. Lin等[18]同样使用原位聚合的方法, 在聚苯乙烯磺酸(PSS)盐溶液中制备聚苯胺(PANI)/还原氧化石墨烯(rGO)复合涂层(PSS-PANI/rGO). 当PANI与铁表面接触时, 可以促使其发生氧化反应, 形成由Fe2O3和Fe3O4组成的致密钝化层. 通过X射线光电子能谱分析发现, 在涂层与金属表面间生成了一层Fe3O4氧化膜, 导致腐蚀电位正向迁移; 此外, 引入的rGO还可以改善团聚现象, 增加气体和离子扩散路径的曲折度从而降低腐蚀电流密度. 由此推测, PSS-PANI/rGO复合材料优异的防腐效果是PANI在金属表面形成的钝化膜与rGO屏蔽机制共同作用的结果.
防腐效果不仅与涂层自身性能相关, 还需要涂层与金属表面有足够强的结合力, 避免涂层的分离和脱落. Parhizkar等[19]通过剥离实验研究了进行功能化处理的氧化石墨烯(FGO)膜对钢表面与环氧涂层之间附着力的影响. 实验发现, FGO膜可以为钢材表面提供—NH2基团, 而在钢表面涂上环氧涂料后, 环氧涂料中存在的环氧基团将与钢表面的—NH2基团形成较强的共价键, 从而改善涂层与金属表面的黏合强度和耐腐蚀性. Xu等[31]将使用简单的球磨法制备的石墨烯均匀包覆在不锈钢球上, 操作方法如图3所示. 铬(Cr)是组成不锈钢的基本成分, 对于提高不锈钢的耐腐蚀性发挥着极大作用. 石墨烯层可以与钢表面反应形成Cr—C键, 并借助Cr—C键牢固地与不锈钢球结合, 由此改善界面间的相互作用. 包覆了石墨烯涂层的不锈钢球不但腐蚀速率明显减慢, 而且在室温下的摩擦系数也有所降低.
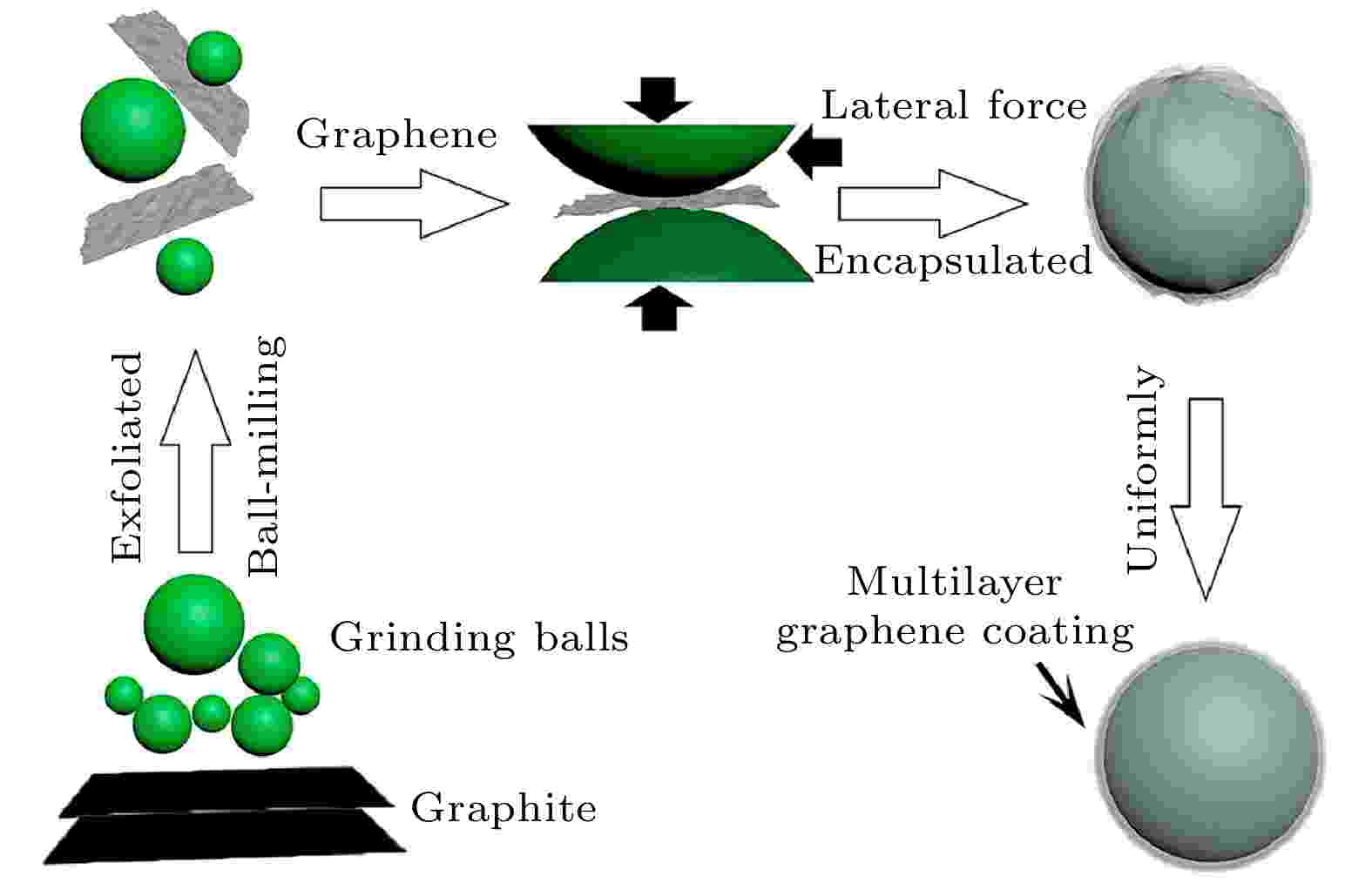
Figure3. Schematics of the preparation of graphene coated stainless steel balls[31].
Ding等[20]研究了石墨烯改性的低锌水性涂料的腐蚀电位和阻抗, 发现石墨烯可以使外层的锌作为阳极后继续与铁构成电偶保护, 即通过阻止电偶腐蚀的发生发挥阴极保护作用, 从而一定程度上延长了涂层的保护作用. Xiao等[32]通过原位聚合的方法合成出分散性良好的GO/PANI复合材料, 并将其掺入锌基涂料中. 当锌基水性涂料中引入少量GO/PANI (质量分数为0.5%)时, 可以完美地保留GO的片层结构, 修饰涂料的阴极保护性能. 同时, GO/PANI复合材料自身良好的屏蔽作用也可以阻止腐蚀介质渗透到钢材表面, 从而表现出良好的耐腐蚀持久性.
2
3.3.电泳沉积石墨烯涂层
电泳沉积(EPD)法是将带电胶体粒子在通有直流电场的悬浮液中沉积到电极上的过程. He等[33]通过EPD在钕铁硼磁铁(NdFeB)的表面形成均匀的EPD-GO涂层. EPD过程会一定程度地还原GO. 这种EPD-GO涂层对NdFeB基底表现出优异的附着力. 根据电化学测试的结果, 腐蚀电流密度的降低和腐蚀电位的正向移动都表明EPD-GO涂层可作为防腐层, 保护NdFeB免受NaCl水溶液的侵蚀. Szeptycka等[34]使用电化学还原法沉积Ni/石墨烯复合涂层. 随着镀液中石墨烯含量的增加, 更多的石墨烯微片被引入涂层, 与Ni同时沉积在金属表面形成Ni/石墨烯复合涂层, 使金属表面暴露在溶液中的面积越来越小. 由此, 与Ni涂层相比, Ni/石墨烯复合涂层具有更好的耐腐蚀性.2
3.4.石墨烯改性缓蚀剂
对于大多数的有机缓蚀剂, 分子中含有N[35,36], S[37], O[38]等杂原子很容易与可以提供空轨道的金属表面形成配位键. 单纯的石墨烯由于自身的非极性性质和无官能团的特点会降低其在水性介质中的溶解度. 而GO结构中含有的丰富的含氧基团使其具备更好的分散性和亲水性. Cen和Chen[39]提出了一种新型石墨烯材料防腐方法, 即作为溶液中的缓蚀剂, 通过吸附在金属界面上来对腐蚀行为进行抑制, 缓蚀机理如图4所示. 功能性氧化石墨烯(FGO)的聚集团在金属表面形成了一层疏水保护膜, 用来隔离溶液中的腐蚀介质. 当FGO的含量为20 mg/L时, 缓蚀效率达到了83.4%, 证明了其作为缓蚀剂优异的防腐能力. 从图4可以看到, 添加FGO后, 颗粒通过扩散效应封闭到界面, 纳米粒子上的含氮杂环与Fe形成共轭键, 从而在金属表面实现化学吸附. Baig等[40]合成了一种二亚乙基三胺官能化的氧化石墨烯(DETA-GO); 将低碳钢样品分别浸入空白和存在不同浓度DETA-GO的1 mol/L HCl溶液, 持续12 h. EIS测试结果显示浸入含有DETA-GO的溶液中的样品阻抗的圆弧半径明显增大, 表明DETA-GO通过吸附在低碳钢表面而抑制腐蚀. DETA-GO的缓蚀效率随着浓度的增加而增加, 当浓度达到25 mg/L时, 得到最佳缓蚀效率92.67%. 进一步地, Baig等[40]通过分子动力学模拟了DETA, GO和DETA-GO的最高占据分子轨道(HOMO)和最低未占据分子轨道(LUMO)的分布图(图5). 其中, DETA的HOMO和LUMO区域主要沿着支链上的氨基进行覆盖; 而GO的HOMO和LUMO区域则分布在苯环和环氧基上. DETA-GO的HOMO主要以GO为中心进行覆盖, 而LUMO的分布与GO相同, 表明DETA-GO中GO对防腐行为起主要贡献.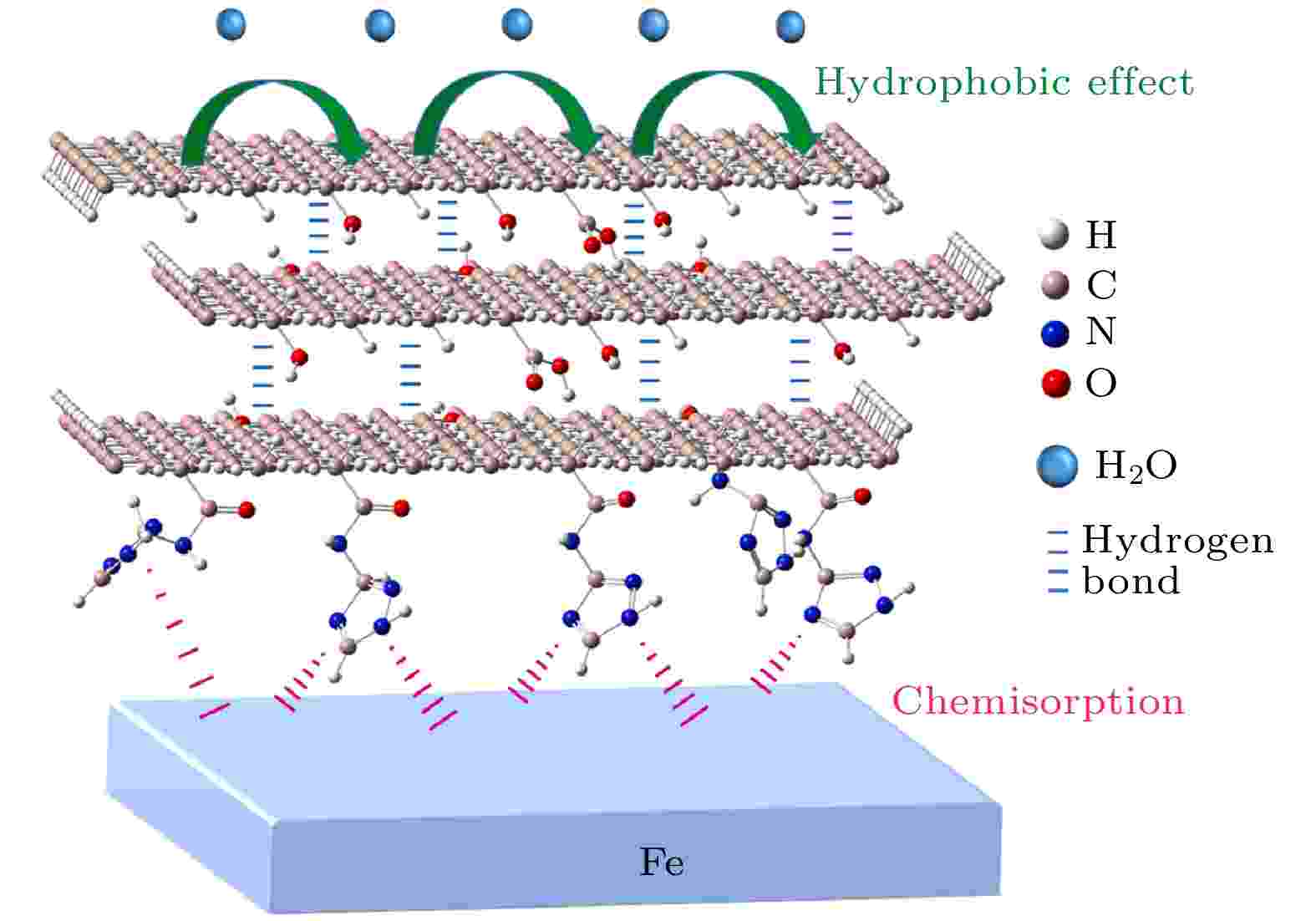
Figure4. Schematics of inhibition mechanism on carbon steel surface for FGO in solution[39].
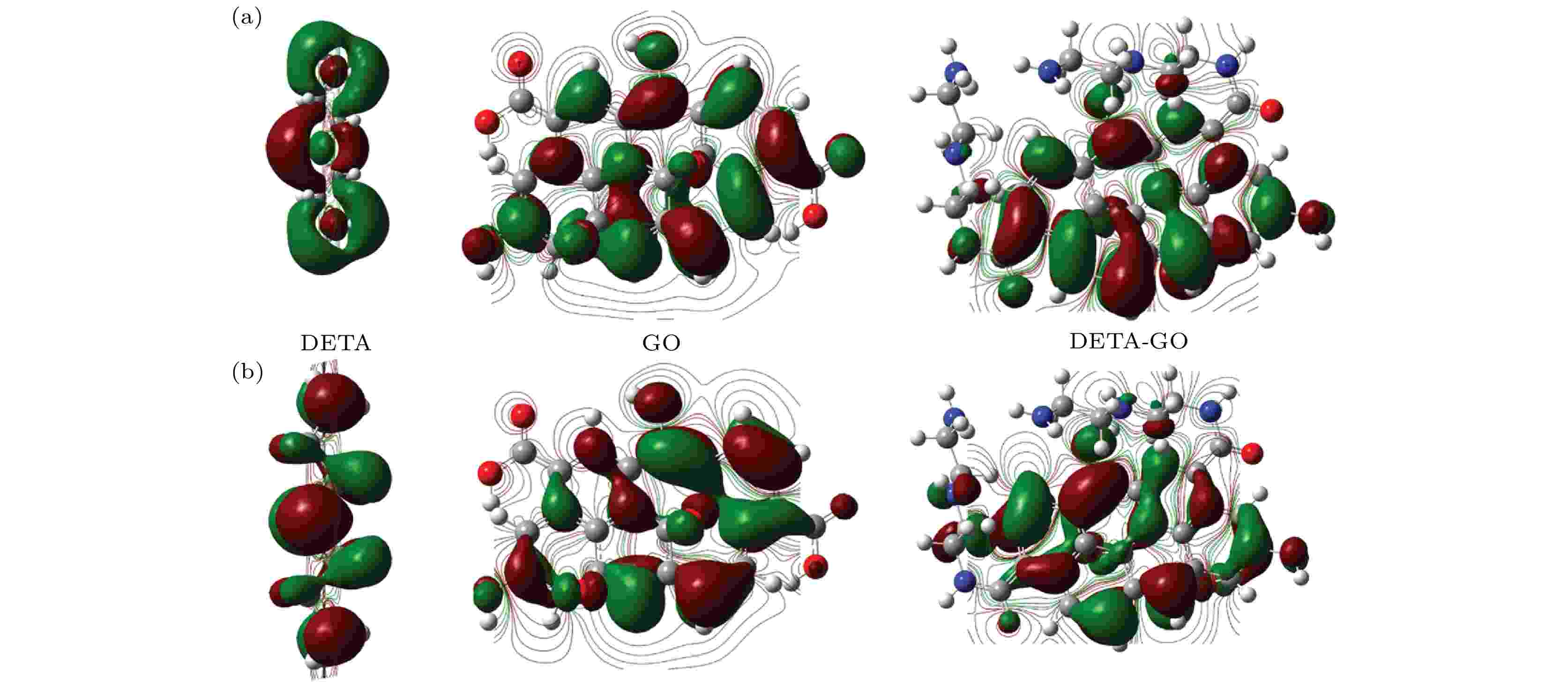
Figure5. HOMO and LUMO distribution maps of DETA, GO and DETA-GO[40]: (a) LUMO; (b) HOMO.
2
3.5.自修复防腐涂层
微胶囊技术在涂层的制备中非常常见, 该方法主要是将自修复剂封装进微胶囊或包衣中, 当涂层破裂时, 自修复剂会自动释放出来在涂层缺陷处形成保护膜, 从而防止金属进一步腐蚀. Zhao等[41]通过聚合作用合成了一种可以承载苯并三氮唑(BTA)分子的中空微球, 制备方法如图6所示. 通过紫外吸收法验证了BTA的释放可以通过pH值变化进行控制, 即在中性溶液中, 微球中的孔隙处于封闭状态; 而在酸性或碱性条件下, 它会逐渐打开, 由此实现控释的作用.
Figure6. Schematics of the preparation of raspberry-like hollow polymeric microspheres loaded with BTA[41].
然而, 仅仅通过微胶囊技术还不足以使涂层获得长期保护能力. 对于自修复涂料而言, 获得优异的阻隔性能仍然极为重要. Ye等[42]制备了承载BTA缓蚀剂的石墨烯基纳米容器. 其中, 通过添加多面低聚倍半硅氧烷(POSS)来增加石墨烯的溶解性, 制备过程如图7所示. 随着浸泡时间的增加, 纯环氧涂层(EP)下的腐蚀和扩散现象非常严重. 而8-PG(POSS/GO)-BTA/EP复合涂层随着时间的推移腐蚀效果逐渐减弱. 这可以归因于BTA分子的释放修复了涂层的缺陷: 一方面被释放的BTA分子被吸附在钢材表面发挥缓蚀作用, 另一方面BTA显著提高了石墨烯涂层的致密性, 抑制了腐蚀介质的纵向扩散, 从而达到防腐的效果(图8). 除了BTA分子可以用作缓蚀剂分子外, Kasaeian等[43]选择苯并咪唑(BIM)与GO进行非共价官能化, 探究BIM在GO纳米片上吸附的最佳条件. 扫描电子显微镜(SEM)测试结果表明, 将表面带有划痕的钢浸泡在含有GO-BIM纳米片的氯化物溶液中后, 划痕部位沉积了一层保护膜, 且划痕内部的膜的形态与BIM分子十分相似. 由此可知, BIM分子从GO上脱离后, 转而吸附在金属表面的缺陷部位上, 证明了GO-BIM涂层优异的自修复能力.
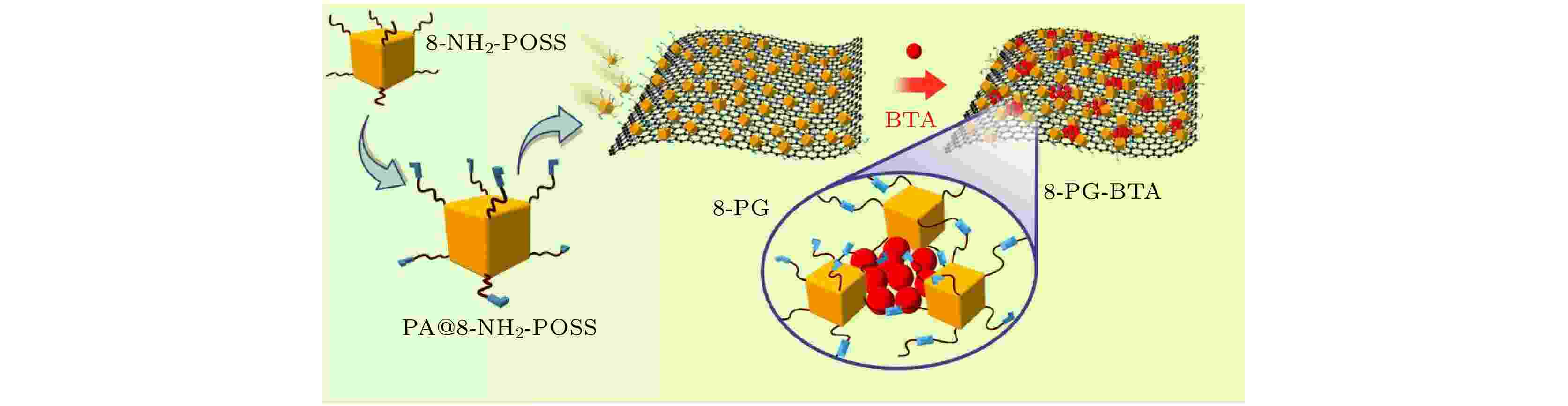
Figure7. Preparation process of graphene-based nanocontainer[42].
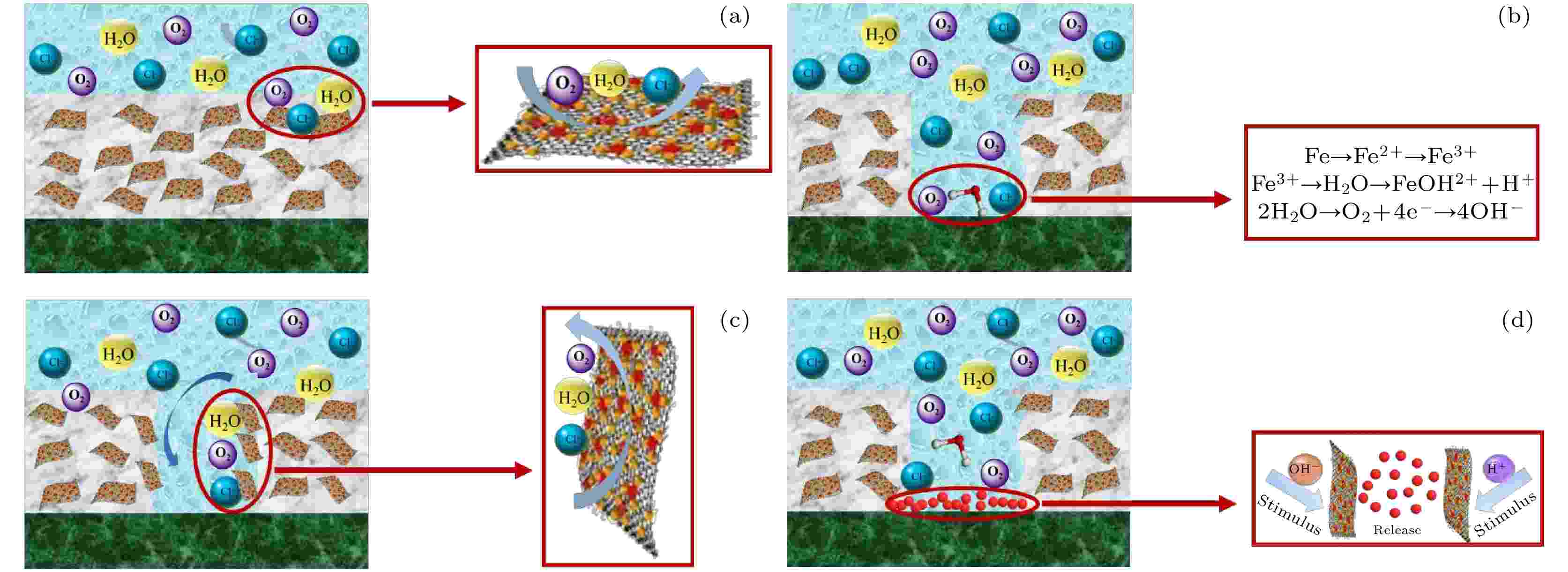
Figure8. Corrosion protection mechanism of 8-PG-BTA/EP coating[42]: (a) Intact coating; (b) defect; (c) corrosion reaction; (d) self-healing behavior.
4.1.石墨烯的缺陷
尽管理论上, 完美结构的石墨烯薄膜可以完全阻隔腐蚀介质对金属表面的作用, 但现有CVD技术制备的石墨烯薄膜仍不可避免地存在结构缺陷, 例如空位、晶界、褶皱等[44-46], 而对于转移的石墨烯薄膜还常常会产生裂缝[47,48]. 当石墨烯作为防腐涂层却无法在金属表面实现均匀覆盖时, 具有一定导电性的石墨烯材料将会作为阴极与成为阳极的金属不断作用, 促进电化学反应反而加快金属腐蚀, 如图9所示[14].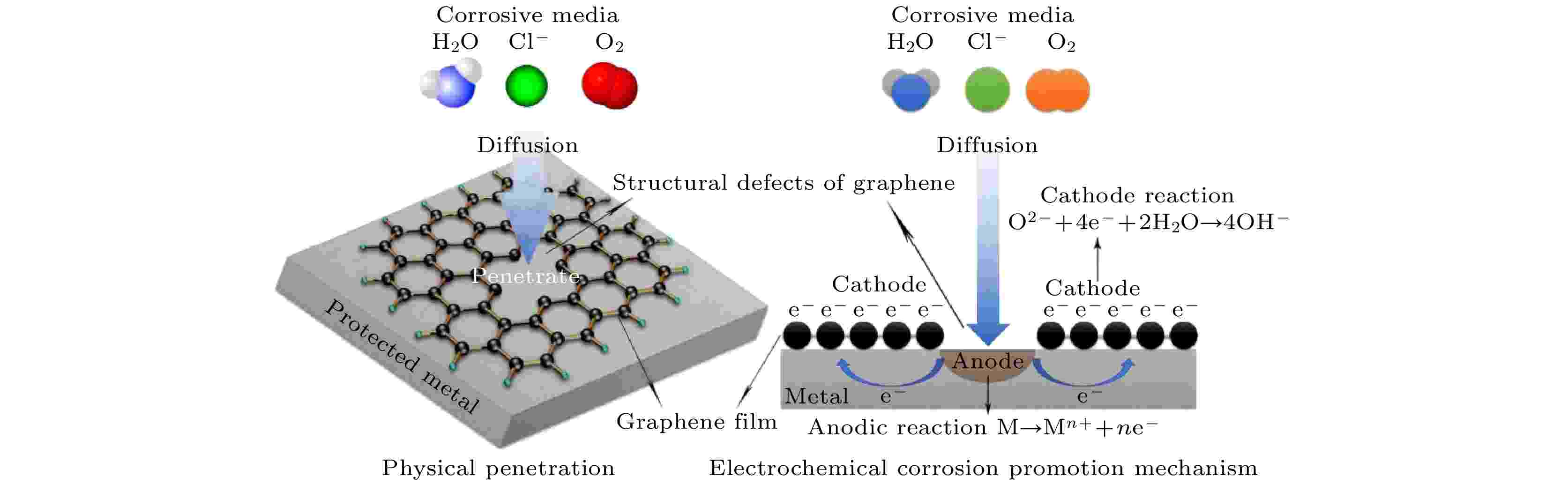
Figure9. Defects of graphene films promote the corrosion of metals[14].
Prasai等[49]在转移多层石墨烯到目标金属表面上时发现, 金属在石墨烯薄膜的裂纹处会发生腐蚀. Zhou等[50]分别将通过CVD法生长出的石墨烯防腐涂层进行了长期和短期的测试. 在空气中暴露六个月后, 样品表面的石墨烯涂层出现了明显的缺陷, 氧气可以透过石墨烯薄膜表面的裂纹对金属进行腐蚀作用. 并且, 因其自身的高电导率, 当石墨烯薄膜与铜表面接触时, 可将电子从铜表面迁移到石墨烯表面, 从而促进金属的腐蚀. 因此, 与长期相比, 石墨烯防腐涂层在短时间内的防腐效果更好. 此外, Hsieh等[51]发现石墨烯薄膜上存在的缺陷在导致石墨烯钝化不完全的同时还将作为电化学反应中的阴极加速金属的腐蚀. 通过调整原子层沉积(ALD)生长的颗粒尺寸将缺陷部位选择性钝化, 可以反过来利用石墨烯薄膜的缺陷抑制腐蚀介质渗透进来, 从而增强石墨烯的防腐性能.
最近Zhao等[52]研究发现, 对于少层石墨烯, 由于各层之间缺陷(主要是晶界)交错排列, 就无法形成连续的扩散通道. 腐蚀分子除了要扩散通过晶界之外, 还必须在层与层之间进行连续扩散才可能达到金属表面. 而计算结果表明水分子虽然可以轻易地穿过单层石墨烯的晶界, 但几乎无法进入双层石墨烯层间, 从而避免了连续扩散的发生(图10).
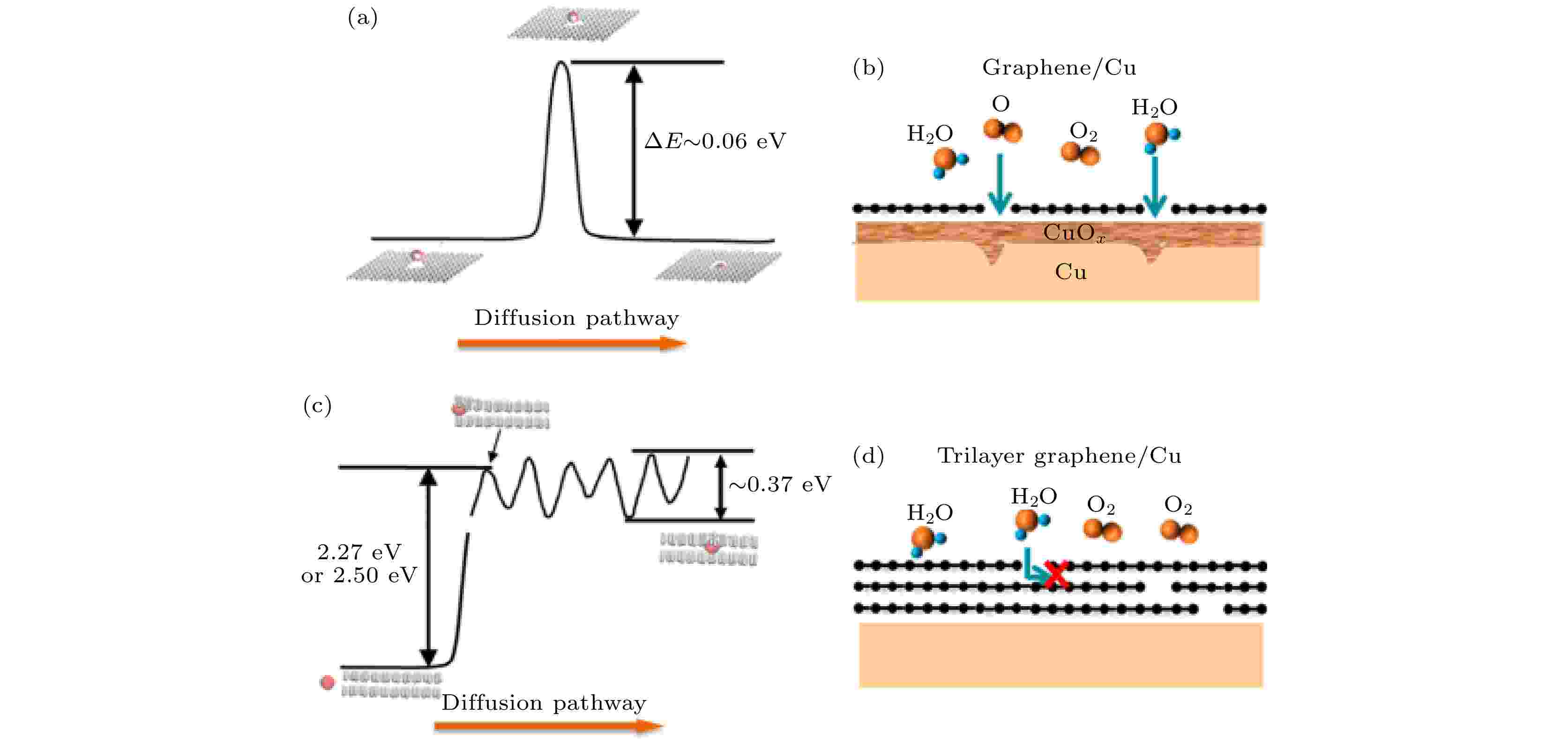
Figure10. Atomic-scale simulations of molecular diffusion through SLG and FLG[52]: (a) Schematics and the calculated energy barrier for a water molecule to diffuse through a defective SLG; (b) schematic showing the easiness of reactive species such as oxygen and water molecules to diffuse through SLG and oxidize the Cu surface; (c) schematics and the calculated energy barrier for a water molecule to diffuse through a defective BLG; (d) schematic showing the difficulties for oxygen and water molecules to diffuse through polycrystalline trilayer graphene and contact with the underlying Cu surface, even when the trilayer graphene contains multiple GB defects.
2
4.2.导电效应
由于石墨烯本身具有优异的导电性, 在石墨烯掺入涂层中进行防腐时, 一旦涂层出现裂纹或脱落, 石墨烯复合涂层也将作为阴极与金属发生微电流腐蚀行为, 增加了金属腐蚀的风险. 因此, 弄清涂层促进腐蚀的电导率阈值至关重要.Liu等[53]通过高速剪切的方法将具有高导电性的片状石墨烯与聚脲(PU)涂层相结合, 系统地研究了石墨烯对涂层局部缺陷的影响. 氧气渗透测试表明, 随着石墨烯浓度的增加, 涂层的O2渗透率的数值从9.24降到了2.73. 这说明, 石墨烯的加入在一定程度上增加了涂层的致密性, 而不是引入缺陷. 由于纯PU涂层是一种低电导率的绝缘材料, 复合涂层的电导率随着石墨烯含量的增加而逐渐增加. 根据电化学测试数据, 随着浸泡时间的增加, 涂层暴露在腐蚀性环境中, 腐蚀电流密度明显增大. 当石墨烯负载量达到0.1% (质量分数)时, 石墨烯对金属的腐蚀表现出了明显的促进作用.
为了研究石墨烯的物理特性与复合材料的电导率之间的关系, Jun等[54]比较了两种尺寸不同的石墨烯(2—15 μm及 > 100 μm)合成的石墨烯/聚二甲基硅氧烷复合材料的电导率, 发现大尺寸石墨烯微片有利于聚合物复合材料电导率的提高.
2
4.3.石墨烯的氧化程度
Guerrero-Contreras和Caballero-Briones[55]制备了不同O/C比的石墨烯粉末. 研究指出, 氧原子的存在会影响电子态密度, 并且在R—OH和R—O—R基团之间形成氢键可能会降低费米能级附近的能态密度, 这将进一步增强材料的功函数. Krishnamoorthy等[56]通过调节反应过程中的氧化剂含量合成六种不同氧化程度的氧化石墨烯. 电化学测试结果如图11所示, 随着石墨烯氧化水平的加深, 样品表面的电荷随之增加, 电势也呈线性增加. 其中, 具有较高氧化程度的两个样品由于表面的高电荷量被电极表面排斥, 从而限制了电化学反应, 呈现出金属到半导体再到绝缘体的趋势. 因此, 通过控制石墨烯的氧化程度可以帮助复合材料获得不同的修饰, 为提高涂层的防腐性能增加了可能性.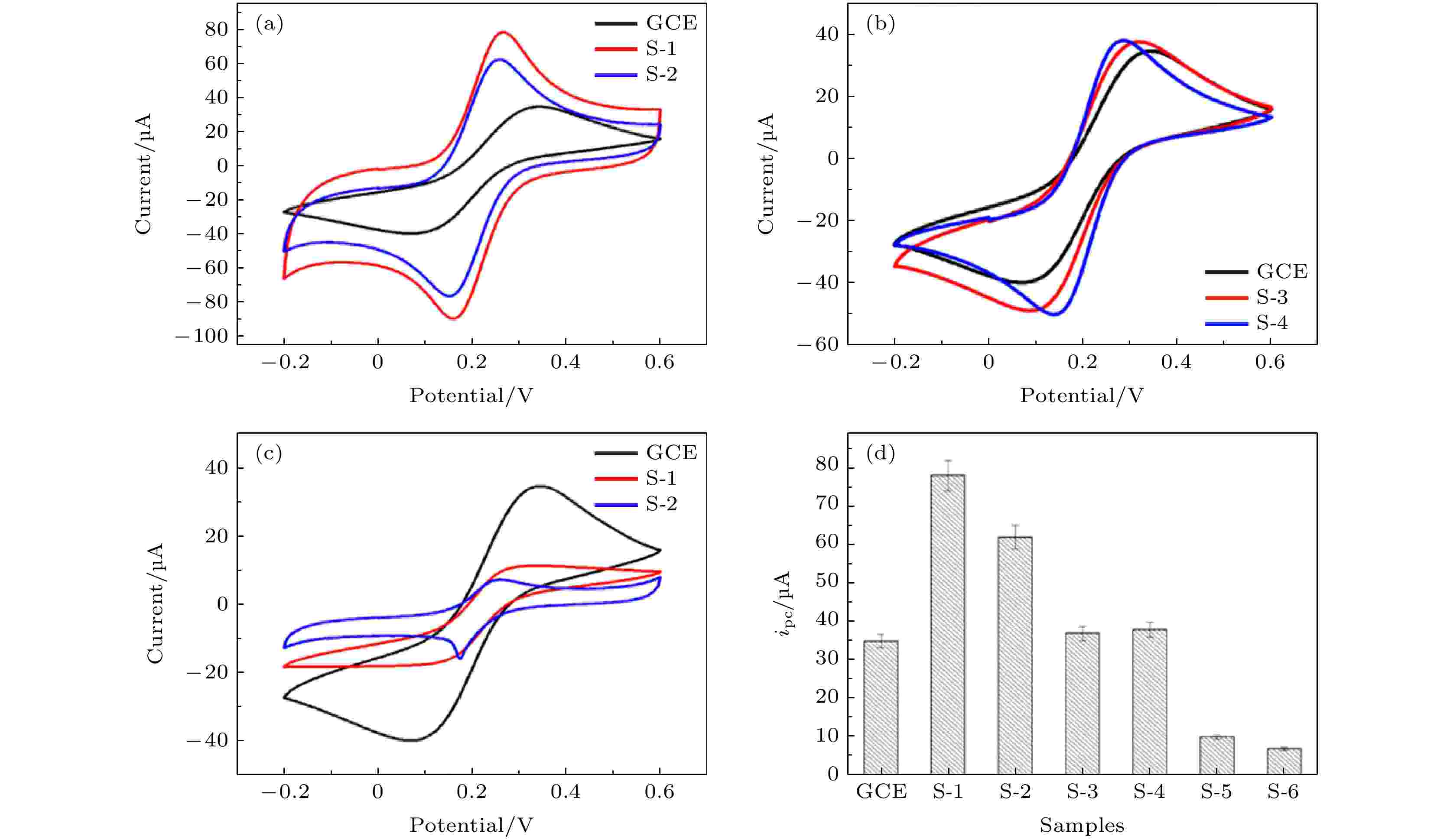
Figure11. (a)?(c) Cyclic voltammetry of GO samples (S-1 to S-6) modified on GCE in 5 mmol/L K3[Fe(CN)6] containing 0.1 mol/L KCl solution; (d) Ipc of the samples with different oxidation levels[56].
2
4.4.氧化石墨烯的片层大小
石墨烯材料的片层大小也会对涂层的防腐性能产生显著影响. 大尺寸的石墨烯在涂层上可能会存在一些裂纹或缝隙, 为腐蚀介质提供渗透到金属表面的途径. Sato等[57]合成三种不同尺寸的Pt/石墨烯复合材料, 对它们的氧化还原活性进行了比较, 首次提出了石墨烯复合材料的尺寸效应. Ramezanzadeh等[58]使用量子力学的方法研究了三种不同尺寸的氧化石墨烯纳米片(0.85, 8.2和38 μm)对环氧复合材料耐腐蚀性的影响. 通过构建环氧树脂与GO表面的量子力学计算模型分析得到, 随着GO尺寸的减小, 更多数量的二胺基团会被枝接到GO的表面. 与环氧树脂内的氢键相互作用, 使得环氧复合材料的防腐性能得到改善.除此之外, 石墨烯材料的尺寸在一定程度上也会影响复合材料的机械性能. 比如, 材料的断裂伸长率和拉伸强度等. 断裂伸长率高, 拉伸强度大, 说明涂层对于发生伸缩、开裂、变形等情况的适应性强. 较大面积的石墨烯材料分散性较差, 从而降低涂层的机械性能和防腐性能. Um等[59]制备了聚氨酯/石墨烯纳米片(PU/GnP)复合材料, 研究GnP尺寸对复合材料机械性能和耐腐蚀性能的影响. 其横截面的SEM表征结果如图12所示, 可以看出, 大尺寸的GnP断裂伸长率最低, 而尺寸较小的GnP均匀地分散在PU中, 在提高材料机械性能的同时, 也延长了腐蚀介质到金属表面(Cu)的扩散路径(图13). GnP的尺寸在决定PU/GnP复合材料的抗腐蚀性能中起着核心作用.
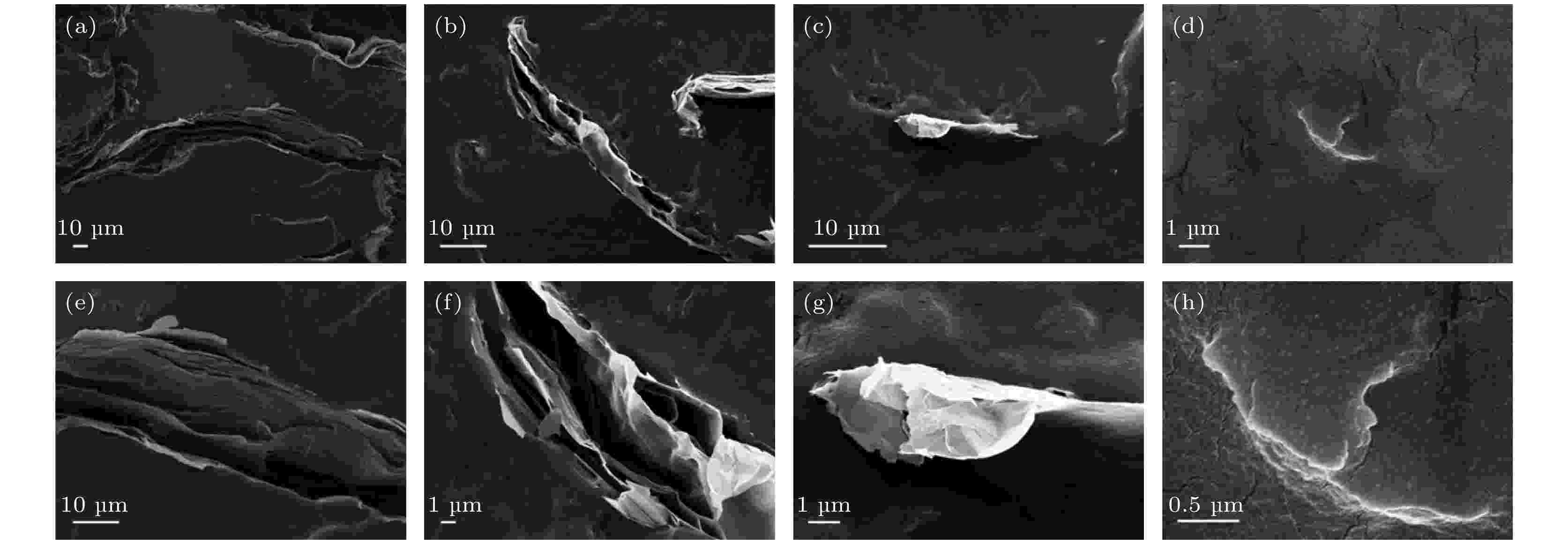
Figure12. Cross-sectional SEM images for the PU/GnP composites (GnP with weight fraction of 1%, (a)?(d) low magnification, (e)?(f) high magnification): (a), (e) PU/H100; (b), (f) PU/M25; (c), (g) PU/M5; (d), (h) PU/C750[59].
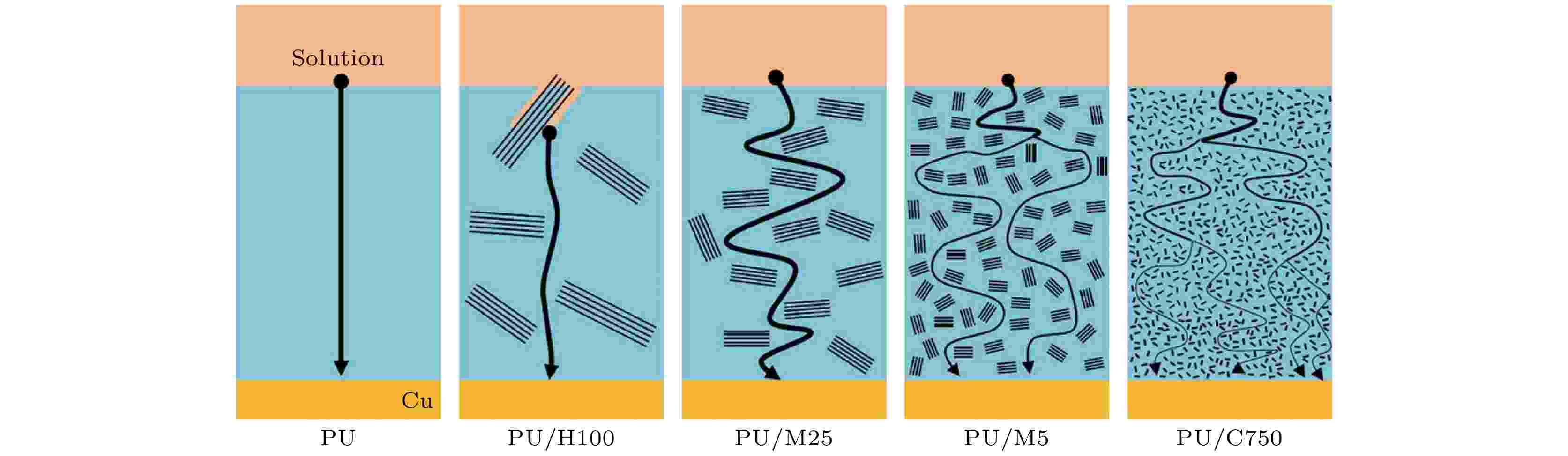
Figure13. Schematic model for the permeation of the corrosive agent passing through the coating layer of the PU composite containing GnP with weight fraction of 1%[59].
2
4.5.石墨烯的含量
虽然石墨烯的添加有助于涂料防腐性能的提高, 但也要考虑石墨烯的团聚及成本问题, 因而需对石墨烯的含量进行优化. Liao等[60]在环氧树脂中加入五种不同含量的多层石墨烯作为填充涂料制备石墨烯/环氧树脂复合材料, 在质量分数为3.5% 的NaCl环境中进行电化学测试. 研究发现, 随着石墨烯含量的增加, 涂层的腐蚀电位正移, 电流密度减小. 当加入的石墨烯质量分数达5%时(研究范围内的最大含量), 涂层防腐效果最好. Cai等[61]以水性聚氨酯为基质、PANI/rGO为防腐填料制备复合材料. 涂层防腐效果的电化学测试结果表明, 随着石墨烯含量的增加, 电化学阻抗值呈现出先增大后减小的趋势, 表明过多地添加石墨烯会导致复合涂层的屏蔽性能下降, 即涂层的防腐效果并不会随石墨烯含量的增加而不断提高.石墨烯粉体作为添加剂用来优化现有涂料使用时, 一方面, 需要对现有涂料在性能上有所提升, 另一方面, 要考虑成本问题. 目前这一应用需要解决的主要是石墨烯在涂料中的团聚问题. 同时, 石墨烯粉体的规模化制备技术仍有待提高, 既要保证产品的可控性和重复性, 也需要继续降低成本, 以提高其竞争力.
EPD法制备的环保友好型EPD-GO涂层与CVD法相比都是使用纯石墨烯材料. 然而, EPD方法生长石墨烯同样对金属基底的选择和耐高温性具有一定的要求, 难以实现大批量生产.
石墨烯材料作为缓蚀剂在使用时可直接添加至腐蚀溶液中进行防腐, 操作简单, 抑制效果突出, 使用时安全又稳定[62-64]. 由于缓蚀剂在金属表面大多具有较强的吸附作用, 常常会导致阴、阳极的反应减弱, 降低腐蚀效率. 然而, 将石墨烯以添加剂的形式进行防腐, 即使添加含量非常低, 体积也有可能大于原始材料. 该方法同样要考虑石墨烯的分散及石墨烯材料本身的制备成本问题.
目前被广泛研究讨论的改性石墨烯涂料大多是利用石墨烯的被动防腐作用—物理屏障来实现对金属表面的防腐, 并未对如何加强石墨烯的主动防腐能力进行深入探索. 石墨烯自修复涂层的出现完美地实现了金属在复杂工况下的服役安全[21,65], 但是想要寻找一种既对金属表面具有一定的缓蚀效果, 又不会与石墨烯材料发生反应的绿色无污染缓蚀剂仍是一个不小的挑战.
我国在石墨烯领域, 不论是基础研究还是产业化的推进, 都有较大的投入, 在石墨烯的规模化制备及部分应用领域处于国际领先地位. 在石墨烯防腐应用领域, 中国科学院宁波材料技术与工程研究所薛群基院士和王立平研究员带领的海洋功能材料团队开发的部分产品已经进行了产业化应用, 如东营港、上海港等港口金属防腐, 国家电网沿海地区和工业大气污染地区大型输电铁塔防腐等[68]; 常州第六元素材料科技股份有限公司、中海油常州涂料化工研究院有限公司、江苏道森新材料有限公司三家单位共同开发的用于海上风力发电塔的石墨烯-锌防腐底漆重防腐涂料和传统的富锌环氧底漆相比非常具有竞争力, 已经在海上风电装置、海边管廊架、集装箱等领域推广应用[69]. 这些均展示了石墨烯在防腐领域广阔的应用前景, 极大地推动了石墨烯材料的产业化进程.