
Application of Explicit Dynamic Sub-Model Method in Parallel Calculation of Aero-Engine Transient Impact
CHAI Xianghai
通讯作者: 柴象海(E-mail:chaixianghai@sohu.com)
收稿日期:2020-09-3网络出版日期:2020-12-20
基金资助: |
Received:2020-09-3Online:2020-12-20
作者简介 About authors
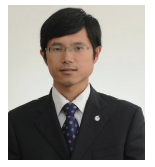
柴象海,中国航发商用航空发动机有限责任公司,博士,研究员级高级工程师,主要从事航空发动机瞬态冲击力学仿真分析与试验验证方法研究。本文中主要负责通过自编译子模型加载载荷算法的方式,实现了边界载荷从整机模型到分析对象的加载,载荷转换效率和转换精度自主可控,并通过试验设计对子模型数值仿真精度进行了验证。
CHAI Xianghai, Ph.D., the professor and senior engineer of AECC Commercial Aircraft Engine Co., LTD, is mainly engaged in simulation analysis and experimental verification method of transient impact mechanics of aero-engine.In this paper, he is mainly responsible for the realization of boundary load loading from the whole machine model to the analysis object by the way of self-compiled sub model loading algorithm. As the result, the load conversion efficiency and conversion accuracy are controlled independently, and the accuracy of numerical simulation of the sub model is verified by experimental design.E-mail: chaixianghai@sohu.com
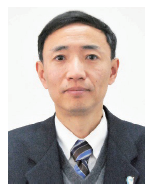
胡寿丰,中国航发商用航空发动机有限责任公司,博士,首席专家,主要从事航空发动机结构强度及复合材料结构件研发。本文中主要负责对子模型建模方法进行理论指导,提出载荷提取及加载策略。
HU Shoufeng, Ph.D, the Chief expert of AECC Commercial Aircraft Engine Co., LTD, is mainly engaged in the research and development of structural strength of aeroengine and composite structural parts.In this paper, he is mainly responsible for the theoretical guidance of sub model modeling method, and puts forward the load extraction and loading strategy.E-mail:shoufenghu@163.com
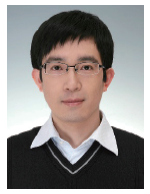
张执南,上海交通大学,博士,副教授,主要从事碰磨载荷作用机理研究。本文中主要负责对航空发动机整机建模与仿真。
ZHANG Zhinan, Ph.D., the associate professor of Shanghai Jiaotong University, is mainly engaged in the research on the mechanism of impact and wear loads.In this paper, he is mainly responsible for modeling and Simulation of aeroengine.E-mail: zhinanz@sjtu.edu.cn
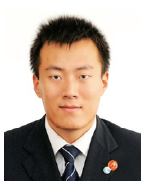
侯亮,中国航发商用航空发动机有限责任公司,硕士,主管设计师,主要从事航空发动机整机仿真并行计算效率与一致性控制策略研究。本文中主要负责提供高效、高精度的航空发动机整机FBO高性能并行计算方法。HOU Liang, Master, the Chief designer of AECC Commercial Aircraft Engine Co., LTD, is mainly engaged in the research of parallel computing efficiency and consistency control strategy of aero-engine simulation.In this paper, he is mainly responsible for providing high-efficiency and high-precision parallel computing method for FBO of aero-engine.E-mail: houl66@163.com

摘要
【背景】商用航空发动机需要满足适航安全性要求,其中风扇叶片脱落载荷是在设计中必须考虑的安全设计载荷。发动机整机瞬态显式动力学分析是个有效的分析工具,但在模型规模、计算效率和计算精度方面存在矛盾。整机模型通过选用合适的并行计算策略,一般能提供较为准确的部件界面载荷,但对于单个部件的应力分析,往往由于网格密度不够而不能获得满意结果。【方法】整机瞬态显式动力学仿真子模型技术,采用航空发动机整机简化模型进行整机计算,通过预先设置的子模型边界输出零部件载荷,作为零部件精细模型动强度分析的输入,在保证计算精度的同时,使计算效率大幅度提高。【结果】本文通过一个机匣等效平板靶板冲击试验算例,将平板特定区域定义为子模型,计算结果表明,子模型法能够与局部细化的整体模型得到相同的计算结果。同时,以航空发动机风扇轴为例,将子模型技术应用于叶片飞脱载荷下零部件动力学分析,建立航空发动机整机瞬态显式动力学仿真子模型分析方法,既可以解决叶片脱落等效载荷方法整机层面对粗网格部件应力分析计算误差大的问题,又能够考虑零部件细观结构对强度计算结果的影响。
关键词:
Abstract
[Background] Commercial aero-engine needs to meet the requirements of airworthiness safety, in which the fan blade shedding load must be considered in the design. Transient explicit dynamic analysis of engine is an effective analysis tool, but there are some contradictions in model scale, calculation efficiency and calculation accuracy. Generally, the whole machine model can provide more accurate component interface load by selecting appropriate parallel computing strategy. However, for the stress analysis of single component, the grid density is not enough to obtain satisfactory results. [Methods] The sub-model technology for whole engine transient explicit dynamic simulation uses the simplified model of aero-engine to calculate the whole machine. The load of parts is output through the pre-set sub model boundary, which is used as the input of dynamic strength analysis of the fine model of parts. The calculation accuracy is guaranteed and the calculation efficiency is greatly improved. [Results] In this paper, a specific area of the plate is defined as a sub model through an example of an equivalent plate impact test of a casing. The calculation results show that the sub model method can obtain the same calculation results as the whole model with local refinement. At the same time, taking the aero-engine fan shaft as an example, the sub model technology is applied to the dynamic analysis of parts under the load of blade flying off, and the sub model analysis method of aero-engine transient explicit dynamic simulation is established, which can not only solve the problem of large calculation error of the blade shedding equivalent load method for coarse grid component stress analysis, but also consider the influence of the microstructure of the components to the results of strength calculation.
Keywords:
PDF (7994KB)元数据多维度评价相关文章导出EndNote|Ris|Bibtex收藏本文
本文引用格式
柴象海, 胡寿丰, 张执南, 侯亮. 显式动力学子模型法在航空发动机整机瞬态冲击并行计算中的应用[J]. 数据与计算发展前沿, 2020, 2(6): 11-20 doi:10.11871/jfdc.issn.2096-742X.2020.06.002
CHAI Xianghai, HU Shoufeng, ZHANG Zhinan, HOU Liang.
引 言
商用航空发动机需要满足适航安全性要求,其中,风扇叶片脱落(Fan Blade-Out,简称FBO)载荷是设计中必须要考虑的极端载荷之一,严重影响飞行安全。FBO载荷通过风扇盘、轴、机匣、安装节等部件,最后传递到机翼。在FBO所引起的转子不平衡载荷以及极限冲击载荷影响下,航空发动机各关键零部件设计能否满足适航安全要求是发动机设计的关键考虑因素之一[1,2]。然而,FBO载荷是瞬态载荷,除了整机试验外,很难用部件试验来等效,这就使得在设计阶段,仿真成为判断FBO载荷下部件是否失效的重要依据[3]。FBO仿真一般采用整机瞬态显式动力学有限元模型进行分析,由于整机模型需要包括所有关键部件,而FBO过程一般都要达到几百毫秒,因此有限元模型规模无法过大,大多数零部件的网格较粗,细节都被忽略[4]。通过这种方法,获得的FBO载荷往往是有效的,但用来判断关键部件是否失效,以及失效后的响应,零部件的简化模型是远远不能满足要求的。
在设计过程中,需要对某一部件FBO载荷下的应力进行详细分析,其中一种解决方案是在整机仿真模型基础上局部细化该部件模型,其他部件保持原简化网格模型[5]。这种方法存在不少问题,首先,粗细网格界面很难处理,用接触或网格局部粗细过渡都可能产生问题;更重要的是,整机模型规模非常大,显式算法时间步长由该细化模型最小单元特征尺寸决定而导致整机加局部细化模型计算效率大幅下降,因此,在实际操作中,这一方法往往很难实现。
根据以上分析,子模型法将是一个能有效进行航空发动机关键零部件详细模型应力分析的方法。子模型法在传统的隐式有限元仿真中已经有了较为成熟的应用,但在瞬态显式有限元分析中尚未见采用。本文提出整机瞬态显式动力学仿真子模型法,用航空发动机整机模型进行FBO计算,通过预先设置的子模型边界输出某零部件边界节点位移时间历程曲线,作为零部件精细模型动强度分析的输入,在保证计算效率的同时,使计算精度大幅度提高。同时,在一次整机运算时可以输出多个部件的边界节点位移,然后再分别进行多个部件的子模型计算,这也是局部细化模型无法比拟的优势。
1 航空发动机整机动力学并行计算
1.1 发动机整机瞬态冲击分析模型
发动机风扇叶片脱落是一个具有非常复杂的非线性瞬态动力学事件,它产生的不平衡力通过各相关部件最后传入机翼。为了能够准确地模拟整个叶片脱落过程,需要一个合适精度的模型来捕捉从叶片开始脱落直到转子转速降到足够低的速度,使得动载荷不再产生任何新的破坏的整个过程。本文针对上述问题,采用有限元方法求解,建立航空发动机整机有限元计算模型,采用显式动力学方法进行求解。本文算例均采用LS-DYNA显式动力学软件进行计算,同样的理论和方法适用于PAM-Crash、Abaqus等其它同类软件。如图1所示,模型包含745 030单元,1 173 203节点,时间步长6.5E-8,计算时长50ms,采用显式动力学计算方法求解。模型由风扇、压气机、燃烧室、涡轮和附件等几部分组成。为了得到叶片脱落后的峰值载荷,通常需要模拟较长的时间历程[6,7],综合考虑航空发动机整机简化模型显式动力学并行效率和计算成本,采用64核并行,计算时间40小时。因此,即使采用简化模型,整机FBO仿真分析也必须采用大规模并行计算。如前所述,采用全局或局部细化的方法对发动机中某个特定的零部件进行FBO载荷分析,所需要的计算资源和计算时间,无法满足工程需求。子模型法很好地解决了这个难题,以下是风扇轴在FBO载荷下应用子模型法的一个算例。
1.2 发动机整机瞬态冲击并行计算策略
本文综合考虑并行模式和区域分解策略对航空发动机的整机FBO计算效率的影响,选用混合式并行(Hybrid)技术作为并行计算方法。Hybrid是一种新型的并行模式,采用MPI(Message Passing Interface)+ OpenMP(open Message Passing Interface)混合编程技术,综合了对称多处理器结构 (SMP: Symmetric Multi-Processor) 和海量并行处理结构 (MPP: Massive Parallel Processing) 并行模式的优势。图1
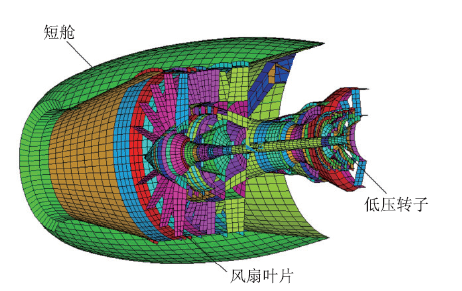
图1航空发动机包容性分析有限元模型
Fig.1Finite element model of aeroengine containment analysis
在SMP、MPP和Hybrid三种并行方式下,采用8核、16核、32核、64核分别对航空发动机整机FBO模型进行计算,MPP并行计算速度最快,SMP并行计算速度最慢。Hybrid并行方式比SMP并行方式耗时少37%。
Hybrid并行模式的并行性能略低于MPP,这是因为为了获得计算结果的一致性,在Hybrid并行模式中开启一致性选项(Consistency flag=1),降低了计算性能。
综合计算效率和计算一致性,本文采用Hybrid并行策略,该并行模式可以获得较高的并行效率和结果一致性,同时,能够通过调整线程并行的数量,实现良好的并行效率和可扩展性,符合航空发动机整机FBO并行计算需求。
2 瞬态显式动力学子模型分析方法
瞬态显式动力学子模型法,包含两个步骤:进行含零部件简化模型的整机模型的有限元计算,并输出子模型边界载荷;建立零部件或特定区域精细模型的子模型,并对该零部件或区域精细模型进行受力分析。下面对两个步骤进行详细说明。对含零部件简化模型的整机模型进行有限元计算,并输出边界节点时间历程曲线。
通过自编译程序对边界节点位移时间历程曲线进行格式转换,生成子模型边界载荷输入文件,即子模型边界单元外圈节点位移时间历程曲线。
图2
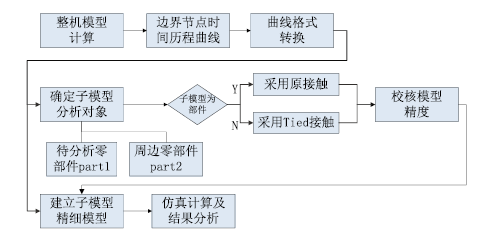
图2瞬态显式动力学子模型分析流程图
Fig.2Flow chart of transient explicit dynamic sub model analysis
确定子模型分析对象,它可以是一个零部件或部件组合,也可以是一个零部件的某一区域。如果以某一零部件为分析对象,通常需要将该零部件及与之存在接触关系的周边零部件的一部分一起定义为子模型。之所以把周边零部件的接触部分也定义为子模型的一部分,是因为可以直接把整机模型输出的边界位移直接加到子模型的节点上,而不需要对粗模型的边界位移插值到精细模型边界的节点上。
通常在发动机整机模型中,可以将所选子模型划分为两部分,定义两个part,包括待分析的零部件模型part 1、与待分析零部件模型具有接触关系的周边零部件模型part 2。其中,part 2最外圈为子模型边界处一层单元,如果子模型是区域则采用绑定(tied)接触,如果子模型是部件则采用原来的接触方式,在整机模型和子模型中网格密度不变,其节点/单元编号也不变,用于整机模型载荷输出和子模型载荷加载。
对子模型进行计算,计算结果与整机模型中的相应模型计算结果进行比较,校核模型精度。
根据设计要求,对待分析零部件进行细化,保证足够的网格密度和细节结构,建立零部件精细子模型,Part 1细化,但Part 2保持不变。
将边界载荷施加到所定义的零部件子模型,对子模型进行求解,获得应力分布。
此外,如果该零部件在正常工作载荷下存在预应力(如旋转件的离心力),同样的方法也适用,不过整个计算需要分两部进行,分别进行预应力分析和瞬态载荷分析并叠加,预应力下的子模型边界位移将不随时间变化。
3 显式动力学子模型分析方法验证
将子模型方法应用于航空发动机瞬态冲击数值仿真,能够为某个零部件或区域进行有效的应力分析。但是我们需要对该方法的准确性进行验证,验证的基本思路是两个模型的结果比较。先用子模型法对整机简化模型下的某一精细子模型进行分析,获得精细模型的应力分布。然后建立发动机的整机模型加局部精细模型并进行计算,提取同一局部精细模型的应力分布,比较两个同网格的有限元子模型在不同方法计算下的应力分布。如果接近,说明子模型法是准确的,如果差别较大,说明子模型法存在问题。由于模型规模及时间步长的限制,很难建立发动机整机简化模型加局部精细模型并进行有限元分析,因此无法用上述方法对其准确性进行检验。所以,本文选取一个小规模计算模型来检验子模型法,即机匣平板靶板冲击模型,通过对比精细子模型和包含精细模型的整体模型计算结果,验证显式动力学子模型分析方法的准确性。
3.1 机匣平板靶板冲击试验
发动机风扇包容机匣等效靶板冲击试验采用空气炮将风扇叶片等效碎片以叶片与机匣等效撞击角度射向风扇包容机匣等效试验件,通过试验结果对风扇叶片脱落机匣包容性分析模型进行标定[8,9]。风扇包容机匣等效靶板冲击试验示例如图3所示,风扇机匣等效平板靶板长宽600mm*600mm,厚度28mm,通过专用夹具安装在试验台上,试验台与水平面夹角35.1o,通过图示角度仪校准,平板采用带失效的弹塑性材料本构,夹具采用线弹性材料本构。实测弹体速度198 m/s,水平方向撞击靶板,弹体底部与靶板接触,弹体采用带失效的弹塑性材料本构。
图3
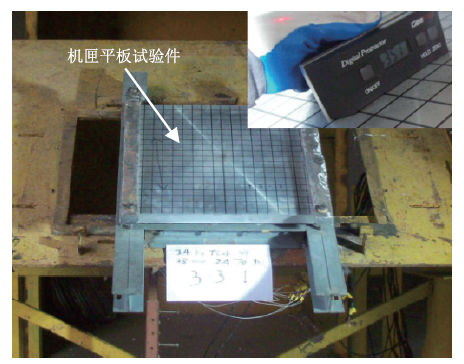
图3机匣平板靶板冲击试验
Fig.3Impact test of case plate target
3.2 靶板冲击试验仿真分析
靶板冲击试验数值仿真模型如图4所示,约束边缘垂直方向自由度,弹体施加初速度载荷。靶板网格长宽均6 mm,厚度方向13层单元,碎片初始速度与机匣平面夹角为35°。机匣平板靶板冲击试验0.85ms时刻分析结果如图5所示(von-Mises应力峰值)。图4
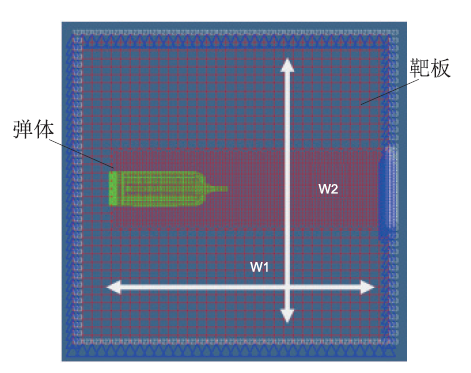
图4机匣平板靶板冲击试验分析模型
Fig.4Analysis model of case plate impact test
图5
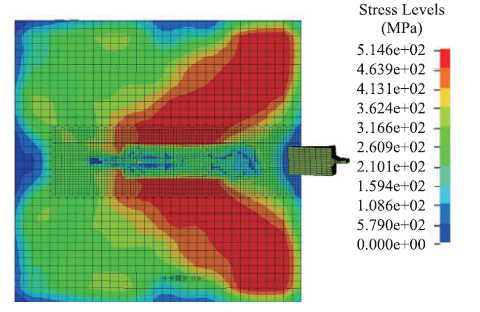
图5机匣平板靶板冲击试验分析结果
Fig.5Analysis results of case plate impact test
3.3 子模型建模及分析
按照子模型建模及分析方法,基于机匣等效平板靶板冲击试验数值仿真分析模型,选取平板特定区域定义为子模型,进行计算结果对比分析,从而验证子模型方法的准确性。在目标靶板上选取如图6所示子模型,Part 1区域定义为分析对象,Part 2区域定义为子模型边界单元,在整体模型计算输入文件中,定义子模型边界单元外圈节点位移时间历程曲线输出。
图6
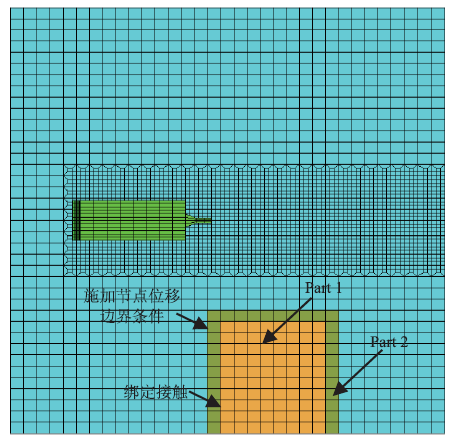
图6子模型选取及边界定义
Fig.6Sub-model selection and boundary definition
在示例中,由于所选取的子模型和整体模型属于同一个零部件,不存在与子模型具有接触关系的周边零部件模型,所以仅包含模型边界单元。对整体模型提交计算,输出节点位移时间历程文件,通过自编译的子模型边界节点位移提取程序,生成子模型边界载荷。
如图7所示,对选取的子模型分析区域进行重新建模和网格细化,建立子模型外圈单元与子模型之间绑定接触,修改子模型输入文件,设置加载边界载荷文件,提交计算子模型。此处,动力学子模型基于的理论基础是载荷在接触对之间传递不存在能量损失,但接触对周边单元仿真精度,符合圣维南原理,因此,需要建立过渡单元,使得分析区域尽可能地远离接触边界。
图7
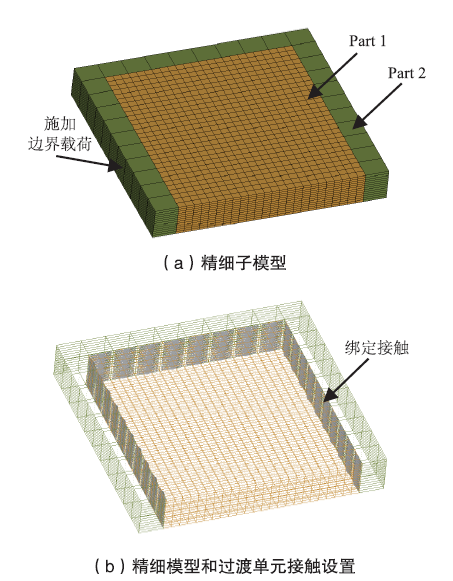
图7精细子模型建模
Fig.7Fine sub-model modeling
3.4 分析结果对比验证
为了验证显式动力学子模型分析方法的准确性,建立如图8所示包含分析区域局部细化模型的整体模型以及细化模型的放大图,局部细化模型和整体模型通过梯形过渡单元相连接,分析区域模型参数与精细子模型参数一致。靶板其它部分约束条件、弹体速度角度等,与图4所示机匣平板靶板冲击试验分析模型一致。图8
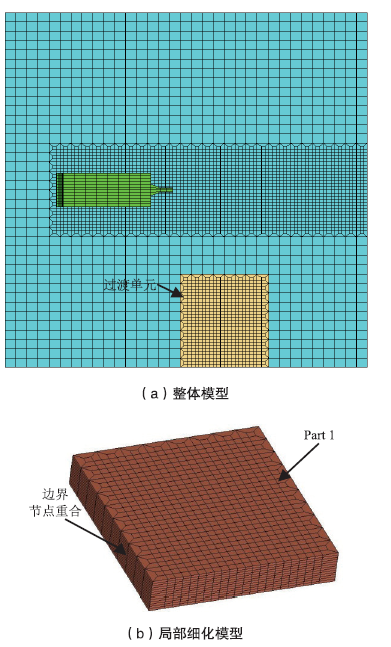
图8含局部细化模型的整体模型
Fig.8Global model with local refinement model
对比包含精细模型的整体模型和细化子模型计算结果之间的差异,如图9所示,应力峰值误差0.2%,发生峰值的时间也一致,而本算例所用的CPU时间是子模型法的二十多倍。
计算结果表明,采用本文方法,对经过试验标定的模型进行仿真计算,分析结果应力峰值误差可以忽略,效率能够满足工程仿真分析需求,所述方法与网格规模无关。如果分析对象拓扑结构不发生改变,在理论上,包含精细模型的整体模型和细化子模型能够得到相同的计算结果,显式动力学子模型方法不存在理论误差,微小的数值误差在工程设计许可范围内。
图9
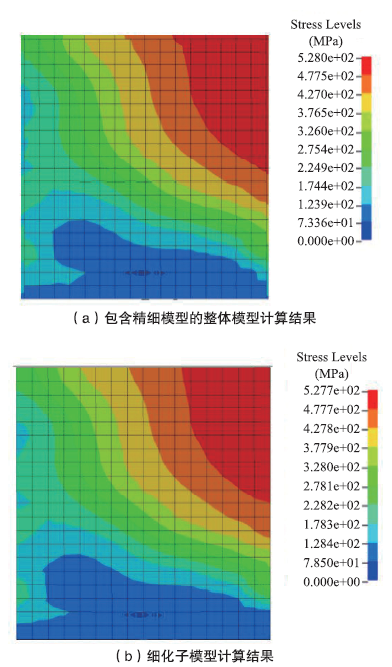
图9应力分析结果对比
Fig.9Comparison of stress analysis results
4 风扇轴叶片飞脱载荷分析
4.1 风扇轴子模型建模
现在以风扇轴为例,将显式动力学子模型技术应用于FBO载荷下零部件动力学强度分析,建立航空发动机整机瞬态显式动力学仿真子模型典型分析方法。风扇轴是风扇盘与发动机低压轴之间的连接部件,通过发动机轴承支撑,如图10所示,从左下到右上四个过渡单元,分别与风扇盘螺栓连接、与航空发动机1#支点棍棒轴承连接、与航空发动机2#支点滚珠轴承连接、与低压轴花键连接。正常工作状态主要是传递扭矩,FBO载荷下,会承受风扇盘传递的叶片丢失后的转子不平衡载荷[10]。在航空发动机设计中,需要通过风扇轴静强度、动强度试验和数值仿真分析,判断发动机风扇轴在极限工况和限制工况下是否满足强度设计要求。
航空发动机整机有限元模型如1.1节所述,在航空发动机整机有限元模型中,如图10所示,首先定义与风扇轴具有接触关系的周边零部件模型,以尽量靠近子模型part为原则,周边零部件最外圈单元定义为过渡单元。
图10
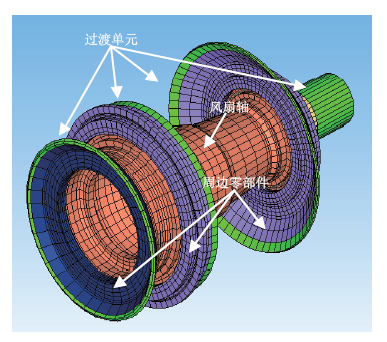
图10整机模型内的风扇轴模型
Fig.10Fan shaft model in the whole machine model
在整机模型计算输入文件中,定义子模型过渡单元外圈节点位移时间历程曲线输出。运行自编译的子模型边界节点位移提取程序,生成子模型边界载荷和所有转动部件节点初速度。
根据设计要求,对风扇轴子模型进行细化建模,建立如图11所示包含细观结构特征的精细有限元模型。建立细化后的子模型和最外圈过渡单元之间的绑定接触。
计算流程与机匣平板靶板冲击试验相同,对选取的子模型分析区域进行重新建模和网格细化后,建立子模型外圈单元与子模型之间绑定接触,修改子模型输入文件,设置加载边界载荷文件,提交计算子模型。
图11
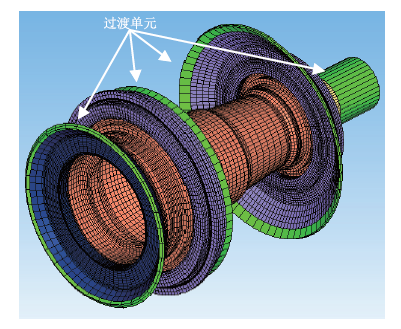
图11风扇轴精细有限元子模型
Fig.11Fine finite element sub model of fan shaft
如前所述,对于风扇轴类转动部件,需要在整机模型计算结果中输出子模型部件初始应力,并在子模型计算文件中增加预应力卡片,所以子模型法需要先计算旋转预应力,再算FBO载荷下的应力。风扇轴预应力计算结果如图12所示。
图12
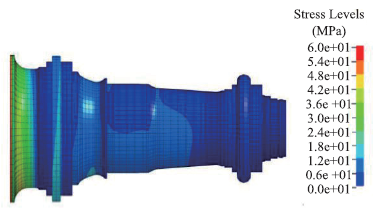
图12风扇轴预应力计算结果
Fig.12Calculation results of fan shaft prestress
4.2 分析结果
子模型计算精度已经在3.4节进行了证明,不再做重复验证。对风扇轴精细有限元子模型提交计算,风扇轴精细有限元模型应力计算结果如图13所示。如前所述结论,显式动力学子模型方法不存在理论误差,微小的数值误差在工程设计许可范围内,因此风扇轴精细有限元模型应力计算结果可以作为风扇轴设计方案强度校核的依据。图13
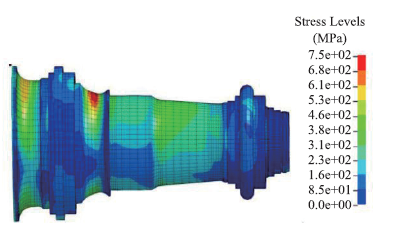
图13风扇轴精细有限元模型应力计算结果
Fig.13Stress calculation results of fan shaft fine finite element model
风扇轴精细有限元模型最大应力位置等效应力时间历程曲线如图14所示,风扇轴最大等效应力<1000MPa,材料屈服极限1400MPa,风扇轴在FBO载荷下强度满足设计要求。
图14
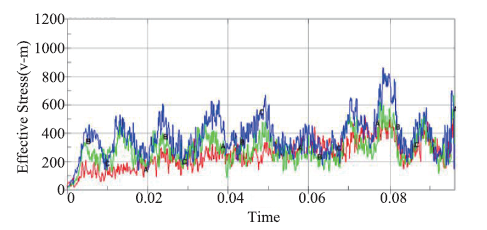
图14风扇轴精细有限元模型应力时间历程曲线
Fig.14Stress curve of fine sub-model for fan axle
将显式动力学子模型法应用于航空发动机零部件整机FBO载荷强度校核,能够避免时间历程动载荷等效静载荷误差问题,而且分析对象在划分足够精细网格的情况下,能够得到具有满足工程需求的计算精度,计算效率满足工程仿真分析需求。
需要特别指出的是,如动态子模型法用于前文所述风扇轴等转子系统的话,由于高速旋转的原因,子模型的边界位移输入的时间间隔就必须比静子系统要小一个数量级,以保证计算结果的准确性。
5 结论
在航空发动机工程设计中,发动机FBO试验耗资巨大,而且必须在整机试车阶段才能进行。在设计阶段很难用部件试验来等效,整机数值仿真模型又存在模型规模、计算效率和计算精度方面相互矛盾的问题。通过整机瞬态显式动力学仿真子模型技术,采用航空发动机整机简化模型进行FBO载荷下零部件的载荷计算,通过预先设置的子模型边界输出零部件载荷,作为零部件精细模型动强度分析的输入,在保证计算效率的同时,使计算精度大幅度提高。通过机匣等效平板靶板冲击试验,将平板特定区域定义为子模型,计算结果表明,如果分析对象拓扑结构不发生改变,精细模型能够与整体模型得到相同的计算结果,应力峰值误差可控制在1%以内。
本文将瞬态显式动力学子模型技术应用于航空发动机叶片飞脱载荷下风扇轴动力学强度分析,建立了航空发动机整机瞬态显式动力学仿真子模型分析方法。该方法解决了模型大小和精度的矛盾,是子模型法在显式动力学领域的成功拓展。它既可以用于静子结构,也可以用于转子结构;既可以用于发动机,也可以用于任何需要建立动态子模型的大型系统。
利益冲突声明
所有作者声明不存在利益冲突关系。参考文献 原文顺序
文献年度倒序
文中引用次数倒序
被引期刊影响因子
[J].
[本文引用: 1]
[本文引用: 1]
[J].
[本文引用: 1]
[J].
DOI:10.1007/s00158-001-0160-4URL [本文引用: 1]

Despite advances in computer capacity, the enormous computational cost of running complex engineering simulations makes it impractical to rely exclusively on simulation for the purpose of design optimization. To cut down the cost, surrogate models, also known as metamodels, are constructed from and then used in place of the actual simulation models. In this paper, we systematically compare four popular metamodelling techniques – polynomial regression, multivariate adaptive regression splines, radial basis functions, and kriging – based on multiple performance criteria using fourteen test problems representing different classes of problems. Our objective in this study is to investigate the advantages and disadvantages of these four metamodelling techniques using multiple criteria and multiple test problems rather than a single measure of merit and a single test problem.
[J].
[本文引用: 1]
[C].
[本文引用: 1]
[J].
[本文引用: 1]
[J].
DOI:10.1061/(ASCE)0893-1321(2008)21:3(174)URL [本文引用: 1]
[J].
[本文引用: 1]
[J].
DOI:10.1016/j.ijimpeng.2008.10.002URL [本文引用: 1]
