全文HTML
--> --> -->在利用化学气相沉积方法(chemical vapor deposition, CVD)制备二维材料之前, 机械剥离和液相剥离是人们获得单层或少层二维材料的常用方法. 机械剥离可以得到较高结晶质量的二维材料, 但是产量低, 层数难以控制且产物面积小, 不适用于大面积应用. 液相剥离可以低成本制备较大量级的二维材料, 但是产品的质量和尺寸难以控制[20]. 要想将材料的尺寸从小片提升到晶圆大小, 需要开发能够制备出大面积单层或者多层材料的技术. CVD提供了一种可控和可扩展的方法, 能够以合理的成本生产高质量、大面积的二维材料. CVD是气态物质在衬底表面发生反应形成固体产物沉积的过程. 通过控制生长参数, 如温度、压强、载流气体流量、源材料的相对数量和源-衬底距离等, 可以控制产物的层数、尺寸、形态和方向, 也可以实现掺杂或缺陷的引入(如图1所示)[21]. 用于制备二维材料的CVD工艺是通过改进用于制备硅、钨、金刚石等传统材料的CVD技术而来, 人们已经可以通过改进的CVD方法实现部分二维材料的大面积、高质量制备. 然而, 实现更多二维材料的大尺寸乃至晶圆级的生长仍然是困难的. 此外, 深入了解CVD生长机理进而指导高质量二维材料薄膜的大面积生长, 可以推动二维材料的研究进程, 加快二维材料从理论走向应用的脚步.
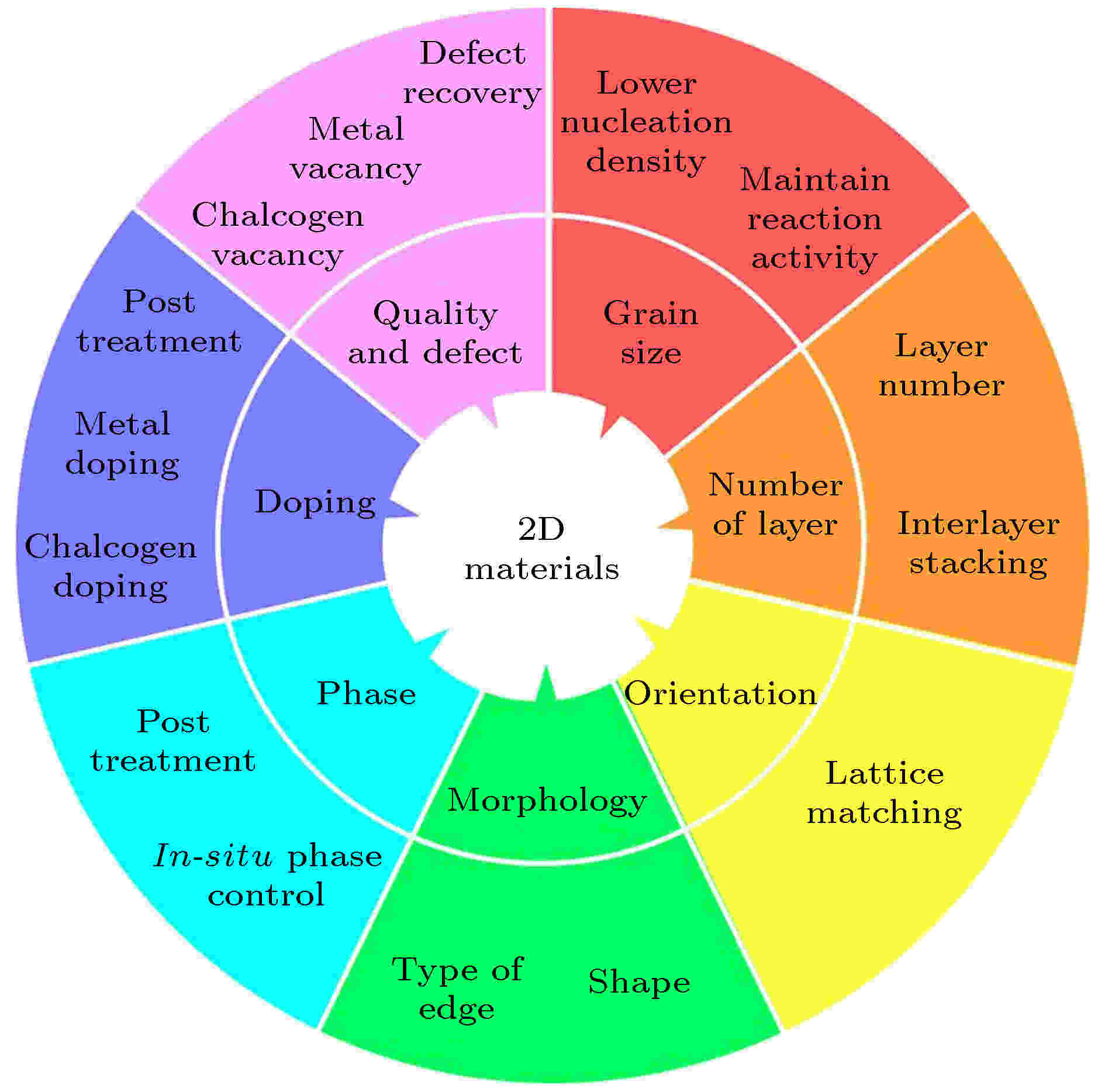
Figure1. The affecting parameters and factors during CVD growth of two-dimensional materials[21].
获得大尺寸、高质量的二维薄膜对推进二维材料从实验室走向实际应用具有重要意义, 目前人们已经成功合成了石墨烯、六方氮化硼(h-BN)亚米级薄膜以及多种二维过渡金属硫族化合物(TMDs)厘米级薄膜, 比如二维WSe2, MoS2, WS2等. 在多种合成方法中, CVD方法作为一种前沿技术, 在提升材料尺寸、减少材料晶界密度、控制材料形貌等方面取得了很好的进展. 然而, 合成过程的复杂性以及制备成本高仍然是制约二维材料走出实验室的限制因素. 因此, 需要基于现有成果对CVD制备大面积二维薄膜的生长机理进行系统的梳理, 以期达到更深入的理解, 为进一步优化二维材料制备、推动工业化进程提供理论依据. 为此, 我们总结了近年来利用CVD技术制备大面积二维材料薄膜的研究进展, 分析了CVD反应过程中物质运输、成核密度以及生长速率等因素对二维材料生长尺寸的影响, 讨论了优化制备大面积二维材料的策略, 指出了目前存在的发展瓶颈以及可能的解决方案.
2.1.金属有机化学气相沉积法
在金属有机化学气相沉积法(metalorganic chemical vapour deposition, MOCVD)的过程中, 前驱体为高纯的有机化合物气体, 以保证薄膜的均匀性, 同时, 足够大的反应装置可以满足样品的大面积生长. 目前, 基于MOCVD方法已经实现多种二维材料的晶圆级制备. Kang等[22]已使用MOCVD方法在SiO2/Si衬底上制备出尺寸为10 cm的MoS2, 然而, 较低的反应物通量导致产物的生长速率缓慢, 整个反应过程需要消耗26 h. 为了减少反应过程中的能量消耗, Kalanya等[23]设计了一种新型的生长系统-脉冲MOCVD, 在该系统中, 固态有机前驱体升华后进入反应腔后被离散化, 并通过系统对每一部分前驱体的脉冲进行校正, 以实现对反应中各变量的精准调控, 该系统在90 s内即可合成了尺寸为5 cm的MoS2薄膜, 大大缩减了生长时间, 降低了功耗. 由于固态前驱体的升华速率难以控制, 重复性不高, Choi等[24]使用液态有机化合物代替固态, 这保证了反应物质的均匀输送, 反应中MoS2的覆盖面积随着生长时间线性增加, 最终在15 min左右合成了尺寸为2 cm的MoS2薄膜, 虽然产物的面积和反应速率不如前两种方法, 但是液相前驱体简化了反应过程, 并增加了实验的可重复性. 从以上几种方法可以看出, MOCVD对于二维材料的晶圆级制备有着很大的潜力, 然而, 由于有机前驱体的元素复杂性, 反应过程中产生的碳元素往往会污染样品表面, 导致产物质量不高, 后来科研人员提出了水氧化和减少前驱体的含量等方法来控制污染, 目前仍需继续完善和开发MOCVD技术, 以期同时提高产物的质量和尺寸.2
2.2.传统的热CVD方法
尽管MOCVD可以快速制备大面积二维材料, 但是反应物质多为毒性较强的气体, 且较低的压强和易燃的气体使生长装置始终处于一个不稳定的状态[25]. 传统的热CVD方法和MOCVD具有相同的生长原理, 但是前驱体通常是无机的, 因此产物不会被碳污染, 且反应不需要在严格的低压条件下进行, 使得反应装置更为简单. 传统的CVD方法主要通过调节CVD参数来控制产物的尺寸、层数和质量, 相比于MOCVD, 产物通常具有更低的晶界密度. Ma等[26]以蓝宝石为衬底成功制备出尺寸为1 cm的MoS2薄膜, 产物在室温下的电子迁移率为192 cm2·V–1·s–1 . 该工作通过抑制反应过程中的硫(S)元素的通量来达到抑制成核的目的, 融合成薄膜的单个晶粒尺寸可达几百微米. 相比于传统衬底SiO2/Si, 蓝宝石的造价相对昂贵, 不适合作为晶体管的衬底. 由于SiO2/Si为非晶体, 产物分子或原子难以在衬底上规则有序的排列, 这会增加产物的晶界密度, 影响产物的质量. 尽管如此, Tao等[27]仍在SiO2/Si衬底上成功合成了尺寸1 cm左右的MoS2薄膜, 而且通过限制反应中钼(Mo)元素的供给以降低成核密度, 最终获得超过100 μm的单个MoS2晶粒, 尺寸较大的晶粒有助于其在电学和光学领域的应用, 并且可以确保材料的均匀性. 由于反应物的供给速率较低, 晶体的生长需要近20 min, 与MOCVD相当. 因此, 二维材料的制备需要平衡好成核密度和生长速率的关系, Qian等[28]在较低的Mo源区温度, 较慢流速和较高的衬底温度的条件下, 制备出尺寸接近3 cm的MoS2薄膜. 同样的方法也可用于其他二维材料, Gong等[29]使用MoO3和硒(Se)作为前驱体, 通过调节反应中的温度、流速和H2的浓度, 实现了MoSe2的晶圆级制备. 目前, 使用热CVD方法已经可以成功实现多种二维材料的晶圆级制备, 比如石墨烯、六方氮化硼、部分TMDs等, 制备尺寸逐渐向MOCVD贴近, 目前仍在不断优化CVD的制备工艺, 以期实现更多种类材料的大面积制备.2
2.3.等离子体辅助增强化学气相沉积
等离子体辅助增强化学气相沉积(plasma-enhanced chemical vapor deposition, PECVD)是以CVD为基础优化发展的一种二维材料的沉积方法, 因其低温环境对基底友好以及无转移生长的优势, 吸引了越来越多研究者的关注[30]. 等离子体中含有大量的高能量电子, 这些电子可以提供化学气相沉积过程中所需要的激活能, 从而改变了反应体系的能量供给方式. 高能电子与气相分子的碰撞可以促进反应气体分子的化学键断裂和重新组合, 生成活性更高的自由基, 而整个反应体系却始终处于较低的温度. 这一特点使得原来需要在高温下进行的CVD过程得以在低温下进行, 满足在多种介电基底表面原位生长石墨烯的应用需求. Zhang等[31]采用远程PECVD技术, 550 ℃的低温下, 在多种衬底(SiO2/Si, Al2O3, 蓝宝石, 石英和云母等)表面直接合成约10 cm的超薄石墨烯薄膜. 调节PECVD中的生长参数也会影响实验结果, Wei等[32]发现石墨烯的边缘生长依赖于H2的浓度、生长温度和系统的压强. 较低的温度和较高的H2含量有助于诱导石墨烯的边缘蚀刻, 而相反的条件有助于石墨烯的成核, 而边缘生长仅发生在成核和边缘蚀刻竞争的温度之间, 通过调整生长参数有助于制备大面积石墨烯薄膜. 此外, PECVD也应用于TMD材料的制备, Kim等[33]以Mo膜和H2S为前驱体, 在150—200 ℃的低温条件下合成了晶圆级MoS2薄膜. 基于传统的PECVD技术, 人们开发出了的电感耦合化学气相沉积法(inductively coupled plasma-CVD, ICP-CVD), 电感耦合等离子体(ICP)是一种极具潜力的低温高密度等离子体源, 在大规模集成电路的刻蚀和大面积均匀薄膜的沉积中具有广泛的发展前景. 值得注意的是, ICP-CVD可以用于设计新型结构的TMDs材料, Lu等[34]使用ICP-CVD在单层的MoS2中提取出顶层S原子, 形成了中间产物MoSH, 之后在加热过程中被硒化, 最终成功制备了具有Janus结构的新型材料——MoSSe. PECVD也是一种极具潜力的可控制备大面积二维材料的有效方法, 在未来的研究中, 需突破对成核及生长速率的控制, 扩大晶粒尺寸, 提升电学性能, 并开发更为先进的PECVD系统, 以期实现具有新型结构的二维晶体的合成以及更大面积的二维薄膜的制备.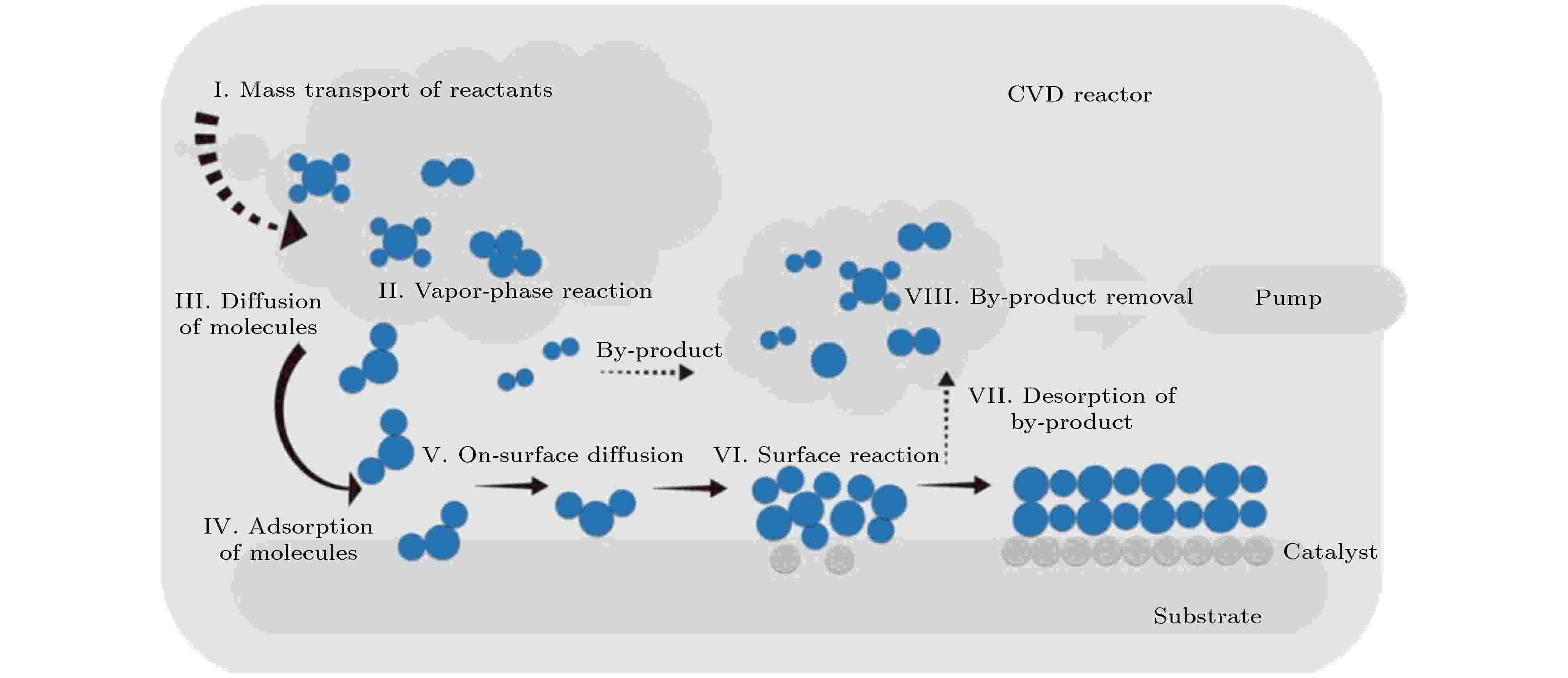
Figure2. Schematic illustration of the reaction processes in a typical CVD reactor[35].
2
3.1.物质运输调控
在CVD过程中, 物质运输主要通过反应室内的载流气体来实现, 即利用稀有气体将气相前驱体运送至衬底表面发生反应. 改变生长条件(温度、压强和载气等)、设计生长系统以及选择合适的前驱体和载气是改善物质运输的有效手段, 调控物质运输过程会在一定程度上影响二维材料的生长环境, 这些改变会在微观尺度上影响产物的生长.3
3.1.1.前驱体的影响
选择合适的前驱体有助于调控二维材料的质量, 以石墨烯的生长为例, 碳源可以选择固态、气态和液态. You等[36]使用固态聚苯乙烯为碳源, 固态的碳源在外部加热的条件下变成气相, 最终成功制备出高质量的石墨烯薄膜. Rao等[37]使用液态的乙醇作为碳源, 乙醇在高温下裂解产生的氧化物对无定形碳具有刻蚀作用, 这有助于清洁衬底表面、提高产物质量. 然而, 以固态或液态碳源作为前驱体, 其在反应室内的浓度难以精确控制. 热分解反应过程中轻微的温度变化会引起反应室中前驱体的浓度呈现梯度分布, 导致获得的产物均匀性较差, 质量不高. 因此, 目前通常选择气态碳源作为石墨烯CVD生长的前驱体, 通过控制反应装置的流量以及前驱体的分压可以调控反应物的输运速率, 精准控制流量可以影响产物的形态、取向和尺寸. 常见的气态碳源有甲烷、乙烷和乙烯等, 乙烷和乙烯由于连接碳原子的化学键是双键结构, 导致反应过程中键的裂解和重新排布比较困难[38], 而甲烷具有较低的脱氢能, 且相对于其他烃类材料更纯净, 因此通常选择甲烷作为制备石墨烯的碳源.在制备二维TMD薄膜的过程中, 固体源常作为反应的前驱体. 由于固体材料的蒸汽气压对温度非常敏感, 因此需要对源区进行精准的温度控制. 反应物在高温下容易发生副反应, 气态副产物会随着载气运输至衬底表面, 导致产物纯度不高, 为了避免这种现象, 实验室通常选择化学元素单一的原料作为前驱体. 比如, 过渡金属氧化物(如MoO3, WO3)、氯化物(MoCl5)或金属箔通常作为金属(钼或钨)源, 而S或Se粉末常作为硫或硒源. 此外, 制备高质量的二维材料需要对前驱体的蒸汽浓度进行精确控制, 这对于保证稳定的生长动力学条件至关重要. 近期, Shi等[39]在CVD反应期间使用氧化物抑制剂辅助生长(oxide inhibitor-assisted growth, OIAG)策略成功制备了MoX2(X = S, Se和Te)的单层薄膜. 在OIAG策略中, 作为Mo源的MoO3被一层氧化物抑制剂(OI)粉末覆盖, 充当“阀门”来操控Mo蒸汽的释放(图3(a)). 在制备MoS2过程中, 选择SnO2作为OI, OIAG策略中OI的工作机制如图3(b)所示, 从图3(b)中可以看出, 产物的沉积区域随着OI剂量的增加而减少, 且较厚的OI层增加了Mo蒸汽的扩散路径, 进而越来越多的Mo源被捕获在OI层内. 因此, 通过对OI剂量的控制, 可以进一步控制反应过程中Mo蒸汽的浓度. 基于此, 该工作探究了Mo∶S比例对MoS2薄膜连续生长的影响, 其中Mo∶S比例的调控是通过调节OI的剂量来实现的, 该比例随着OI剂量的增加而减少, 实验结果如图3(c)—(f)所示, 当剂量为4 mg时, 衬底上产生了平均尺寸约为100 μm的MoS2薄片(图3(c)); 当剂量增加到5 mg时, 衬底上出现了均匀的MoS2单层薄膜(图3(d)); 当剂量进一步增加时至6 mg时, 在预先生长的单层薄膜上形成了一些黄色区域(多层MoS2)(图3(e)); 当剂量为7 mg时, MoS2的面内生长受阻(图3(f)). 以上结果表明, 适当的Mo:S比例有助于促进单层MoS2的横向生长, 进而形成连续薄膜. 当Mo:S比例远小于预期值时, MoS2的面外生长会增强, 这会导致多层MoS2的随机生长. 因此, 对前驱体的浓度进行精准控制可以有效地调控二维薄膜生长过程的动力学行为, 促进二维材料的连续成膜生长. 此外, 由于MOCVD系统中的前驱体是高纯的气态有机化合物, 生长过程更容易调控. 目前, 人们已经通过MOCVD方法合成多种晶圆级薄膜. Kang等[22]将气相的Mo(CO)6, W(CO)6和(C2H5)2S作为前驱体, 成功制备了尺寸为4英寸的MoS2和WS2薄膜, 且样品表面均匀, 具有较高的迁移率(温度为90 K时迁移率为114 cm2·V–1·s–1). 该工作发现, 产物的晶粒尺寸与H2, H2O和(C2H5)2S的浓度有关, 这是由于H2和H2O会促进(C2H5)2S的分解, 导致反应腔内S蒸汽的浓度增加, S元素的含量会影响晶体的成核动力学和晶粒尺寸. MOCVD通过精准控制反应物的浓度和流量, 促使反应腔中的物质运输状态始终保持稳定, 这对于制备高质量、大面积的TMD薄膜来说具有重要意义.
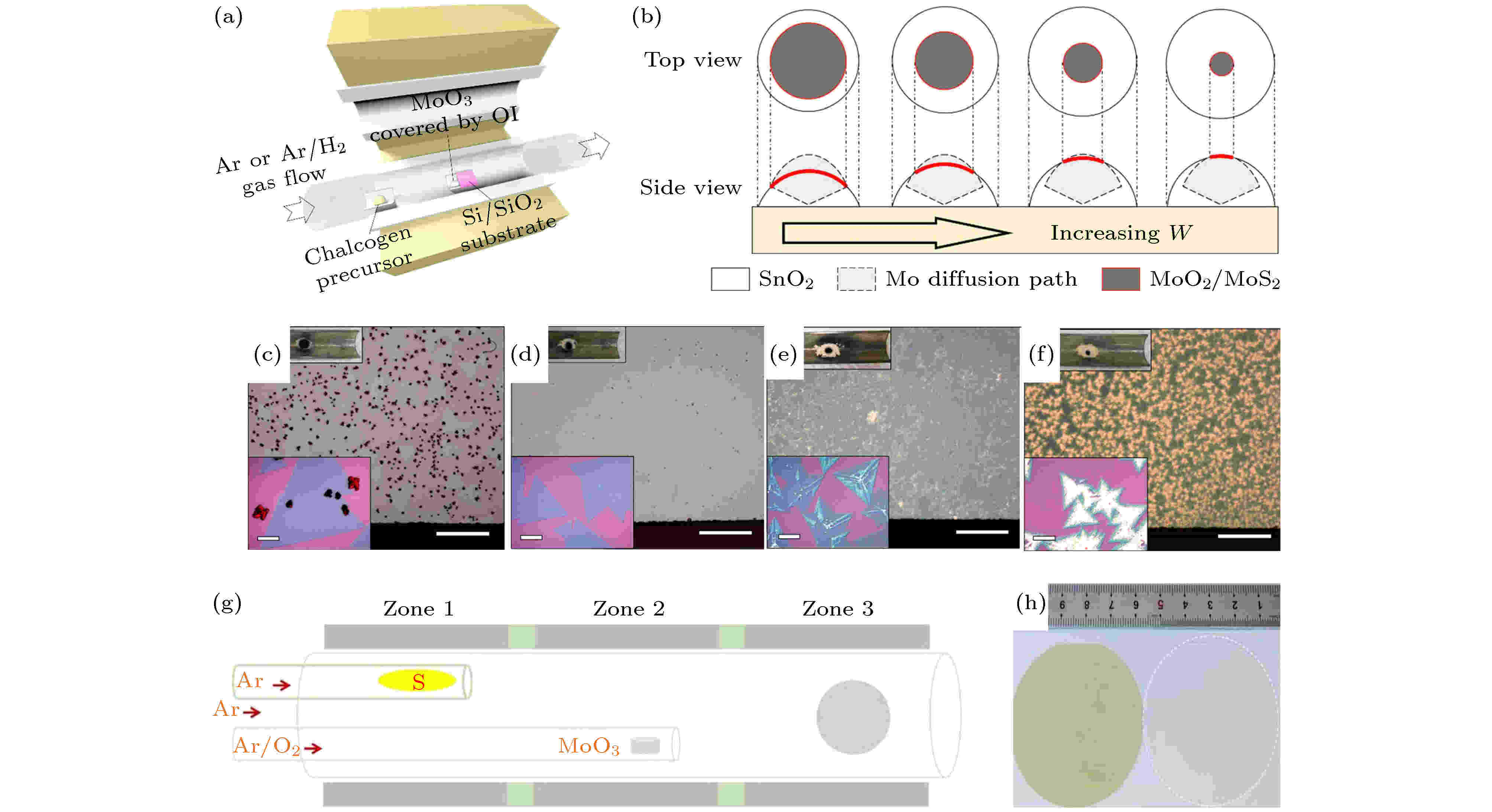
Figure3. Schematic illustration of (a) the growth of MoX2 by OIAG and (b) the working mechanism of OI in the progress of OIAG; (c)?(f) optical images of MoS2 with different concentrations: (c) 4 mg, (d) 5 mg, (e) 6 mg, (f) 7 mg[39]; (g) schematic illustration of the modified CVD system for MoS2 growth; (h) photograph of MoS2 film grown on sapphire substrates[40].
3
3.1.2.载流气体的影响
反应物质的运输过程主要是通过载气完成的, 对于石墨烯来说, 通常选择H2来作为反应中的载流气体, H2不仅可以作为载气, 还可以作为还原剂, 防止衬底上的石墨烯在降温过程中被氧化. 以在铜(Cu)衬底上制备石墨烯为例, 反应中H2不仅作为碳源的稀释气体, 还可以用于清洁Cu表面的氧化物, 同时提供氢(H)原子腐蚀无定形碳, 提高石墨烯质量. 当H2分压较低的时候, 石墨烯的边界不能被H钝化, 氢原子更容易吸附在Cu表面, 导致活性炭不容易进入顶层碳原子以下, 因此容易得到大面积单层的石墨烯. 当H2分压较高时, 石墨烯的边界会被氢终止, 碳原子会进入顶层石墨烯以下形成吸附层, 导致产物通常为双层或者少层的相对面积较小的石墨烯. 在制备二维TMDs过程中, 载流气体通常选择惰性气体-氩气(Ar), Ar将气相前驱体运送到衬底表面, 并且不参与反应. 为了实现对载气的精准控制, Zhang等[40]设计了一种独特的进气系统(图3(g)), 相比于传统的单气路的生长系统(图2), 该工作将前驱体S和MoO3分别放置于两个石英管内, 这种进气系统可以通过注入载气对两条路径独立调控, 使S蒸汽和MoO3蒸汽只在衬底上发生反应, 减少副反应的发生, 最后成功制备了晶片级别的MoS2薄膜(图3(h)).3
3.1.3.温度和压强的影响
在CVD反应中, 温度是一项重要的工艺参数, 合适的温度会使反应气体活化, 衬底的催化能力增强. 以石墨烯的生长为例, 在镍(Ni)衬底上制备石墨烯时, 主要以融入Ni中的碳作为碳源, 碳在Ni中的溶解度主要依赖于生长温度. Regmid等[41]分析了不同温度对石墨烯生长的影响, 当温度低于850 ℃的时候, 没有石墨烯形成, 温度高于850 ℃的时候, 石墨烯逐渐形成, 可以看出温度的升高有利于碳原子在衬底表面的移动, 使得衬底表面的石墨烯形成较好的排布. 对于合成二维TMDs来说, 一个微小的温度变化就会使气化固相前驱体的饱和压力发生巨大变化. 因此, 对反应室内温度进行精确调控, 可以改善CVD反应中的物质运输过程. Li等[42]设计出一种低温合成二维WTe2的方法(图4), 使用具有三个温区的管式炉, 对每个区域设置不同的温度曲线, 成功制备了厘米级的WTe2薄膜.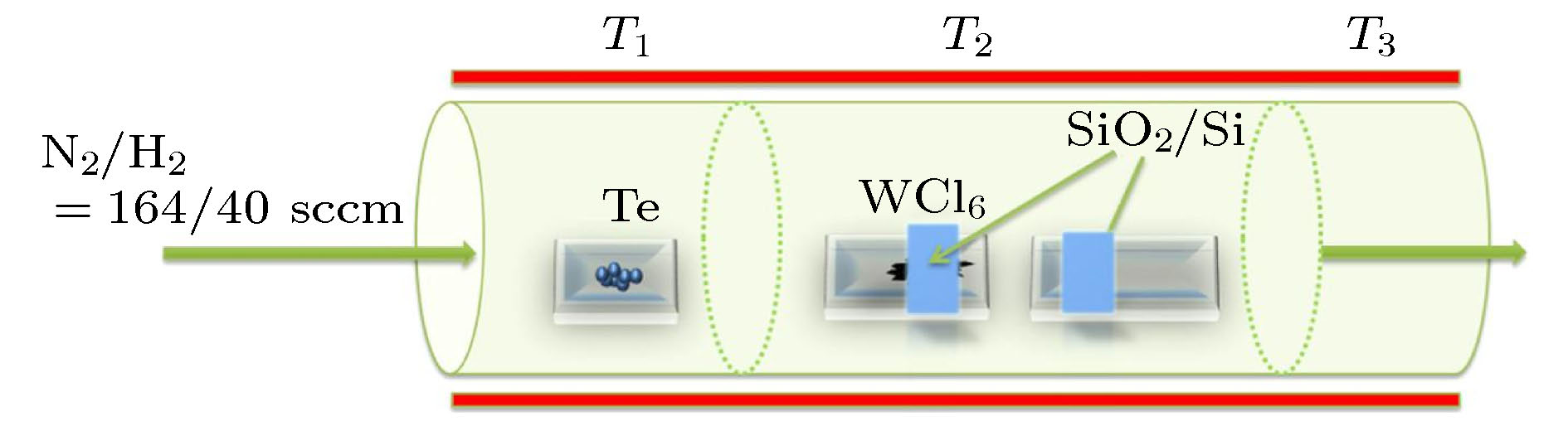
Figure4. Schematic illustration of the growth of WTe2 film with centimeter-scale by three-zone chemical vapor depo-sition[42].
当前驱体在源区受热分解时, 气体原子或者分子的平均自由程会受到压强的严重影响. CVD腔内的压强变化范围很广, 从几个大气压到几个mTorr (1 Torr =1.33 × 102 Pa)甚至更低, 压强的改变对气体流动特性有很大的影响. 根据理想气体方程, 在低压条件下, 摩尔流量不变, 前驱体浓度越小, 体积流量越大, 气体流速也随着增大. 较低的前驱体浓度和较高的输运速率可以使反应更加可控, 因此, 在合成晶圆级连续的薄膜时通常会选择在低压的条件下进行[43,44]. Ge等[45]研究了不同压强对石墨烯生长行为的影响, 发现在生长压强较低时, 石墨烯的质量较高且形貌较为规整, 随着生长压强逐渐增大, 形貌的不可控性也逐渐增大, 容易形成不规则的石墨烯, 这是由于随着压强的增大, 碳源裂解的平均自由程逐渐降低, 使得碳原子在不断碰撞中消耗了大量的能量, 以至于到达衬底表面时能量较低, 这将导致碳原子的重新排列运动能力下降, 容易出现大块碳聚集的现象.
2
3.2.成核控制
成核是通过自组装生成热力学稳定或具有更低自由能新相的前提, 成核过程决定了新相形成和自组装结构出现的时间, 而成核密度决定了薄膜的几何形状和晶粒尺寸[46-48]. 然而量化成核过程却极其困难, 该过程发生在分子水平, 临界晶核大小及形成时间很难通过实验准确确定. 为了理解晶体的成核机理, 人们提出了晶体的成核理论(crystal nucleation theory, CNT)[49-52], 该理论最初用于理解气态向液态转化的过程, 随后逐渐用于解释新的液体和固体热力学相的形成. 在CVD过程中, 晶核的形成处于基础性地位, 并且二维材料的生长机制遵从晶体生长的成核和连续生长模型. 对生长过程中的成核过程进行深入研究, 有助于为制备高质量和大面积二维材料提供理论基础, 使二维薄膜的可控生长成为可能.3
3.2.1.衬底对成核的影响
成核位点一般集中在衬底的高表面能区域, 因此对衬底进行处理可以有效地影响反应的成核过程. 以在Cu表面生长h-BN为例, Cu表面的晶界处、杂质或表面的褶皱处的成核分布相对平坦处更为密集. 对衬底进行抛光处理是一种优化衬底表面的常见方法. 如图5(a)和图5(b)所示, 抛光后的铜箔杂质减少、粗糙度降低、表面更加平整, 有助于生长均匀连续的二维薄膜[53]. 衬底表面越平整, 表面的高能区就越少, 分子或原子在表面吸附位点也随之减少, 使微观晶体粒子具有有更长的扩散距离并沿着衬底表面的活性位点自由移动. 除了抛光处理, 对衬底的处理方式还包括高温退火、折叠处理等, 不同处理方式的主要目的都是为了钝化(减少)衬底上的活性位点, 以避免在生长过程产生缺陷和杂质.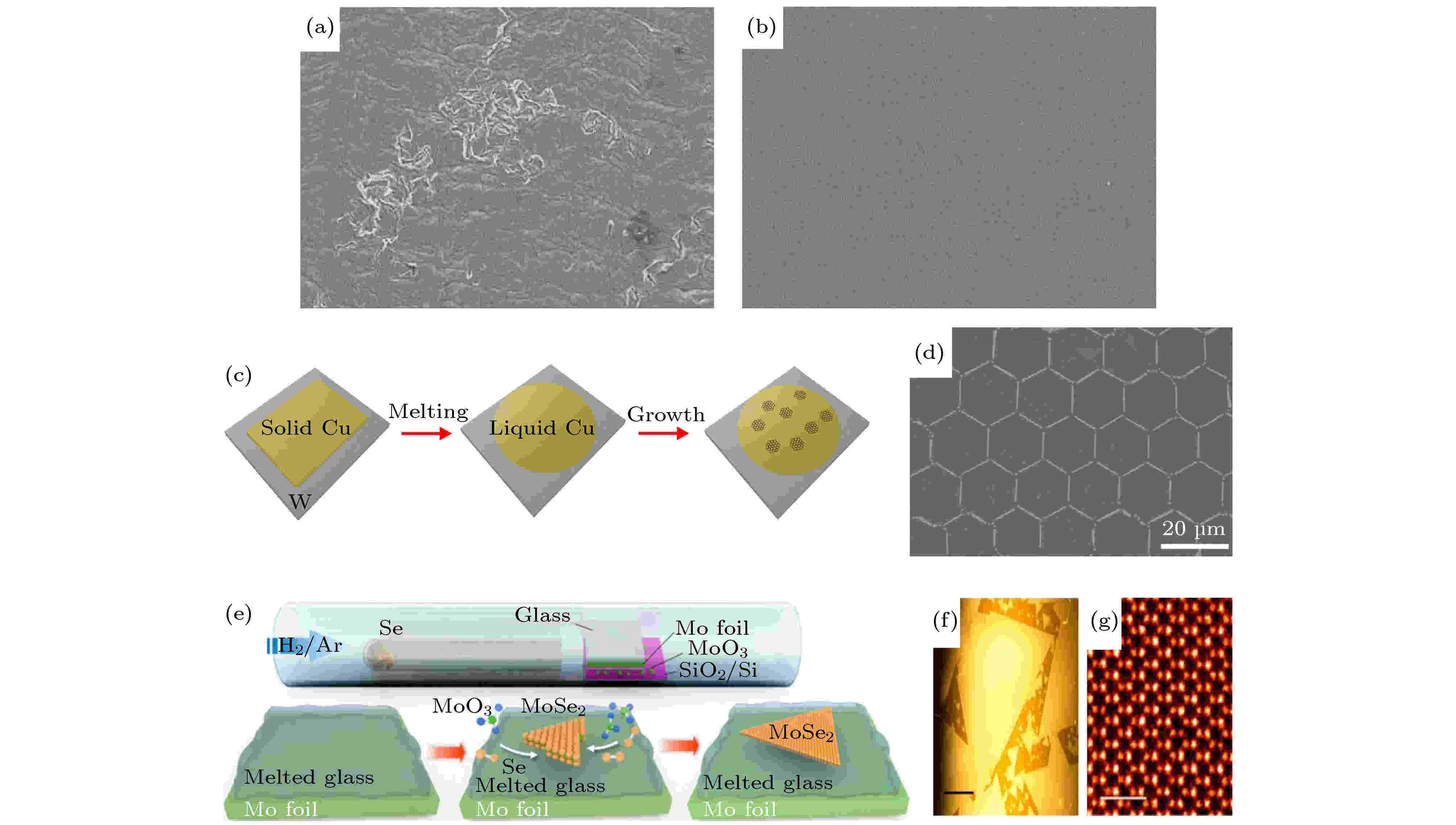
Figure5. SEM images of Cu foil (a) before- and (b) after-polishing[53]; (c) schematic illustration of the synthesis of graphene on the liquid Cu surface; (d) SEM image of “self-assembling sample behavior” of hexagonal graphene domains on liquid Cu surface[54]; (e) schematic demonstration of the growth of the WTe2 film by CVD; (f) optical image of MoSe2 film; (g) STM image of MoSe2 film[55].
液态金属具有较为光滑的表面, 可以有效降低衬底表面的活性位点, 因此, 液态金属常作为二维材料的生长衬底. Geng等[54]使用液态Cu作为衬底(图5(c)), 成功合成了连续的石墨烯薄膜. 实验中采用钨或钼支撑板, 以避免熔化的Cu(直接放置或预先电镀)在较强表面张力下的起球行为. 研究发现, 石墨烯在液态Cu上的成核密度明显小于固体Cu衬底上的成核密度, 且产物为具有小旋转角的六方畴并呈现出“自组装”的形式(图5(d)). 此外, 碳源在液态衬底上更容易扩散, 这有助于石墨烯的连续成膜生长. 液态非金属也可以作为生长衬底, Loh等[55]以熔融玻璃为衬底, 成功制备了毫米级的MoSe2单晶(图5(e)). 随着温度的升高, 固体玻璃熔化并产生干净的原子级平坦液体表面, 该表面几乎没有任何缺陷且活性位点较少, 可以促进大尺寸的MoSe2晶体的形成(图5(f)). 通过对不同区域的晶体结构和晶格取向进行表征, 证实了产物具有单晶性(图5(g)).
3
3.2.2.化学势的影响
由晶体的生长理论可知, 吉布斯自由能是影响成核过程中反应方向的有效参量, 反应中的吉布斯自由能与化学势有关[56], 因此调整CVD中的化学势可以进一步影响二维材料的成核行为, 以石墨烯为例, 单位面积的临界成核率为[57]


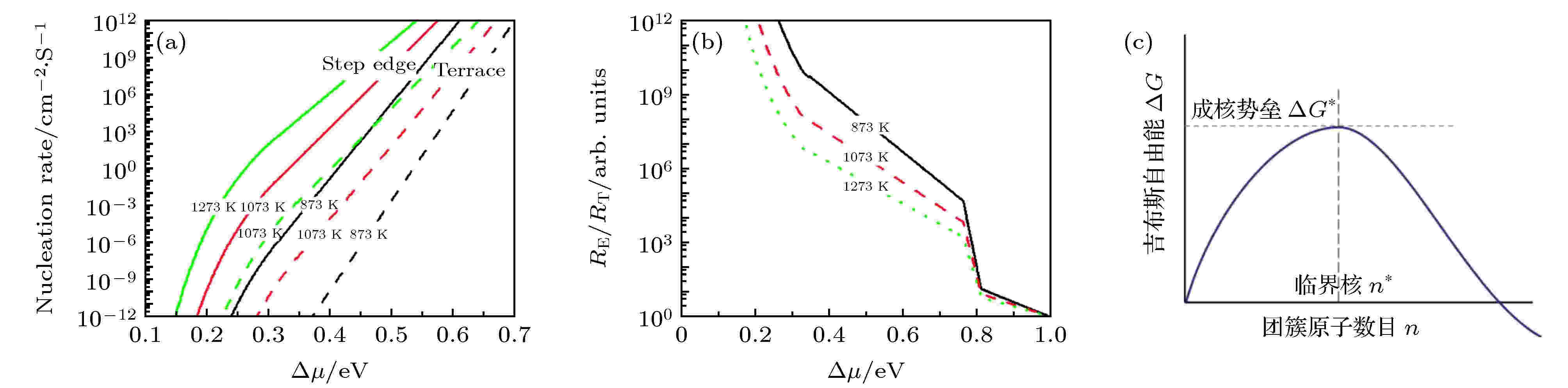




Figure6. (a) Nucleation rates of graphene growth on a Ni(111) terrace and near a step edge as a function of




3
3.2.3.载气和生长时间的影响
上文中, 我们介绍了载气对物质输运过程的影响, 载气不仅会影响CVD中的物质输运过程, 而且会对产物的成核过程产生影响. 以Cu箔上生长石墨烯为例[58], 在石墨烯生长阶段, 一般只通入CH4和H2, H2起到载气和还原剂的作用, 以防止衬底上的碳原子在退火过程中被氧化(图7(a)). Cheng等[59]在生长阶段通入了Ar, Ar的主要作用是在生长过程中对石墨烯成核位点进行钝化撞击, 被Ar钝化撞击的成核点处碳原子的结合能大大提高, 从而降低了石墨烯的成核密度. 此外, 使用Ar退火时, 退火时间越长, 成核密度越低(图7(b),(c)). 载气的浓度也会影响反应的成核过程, 在CVD腔内分别通入不同比例的CH4和H2, 所获得样品如图7(d)—(g)所示, 可以看出, H2的比例越大, 石墨烯的尺寸越小, 说明H2对石墨烯具有一定的刻蚀作用, 以此可以引入Ar, 其不仅能降低成核密度, 还能抑制H2对石墨烯的刻蚀作用.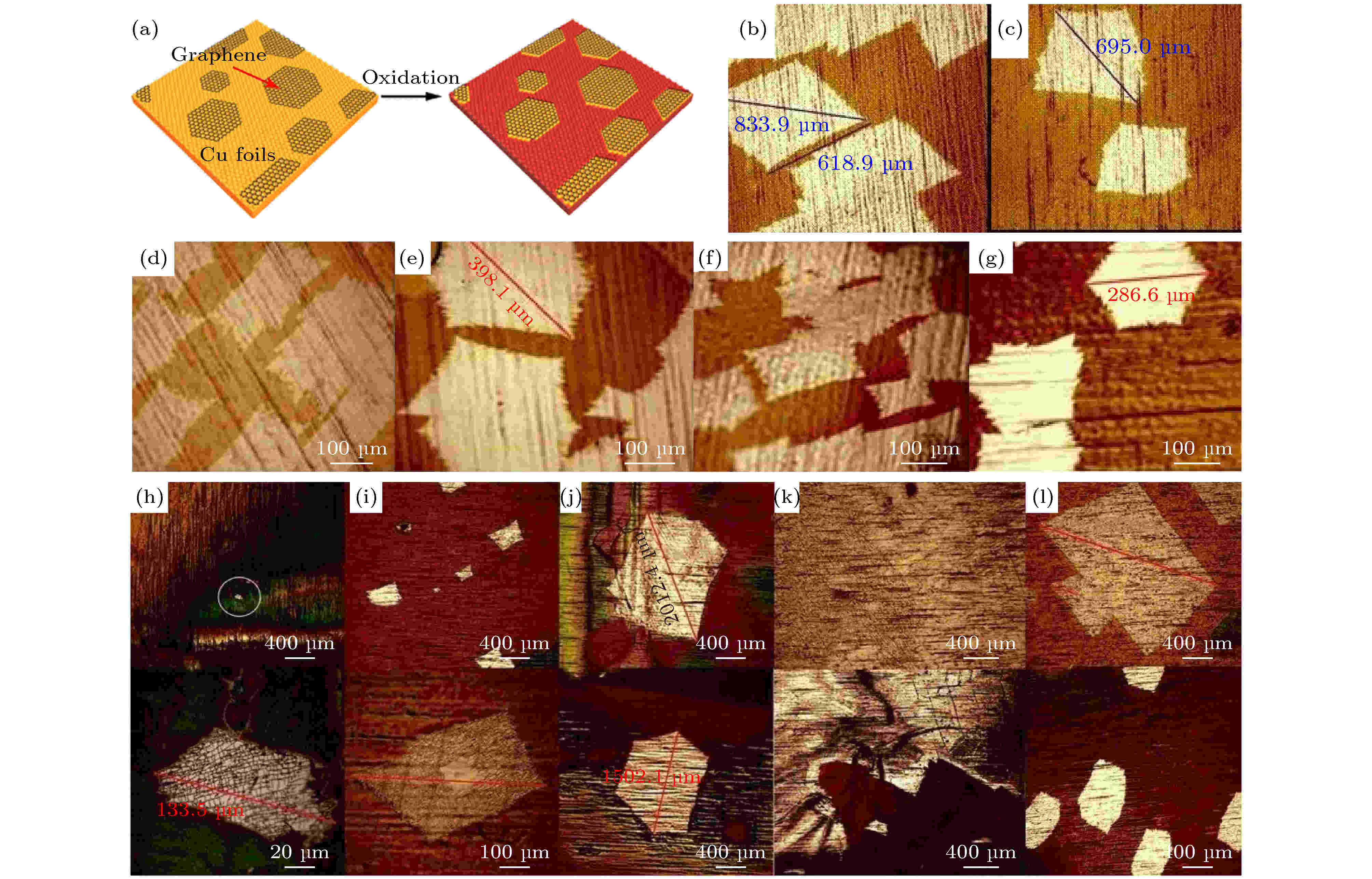
Figure7. (a) Comparison diagram of Cu foil with/without oxidation[58]; optical images of graphene for different annealing time: (b) 50 min; (c) 90 min; optical images of graphene for different proportion of CH4 and H2: (d) 2 sccm:60 sccm; (e) 1 sccm:80 sccm; (f) 1 sccm∶100 sccm; (g) 0.5 sccm∶80.0 sccm; optical images of graphene for different growth time: (h) 100 min; (i) 200 min; (j) 420 min; (k) 500 min; (l) 660 min[59].
生长时间对二维材料的生长也至关重要, 生长时间过长会使二维材料层数过多, 导致合成的薄膜不均匀, 生长时间过短将导致薄膜的尺寸较小. 调整生长时间可以使底物反应更充分, 有助于薄膜的连续生长. 对于石墨烯来说, 生长时间越长, 外延生长的范围越大. 图7(h)—(l)为不同生长时间下的石墨烯图像, 可以看出, 只要增加生长时间, 即使石墨烯的核点密度极小, 石墨烯薄膜的尺寸也会慢慢变大. Zafar等[60]在制备WS2薄膜的过程中(图8), 发现控制S源参与反应的时间可以精准控制产物的尺寸, 在S参与反应为15 min的时候, WS2薄膜的尺寸达到最大值, 近500 μm左右. 因此, 在一定范围内调控生长时间也是制备大面积二维薄膜的一种手段.
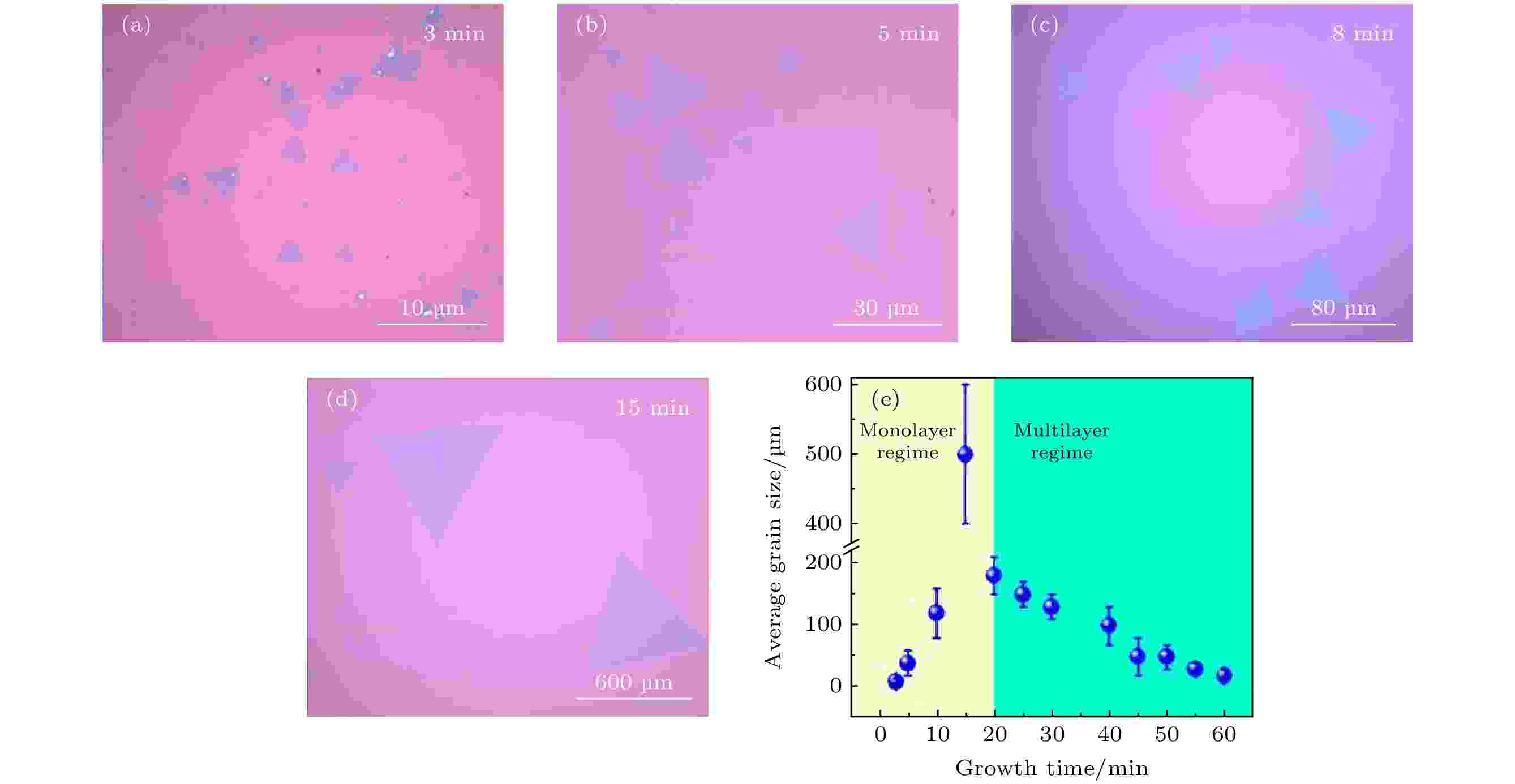
Figure8. Optical images of WS2 for different time: (a) 3 min; (b) 5 min; (c) 8 min; (d) 15 min; (e) plot of average flake size versus growth durations[60].
2
3.3.生长速率调控
在一定范围内提高二维材料的生长速率可以改善其生长效率, 并且较快的反应速率也会降低新核的形成, 有助于单晶薄膜的形成. 然而生长速率过快, 会导致产物来不及修复生长过程中的缺陷, 无法实现材料的高质量可控生长. 因此, 基于生长动力学调控二维材料的生长速率, 改变维持反应进行所需的最低活化能, 有助于进一步探索影响材料尺寸的机理和因素.3
3.3.1.衬底的催化作用
一些具有催化作用的金属或非金属材料可以作为二维材料的生长衬底, 在石墨烯和h-BN的生长中, 通常使用金属衬底作为反应的催化剂. Patera等[61]研究了Ni原子在石墨烯生长过程中的催化行为. 从图9(a)和图9(b)可以看出, 单个Ni原子会自发与两个顶端碳原子在纽结处形成了一个稳定结构. 模拟结果显示, 与没有Ni原子参与的反应相比, 该生长过程中的能量势垒降低了35%左右(从2.46到1.61 eV), 可以看出, 单个Ni原子对石墨烯边缘起到了催化作用, 促进产物的生长过程. 此外, 金属单原子也可以参与衬底表面的多种反应, 这有望为石墨烯和其他材料的催化生长带来更加深入的思考.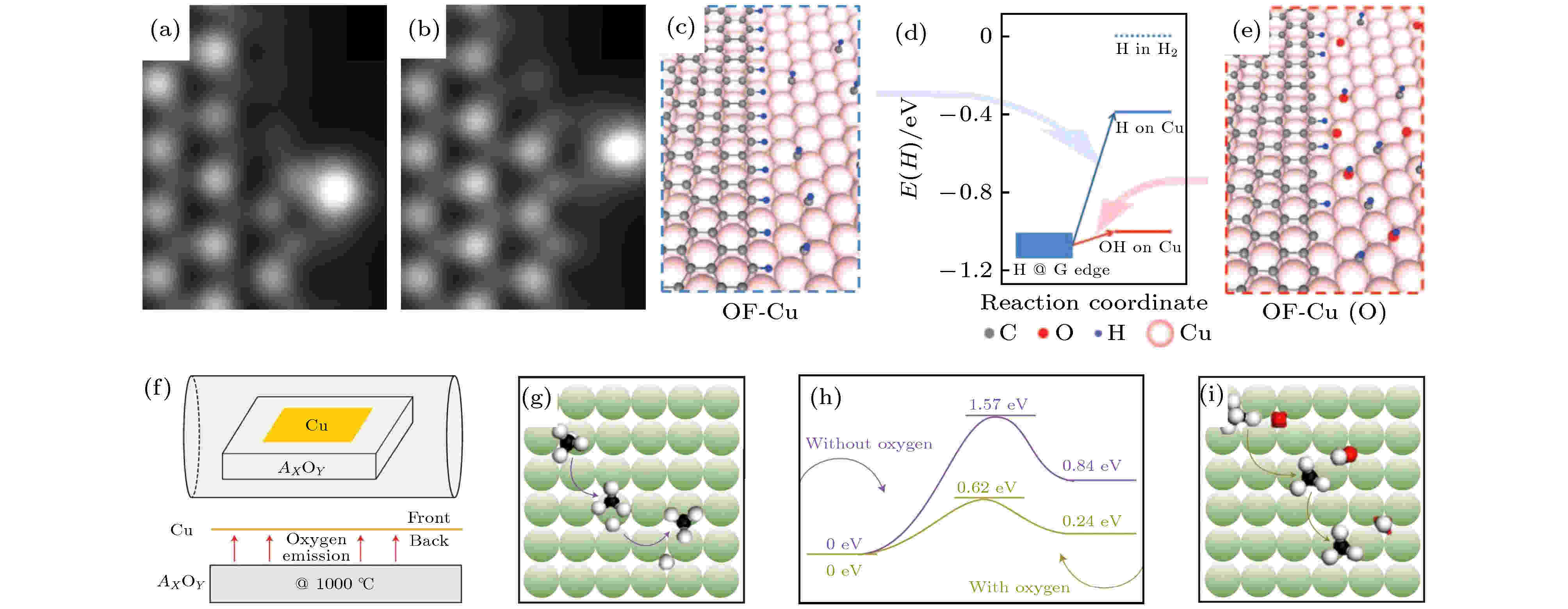
Figure9. (a), (b) STM images of the Ni adatoms at the graphene edges[61]; (c)?(e) schematic illustration of graphene edges (e) with and (c) without oxygen and (d) the corresponding DFT calculations of the energies for H attachment[62]; (f) schematic illustration of the growth of WTe2 film by local-oxygen-feeding method; (g)?(i) the energy profiles of the reaction of CH4 decomposition (i) with and (g) without oxygen supply on Cu surface and (h) the corresponding DFT calculations of the energy dispersion[63].
二维材料生长的本质就是畴边缘的附着, 对畴边缘处理可以有效地促进二维薄膜的生长. 以石墨烯的生长过程为例, 当碳团簇长成一定大小的纳米片后, 石墨烯的生长就只发生在边界, 进一步的生长行为必然依赖畴边界的原子结构. 理论计算表明, 石墨烯的氢端在Cu表面上具有能量优势, 因此需要在碳原子附着之前对边缘进行脱氢处理. Hao等[62]通过在Cu衬底表面引入氧元素以形成OH基团, 这种处理可以使每个附着在Cu表面的H原子能量降低0.6 eV(图9(c)—(e)). 此外, 根据Bell-Evans-Polanyi原理, 引入氧原子可以有效地降低边缘脱氢的活化能, 并且氧可以加快烃原料的分解, 加速碳原子在边缘的附着, 进而增大石墨烯晶畴的面积. 由于反应系统中的H2具有中和作用, 所以需要氧元素的连续供给, Xu等[63]设计了一种可以持续供氧的生长系统(图9(f)), 该系统通过打破石英板(与铜箔相距15 μm左右)中的悬挂键来释放氧元素. 释放的氧气聚集在石英板和铜箔之间的狭窄区域, 从而加强了氧原子对衬底表面的催化作用, 因此5 s内即可合成尺寸为0.3 mm的石墨烯单晶薄膜. 从CH4分解过程中的能量变化(图9(g)—(h))可以看出, 氧参与反应的能量势垒降低了0.95 eV左右. 这种局部供氧的方法同样适用于其他二维材料的生长, 比如h-BN、部分TMDs等.
3
3.3.2.辅助剂的影响
在反应中添加辅助剂可以有效地调控二维材料生长速率, 目前盐辅助法常用于二维TMD薄膜的生长, 盐(可以是碱金属卤化物, 包括NaCl, KCl, NaBr和KI)可与过渡金属氧化物(MoO3, WO3等)发生反应形成中间体, 中间体会进一步参与反应从而得到最终产物. 与原路径相比, 盐的引入降低了反应所需的最低活化能, 提高了产物的生长速率. Zhang等[64]使用盐辅助法成功制备了大面积MoS2薄膜(图10), 该方法以Mo箔和S粉为前驱体, 以钠钙玻璃为衬底并提供Na元素, 反应中Mo箔在氧气氛围中被氧化成MO3–x (x = 2, 3), 然后与S发生反应形成MoS2, 其反应温度为500 ℃, 低于Mo箔的熔点. 图10(a)展示了用这种方法合成的MoS2薄膜的光镜图像, 其薄膜尺寸可达到14 cm × 6 cm. 为了研究引入Na离子后MoS2的生长机理, 该工作研究了MoS2在钠钙玻璃和常规衬底上的生长行为(图10(b)和图10(c)), 结果发现, 引入Na元素以后, 反应势垒从0.53 eV降低至0.29 eV, 从而加快了反应速率, 实现了MoS2薄膜的快速生长. 此外, Liu等[65]通过盐辅助CVD法合成了47种TMD材料(图10(d)), 并研究了盐对WX2的生长速率的影响, 发现NaCl参与反应后会形成中间产物WOCl4, 通过计算可得, 以WOCl4作为W源反应时, 生长速率相对于传统的WO3提高了103—104倍, 合成1 cm的WX2样品仅需3 min. 因此, 选择合适的辅助剂, 可以促进反应物质的分解, 降低生长过程中的势垒, 并能创造一个适合晶体外延的反应环境.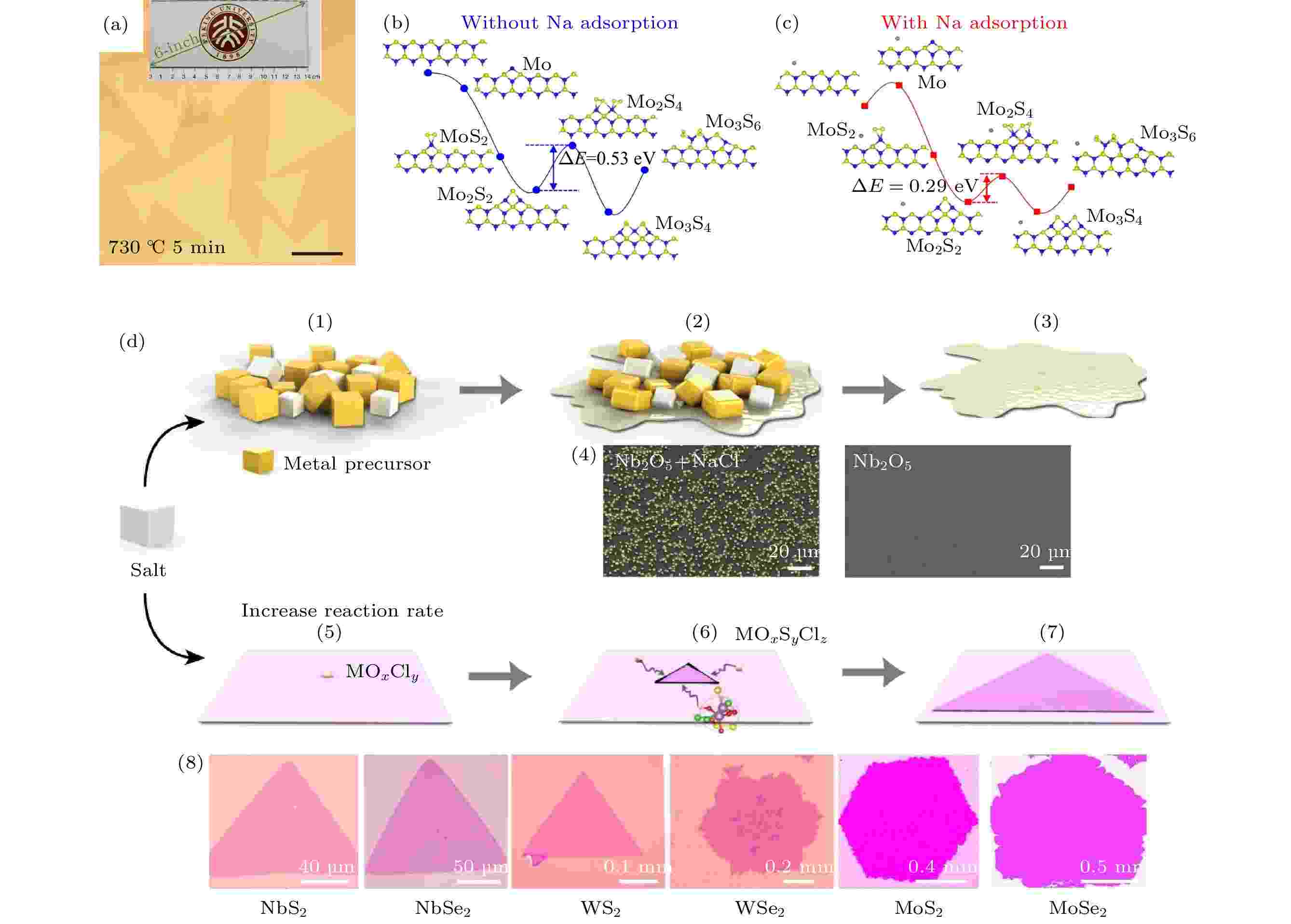
Figure10. (a) Optical image of monolayer MoS2 film; (b), (c) DFT calculations for the growth of MoS2 (b) without and (c) with Na[64]; (d) schematic illustration of the salt-assisted reaction process and optical images of TMDs films[65].
1) 将晶体成核动力学和CVD方法设计相结合
依据晶体生长理论, 可以得出一定条件下材料的成核尺寸和成核势垒. 如第2节提到的石墨烯的种子生长法, 依据石墨烯生长所需的临界能量, 可以在较低的化学势下实现单个晶粒薄膜的连续生长. 深入了解更多材料的生长机理, 有利于基于其生长动力学精准合成大面积的二维材料. 此外, 在金属表面生长石墨烯, 边界的重构依赖于石墨烯和衬底相互作用的强度, 新奇的边界结构会显著改变石墨烯晶粒的平衡形貌和生长行为.
2) 寻找并设计晶格适配的衬底
晶格的取向可以由衬底的表面对称性决定, 对衬底操作可以再现原子核的能量优先取向. 选择与二维材料具有相同表面对称性的衬底, 更容易沉积大面积且取向一致的薄膜, 如, Cu(111)衬底与石墨烯具有相同的晶格取向, 因此Cu(111)是制备石墨烯薄膜的常用衬底, 目前已经在此衬底上成功制备了半米级的薄膜. 这种方法也适用于其他材料, Tan等[66]发现绝缘钙钛矿氧化物衬底[SrTiO3, LaAlO3, (La, Sr)(Al, Ta)O3]与Bi2O2Se有完美的晶格匹配性, 并将其作为衬底合成了晶圆级Bi2O2Se薄膜. 此方法也可广泛应用于其他大面积二维单晶的外延生长.
3) 生长系统的创新和改进
二维TMDs的生长通常涉及固体前驱体, 其浓度难以精确控制. 因此需要开发先进的CVD系统, 使材料生长具有更好的可控性. 目前开发的MOCVD可以使反应腔内的前体浓度保持稳定, PECVD和ICP-CVD也可以显著改善反应环境. 此外, 还需要有技术上的创新, 例如通过使用激光、电场或磁场等精准控制反应条件.