全文HTML
--> --> -->未经Cs/O激活的GaAs光电阴极仅对高能光子的光束产生微弱的电子发射, 而在可见光波段则不会产生电子发射现象. 虽然场助光电阴极的电子发射能力高于普通阴极的电子发射能力, 但是场助光电阴极同样无法承受长时间、高能量光束照射, 其每平方厘米面积的发射电流也无法达到的安培量级. 在场助光电阴极组件中, 随工作电压增加, 阴极与栅极之间容易出现打火或短路等现象, 增加了器件的封装难度. 场发射阴极组件中, 由覆膜工艺制备的绝缘层可保障栅极和阴极之间距离的一致性, 使阴极表面的电场强度达到107 V/cm量级, 可以有效降低阴极表面势垒, 使阴极产生电子发射[20,21]. 因此可以通过在GaAs晶体表面制作真空沟道结构的方式来制备大电流密度的场助光电阴极. 由于GaAs晶体仅在光束照射时才会产生自由扩散的电子, 所以GaAs晶体作为负极材料制作场发射组件时, 只有光束照射到GaAs阴极材料上时才会产生电子发射, 可以实现光束对阴极电子发射特性的调制作用. 另外光激发电子所拥有的能量高于其他场发射材料中电子的能量, 这部分电子运动到阴极材料表面后隧穿表面势垒的几率也较大, 所以真空沟道结构光电阴极的工作电压将低于同等条件下其他场发射阴极的工作电压. 本文使用覆膜与刻蚀工艺制备了真空沟道结构光电阴极组件, 测试了不同激光功率和工作温度条件下阴极组件的电子发射特性, 分析了温度对阴极电子发射稳定性的影响, 并仿真了真空沟道结构对阴极组件发射电子束形状的影响.
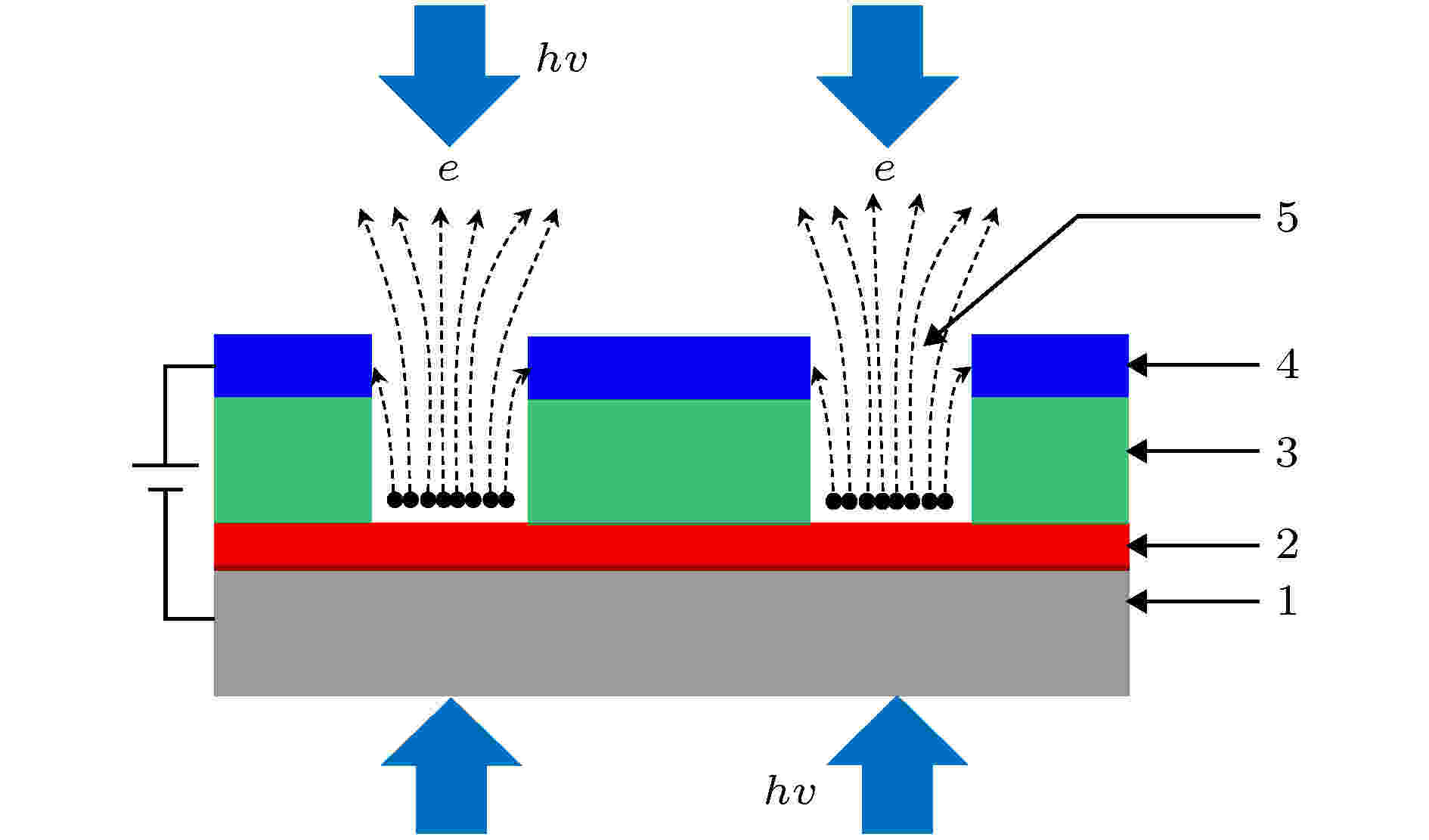
Figure1. Working principle of photocathode with vacuum channel. Symbol 1, 2, 3, 4 and 5 are negative electrode, photocathode material, insulation, grid electrode and vacuum channel, respectively.
实验所用的光电阴极材料为GaAs衬底材料. 负极和栅极材料均为Mo, 厚度分别为150和250 nm. 绝缘层材料为Al2O3, 厚度为150 nm. 为了便于光电阴极组件的制备和性能评估, 组件中真空沟道结构设计为长方形, 宽度为3 μm, 长度为700 μm. 为了提高阴极的发射电流, 设计了阵列式真空沟道结构, 沟道数量为100. 真空沟道的中心间距为7 μm, 即绝缘层和栅极的宽度为4 μm, 因此阴极组件电子发射区域的尺寸为700 μm × 700 μm, 即阴极的面积为0.0049 cm2.
首先使用丙酮和无水乙醇等对阴极材料进行清洗, 去除阴极材料表面的污染物, 提高阴极材料表面的覆膜效率和薄膜的均匀性. 真空沟道结构光电阴极组件制备工艺为使用电子束双向沉积设备依次在材料表面覆Al2O3(绝缘层)和Mo金属膜(栅极); 利用光刻技术在材料表面曝光出真空沟道结构; 再使用感应耦合反应离子体刻蚀设备对真空沟道中的Mo金属薄膜进行刻蚀; 最后使用氢氟酸和氟化铵混合溶液对Al2O3薄膜进行腐蚀, 直至阴极材料暴露出来, 此时阴极表面就获得了真空沟道结构. 使用扫描电子显微镜观察阴极组件的真空沟道结构, 如图2所示.
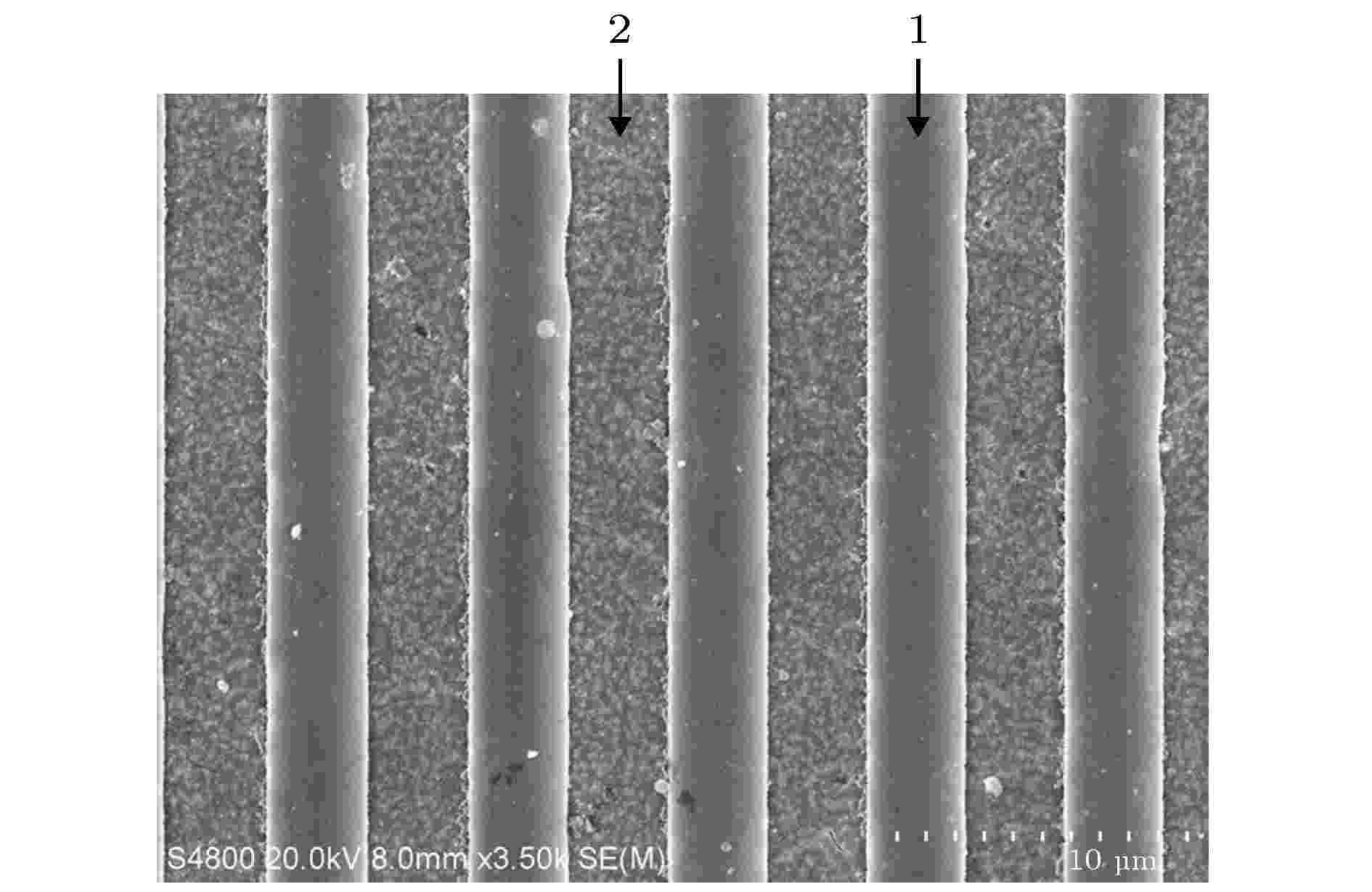
Figure2. Surface microtopography of vacuum channel structure. Symbol 1 and 2 are photocathode material grid electrode, respectively.
对制备好的光电阴极组件进行装架, 其中GaAs衬底材料作为阴极组件的负极. 使用钼片作为栅极和负极的引线. 将阴极封装于玻壳内, 并在排气台上对阴极组件及玻壳进行除气. 玻壳除气温度为250 ℃, 阴极组件除气温度为550 ℃, 保持玻壳内真空度在10–6 Pa量级. 待玻壳温度降为常温后将玻壳进行封离. 使用连续激光器对阴极的电子发射性能进行测试, 主要包括光束功率、工作温度对阴极发射电流的影响, 同时也开展了阴极组件寿命试验和贮存试验.
使用532 nm连续激光器对光电阴极的电子发射特性进行测试, 阴极组件在不同功率的激光光束照射下的直流发射特性如图3所示. 栅极电压为25 V时, 真空沟道内的最大电场强度为1.6 × 106 V/cm, 低于场发射阴极所需的电场强度, 降低了阴极组件中发生击穿和打火的概率. 随激光光束功率和阴极组件的工作电压增加, 阴极组件的发射电流均逐渐增大. 但是当激光功率较大时, 随着组件工作电压增大, 发射电流增长幅度逐渐变大. 激光功率为1和5 W时, 阴极组件的发射电流分别为2.54和26.12 mA, 阴极发射电流密度分别为0.52和5.33 A/cm2, 对应的光谱响应分别为和5.22 mA/W, 量子效率分别为0.59%和1.22%.
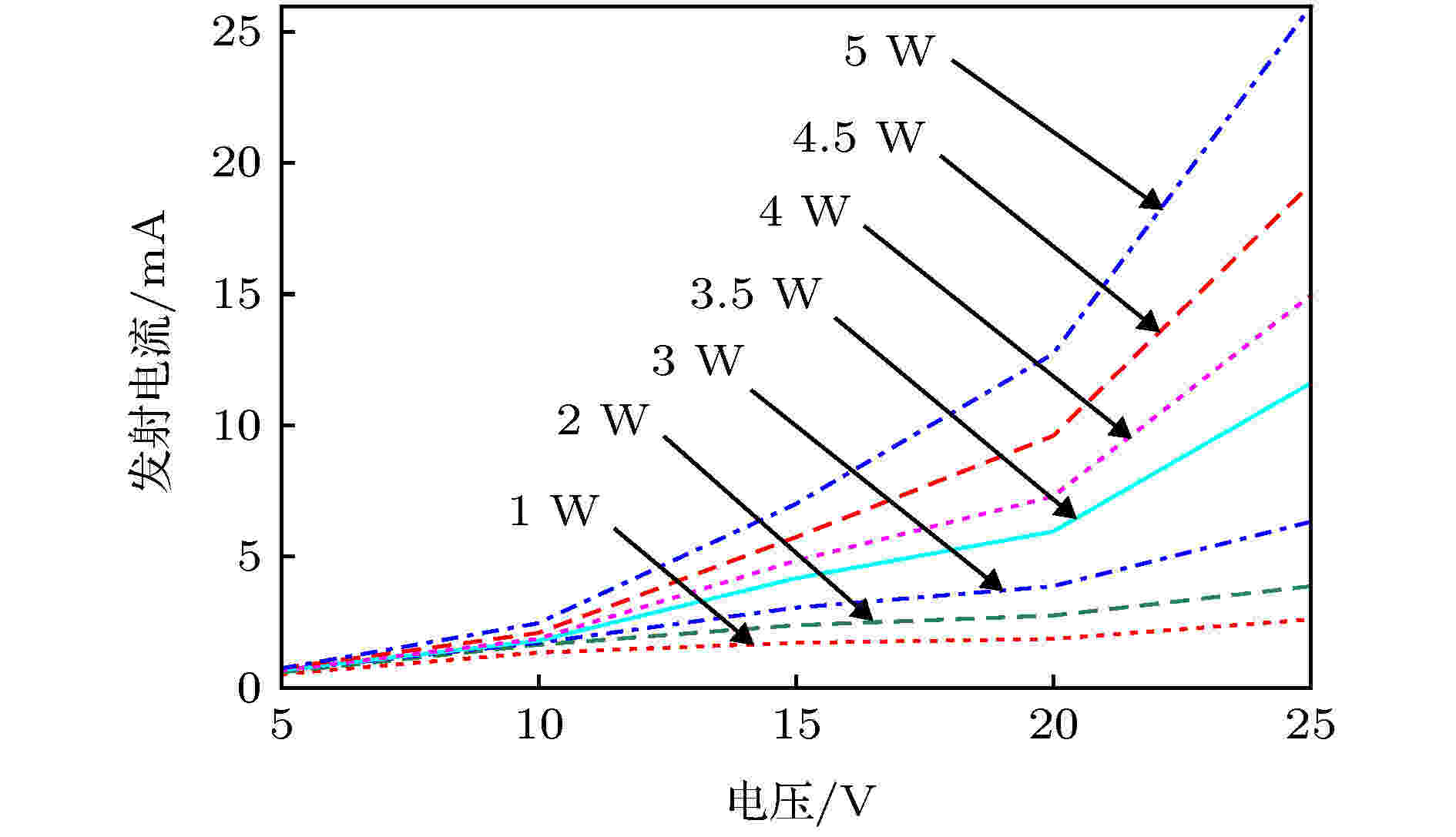
Figure3. DC emission characteristics of photocathode module with different laser bean power.
在阴极电子发射特性测试过程中, 当激光光束照射到阴极组件上时, 阴极的发射电流并非直接到达一个相对稳定的数值, 而是随测试时间增加, 电流逐渐增大, 最终到达一个稳定值, 持续时间约为20 min. 这是由于阴极材料为半导体材料, 激光光束的能量密度较大, 对阴极组件具有一定的加热作用. 随着GaAs晶体温度增加, 晶体内的载流子浓度增大, 其电导率也相应地增大, 提高了负极对阴极材料内电子的补充效率, 此时负极对真空沟道附近区域的补充电流逐渐增大. 另外, 随着GaAs晶体材料内电流增加, 电子与晶格碰撞的次数也大幅度增大, 因碰撞而损失的能量将转化为晶体的内能, 进一步提高阴极的温度. 所以才出现了光束功率和阴极组件工作电压越高, 阴极的发射电流就越大这一现象.
为了验证温度对阴极性能的影响, 分别测试了不同温度条件下阴极电子发射特性. 测试过程中, 激光光束功率为3 W, 波长为532 nm, 阴极组件的温度分别为室温、200 ℃和400 ℃, 测试结果如图4所示. 测试过程中, 随着阴极组件温度升高, 阴极发射电流到达稳定值所需时间逐渐增大. 为了避免测试电流过大对阴极组件造成损伤, 三次测试的最大电流和电压分别为27.49 mA@40 V, 78.22 mA@35 V和89.69 mA@26 V. 由此可知, 工作温度对光电阴极组件的电子发射特性存在较大程度的影响, 光电阴极组件发射连续电子束时需要对阴极组件的工作温度进行适当控制. 同时提高阴极工作温度也成了提高光电阴极组件电子发射电流的有效途径.
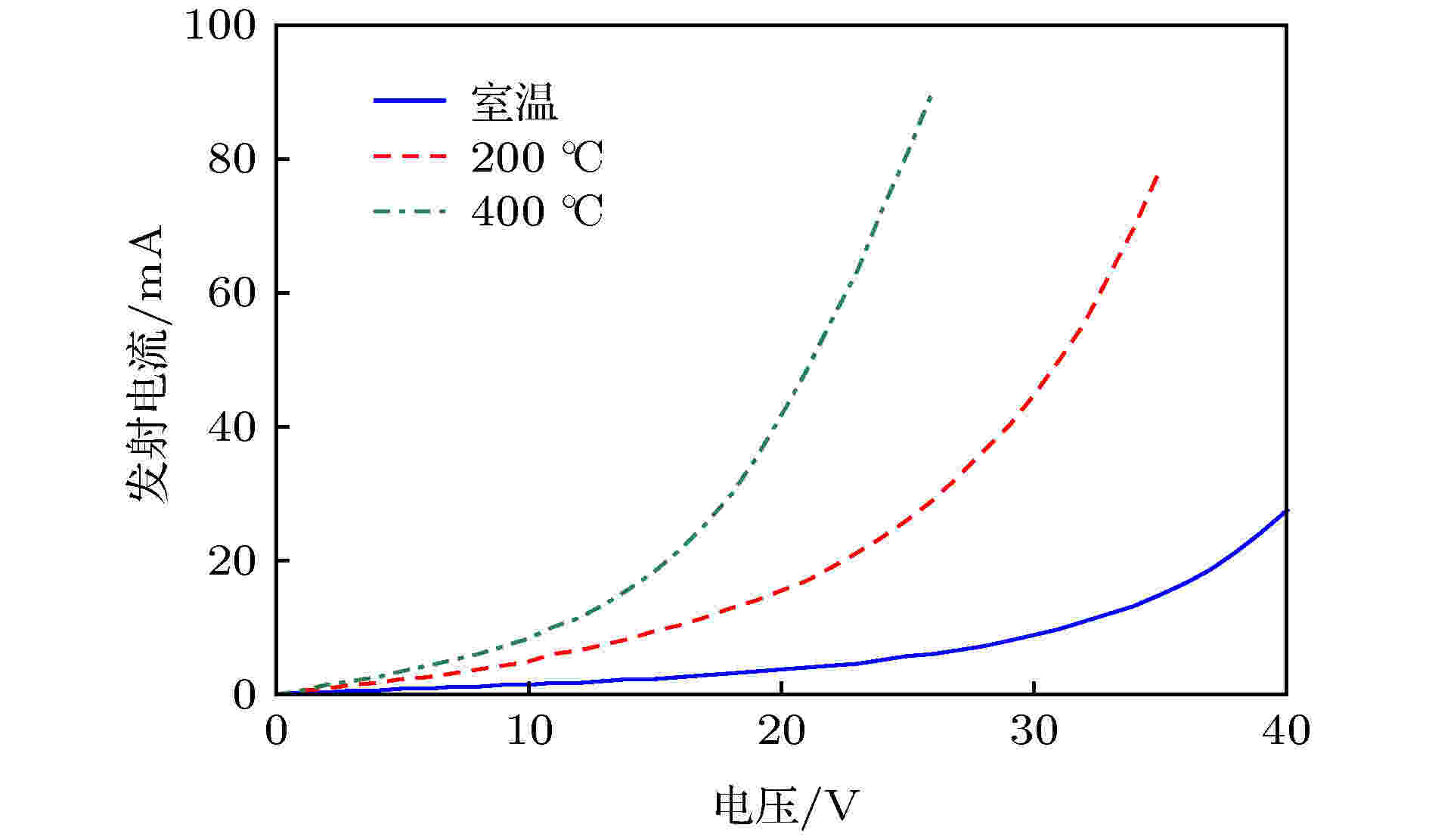
Figure4. DC emission characteristics of photocathode module with different temperature.
实验中所用的光电阴极材料为GaAs衬底材料, 入射光可被衬底材料完全吸收, 除发射到真空的电子所携带的小部分能量外, 大部分能量转化为材料的内能. 即光电阴极工作过程中, 只有距阴极表面的距离小于电子扩散长度的光激发电子才能运动到阴极材料表面, 参与阴极电子发射. 而距阴极表面距离大于电子扩散长度的电子最终将跃迁至导带, 而无法参与阴极电子发射, 其能量也会转化为阴极的内能.
在强光照条件下, 光电阴极材料的最优厚度完全依赖于阴极材料的电子扩散长度. 当光电阴极材料为薄膜材料且衬底为透光率较高的材料时, 光电转换过程仅存在于阴极薄膜内, 衬底材料将不再是热源, 阴极组件的热量传导方向为自阴极薄膜向衬底方向. 在此条件下, 阴极薄膜的温度可迅速达到平衡状态, 也使阴极的发射电流在短时间内达到稳定状态.
真空沟道结构GaAs光电阴极组件结构与传统GaAs光电阴极组件结构存在较大的差异, 传统光电阴极表面吸附着单层的Cs/O激活原子, 强光工作环境和离子轰击过程中, Cs和O原子会迅速从阴极表面脱附, 导致阴极性能衰减. 而在真空沟道结构GaAs光电阴极组件中, 除部分阴极材料暴露于真空沟道外, 其他部分被Al2O3和Mo金属层覆盖. 由于真空沟道结构占整个阴极组件面积的比例比较小, 所以离子轰击到阴极材料表面的几率也相应地会降低. 因此在阴极工作过程中, 大部分离子会轰击到Mo金属膜上, 对阴极材料起到一定的保护作用. 由于GaAs晶体表面不存在激活原子, 当部分离子轰击到GaAs晶体表面时, 不会造成阴极性能大幅度衰减. 即使部分GaAs晶体在离子轰击作用下出现破损, 只要阴极组件中仍有足够厚度的GaAs晶体可吸收入射光, 阴极组件的性能就不会衰减.
为了研究光电阴极电子发射特性的稳定性, 开展了阴极寿命测试实验. 实验中连续激光光束功率为3.5 W, 波长为532 nm, 栅极电压为15 V. 测试时间为144 h, 测试结果如图5所示, 虽然测试过程中阴极发射电流出现波动, 但是发射电流并未出现衰减, 阴极发射电流基本保持在4.5 ± 0.3 mA. 造成阴极发射电流变化的主要原因是激光器长时间工作过程中光束功率稳定性变差, 光束功率范围为3.0 ± 0.1 W. 由此可推断, 如果激光器可提供功率稳定的光束, 真空沟道结构光电阴极就可以产生稳定的发射电流.
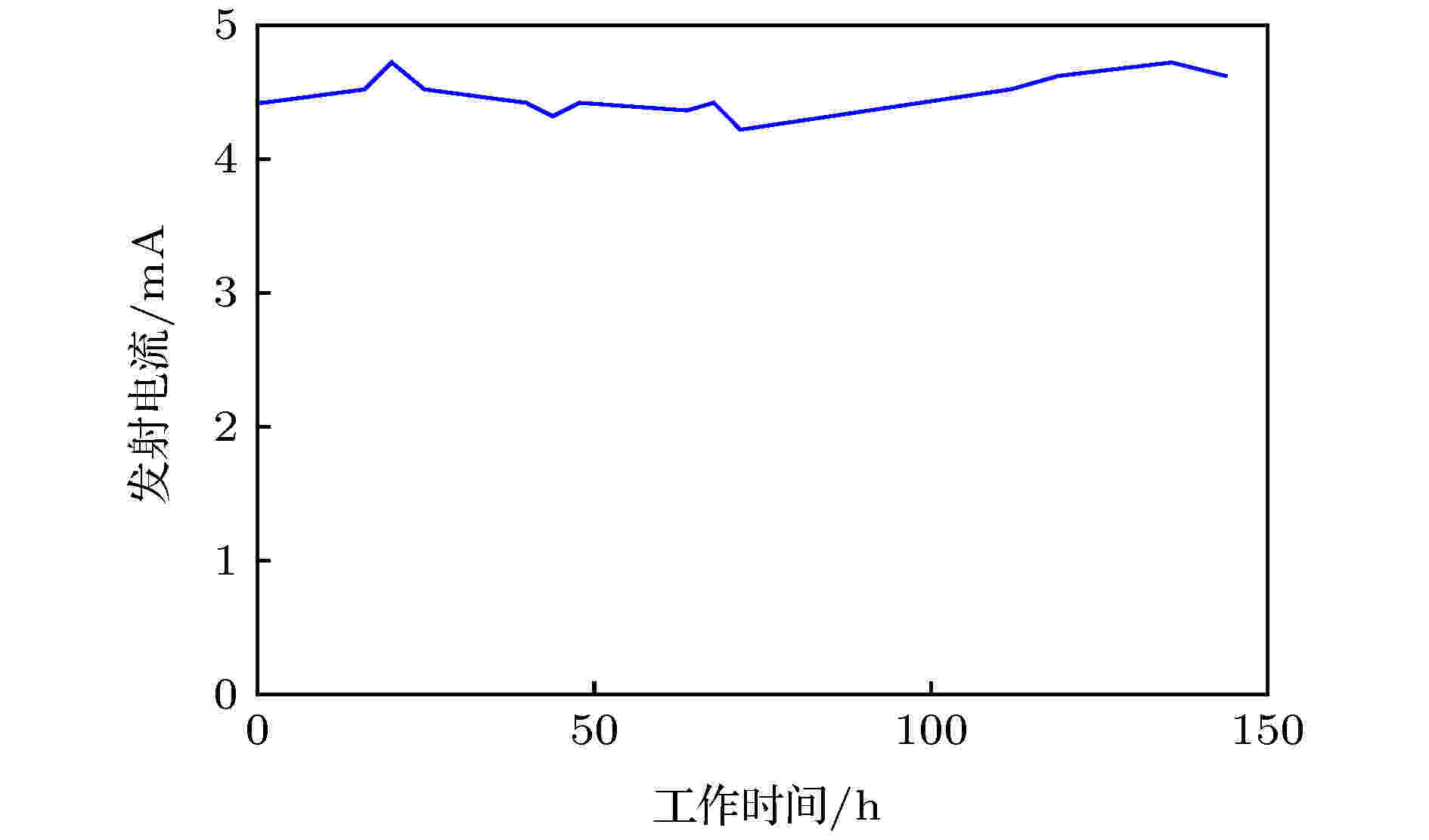
Figure5. The lifetime test curve of photocathode module.
另外对光电阴极组件进行了贮存实验, 高温贮存温度为85 ℃, 时间为48 h, 低温贮存温度为–55 ℃, 时间为24 h. 在贮存期间阴极组件封装在玻壳中且为非工作状态, 实验前激光光束功率为2.8 W, 电源电压为15 V时, 阴极的发射电流为5.50 mA. 经高温和低温贮存后, 相同测试条件下阴极的发射电流分别为5.63和5.68 mA. 虽然在贮存实验前后阴极发射电流出现变化, 但是发射电流并未出现衰减的现象.
上述实验所用阴极组件的真空沟道为1 × 100的阵列式结构, 单个真空沟道的尺寸为700 μm × 3 μm × 0.4 μm, 使用CST对上述阴极组件的电子发射特性进行仿真模拟. 建立的仿真模型如图6所示, 绝缘层和栅极的厚度为0.4 μm, 阳极距阴极之间的距离为30 μm. 栅极和阳极电压分别为100和1000 V. 阴极组件发射电子束中横向截面电子分布如图7所示, 由于阴极组件发射的电子均源于真空沟道区域, 所以阴极发射的电子束形状与真空沟道结构形状相似. 随距栅极距离增加, 电子束中的电子将趋于均匀分布. 由此可知, 可通过改变真空沟道结构的方式, 来获得不同形状的电子束, 如圆形电子束、椭圆形电子束或带状电子束等.
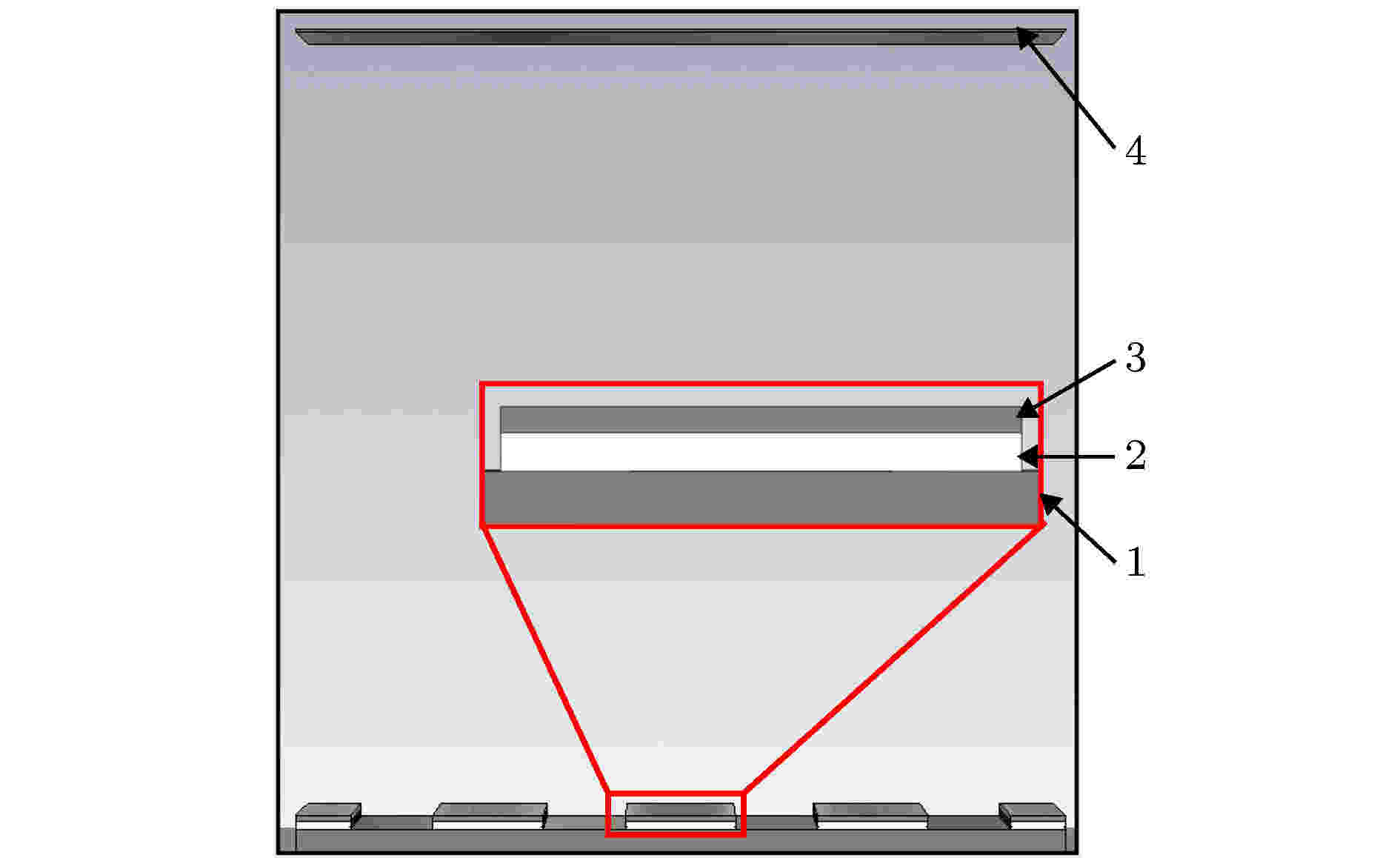
Figure6. Simulation model of photocathode module with rectangular vacuum channel. Symbol 1, 2, 3 and 4 are photocathode material, insulation, grid electrode and positive electrode, respectively.
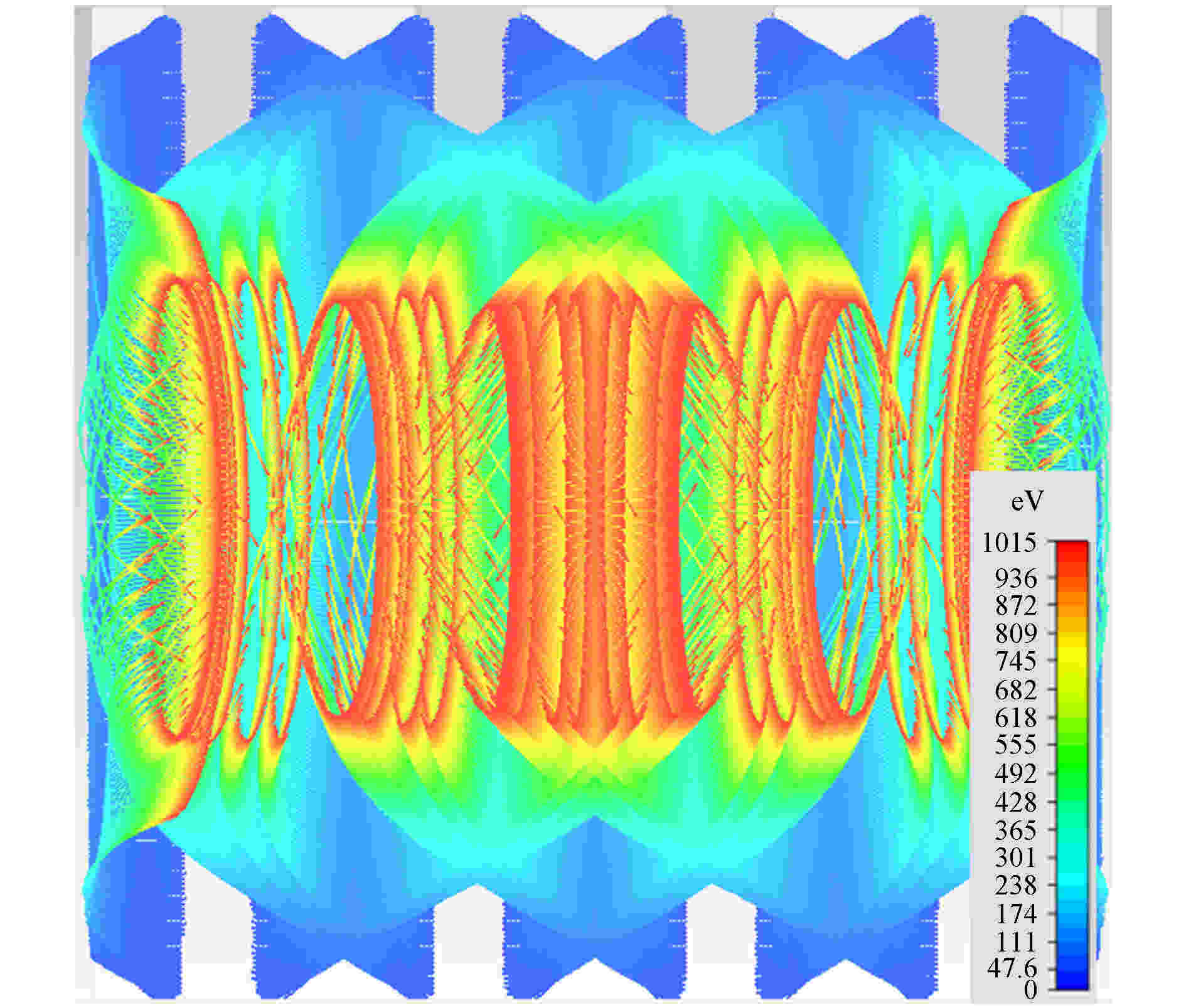
Figure7. Electronic distribution of lateral interface of photocathode module electron beam with rectangular vacuum channel.
栅极电压为100 V时, 阴极材料表面电场强度的峰值达到2.5 × 106 V/cm, 阴极组件的平均发射电流密度达到21.3 A/cm2. 将栅极电压增加至150 V时, 阴极组件的平均发射电流密度可达到65.7 A/cm2. 通过计算仿真, 栅极与绝缘层的总厚度h与真空沟道宽度l的比值为0.5时, 阴极组件的发射电流密度达到最大值, 即栅极电压为100 V时, 发射电流密度达到115.9 A/cm2. 当h/l值远小于0.5时, 真空沟道中心位置的电场强度最低, 此时在阴极材料表面仅在靠近真空沟道边缘的区域才存在电子发射, 如图7所示. 随h/l值逐渐增大, 真空沟道中心位置的电场强度逐渐增强, 阴极材料表面参与电子发射的区域面积逐渐增大, 阴极的电子发射能力也相应地逐渐增强. 但是当h/l值大于0.5时, 真空沟道结构对栅极所提供的电场产生了屏蔽作用, 其影响最严重的区域为阴极材料表面靠近真空沟道边缘的位置. 随h/l值增加, 其影响区域逐渐向真空沟道的中心位置扩大. 当h/l值约为2时, 阴极组件几乎丧失电子发射能力. 因此, h/l值和栅极电压均影响着阴极组件的电子发射能力, 优化阴极组件的真空沟道结构参数和工作条件可有效提高阴极组件的电子发射能力.
目前常用的真空器件中电子束的形状为圆形, 为此使用仿真软件建立的圆形真空沟道结构的光电阴极组件, 对其发射电子束的形状进行仿真, 如图8(a)所示. 其中绝缘层和栅极的厚度分别为150和250 nm, 中心部分圆形沟道区域直径为5 μm, 栅极宽度为1 μm, 外部环形沟道内径为9 μm, 外径为12 μm. 阳极距阴极之间的距离为30 μm. 计算过程中栅极电压为100 V, 阳极电压为1000 V, 计算结果如图8(b). 由于连接中心圆形沟道和外部沟道的栅极所覆盖的位置未产生电子发射, 所以在电子束中电子的分布呈近似圆形分布. 为了完善阴极发射电子束的形状, 光电阴极真空沟道结构可采用场发射阴极的独立式圆形沟道结构进行设计. 然后根据所需的电子束形状, 对独立式圆形沟道的阵列结构进行合理调整, 即可获得电子分布较为均匀的电子束.
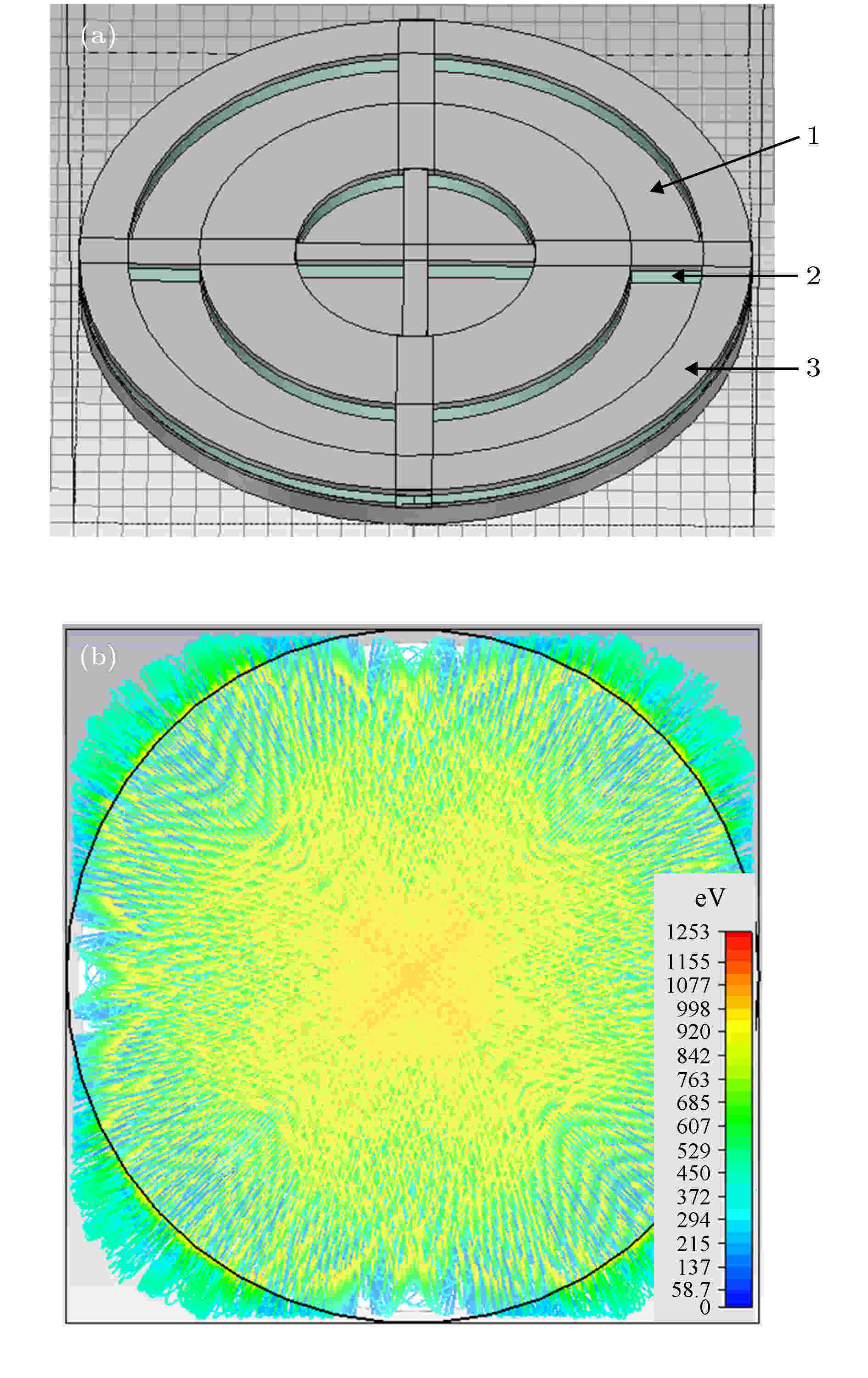
Figure8. Simulation of electronic emission characteristics of photocathode module with circular vacuum channel: (a) Structure model; (b) electronic distribution of lateral interface. Symbol 1, 2 and 3 are photocathode material, insulation, and grid electrode, respectively.