
2Department of Mathematics, College of Arts and Sciences,
3Department of Mathematics, Faculty of Science,
4Department of Mathematics, Faculty of Science,
First author contact:
Received:2021-02-12Revised:2021-04-12Accepted:2021-04-16Online:2021-06-01

Abstract
Keywords:
PDF (2783KB)MetadataMetricsRelated articlesExportEndNote|Ris|BibtexFavorite
Cite this article
Faisal Shahzad, Wasim Jamshed, Tanveer Sajid, Kottakkaran Sooppy Nisar, Mohamed R Eid. Heat transfer analysis of MHD rotating flow of Fe3O4 nanoparticles through a stretchable surface. Communications in Theoretical Physics, 2021, 73(7): 075004- doi:10.1088/1572-9494/abf8a1
Nomenclature
1. Introduction
Rotating flow and heat transportation problems have importance in a vast range of geophysical as well as engineering applications. The rotating flow has greater utilization [1] in chemical reactors, rotating machinery, magnetohydrodynamic (MHD) pumps, petroleum refineries, biochemical problems, lubrication and refrigeration systems etc. Wang [2] has analyzed rotating flow over an elongated sheet. Nazar et al [3] studied time-dependent rotating flow via a stretching sheet. Rosali et al [4] interrogated the boundary-layer rotating flow result in a shrinking surface by considering the suction effect. Sulochana et al [5] considered the radiative, viscous dissipative flow and chemical reaction influences on flow past a rotating sheet. Seth et al [6] examinated the boundary-layer flowing of rotating nanofluid with entropy generation results in an expandable plate. Gireesha et al [7] probed the impact of nonlinear thermal radiation on time-dependent rotating fluid flow of nanotubes using the shooting method technique.In recent times, there have been many publications about nanotechnology in the area of science by a huge number of researchers, attributable to its larger thermal conductance. The outlook of nanofluid has been initially introduced by Choi [8]. Nanofluid is an amalgamation of nanometer-sized (10−9 to 10−11 nm) solid nanoparticles with conventional liquid. The metallic very small particles utilized in nanofluid are prepared from metals (e.g. Ti, Ag, Cu), non-metals (e.g. carbon nanotubes) and oxides (e.g. TiO2,Al2O3). Buongiorno [9] has studied convective heat transport augmentation using nanofluid. Nanoliquids were found to obtain suitable thermophysical characteristics, such as thermal conductivity and thermal diffusivity, together with viscosity [10–13]. The effect of metallic oxide sub-microns on the flux and heat transfer has been studied by Pak and Cho [14]. They found that the heat rate for the dispersed fluids was enhanced with raising the concentration of nanoparticles and Reynolds number. Zaraki et al [15] assessed the influence on convective border layer flow and heat transfer of nanofluid on the size, shape and form of metallic components. The effect of various types on the normal convection of ${{\rm{SiO}}}_{2}$-water nanofluid in the trapezoidal cavity has been studied by Selimefendigil [16]. Nayak et al [17] reviewed the mixed convective flow of a nanoliquid inside a skewed enclosure. They investigated the influences of Brownian diffusivity and thermophoretic diffusion on the mixed convective flow of a nanoliquid. Ashorynejad et al [18] deliberated on the nanofluid flow through a wavy U-turn channel. They concluded that the thermal-hydraulic functionality factor improves by boosting the volume fraction of nanoparticles. Jeong et al [19] experimentally scrutinized the impact of particle shape on the thermal conductance besides the viscosity of the nanofluid flow. They noticed that the rectangular shape nanoparticle viscosity is enhanced as compared to that of the spherical nanoparticles. Timofeeva et al [20] experimentally revealed that the nanoparticle shape played a significant role in the rise in the thermal conductance of the base fluid. They also revealed, in contrast to other types, that the blades have a greater thermal conductivity.
The investigation of nanofluids with the impacts of MHD has substantial applications in areas of metallurgy, as well as engineering development. In recent years, the cooling aspects of the heat transport equipment have been restricted, resulting in the lowered thermal conductance of traditional coolants such as H2O, ethylene glycol and oil. Metals possess greater thermal conductivity than fluids. An electrical conductivity nanofluid with the influence of the magnetic parameter known as the ferrofluid is very helpful in lots of applications. Ferrofluid consists of nanoparticles dependent on iron, such as magnetite, cobalt ferrite, hematite, etc. This kind of iron-based nanoparticle works extremely well in proficient drug transportation, by controlling the particles by means of external magnets [21, 22]. Magnetofluids are of distinctive use in magnetic cell separation, ecological remediation, malignant tumor treatment (chemotherapy and radiotherapy), magnetic resonance imaging, and magnetic particle imaging. Sheikholeslami et al [23] inspected the combined impacts of MHD and ferrohydrodynamics on the heat transport flow of ferrofluid confined in a semi annulus box with a sinusoidal warm surface. They argued that the amount of Nusselt increases both with the Rayleigh count and with a strong volume fraction. Li et al [24] addressed the impact on heat transport and ferronanofluid flow due to a magnetic field of Lorentz force and anisotropical heat conductivity. They found that with the use of MHD, vortices in the wake area are suppressed, so the flow becomes more stable. Jue [25] evaluated the influences of thermal buoyancy and magneto gradient on ferrofluid flowing inside a cavity using a numerical method. Salehpour et al [26] experimentally discussed the impacts of the alternating as well as constant magnetic fields on the MHD ferrofluid flow within a rectangle-shaped permeable channel. In light of the results of the Cattaneo-Christov heat flow model, Ali and Sandeep [27] examinated Magneto Casson heat transport of ferrofluid. Karimipour et al [28] analyzed the heat transfer flowing of MHD nanoliquid with slip velocities and temperature differences in the presence of diverse nanoparticles. The effect of quadrupole electromagnetic effect on heat transport of Mn-Zn ferrite-H2O ferrofluid flow in a circular pipe has been examined by Bahiraei et al [29]. Flow of nanofluid and heat transport with to the magnetic effect can also be initiated in [30–34].
Stretching/extending sheet flow problems are important in a vast variety of production, metallurgical and manufacturing processes. These contain polymer sheets, spinning of fibers, food processing, film coating, glass wasting, drawing of Cu wires, and so on. Sakiadis [35] found the analytical solution for a flow of boundary-layer via a continuous solid sheet. Tsou et al [36] presented the analytical and experimental analysis of heat transportation boundary layer flow past an expanding wall. Dutta [37] examined the impact of injection (suction) on heat transfer due to a movement unremitting flat sheet. The impacts of viscous and ohmic dissipations on MHD viscoelastic fluid flowing and heat transport is discussed by Abel et al [38]. Vajravelu [39] performed a study to explore the influences of thermophysical features on the flowing and heat transportation in a thin film of a Ostwald-de Waele fluid via an extending wall with viscous dissipative flow. In recent times, several articles [40–43] have been produced on the heat transport of boundary-layer nanofluid flow near an elongated surface. Notably, the consideration of nanofluid movement within a channel under the lower surface expanding into flow has not been emphasized so much. The effect of magnetic field on thermal flow in a revolving device has been seen by Borkakoti and Bharali [44]. Freidoonimehr et al [45] investigated the effects of different nanoparticles on fluid flow and heat transport in a rotating frame. Hussain et al [46] worked on the heat transportation and fluid flowing amongst parallel surfaces with carbon nanotubes. They also established that nanoparticles greatly affect skin friction and heat transfer rate. Rasool et al [47] scrutinized the effect of second-grade nanoflow over the Riga plate. They expressed that the opposite flow reduced the wall drag due to Lorentz force, and that a binary chemical reaction enriches the concentration of the nano suspension. Recent additions considering nanofluids with heat and mass transfer in various physical situations are given by [48–59].
The theme of the current article is to explore the impacts of Fe3O4 nanoparticles on the heat transport flow of H2O-based nanoliquid in a rotating frame, considering the influence of the magnetic field by using the Tiwari and Das model [60]. In this model (single-phase model) the fluid, velocity and temperature are taken as the same. The advantage of the single-phase model is that we ignore the slip mechanisms, so the model is a simplified one and is easy to solve numerically. However, the disadvantage of this method is that in some cases the numerical results differ from those obtained by experiments. In this model, the volume concentration of nanoparticles ranges between 3% and 20%. Numerical solutions by shooting procedure are applied to the governing scheme of nonlinear ordinary differential equations. Emphasis is given to the effect of embedded flow factors on the velocities and temperature outlines. The flow, along with thermal fields, are discussed by plotting graphs. Additionally, the graphs of surface drag force coefficient and heat transport rate (local number of Nusselt) are plotted to evaluate the coefficient of skin friction and the rate of heat exchange for the volume fraction of nanoparticles, together with other relevant parameters.
2. Problem formulation
Let us contemplate a steady MHD rotating flow of H2O-based Fe3O4 nanofluids between two plates having angular swiftness ${\boldsymbol{\Omega }}$ $[0,{\rm{\Omega }},0].$ The lower surface is stretched in the x-direction having the velocity ${U}_{w}=ax\left(a\gt 0\right)$ and the higher surface is permeable. The steady flow field is represented by ${\boldsymbol{V}}$ $\left[u,v,w\right],$ wherein $u,v,w$ are the swiftness components alongside the x, y and z orientations accordingly. A unvarying magneto impact of strength ${B}_{0}$ is worked parallel to the y-axis. Using the presumption of tiny magnetic Reynolds, the caused magneto field effect is unchecked. The physical configuration of flowing is specified in figure 1.Figure 1.
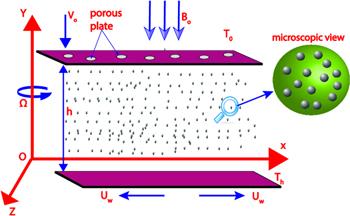
Figure 1.Geometry of the problem.
In case of the rotating flow, the conservative momentum equation is given as [61]
Nanofluid active density [60] is described as
For uniform injection/suction, the velocity component $v$ is fixed at the top surface due to the porosity. The temperature gradient is created across the fluid such that the upper surface has less temperature ${T}_{0}$ than the lower surface temperature ${T}_{h},$ i.e. ${T}_{0}\lt {T}_{h}.$ Thermophysical features of water and magnetite are prearranged in table 1.
Table 1.
Table 1.Thermophysical features of water and magnetite [23].
Physical properties | Water | Magnetite |
---|---|---|
ρ (kg m−3) | 997 | 5180 |
${c}_{p}$ (J kg−1 K) | 4179 | 670 |
$k$ (W m−1 K) | 0.613 | 9.7 |
Σ (ω−1 m−1) | 0.05 | 25000 |
New window|CSV
The end point conditions at the upper and lower walls are provided below.
Making use of the similarity transformation earlier mentioned, equation (
3. Methodology of solution
The equations (The system of nonlinear ordinary-differential formulas (
The nonlinear energy and momentum equations are transformed into the next eight first-order schemes of ODEs together with the initial conditions. The flow chart of the shooting method is displayed in figure 2.
Figure 2.
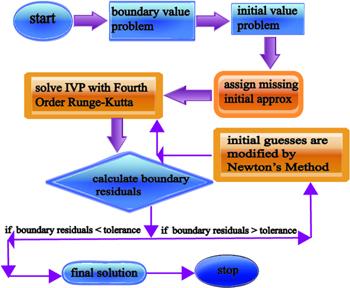
Figure 2.Computational flowchart for shooting method.
Table 2.
Table 2.Comparison of ${C}_{f}R{e}_{x}^{1/2}$and $R{e}_{x}^{-1/2}N{u}_{x}$ with results of reference [46] for diverse values of $S$ and $\phi $ at lower/upper surface.
${C}_{f}R{e}_{x}^{1/2}$ at $\eta =0$ | $R{e}_{x}^{-1/2}N{u}_{x}$ at $\eta =0$ | ${C}_{f}R{e}_{x}^{1/2}$ at $\eta =1$ | $R{e}_{x}^{-1/2}N{u}_{x}$ at $\eta =1$ | ||||||
---|---|---|---|---|---|---|---|---|---|
$S$ | $\phi $ | Present | Reference [46] | Present | Reference [46] | Present | Reference [46] | Present | Reference [46] |
−1 | 0 | −9.54155 | −9.54155 | 0.39001 | 8.85752 | 0.39001 | 8.85752 | 4.82296 | 4.82296 |
0 | 0 | −4.09595 | −4.09595 | 1.33610 | 1.33610 | 1.95289 | 1.95289 | 0.80249 | 0.80249 |
1 | 0 | 2.23565 | 2.23565 | 2.19498 | 2.19498 | −3.81099 | −3.81099 | 0.05776 | 0.05776 |
New window|CSV
4. Results and discussion
The numerical estimations of $R{e}_{x}^{-1/2}N{u}_{x}\,$ besides ${C}_{f}R{e}_{x}^{1/2}$ for a variety of values of the Reynolds number ${A}_{1},$ rotating parameter ${A}_{2},$ magneto parameter ${A}_{3},$ injection (suction) parameter S and volume fraction of nanoparticle φ are available in tables 3–6. From table 3, it is found that a surge of the concentration of nanoparticles φ is inclined to reduce the local skin friction at lower surface, and a similar trend is noted for the upper surface regarding table 4. Table 5 tells us that an upsurge in the nanoparticles volume concentration φ is inclined to improve the heat rate for $S=-1$ and diminish the heat rate for $S=0,1$ at the lower surface, although an opposite trend is noticed for the upper surface regarding table 6.Table 3.
Table 3.Values of ${C}_{f}R{e}_{x}^{1/2}$ at $\eta =0$ for diverse amounts of the emergent parameters at lower surface ($Pr=6.2,m=3$).
${A}_{2}=0,{A}_{3}=0$ | ${A}_{2}=0,{A}_{3}=0$ | ${A}_{2}=0,{A}_{3}=1$ | ${A}_{2}=1,{A}_{3}=1$ | ||||||
---|---|---|---|---|---|---|---|---|---|
$S$ | $\phi \,$ | ${A}_{1}=0.5$ | ${A}_{1}=1$ | ${A}_{1}=0.5$ | ${A}_{1}=1$ | ${A}_{1}=0.5$ | ${A}_{1}=1$ | ${A}_{1}=0.5$ | ${A}_{1}=1$ |
−1 | 0.0 | −9.73485 | −9.46810 | −9.79701 | −9.54155 | −9.85479 | −9.71457 | −9.91343 | −9.77916 |
.05 | −9.13191 | −8.86501 | −9.19873 | −8.94492 | −9.26257 | −9.13383 | −9.32502 | −9.20260 | |
0.1 | −8.90239 | −8.63544 | −8.97118 | −8.71810 | −9.04916 | −8.93734 | −9.11280 | −9.00691 | |
0 | 0.0 | −4.04282 | −4.08556 | −4.05316 | −4.09595 | −4.10870 | −4.21578 | −4.11862 | −4.22533 |
.05 | −3.80166 | −3.84440 | −3.81267 | −3.85545 | −3.87325 | −3.98571 | −3.88373 | −3.99574 | |
0.1 | −3.70986 | −3.75259 | −3.72115 | −3.76393 | −3.79018 | −3.91095 | −3.80085 | −3.92109 | |
1 | 0.0 | 2.10694 | 2.21327 | 2.13398 | 2.23565 | 2.08922 | 2.17591 | 2.11487 | 2.19632 |
.05 | 1.98635 | 2.09260 | 2.01478 | 2.11584 | 1.96702 | 2.05181 | 1.99379 | 2.07274 | |
0.1 | 1.94044 | 2.04667 | 1.96944 | 2.07024 | 1.91874 | 2.00092 | 1.94581 | 2.02185 |
New window|CSV
Table 4.
Table 4.Values of ${C}_{f}R{e}_{x}^{1/2}$ at $\eta =1$ for diverse amounts of the emergent parameters at upper surface ($Pr=6.2,m=3$).
${A}_{2}=0,{A}_{3}=0$ | ${A}_{2}=0,{A}_{3}=0$ | ${A}_{2}=0,{A}_{3}=1$ | ${A}_{2}=1,{A}_{3}=1$ | ||||||
---|---|---|---|---|---|---|---|---|---|
S | $\phi $ | ${A}_{1}=0.5$ | ${A}_{1}=1$ | ${A}_{1}=0.5$ | ${A}_{1}=1$ | ${A}_{1}=0.5$ | ${A}_{1}=1$ | ${A}_{1}=0.5$ | ${A}_{1}=1$ |
−1 | 0.0 | 8.38630 | 8.80893 | 8.43150 | 8.85752 | 8.41637 | 8.86134 | 8.45885 | 8.90381 |
.05 | 7.90512 | 8.33141 | 7.95344 | 8.38359 | 7.93761 | 8.38735 | 7.98257 | 8.43195 | |
0.1 | 7.72200 | 8.14982 | 7.77163 | 8.20351 | 7.75840 | 8.21225 | 7.80408 | 8.25710 | |
0 | 0.0 | 1.97639 | 1.95318 | 1.97585 | 1.95289 | 1.96054 | 1.92301 | 1.95995 | 1.92260 |
.05 | 1.85583 | 1.83265 | 1.85527 | 1.83238 | 1.83865 | 1.80013 | 1.83804 | 1.79970 | |
0.1 | 1.80993 | 1.78677 | 1.80937 | 1.78651 | 1.79071 | 1.75049 | 1.79008 | 1.75005 | |
1 | 0.0 | −3.88037 | −3.77309 | −3.92117 | −3.81099 | −3.94475 | −3.89718 | −3.98358 | −3.93178 |
.05 | −3.63962 | −3.53346 | −3.68284 | −3.57339 | −3.70947 | −3.66769 | −3.75030 | −3.70367 | |
0.1 | −3.54799 | −3.44230 | −3.59221 | −3.48305 | −3.62631 | −3.59253 | −3.66774 | −3.62872 |
New window|CSV
Table 5.
Table 5.Values of $R{e}_{x}^{-1/2}N{u}_{x}\,$at $\eta =0$ for diverse amounts of the emergent parameters at lower surface ($Pr=6.2,m=3$).
${A}_{2}=0,{A}_{3}=0$ | ${A}_{2}=0,{A}_{3}=0$ | ${A}_{2}=0,{A}_{3}=1$ | ${A}_{2}=1,{A}_{3}=1$ | ||||||
---|---|---|---|---|---|---|---|---|---|
$S$ | $\phi $ | ${A}_{1}=0.5$ | ${A}_{1}=1$ | ${A}_{1}=0.5$ | ${A}_{1}=1$ | ${A}_{1}=0.5$ | ${A}_{1}=1$ | ${A}_{1}=0.5$ | ${A}_{1}=1$ |
−1 | 0.0 | 0.67952 | 0.39074 | 0.67911 | 0.39001 | 0.67831 | 0.38720 | 0.67792 | 0.38656 |
0.05 | 0.72001 | 0.45850 | 0.71957 | 0.45763 | 0.71873 | 0.45436 | 0.71832 | 0.45362 | |
0.1 | 0.75438 | 0.51950 | 0.75396 | 0.51859 | 0.75304 | 0.51488 | 0.75265 | 0.51412 | |
0 | 0.0 | 1.16185 | 1.33661 | 1.16161 | 1.33610 | 1.16061 | 1.33143 | 1.16038 | 1.33096 |
0.05 | 1.14116 | 1.29207 | 1.14092 | 1.29157 | 1.13991 | 1.28691 | 1.13968 | 1.28646 | |
0.1 | 1.12372 | 1.25487 | 1.12350 | 1.25441 | 1.12247 | 1.24974 | 1.12226 | 1.24933 | |
1 | 0.0 | 1.62894 | 2.19513 | 1.62886 | 2.19498 | 1.62793 | 2.19164 | 1.62785 | 2.19150 |
0.05 | 1.55400 | 2.06685 | 1.55390 | 2.06665 | 1.55296 | 2.06314 | 1.55287 | 2.06295 | |
0.1 | 1.48916 | 1.95237 | 1.48907 | 1.95215 | 1.48810 | 1.94848 | 1.48801 | 1.94828 |
New window|CSV
Table 6.
Table 6.Values of $R{e}_{x}^{-1/2}N{u}_{x}\,$at $\eta =1$ for diverse amounts of the emergent parameters at upper surface ($Pr=6.2,m=3$).
${A}_{2}=0,{A}_{3}=0$ | ${A}_{2}=0,{A}_{3}=0$ | ${A}_{2}=0,{A}_{3}=1$ | ${A}_{2}=1,{A}_{3}=1$ | ||||||
---|---|---|---|---|---|---|---|---|---|
$S$ | $\phi $ | ${A}_{1}=0.5$ | ${A}_{1}=1$ | $A{}_{1}=0.5$ | ${A}_{1}=1$ | ${A}_{1}=0.5$ | ${A}_{1}=1$ | ${A}_{1}=0.5$ | ${A}_{1}=1$ |
−1 | 0.0 | 2.43038 | 4.82218 | 2.43055 | 4.82296 | 2.43193 | 4.83047 | 2.43209 | 4.83117 |
.05 | 2.20060 | 4.14128 | 2.20078 | 4.14220 | 2.20212 | 4.14988 | 2.20229 | 4.15068 | |
0.1 | 2.01768 | 3.60497 | 2.01785 | 3.60587 | 2.01917 | 3.61358 | 2.01933 | 3.61435 | |
0 | 0.0 | 0.89872 | 0.80217 | 0.89889 | 0.80249 | 0.89964 | 0.80560 | 0.89981 | 0.80590 |
.05 | 0.91101 | 0.82579 | 0.91118 | 0.82611 | 0.91195 | 0.82930 | 0.91212 | 0.82960 | |
0.1 | 0.92151 | 0.84603 | 0.92167 | 0.84634 | 0.92246 | 0.84961 | 0.92261 | 0.84989 | |
1 | 0.0 | 0.26551 | 0.05769 | 0.26564 | 0.05776 | 0.26592 | 0.05810 | 0.26605 | 0.05817 |
.05 | 0.31627 | 0.08475 | 0.31642 | 0.08485 | 0.31675 | 0.08535 | 0.31690 | 0.08544 | |
0.1 | 0.36629 | 0.11706 | 0.36646 | 0.11719 | 0.36685 | 0.11787 | 0.36700 | 0.11799 |
New window|CSV
Results are described in figures 3–7 for the study of the nanofluid flow and heat transport showing the velocity $f^{\prime} \left(\eta \right),$ $g\left(\eta \right)$ and temperature profile $\theta \left(\eta \right)$ variance within the geometry-defined constrained domain. Figures 3(a)–(c) describe the impact of the diverse amounts of nanoparticle concentration $\phi $ on $f^{\prime} \left(\eta \right),$ $g\left(\eta \right)$ and $\theta \left(\eta \right).$ Figure 3(a) shows that there is a small variation in the velocity $f^{\prime} \left(\eta \right)$ with an increase in $\phi $; however it may be noticed within the insertion of the figure that Fe3O4 has a comparatively higher velocity profile in comparison with the base fluid. For varied $\phi $ values, figure 3(b) exposes the variation in $g\left(\eta \right).$ We can see that the standard liquid has moderately larger velocity outline in comparison with the water -based magnetite. Difference of temperature outlines with $\phi $ is demonstrated in figure 3(c). We can see in figure 3(c) that with an increment in the nanoparticle concentration $\phi ,$ the distribution of temperature is enhanced.
Figure 3.
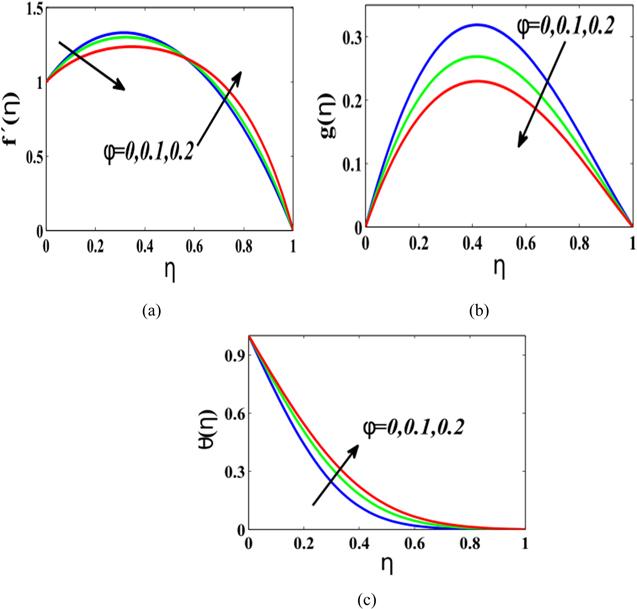
Figure 3.(a) $f^{\prime} \left(\eta \right),$ (b) $g\left(\eta \right),$ (c) $\theta \left(\eta \right)\,$ for nanoparticle concentration $\phi $ when ${A}_{1}={A}_{2}={A}_{3}=2,S=1.$
Figure 4.
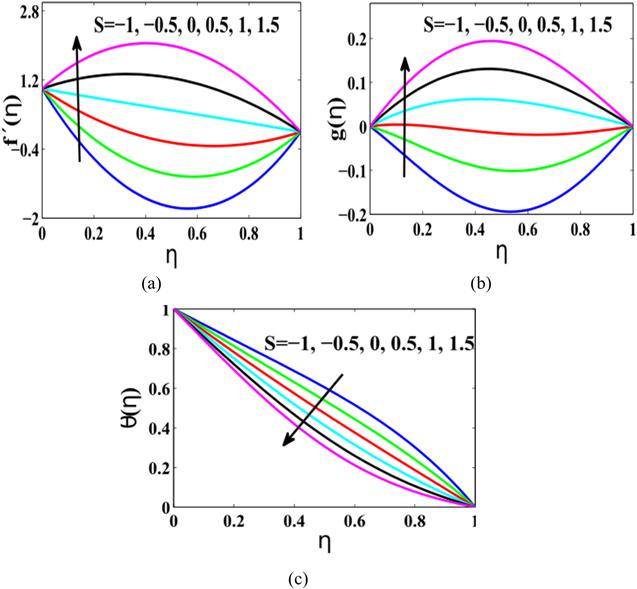
Figure 4.(a) $f^{\prime} \left(\eta \right),$ (b) $g\left(\eta \right),$ (c) $\theta \left(\eta \right)\,$ for magnetite-water nanofluid with parameter S when ${A}_{1}={A}_{2}={A}_{3}=0.5,\phi =0.2.$
Figure 5.
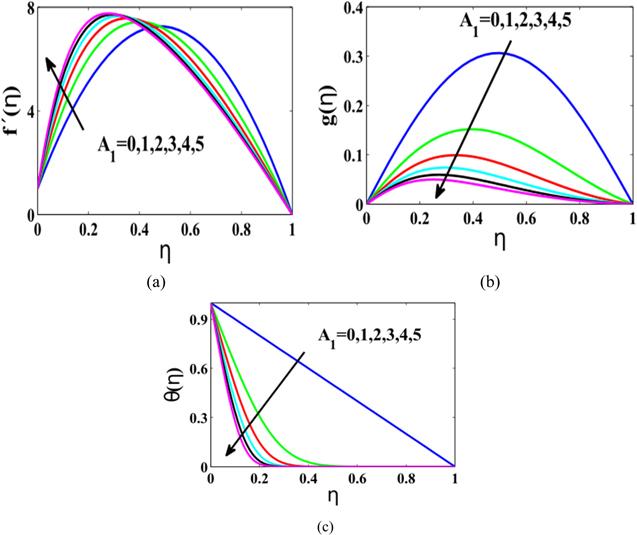
Figure 5.(a) $f^{\prime} \left(\eta \right),$ (b) $g\left(\eta \right),$ (c) $\theta \left(\eta \right)\,$ for magnetite-water nanofluid with parameter S when ${A}_{2}=0.2,{A}_{3}=0,\phi =0.2,S=5.$
Figure 6.
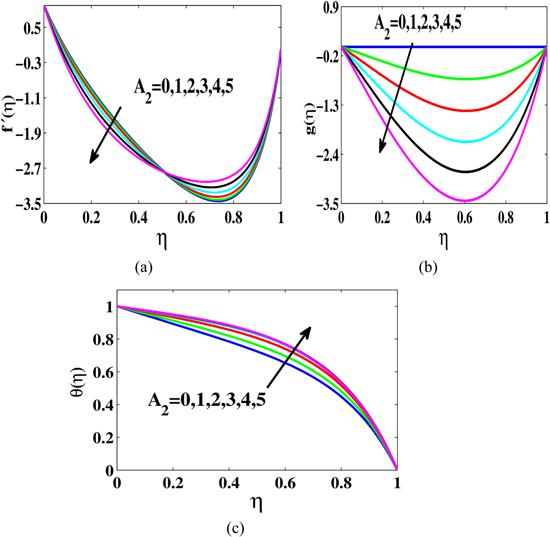
Figure 6.(a) $f^{\prime} \left(\eta \right),$ (b) $g\left(\eta \right),$ (c) $\theta \left(\eta \right)\,$ for magnetite-water nanofluid with parameter ${A}_{2}$ when ${A}_{1}=0.2,{A}_{3}=0,\phi =0.2,S=-3.$
Figure 7.
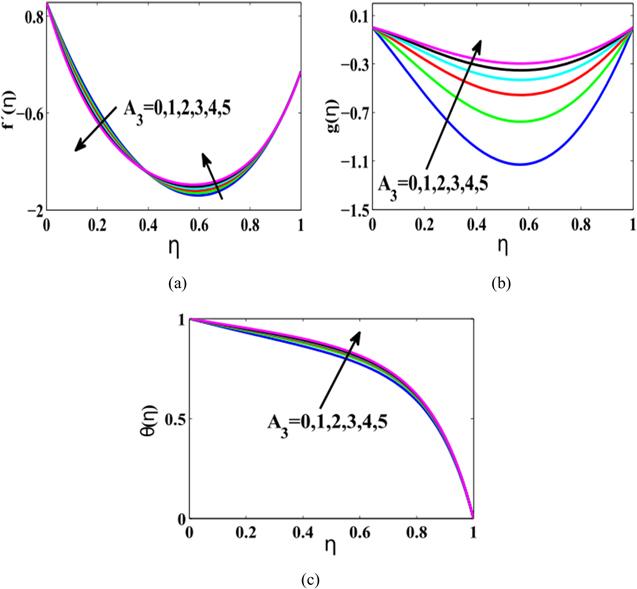
Figure 7.(a) $f^{\prime} \left(\eta \right),$ (b) $g\left(\eta \right),$ (c) $\theta \left(\eta \right)\,$ for magnetite-water nanofluid with parameter ${A}_{3}$ when ${A}_{1}=2,{A}_{2}=2,\phi =0.2,S=-1.$
Figures 4(a)–(c) display the impact of injection/suction parameter S on the velocities and temperature. For the injection/suction case, the velocity profile $f^{\prime} \left(\eta \right)$ and $g\left(\eta \right)$ get bigger. Furthermore, it might be noticed that a distinction in the velocities is remarkable at the mean position of the channel. Besides that, the extreme amount of the swiftness moves marginally toward the lower surface for non-negative S, while for negative S it moves marginally toward the higher surface. With diverse amounts of the suction (blowing) parameter $S,$ figure 4(c) provides the temperature distribution profile. It can be identified that escalating the injection/suction parameter $S,$ thwarts the temperature distribution; hence it offers a reduction in the temperature field.
Figures 5(a)–(c) pronounce the influence of the parameter ${A}_{1}$ on swiftness and temperature domain. Figure 5(a) indicates two distinctive characteristics of the velocity field for the parameter ${A}_{1}$ and it is found that velocity field swaps the behaviour from rising to reducing for various values of ${A}_{1}.$ This outcome is mostly a consequence of the expanding of the lesser surface. The velocity distribution $g\left(\eta \right)$ in figure 5(b) exhibits a uniform reducing behaviour for greater values of ${A}_{1}.$ In case the lower plate is fixed, the velocity displays a symmetrical behaviour at the central position. On the other hand, the the highest value of the velocity field moves marginally toward the lower plate when the value of ${A}_{1}$ is enhanced. The thermal field $\theta \left(\eta \right)\,$exhibits a reducing behaviour with a boost in the values of ${A}_{1}$ (figure 5(c)). In case of the lower plate at rest (i.e. ${A}_{1}=0$), the thermal field manifests a linear reducing behaviour, although a nonlinear lessening behaviour is found for the remainder of the values of ${A}_{1}.$
Figures 6(a)–(c) are sketched to observe the influence of ${A}_{2}$ on the dynamics of the velocities $f^{\prime} \left(\eta \right),$ $g\left(\eta \right)$ and thermal field $\theta \left(\eta \right)\,.$ Figure 6(a) elaborates the change in the speed distribution $f^{\prime} \left(\eta \right),$ inside the constrained area exhibiting a double natural behaviour. It is noted that the swiftness distribution $f^{\prime} \left(\eta \right),$ reveals a lessening behaviour inside the domain $0\leqslant \eta \lt 0.5,$; however the outcomes are entirely different inside the domain $0.5\lt \eta \leqslant 1.$ In figure 6(b), it is noted that there is no variation in vertical velocity component when ${A}_{2}=0,$ and consequently the problem reduces to the steady 2D flow without having the rotation parameter. However, it is obvious that an escalation in the values of ${A}_{2}$ reduces the velocity distribution $g\left(\eta \right).$ Furthermore, fluctuation in the velocity is bigger at the central position when compared with the upper as well as lower surfaces. Figure 6(c) implies that the temperature field $\theta \left(\eta \right)\,$is enhanced when the rotation parameter ${A}_{2}$ goes up.
Figures 7(a)–(c) explore the impact of the magneto parameter ${A}_{3}$ on velocities and thermal fields. Figure 7(a) yields dual characteristics of the flow field $f^{\prime} \left(\eta \right),$ within the constrained domain. It can be seen that the velocity profile $f^{\prime} \left(\eta \right),$ demonstrates a lessening behaviour for growing values of the magnetic parameter ${A}_{3}$ within the domain $0\leqslant \,\eta \lt 0.4,$ while the reverse behaviour is found in the domain $0.4\lt \eta \leqslant 1.$ The velocity distribution $g\left(\eta \right)$ offers the escalating behaviour for the rising values of ${A}_{3}$ as shown in figure 7(b). Also, it can be viewed that variation in the velocity is higher at the central position when compared with the upper as well as lower surfaces. Figure 7(c) suggests the influence of the electomagnetic field ${A}_{3}$ on thermal distribution $\theta \left(\eta \right).$ It is observed that heat is enhanced for greater amounts of ${A}_{3}.$
The drag coefficient of the nanofluid is examined at the lesser plate of the channel, and outcomes are designed for various parameters. Figure 8(a) displays the impact of $\phi $ and $S$ on the drag force factor. It is seen that the drag force absolute values escalate as $\phi $ rises for $S\,=\,0,-1,$; however it declines for S=1. Figures 8(b)–(d) portray the difference in the drag force with nanoparticle concentration $\phi .$ Drag force factor reduces with a rise in $\phi .$ The outcomes suggest that it is raised with a boost in ${A}_{1}$ and ${A}_{2}$, but it lessens with an intensification of the electromagnetic field ${A}_{3}.$ Figures 9(a)–(d) depict the impact of physical parameter on the drag force coefficient at the higher surface of the duct. Largely, friction coefficient indicates a reducing behaviour with respect to $\phi $, regardless of the extra related factors. For ${A}_{1},$ the drag force at the higher plate displays a diminishing behaviour.
Figure 8.

Figure 8.Change of $R{e}_{x}^{1/2}{C}_{f}$ at $\eta =0$ for diverse values of (a) S, (b) ${A}_{1},$ (c) ${A}_{2},$ (d) ${A}_{3}.$
Figure 9.
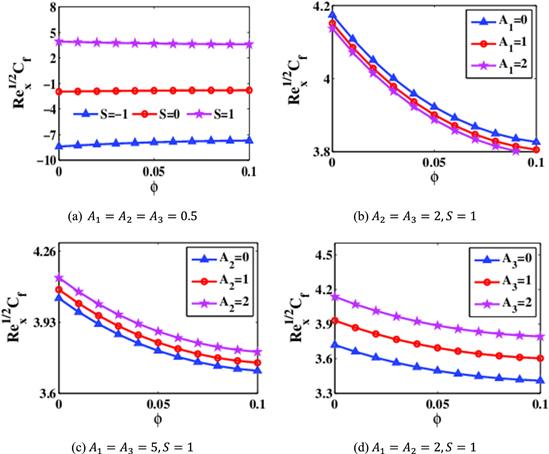
Figure 9.Change of $R{e}_{x}^{1/2}{C}_{f}$ at $\eta =1$ for diverse values of (a) S, (b) ${A}_{1},$ (c) ${A}_{2},$ (d) ${A}_{3}.$
Figures 10(a)–(d) demonstrate the variation of rate of heat transport at lower plate versus the nanoparticle concentration. In figure 10(a), it is noted that for S=0 and S=1, there is a declining behaviour in the heat transport rate with $\phi .$ However, the impact of $S\,$= −1 is reverse in nature with respect to $\phi .$ The impact of ${A}_{1},$ ${A}_{2},$ ${A}_{3}$ and $\phi $ on the rate of heat transportation is plotted in figures 10(a)–(d). It is noticed that there is a surge in rate of heat $N{u}_{x}$ with the enhancement in $\phi .$ Furthermore it is observed that Fe3O4 possesses advanced heat transport rate in contrast with the standard liquid. Figures 11(a)–(d) display the dynamics of the heat transfer rate versus Fe3O4 volume fraction at the upper surface. Figures 11(a)–(d) exhibit a rise in $N{u}_{{\rm{x}}}$ producing the enhancing values of $S,$ ${A}_{1},$ ${A}_{2}$ and ${A}_{3}.$ From figure 11(b), we assert that $N{u}_{{\rm{x}}}$ is a reducing function of the concentration $\phi .$ Streamlined variations are plotted in figures 12(a)–(c) for diverse amounts of S. It is seen from figures 12(a)–(c) that the gaps between stream lines decrease with increasing the magnitude of the injection/suction parameter $S.$ The injection/suction parameter S thus significantly alters the fluid dynamics of the stretching sheet region.
Figure 10.
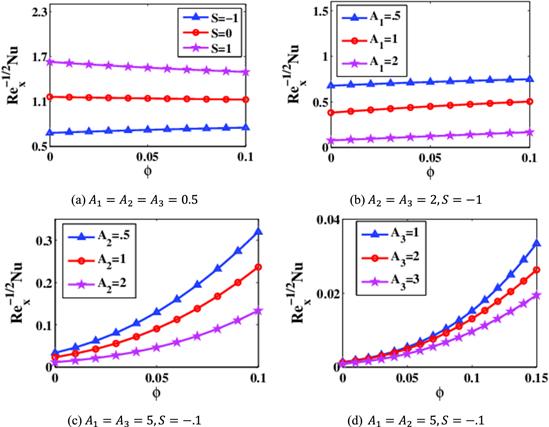
Figure 10.Change of $R{e}_{x}^{-1/2}N{u}_{x}$ at $\eta =0$ for various values of (a) S, (b) ${A}_{1},$ (c) ${A}_{2},$ (d) ${A}_{3}.$
Figure 11.
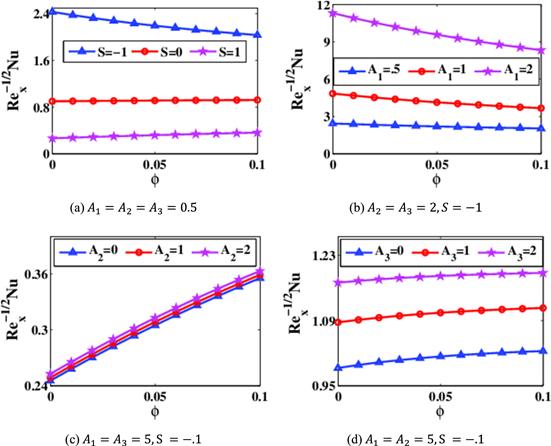
Figure 11.Change of $R{e}_{x}^{-1/2}N{u}_{x}$ at $\eta =1$ for diverse values of (a) S, (b) ${A}_{1},$ (c) ${A}_{2},$ (d) ${A}_{3}.$
Figure 12.
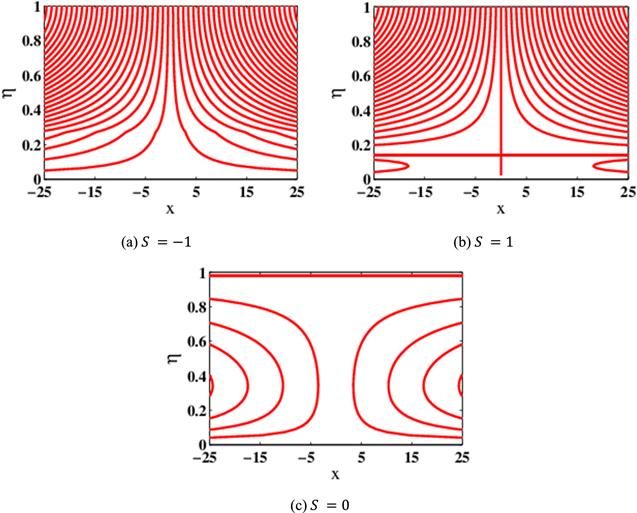
Figure 12.Change of streamlines for diverse S values.
5. Conclusions
In the current research, the rotating flow of magnetite-water nanofluid past a stretching surface in the existence of the electromagneto impact is examined. With the aid of graphs, impacts of magnetite nanoparticles on the drag force as well as the Nusselt number are described. The key findings of the analysis are provided below:The concentration of nanoparticles increases the velocity, along with the temperature of the nanofluid.The flow field is emphatically impacted by the injection/suction parameter.
A surge in the magnetic as well as rotation factor results in a boost in the thermal field.
The rate of heat transfer boosts for the magnetite-water nanofluid when compared to that for the standard fluid against the concentration of nanoparticles.
The magnetic parameter augments the Nusselt number, although it diminishes the coefficient of the drag force.
Drag force coefficient is lower for the magnetite-water nanofluid as compared to that for the standard fluid against the nanoparticle concentration.
The rotation factor tends to increase the drag coefficient, although it slightly diminishes the Nusselt number.
Reference By original order
By published year
By cited within times
By Impact factor
DOI:10.2306/scienceasia1513-1874.2014.40S.058 [Cited within: 1]
DOI:10.1007/BF00945764 [Cited within: 1]
DOI:10.1016/j.mechrescom.2003.09.004 [Cited within: 1]
DOI:10.1016/j.molliq.2015.08.026 [Cited within: 1]
DOI:10.1108/MMMS-05-2017-0042 [Cited within: 1]
DOI:10.1016/j.molliq.2018.07.071 [Cited within: 1]
DOI:10.1007/s00396-018-4374-z [Cited within: 1]
[Cited within: 1]
DOI:10.1115/1.2150834 [Cited within: 1]
DOI:10.1115/1.3056479 [Cited within: 1]
DOI:10.1080/01457630701850851
DOI:10.1080/01457630600904593
DOI:10.1080/17455030.2020.1810365 [Cited within: 1]
DOI:10.1080/08916159808946559 [Cited within: 1]
DOI:10.1016/j.apt.2015.03.012 [Cited within: 1]
DOI:10.1007/s40997-017-0083-3 [Cited within: 1]
DOI:10.1016/j.ijheatmasstransfer.2018.04.088 [Cited within: 1]
DOI:10.1016/j.ijheatmasstransfer.2017.11.117 [Cited within: 1]
DOI:10.1016/j.ijrefrig.2013.07.024 [Cited within: 1]
DOI:10.1063/1.3155999 [Cited within: 1]
DOI:10.1016/S0304-8853(02)00706-0 [Cited within: 1]
DOI:10.1016/S0304-8853(99)00062-1 [Cited within: 1]
DOI:10.1016/j.energy.2014.07.089 [Cited within: 2]
DOI:10.3390/en10071065 [Cited within: 1]
DOI:10.1016/j.icheatmasstransfer.2006.02.001 [Cited within: 1]
DOI:10.1016/j.expthermflusci.2017.08.032 [Cited within: 1]
DOI:10.1016/j.rinp.2016.11.055 [Cited within: 1]
DOI:10.1016/j.physe.2016.10.015 [Cited within: 1]
DOI:10.1007/s10948-013-2299-9 [Cited within: 1]
DOI:10.1016/j.cnsns.2011.05.035 [Cited within: 1]
DOI:10.1016/j.proeng.2016.08.371
DOI:10.1007/s13369-020-04943-3
DOI:10.1038/s41598-020-71543-4
DOI:10.1016/j.surfin.2021.100971 [Cited within: 1]
DOI:10.1002/aic.690070211 [Cited within: 1]
DOI:10.1016/0017-9310(67)90100-7 [Cited within: 1]
DOI:10.1002/zamm.19880680617 [Cited within: 1]
DOI:10.1016/j.cnsns.2007.04.007 [Cited within: 1]
DOI:10.1016/S1001-6058(13)60333-9 [Cited within: 1]
DOI:10.1016/j.ijmecsci.2017.07.064 [Cited within: 1]
DOI:10.1016/j.jmmm.2014.08.021
DOI:10.1016/j.molliq.2016.05.005
DOI:10.1166/jon.2017.1347 [Cited within: 1]
DOI:10.1090/qam/693878 [Cited within: 1]
DOI:10.1155/2014/692728 [Cited within: 1]
DOI:10.1016/j.molliq.2015.11.042 [Cited within: 8]
DOI:10.1088/1402-4896/ab3990 [Cited within: 1]
DOI:10.1515/phys-2020-0191 [Cited within: 1]
DOI:10.1088/0253-6102/69/4/441
DOI:10.1088/0253-6102/68/3/387
DOI:10.1088/1572-9494/aba250
DOI:10.1007/s13204-020-01625-2
DOI:10.3390/sym12091421
DOI:10.1002/num.22705
DOI:10.1007/s10973-020-09865-8
DOI:10.1002/er.6554
DOI:10.1016/j.icheatmasstransfer.2020.104973
DOI:10.1088/1402-4896/abecc0 [Cited within: 1]
DOI:10.1016/j.ijheatmasstransfer.2006.09.034 [Cited within: 2]
DOI:10.1007/s13369-019-04257-z [Cited within: 1]
DOI:10.1063/1.1700493 [Cited within: 1]
DOI:10.1016/S0017-9310(03)00156-X [Cited within: 1]
[Cited within: 1]
[Cited within: 1]