全文HTML
--> --> -->对于In2O3体系来说, In元素有毒、含量稀少且价格昂贵, 会造成环境污染, 因此迫切需要开发出无In的TCOs和TSOs材料. 对于ZnO体系来说, ZnO无毒、含量丰富、价格便宜且对环境无污染, 是In2O3的一种潜在替代材料. 但ZnO薄膜本征导电性一般, 且易与空气中的水氧反应, 导致其电学性能劣化. 此外, ZnO薄膜对酸或碱刻蚀液敏感, 导致图形化严重不均匀. 对于SnO2体系来说, SnO2不仅无毒、无污染、价格低廉, 而且还具有良好的电学性能和化学稳定性, 具有很大的发展潜力.
现今TCOs和TSOs薄膜的制备主要依赖于真空技术, 如磁控溅射[10–12]、脉冲激光沉积[13]、电子束蒸发[14]、化学气相沉积[15,16]和原子层沉积[17]等. 真空技术制备的薄膜具有高致密度、低粗糙度和高均匀性等优点, 但此类沉积技术需要面对设备结构复杂、价格昂贵、能耗高、制备工艺复杂、生产成本高等缺点. 未来薄膜制备朝大面积、低成本化方向发展, 真空技术难以满足需求. 与真空技术相比, 溶胶-凝胶法具有工艺简单、设备要求低、生产成本低等优点, 且比较容易通过溶液成分设计实现薄膜性能的调控, 符合未来薄膜制备技术的发展要求[18].
本文综述了溶胶-凝胶法制备SnO2基薄膜在n型TCOs, 薄膜晶体管 (thin-film transistor, TFT) 以及p型TSOs中的应用和发展, 总结出一些当前存在的关键问题, 促进了SnO2薄膜在TCOs和TSOs领域的应用.
2.1.氧化锡的结构特性和导电机制
图1(a)展示了SnO2的晶体结构 (红色为O原子, 灰色为Sn原子), 为四面体金红石结构, 属于P42/mnm空间群. 其中晶格常数为a = b = 4.7193 ?, c = 3.2105 ?[19]. 原胞包含两个Sn原子和4个O原子, 原胞的体心和顶角位置都被Sn4+离子占据, Sn4+离子的位置为 (0, 0, 0) 及(1/2, 1/2, 1/2), O2–离子的位置为 ±(u, u, 0) 及 ±(1/2 + u, 1/2 – u, 1/2), 其中u为0.306[20,21]. 图1(b)为SnO2薄膜的XRD图谱, 表明薄膜依然保持多晶结构. 通常, SnO2薄膜晶粒的生长择优取向会与衬底材料和衬底温度等密切相关. 沉积后的薄膜经过高温退火处理后主要沿着 (110), (101) 和 (211) 等晶面生长. 图1(c)为第一性原理计算的SnO2能带结构. 它的导带和价带分别由Sn5s和O2p轨道构成, 并且导带底和价带顶同时出现在布里渊区的Γ点处, 表明SnO2为直接带隙半导体, 禁带宽度为3.6 eV.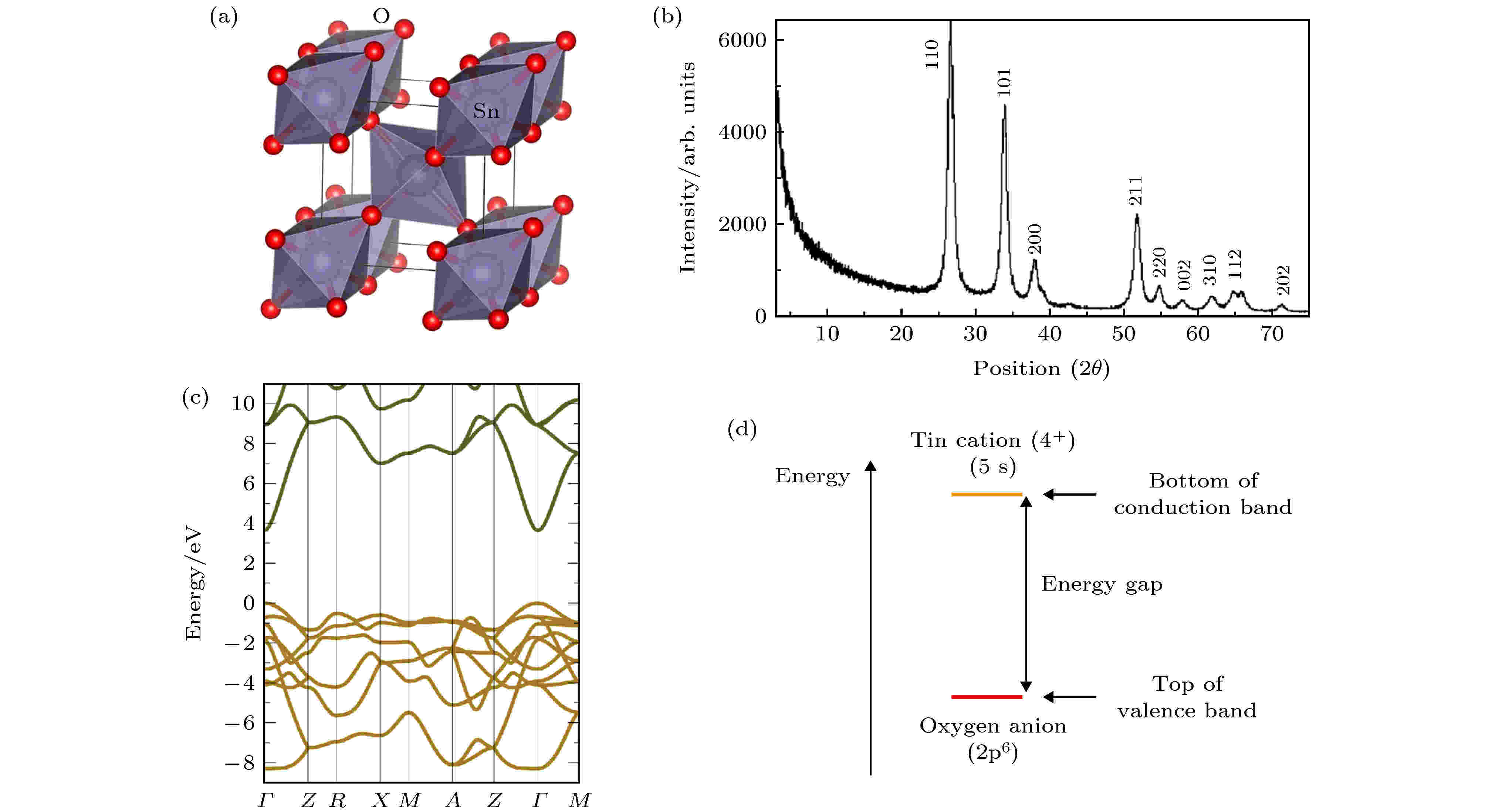
Figure1. SnO2: (a) Crystalline structure; (b) XRD pattern[22]; (c) band structure[23]; (d) band structure schematic[7].
理论上, 符合化学计量比的SnO2薄膜具有较低的载流子浓度和高电阻率 (~108 Ω·cm) [24–26]. 然而, 在实际薄膜制备和生长过程中, 薄膜组分会发生偏析, 导致各种晶格缺陷的产生, 使得薄膜具有较高的载流子浓度 (1018—1020 cm–3)[8]. 图2展示了SnO2薄膜内部不同本征点缺陷的形成能. SnO2薄膜内部缺陷主要有氧空位 (VO)、间隙锡 (Sni)、间隙氧 (Oi) 和锡空位 (VSn). 在价带顶附近, VO和Sni缺陷态的形成能为负值, 表明它们能够自发地形成, 从而导致非化学计量比的SnO2薄膜形成. 在所有缺陷中, VSn缺陷态的形成能最高, 这是因为在以Sn原子为中心的八面体中, 带负电荷的氧原子之间产生较大的静电排斥. 总体来说, VO和Sni缺陷态的形成能要远远低于 Oi和VSn缺陷态, 使得VO或Sni缺陷在SnO2薄膜中占主导地位. 另外, Sni缺陷态转变 (+4→+3) 发生在高于导带底0.203 eV能级处; VO缺陷态转变 (+2→0) 发生在低于导带底0.114 eV能级处, 它在室温下可全部离化, 为导带提供高浓度的电子. 因此, SnO2薄膜表现为n型半导体特性.
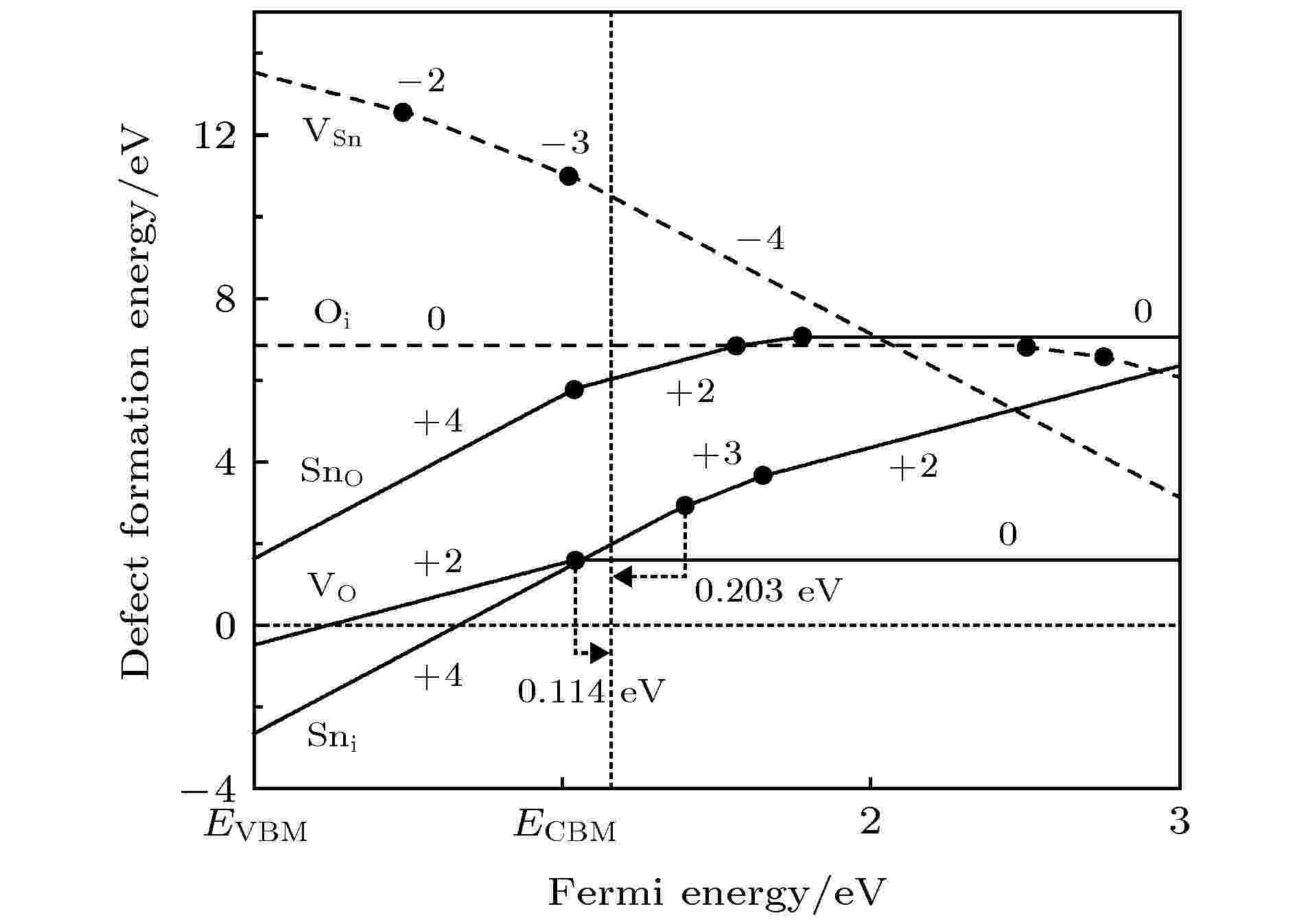
Figure2. Formation energy of intrinsic point defects in SnO2[26].
2
2.2.元素掺杂机理
由于TCOs和TSOs薄膜对电学性能要求不同, 而SnO2薄膜的电学性能并不满足. 因此, 需要通过元素掺杂分别实现SnO2薄膜在TCOs和TSOs领域的研究和应用. 在半导体中, 掺杂原子的价电子数与主体材料晶格原子的价电子数的关系决定杂质原子的行为 (即施主杂质和受主杂质). 施主杂质是指能够向导带中提供电子的杂质, 即掺杂原子的价电子数高于主体材料原子的价电子数; 受主杂质是指能够向价带提供空穴的杂质, 即掺杂原子的价电子数低于主体材料原子的价电子数. 图3展示了掺杂元素对半导体能带的影响. 根据元素掺杂薄膜导电类型的不同, 将掺杂元素分为n型掺杂和p型掺杂.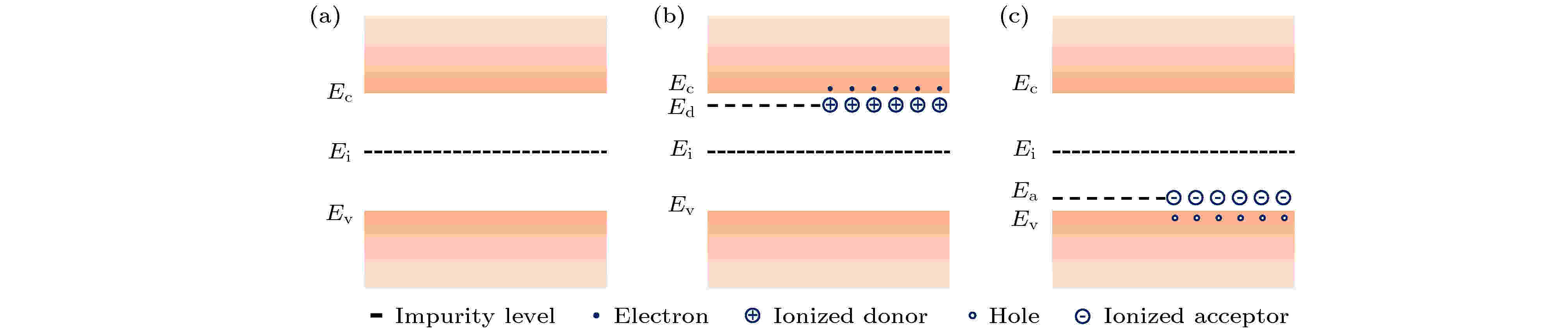
Figure3. The energy band schematic of semiconductors: (a) intrinsic (b) n type; (c) p type.
对于TCOs薄膜的应用, 电导率是衡量TCOs薄膜的一个重要指标, 主要与载流子浓度和霍尔迁移率有关:

对于TFT的应用, SnO2薄膜由于具有较高的载流子浓度, 很难被栅极电压调控, 因此, 需要降低薄膜内部载流子浓度. 对掺杂元素需要考虑标准电极电位、带隙和低电负性三个因素. 标准电极电位代表金属氧化的程度, 掺杂元素的标准电极电位越低, 越容易减少薄膜内部的氧空位含量; 掺杂元素氧化物的带隙宽度越大, 能够使得施主态能级朝更深能级方向移动的可能性越大; 随着金属和氧原子之间的电负性差值增大, 更加有利于减少薄膜内部的氧空位含量, 相比O元素的电负性, 掺杂元素的电负性越小越合适.
对于p型TSOs的应用, SnO2薄膜需要掺入受主杂质, 实现薄膜从电子型导电向空穴型导电的转变. 掺杂元素需要选择具有低化合价 (< +4) 的阳离子. 然而, 并不是所有化合价低于+4的元素都适合掺杂SnO2. 例如, 第IA主族Li, Na和K元素掺杂, 理论上能够形成深受主态, 但它们趋于占据间隙位形成施主态[27]. 有效的p型掺杂需要满足两个条件: 1) 掺杂浓度较大, 即掺杂剂溶解度高; 2) 容易形成较浅的受主能级[28].
2
2.3.载流子散射机理
在TCOs和TSOs薄膜中, 载流子迁移率是一个关键参数, 其与载流子浓度、温度、晶界等有关[29,30]. 当前, 影响SnO2薄膜迁移率的机制主要有晶界散射和电离杂质散射[31] (图4). 当薄膜结晶度较差且载流子浓度较低时, 晶界散射机制占主导. 因为晶界处存在许多悬挂键, 这些悬挂键捕获电荷形成带电缺陷, 在禁带中形成缺陷态, 从而使晶界处出现弯曲势垒, 阻碍载流子进行流动. 当薄膜结晶性良好且载流子浓度较高时, 电离杂质散射机制为主要影响机制. 这是因为电离的杂质是带电的离子, 相互之间会产生库仑势场, 当载流子从电离杂质附近经过时, 受到库仑势场的影响, 载流子运动方向改变. 此外, 也可通过计算自由载流子的平均自由程 (l) 来判定影响机制, 计算公式如下[32]: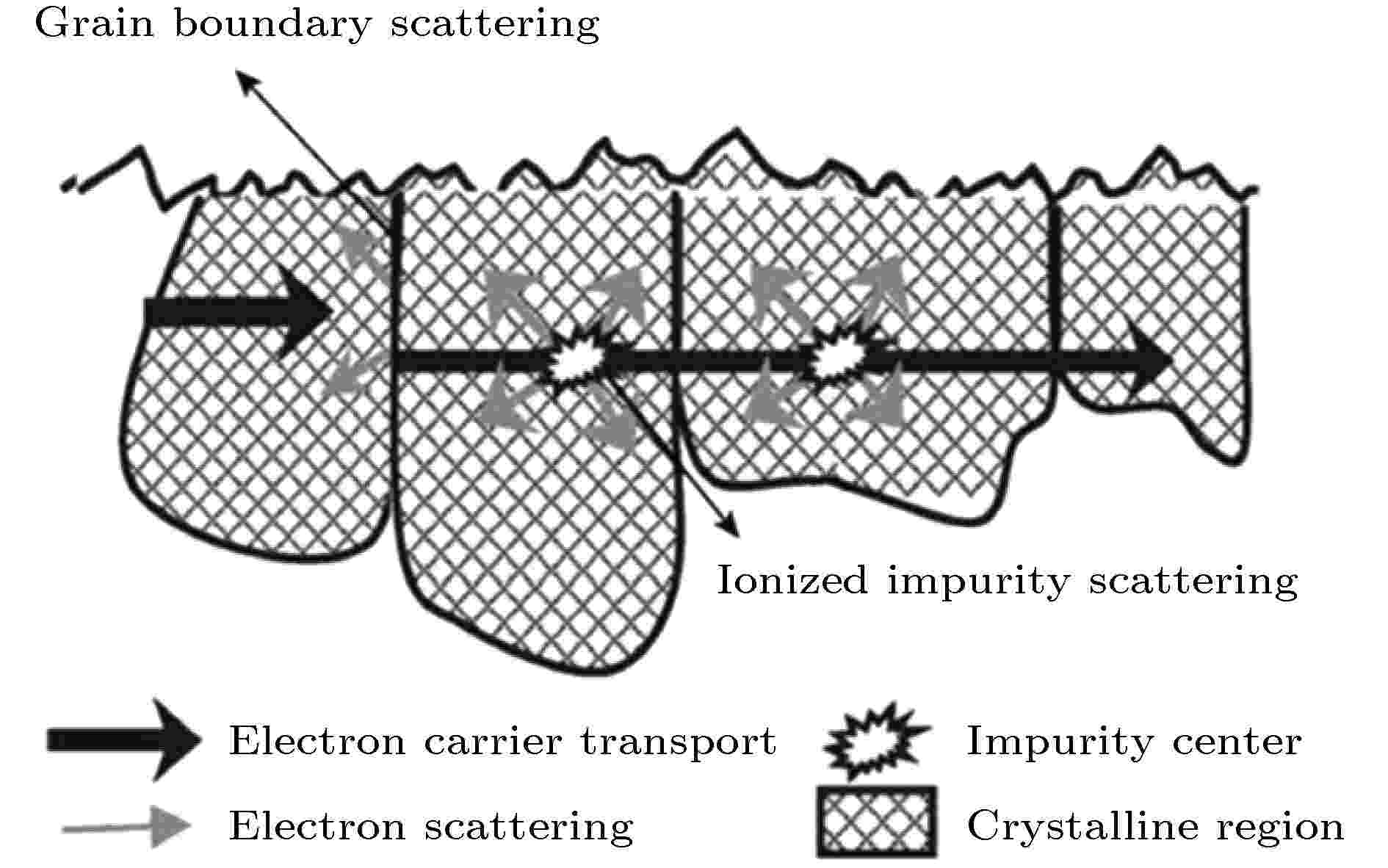
Figure4. The schematic of grain boundary scattering and ionized impurity scattering mechanism[31].
3.1.溶胶-凝胶法原理
溶胶-凝胶法是以无机盐或者金属醇盐作为前驱体, 通过水解、缩聚化学反应, 在溶液中形成稳定的透明溶胶体系, 其中溶胶以胶态金属氧化物/氢氧化物沉淀存在; 接着经过低温加热, 溶胶向凝胶转变, 溶胶中的金属氧化物或者氢氧化物沉淀缓慢聚合, 形成聚合物网络包围着溶剂; 最后, 凝胶在较高的温度下加热, 有机化合物蒸发或者分解, 获得所需材料(图5)[33]. 在整个反应过程中, 主要发生如下反应[34]: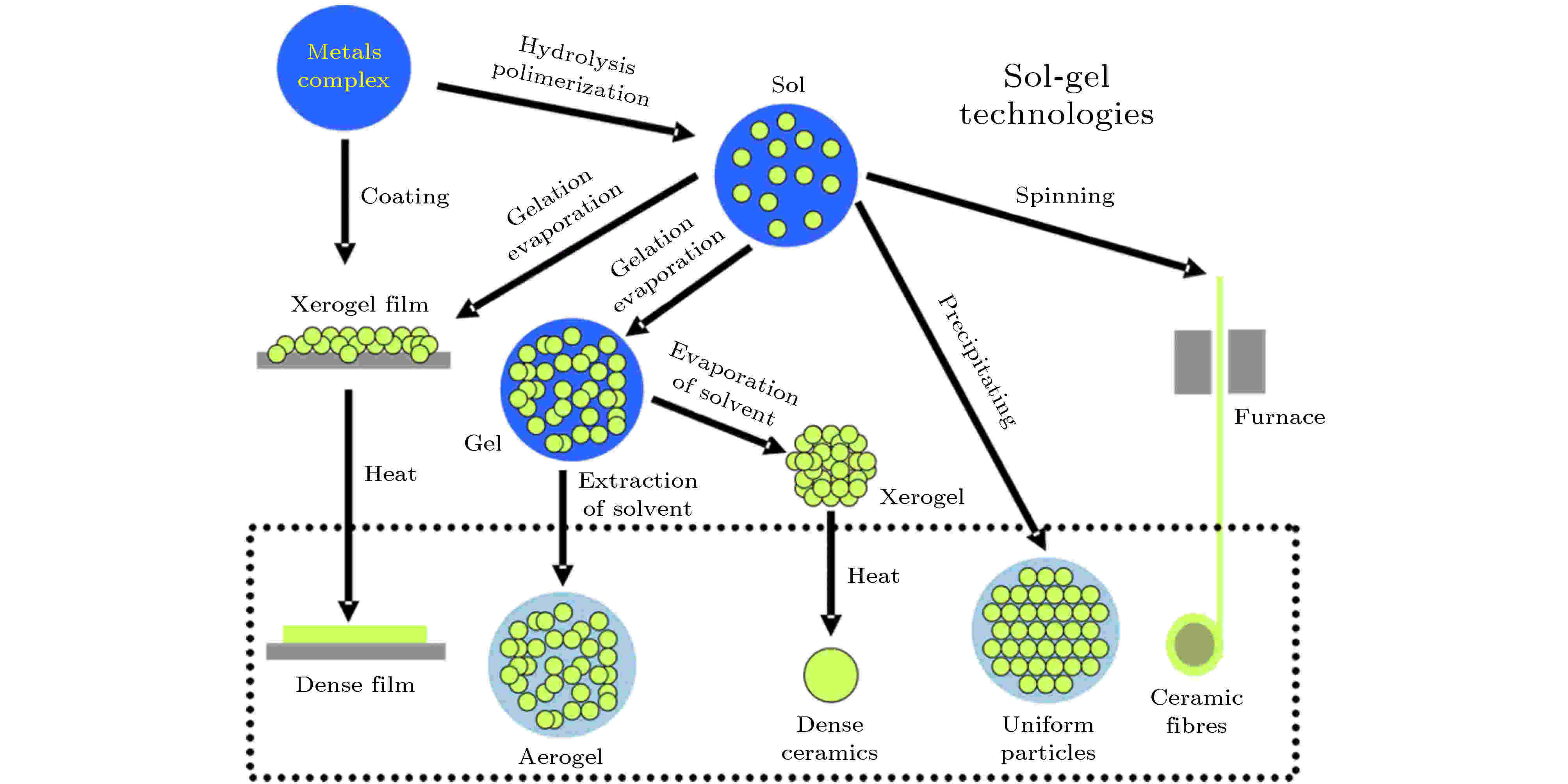
Figure5. The overview of the sol-gel technologies[33].
2
3.2.溶胶-凝胶法制备方法
目前, 基于溶胶-凝胶体系制备薄膜的技术主要有旋涂法、喷雾热解法、浸涂法和喷墨打印法(图6).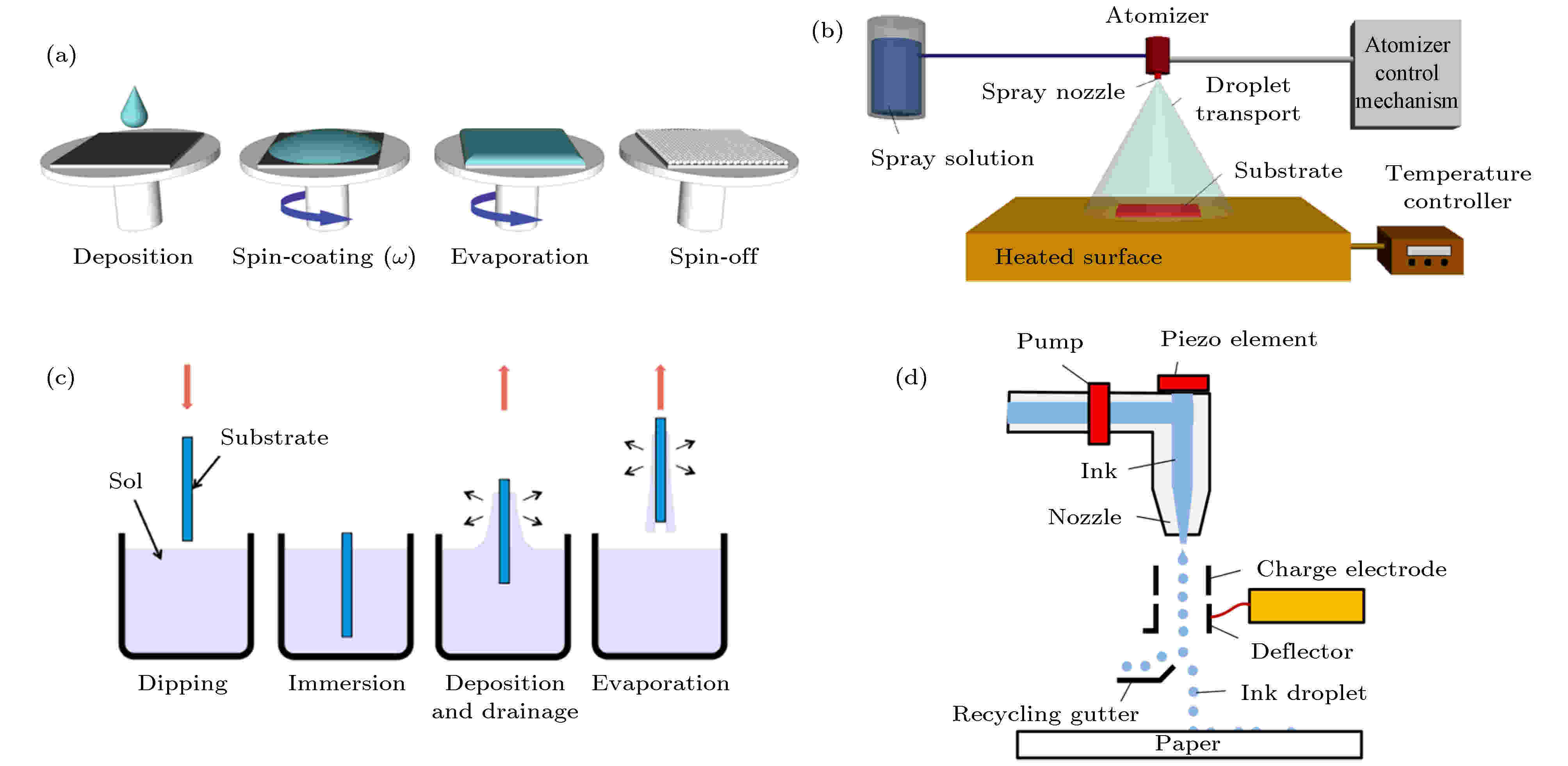
Figure6. The solution-processed fabrication techniques of thin film: (a) Spin coating[35]; (b) spray pyrolysis[36]; (c) dip coating[37]; (d) inkjet print[38].
旋涂法 (spin coating). 在刚性基板上制备氧化物薄膜时, 旋涂法是学术界使用最广泛的技术之一. 其普遍应用的原因在于工艺简单、薄膜均匀、可重复性高、成本低和易于与常规微加工技术兼容. 该技术的原理是利用旋转基板的离心力与溶液的粘力处于平衡状态时在基板上形成均匀薄膜, 旋涂的流程如图6(a) 所示. 通常, 薄膜厚度


喷雾热解法 (spray pyrolysis). 喷雾法是一种大面积非接触式溶液沉积方法. 其原理是利用载气将前驱体溶液转变为气溶胶, 通过喷嘴喷洒到已预加热的基板上, 溶液经过热分解形成薄膜(图6(b)). 喷雾热解法制备薄膜的厚度和质量依赖于溶液喷射的速率、压力、溶液浓度、喷雾时间[40]. 其优点在于工艺简单, 成本低, 可重复性高, 基板图形可多样化. 然而, 该技术也存在缺点: 首先, 对前驱体溶液要求很苛刻, 必须具有低粘度和高挥发性以有助于气化成气溶胶; 其次, 基板温度必须要严格控制, 否则会降低薄膜的均匀性和结晶性; 第三, 该技术制备的薄膜的表面形貌要比旋涂法制备的薄膜更粗糙[41,42].
浸涂法 (dip coating). 浸涂法是一种接触式溶液沉积方法. 其原理是将基板以恒定速度浸没在盛有前驱体的槽中, 很短时间后, 再以恒定速度取出, 溶液将会覆盖在基板表面, 最后通过干燥和热处理去除多余的溶剂, 形成均匀的薄膜(图6(c)). 浸涂法制备薄膜的厚度主要是由基板取出速度、浸没时间、浸没次数、溶液浓度和粘度决定的. 如果基板取出速度选定在剪切速率使系统处于牛顿状态时, 那么薄膜的厚度 (T) 可以通过 Landau-Levich 方程获得.


喷墨打印法 (inkjet printing). 喷墨打印法是一种非接触式的薄膜沉积且图形化的技术, 近些年受到电子行业的广泛关注. 其原理是将前驱体溶液经喷嘴变成细小液滴喷射到基板上形成薄膜(图6(d)). 该技术优势在于不需要考虑基板形状和材质, 薄膜可直接图形化, 数字化控制喷墨, 精确定位, 减少了溶液和材料的浪费, 有效地降低了制造成本和时间. 但它的缺点在于薄膜受到“咖啡环效应”影响, 导致薄膜均匀性差[18]; 喷嘴容易堵塞, 需要浪费大量的墨水清洗喷头和经常性更换喷头[44].
通常, 高电导率是TCOs薄膜的关键性指标. 为了实现SnO2基TCOs薄膜的开发和应用, 高电导率掺杂SnO2薄膜一直是研究热点. 在SnO2薄膜中掺入施主杂质, 能有效增强薄膜的导电性. 根据元素掺杂调控机制, 卤素元素和具有高化合价的阳离子元素适合掺杂 SnO2. 卤素元素有氟 (F)、氯 (Cl)、溴 (Br)、碘 (I) 和砹 (At). 其中, At元素具有极高的放射性且化学活度低, 不宜常规应用; I元素掺杂含量增加会造成溶液浑浊增加, 不适合制备薄膜. Agashe和Major[49]以SnCl4·5H2O和NH4X (X= F, Cl和Br) 为原料, 利用喷雾热解技术制备了卤素元素掺杂的SnO2薄膜, 以研究 F, Cl和Br对薄膜生长速率和结构特性的影响[49]. 在喷雾过程中会发生如下反应:
Element | Electroneg- ativity | BDE of X-H/kJ·mol–1 | Atomic radius/nm | BDE of X-Sn/kJ·mol–1 |
F | 4.0 | 569.68 | 0.42 | 476 |
Cl | 3.0 | 431.36 | 0.79 | 350 |
Br | 2.8 | 366.16 | 1.2 | 337 |
BDE: Bond dissociation energy |
表1不同卤素元素的电负性、X—H和X—Sn键解离能和原子半径[31,50]
Table1.The electronegativity, BDE of X—H and X— Sn, atomic radius for halogen elements[31,50].
Karthick[51]等以SnCl2·2H2O和NH4F作为前驱体溶液, 利用喷雾热解技术制备F掺杂 SnO2 (FTO) 薄膜. 在退火温度350 ℃下, FTO薄膜在可见光范围透明度高达86%, 电阻率低至2.988 × 10–3 Ω–1·cm–1, 载流子浓度为2.62 × 1020 cm–3, 霍尔迁移率为7.96 cm2/(V·s). 他们把FTO薄膜作为透明电极, 应用于染料敏化太阳能电池, 获得了4.02%的光电转换效率. Tran[52]等提出一种绿色环保制备FTO薄膜的方法, 用无毒的SnF2代替有毒的HF或者NH4F, 与SnCl4·5H2O混合作为前驱体, 利用浸涂法制备FTO薄膜, 研究不同F掺杂浓度对SnO2薄膜的结构和电学性能的影响(图7). 随着掺杂SnF2浓度增加, 晶粒尺寸逐渐减小, 但薄膜依然维持多晶结构特性. 载流子浓度随着掺杂SnF2浓度增加, 先增大再减小, 而电阻率和迁移率呈相反的变化. 在SnF2浓度为6 mol%时, 获得最佳品质因数 (FOM), FTO薄膜电阻率低至7 × 10–4 Ω·cm, 载流子浓度高达1.1 × 1021 cm–3, 迁移率为8.1 cm2·V–1·s–1, 在可见光范围透明度高达90%. 此外, 研究人员提出多元共掺杂想法, 如Li + F[53]和P + F[54]共掺杂SnO2, 利用元素之间的协同增强作用, 进一步提升SnO2薄膜的性能.
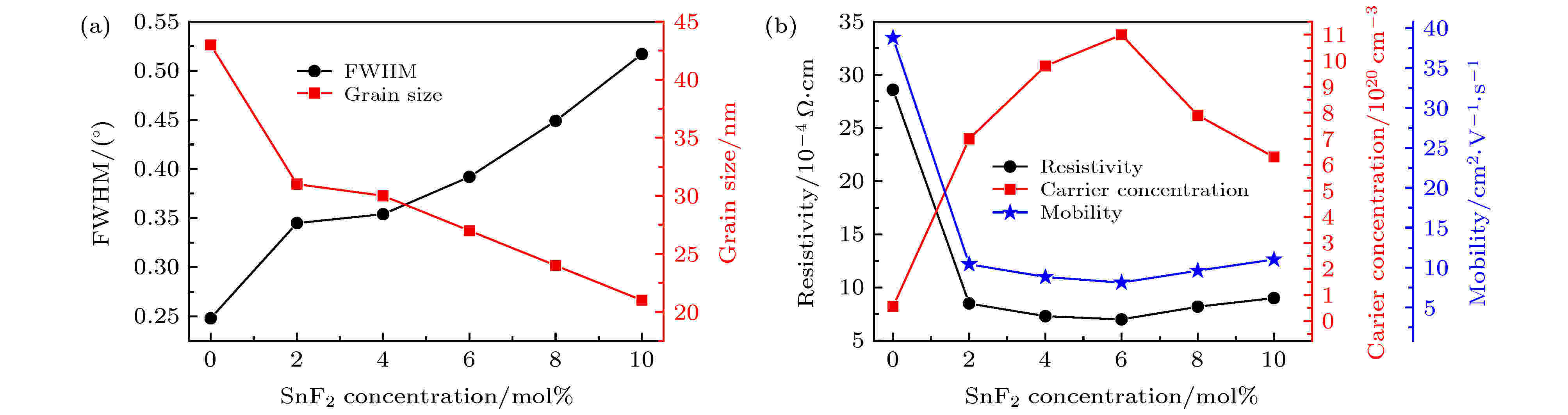
Figure7. (a) Variation of full-width-at-half-maximum and grain size estimated along (1 1 0) diffraction and (b) electrical resistivity, carrier concentration and Hall mobility of the FTO films as a function of SnF2 concentration, 0–10 mol%[52].
高化合价阳离子掺杂元素主要有锑 (Sb)、钽 (Ta)、铌 (Nb)、镨 (Pr) 和钨 (W) 等, 利用它们的高价态离子取代Sn, 可产生额外的载流子, 提高薄膜的电导率. 其中, Sb掺杂SnO2薄膜研究最为广泛. An等[55]以SnCl4·5H2O和SbCl3为原料, 配置Sn/Sb摩尔比为10/1的前驱体溶液, 利用旋涂法制备Sb掺杂SnO2 (ATO) 薄膜, 研究不同旋涂层数ATO薄膜的结构、电学和光学特性. 结果发现, 5层ATO薄膜具有最大的致密度且电学性能最佳, 电阻率低至2.81 × 10–3 Ω·cm, 载流子浓度高达6.37×1021 cm–3, 迁移率为0.347 cm2·V–1·s–1, 在可见光范围透明度为61%. Elangovan等[56]用SnCl4·5H2O和SbCl3配置前驱体溶液, 利用喷雾热解技术制备ATO薄膜, 研究不同Sb掺杂浓度对SnO2薄膜电学性能的影响(图8). 随着Sb掺杂浓度增加, ATO薄膜的方阻和电阻率先减小后增加, 当Sb掺杂量为2 wt%时, ATO薄膜获得最小的方阻和电阻率. 当Sb掺杂含量小于2 wt%时, 晶格中部分Sn4+被Sb5+取代, 造成载流子含量增多, 导致薄膜方阻和电阻率减小; 当Sb掺杂含量高于2 wt%时, 部分Sb5+向Sb3+转变, 导致受主态的产生并伴随着载流子部分减少, 进而导致薄膜方阻和电阻率增大. 随着Sb掺杂浓度增加, ATO薄膜的霍尔迁移率逐渐减小, 载流子浓度逐渐增加, 这归因于ATO薄膜属于简并半导体材料.
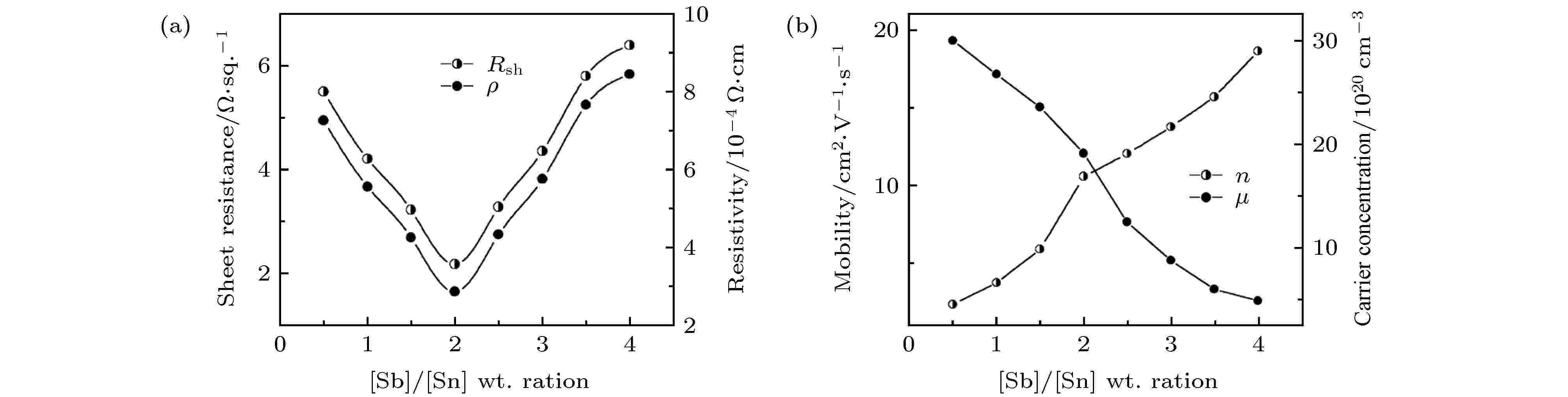
Figure8. The variation of (a) Sheet resistance and resistivity and (b) Hall mobility and carrier concentration for ATO film with different Sb concentrations[56].
与此同时, 研究人员还研究了其他元素掺杂对SnO2薄膜电学性能的影响. 图9展示了在不同掺杂浓度下氧化锡基TCO薄膜 (Ta, Nb, Pr, W掺杂SnO2) 的电学性能变化[57–60]. 它们电阻率的变化趋势大致相同, 当掺杂浓度较低时, 薄膜的电阻率会随着掺杂元素含量增加而降低, 这是由于高价态的掺杂阳离子取代了晶格中的Sn4+离子, 提供额外的载流子, 使得载流子浓度增加, 导致薄膜电阻率降低; 当掺杂浓度较高时, 由于掺杂元素含有多价态, 部分高价态阳离子向低价态阳离子转变, 低价态阳离子取代晶格中的Sn4+离子, 导致受主态的形成和部分载流子损失, 进而导致薄膜电阻率增加.
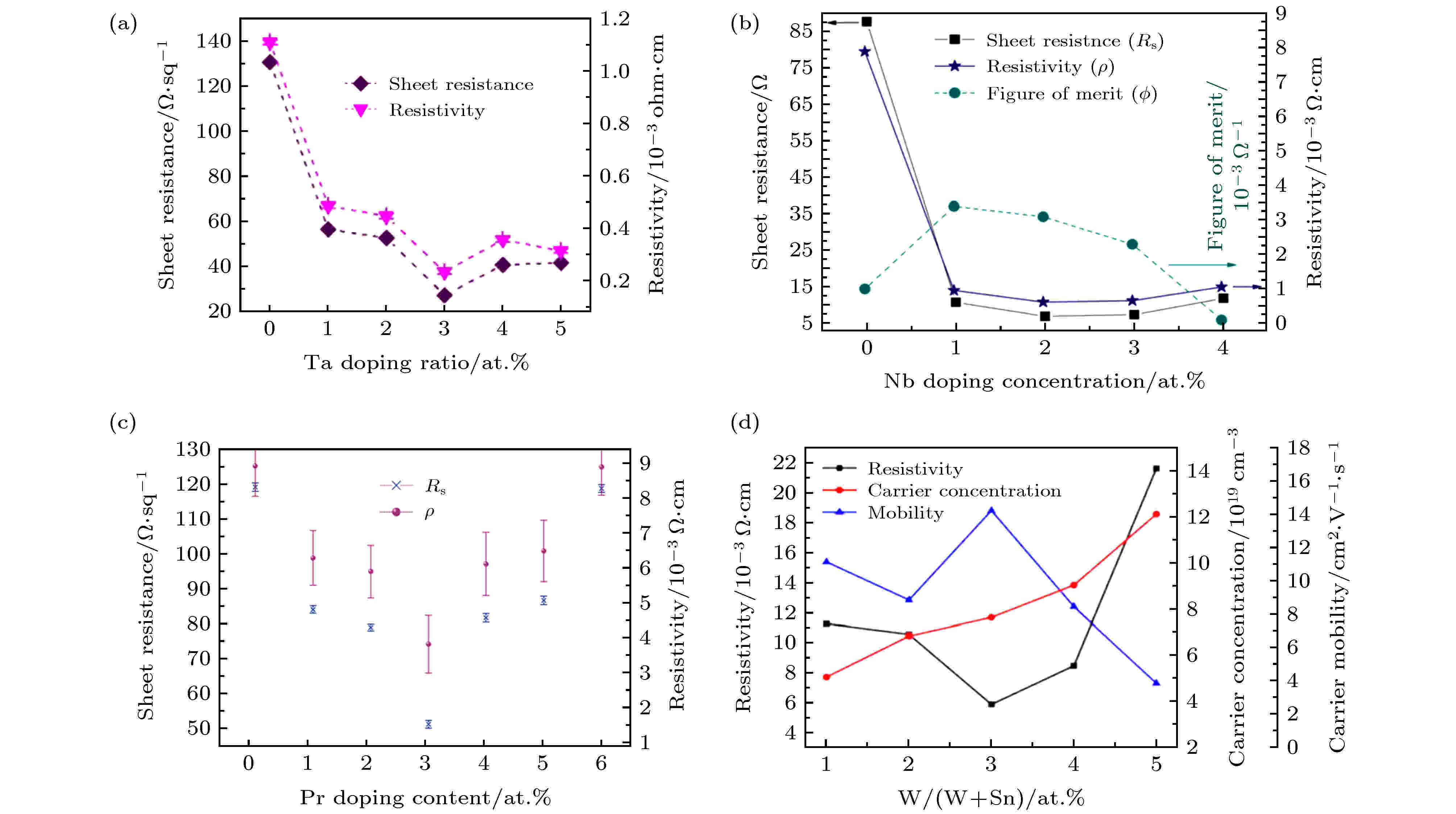
Figure9. The variation of electrical properties for SnO2-based TCOs films with different dopants concentrations: (a) Ta[57]; (b) Nb[58]; (c) Pr[59]; (d) W[60].
除了导电率之外, 光学透过率也是TCOs薄膜的一个重要指标. 通常, 可见光波长范围约在400—800 nm (相对应的光子能量范围为1.6—3.1 eV). TCOs薄膜透射光波长的短波极限由氧化物的能带宽度决定; 而透射光波长的长波极限则与载流子浓度有关, 载流子浓度增大, 入射光子与载流子的相互作用增强, 导致反射损失也增大. 相比导电金属, TCOs薄膜载流子浓度要低的多, 它的长波极限处在红外光区, 可见光能够透过[29]. 众所周知, 薄膜的透明性和导电性是相矛盾的, 而TCOs薄膜既要具有较高的导电率, 也要保证较高的透明度. 因此, TCOs薄膜整体质量的好坏需要评估薄膜的品质因数 (figure of merit, FOM)[52]:

Doping elements | Conductivity/Ω–1·cm–1 | Carrier density /cm–3 | Hall Mobility /cm2·V–1·s–1 | Transmittance/% | Technique | Ref. |
F | 0.33 × 103 | 2.62 × 1020 | 7.96 | 86 | spray pyrolysis | [51] |
F | 1.43 × 103 | 1.10 × 1021 | 8.1 | 90 | dip-coating | [52] |
Li, F | 2.70 × 103 | 5.62 × 1020 | 29.1 | 70 | spray pyrolysis | [53] |
P, F | 4.0 × 105 | 8.30 × 1026 | 0.0032 | 86 | spray pyrolysis | [54] |
Sb | 0.36 × 103 | 6.37 × 1021 | 0.347 | 61 | spin-coating | [55] |
Sb | 3.50 × 103 | 1.68 × 1021 | 12.03 | — | spray pyrolysis | [56] |
Ta | 0.50 × 103 | 1.30 × 1020 | 29.26 | 80 | spray pyrolysis | [57] |
Pr | 0.26 × 103 | 8.70 × 1019 | 18.75 | 80 | spray pyrolysis | [59] |
W | 0.17 × 103 | 7.60 × 1019 | 14.2 | 90 | dip-coating | [60] |
Nb | 0.23 × 103 | 5.00 × 1019 | 25 | 70 | spray pyrolysis | [61] |
表2不同元素掺杂SnO2薄膜的电学参数和透过率
Table2.The electrical parameters and transmittance of SnO2 thin films with different dopants.
对于TFT应用来说, 沟道层中的载流子浓度需要小于1018 cm–3才能实现开关特性[62]. SnO2薄膜的载流子浓度高, 使得SnO2TFT的“关态”电流很大, 甚至很难被关断, 制约着它的发展. 目前, 很多文献报道利用真空工艺及元素掺杂技术已经成功制备出高性能SnO2基TFT, 但对于溶液法工艺的文献报道很少. 近年, 利用溶胶-凝胶法制备的SnO2基TFTs器件及其电学性能如表3所示. Jang等[63]以SnCl2·2H2O作为锡源, 溶于乙醇配制前驱体溶液, 通过旋涂法制备SnO2薄膜, 研究不同退火温度和不同前驱体浓度对器件性能的影响. 退火温度的升高, 不仅促使更多Sn2+离子向Sn4+离子转变, 形成n型导电薄膜, 而且减少了薄膜内部OH基团含量, 获得了高质量薄膜. 当前驱体溶液浓度为0.02 mol/L, 退火温度为500 ℃时, SnO2薄膜厚度最小且获得了最佳的器件性能, 结果如图10(a)所示. Avis等[64]将SnCl2溶于乙腈/乙二醇混合溶液配制浓度为0.167 mol/L的前驱体溶液, 通过旋涂法制备SnO2薄膜. 经过300 ℃退火处理, SnO2薄膜呈非晶态结构(图10(b)). 同时, 作者以高介电常数的氧化铪为栅极绝缘层制备SnO2TFT, 获得了较好的器件性能, 迁移率高达99.16 cm2/Vs, 开关比为1.7 × 108, 亚阈值摆幅低至0.114 V/decade. Liu和Wang[65]考虑到SnO2薄膜内部载流子浓度高, 很难被栅极电压调控, 选用Ga(NO3)3·xH2O作为掺杂剂, 以SnCl2·2H2O作为锡源, 溶于乙二醇单甲醚配制成浓度为0.12 mol/L的前驱体溶液. 以热氧化硅为衬底, 通过旋涂法制备镓掺杂SnO2(GTO) 薄膜, 并采用光刻技术图形化有源层, 制备出GTO TFT(图10(c)). 该器件具有良好的电学性能, 迁移率为4.1 cm2/(V·s), 开关比为6 × 106, 亚阈值摆幅低至0.77 V/decade.
Solute | Dopant | Concentration /mol·L–1 | Substrate | Channel thickness/nm | Annealing temperature /℃ | Mobility /cm2·V–1·s–1 | Ion/Ioff | SS/V·dec–1 | Ref. |
SnCl2·2H2O | — | 0.02 | SiO2/Si | 3.8 | 500 | 11.2 | 6.8 × 106 | 0.78 | [63] |
SnCl2·2H2O | — | 0.167 | HfO2/Mo | 9.2 | 300 | 99.16 | 1.7 × 108 | 0.114 | [64] |
SnCl2·2H2O | Ga(NO3)3 ·xH2O | 0.12 | SiO2/Si | — | 400 | 4.1 | 6.6 × 106 | 0.77 | [65] |
SnCl2·2H2O | — | 0.03 | SiO2/Si | — | 500 | 12.18 | 5 × 107 | 1.17 | [66] |
SnCl2·2H2O | — | 0.1 | ZrO2/ITO | 22 | 400 | 103 | 104—105 | 0.3 | [67] |
C16H30O4Sn | — | 0.5 | Al2O3/ITO | 15 | 350 | 96.4 | 2.2 × 106 | 0.26 | [68] |
表3溶液法制备SnO2基TFTs的电学性能
Table3.Electrical properties of solution-processed SnO2-based TFTs.
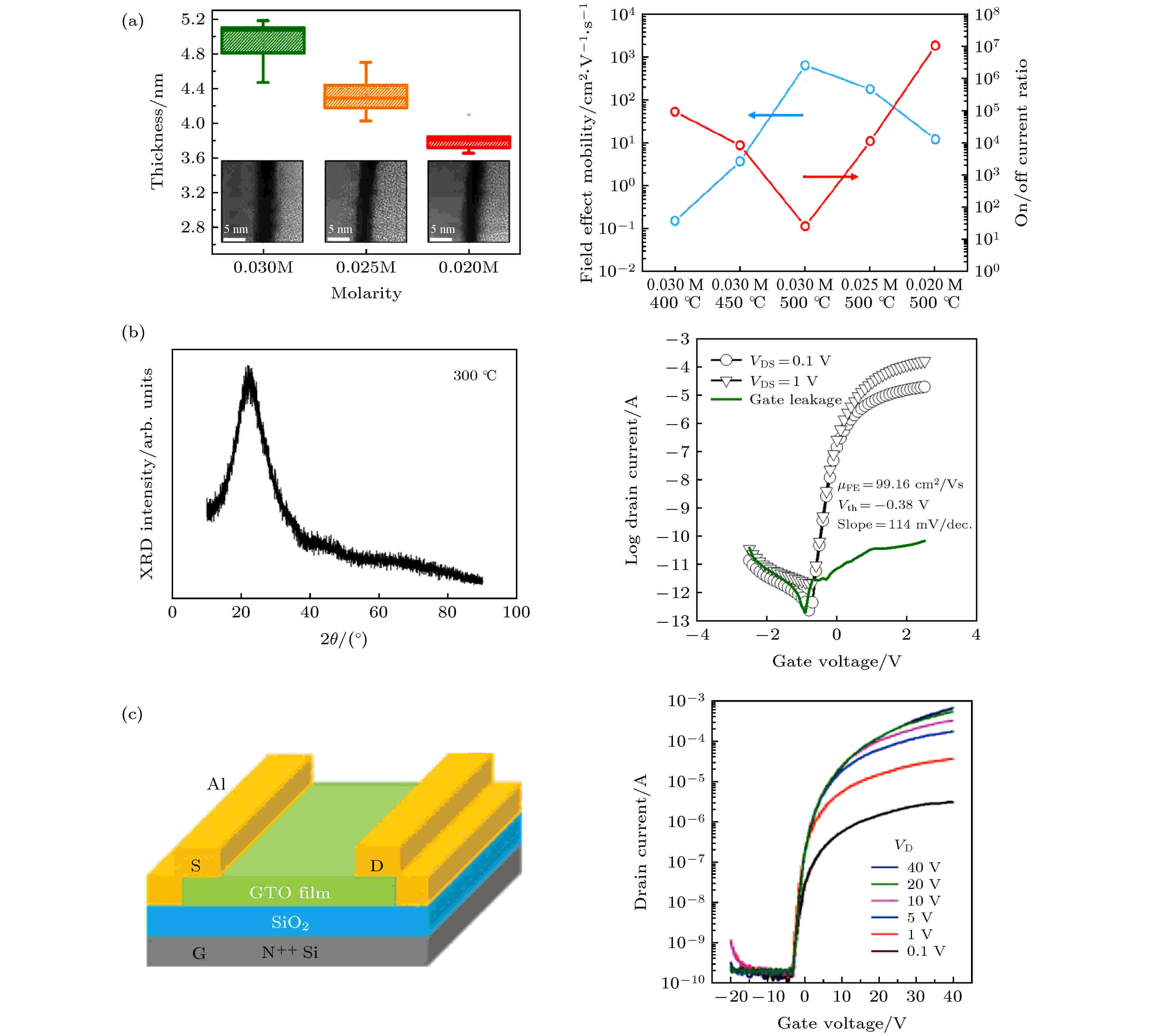
Figure10. (a) The thickness and electrical properties of SnO2 films with different concentration[63]; (b) the XRD pattern of SnO2 film and the transfer characteristic curve of SnO2 TFT[64]; (c) the schematic cross-sectional diagram of Ga doped SnO2 TFT and corresponding transfer characteristic curve[65].
对比列表3中器件的相关信息, 发现一些关键性参数如前驱体溶液浓度、掺杂剂和衬底材料对器件性能影响很大. 如制备纯SnO2TFT时, 前驱体溶液浓度较低, 对配制溶液精准度要求非常高. 此外, 较低浓度的前驱体溶液会导致薄膜成膜性差, 难以制备出较好的器件. 基于上述文献, 总结出以下经验:
1)前驱体. 是锡的醇盐或氯化物以及锡的羧酸盐. 图11(a)展示了锡前驱体的热重分析结果. 锡的醇盐或氯化物的前驱体溶液需要添加足够的乙醇胺以避免沉淀产生; 锡的羧酸前驱体溶液更稳定且对水不敏感, 甚至不需要稳定剂.
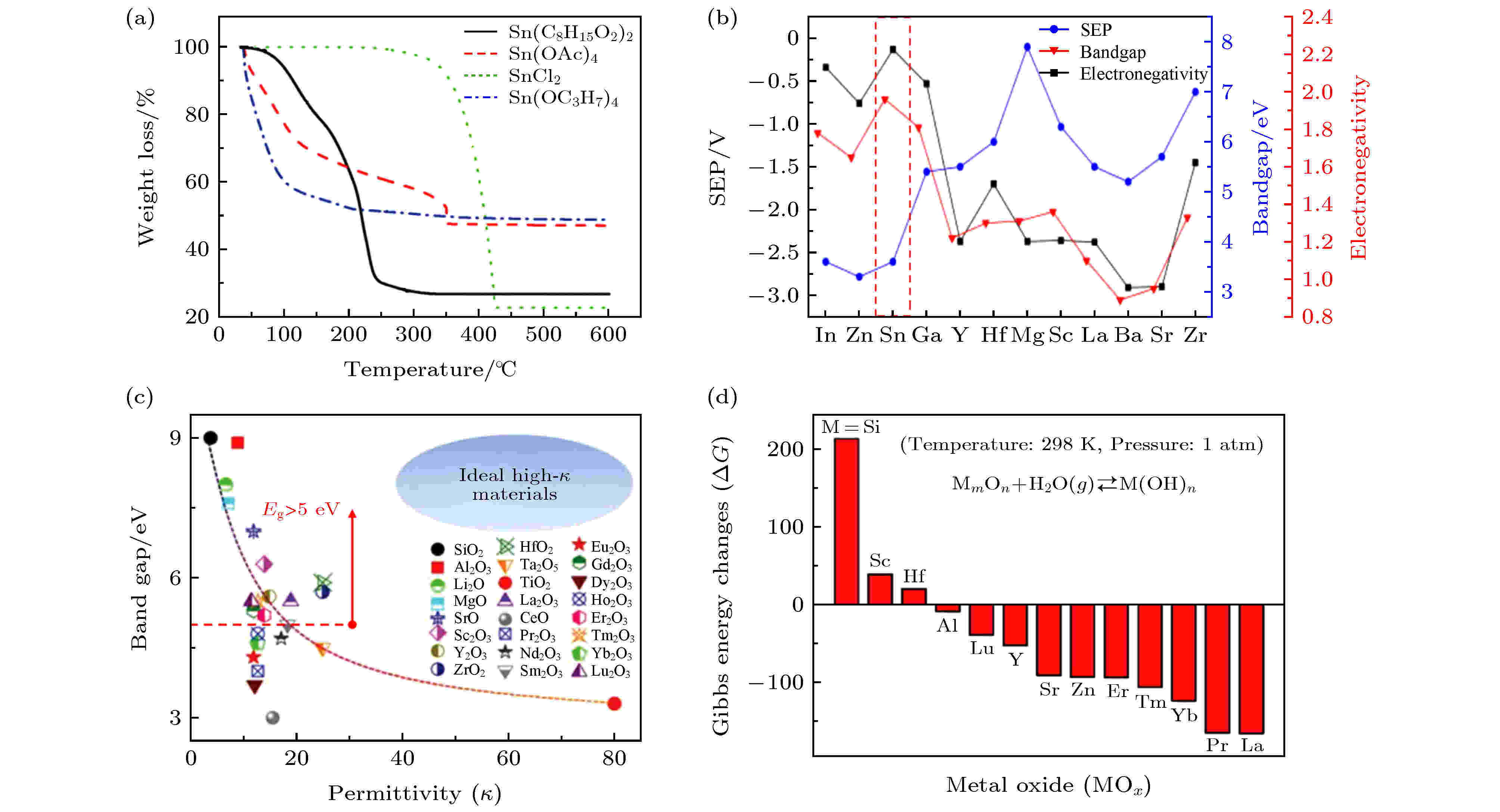
Figure11. (a) Thermogravimetric analyses curves of various Sn precursors[69]; (b) standard electrode potential, bandgap, and electronegativity of In, Zn, Sn, and carrier suppressible atoms[70]; (c) permittivity and band gap for different oxide dielectrics[71]; (d) Gibbs energy changes for moisture absorption reactions in high permittivity oxides under standard conditions[71].
2)掺杂剂. 选择具有低标准电极电位、宽带隙和低电负性的掺杂剂, 如图11(b)所示. 添加掺杂剂可以适当地提高前驱体溶液浓度.
3)栅极绝缘层材料. 优先选择高介电常数的绝缘层材料. 然而并不是所有的高介电常数的绝缘材料都适合于氧化物TFT的制备. 对绝缘层材料的选择有以下两个要求: (1) 光学带隙要大于5 eV, 以确保与半导体有足够大的带偏移量 (> 1 eV), 可以根据图11(c)选择合适的介电层材料; (2) 耐吸湿性. 大量的水蒸气吸附在绝缘层表面会造成器件性能的恶化, 可根据金属氧化物吸湿气反应的吉普斯自由能变化选择合适的介电层材料(图11(d)).
目前, 一些课题组已经成功制备出透明p型导电SnO2基薄膜, 主要以第IIIA主族元素掺杂. Bagheri-Mohagheghi等[74]利用喷雾热解技术制备了Al掺杂SnO2薄膜. 在掺杂浓度较低时, 薄膜保持n型导电; 当掺杂浓度增加到8 at%时, 薄膜导电类型从n型向p型转变. 当掺杂浓度为8.4 at%时, p型Al掺杂SnO2薄膜的电学性能最佳, 此时, 空穴载流子浓度为6.7 × 1018 cm–3, 霍尔迁移率为25.90 cm2/(V·s), 电阻率为3.6 × 10–2 Ω·cm. 随着Al掺杂浓度增加, 薄膜依然维持多晶结构, 主要沿着 (110), (211) 和 (301) 晶面择优生长. Tsay和Liang[75]以Ga(NO3)3·H2O为掺杂剂, 利用旋涂技术制备p型Ga掺杂SnO2薄膜. 当掺杂浓度达到10 at%时, 薄膜内部载流子以空穴为主, 呈现p型导电. 当掺杂浓度为15 at%时, 薄膜空穴载流子浓度达到最大 (1.70 × 1018 cm–3), 霍尔迁移率为6.34 cm2/(V·s), 电阻率为1.6 Ω·cm. 所有薄膜呈四方金红石结构, 沿着 (110), (101) 和 (211) 晶面生长. 但平均晶粒尺寸会随着Ga掺杂浓度增大而逐渐减小, 这是因为Ga进入SnO2晶格会引起晶格扭曲, 导致晶格缺陷和形核中心的产生. Ji等[76]尝试以InCl3·4H2O作为掺杂剂, 制备p型导电的In掺杂SnO2薄膜. 考虑到In掺杂浓度不宜过高, 否则薄膜类似ITO薄膜呈n型导电. 他们采用浸涂技术制备In/Sn比为0.2的In掺杂SnO2薄膜, 通过调整退火温度, 实现薄膜导电类型发生转变. In掺杂SnO2薄膜在退火温度高于450 ℃时, 才能获得p型导电薄膜. 这是因为较低的退火温度不能激发In原子去形成受主态, 薄膜依然保持n型导电. 当高退火温度可以激发In取代Sn形成受主缺陷态时, 薄膜呈p型导电. 当退火温度为500 ℃时, 薄膜获得最佳p型导电性能, 空穴载流子浓度达到1.85 × 1017 cm–3, 霍尔迁移率为1.57 cm2/V s, 电阻率为20.4 Ω·cm. 虽然单独In和Ga掺杂SnO2已经能够实现SnO2薄膜p型导电, 但薄膜的空穴迁移率通常很小. Mao等[77]提出利用In和Ga共掺杂方法来提高SnO2薄膜的空穴载流子迁移率. 他们以SnCl2·2H2O, InCl3·4H2O和GaCl3配制前驱体溶液, 采用喷雾热解技术制备In-Ga掺杂SnO2薄膜. 当退火温度为500 ℃时, 薄膜的空穴迁移率高达39.2 cm2/(V·s), 载流子浓度达到9.5 × 1017 cm–3, 电阻率为0.17 Ω·cm. 除此之外, 一些课题组还利用其他低价态阳离子 (如Mg2+, Fe3+等) 掺杂SnO2, 成功制备出p型导电薄膜, 薄膜电学性能如表4所示.
Solute | Dopant | Resistivity /Ω·cm | Carrier density/cm–3 | Hall Mobility /cm2·V–1·s–1 | Bandgap/eV | Technique | Ref. |
SnCl2·2H2O | AlCl3 | 3.6 × 10–2 | 6.7 × 1018 | 25.90 | 4.11 | spray pyrolysis | [74] |
SnCl2·2H2O | Ga(NO3)3·H2O | 1.6 | 1.70 × 1018 | 6.34 | 3.83 | spin-coating | [75] |
SnCl2·2H2O | InCl3·4H2O | 20.4 | 1.85 × 1017 | 1.57 | 3.8 | dip-coating | [76] |
SnCl2·2H2O | InCl3·4H2O, GaCl3 | 0.17 | 9.5 × 1017 | 39.2 | 3.38 | spray pyrolysis | [77] |
SnCl2·2H2O | FeCl3·6H2O | 660 | 1.4 × 1015 | 6.75 | 3.75 | dip-coating | [78] |
SnCl2·2H2O | MgCl2·6H2O | 2.5 × 104 | 1014 | 1.6 | 3.73 | spin-coating | [79] |
SnCl2·2H2O | MnCl2 | 359.1 | 6.72 × 1014 | 6.14 | 3.85 | dip-coating | [80] |
SnCl2·2H2O | CoCl2·6H2O | 140 | 1.47 × 1015 | 8.25 | 3.81 | spin-coating | [81] |
表4溶液法制备p型SnO2基薄膜的电学性能
Table4.Electrical properties of solution-processed p type SnO2-based films.
对比上述p型导电的SnO2基薄膜的光学带隙, 发现它们的光学带隙普遍较大 (Eg > 3.0 eV), 在可见光区间依然保持较高的透明度. 但薄膜的光学带隙随着掺杂浓度的增加而降低 (图12), 这与施主掺杂的结果相反. 从结构上来说, 掺杂浓度的增加, 加剧SnO2薄膜晶格结构紊乱, 导致晶粒变小, 晶界增多, 使得薄膜的透过率降低; 从微观上来说, 掺杂离子的局域态的d轨道电子与导带或者价带中电子发生sp-d轨道交换作用. 其中, s-d和p-d的轨道交换作用对导带边和价带边分别造成负和正校正, 进而导致薄膜光学带隙的降低[78].
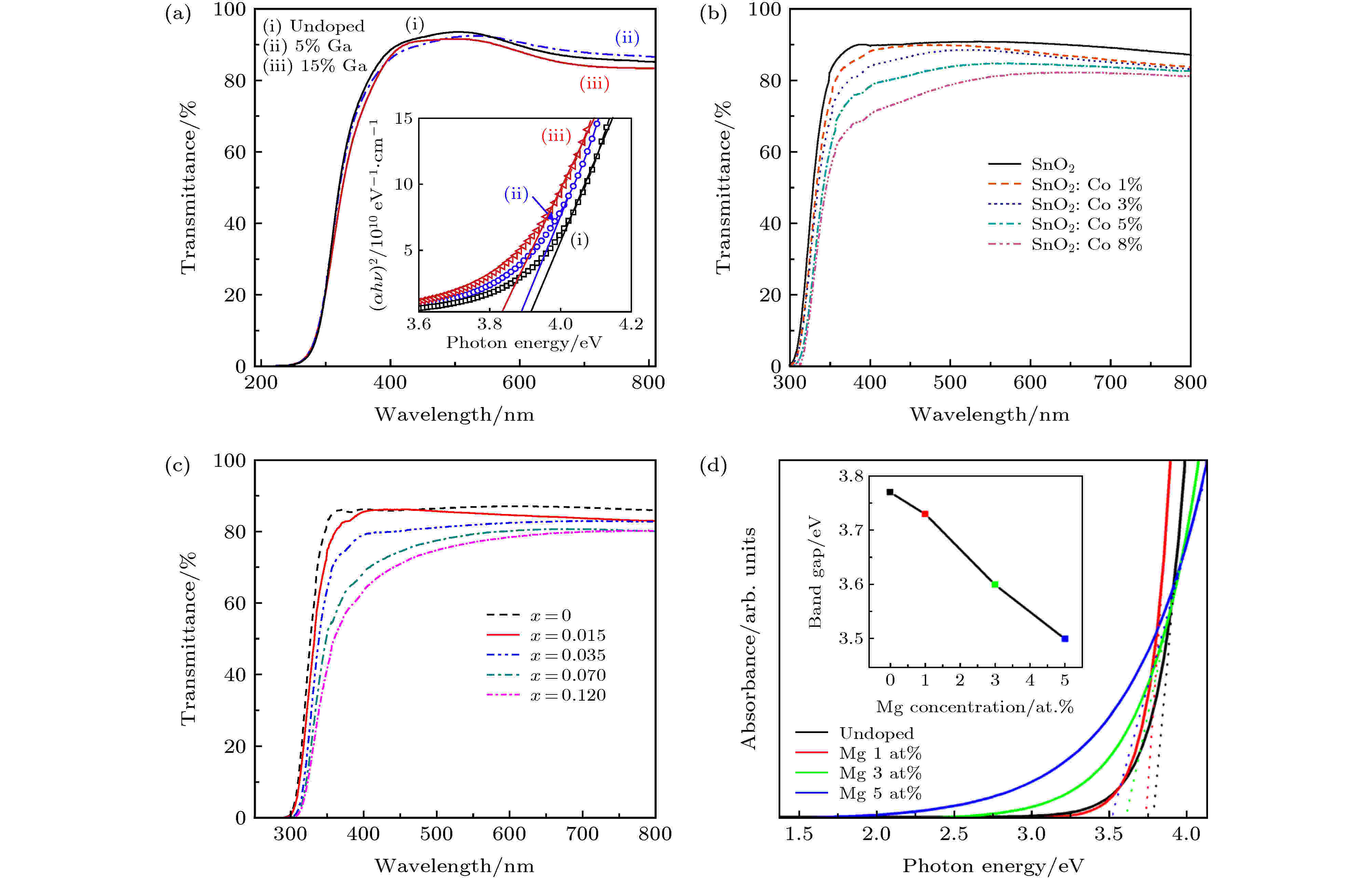
Figure12. The transmittance spectra of SnO2-based films with different dopant concentration: (a) Ga doped SnO2[75]; (b) Co doped SnO2[81]; (c) Mn doped SnO2[80]; (d) the optical absorption spectra of Mg-doped SnO2 thin films with different concentration[79].
目前, 大部分文章报道通过溶液法制备出了p型导电SnO2基薄膜, 但对其薄膜的应用很少提到. 由于p型导电SnO2基薄膜的载流子浓度较低, 电阻率较大, 所以不适于TCO薄膜方面的应用. 而与n型半导体薄膜结合制备p-n结, 对溶液法制备的p型导电SnO2基薄膜是一种简单、直接且快速的应用(图13). Tsay等[75]利用p型导电的Ga掺杂SnO2薄膜与n型导电的Al掺杂ZnO半导体薄膜搭配制备出p-n结. 其I-V曲线具有单向导通特性, 正向开启电压低至0.65 V, 反向击穿电压高至–3 V. Ye等[82]通过旋涂法分别制备出p型导电的Ga掺杂SnO2薄膜和n型导电的Si掺杂SnO2薄膜, 并将两种薄膜搭配制备出p-n结, 该p-n结具有较好的单向导通特性且反向耐击穿性强.
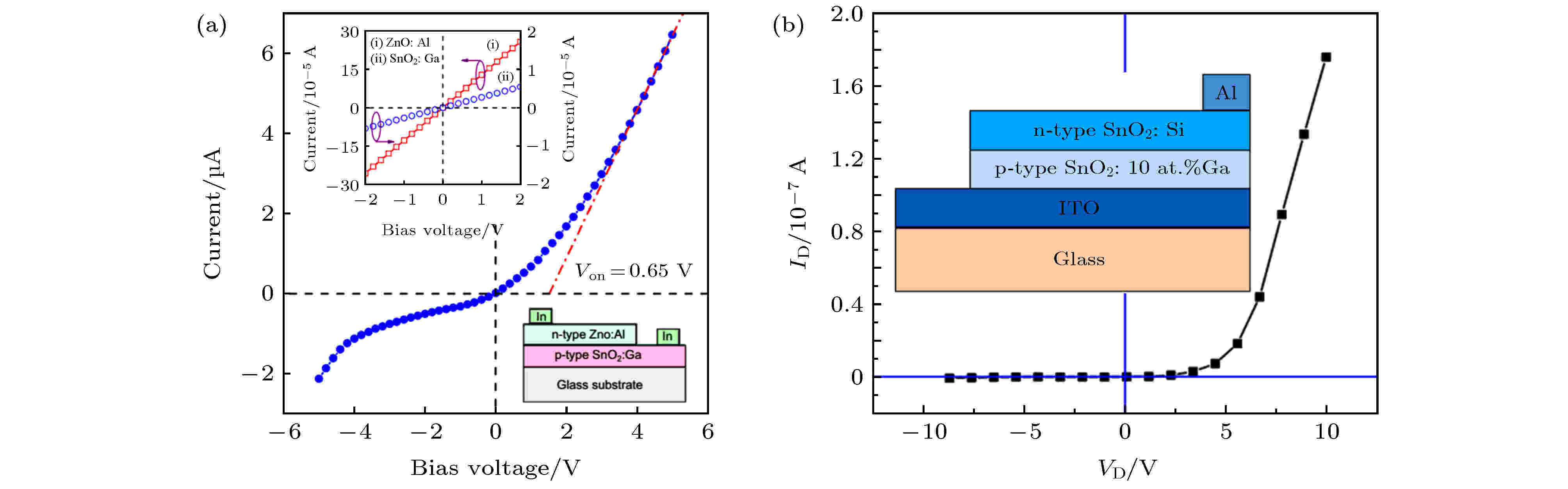
Figure13. The current–voltage characteristics curve of p-n heterojunction: (a) SnO2:Ga/ZnO:Al[75]; SnO2:Ga/SnO2:Si[82].
1)对于TCOs薄膜应用, n型SnO2基TCOs薄膜的电导率还无法与ITO薄膜相媲美; p型SnO2基薄膜的电阻率很大, 处于半导体范围, 距实现p型TCOs薄膜的应用还有很长的路要走. 多元共掺杂通过元素之间的协同增强作用可以调控和改善薄膜的性能, 是未来SnO2基TCOs薄膜的研究热点之一.
2)对于TFT器件应用, n型SnO2基TFTs已经被成功制备出, 但器件的可重复性和稳定性较差. 因此, 未来开发出可重复性和高稳定性的n型SnO2基TFTs至关重要.
3) p型SnO2基TSOs薄膜具有多晶结构, 薄膜均匀性差, 不利于大面积器件应用. 制备出非晶结构的p型SnO2基TSOs薄膜是未来研究热点之一.
4)目前溶胶-凝胶法制备SnO2基薄膜主要通过喷雾热解技术和旋涂技术, 薄膜均匀性较差, 不利于图形化. 由于喷墨打印技术可直接对薄膜图形化, 避免溶液和材料的浪费, 是未来SnO2基薄膜制备的重要研究方向.
5)柔性电子器件成为当下研究的热点, 而SnO2基薄膜需要较高的工艺温度, 难以与柔性基板相兼容. 要实现SnO2基薄膜在柔性电子器件中的应用, 低温工艺的开发十分关键.