全文HTML
--> --> -->
自科学家们发现二次电子发射(secondary electron emission, SEE)是诱发空间中不良效应的根本原因之一起, 许多研究者开始探索能够应用于空间科学中以提高空间微波部件可靠性的低SEY工程表面. 由于SEY对于材料的本征特性(物理密度、功函数等)、表面形貌、表面状态(沾污、氧化等)均较为敏感[6-8], 因此现有的SEY抑制技术均是通过改变以上参量从而达到改善SEY的目的. 目前领域内较为成熟的低SEY技术大体可分为以下五类: 1)表面粗糙化(物理、化学刻蚀[4,9-11]); 2)表面涂覆低SEY薄膜(TiN[12-14]、非蒸散型吸气剂(non-evaporable getter, NEG)[15,16]、无定形碳[17]等); 3)表面生长与基体材料同质的纳米结构[18,19]; 4)使用低SEY材料作为基体; 5)以上四类方法的多种结合[11,20]. 以上低SEY表面的实现大多依赖较为昂贵的设备(如原子层沉积、磁控溅射、真空蒸发等)或较为苛刻的环境(如高真空、超净). 相比于其他的低SEY表面工程, 使用激光刻蚀技术在材料表面制备微纳结构是较为容易实现的表面处理方法, 且激光刻蚀具有以下优点: 1)环境要求度低, 无需超净或真空环境等; 2)设备简易、操作简单、灵活度高且表面处理效率高; 3)表面处理仅通过光束辐照表面完成, 无其他接触, 因此在做适当保护的情况下表面不易产生沾污; 4)所制备微结构稳定, 不易被破坏. 目前已有文献[11, 21]表明, 使用激光刻蚀在铜、铝及不锈钢表面形成的微纳结构能够有效抑制相应金属表面的SEY, 而关于使用激光刻蚀技术在镀金金属表面制备微结构抑制SEY的研究还相对较少.
实验中使用红外激光扫描刻蚀技术在铝合金样品表面制备了多种不同特征尺寸的微米阵列结构, 使用磁控溅射在所制备微阵列结构样品表面镀约250 nm厚的金层; 使用显微技术表征了样品的二维及三维精细形貌, 探究了微阵列特征尺寸与激光刻蚀参数之间的关系; 使用SEE测试平台表征了各微阵列结构的SEE特性, 验证了微米阵列结构对镀金表面SEY的显著抑制作用, 同时研究了微阵列结构表面SEY对结构深宽比及孔隙率的依赖规律; 比较了激光刻蚀样品与其他工艺所制备样品对SEY的抑制程度, 证明了激光刻蚀微结构对SEY的显著抑制效果. 在获得平滑镀金表面SEY测试数据的基础上, 使用蒙特卡罗模拟方法, 并结合金属SEE唯象概率模型和电子运动轨迹追踪算法, 对各微阵列表面电子出射情况进行了仿真, 理论上验证了表面孔隙率及结构深宽比对SEY的影响规律, 揭示了激光刻蚀微阵列结构有效抑制镀金表面SEY的机理. 对比分析了微阵列结构实测SEY与仿真结果之间的差异, 给出了二级粗糙结构对实测SEY的影响规律.
2.1.激光刻蚀制备微阵列结构
实验中使用波长为1064 nm的脉冲式红外光纤激光器(GSS-Fiber-20, 西安高斯激光)对铝合金样品表面进行扫描刻蚀. 激光器最大刻蚀功率为20 W, 最小束斑直径约为

Figure1. Etching patterns: (a) Micro hole array; (b) etching unit of the micro hole array; (c) orthogonal groove array; (d) etching unit of the orthogonal groove array
样品编号 | |||||||
#1 | #2 | #3 | #4 | #5 | #6 | #7 | |
激光功率/W | 16 | 12 | 10 | 6 | 12 | 12 | 12 |
$d/{\text{μ}}\rm{m}$ | 150 | 150 | 150 | 150 | 150 | 100 | 50 |
$b/{\text{μ}}\rm{m}$ | 50 | 50 | 50 | 50 | 50 | 100 | 150 |
$l/{\text{μ}}\rm{m}$ | 200 | 200 | 200 | 200 | 200 | 200 | 200 |
扫描次数 | 400 | 100 | 25 | 5 | 250 | 250 | 250 |
理论孔隙率A/% | 44.18 | 44.18 | 44.18 | 44.18 | 43.75 | 75.00 | 93.75 |
表1各样品刻蚀单元内图形尺寸及激光刻蚀参数
Table1.Sizes of the etching patterns and the detailed etching parameters
2
2.2.表面形貌及SEE特性表征
表征实验中, 使用激光扫描显微镜(laser scanning microscopy, LSM, Keyence-VK9700)对激光刻蚀前后样品的三维形貌进行了表征; 使用扫描电子显微镜(scanning electron microscope, SEM, Hitachi S-4800)对刻蚀前后样品的二维精细形貌进行了表征. 此外, 实验中使用能量色散X射线谱(energy dispersive X-Ray spectroscopy, EDX, Hitachi S-4800附件)分别对不同状态下样品的表面元素组分进行了分析. 样品SEE特性测试使用超高真空金属SEE研究平台完成, 关于该系统的具体参数及相关描述已在文献[22]中做了详尽报道. 样品的SEY测试使用传统的样品电流法, 关于样品电流法的详细原理及误差分析可见文献[23], 该测试过程可简述为如下两步: 首先在样品上施加 + 500 V的偏压, 在此种入射情况下, 几乎所有逃逸的二次电子都会被吸引回样品表面, 此时测得的电流为该过程中所有电子束流之和IP; 然后在样品上施加–20 V的偏压, 此种入射条件下, 所有逃逸的电子均会受到样品表面负偏压的排斥作用而加速远离样品表面, 此时测得样品上流过的电流IS即为总的电子束流IP减去逃逸的电子束流. 在得到IP和IS的情况下, 样品表面的SEY可由(3)式计算得到:3.1.微阵列结构显微分析
图2(a)—(d)为使用LSM观测得到的激光刻蚀圆孔阵列#1—#4样品的三维形貌, 图2(e)—(g)为所刻蚀正交沟槽阵列#5—#7样品的三维形貌, 图2(h)给出了未经激光刻蚀处理的平滑镀金表面的三维形貌作为对照. 图3(a)—(d)给出了图2中部分样品的二维形貌, 插图为对应样品局部区域的精细形貌表征结果. 表征实验中, 通过LSM给出的样品三维形貌, 提取了7种微阵列结构的特征尺寸(微孔阵列特征尺寸为表面孔径和孔深, 交错沟槽阵列特征尺寸为槽宽和槽深). 表2列出了7种微结构的深宽比(记为H), 此处将两类样品的深宽比定义为: 微孔(或沟槽)平均深度与微孔孔径(或沟槽槽宽)之比. 对于圆柱微孔阵列, 其尺寸标注如图1(b)所示, 微孔深宽比由(4)式计算得到: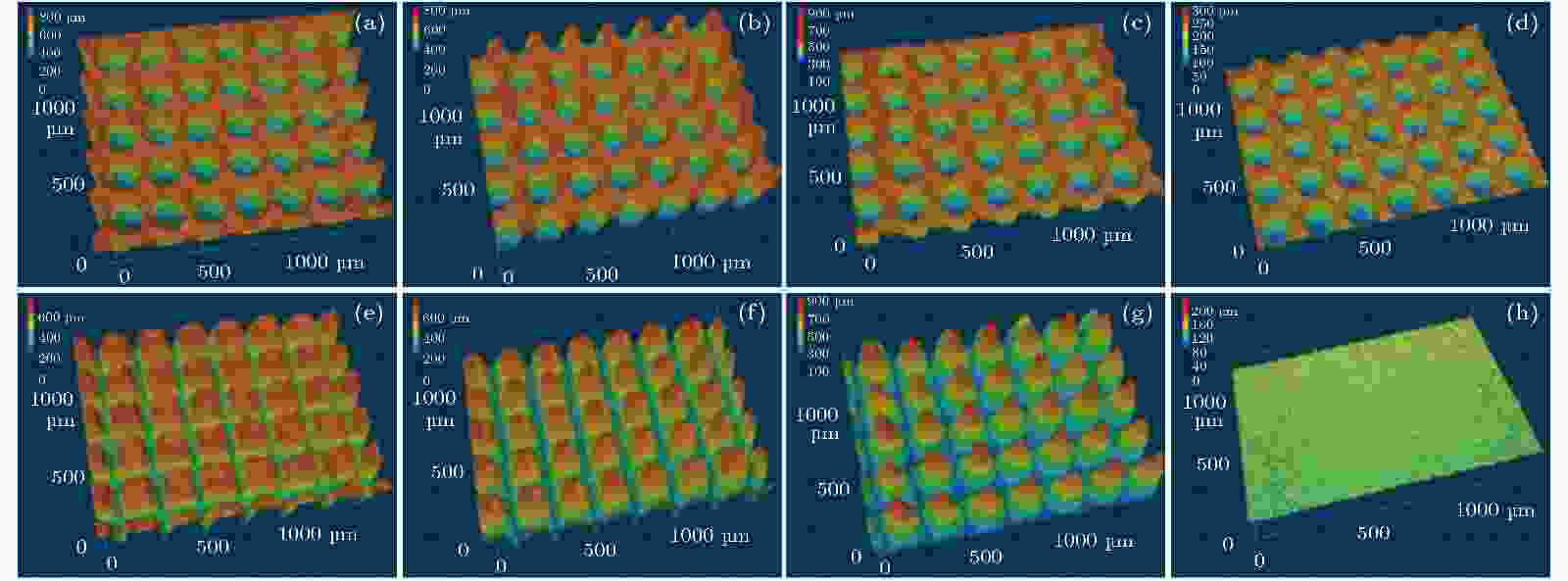
Figure2. Three-dimensional morphologies of various gold coated samples: (a) Sample #1; (b) sample #2; (c) sample #3; (d) sample #4; (e) sample #5; (f) sample #6; (g) sample #7; (h) untreated flat gold coated surface

Figure3. Accurate two-dimensional morphologies of various samples characterized by SEM: (a) Sample #1; (b) sample #4; (c) sample #5; (d) sample #7
样品编号 | |||||||
#1 | #2 | #3 | #4 | #5 | #6 | #7 | |
$d/{\text{μ}}\rm{m}$ | 165 | 164 | 158 | 155 | 121 | 83 | 34 |
$h/{\text{μ}}\rm{m}$ | 437 | 324 | 253 | 181 | 306 | 373 | 416 |
深宽比H | 2.65 | 1.98 | 1.60 | 1.17 | 3.87 | 3.19 | 2.51 |
孔隙率A/% | 53.46 | 52.81 | 49.01 | 47.17 | 63.40 | 82.78 | 97.11 |
表2各激光扫描刻蚀样品的特征尺寸、深宽比及孔隙率统计
Table2.Characteristic sizes, aspect ratio and porosity of the laser etched samples

此外, 观察图2和图3中的样品形貌可以看出, 两类微结构阵列除了表面有意刻蚀得到的微孔或沟槽这类一级粗糙结构外, 微孔和沟槽的边缘及内壁还存在一定的二级粗糙结构, 例如图3(a)和图3(b)中的孔洞边缘堆积着一些十几微米的金属颗粒, 图3(c)中沟槽阵列顶部未经处理的区域也有一些微米颗粒堆积. 这类二级粗糙结构并非理论设计时有意为之, 而是实验过程中受实验环境影响所致, 即实验环境为大气环境时, 孔洞内受热熔融而飞溅出的金属颗粒受空气阻力影响, 不能够及时远离样品表面, 故而冷凝堆积在孔洞及沟槽的内壁或边缘, 因此形成了这类二级粗糙结构. 通过对比图3(a)和图3(b)中的微孔结构可知, 当微孔较深时(#1样品, 图3(a)), 孔洞边缘堆积的颗粒较多, 但微孔内壁相对光滑, 此时二级粗糙结构仅存在于孔洞边缘; 而当微孔较浅时(#4样品, 图3(b)), 孔洞边缘堆积的微米颗粒尺寸变大、数量变多, 且微孔内壁也较为粗糙, 此时二级粗糙结构存在于孔洞边缘、内壁及底部. 对比图3(c)和图3(d)中的交错沟槽结构可以看出, 刻蚀区域小且槽深较浅的#5样品(图3(c))其顶部堆积的微颗粒相对较多, 形成了该样品的二级粗糙结构, 相比于顶部的微米颗粒, 该类沟槽结构的侧壁相对光滑; 对于刻蚀区域大且槽深较深的#7样品(图3(d)), 其刻蚀区域接近于100%, 几乎没有顶部的未刻蚀区域, 其侧壁在高倍显微图像中可以观察到不同程度的二级粗糙结构, 尺寸约在几微米量级.
除对样品的表面形貌进行了分析外, 表征实验中还使用EDX对样品原始表面、激光刻蚀后、刻蚀 + 镀金后三种表面状态下的表面元素进行了定量分析, 表3列出了#4样品三种状态下表面元素的定量分析结果(各元素原子数量比). 表3的测试结果表明: 对于原始的铝合金镀银样品, 其表面存在一定程度的氧化, 根据元素测试结果推测其表面以氧化银为主; 对于激光扫描后的样品, 其表面的镀银层经刻蚀从表面剥离, 铝合金基体裸露于表面, 故铝含量较高, 此外对比发现刻蚀区域的氧含量明显降低, 该类情况下, 刻蚀区域表面以铝和氧化铝的混合物为主; 对于刻蚀+溅射镀金后的样品, 镀金层已基本覆盖了刻蚀区域表面, 其表面金原子比例达到45.64%, 而测试中之所以仍然能够探测到氧、铝、银元素的含量, 是因为EDX的探测深度(几微米)大于镀金层厚度(250 nm)所致.
元素 | ||||
O | Al | Ag | Au | |
原始表面 | 51.64% | 8.24% | 40.12% | 0 |
激光刻蚀后 | 15.51% | 78.76% | 5.73% | 0 |
刻蚀 + 镀金后 | 11.78% | 38.66% | 3.92% | 45.64% |
表3三种状态下#4样品表面元素原子比例定量分析
Table3.Quantitative analysis of atomic proportion under three surface states for sample #4
2
3.2.微阵列结构SEE特性
图4给出了两种微阵列结构的SEE特性表征结果, 其中图4(a)为#1—#4微孔阵列结构SEY, 这4种样品孔隙率相近但深宽比相差较大; 图4(b)为#5—#7交错沟槽阵列结构的SEY, 这3种样品孔隙率和深宽比均有一定差异; 其中的插图为各样品归一化SEY (设各初始电子能量下, 平滑镀金表面SEY为1). 图4的SEY测试结果表明, 两类微阵列结构都能够大幅降低镀银层表面SEY, 且#1样品表现出最小的SEY, 其



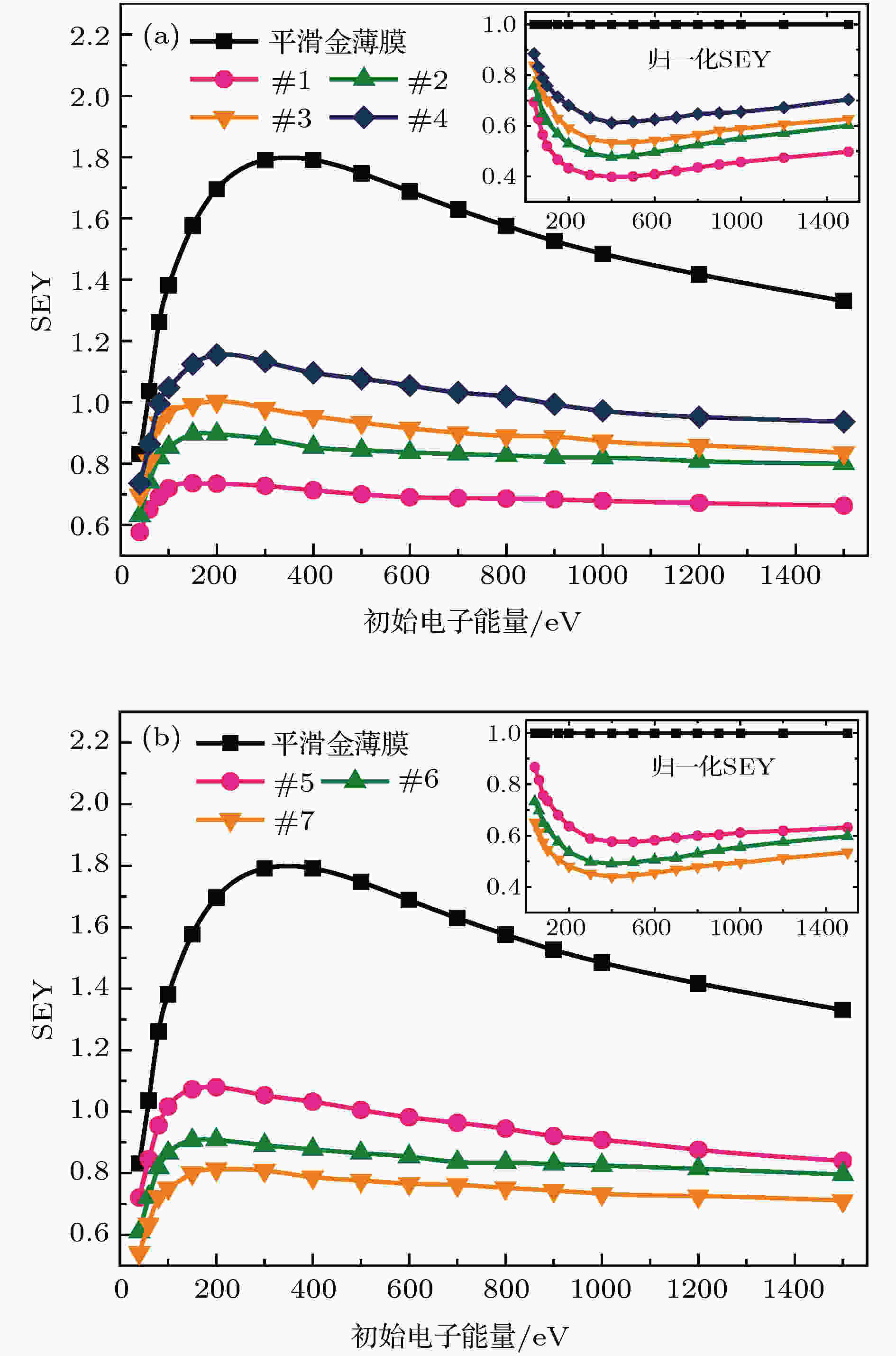
Figure4. Measured SEE characteristics of laser etched samples: (a) Micro hole array; (b) orthogonal groove array
图5给出了其他工艺制备的低SEY表面与本实验中激光刻蚀微结构表面SEY的对比结果. 所展示的样品包括: 本实验中使用激光刻蚀制备的#1和#7微阵列结构、氩离子清洗后的镀金铝合金表面[5]、低气压蒸发制备的金纳米结构(蒸发气压为70 Pa)[19]、磁控溅射TiN薄膜(经氩离子清洗)[12]及磁控溅射NEG薄膜[15]. 图5的SEY对比结果显示, 相比于其他的金表面(金纳米结构表面及氩离子清洗镀金表面), 激光刻蚀得到的镀金微阵列结构能够大幅降低镀金表面的SEY, 表明激光刻蚀微结构能够有效束缚表面电子出射, 且抑制二次电子能力优于其他类型的粗糙金属表面; 相比于TiN和NEG镀层表面, 激光刻蚀的镀金微阵列结构在200—1000 eV初始电子能量范围内表现出更小的SEY, 该结果表明在此能量范围内激光刻蚀微结构对二次电子的束缚能力优于低SEY薄膜.
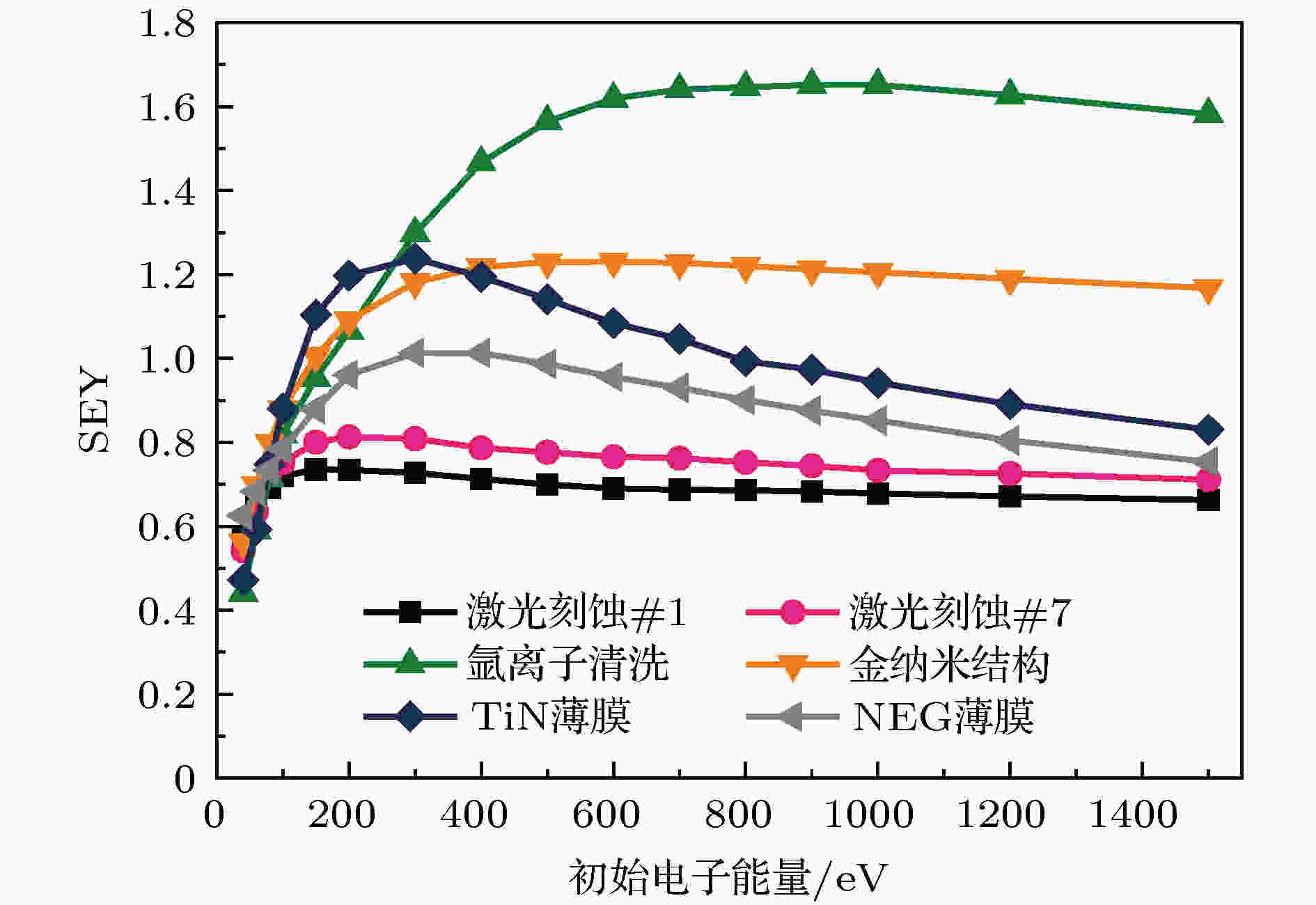
Figure5. SEY comparison among some surfaces acquired by various surface treatment technics
2
3.3.微阵列结构SEE特性仿真
为验证3.2节中所制备微阵列结构深宽比及孔隙率对镀银表面SEY的影响规律, 本节中使用如图1(a)和图1(c)中的规则几何阵列分别对激光刻蚀制备的两类微阵列结构进行等效, 等效模型的几何参数选用表2中所制备样品的实际尺寸. 仿真过程与文献[24]中报道的方法类似, 可简述如下: 1)使用MEST SEE唯象概率模型[25]模拟平滑镀金表面的SEE特性以确定模型中的部分待定参数; 2)使用蒙特卡罗模拟方法并结合已确定参数的MEST模型模拟电子的碰撞及出射过程; 3)基于电子的出射信息并借助电子轨迹追踪算法模拟电子在微结构中的运动过程; 4)判断电子在该运动过程中的最终状态(从微结构中逃逸成为出射电子, 或再次碰撞微结构表面); 5)重复以上过程2)—4), 直至所有初始电子的碰撞过程均模拟完毕. 对于每种微阵列结构, 仿真过程中入射电子设置为5 × 104个, 入射位置均匀分布于样品表面, 且均为垂直入射.图6(a)和图6(b)分别给出了4种微孔阵列及3种正交沟槽阵列的SEY仿真结果, 并列出了图4中的SEY测试结果作为对比. 从图6(a)可以看出, 对于孔隙率相近、深宽比依次减小的#1—#4号样品, 其SEY的仿真结果与微孔深宽比呈现反关系, 即深宽比越大的微孔其SEY越低, 抑制二次电子能力越强, 深宽比越小的微孔其SEY越高, 抑制二次电子能力越弱. 该仿真结果从趋势上验证了实验现象的合理性, 并且从理论上证明了单一因素情况下深宽比对SEY的影响规律. 图6(b)中对深宽比各异、孔隙率不同的正交沟槽微结构的仿真结果表明: 在深宽比均较大的情况下, 深宽比对SEY的影响较小而孔隙率对SEY的影响较大, 且孔隙率越大的微阵列(#7)结构其SEY越低, 对SEE的抑制作用越强烈. 该仿真结果证明了实验中激光刻蚀沟槽阵列对镀金表面SEY的抑制规律, 并从理论上证明了多因素条件下, 孔隙率对SEY的影响更为显著. 综上所述, 仿真结果从趋势上验证了实验结果的正确性, 并且为激光刻蚀微阵列结构抑制电子发射提供了理论依据.
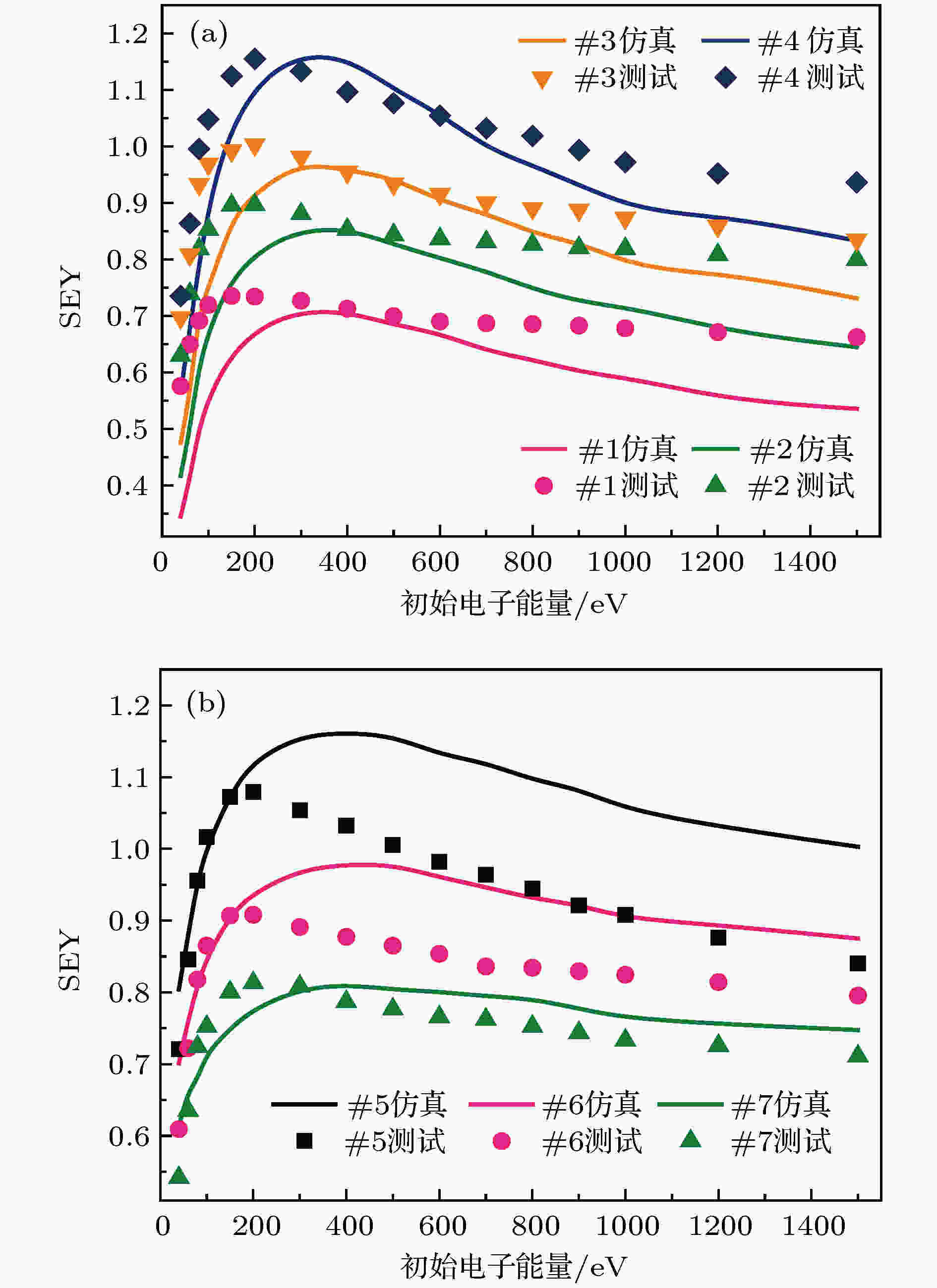
Figure6. Simulated SEE characteristics of laser etched samples: (a) Micro hole array; (b) orthogonal groove array
此外, 图6表明: SEY仿真结果与实测值之间表现出一定的差异, 具体如下: 对于图6(a)中#1—#4微孔阵列结构, 仿真得到的SEY几乎均小于实测值; 对于图6(b)中#5—#7沟槽阵列结构, 仿真得到的SEY几乎均大于实测值. 此处我们认为激光刻蚀过程中产生的非理想二级粗糙结构(如图3中各样品的二维精细形貌所示)是引起该差异的主要原因. 由图3可知, 激光刻蚀样品的二级粗糙结构主要由球形颗粒和随机形状的间隙结构组成, 而这两类结构对于SEY的影响可参考文献[24]中的理论模型及其对SEY的作用规律. 文献[24]探讨了金属纳米结构中球形颗粒结构和间隙结构对SEE的作用机制, 即: 球形颗粒能够增强表面SEY, 间隙结构抑制表面SEY, 而金属纳米结构由球形颗粒结构和间隙结构组合而成, 因此纳米结构表现出的SEY是两类结构加权平均作用的结果.
观察图3(a)和图3(b)中样品的精细形貌可知, 对于微孔阵列结构, 其表面微颗粒比例大而间隙结构比例较小, 因此二级粗糙结构中, 球形颗粒对SEY的增强作用大于间隙结构对SEY的抑制作用, 从而导致微孔阵列的SEY测试值略大于仿真值. 对于交错沟槽微阵列结构, 图3(c)和图3(d)显示其表面和侧壁有很大比例的间隙结构, 而球状颗粒结构则仅存在于顶部部分区域, 因此二级粗糙结构中球状颗粒所占的比例远小于间隙结构所占比例, 在影响电子出射方面, 即表现为沟槽结构对SEY的抑制作用大于球状颗粒对SEY的增强作用, 从而导致沟槽阵列的SEY测试值小于仿真值.