全文HTML
--> --> -->在粉末气力加注过程中, 粉末供给、流化、输送主要靠粉末供给系统实现. 粉末供给系统可以通过控制活塞推送粉末的速度实现粉末燃料的定量供给[8-10]. 就活塞的驱动方式而言, 粉末供给系统可分为气压驱动活塞式和电机驱动活塞式[11-13]. 电机驱动的力量小且系统集成度低, 一般应用于小流量供给系统, 因此目前粉末发动机中多采用气压驱动活塞式供粉系统. 事实上, 在粉末发动机领域[14,15], 不管是电机驱动式还是气压驱动式供粉系统, 粉末燃料供给均是通过气体流化输送实现的, 因此粉末燃料的气力加注也可以通过粉末供给系统实现.
在粉末供给系统工作过程中, 储箱内的粉末一般为松装状态[16], 研究者们常认为粉箱内的粉末堆积密度保持不变[17], 采用活塞移动速度来表征粉末质量流率, 因此可以通过调节活塞移动速度来实现粉末流量调节. 实际上, 当活塞推送粉末时, 活塞会对粉末产生挤压作用[18,19], 改变粉末堆积密度, 因此为了实现粉末气力加注精确控制必须弄清粉末的压缩机理, 考虑活塞挤压作用对粉末流量的影响.
气固两相流的分离方式有惯性分离法, 旋风分离法、过滤法和静电分离法等. 惯性分离法[20]的分离效率较低, 通常用于气固两相的预分离阶段. 旋风分离法[21]可分离10—20 μm颗粒, 分离效率可达97%—99%, 但旋风分离设备较大. 过滤分离是最有效的分离方法[22], 其分离效率可达99%以上. 静电法[23]会使得粉末燃料或粉末氧化剂带电, 安全性较差. Loftus等[8]在研究Al/AP粉末火箭发动机时, 通过在粉末推进储箱端盖上方开设排气口, 首次成功地采用气力输送的方式将粉末推进剂从一个独立的储箱输送至粉末发动机推进剂储箱中, 但他们并未对粉末颗粒的气力加注特性进行详细研究.
为了揭示粉末颗粒气力加注特性与储箱内粉末堆积密度的动态变化规律, 本研究将搭建粉末供给系统与设计粉末收集装置来开展粉末颗粒气力加注实验, 研究加注位置、流化气量对粉末颗粒气力加注特性的影响, 同时采用电子天平对粉末加注质量进行实时测量, 通过对比天平测量值与活塞位移换算值, 分析活塞挤压作用对储箱内粉末堆积密度的影响规律.
2.1.粉末样品
微小粉末推进剂弥散至空气中可能会发生闪爆[24], 考虑到粉末推进剂的流化输送特性与其化学性质无关, 所以在进行粉末发动机点火试验前, 常采用粒径相近的Al2O3粉末颗粒替代粉末推进剂进行供粉系统参数标定[17], 因此本研究将采用Al2O3粉末颗粒(上海水田材料科技公司)替代粉末推进剂开展粉末气力加注实验.在粉末发动机中, 为保证粉末推进剂的点火、燃烧性能, 实际使用的粉末推进剂粒径一般为1—100 μm, 同时为提高粉末推进剂的装填率, 通常会将不同粒径的颗粒按一定比例混合[25,26], 但由于不同粒径的颗粒惯性和随流性不同, 采用气力加注方式可能会对集粉箱内的粉末粒径分布均匀性造成影响. 因此为了研究气力加注方式对级配粉末粒径分布均匀性的影响, 本研究使用的Al2O3粉末颗粒标称粒径分别为5 μm和100 μm, 其激光粒度分析结果如图1所示. 在图1中, D[4, 3]和D[3, 2]分别代表颗粒的体积平均直径和表面积平均直径, 它们之间的差异越大, 粒度分布越宽. 另外, d(0.1)、d(0.5)和d(0.9) 分别为粒度仪的10值、50值和90值(达到该百分比的粒度), 即粒径按从小到大排列, 10%, 50% 和90% 处颗粒的粒径大小, 因而d(0.5)值就代表中间粒径的大小.
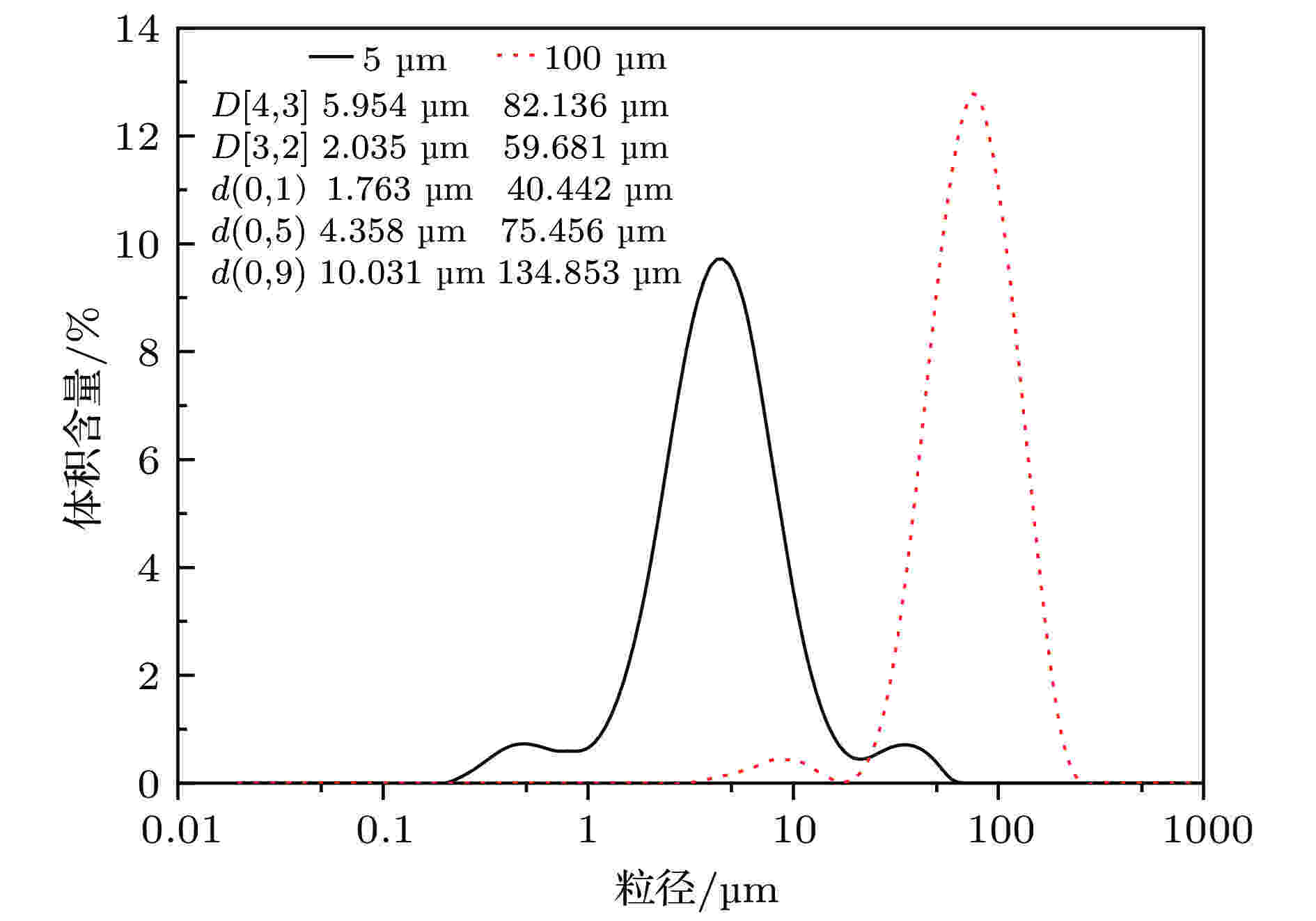
Figure1. Particle size distribution of single powder sample
实验前对两种粉末样品的松装密度进行了测量, 得到5 μm和100 μm的Al2O3松装密度分别为0.896 g/cm3和0.969 g/cm3. 由于Al2O3的理论密度为3.97 g/cm3, 因此5 μm和100 μm的Al2O3的装填率分别为22.6%和24.4%, 根据粉末致密装填理论[27], 5 μm和100 μm的Al2O3的理论最佳质量配比为1∶1.43, 但由于5 μm的Al2O3流化性较差, 含量过高会导致供粉系统流化输送困难, 因此本研究采用的5 μm和100 μm的Al2O3质量配比为1∶4. 实验前还采用JHX50型双运动混合机对两种粉末进行充分混合, 同时为验证所得混合粉末的均匀性, 从混合粉中随机取三个样品进行粒度分析, 结果如图2所示. 可以看出混合粉具有较好的粒径分布均匀性. 最终测量得到Al2O3混合粉样品的松装密度为1.031 g/cm3.
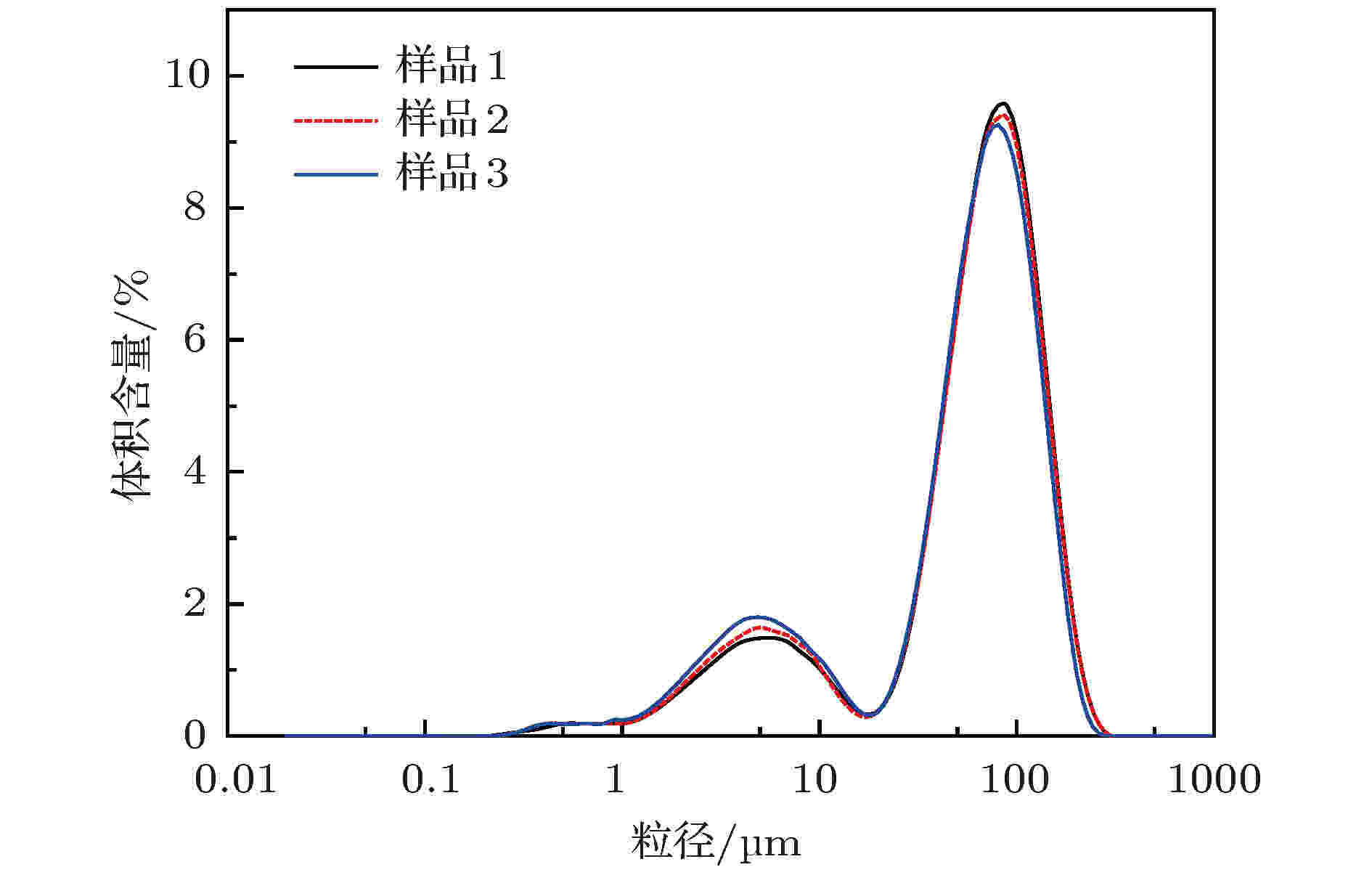
Figure2. Particle size distribution of mixed powder sample
2
2.2.实验系统
粉末气力加注实验系统如图3所示. 该系统由气源, 粉末供给系统, 测控系统和集粉箱等组成. 气源主要用于给粉末供给系统提供驱动气和流化气. 粉末供给系统的作用是将粉末颗粒以气固两相流的形式输送至集粉箱中, 该系统的详细组成如图4所示. 测试系统可以采集驱动腔、流化腔和集粉箱的压强, 活塞位移以及集粉箱内收集的粉末质量. 控制系统用于控制实验系统的启动和关闭.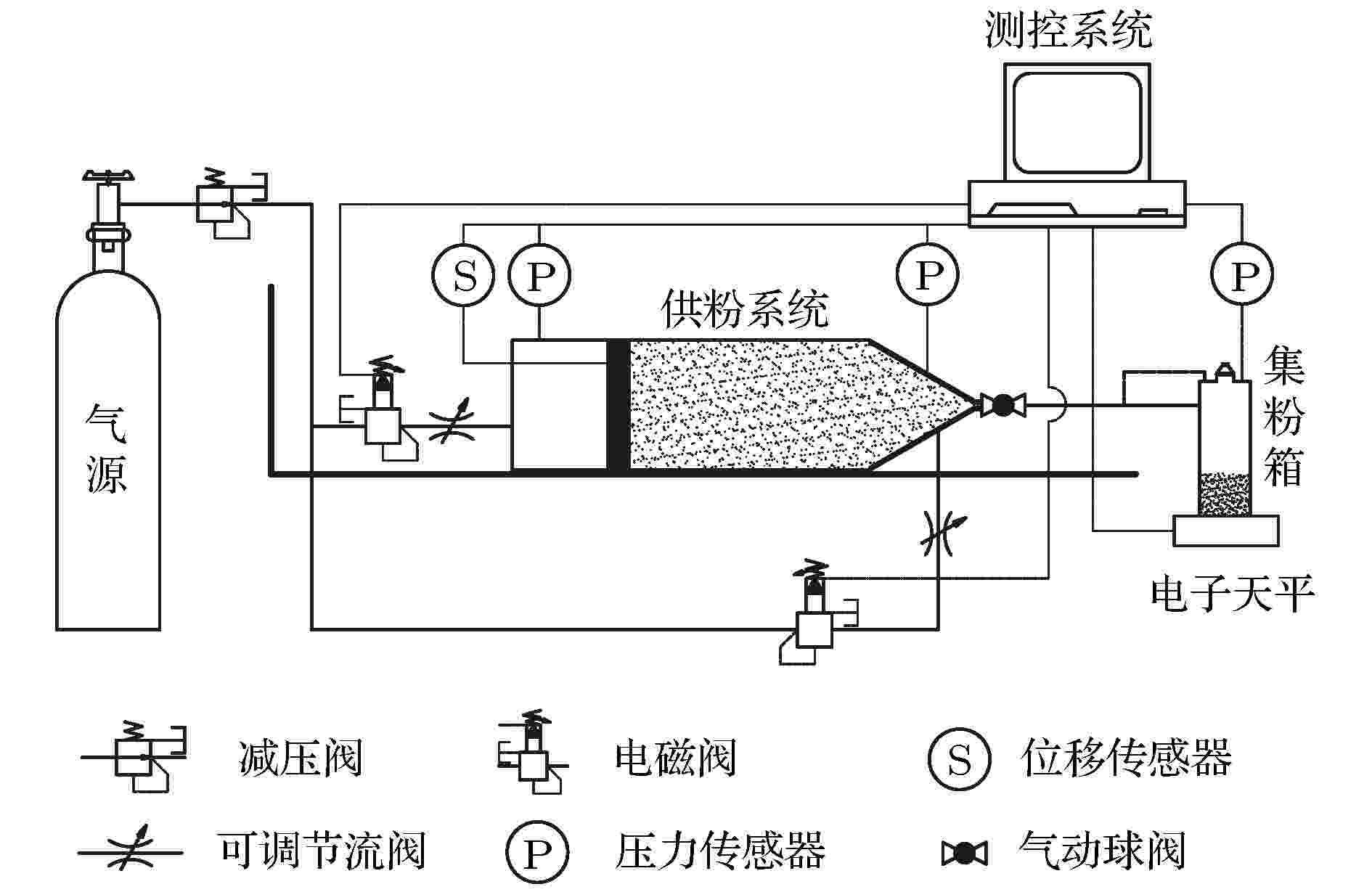
Figure3. Powder pneumatic filling system.
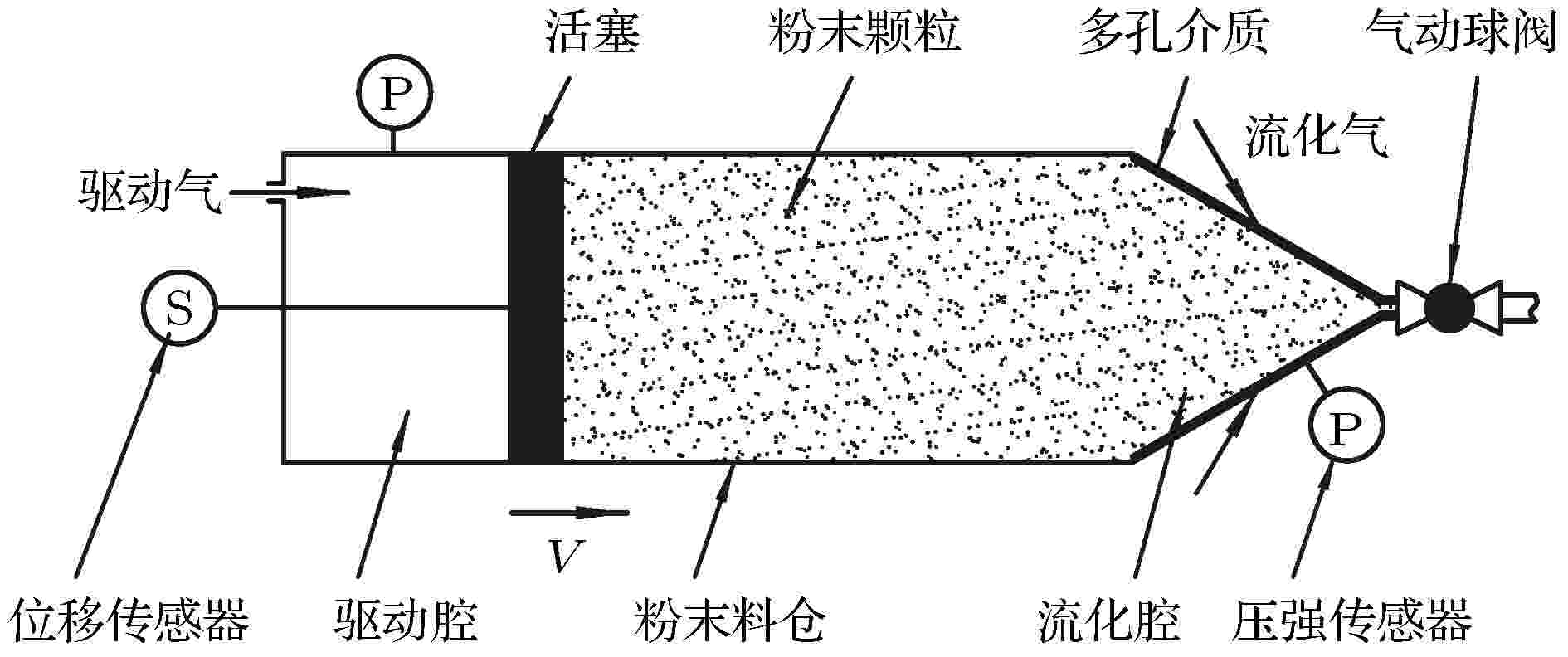
Figure4. Powder feeding system.
本研究采用的集粉箱如图5所示. 该装置主要包含粉箱筒体、端盖、压强传感器、进粉接口、排气口、筛网. 集粉箱设计直径为80 mm, 深度为256 mm, 根据混合粉末样品松装密度, 得到集粉箱的理论最大装粉量约为1286 g. 集粉箱进粉口共两个, 一个位于筒体壁面切向位置, 另一个在端盖垂直位置, 可研究不同加注位置对粉末加注的影响. 筛网共有两层, 布置在端盖排气通道中, 筛网目数为10000, 对应孔径为1.3 μm, 可防止小粒径粉末颗粒逸出集粉箱, 提高加注率.
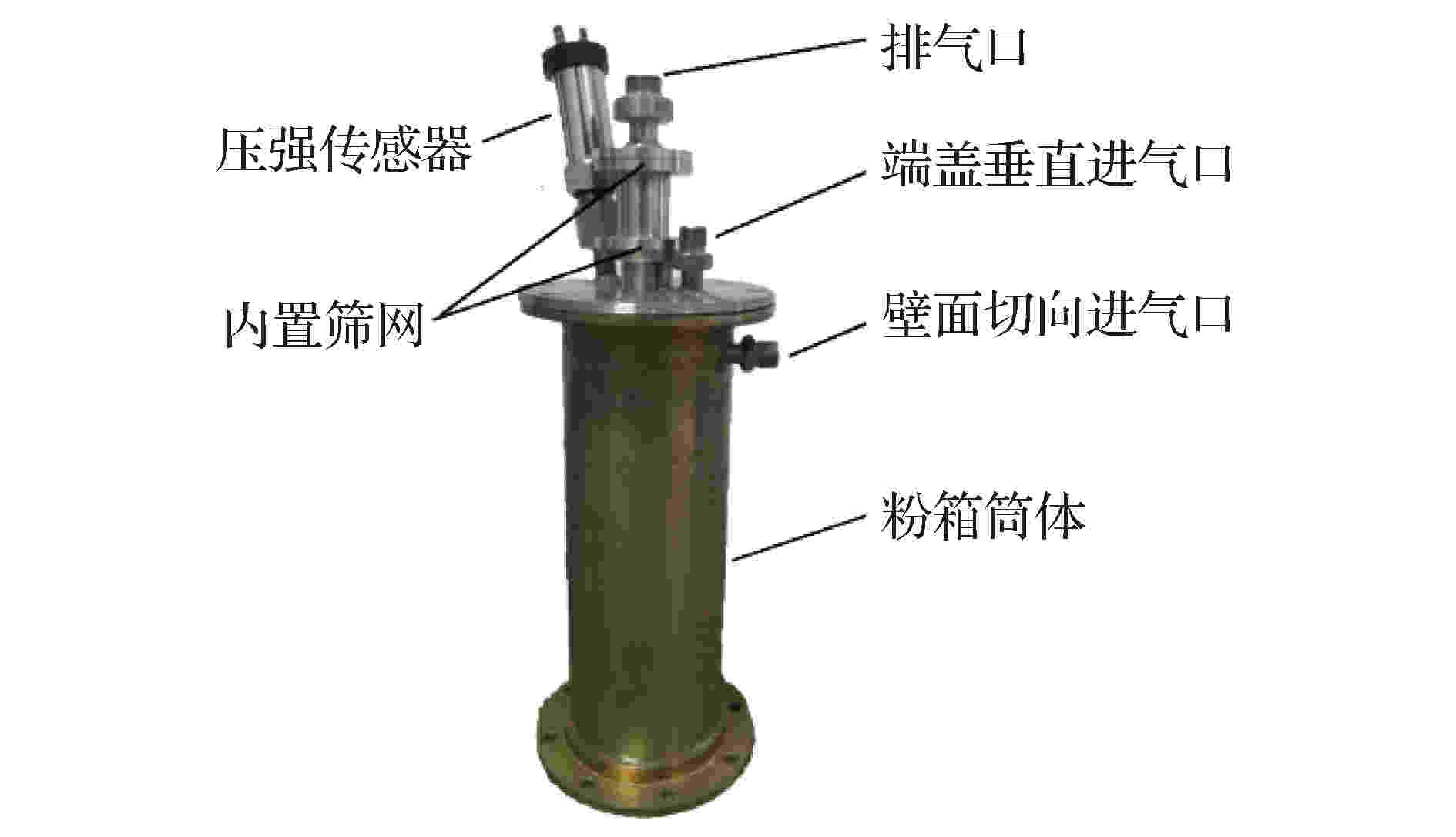
Figure5. Powder collection box.
粉末气力加注实验的工作过程为: 首先, 将减压阀和可调节流阀调节至设定开度, 然后同时打开驱动气路、流化气路的电磁阀和气动球阀. 此时, 活塞在驱动气的作用下将储箱中的粉末颗粒推送至流化腔, 而粉末颗粒在流化气的作用下形成气固两相流经气动球阀输送至集粉箱中, 最后气固两相流在集粉箱中分离, 气体从排气口逸出, 粉末则留在集粉箱中. 活塞位移信号可以用来监测粉末气力加注过程, 当活塞不在向前移动时, 认为加注过程结束, 关闭加注系统. 实验结束后, 将集粉箱打开, 测量内部装粉高度.
2
2.3.实验工况
实验工况如表1所示. 本研究以工况1#为基准, 通过对比研究工况1#和工况2#以获得流化气体的质量流量对粉末气力加注特性的影响. 其次, 通过对比研究工况1#和工况3#以获得集粉箱加注位置对粉末气力加注特性的影响. 表1中所有工况的驱动腔、流化腔和集粉箱的初始压力相同.工况 | 加注位置 | 流化气量/(g·s–1) |
1# | 壁面切向 | 3.2 |
2# | 壁面切向 | 6.4 |
3# | 垂直端盖 | 3.2 |
表1实验工况
Table1.Experiment conditions.
3.1.粉末气力加注稳定性分析
不同加注方式下粉末气力加注系统工作过程中的参数变化如图6所示. 当工况1#采用小流化气量壁面切向加注方式时, 如图6(a)所示, 驱动腔、流化腔和集粉箱内压强均不断上升, 活塞位移速率也在不断下降, 而在工况2#大流化气量切向加注条件下, 如图6(b)所示, 驱动腔、流化腔和集粉箱压强在上升一段时间后趋于稳定, 活塞位移速率较平稳, 说明在壁面切向加注方式下, 大流化气量有利于加注系统工作稳定. 这是因为粉末样品中小粒径颗粒在进入到集粉箱后会随着气流向集粉箱出口流动, 但由于筛网的阻隔, 小粒径颗粒会附着在筛网上, 导致集粉箱出口等效通径减小, 压强上升. 而当流化气量较大时, 由于气流湍动能较强, 小粒径粉末不易附着在筛网上, 集粉箱出口等效通径能够保持恒定, 因此集粉箱腔内压力状态相对稳定.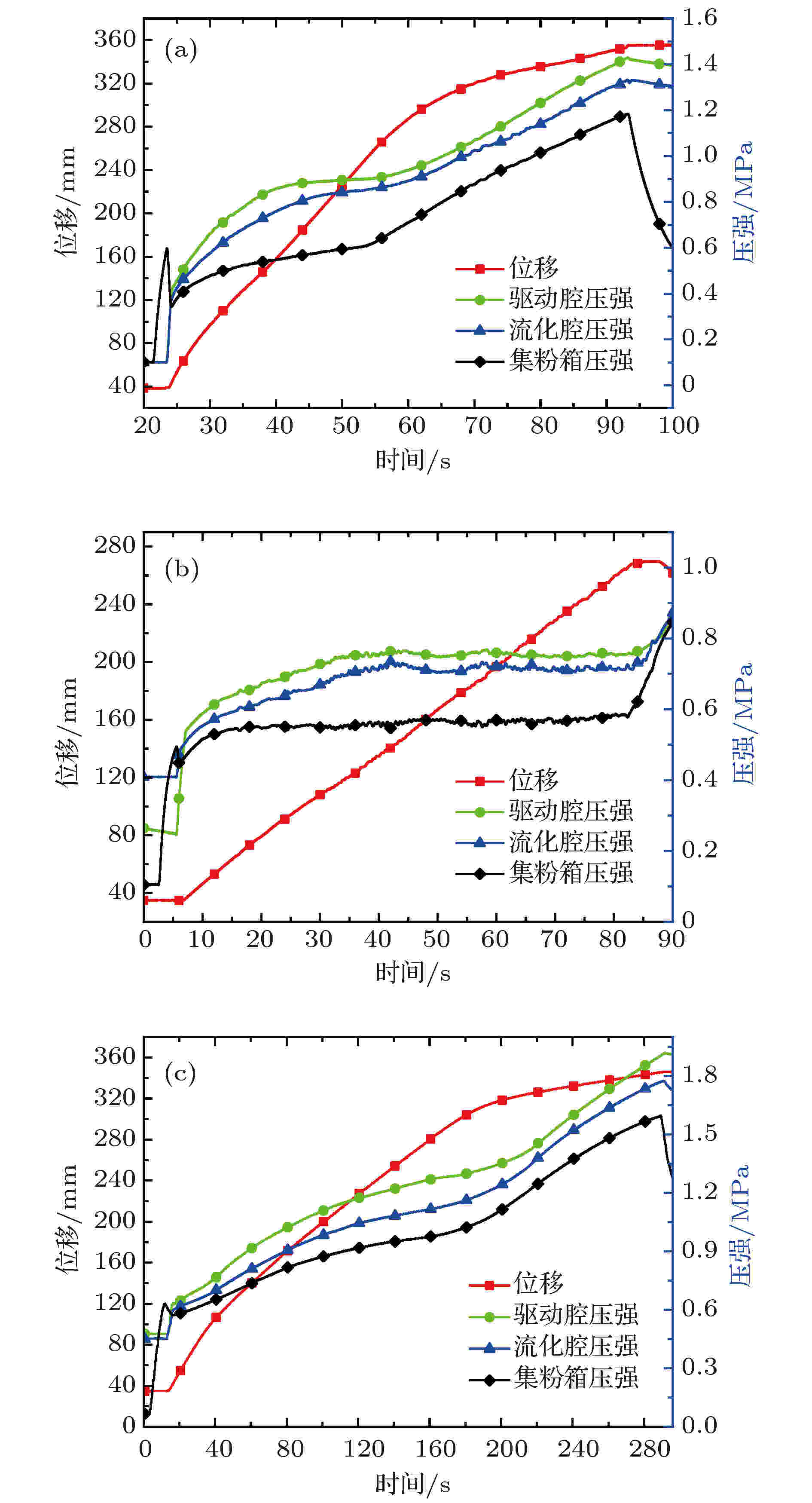
Figure6. Working parameters of different tests: (a) Test 1#; (b) test 2#; (c) test 3#
当工况3#采用小流化气量垂直端盖进气方式时, 如图6(c)所示, 供粉系统的参数变化规律基本与工况1#类似, 但在工况3#条件下, 驱动腔、流化腔和集粉箱压强的上升幅度更大, 且集粉箱压强在加注初始阶段便迅速上升, 导致活塞的移动速度更慢, 这是因为采用壁面切向加注方式会产生类似旋风分离器的气固两相分离效果[21], 使得粉末不易跟随气流向集粉箱排气通道运动, 降低了筛网的堵塞程度, 所以工况1#的集粉箱压强在初始加注阶段的上升幅度较低, 活塞移动速度更快, 但随着集粉箱内装粉高度增加, 壁面切向加注方式的气固分离效果减弱, 系统压强迅速上升, 致使活塞速度减慢.
2
3.2.粉末加注率及均匀性分析
粉末加注性能参数主要包括粉末加注时间(







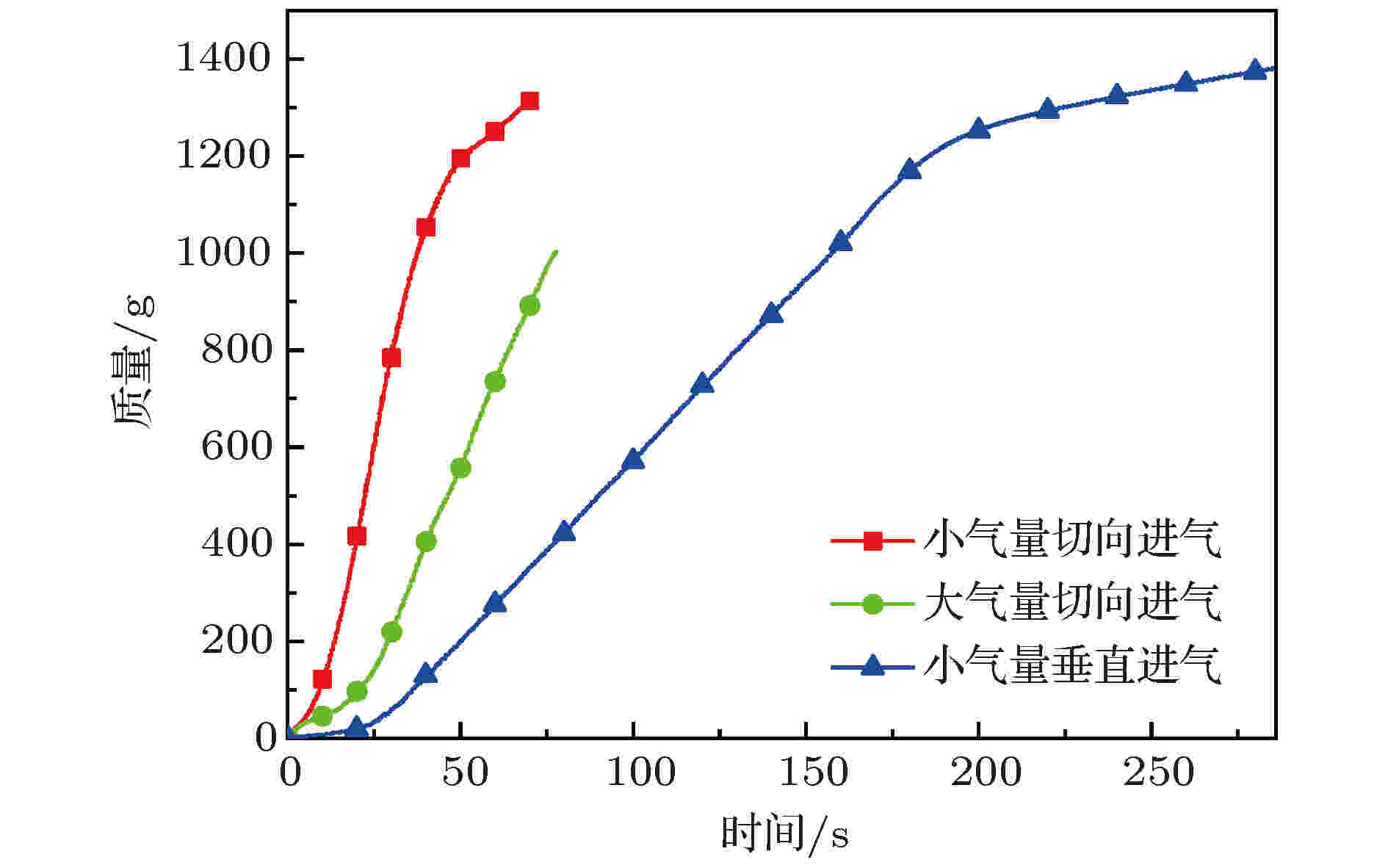
Figure7. Mass curves measured by electronic balance at different filling methods.
工况 | $t{\rm{/s}}$ | $m{\rm{/g}}$ | ${\bar {\dot m}}/({\rm{g}} \cdot {{\rm{s}}^{ - 1}}{\rm{)}}$ | $H{\rm{/mm}}$ | ${\rho _{\rm{c}}}{\rm{/(g}} \cdot {\rm{c}}{{\rm{m}}^{{\rm{ - 3}}}}{\rm{)}}$ | $\eta $ |
1# | 70 | 1316 | 18.8 | 240.5 | 1.101 | 93.9% |
2# | 77 | 1002 | 13 | 174.3 | 1.142 | 68.1% |
3# | 286 | 1381 | 4.83 | 244.5 | 1.127 | 95.5% |
表2部分加注性能参数
Table2.Some performance parameters of powder filling
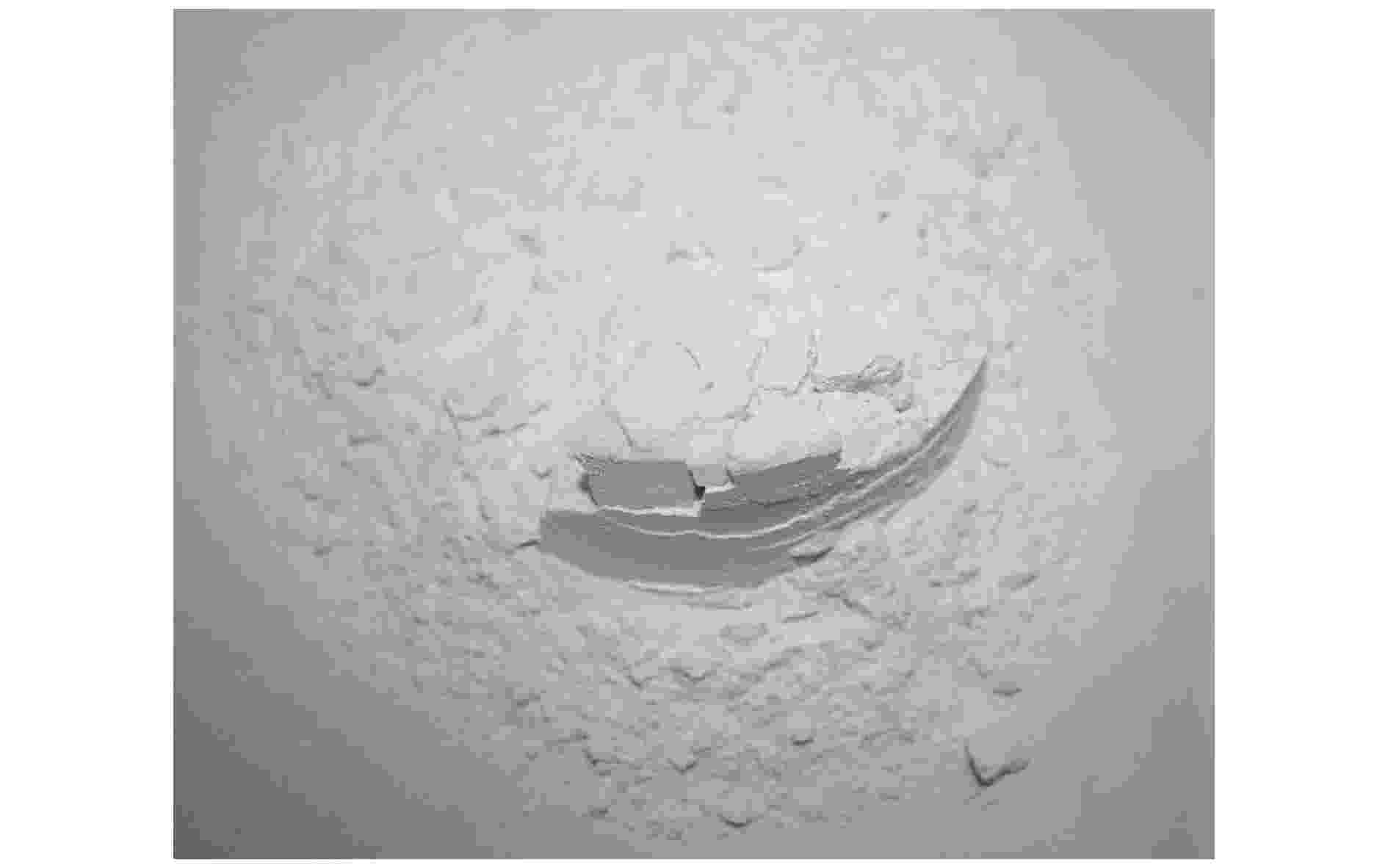
Figure8. Compacted powder in collection box.
在上述三种加注方式中, 大流化气量壁面切向加注过程最稳定, 但其粉末加注总量却是最低的, 这是因为随着加注实验的进行, 集粉箱中的粉量在持续增加, 当其装粉高度到达一定值后, 这种速度较大的气固两相流反而更容易造成筛网堵塞, 导致加注实验终止. 虽然小流化气量垂直端盖加注方式的加注量最大, 但加注时间却是最长的, 这是因为垂直端面进入到集粉箱中的气固两相流会直接撞击在集粉箱底部并反弹, 因此粉末会随气流向集粉箱排气口流动, 造成筛网堵塞, 导致集粉箱压强迅速升高, 减缓粉末加注速度.
在集粉箱不同深度位置取样并进行粒度分析, 获得样本粒径分布与加注高度之间的关系如图9所示. 可见, 工况1#中各样本粒径分布差异较小, 各层粉末粒度分布较为均匀, 而工况3#的粒度分布均匀性最差, 说明切向加注位置对粉末粒度分布的影响较小, 对比工况2#和工况3#发现加注位置对粉末粒度分布均匀性的影响大于流化气量, 因此为保证粉末加注的均匀性宜采用小流化气量切向加注方式.
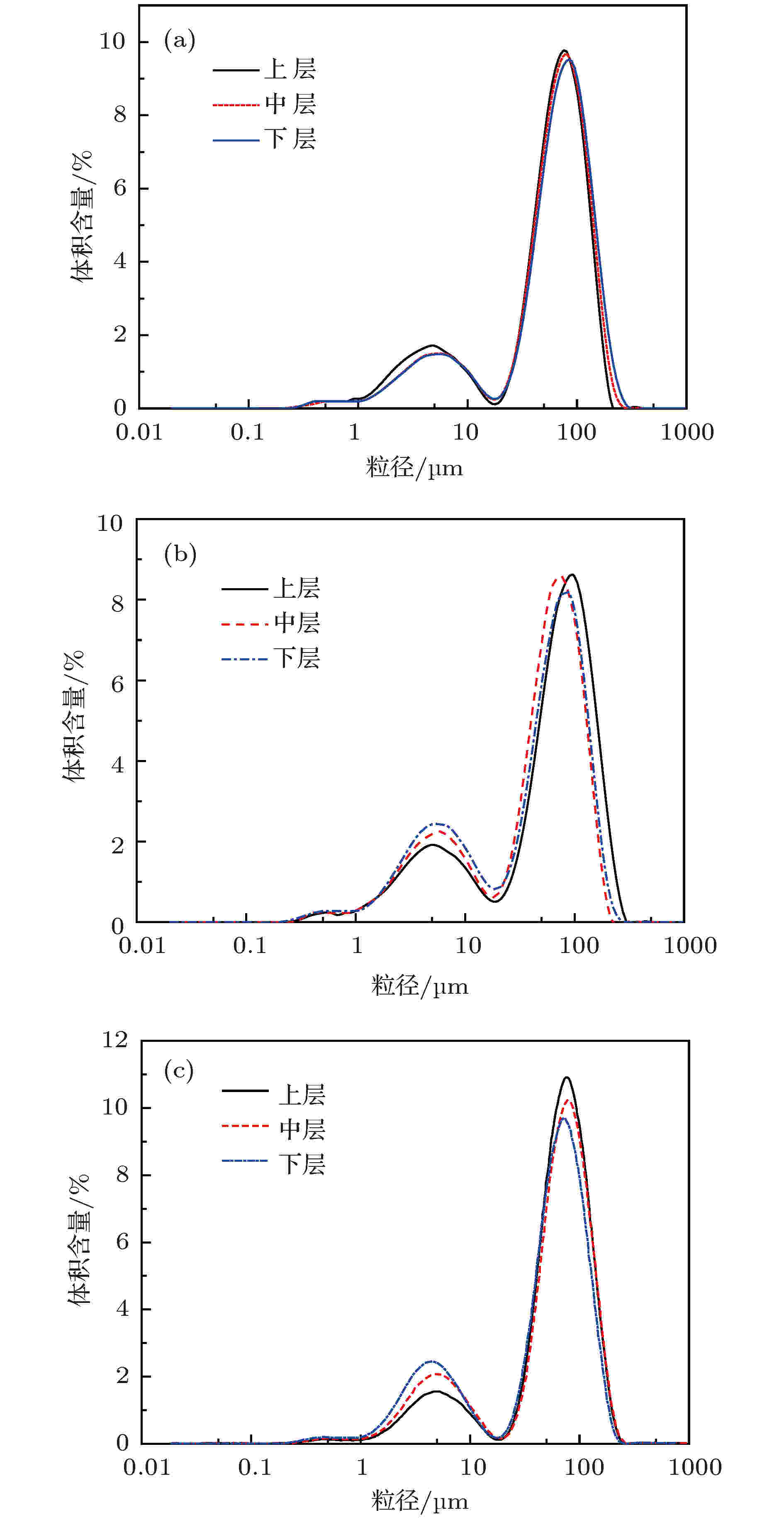
Figure9. Uniformity of powder in collection box: (a) Test 1#; (b) test 2#; (c) test 3#.
2
3.3.储箱内粉末堆积密度动态变化分析
为证明储箱内粉末堆积密度存在动态变化过程, 本研究先采用文献[17]中的供粉质量计算方法, 将实验工况1#获得的活塞位移曲线换算成质量曲线, 再将其与天平测量曲线进行对比, 如图10所示. 可以发现, 活塞位移换算得到的粉末质量始终大于天平实际测量得到的粉末质量, 两者的质量之差先快速增加后缓慢降低, 同时在加注初始阶段, 活塞换算质量曲线曲率逐渐降低, 而天平测量质量曲线曲率却逐渐增大, 说明活塞位移换算的累积量与真实值具有较大差别, 活塞挤压作用会对储箱内粉末的堆积密度造成较大影响.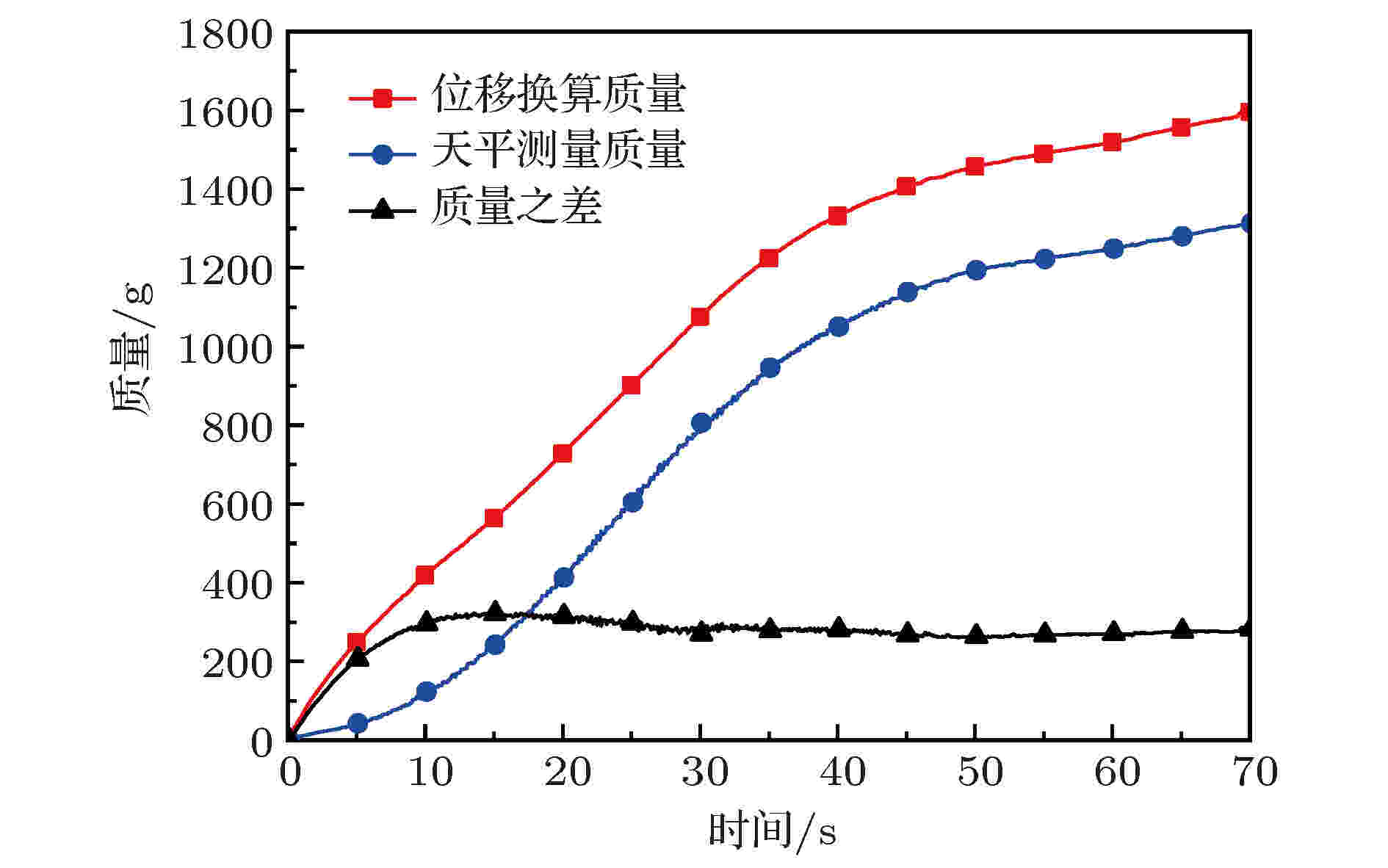
Figure10. Mass curves converted by position displacement and measured by electronic balance.
根据上述分析, 可假设活塞位移









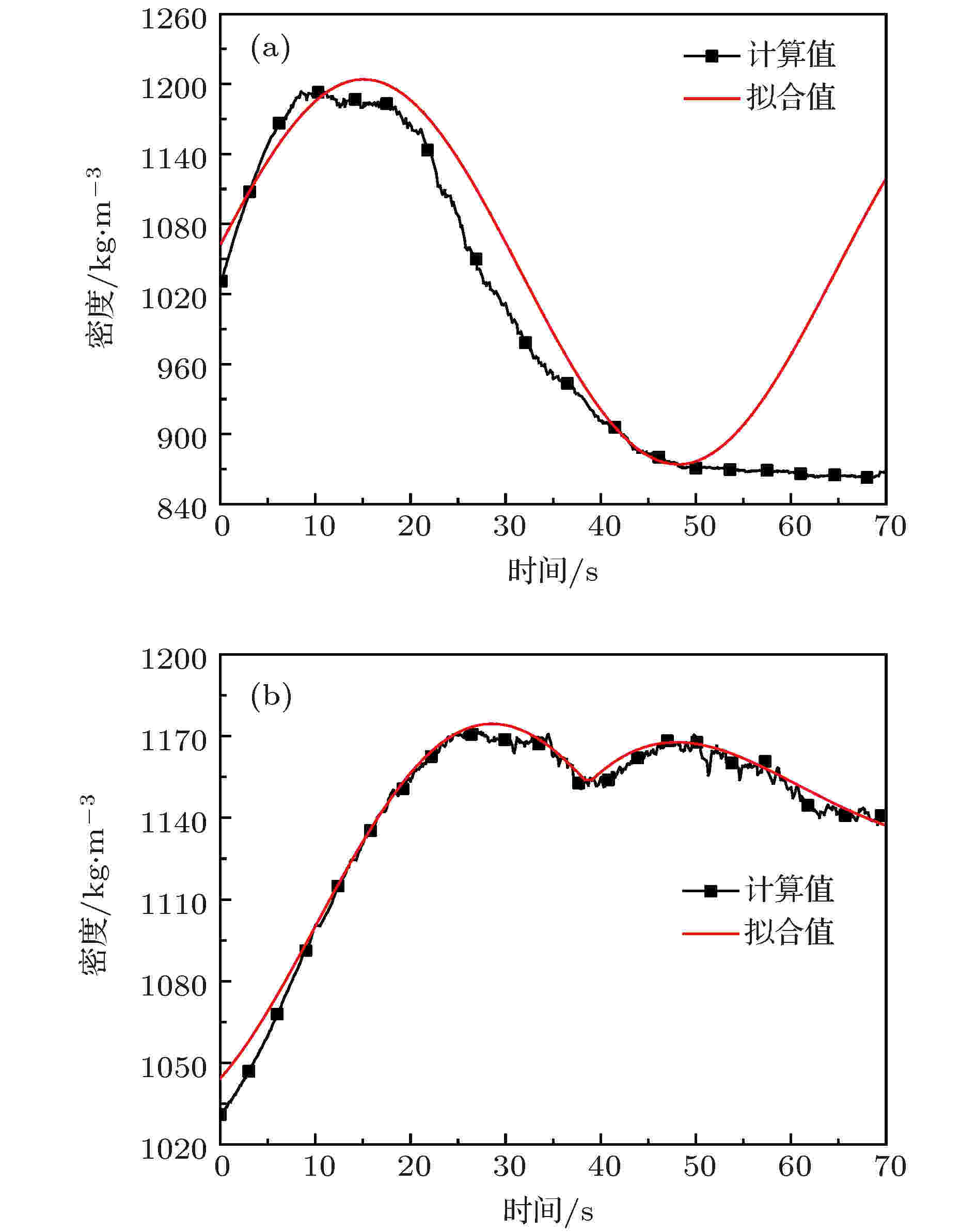
Figure11. Powder bulk density in tank of test 1# and test 2#: (a) Test 1#; (b) test 2#.
上述密度变化类似于阻尼弹簧振子作受迫振动时的运动规律, 其区别在于两者的阻尼系数不同, 从图11中可以看出小流化气量壁面切向加注方式的阻尼系数较小, 近似作等幅压缩膨胀, 但由于粉末是离散型物质, 气量较小时无法将膨胀后的粉末再次压缩, 因此储箱内粉末堆积密度减小后不会再次增加; 而大流化气量壁面切向加注方式阻尼系数较大, 近似为减幅振荡, 这是因为较大的流化气量可以将膨胀后的粉末再次压缩, 所以该工况下的粉末堆积密度表现为振荡衰减过程.
上述物理变化过程与欠阻尼二阶系统的响应过程类似, 其响应函数表示可用(4)式表示. 式中





系统参数 | ${\rho _{\min }}$ | $K$ | $\zeta $ | ${\omega _{\rm{n}}}$ | $\tau $ | 备注 |
工况1# | 874 | 165 | 0 | 0.095 | –18.0 | — |
工况2# | 1031 | 83 | 0.1 | 0.090 | –6.5 | $t$ ≤ 38 s |
1031 | 107 | 0.38 | 0.100 | 14.0 | $t$ > 38 s |
表3工况1#和工况2#下二阶系统参数
Table3.Second-order system parameters of test 1# and test 2#.
1)采用较大流化气量的加注方式有利于加注系统工作参数稳定, 但加注后期对集粉箱内粉末扰动较大, 集粉箱加注率较低, 仅有68.1%. 虽然采用较小流化气量的加注方式加注参数稳定性较差, 但集粉箱加注率更高, 可达93.9%;
2)与集粉箱端盖加注方式相比, 壁面切向加注方式对集粉箱内已有粉末的扰动较小, 所以均匀性较好. 气力加注方式下集粉箱内粉末堆积密度大于储箱内初始堆积密度;
3)加注过程中储箱内粉末的堆积密度会发生动态变化. 采用较小流化气量加注时, 储箱内粉末的堆积密度是先增大后减小, 最终堆积密度小于初始值, 而采用较大流化气量加注时, 储箱内粉末堆积密度的密度变化是先增大后减小再增大再减小, 最终堆积密度大于初始值;
4)储箱内的粉末密度变化类似于阻尼弹簧振子作受迫振动时的运动规律, 流化气量较小时系统的阻尼系数较小, 而流化气量较大时系统阻尼系数较大, 且是一个变阻尼过程.