全文HTML
--> --> -->除此之外, 共聚焦激光扫描显微镜(confocal laser scanning microscopy, CLSM)因具有高分辨率与深度选择性也得到广泛应用[5]. 相对于其他方法, 它结构简单、非侵入式、无需样品的先验知识, 因此适用于大多数样品, 在生物活体研究方面有很大优势. 不过, 在一般条件下(空气环境中或油浸), 它的分辨率只达到180 nm左右, 不及几种常用的荧光超分辨显微技术. 近年来, 有不少关于柱对称矢量光场的研究提供了提高CLSM分辨率的方法. 利用经空间调制的径向偏振光可以得到一个更小的聚焦光斑, 适用于空气中、液体浸润和固体浸润环境中[6—9]. 文献[10]采用532 nm波长的高对称径向偏振光场为激发光源, 通过光场调控实现矢量光场CLSM的点扩散函数的约束, 实现了115 nm的分辨率, 比一般的共聚焦显微镜提高了不少. 该结果是在纳米铝三角岛样品上一个尖角处测得的, 与许多文献用到的分辨率测试方法类似[3,10—15], 都是对分散的粒子或单一结构成像, 再根据结果算出该显微镜的分辨率. 这种测试方法只能说明显微镜有能力分辨某一大小的物体或者某给定间隔的两个物体, 无法提供足够多的数据进行对比, 也无法精确地描述超分辨显微镜的分辨率, 故需要足够精确与严谨的方法用于准确检测矢量光场CLSM的分辨率. 此外, 在矢量光场CLSM中, 矢量光场可以提供高对称度的激发与探测方式[6], 避免线性偏振光场的非对称聚焦光斑[16], 在这种情况下, 更需要标准样品来检测各个方向上的偏差, 以保证光路中光场的高对称度, 从而减小实验误差. 人们在检测摄像机或传统光学显微镜的最佳分辨率时, 常用推荐性国家标准GB/T 6161-2008 (等同于ISO 3334: 2006标准)中的ISO 2号解像力测试图进行测试[17], 该解像力测试图由一系列测试图样组成, 单个测试图样包含两组相互垂直的平行线段, 每一组5条线段, 线段的线宽与间隔等宽. 该标准以测试图样的5条线段能否全部被辨别作为系统分辨能力的判断依据. 参照该判断依据, 针对CLSM点扫描式的特点, 本文提出纳米分辨率测试标准样品(以下简称纳米标样)应具备以下特点: 多方向的周期性测量图案、合理紧密的线宽梯级序列分布、明确的指示标记图案、高精确度和高对比度等.
2.1.设计方案
目前, 与纳米标样相关的成果包括: Stark团队[18]利用聚焦离子束刻蚀技术, 在掺有荧光分子的聚甲基丙烯酸甲酯(poly(methyl methacrylate), PMMA)电子胶上刻出若干等宽 (100 nm)的纳米线条和同心圆环; Iketaki团队[19]利用紫外纳米压印技术, 在染色紫外光刻胶上制备出多组纳米线条, 包含从80 nm到160 nm的线宽; Huebner团队[20]运用电子束曝光与刻蚀技术, 在非晶硅上制备多组纳米标记图案, 包括线条、棋盘和圆环三种图形, 可用于多个方向上的分辨率测试. 然而, 以上方法都没有合理的线宽梯级序列, 无法达到精确测试超分辨显微系统性能的目的.图1所示是本工作提供的纳米标样设计方案, 分为测量区域和指示标记两个区域. 其中, 测量区域包括了29个测量图案, 它们按照空间频率递增的方式, 螺旋排列于测量区域. 每一个测量图案都包含了5个部件, 包括一维光栅 (X方向和Y方向)、二维光栅、同心圆环光栅和数码标识. 在测量区域周围四个方向上分布了大小两种直角三角形指示标记, 它们指向测量区域, 能够明确地指出测量区域的位置. 该设计方案具有测试功能齐全、测量精度高、测量范围宽、图案排列紧凑、线宽序列分布合理、指示标记巧妙等优点, 适用于点扫描式的超分辨显微系统, 如矢量光场CLSM.
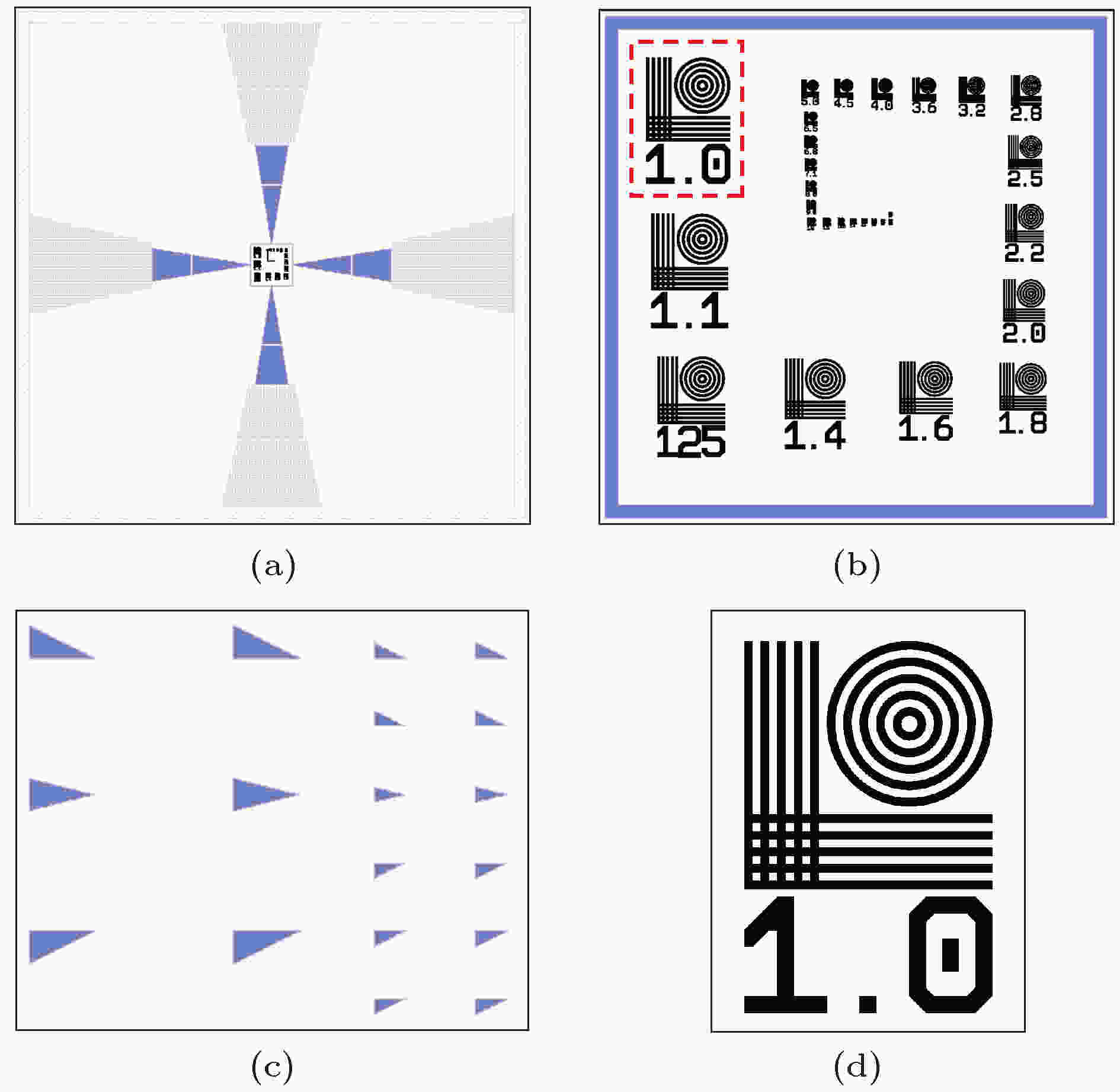
Figure1. Designing of the nanoscale standard sample: (a) Over-view of the standard sample; (b) measure area; (c) direction marks; (d) a single measure pattern.
另一方面, 设计方案中不同的结构线宽大小相差高达25倍, 这会给制备带来困难. 在制备时要同时考虑效率与精确程度, 应采用不同工艺参数实现不同的结构.
3
2.1.1.测量区域
测量区域是一个大小为150 μm × 150 μm的区域, 测量区域的设计参考了GB/T 6161-2008 ISO 2号解像力测试图[17], 并加以改进, 使之功能更全面. 如图1(b)所示, 测量区域一共包括29个测量图案, 其梯级序列参考了国家标准GB/T 321-2005所提供的R20系列优先数[21], 从1.0开始, 以空间频率递增的方式呈螺旋排列. 如图1(d)所示, 每个测量图案包含的4组光栅(水平方向一维光栅、垂直方向一维光栅、二维光栅、同心圆环光栅)都是等间距分布, 且结构宽度与间隔相等, 可以用于多方向的分辨率测试, 同时可以用于检验显微系统的畸变情况. 而数码标识对应测量图案中各组光栅每微米空间频率大小的两倍, 单位是cycles/μm, 恰好是各组光栅结构线宽(以μm为单位)的倒数, 因此通过辨认数码标识就可以直接得出该测量图案结构的线宽大小.综上, 测量图案包含多个方向上的周期性结构, 功能齐全, 且拥有合理的线宽序列和紧凑的排列方式, 只需要在测试区内小范围移动样品就可以快速找到临界测试位置. 一次测试结果就可以得到不同方向和位置的分辨率数据, 同时可以检测畸变程度等其他性能指标, 能够有效全面地测试显微镜的性能, 为矢量光场CLSM的性能测试和调试提供了一种更加严谨的途径.
3
2.1.2.指示标记
在点扫描式的CLSM中, 要在空白背景下寻找150 μm × 150 μm大小的测量区域是非常困难的, 因此需要指示标记来帮助我们快速寻找测量区域的位置.如图1(c)所示, 指示标记为分布在测量区域四个方向上的直角三角阵列, 以其最小的锐角为方向指向测量区域中心. 指示标记按照距离测量区域的远近分为两种尺寸, 一级标记位于距测量区域500—1000 μm的范围, 长直角边长2 μm, 短直角边长1 μm; 二级标记位于距测量区域10—500 μm的范围, 长直角边长1 μm, 短直角边长0.5 μm.
当找到任意一个三角形标记时, 通过观察其指示方向和大小, 即可直接得知测量区域的大致方位与距离, 在测试中可快速定位到测量区域, 提高实验效率. 此外, 用文献[10]中类似的方法, 利用该标记的尖端也可以粗略测试显微镜的分辨率.
2
2.2.制备与检测
首先制备了硅纳米标样, 适用于反射式矢量光场CLSM. 制备过程使用厚度为500 μm的单抛非晶硅片作为衬底, 将比例为1∶4的氢倍半硅氧烷薄膜(hydrogen silsesquioxane, HSQ, 采用DOW公司FOxTM 16型号产品)与甲基异丁酮(methyl isobutyl ketone, MIBK)混合溶液以旋涂工艺覆盖到衬底上, 并在90 ℃热板上烘5 min, 得到200 nm厚的电子抗蚀层, 用于电子束曝光. 完成曝光后, 在四甲基氢氧化铵(tetramethylammo-nium hydroxide)显影液中浸泡90 s, 纯水中浸泡30 s, 氮气吹干, 得到带有标样图案的HSQ抗蚀层.在纳米加工中, 线宽的准确性通常是最重要的考虑因素[22]. 在制备过程中, 曝光剂量、显影时间和束斑步长都会影响显影后图案的平面与截面的形状, 进而影响刻蚀后结构线宽的准确性, 而对于不同线宽大小的结构, 这种影响的显著程度是不同的. 在未经参数调整的情况下产出的样品中, 大线宽的结构(标识1—4.5)的误差小于15 nm, 相对误差较小; 但是部分小线宽结构(标识5—25)的误差可以达到25 nm左右, 相对误差最高达52.7%, 标识20—25的测试图案甚至出现图案不完整或者粘连的情况.
为了克服大线宽跨度带来的制备困难, 尽可能保证线宽的精确性, 需要根据已有实验的结果, 按组进行曝光剂量调整与线宽修正. 在进行电子束曝光时, 将图案分为4组, 采用不同的曝光剂量、不同大小的束斑步长与不同的宽度修正等参数进行曝光, 经过近十次的工艺探索, 筛选出的具体曝光参数如表1所列, 其中指示标记对精确程度要求不高, 使用大束流可以提高曝光效率.
组别 | 数码标识 范围 | 曝光剂量/ μC·cm–2 | 束斑步长/ nm | 宽度修正/ nm | 束流大小/ nA |
1 | 1—4.5 | 1100 | 2 | 7.5 | 2 |
2 | 5—18 | 1500 | 2 | 5 | 2 |
3 | 20—25 | 2000 | 1 | 5 | 2 |
4 | 指示标记 | 1100 | 2 | 0 | 40 |
表1硅纳米标样曝光参数
Table1.Exposure parameters of the silicon nano-standard sample.
完成显影后, 使用电感耦合等离子体刻蚀技术, 以溴化氢气体作为刻蚀气体, 将HSQ抗蚀层的图案转移到硅片上, 刻蚀深度200 nm. 刻蚀后用10% 氢氟酸溶液浸泡样品, 去除残留的HSQ抗蚀层, 完成纳米标样的制备.
制备完成后使用扫描电镜(scanning electron microscope, SEM)检验纳米标样制备效果. 图2所示为硅纳米标样各区域的形貌细节.
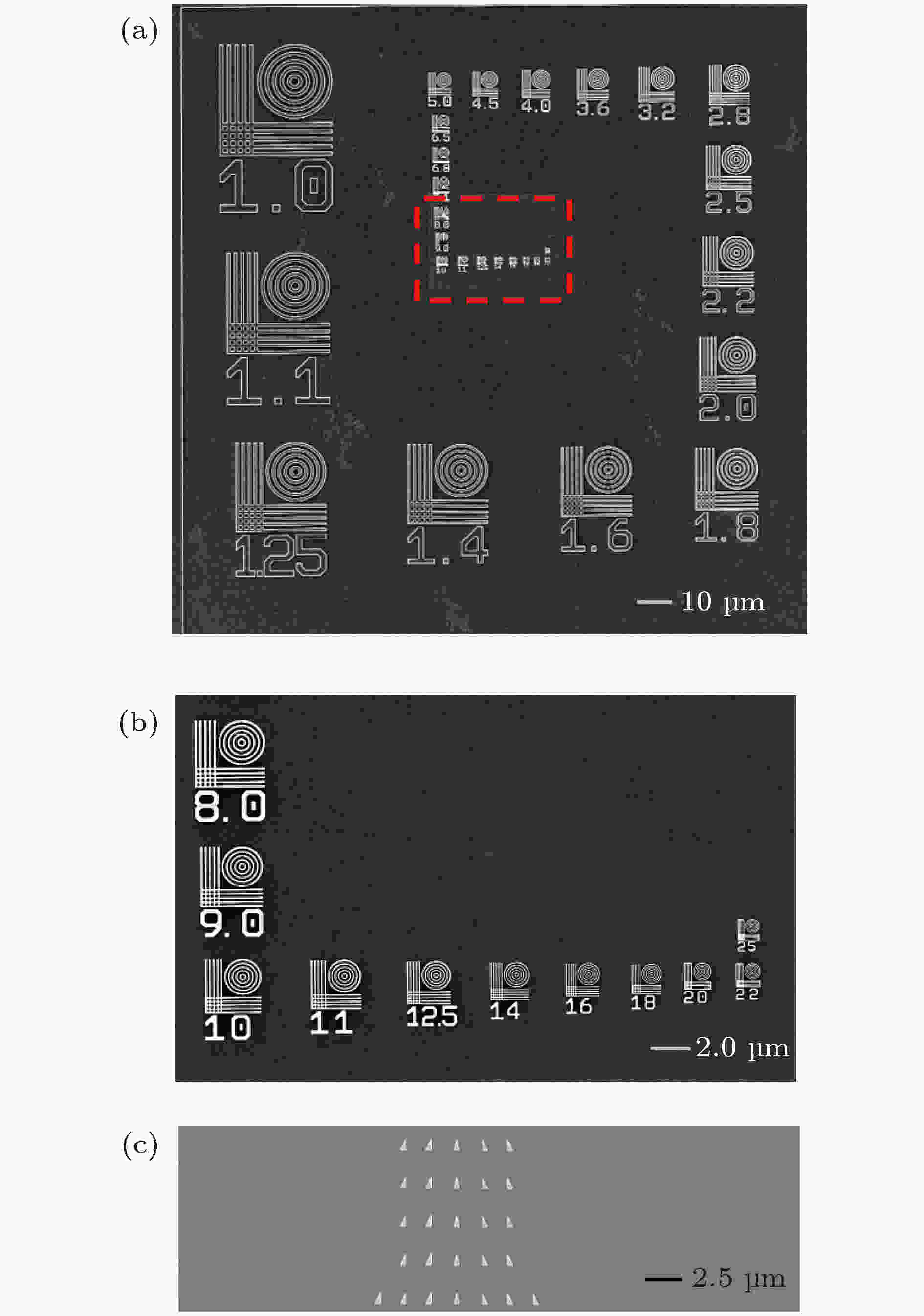
Figure2. SEM images of Si standard sample: (a) Overview of standard sample; (b) details of the red dash area in (a); (c) direction marks.
利用SEM的测量功能, 对每一个测试图案中各组光栅的各结构进行多次测量, 取其平均值作为该测试图案的线宽, 并与设计线宽做比较, 各测试图案的误差与相对误差如图3所示.
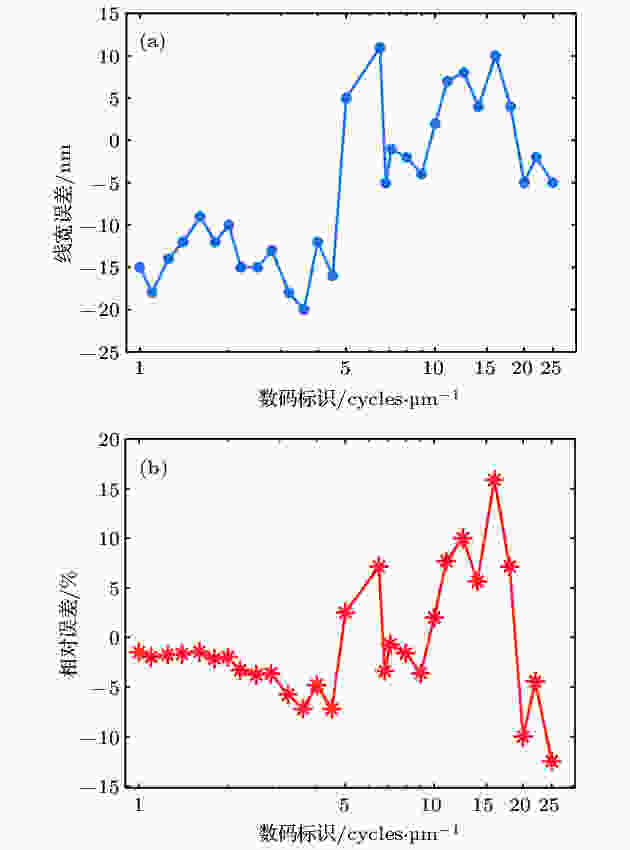
Figure3. Fabrication error distributions of the silicon nano standard sample, in which use logarithmic axis as x-axis: (a) Linewidth error distribution; (b) relative error distribution.
图2表明, 该样品细节完整, 图案清晰, 没有出现结构残缺或粘连的情况. 图3中误差的分布情况表明各结构的误差都比较小, 大部分测试图案的相对误差都保持在 ± 10%范围内, 仅有2个测试图案(数码标识为16和25的测试图案)超出该范围. 计算得到误差平均值–5.93 nm, 标准差为9.32 nm; 同时也可以看出不同曝光参数使得不同组之间的误差分布有明显不同, 第1组与第2组的误差分布存在突变, 但整体线宽更接近设计线宽. 其中第1组(标识1—4.5)整体线宽偏小, 误差最大, 但其线宽大于200 nm, 相对误差很小, 可以满足衍射极限内光学显微镜的分辨率测试要求; 第2组(标识5—18)经修正后, 误差得到缩小, 绝对值小于12 nm; 第3组(标识20—25)的误差绝对值小于5 nm, 十分接近设计线宽. 这种精度已经可以满足我们检测超分辨显微系统性能的要求.
以上结果表明, 以这种工艺制备得到的样品, 符合第1节提出的样品要求, 可以作为检验矢量光场CLSM性能的标准样品.
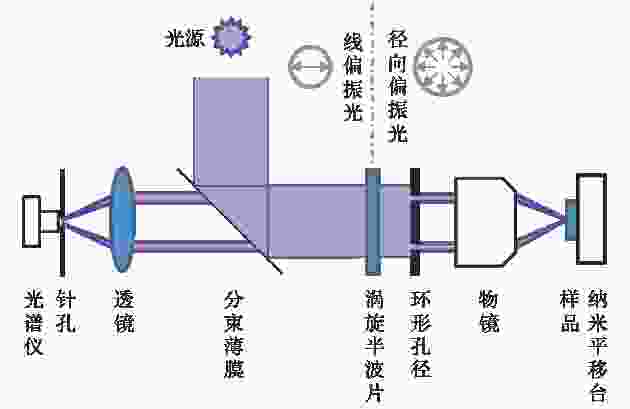
Figure4. Optical path of vector beams field CLSM.
测试采用波长为405 nm的线偏光作为矢量光场CLSM的光源, 光线经过涡旋半波片转换成径向偏振光, 经环形孔径调制后称为环形光场, 通过油浸物镜 (Olympus UPlanSApo 100 ×/1.40, 介质油折射率n = 1.5)聚焦到纳米标样上, 反射光线再反向经过环形孔径和涡旋片, 转换成线偏光, 经透镜聚焦通过直径为15 μm的针孔将光信号传入光谱仪中. 移动纳米平移台, 逐点将信号发送给计算机处理并输出相应结果.
在矢量光场CLSM的成像分辨率测量实验中, 所使用的硅纳米标样(未经线宽修正)所有的测试图案的线宽都经SEM测量, 与数码标识一一对应, 将光学测试图像与SEM图像对比即可得出分辨率数据. 图5展示了硅纳米标样部分测试图案光学扫描结果及SEM扫描结果的对比, 第一行是光学扫描输出结果, x-y轴均为相对位置, 信号强度单位为光子数, 第二行是相应的测试图案电镜扫描结果, 用红框标出了第一行的图案对应的位置. 其中5个测试图案的结构线宽经SEM测量, 分别是985, 205, 113, 96和88 nm. 初步分析表明, 矢量光场CLSM的分辨率可以达到亚100 nm数量级. 同时由于受到样品光电物性的影响, 矢量光场CLSM读出信号的强弱分布与样品的形貌有关, 如图5(a)中数码标识“1”字, 其结构连接处产生了强信号.
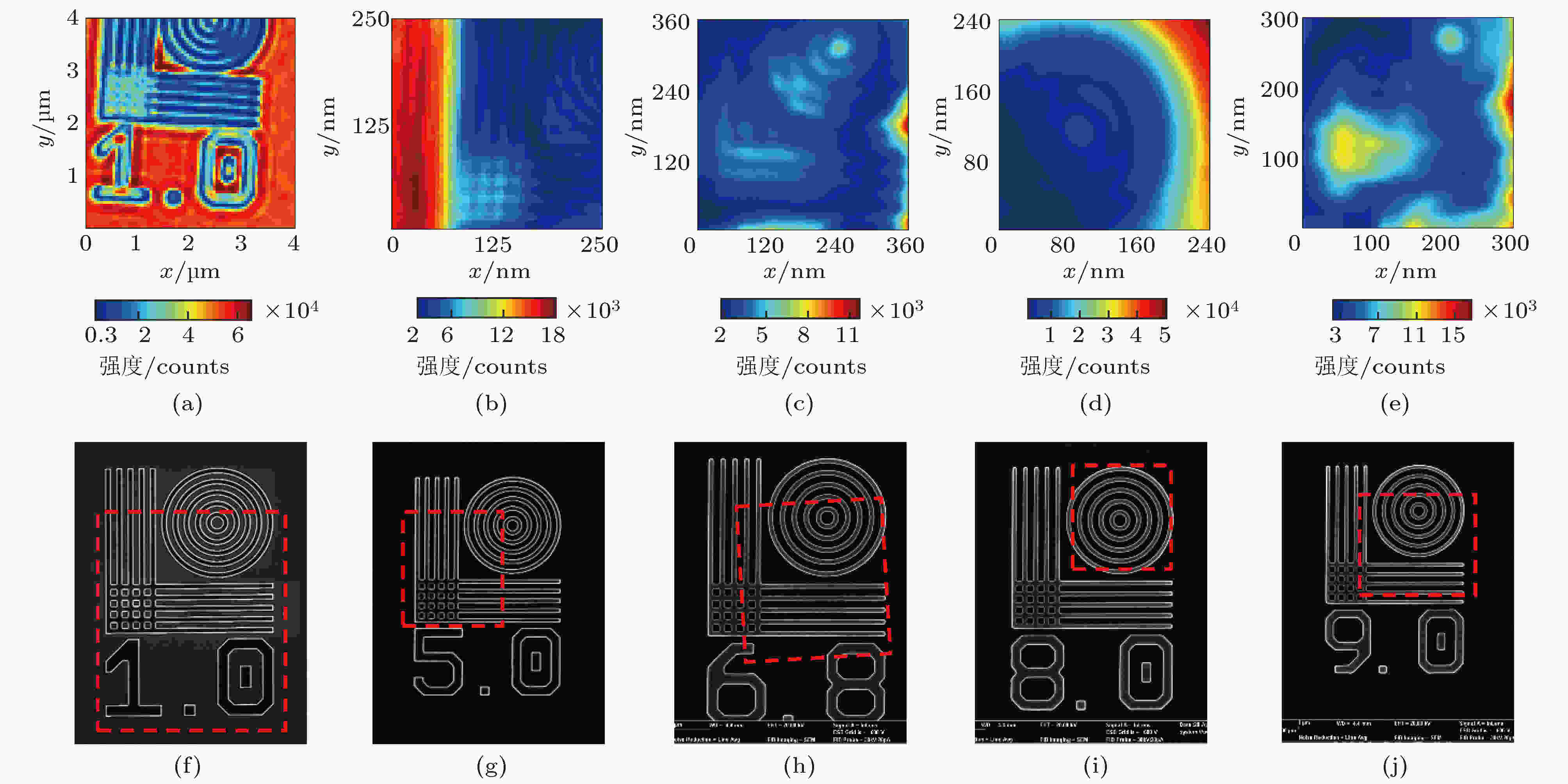
Figure5. Comparison between optical scanning images (first row) and SEM images (second row) of the Si standard sample. The corresponding positions are marked by red dash squares.
由于光与物质的相互作用, 图5的光学扫描结果部分结构之间的光场发生了相互干扰, 降低了信号与背景对比度, 也降低了信号的规律性, 从而影响了直接用肉眼来判读分辨率(特别是图5(e)). 但抛开其他指标, 仅仅针对分辨率测试而言, 可以通过绘制强度变化曲线, 从曲线的斜率变化中找到结构对应的信号, 并确定可被分辨的结构的数量. 以图5(d)中恰好能被分辨的最小测试图案为例, 如图6所示. 图6(a)中白色虚线位置的信号强度变化可绘制为图6(b)中的强度分布曲线. 受相互作用现象影响, 结构信号都是弱信号, 而背景的强度波动显著, 会给判读带来干扰. 从强度曲线上可以找到5处类似于“缺口”的弱信号(曲线上红色方形标记)的位置, 即为5处圆环结构, 因此认为矢量光场CLSM能够分辨该测试图案. 相应地, 利用该方法, 图5(a)—(c)中的测试图案都可以被完整分辨, 对于图5(e)乃至更小的测试图案, 则无法分辨. 受限于篇幅, 在此不一一展示.
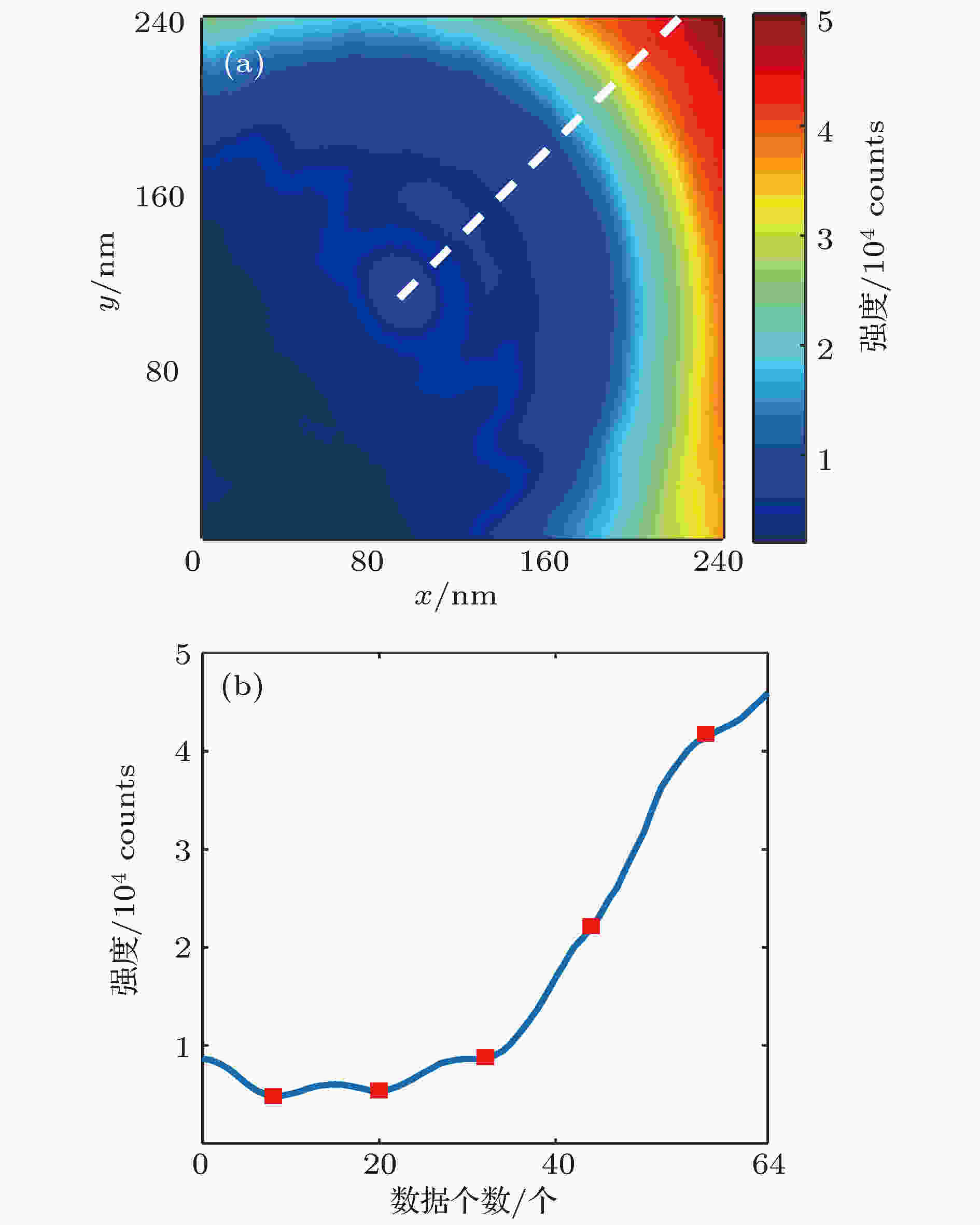
Figure6. Data analysis result: (a) The critical resolution measurement image obtained by microscopy; (b) amplitude distribution of white dash line, according to the slope variation, 5 weak signal (red square marks) can be found.
从以上结果中得到的结论是: 该纳米标样可用于矢量光场CLSM的分辨率测试, 同时测得采用405 nm光源的矢量光场CLSM可以在介质油环境(n = 1.5)中达到96 nm的分辨率. 在测试过程中也暴露了显微系统的若干问题, 由于严格对称的矢量光场对于系统的稳定性要求很高, 在进行长时间的测试后, 得到的结果将出现变形, 无法得到精细扫描的大范围结果, 需要进一步加强显微系统的稳定性.
理论研究结果表明[10,15], 在矢量光场CLSM中使用合适的环形孔径和针孔、约束系统点扩散函数, 有望达到小于1/5λ的分辨率. 以405 nm波长为光源, 矢量光场CLSM有望达到81 nm的分辨率, 比532 nm光源理论上的分辨率(106 nm)更进一步. 不过目前矢量光场CLSM的分辨率离理论值还有一些差距, 需要在后续调试中进一步提高分辨率.
另一方面, 图5的光学扫描结果表明, 纳米尺度光学的成像会受到光场在纳米结构中的光子态密度、光场模式分布和样品材料物性的影响, 这种影响随着线宽的减小而变得更加显著, 导致对比度下降, 使得获取到的图像逐渐偏离扫描电镜的物理形貌测量结果, 阻碍分辨率的精确测量.
为此, 在石英衬底上制备金属结构纳米标样(简称石英-金属纳米标样)被进一步提出. 该样品(共两层: 10 nm钛和100 nm金, 其中钛层是为了增加结构的黏附性)的分辨率测试图案, 适用于透射式与反射式的CLSM. 石英-金属纳米标样的衬底与结构的材料物性相差很大, 反射率差达40%以上(405 nm), 有望避开上述影响. 首先在厚度为1 mm的石英玻璃上旋涂500 nm PMMA电子胶, 再溅射50 nm厚的铝层用于增强样品导电性, 经过电子束曝光后, 使用5%磷酸溶液50 ℃水浴去除铝层, 依次使用MIBK、异丙醇和纯水浸泡显影, 得到带测量图案的PMMA层. 采用电子束蒸镀技术在样品上蒸镀10 nm钛和100 nm金, 最后用丙酮溶液浸泡样品, 去除PMMA残胶, 得到石英-金属纳米标样.
图7所示为两种不同材料样品的光学扫描图像的对比, 选用扫描的对象是纳米等边三角形, 材质分别是石英衬底金属材质(边长4 μm)和硅材质(边长0.8 μm), 纳米三角所处位置在图中用红色虚线标出, x-y坐标轴均表示相对位置, 信号强度单位为光子数.
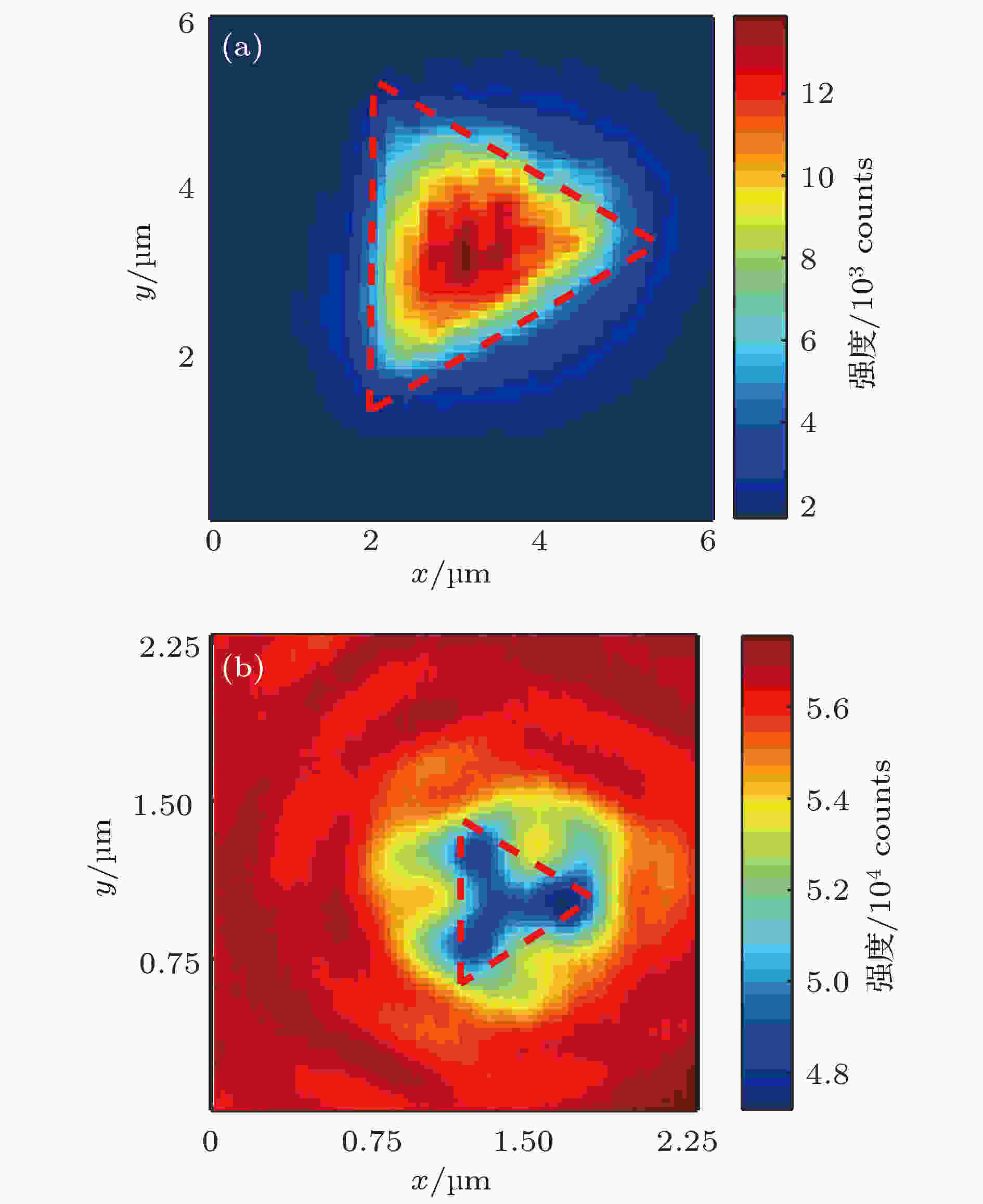
Figure7. Comparison between optical scanning images of two nano-triangles made from different materials: (a) A quartz substrate metal nano equilateral triangle; (b) a silicon nano equilateral triangle.
反射光信号对比度C定义为
根据(1)式, 石英/金属纳米三角的信号对比度为0.786, 硅纳米三角的信号对比度为0.099. 计算结果表明, 石英/金属纳米样品比硅样品拥有更高的反射率差和对比度, 对于分辨率的精确测量将提供更大帮助. 另一方面也可以看到, 图7(b)中硅三角岛的光学成像结果也在一定程度上偏离了物理形貌, 上述样品的光电物性对光学显微结果的作用机理尚待进一步深入探讨.
不过石英-金属纳米标样制备方法更复杂, 制备精度受限于蒸镀金属材料(钛和金)的颗粒大小, 精度差于硅纳米标样; 制备过程中线宽小于100 nm的结构容易脱落, 导致测试图案不完整. 这些问题对制备高质量的石英/金属纳米标样带来很大挑战, 因此该制备方案还需进一步探索, 完善制备工艺, 以制作出高质量的石英-金属纳米标样.
后续的工作将进一步探索透明基底金属纳米标样更精确的制备工艺, 做出更精确与更高对比度的纳米标准样品, 为远场矢量光共聚焦显微镜探寻更小尺度的光学成像过程提供更多支持; 另一方面, 也将对纳米尺度光学成像过程中, 样品的光电物性对于形貌表征的影响机制进行深入研究.
感谢中山大学光电材料与技术国家重点实验室李俊韬教授与周丽丹工程师在样品制备过程中提供的思路与帮助.