
2Department of Mathematics,
Received:2019-09-5Revised:2019-11-1Accepted:2019-12-23Online:2020-02-05

Abstract
Keywords:
PDF (1202KB)MetadataMetricsRelated articlesExportEndNote|Ris|BibtexFavorite
Cite this article
G Sowmya, B J Gireesha, S Sindhu, B C Prasannakumara. Investigation of Ti6Al4V and AA7075 alloy embedded nanofluid flow over longitudinal porous fin in the presence of internal heat generation and convective condition. Communications in Theoretical Physics, 2020, 72(2): 025004- doi:10.1088/1572-9494/ab6904
1. Introduction
Due to the wide range of applications of nanofluid in the field of heat exchangers, solar collectors, electrical cooling systems, biomedicines etc., the heat management using nanofluids is one of the trending topics of research. The nanoparticles considered for the nanofluid preparation may be polymeric, semiconductor, metal, ceramic, or carbon based etc. The proper composition of metals gives rise to alloys of greater strength or resistance. The suspension of alloy as a nano-sized particle in the base fluid can be used as nanofluid. In this regard, Zitnansky and Caplovic [1] obtained that thermal and mechanical treatment enabled them to produce an alloy with microstructure. Aminfar et al [2] numerically examined the hydro thermal properties of ferrofluid. Experimental analysis on thermal conductivity and dynamic viscosity of ${Ag}-{MgO}/{H}_{2}O$ hybrid nanofluid has been carried out by Esfe et al [3]. Experimental study on the mechanical properties of copper alloy has been studied by Nassar et al [4]. Superplasticity in Ti6Al4V has been studied experimentally by Alabort et al [5]. They found that after long deformation, microstructure remains equiaxed. Mahmoodi and Kandelousi [6] examined the kerosene-alumina nanoliquid flow in the semi cryogenic engine channel. Farooq et al [7] considered non-Darcy porous medium to scrutinize the squeezed nanoliquid flow. TiO2-ethylene glycol nanofluid flow in a stretching surface was analysed by Hosseinzadeh et al [8]. MHD Couettee-Poiseuille flow of nanofluids in a rotating channel was discussed by Tlili et al [9] and they revealed that entropy generation rate diminishes for nanofluid parameter due to mass and heat transfer. Makinde et al [10] described the influence of AA7075 and ${Ti}6{Al}4V$ nanoparticles on fluid flow across a rotating disk. The finite element method based on the control volume is utilized by Sheikholeslami et al [11] to analyse the nanofluid free convection in the presence of electric field. Shashikumar et al [12] have investigated the influence of the alloy nanoparticle on the fully developed stream of nanofluid in a microchannel. Rakesh et al [13] have done the comparative study between the slip nanofluid flow and no-slip nanofluid flow in the existence of viscous dissipation and Joule heating. They showed that heat transfer rate is significantly controlled by velocity slip and temperature jump. By applying the homotopy perturbation method, Abbasi et al [14] have examined the peristalsis of nanofluid in the presence of Hall effect and ohmic heating, whereas Abbasi et al [15] extended the work for temperature-dependent viscosity and they graphically discussed the Bejar number and entropy generation.Another method in enhancing heat transport rate is by considering fin structure. Fin has a wide range of applications in electrical chips, air conditioner, automobile, refrigeration, air cooled craft engines, vehicle radiators etc. Hence, Kiwan and Nirm [16] have investigated the performance of permeable fin in the improvement of heat transport rate. The comparative study between solid convectional fin and porous fin is carried out and found that porous fin displays better performance. Kiwan [17] also carried out the study of porous fin under natural convection conditions and analysed the performance of finite length fin and infinite long fin. Sharqawy and Zubair [18] have analytically examined the mass and heat transfer phenomena of straight fin and comprehensively presented the optimization as well as efficiency of fin. In addition to the convection, radiation also affects the heat transport phenomenon. Hence, Gorla and Bakier [19] have examined the radiation and natural convection condition on permeable fin and proved that fin with radiation transfer extra heat than fin without radiation. Aziz and Khani [20] developed an analytical solution to solve a physical problem of moving fin under variable thermal conductivity condition applying the homotopy analysis method (HAM). Darvishi et al [21] also used the HAM method to solve the problem on permeable fins under radiation as well as the natural convection condition. Darvishi et al [22] have extended the earlier study by considering porous fin’s unsteady thermal response.
The study of fin efficiency and temperature performance is carried out under variable thermal conductivity and the generation of th eheat condition by Aziz and Bouaziz [23] by applying the least square method. Hatami et al [24] have carried out the analysis by considering different fin materials like Al and ${{Si}}_{3}{N}_{4}$. Ghasemi et al [25] have utilized the differential transform method to examine fin performance in the presence of generation of heat internally. The fin of concave, triangular, convex and rectangular profiles were taken for the investigation by Mosayebidorcheh et al [26] and analysed the thermal behaviour using the hybrid method. Sobamowo [27] have taken rectangular fin for analysis and applied the finite difference method.
The wet condition around the fin surface improves the exchange of heat. Therefore, Hatami et al [28] have focused on the investigation of fully wet fin of the semi spherical profile under permeable nature and determined its refrigerator efficiency. Hatami and Ganji [29] have discussed mass and heat transfer analysis from circular fin under fully wet conditions. Vahabzadeh [30] have performed the analytical study on fully wet pin fin by applying the least square method. The variable heat generation and conductivity in the moving fin is described analytically utilizing the DTM method by Dogonchi and Ganji [31]. Furthermore, Darvishi et al [32] have utilized the Spectral Collocation technique to explain the performance of longitudinal fin under wet conditions. Gireesha et al [33] have developed the finite element method to examine wetted moving fin of the radial profile.
Based on the aforementioned literature investigation, we endeavour to combine the heat transfer rate enhancing factors like alloy-embedded nanofluid flow as well as porous fin under wet condition in the presence of natural convection and radiation. The generation of internal heat is considered for the analysis and convective boundary condition is taken for the study. Here, the Runge–Kutta–Fehlberg method is applied and the mathematical study is carried out by graphical interpretation of the obtained results.
2. Mathematical formulation
A flow of nanoliquid over the porous fin under radiation and natural conduction conditions is considered for the analysis. The attached fin to the prime surface is in longitudinal geometry with length L, thickness t and width w and it is displayed in figure 1. The fin base is kept at contact temperature Tb and the temperature of surrounding fluid is Ta. The fin is assumed to be stagnated along with internal heat generation. For the flow of fluid to infiltrate through the porous nature of the fin, Darcy’s model has been taken for the analysis. The small element of the fin dx is considered and a steady state energy balance equation of the present model on dx isFigure 1.
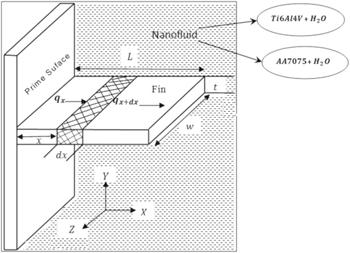
Figure 1.Coordinate system of the physical model.
By applying equations (
Further, the nanoparticle of titanium alloy (${Ti}6{Al}4V$) and aluminium alloy (AA7075) with base fluid water are in thermal equilibrium state. The nanoparticle AA7075 contains 90% Al, 5%–6% Zn, 2%–3% Mg, 1%–2% Cu and less than a half percent of other metals. ${Ti}6{Al}4V$ is made up of 90% Ti, 6% Al, 4% V, 0.25% Fe and less than a half percent of other metals. The thermophysical quantities like thermal conductivity (k), coefficient of thermal expansion (β), specific heat (Cp), density (ρ) and dynamic viscosity (μ) of the nanofluid are as presented in table 1. These thermophysical properties are modelled via mixture theory. They are as follows:
Table 1.
Table 1.Thermophysical properties of water, Ti6Al4V and AA7075 [10].
Physical properties | $k(W/{mk})$ | ${C}_{p}(j/{kgk})$ | $\rho ({kg}/{m}^{3})$ | $\beta \times {10}^{5}(1/K)$ |
---|---|---|---|---|
Water | 0.613 | 4179 | 997.1 | 21 |
${Ti}6{Al}4V$ | 7.2 | 0.56 | 4420 | 0.86 |
AA7075 | 173 | 960 | 2810 | 2.34 |
New window|CSV
The following dimensionless variables are considered:
3. Numerical procedure
The nonlinear ordinary differential equation (4. Results and discussion
In order to scrutinize the salient feature of temperature field for diverse values of relevant parameters, a numerical analysis is carried out by the Runge–Kutta–Felhberg method. The numerical results for both the alloys are represented in figures 2–12.Figure 2.
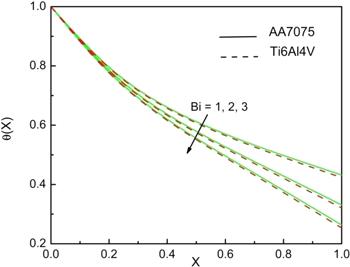
Figure 2.Impact of Bi on the temperature performance of the fin when G=0.1, Nc=10, Nr=5, m2=1, ϵG=0.2, θa=0.4, and n=1.
Figure 2 shows the impact of the Biot number on the thermal profile along fin length for ${AA}7075-{H}_{2}O$ and ${Ti}6{Al}4V-{H}_{2}O$ nanofluid. It is noticed that, with the increase in Bi from 1 to 3, the temperature of the fin decreases. Physically, Biot number is proportional to convection at the surface and inversely proportional to conduction within the surface. Hence, convective heat transfer intensifies for higher values of Bi. Additionally, water-based titanium alloy nanofluid displays relatively more heat transfer than aluminium alloy nanofluid.
The influence of variation of radiative parameter on the temperature field of the fin for ${AA}7075-{H}_{2}O$ and ${Ti}6{Al}4V-{H}_{2}O$ nanofluid is as depicted in figure 3. It is clearly visible that, as the Nr value amplifies, temperature of the fin reduces. This is due to the fact that increase in Nr means enhancement in the radiation effect, which decreases the fin temperature. Hence, radiation effect impacts on the fin cooling process. Clearly, titanium alloy nanofluid shows lower temperature compared to aluminium alloy nanofluid.
Figure 3.

Figure 3.Impact of Nr on the temperature performance of the fin when G=0.1, Nc=10, m2=1, ϵG=0.2, θa=0.4, n=1, and Bi=1.
The effect of different values of convective parameter on the fin temperature distribution is as displayed in figure 4. As the convective factor enhances, temperature of the fin decreases. This is because Nc is a product of Rayleigh number and Darcy’s number. With the raise in Nc, Da enhances, which means permeability increases. On the other hand, the increase in Ra leads to a reduction in thermal resistance. Hence, with the enhancement in the convective parameter, transfer of heat from the surface of fin amplifies. At lower Nc value, ${Ti}6{Al}4V$ exhibits a better heat transfer rate but for higher Nc value both the nanofluid presents the same nature.
Figure 4.
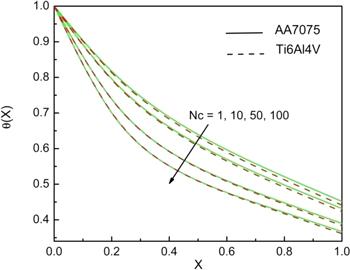
Figure 4.Impact of Nc on the temperature performance of the fin when G=0.1, Nr=5, m2=1, ϵG=0.2, θa=0.4, n=1, and Bi=1.
Figure 5 illustrates the influence of wet porous factor on temperature behaviour of fin. It is observed that, as m2 rises from 0.1 to 1, minute difference is seen, but rise of m2 from 1 to 10 shows large variation and temperature of the fin decreases rapidly. Since, the permeable nature of fin assists in the flow of fluid to penetrate through it. Hence, we notice more heat transfer rate. Additionally, for a higher m2 value, titanium alloy displays relatively more heat transfer than aluminium alloy nanofluid.
Figure 5.
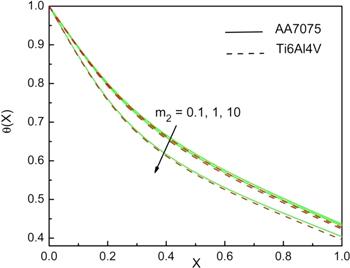
Figure 5.Impact of m2 on the temperature performance of the fin when G=0.1, Nc=10, Nr=5, ϵG=0.2, θa=0.4, n=1, Bi=1.
The impact of power index (n) on the thermal profile of the fin with flow of titanium and aluminium alloy embedded nanofluid is plotted in figure 6. As the n rises from 0 to 4, there will be more thermal profile. The different n values depict the different flow natures. It is clear observed that n=0 represents the linear case and n>0 presents the nonlinear case.
Figure 6.
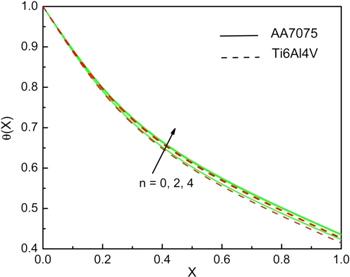
Figure 6.Impact of n on the temperature performance of the fin when G=0.1, Nc=10, Nr=5, m2=1, ϵG=0.2, θa=0.4, and Bi=1.
The influence of ambient temperature on thermal behaviour of the fin is as explored in figure 7. It is found that the thermal profile is an increasing function of ambient temperature. This is because of the increase in surrounding fluid temperature, heat transfer from fin decreases. The aluminium alloy nanofluid shows more temperature of the fin compared to titanium alloy nanofluid.
Figure 7.
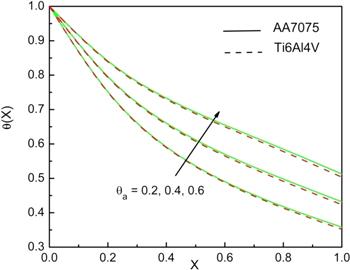
Figure 7.Impact of θa on the temperature performance of the fin when G=0.1, Nc=10, Nr=5, m2=1, ϵG=0.2, n=1, and Bi=1.
Figure 8 reveals the influence of generation number on the fin thermal field. An increase in fin temperature for higher values of the generation number is noticed. The generation of internal heat within the fin, leads to a rise in temperature of the fin surface. Hence, transfer of heat diminishes. In addition, ${Ti}6{Al}4V$ exhibits relatively more heat transfer than AA7075.
Figure 8.
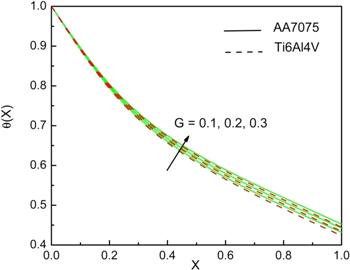
Figure 8.Impact of G on the temperature performance of the fin when Nc=10, Nr=5, m2=1, ϵG=0.2, θa=0.4, n=1, Bi=1.
The effect of simultaneous variation in radiative and convective parameter on the thermal gradient at the base point is as shown in figure 9. It is noticed that thermal gradient is more for larger values of radiative and convective parameter for both titanium and aluminium alloy nanofluid. The thermal gradient variation due to simultaneous change in generation number and internal heat generation parameter is analysed from figure 10. Clearly, the gradient decreases as the G and ϵG increases. Hence, the generation of internal heat negatively affects the fin rate of heat transfer. It is also observed that ${Ti}6{Al}4V$ alloy displays a higher gradient than the AA7075 alloy.
Figure 9.
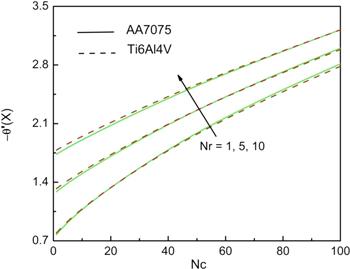
Figure 9.Influence of Nc and Nr on the temperature gradient at fin base when G=0.1, m2=1, ϵG=0.2, θa=0.4, n=1, and Bi=1.
Figure 10.
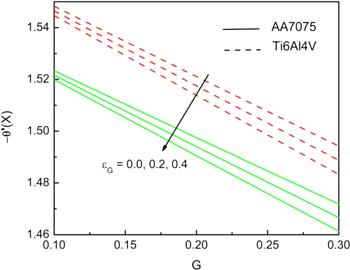
Figure 10.Influence of ϵG and G on the temperature gradient at the fin base when Nc=10, Nr=5, m2=1, θa=0.4, n=1, and Bi=1.
Figure 11 presented the influence of combined wet porous parameter and Biot number on the fin temperature gradient for both the nanofluids. Here, with the increase in m2 and Bi, the gradient keeps on increasing. It is also noticed that, for larger m2, more gradient effect is observed and also heat transfer due to the titanium alloy being better than the aluminium alloy. The impact of ambient temperature and power index on the thermal gradient variation at the fin base is as plotted in figure 12. The gradient is a decreasing function, for increase in power index as well as ambient temperature for both water-based titanium and aluminium alloy.
Figure 11.
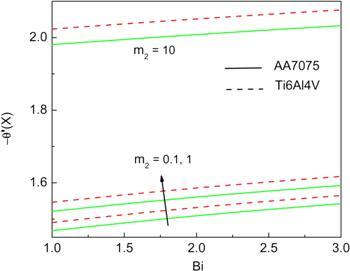
Figure 11.Influence of m2 and Bi on the temperature gradient at the fin base when G=0.1, Nc=10, Nr=5, ϵG=0.2, θa=0.4, and n=1.
Figure 12.
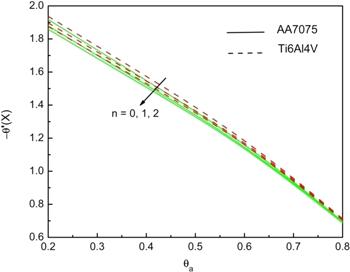
Figure 12.Influence of n and θa on the temperature gradient at the fin base when G=0.1, Nc=10, Nr=5, m2=1, ϵG=0.2, and Bi=1.
5. Conclusion
The transfer of heat through longitudinal porous fin wetted with nanofluid of ${Ti}6{Al}4V$ and AA7075 alloy immersed in base water is examined in the existence of natural convection and radiation condition along with convective boundary condition and the generation of internal heat. From the current analysis, the following conclusions are drawn:The radiation and convection characteristics showed a significant effect on the rate of heat transfer.The wet porous nature of the fin enhances the heat transfer rate.
The internal heat generation negatively affects the fin cooling procedure.
The presence of nanofluid favors the heat transfer phenomenon.
The ambient temperature and power index increases temperature field and as a result decreases the heat transfer rate.
Both titanium and aluminum alloy nanofluid enhances the temperature gradient.
It is found that the ${Ti}6{Al}4V-{H}_{2}O$ nanofluid is better in enhancing heat transfer from the fin surface compared to ${AA}7075-{H}_{2}O$ nanofluid.
Reference By original order
By published year
By cited within times
By Impact factor
DOI:10.1016/j.jmatprotec.2004.07.151 [Cited within: 1]
DOI:10.1016/j.jmmm.2011.09.028 [Cited within: 1]
DOI:10.1016/j.icheatmasstransfer.2015.06.003 [Cited within: 1]
DOI:10.17605/OSF.IO/WHTZV [Cited within: 1]
DOI:10.1016/j.actamat.2015.04.056 [Cited within: 1]
DOI:10.1016/j.nucengdes.2015.05.022 [Cited within: 1]
DOI:10.1115/1.4041497 [Cited within: 1]
DOI:10.1016/j.csite.2018.04.008 [Cited within: 1]
DOI:10.1007/s10973-018-7066-5 [Cited within: 1]
DOI:10.4028/www.scientific.net/DDF.384.69 [Cited within: 2]
DOI:10.1088/0253-6102/69/6/667 [Cited within: 1]
DOI:10.1108/HFF-06-2018-0301 [Cited within: 1]
DOI:10.1088/0253-6102/71/7/779 [Cited within: 1]
DOI:10.1088/1402-4896/aaf600 [Cited within: 1]
DOI:10.1016/j.jmmm.2018.10.132 [Cited within: 1]
DOI:10.1115/1.1371922 [Cited within: 1]
DOI:10.1007/s11242-006-0010-3 [Cited within: 1]
DOI:10.1016/j.applthermaleng.2008.01.003 [Cited within: 1]
DOI:10.1016/j.icheatmasstransfer.2010.12.024 [Cited within: 1]
DOI:10.1016/j.jfranklin.2011.01.008 [Cited within: 1]
DOI:10.1108/HFF-12-2011-0264 [Cited within: 1]
DOI:10.1007/s00231-014-1341-1 [Cited within: 1]
DOI:10.1016/j.enconman.2011.04.003 [Cited within: 2]
DOI:10.1016/j.enconman.2013.04.034 [Cited within: 1]
DOI:10.1016/j.csite.2014.05.002 [Cited within: 1]
DOI:10.1016/j.enconman.2014.05.033 [Cited within: 1]
DOI:10.1016/j.aej.2016.04.022 [Cited within: 1]
DOI:10.1016/j.enconman.2014.05.007 [Cited within: 1]
DOI:10.1016/j.ijrefrig.2013.11.002 [Cited within: 1]
DOI:10.1016/j.csite.2014.11.002 [Cited within: 1]
DOI:10.1016/j.applthermaleng.2016.04.121 [Cited within: 1]
DOI:10.1108/HFF-06-2015-0230 [Cited within: 2]
DOI:10.1108/HFF-12-2018-0744 [Cited within: 1]