全文HTML
--> --> -->李亚江等[11]和白莉[12]采用真空扩散焊制备铜/铝复合材料时, 发现在铝侧靠近界面位置有大量孔洞存在. 李小兵等[13]应用透射电子显微镜对轧制和退火制备而成铝/铜复合材料的界面进行观察, 在铝侧也发现大量孔洞. 路王珂等[14]对退火后的铜铝复合板的力学性能进行测试和对界面组织结构研究时, 发现铝侧孔洞的数量随退火温度的升高而增多. 王波等[15]用热辅助超声波进行铜/铝层状复合材料増材制造并对材料进行拉伸, 结果显示孔洞在界面位置形核. 而在异种金属连接上, 在应力拉伸或疲劳作用下, 发现孔洞都是首先在铜/镍薄膜的界面处形核[16-17]. 而对面心立方结构金属内部孔洞缺陷微观结构演化的研究则主要集中在单金属材料内部. 在实验方面, 祁美兰[18]对高纯铝进行了一维应变平面冲击波加载实验, 结果表明, 离准层裂面距离近则孔洞尺寸大、数量多, 反之则孔洞尺寸小、数量少. 冉小霞[19]对纯铝进行冲击加载的实验结果是孔洞在晶界处产生并沿晶界成长. 徐斌等[20]则研究了压下率和变形温度对孔洞闭合的影响. 刘宏伟[21]的纯铝压缩和拉伸实验显示, 孔洞之间相距较远时孔洞单独生长, 相邻较近时孔洞粘连生长.
理论上, 用分子动力学模拟方法, Avinash等[22]对纳米多晶铜体系进行动态加载, 指出低温下塑性变形是孔洞形核与生长的主要方式, 高温扩散促进孔洞的形核与生长. 庞卫卫等[23]研究了在拉伸应变下单晶铜内纳米孔洞的形核, 认为孔洞在位错密集区通过不同层错面的不断交割而形核. 在孔洞生长方面, Belak[24]对单晶铜进行加载实验, 研究表明孔洞的生长是由于各向异性位错形核和发射实现的. Sirirat等[25]模拟了单轴拉伸应变下铜单晶的孔洞生长机制, 发现孔洞生长的主要原因是切向应力的释放. 张宁等[26]针对单向拉伸载荷作用下含孔洞双晶铜晶体的力学行为, 研究了晶粒内部孔洞大小、数量和晶界对孔洞力学行为的影响. Simar等[27]研究了镍单晶内部刃型位错与孔洞的相互作用, 发现随孔洞尺寸的增加, 孔洞阻碍位错强度增大. 另外, 胡晓燕等[28]、梁华和李茂生[29]研究了单轴加载下单晶铝内部晶向对纳米孔洞的生长和附近区域形变的影响. 方洲等[30]研究了单轴拉伸作用下含孔洞单晶铝的裂纹扩展行为, 指出孔洞尺寸越大, 孔洞越容易与邻近孔洞聚合. Yang等[31]研究了单晶铜板内孔洞周围原子应力集中的现象, 发现孔洞附近原子的排布方式是原子应力集中的关键因素. 郭巧能等[32]在超薄铜膜的疲劳性能影响研究中指出, 在循环载荷作用下, 孔洞于位错交截处形核, 孔洞尺寸随循环次数增大. 在孔洞闭合方面, 张永军[33]对含孔洞纯铜在500℃下保温, 发现孔洞填充是孔洞闭合的主要过程.
以上对孔洞的研究主要集中在面心立方单金属材料内部, 对铜/铝复合材料或是异种金属内部孔洞形核演化的研究较少. 因此, 本文采用分子动力学方法研究了在循环载荷作用下, 铜/铝薄膜内部孔洞形核、生长和闭合的微观结构变化及形变机制.



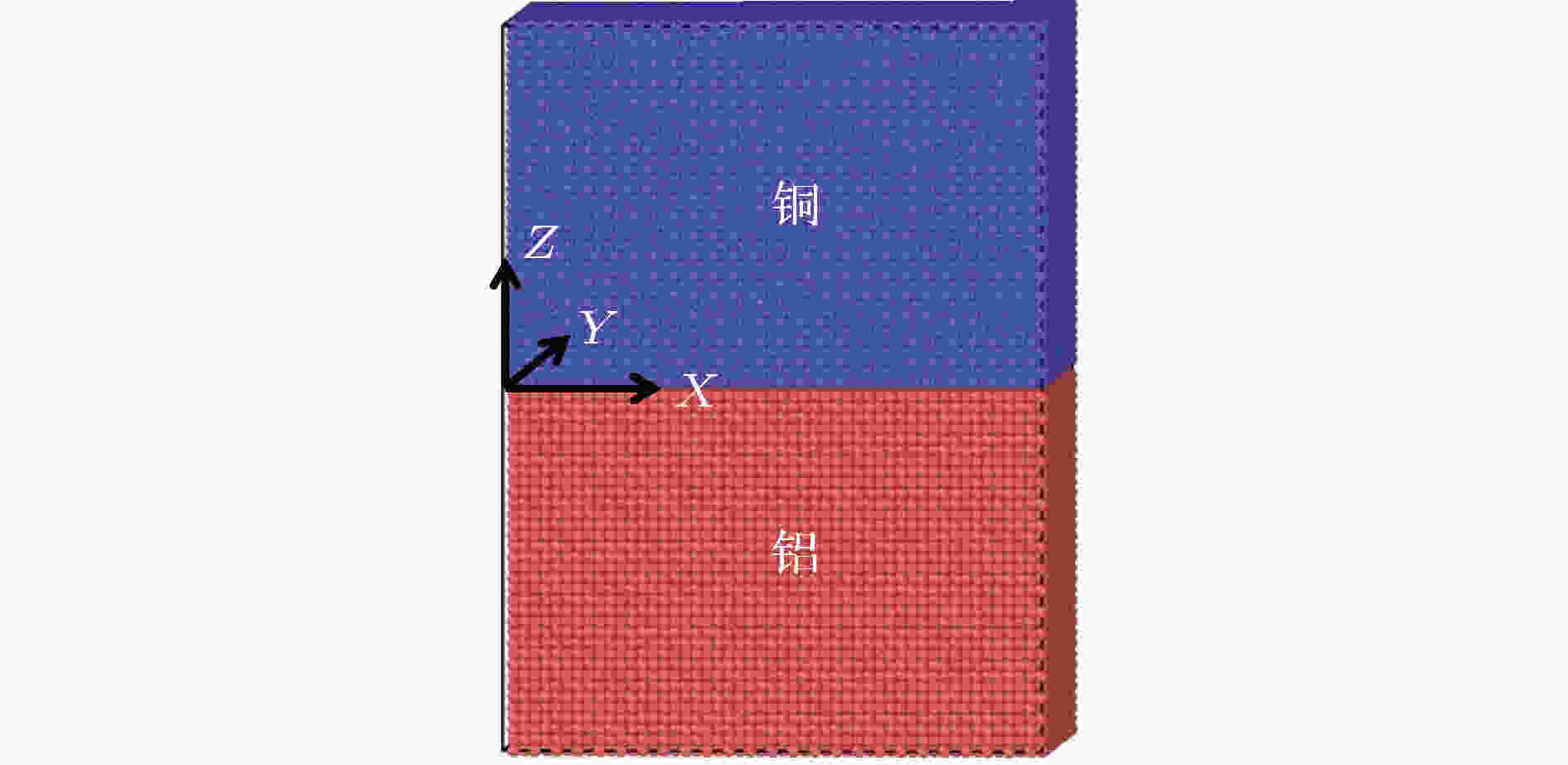
Figure1. Cu/Al bilayer films model (The upper blue for copper atoms and the lower red for aluminum atoms).
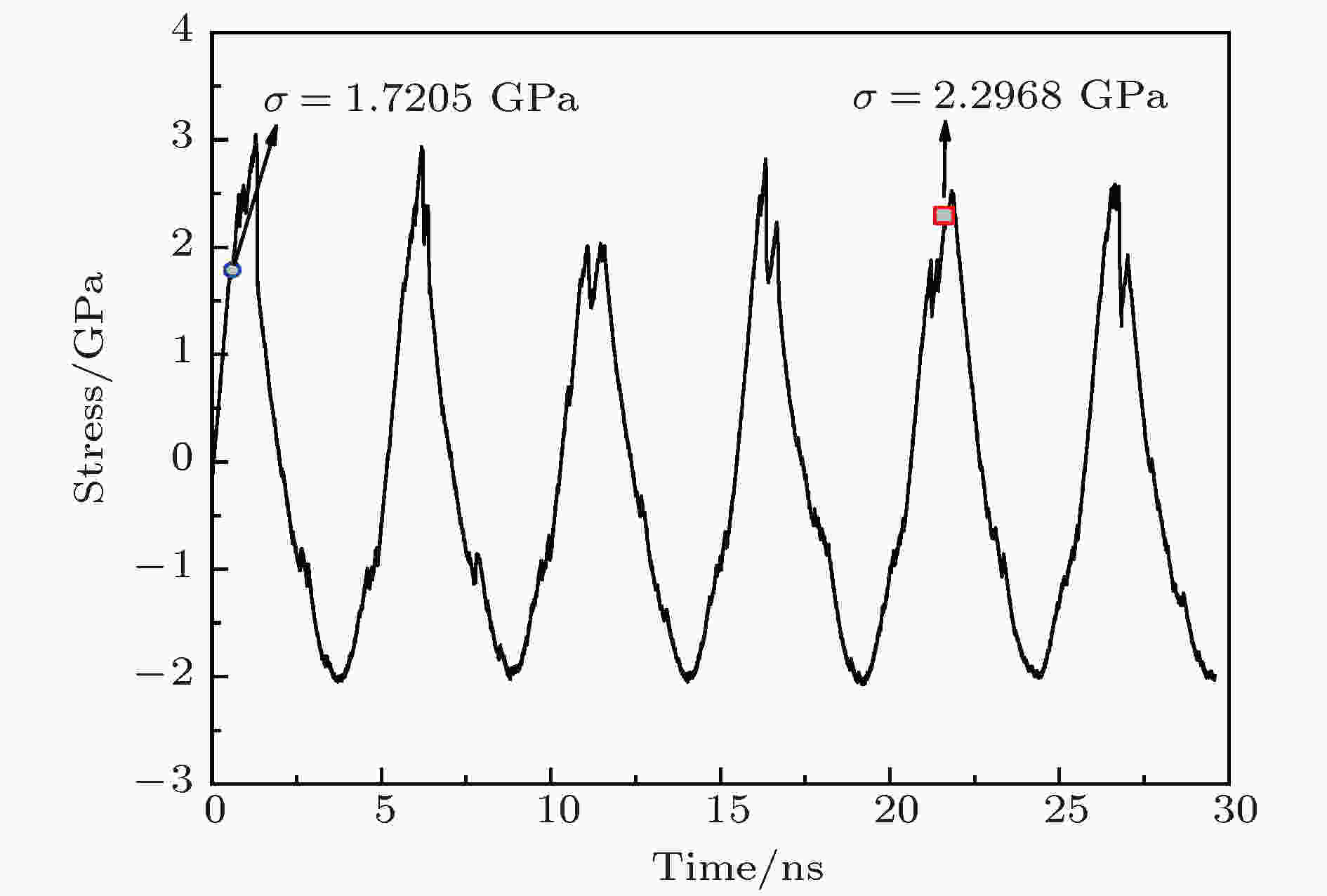
Figure2. Stress-time curve of Cu/Al bilayer films under cyclic loading.
2
3.1.孔洞Ⅰ的演化: 铜铝扩散形成双层膜时所产生出的空隙缺陷引发孔洞的形核、生长和闭合
33.1.1.孔洞Ⅰ的形核
图3和图4分别为铜/铝双层膜在应变加载下孔洞形核Ⅰ演化的成分原子位置图和原子结构图, 这些图是沿[100]晶向截取孔洞附近区域3层原子厚度的局部图. 从图3(a)可以看出, 当应变ε = 0.0000时即循环应变加载前, 铜/铝双层膜中铝侧扩散铜原子附近的铝原子排列稍显混乱, 并已经有空隙存在. 而且从图4(a)可以看出, 循环应变加载前, 孔洞形核前的孔洞位置及附近区域原子结构已经由面心立方结构(face-centered cubic, FCC)变为无序结构(OTHER)和少量密排六方结构(hexagonal closepacked structure, HCP), 表明该位置区域出现了缺陷. 这些空隙缺陷和OTHER结构是由于铜原子向铝侧内扩散过程中产生了柯肯达尔效应, 使得铝侧铜原子扩散位置处发生点阵变形, 由此产生了一定量的空隙、位错和OTHER结构.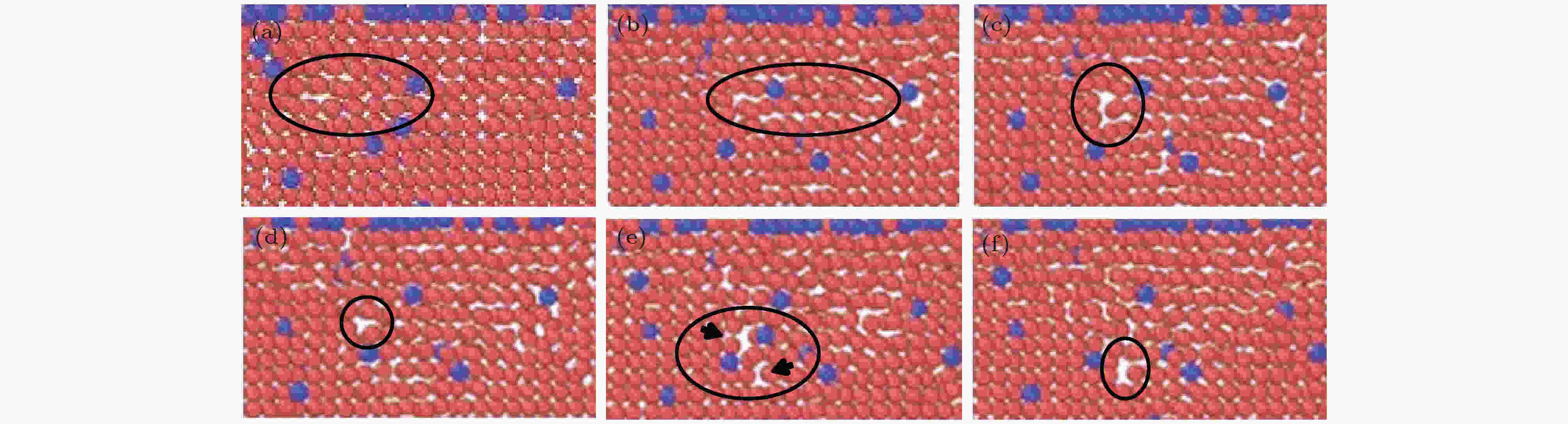
Figure3. Void I: screenshot of the nucleation evolution of the void (red for aluminum atoms, blue for copper atoms), ε is (a) 0.0000; (b) 0.0528; (c) 0.0531; (d) 0.0534; (e) 0.0537; (f) 0.0540.
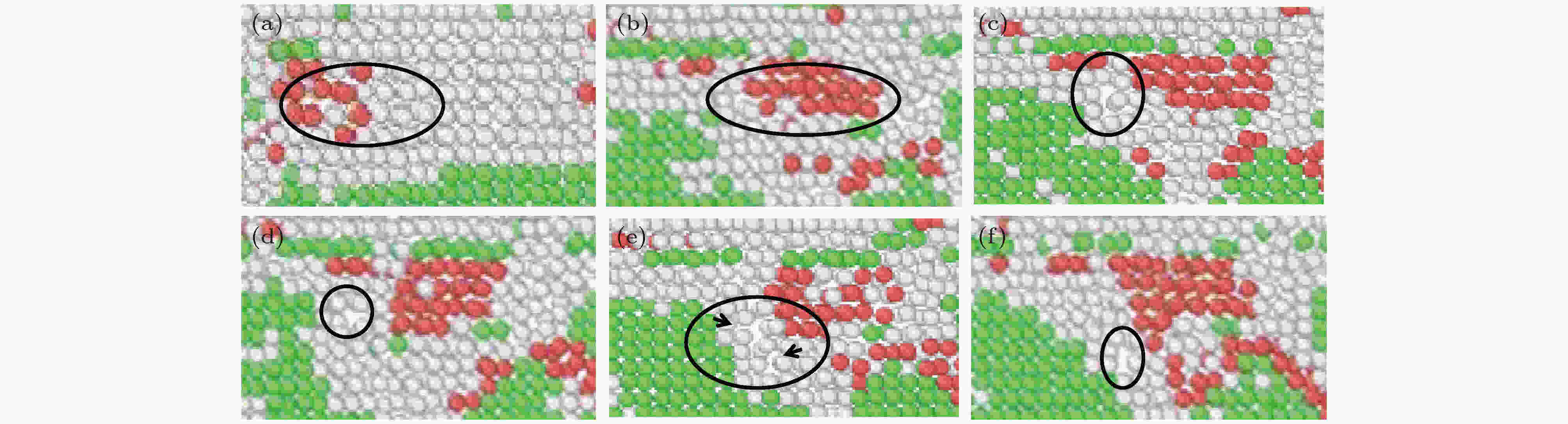
Figure4. Void I: screenshot of the atomic structure of nucleation evolution of the void (red for HCP structure, green for FCC structure, white for OTHER structure), ε is (a) 0.0000; (b) 0.0528; (c) 0.0531; (d) 0.0534; (e) 0.0537; (f) 0.0540.
随应变增加, 当ε = 0.0510时, 在距离孔洞形核中心位置的附近出现了2条肖克莱位错线S1, S2和1条OTHER位错线Q1(图5). 另外, 在孔洞形核位置附近有HCP结构产生, 由于在孔洞形核位置附近产生层错使得这一区域应力集中释放的同时空隙变大.
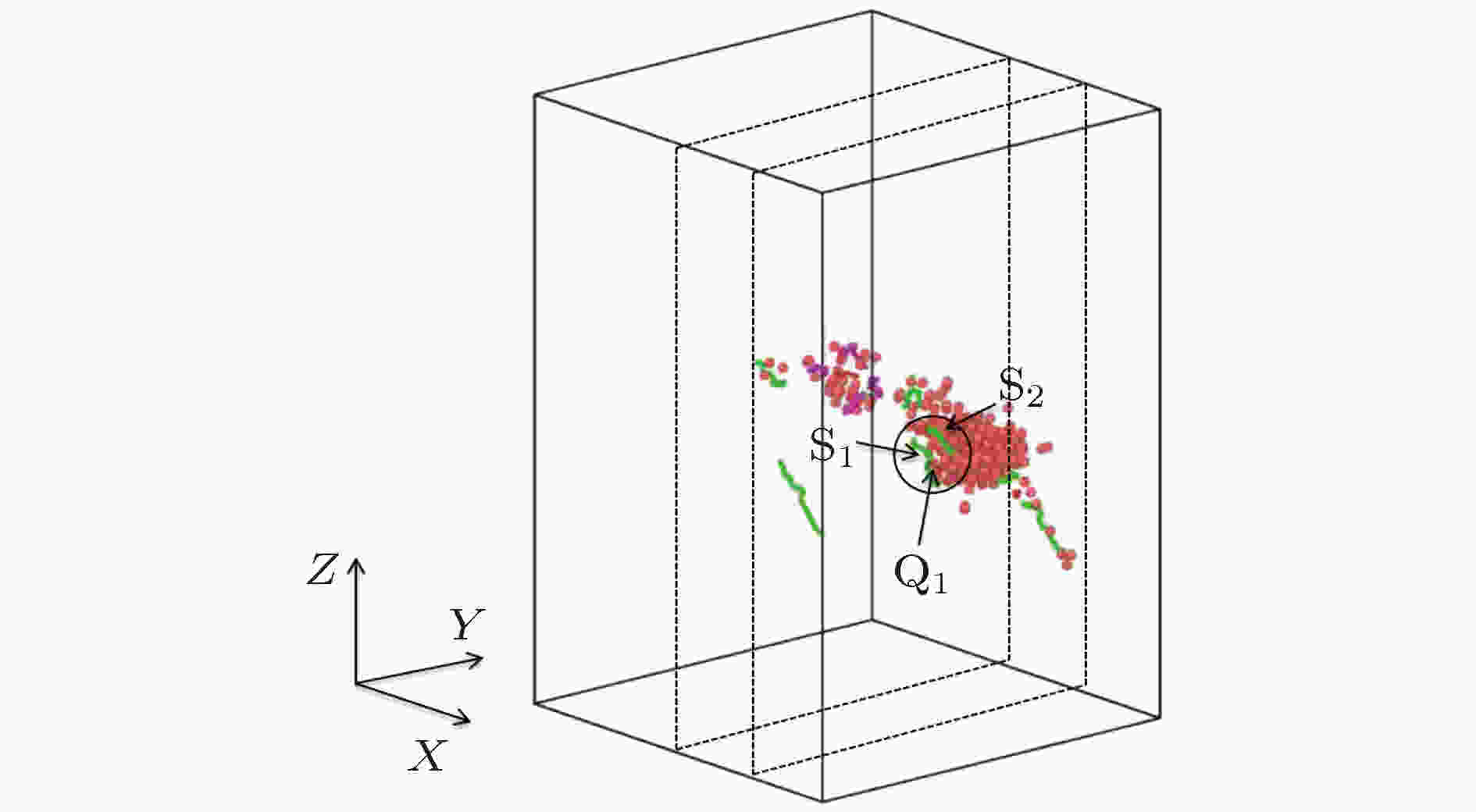


Figure5. ε = 0.0510, Void I: screenshot of dislocation analysis at the nucleation position of the void (red atoms are HCP structure atoms, purple represents


随拉伸应变的继续增加, 当ε = 0.0528时, 孔洞形核位置区域(110)面之间的空隙增大(图3(a)), 这是由于肖克莱位错S1和S2交截形成了一个压杆位错R1(图6), 此压杆位错对应的割阶导致原空隙变大(图4(b)). 当进一步加载到ε = 0.0531时, 此变大了的空隙向铜原子的位置处移动, 并在扩散铜原子左侧聚集形成一个空位(图3(c)和图4(c)), 这是由于空位与扩散铜原子之间存在一定的结合能[39], 在拉伸应力的作用下, 空位向扩散铜原子数量相对较多的位置发生移动形成了稳定的空位-溶质原子结构[40]. 继续加载时由于该空位附近新产生出的肖克莱位错与压杆位错R1相互作用形成肖克莱位错而导致此压杆位错消失, 这种情况类似于徐振海等[41]在单晶铜纳米线屈服机理的分子动力学模拟研究中观察到的情况.
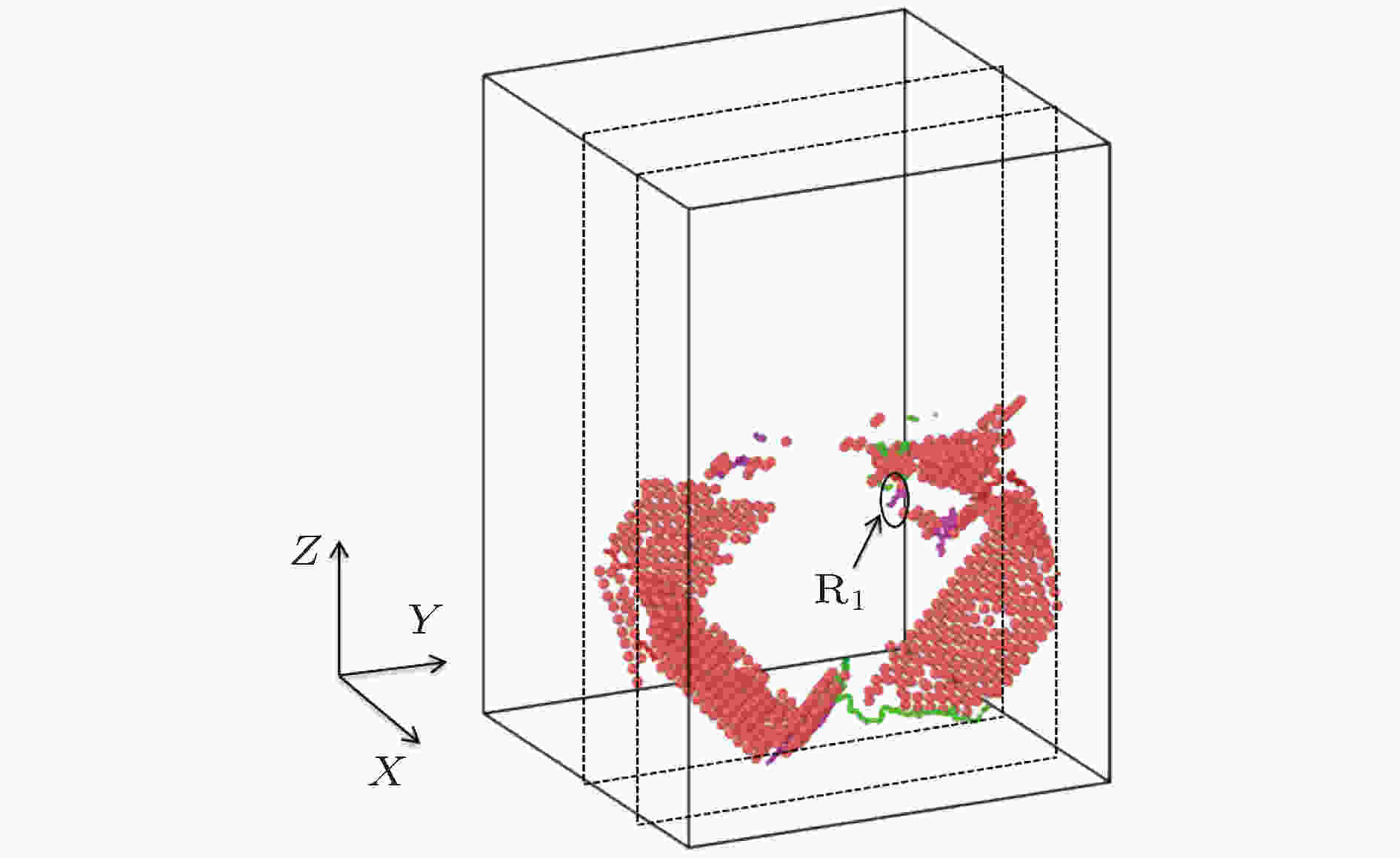


Figure6. ε = 0.0528, Void I: screenshot of dislocation analysis at the nucleation position of the void (red atoms for HCP structure atoms, purple represents


继续加载到ε = 0.0537时, 在拉伸应力的作用下, 空位向铜原子数较多的区域移动. 另外, 另一个新形成的空位也向铜原子数较多的位置移动(图3(d)—(e)), 这是由于在所研究空位的正前方附近形成了新的肖克莱位错S3, 其右上及右下位置各自又形成了2个新的压杆位错R2和R3, 如图7位错分析图所示, 正是这些压杆位错、扩散铜原子与空位的相互作用导致此空位沿Z轴继续向下移动, 并与新形成的空位相聚集形成空位团(图3(f)和图4(f)).
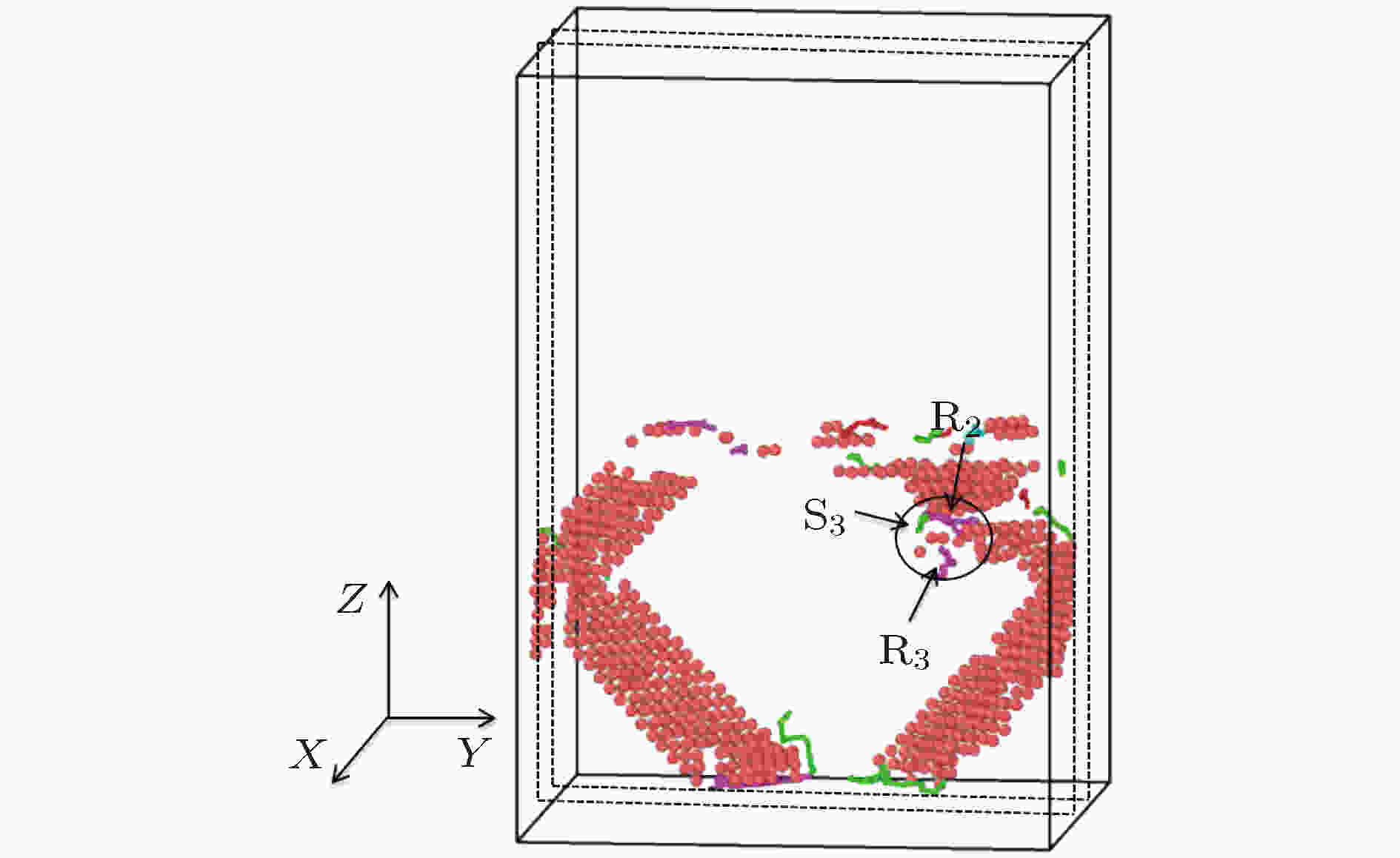


Figure7. ε = 0.0537, Void I: screenshot of dislocation analysis at the nucleation position of the void (red atoms are HCP structure atoms, purple represents


3
3.1.2.孔洞Ⅰ的生长
图8和图9分别为铜/铝双层膜在应变加载下孔洞生长Ⅰ演化的成分原子位置图和原子结构图, 这些图是沿[100]晶向截取孔洞附近区域3层原子厚度的局部图. 如图8(a)—(b)所示, 当负载增加到ε = 0.0600时, 空位团周围空隙继续向空位团处聚集, 使得空位团沿应变拉伸方向长大, 形成微孔洞, 同时, 孔洞周围原子面之间的空隙消失; 从图9(a)—(b)可以看出, 此时孔洞位置处HCP结构继续向OTHER结构转化, OTHER结构向FCC结构转变, 同时孔洞沿拉伸应变方向长大, 这是由于空位团形成后, 该区域应力被释放, 又重新恢复FCC晶格结构. 当外载达到ε = 0.0750时, 孔洞便开始在固定位置生长, 在随后拉伸应变过程中, 周围原子面间距再次拉大形成空隙, 空隙向微孔洞处聚集, 孔洞沿与应力拉伸相垂直的方向长大, 孔洞体积增大, 形状趋向球形发展, 此时孔洞附近区域的空隙随之稍减小, 原子又恢复原来排列方式, 如图8(c)所示, 这是由于在右侧新生层错的作用下, 空位团沿拉伸方向长大形成微孔洞(图9(c)). 在随后的拉伸应变过程中, 如图8(d)—(f)所示, 孔洞以上述方式成长, 当达到应变幅时, 孔洞外形生长不大, 这是由于孔洞周围没有较大的晶格结构变化, 所以孔洞体积几乎不变, 但周围扩散铜原子有向孔洞位置处聚集的趋向(图9(d)—(f)).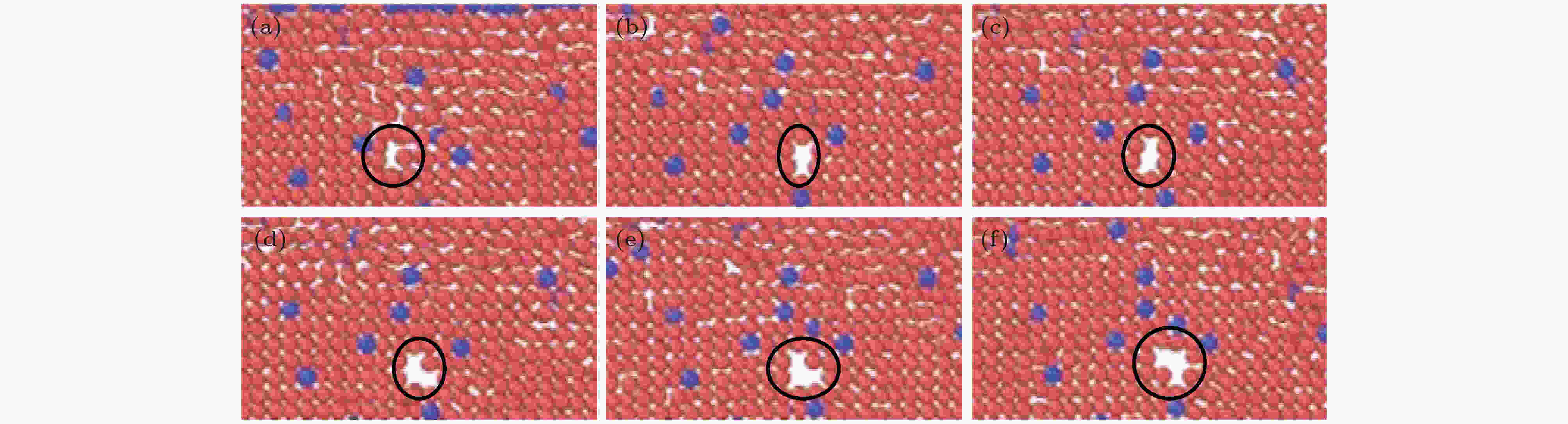
Figure8. Void I: screenshot of the growth evolution of the void (red for aluminum atoms, blue for copper atoms), ε is (a) 0.0540; (b) 0.0600; (c) 0.0750; (d) 0.0900; (e) 0.1050; (f) 0.1206.
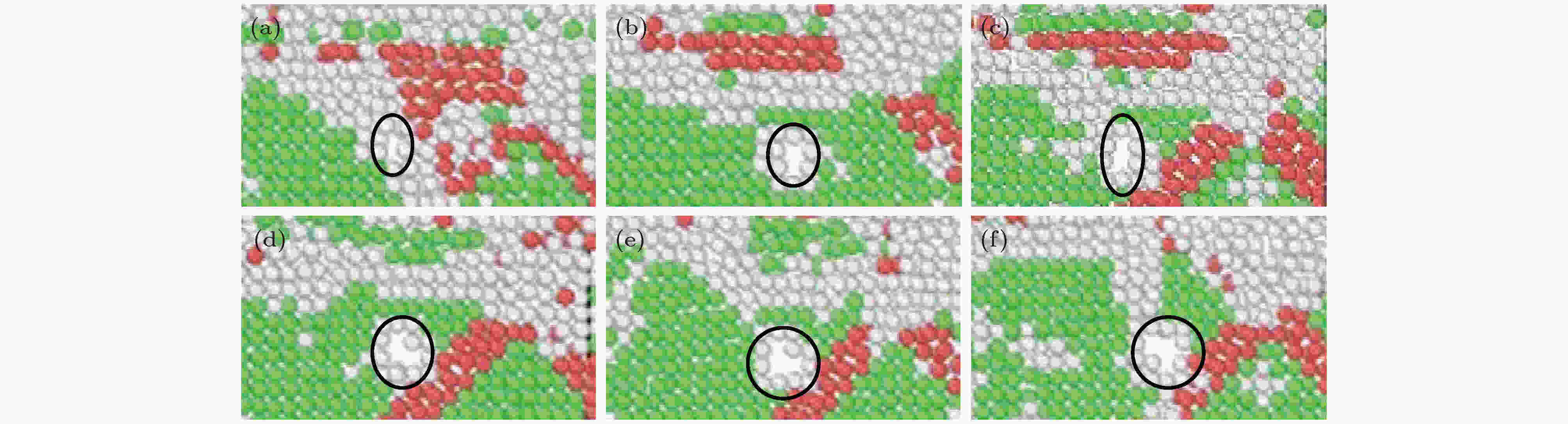
Figure9. Void I: screenshot of the atomic structure of the growth evolution of the void (red for the HCP structure, green for the FCC structure, white for the OTHER structure), ε is (a) 0.0540; (b) 0.0600; (c) 0.0750; (d) 0.0900; (e) 0.1050; (f) 0.1206.
总之, 孔洞长大是由于孔洞周围原子面间距在拉伸应变的作用下产生空隙, 空隙向孔洞聚集, 从而使得孔洞长大. 从结构上整体分析, 孔洞在位错的作用下长大, 当孔洞周围晶格结构不发生变化时, 孔洞外形变化不大, 几乎不成长. 这种孔洞几乎不生长的原因是由于扩散铜原子在铝侧局部区域置换铝原子形成了置换固溶体, 造成该区域强化(固溶强化), 从而使得孔洞不易长大. 经计算得出孔洞形核区域铜原子的原子数密度范围为1.72%—2.63%, 如图10两竖直线段中间区域所示, 此浓度在Cu-Al相图[42]上为χ固溶体(铝作为溶剂), 实验证明, 从铜铝过渡层(铜铝浓度均大于5%)到铝侧中显微硬度逐渐降低, 但大于纯铝的硬度[11,43].
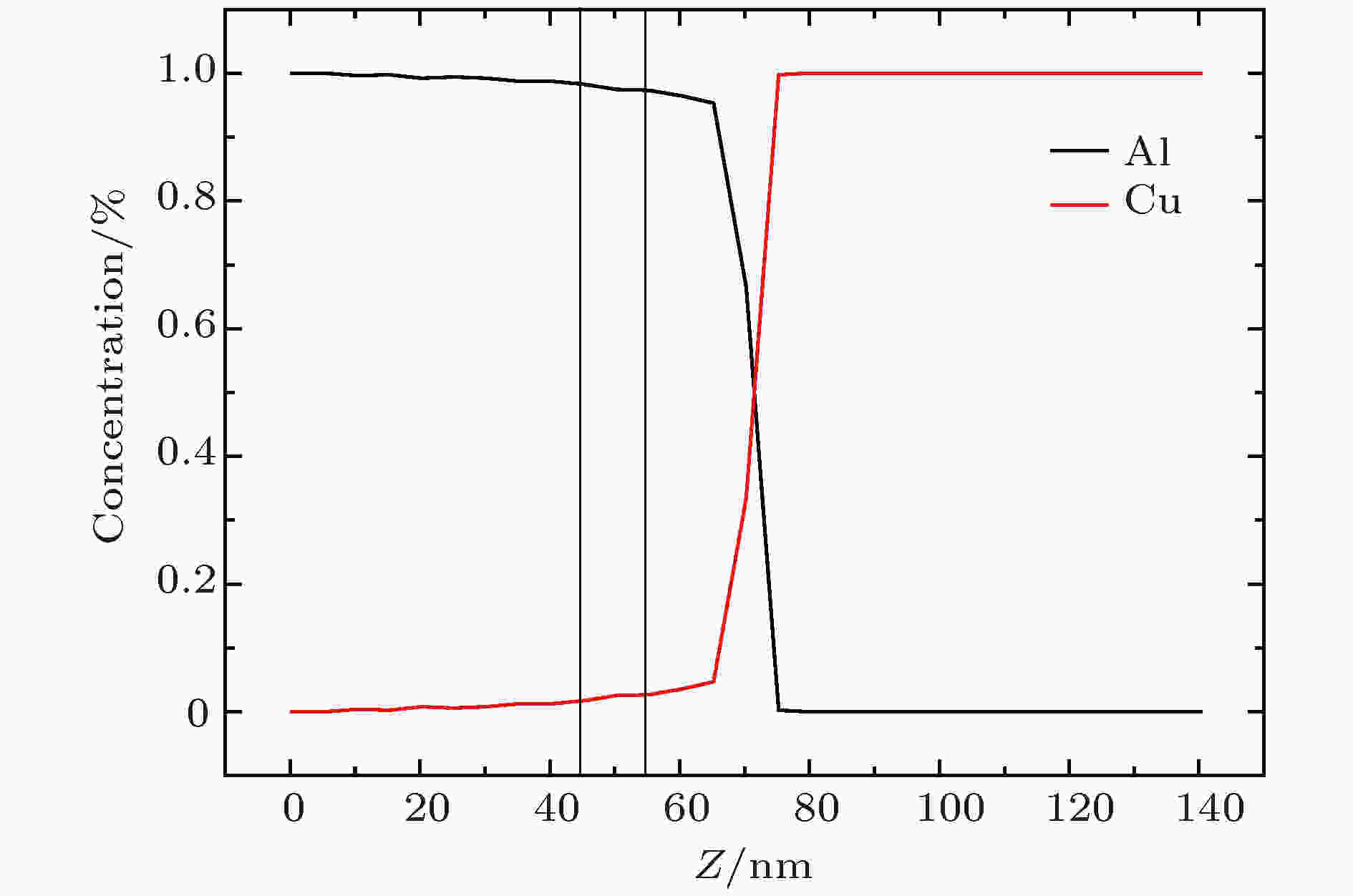
Figure10. Atomic concentration distribution of copper and aluminum atoms in the tensile direction (Z-axis) after diffusion.
3
3.1.3.孔洞Ⅰ的闭合
从应变卸载阶段的图11(a)—(d)可以看出, 孔洞沿应变卸载方向变成椭球状(压缩平面与压缩方向垂直), 椭球型孔洞沿长轴[010]晶向由两端逐渐向椭球中心闭合减小, 这时孔洞周围有新层错的生成(图12(a)—(c)). 继续卸载, 如图12(c)—(d)所示, 孔洞附近位错转变为FCC结构, 当应变卸载至0时, 模型内部层错也随之减少直至消失.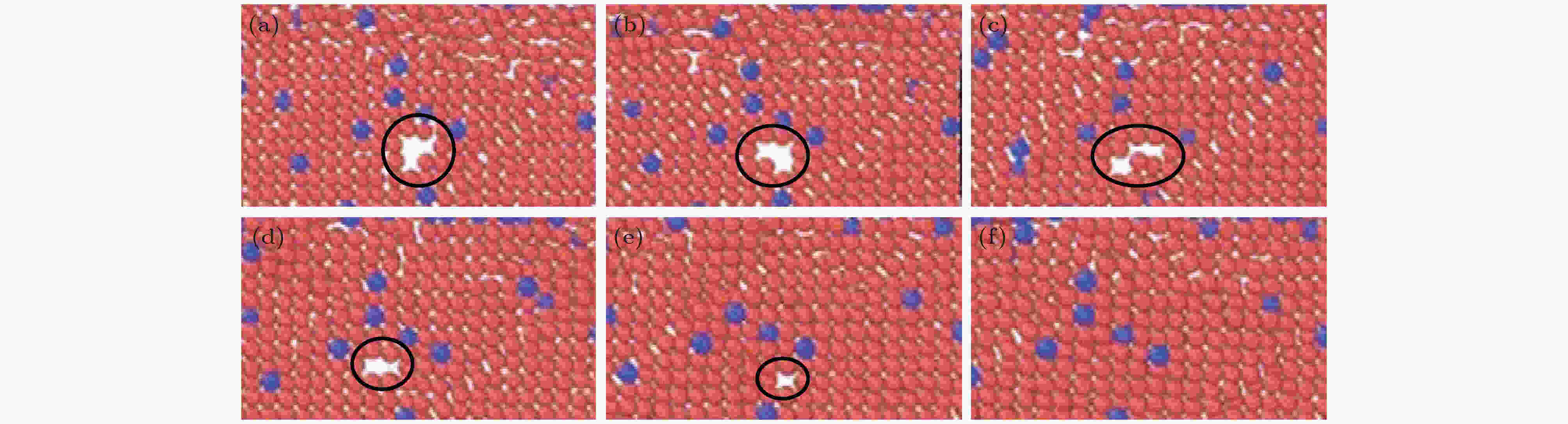
Figure11. Void I: screenshot of the closure evolution of the void (red for aluminum atoms, blue for copper atoms), ε is (a) 0.0906; (b) 0.0606; (c) 0.0306; (d) 0.0006; (e) –0.0294; (f) –0.0444.
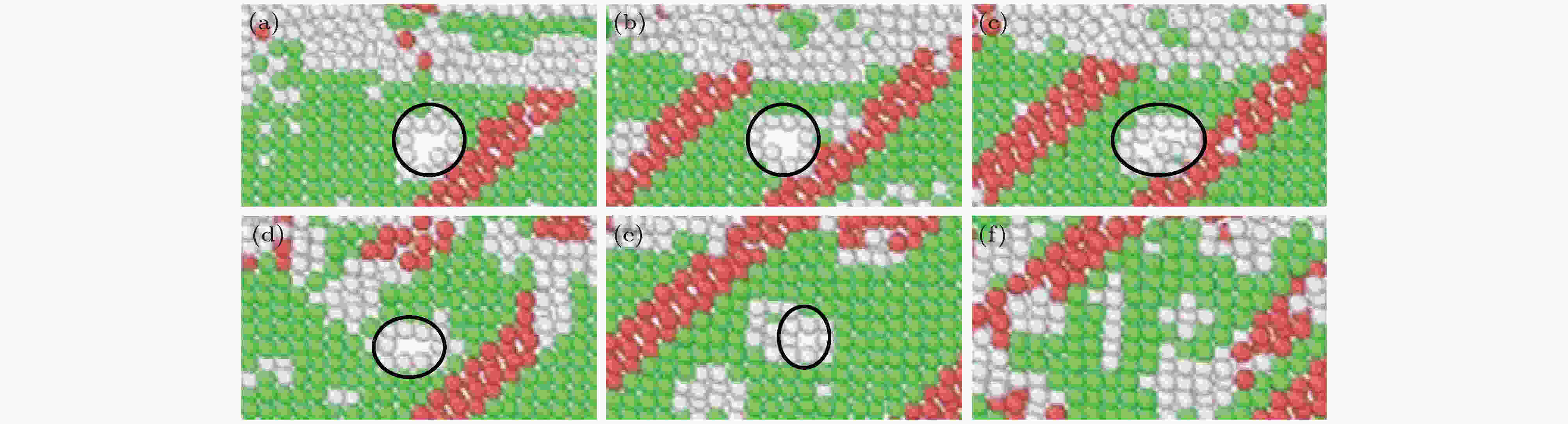
Figure12. Void I: screenshot of the atomic structure of the closure evolution of the void (red for HCP structure, green for FCC structure, white for OTHER structure), ε is (a) 0.0906; (b) 0.0606; (c) 0.0306; (d) 0.0006; (e) –0.0294; (f) –0.0444.
在如图11(e)—(f)所示的应变压缩阶段, 当椭球形孔洞减小至单空位时, 空位随应变压缩向下移动, 随应变压缩的增加, 单空位消失, 此时孔洞完全闭合. 从图12(d)—(e)来看, 在应变反向压缩阶段, 孔洞沿[010]晶向继续减小直至消失, 孔洞被OTHER结构原子占据, OTHER结构原子向FCC结构原子转化, 恢复FCC结构. 在孔洞闭合阶段, 孔洞相邻的层错对孔洞闭合起主要作用, 层错原子填充进孔洞内部, 使得孔洞体积变小, 随后才是孔洞周围原子填充, 最后孔洞完全闭合.
总之, 孔洞在闭合过程中, 首先沿应变卸载方向收缩成椭球形, 随后孔洞沿椭球型短长轴方向向椭球中心闭合[33], 这是由于在应变卸载时, 铜/铝双层膜内有残余应力, 使得铜/铝双层膜内的孔洞仍有部分恢复原状的能力, 但不能完全恢复[44]; 随应变反向加载, 在压应力的作用下, 椭球型孔洞逐渐压缩减小, 直至消失[45].
在随后的应变循环过程中, 该孔洞位置处没有产生缺陷的循环积累, 孔洞在铝侧的其它OTHER结构空隙缺陷位置处形核.
2
3.2.孔洞Ⅱ:由压杆位错被克服所产生出的空隙缺陷引发孔洞的形核、生长和闭合
33.2.1.孔洞Ⅱ的形核
33.2.1.1.空隙的形成
与孔洞Ⅰ情况相比, 一方面孔洞Ⅱ周围的扩散铜原子成分比孔洞Ⅰ少得多, 所以铜原子对孔洞演化过程影响较小; 另一方面由于孔洞处在扩散层以外较远位置, 所以其周围没有像孔洞Ⅰ那样在铜铝扩散时形成空隙, 孔洞Ⅱ的空隙是在循环拉伸加载阶段形成的.在第五次应变循环拉伸加载到ε = 0.0600时, 如图13所示, 在孔洞形核位置处分别形成了两个内禀堆垛层错, 一个位于




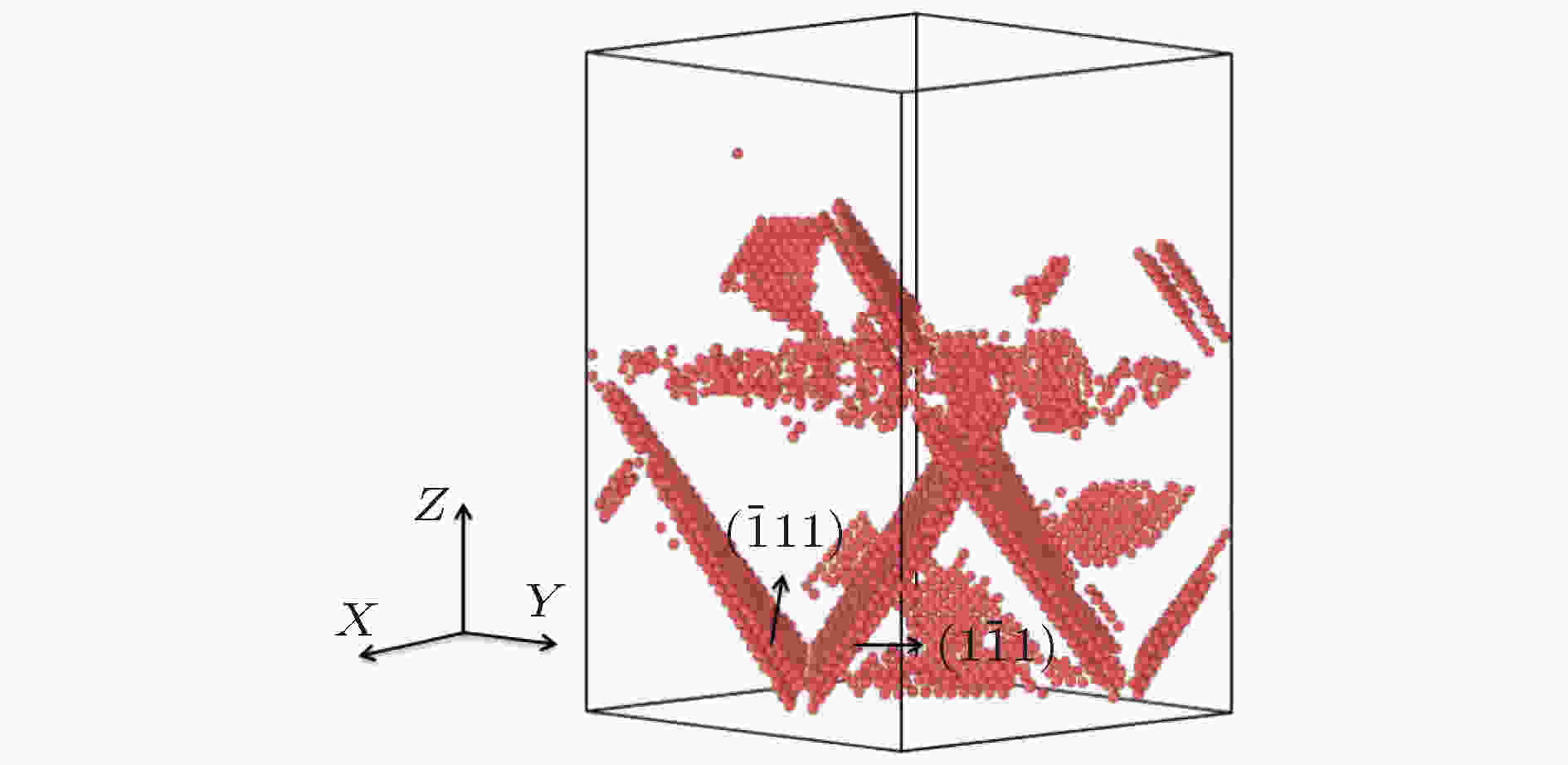


Figure13. Void II: An analytical diagram of the stair-rod dislocation formed by the intersection of


3
3.2.1.2.孔洞Ⅱ的形核
图14和图15分别为铜/铝双层膜随应变加载下孔洞形核Ⅱ演化的成分原子位置图和原子结构图, 这些图是沿[100]晶向截取孔洞附近区域3层原子厚度的局部图.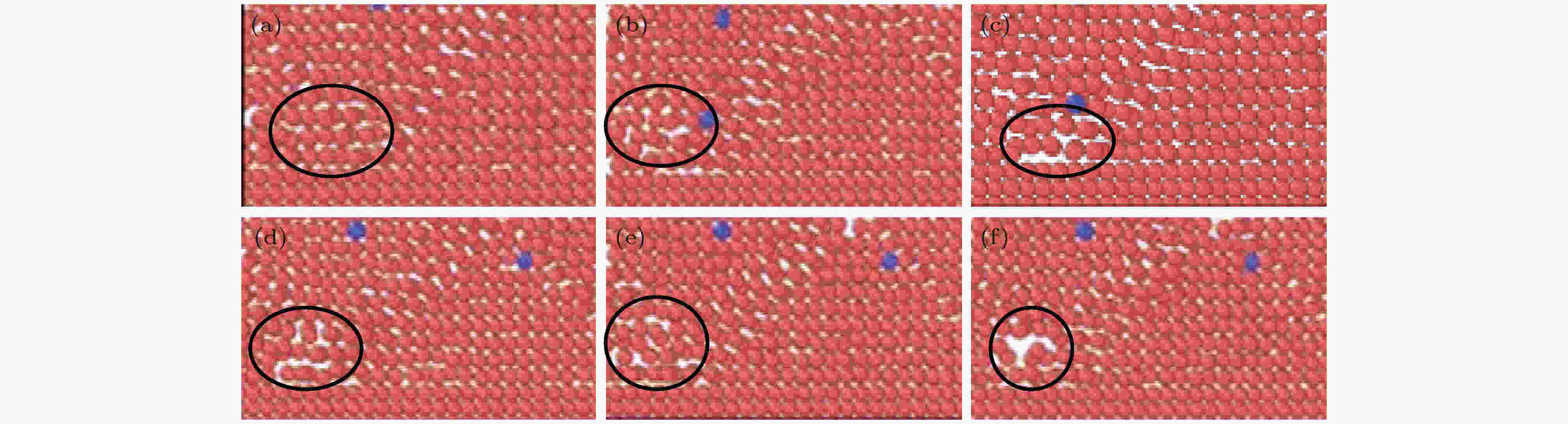
Figure14. Void Ⅱ: screenshot of the nucleation evolution of the void (red for aluminum atoms, blue for copper atoms), ε is (a) 0.1050; (b) 0.1155; (c) 0.1158; (d) 0.1161; (e) 0.1164; (f) 0.1167.
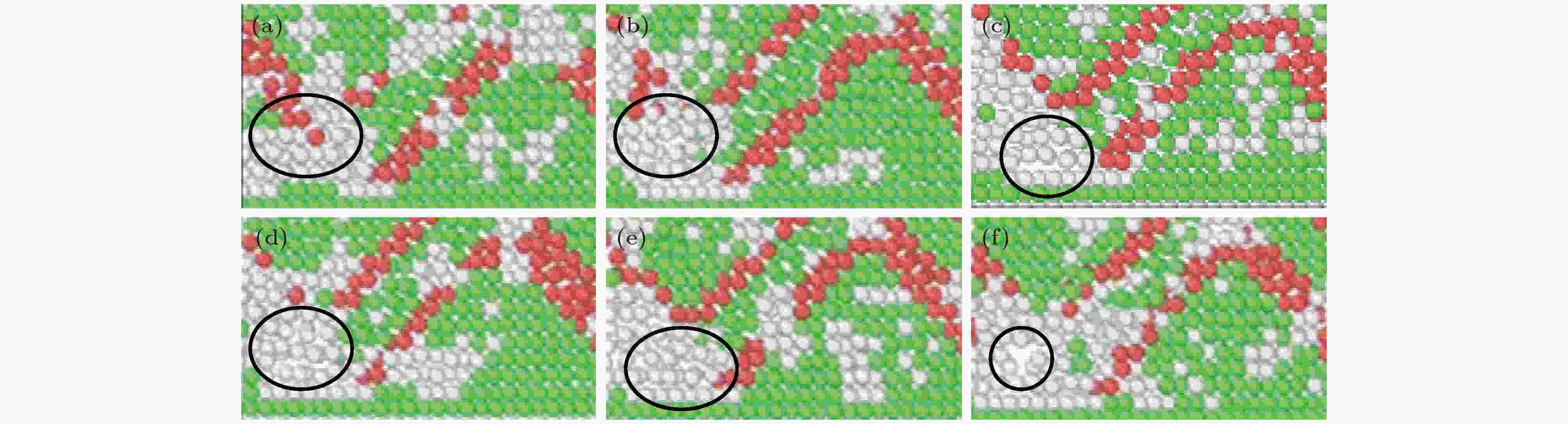
Figure15. Void Ⅱ: screenshot of the atomic structure of the nucleation evolution of the void (red for HCP structure, green for FCC structure, white for OTHER structure), ε is (a) 0.1050; (b) 0.1155; (c) 0.1158; (d) 0.1161; (e) 0.1164; (f) 0.1167.
如成分原子位置图14(a)—(d)和原子结构图15(a)—(c)所示, 随应变的增加, 当达到ε = 0.1050时, 铜/铝双层膜中铝侧压杆位错被克服, 孔洞形核位置处


另外, 如图4和图15所示, 孔洞Ⅰ与孔洞Ⅱ的形核都是在排列紊乱的OTHER原子结构区域内部形核.
3
3.2.2.孔洞Ⅱ的生长
如图16(a)—(b)和图17(a)—(c)所示, 随拉伸负载增加, 孔洞沿拉伸方向增长, 孔洞体积相应增大, 孔洞附近OTHER结构原子开始增多, 有部分OTHER结构向HCP结构转化. 继续拉伸, 如图16(c)—(e)和图17(c)—(e)所示, 孔洞沿[010]晶向(与拉伸方向垂直的方向)增大, 孔洞形状为近球形, 孔洞附近OTHER结构原子继续增多. 如图16(f)和图17(f)所示, 当拉伸应变达到幅值ε = 0.1206时, 孔洞体积几乎不变, 形状向球形转变.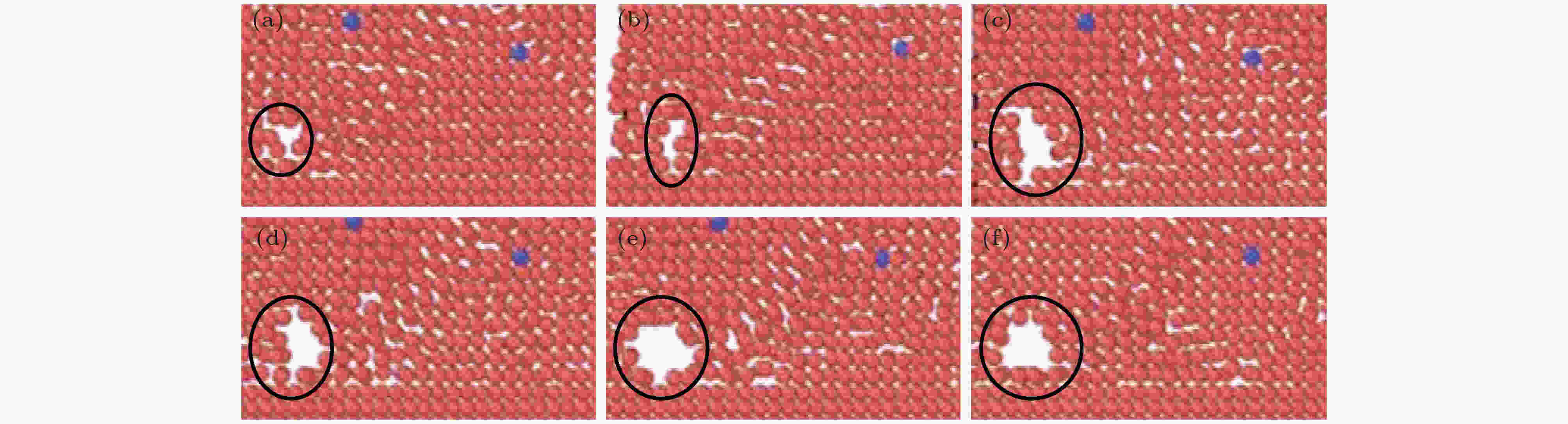
Figure16. Void Ⅱ: screenshot of the growth evolution of the void (red for aluminum atoms, blue for copper atoms), ε is (a) 0.1170; (b) 0.1173; (c) 0.1179; (d) 0.1182; (e) 0.1185; (f) 0.1206.
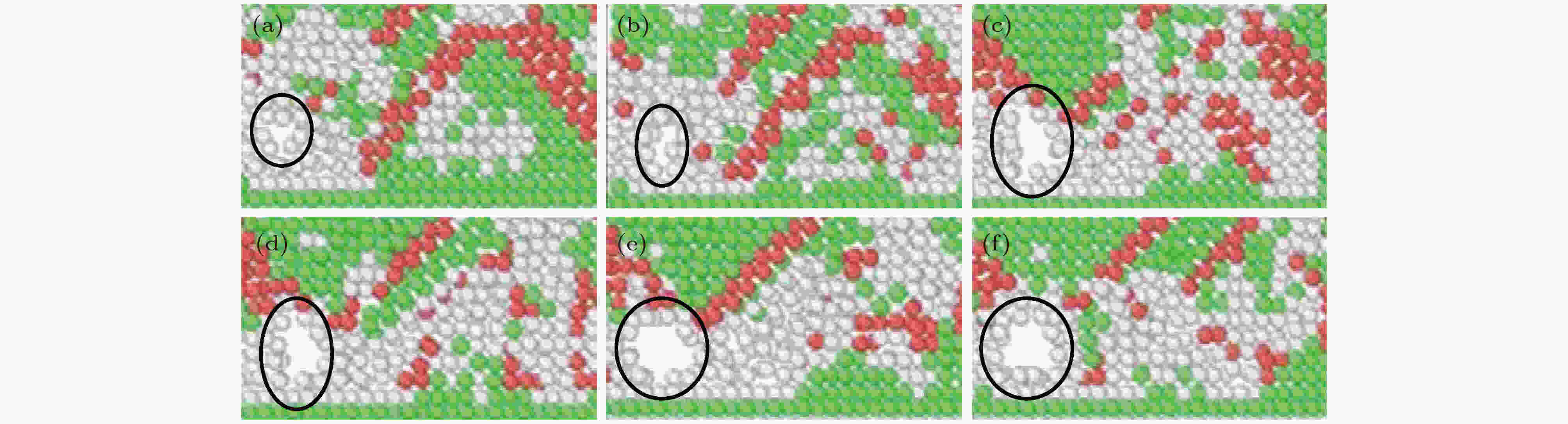
Figure17. Void Ⅱ: screenshot of the atomic structure of the growth evolution of the void (red for the HCP structure, green for the FCC structure, white for the OTHER structure), ε is (a) 0.1170; (b) 0.1173; (c) 0.1179; (d) 0.1182; (e) 0.1185; (f) 0.1206.
与孔洞Ⅰ相比, 如图17和图8所示, 孔洞Ⅱ在生长过程中孔洞尺寸较大, 孔洞Ⅱ生长经历了Δε = 0.0036的应变, 远小于孔洞Ⅰ生长所经历的Δε = 0.0666应变, 孔洞Ⅱ长大速度较快, 但它们的生长外形变化方式相同.
3
3.2.3.孔洞Ⅱ的闭合
在卸载阶段, 如图18(a)—(c)和图19(a)—(c)所示, 孔洞两侧{111}面原子向孔洞处滑移, 产生大面积的层错, 孔洞沿[001]晶向(拉伸应变卸载方向)减小, 收缩成椭球形. 卸载到ε = 0.0456时, 如图18(c)—(e)和图19(c)—(e)所示, 孔洞沿椭圆短长轴([010]晶向)向孔洞中心收缩减小, 紧接着孔洞几乎完全被OTHER原子填充, 孔洞位置处又处于位错交截状态[48]. 卸载到ε = 0.0306时, 如图18(f)和图19(f)所示, 孔洞位置处原子间距进一步减小, 原子排列紧密, 孔洞位置处HCP结构继续向OTHER转变直至几乎全部消失, OTHER结构转化为FCC结构.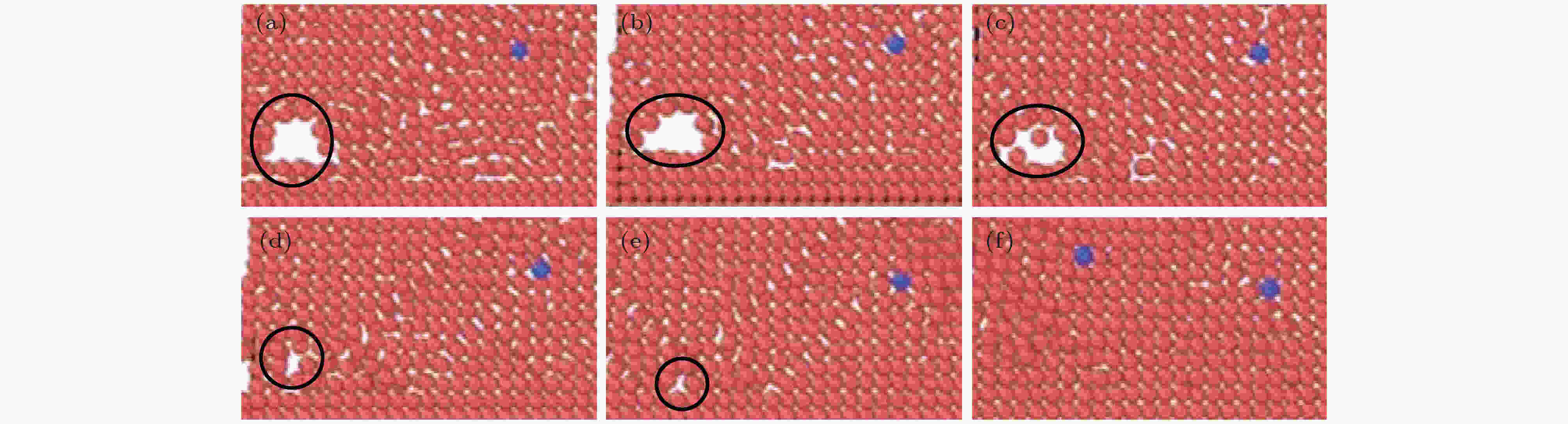
Figure18. Void Ⅱ: screenshot of the closure evolution of the void (red for aluminum atoms, blue for copper atoms), ε is (a) 0.1203; (b) 0.0906; (c) 0.0756; (d) 0.0606; (e) 0.0456; (f) 0.0306.
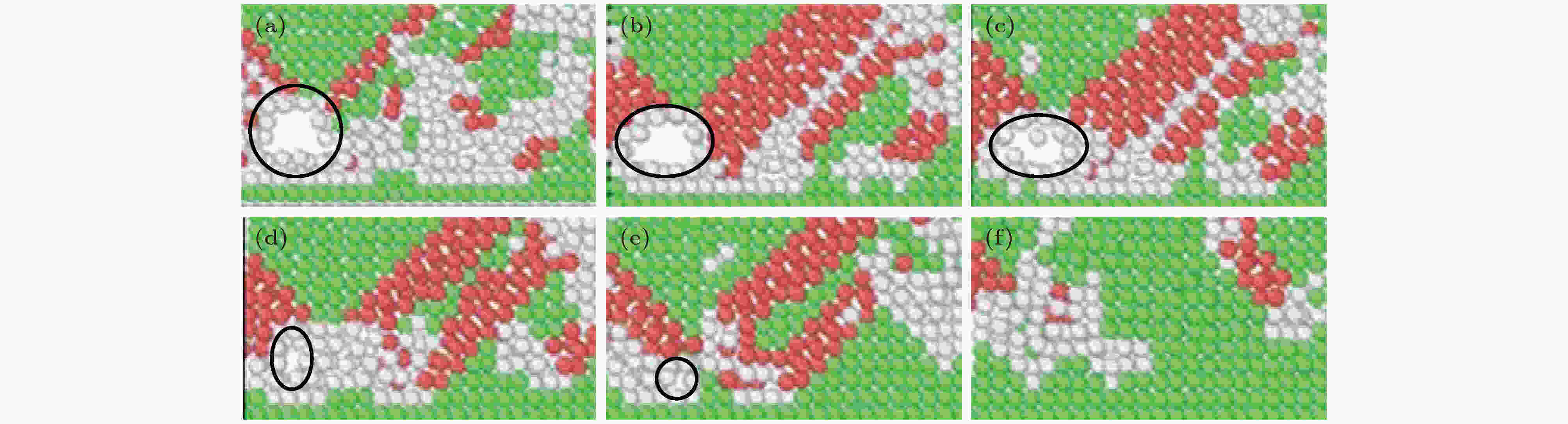
Figure19. Void Ⅱ: screenshot of the atomic structure of the closure evolution of the void (red for HCP structure, green for FCC structure, white for OTHER structure), ε is (a) 0.1203; (b) 0.0906; (c) 0.0756; (d) 0.0606; (e) 0.0456; (f) 0.0306.
与孔洞Ⅰ相比, 孔洞Ⅱ闭合经历了Δε = 0.0897的应变, 小于孔洞Ⅰ生长所经历的Δε = 0.1650应变, 孔洞Ⅱ在闭合过程中闭合较快, 并且在没有进入反向压缩阶段就已完全闭合, 孔洞Ⅱ两侧位错向孔洞处发展, 最后又回到压杆位错状态, 这说明在卸载过程中, 位错又重新生成并沿反向演化. 但孔洞Ⅱ与孔洞Ⅰ在闭合过程中外形变化形式相同.
1)在应变循环载荷作用下, 孔洞形核、生长以及闭合存在于不同的应变阶段, 在应变拉伸阶段孔洞形核、长大, 在应变卸载或反向加载阶段孔洞闭合. 在孔洞形核阶段, 都是在紊乱的OTHER结构区域内形核. 孔洞长大过程中, 外形首先沿应变加载方向拉伸长大, 然后沿与应变加载方向相垂直的方向长大, 趋向球形发展. 孔洞闭合过程中, 沿应变卸载方向收缩减小, 最后沿与应变卸载相垂直的方向闭合消失.
2)孔洞有两种演化方式: 孔洞Ⅰ是铜扩散到铝原子过程中引发的空隙缺陷而形核, 空隙缺陷形成空位后, 空位在铝侧OTHER结构内部向铜原子数相对密集的区域发生位置的移动, 当空位聚集形成孔洞时便在固定位置生长扩大; 孔洞Ⅱ形核前主要是压杆位错被克服而引发的空隙缺陷而形核, 孔洞形核后在铝侧没有位置的移动. 与孔洞Ⅰ相比, 孔洞Ⅱ形核时的应力大, 形核后迅速长大, 尺寸大, 在闭合过程中孔洞闭合消失也较快.