张立浩,钱波,张朝瑞,茅健,樊红日
(上海工程技术大学 机械与汽车工程学院,上海201600)
摘要:
近年来金属增材制造技术的快速发展,使其在航空航天、医疗行业、汽车制造等领域得到了大量应用。本文简要介绍了金属增材制造的典型工艺、金属粉末和金属丝材的制备方法以及基于文献统计的方法分析金属增材制造目前的研究热点和发展趋势。结果表明,金属增材制造技术在仿真设计、制造工艺、过程监控、质量评估、后续处理等领域还没有形成完善的研究体系和标准规范,阻碍了不同增材制造技术的应用融合。研究的深入以及材料和工艺的扩展会促进金属增材制造技术的不断突破以更好的满足现代生产的需求,工艺数据库也会应运而生,对零件的性能控制更细化更完善。
关键词: 金属增材制造 激光选区熔化 电子束选区熔化 统计分析 增材制造发展趋势
DOI:10.11951/j.issn.1005-0299.20210111
分类号:TB31
文献标识码:A
基金项目:国家重点研发计划-面向增材制造的模型处理以及工艺规划软件项目 (2018YFB1105300).
Summary of development trend of metal additive manufacturing technology
ZHANG Lihao, QIAN Bo, ZHANG Chaorui, MAO Jian, FAN Hongri
(School of Mechanical and Automotive Engineering, Shanghai University of Engineering Science,Shanghai 201600, China)
Abstract:
In recent years, with the rapid development of metal additive manufacturing, it has been widely applied in aerospace, medical industry, automobile manufacturing, and other fields. In this paper, the typical processes of metal additive manufacturing, preparation of metal powder and metal wire are introduced,and the research hotspots and development trend of mental additive manufacturing are analyzed based on literature statistics. Results show that concerning the application of metal additive manufacturing technology, it has not formed a complete and standard research system in simulation design, manufacturing process, process monitoring, quality assessment, and post processing, which hinders the integration of different additive manufacturing technologies. With further research and expansion of materials and processes, more breakthroughs in metal additive manufacturing will be made continuously to better meet the needs of modern production. The process database will emerge in response to the proper time, and the control of part performance will be more refined and accurate.
Key words: metal additive manufacture laser selective melting electron beam selective melting statistical analysis development trend of additive manufacturing
张立浩, 钱波, 张朝瑞, 茅健, 樊红日. 金属增材制造技术发展趋势综述[J]. 材料科学与工艺, 2022, 30(1): 42-52. DOI: 10.11951/j.issn.1005-0299.20210111.

ZHANG Lihao, QIAN Bo, ZHANG Chaorui, MAO Jian, FAN Hongri. Summary of development trend of metal additive manufacturing technology[J]. Materials Science and Technology, 2022, 30(1): 42-52. DOI: 10.11951/j.issn.1005-0299.20210111.

基金项目 国家重点研发计划-面向增材制造的模型处理以及工艺规划软件项目(2018YFB1105300) 通信作者 钱波, E-mail: qianbo@sues.edu.cn 作者简介 张立浩(1997—), 男, 硕士研究生 文章历史 收稿日期: 2021-05-12 网络出版日期: 2021-08-16
Contents Abstract Full text Figures/Tables PDF
金属增材制造技术发展趋势综述
张立浩, 钱波


上海工程技术大学 机械与汽车工程学院,上海 201600
收稿日期: 2021-05-12; 网络出版日期: 2021-08-16
基金项目: 国家重点研发计划-面向增材制造的模型处理以及工艺规划软件项目(2018YFB1105300)
作者简介: 张立浩(1997—), 男, 硕士研究生.
通信作者: 钱波, E-mail: qianbo@sues.edu.cn.
摘要: 近年来金属增材制造技术的快速发展,使其在航空航天、医疗行业、汽车制造等领域得到了大量应用。本文简要介绍了金属增材制造的典型工艺、金属粉末和金属丝材的制备方法以及基于文献统计的方法分析金属增材制造目前的研究热点和发展趋势。结果表明,金属增材制造技术在仿真设计、制造工艺、过程监控、质量评估、后续处理等领域还没有形成完善的研究体系和标准规范,阻碍了不同增材制造技术的应用融合。研究的深入以及材料和工艺的扩展会促进金属增材制造技术的不断突破以更好的满足现代生产的需求,工艺数据库也会应运而生,对零件的性能控制更细化更完善。
关键词: 金属增材制造 激光选区熔化 电子束选区熔化 统计分析 增材制造发展趋势
Summary of development trend of metal additive manufacturing technology
ZHANG Lihao, QIAN Bo


School of Mechanical and Automotive Engineering, Shanghai University of Engineering Science, Shanghai 201600, China
Abstract: In recent years, with the rapid development of metal additive manufacturing, it has been widely applied in aerospace, medical industry, automobile manufacturing, and other fields. In this paper, the typical processes of metal additive manufacturing, preparation of metal powder and metal wire are introduced, and the research hotspots and development trend of mental additive manufacturing are analyzed based on literature statistics. Results show that concerning the application of metal additive manufacturing technology, it has not formed a complete and standard research system in simulation design, manufacturing process, process monitoring, quality assessment, and post processing, which hinders the integration of different additive manufacturing technologies. With further research and expansion of materials and processes, more breakthroughs in metal additive manufacturing will be made continuously to better meet the needs of modern production. The process database will emerge in response to the proper time, and the control of part performance will be more refined and accurate.
Keywords: metal additive manufacture laser selective melting electron beam selective melting statistical analysis development trend of additive manufacturing
1 金属增材制造技术简介金属增材制造技术[1]从上世纪80年代发展到今天,技术逐步得到改进和完善。金属增材制造技术与传统加工的“等材制造”和“减材制造”原理大不相同[2],它依靠粉末或者丝材实现成形制造,如图 1所示,通过运用“分层-叠加”原理[3],把三维模型分层处理,按照分层所得截面数据规划路径,热源逐层熔融粉末或丝材达到成形目的[4-7]。金属增材制造技术以缩短生产时间、降低材料消耗量和多材料一体成型为特点[8-12],可以不受限于结构的复杂性,制造复杂结构零件或者薄壁零件,成形壁厚可以达到80 μm,能够快速、高效、优质、经济的打印制造出三维实体模型。金属增材制造技术的智能化、柔性化制造优势使定制化制造拥有了无限的潜力[13]。
图 Figure1(Fig.Figure1)
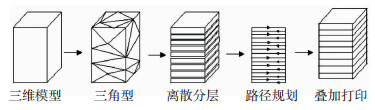
金属增材制造技术作为高端数字化智能制造技术,是先进制造业中最具潜力和最有发展前景的制造技术,是“引领第三次工业技术革命的核心技术之一”。随着新一轮科技革命与产业革命的逐渐兴起,智能化制造成为工业制造领域的一个新的热点,金属增材制造技术的智能化加工过程作为一个全新的切入点,各个国家也都重视起来,以期在未来能够领跑高新技术加工制造[14]。我国2015年颁布的《中国制造2025》提出把智能加工作为重点发展方向之一,金属增材制造技术节能环保的技术特点高度契合我国的可持续发展战略[15]。
2 金属增材制造技术的分类金属增材制造技术的原理是对三维数字模型进行切片,得到每层切片的截面数据,规划扫描路径传输给控制系统,同时刮刀预先铺粉,Z轴向下移动一个层厚,系统控制热源按照待加工层扫描路径快速扫描,材料熔化与已成形层形成冶金状态的结合,循环逐层沉积,成形CAD模型的实体[16]。热源主要分为激光束、电子束和电弧,原料按照物理状态主要分为粉末、丝状。金属增材制造技术可分为直接能量沉积[17](Directed Energy Deposition, DED)和粉末床熔融[18-20](Powder Bed Fusion, PBF)。DED包括电弧增材制造(Wire Arc Additive Manufacturing, WAAM)和激光近净成形(Laser Engineered Net Shaping, LENS);PBF包括电子束选区熔化(Electron Beam Selective Melting, EBSM)和激光选区熔化(Selective Laser Melting, SLM)[2]。
2.1 电弧增材制造(WAAM)电弧增材制造是在电弧焊的基础上发展的新型加工技术。电弧焊是一种堆焊,金属丝材熔化层层累加,凝固堆积成形。丝材加工过程中热量集中不容易发散,熔池大小不易控制,热影响区较大[21-22],对成形件的尺寸精度和表面质量影响较大,会降低成品质量,甚至无法满足使用要求。WAAM通常选取金属丝材为原材料,适合大尺寸复杂零件的高效、快速、经济加工,在高性能高附加值成形件方面有较多的成功案例[23-24]。WAAM的热源是电弧,对金属材料的光反射率不敏感,可以加工如铜合金,铝合金等高反射率的金属材料。
2.2 电子束选区熔化(EBSM)图 2是EBSM成形原理简图,电子束选区熔化技术依靠电磁线圈控制电子束精确、快速偏转[25],按照截面轮廓规划的路径扫描,利用电子束熔化预铺设的金属粉末,循环层层累加,加工出三维零件[4]。EBSM电子束能量密度高,加工高效快速,加工精度高,成形件力学性能好,表面质量高,适合钛合金、钛铝基合金等难熔金属的小批量、小尺寸、结构复杂及高附加值零件的加工[26]。EBSM在结构复杂件的制造中能充分发挥高精度制造的优势,但EBSM技术需要一整套配套设备,要求在真空环境下操作,前期准备成本较高[2],故更适合单件或小批量样品的快速加工,能快速响应产品的设计,缩短产品研发周期。
图 Figure2(Fig.Figure2)
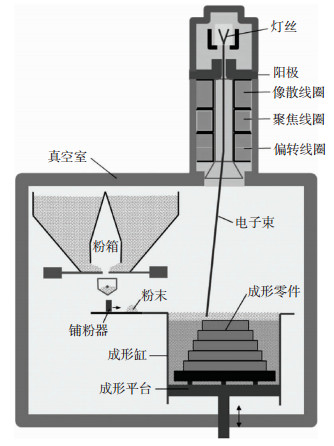
2.3 激光近净成形(LENS)激光近净成形是热源和粉末材料同轴或者旁轴输送,热源熔化粉材,逐层固化黏结累加实现三维模型成形的新型加工技术。图 3是LENS技术成形金属零件的简要示意图,金属粉末是旁轴输送,其加工原理是:三维模型进行分层切片,确定每层的运动路径信息,系统控制热源和送粉头按照每层截面的运动路径以一定的速率在XY平面运动,热源熔化材料形成熔池并快速冷却,堆积成形,层间结合具备冶金效果。
图 Figure3(Fig.Figure3)
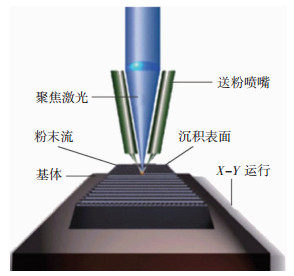
获得的实体零件致密度可达到99%,可承载力学载荷[27];材料利用率高,几乎不会浪费材料[9];但激光束束径较大,加工成形精度较低(毫米级),适合于大尺寸毛坯件的加工成形,一般还需要后续加工处理才能获得所需精度的零件。同时,加工过程中,加工成形区温度分布不均匀形成温度梯度,成形件热应力集中容易发生边缘翘曲[28-29],降低成形件的成形质量和成品率,增加制造成本和时间。
2.4 激光选区熔化成形(SLM)SLM的原理与LENS相似,但不同于LENS的同轴或旁轴送粉,SLM需要预铺粉,铺设粉末依靠图 4所示刮刀往复运动。铺粉装置在工作平台铺设一层高度为预设层厚的金属粉末,激光束按照当前层的运动路径对工作平面进行快速扫描熔化粉末,逐层累加加工零件。通过调节激光束功率、扫描宽度、扫描速度、扫描间隙等工艺参数[30]可以加工同种材料的匀质件及异质材料的过渡功能或梯度功能零件。所使用的激光功率较小,一般在200~1 000 W,激光束直径小,成形精度高,成形件表面质量较其他增材技术高,但成形效率较低,适合小尺寸复杂结构零件的加工制造[31]、模具设计制造,可以有效地缩短设计周期,加速产品研发。对于结构复杂件,变截面以及异形构件[32]的加工,激光选区熔化加工技术具有独特优势。同时,加工过程中,由于层厚小,金属粉末经历了完全的熔化和快速凝固过程,成形件致密度高,可达到100%,同时兼具了高精度和优良性能的制造要求。因此,SLM加工技术被认为是金属增材制造领域最具发展潜力,最有发展前景的加工技术之一[33]。
图 Figure4(Fig.Figure4)
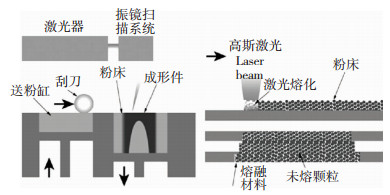
图 5为本文采用SLM-M150多材料打印设备对规格为15~53 μm的316L粉末打印成形的样品。
图 Figure5(Fig.Figure5)
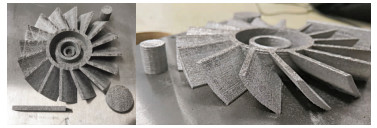
3 金属粉末、丝材制备和成分设计3.1 金属粉末制备3.1.1 雾化法雾化法以水或者高速气流作为雾化介质,粉碎金属液流制备金属粉末。水雾化法[34]在制备镍基及钢铁粉末等工艺中广泛应用,但水作为介质易与活性金属发生化学反应,增加粉末含氧量。水的比热容大,在制备过程中,粉碎的金属液滴快速凝固会直接影响粉末球形度,增加卫星粉数量,难以满足粉末使用要求,限制了水雾化法的应用。气雾化法[35]采用高速气流粉碎金属液滴。采用惰性气体制备的金属粉末含氧量较水雾化法更低,粉末球形度较高,杂质含量更低,容易控制粉末粒度。但是由于气体具有的能量较低,在粉碎金属液滴过程中会降低制备效率,同时惰性气体的使用也会增加成本。
3.1.2 等离子法等离子旋转电极雾化工艺以惰性气体为氛围,材料电极和等离子弧热源水平对向同轴放置,材料电极被加热的同时高速旋转,依靠离心力甩出顶端被熔化的金属液滴,受表面张力作用最终凝固为球形粉末。可以通过调节材料电极的转速和等离子弧电流控制粉末粒径,得到球形度高,氧含量低的金属粉末[36]。最终成形依赖液滴表面张力,因此粉末中的卫星粉、空心粉含量低。
等离子熔丝雾化工艺以金属丝材为原材料,垂直送入雾化炉,经等离子体热源加热雾化形成球形度高,纯度高的金属粉末。同时在氩气等惰性气体氛围中,可有效减少杂质含量。控制丝材进给速度可以调控粉末粒径,制备特定粒径的金属粉末。
等离子球化工艺是对不规则金属粉末二次熔化再加工的粉末制备技术[37]。不规则金属粉末在气流作用下经过热等离子体加热熔化,冷却凝固过程中受自身表面张力作用和温度变化作用成形,得到球形度高,致密度高的金属粉末。
表 1列出了常用金属粉末制备方法的优缺点,根据成形件的性能要求可选择不同的制备方法。目前国内金属粉末制备存在氧含量高、球形度差和粒径分布不均匀等问题,超细粉及优质粉末仍需进口,亟需加大研究突破制备工艺。
表1(Table 1)
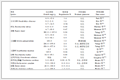
气雾化法[38] 利用高压气流件将熔融金属液滴破碎成小液滴并凝固成粉末 氧含量低,粉末粒度可控,球形度高,制备速率大 制备的粉末空心粉和卫星粉多
等离子旋转电极雾化工艺[39] 等离子体加热棒体材料并依靠离心力细化熔融金属液滴,在表面张力作用下球化形成粉末 适用于钛合金、高温合金等合金粉末的制备,球形度高,流动性好 粉末整体偏粗,对设备密封、振动等要求较高
等离子熔丝雾化工艺[40] 高温等离子体加热熔融金属丝,利用低温氩气冷却凝固成超细粉末 金属粉末呈近规则球形,粉末整体粒径偏细 丝材制粉限制了可使用金属类型且增加了制备粉末成本
等离子球化工艺[40] 利用载气将粉末送到高温等离子体中,粉末颗粒迅速熔融,表面张力使其成形为球体,快速冷却得到球形粉末 颗粒致密,规则球形 难以制备低氧含量细粒径钛合金粉末
表 1 常用金属粉末制备方法Table 1 Preparation methods of metal powder
3.2 金属丝材制备现阶段,增材制造用丝材要经冶炼、拉拔等工艺制备,受工艺限制,对能冶炼但无法拉拔成丝材的材料无法加工,只能对特定金属材料进行加工。同时受增材制造工艺限制,对丝材的焊接性能要求高,进一步限制了金属丝材的种类和数量。目前,激光近净成形等以丝材为耗材的增材制造工艺多以钛合金、镍基合金、不锈钢为主要材料。
3.3 金属粉末成分设计粉末材料的物理特性对加工质量有很大影响[41-42],提升粉末材料在加工及成形零件时的有益特性很有必要。在粉材中加入不同种类的纳米添加剂可以有效提高粉材的流动性和光学特性。通过加入少量添加剂来有效改善加工过程中的缺陷和成形件的机械性能是目前粉材制备中的一个研究热点。Lüddecke等人[43]通过实验研究碳化硅、石墨烯原子层在不锈钢、工具钢和铝合金钢对激光吸收率和润滑性上的影响,发现纳米添加剂提高了金属粉末的光吸收率和流动性。Karunakaran等人[44]研究发现在镁粉中加入钇和钕等高活性金属粉末可以提高镁粉的加工性,提升机械性能。根据不同的加工工艺和功能要求针对性的设计粉末成分,提高成形件的性能和质量,满足使用要求,是亟需发展的研究方向。
4 文献分析金属增材制造技术发展至今,相关领域发表了大量的文献资料,通过对文献统计分析,了解增材制造技术的发展方向,洞悉增材制造的研究热点,在此基础上分析未来的发展趋势。
4.1 论文发表情况在web of science数据库,以标题“additive manufacturing”并含“3D printing”为检索条件,经过严格的去重筛选,剔除其中出现的重复论文、会议摘要、无作者以及与内容无关的无效结果,共得到23 282篇有关文献。从图 6可以看出,2010年以来,文献数量逐年增加,发文量呈指数式增长,2020年发表了5 171篇文献,近几年来发文量较多,近十年金属增材制造技术研究热度逐年递增。
图 Figure6(Fig.Figure6)
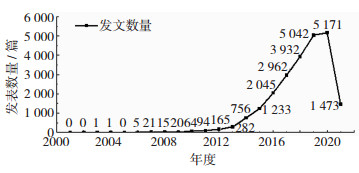
从图 7分析文献分布的学科领域,ENGINEERING、MATERIALS SCIENCE和PHYSICS发文量占据前三。ENGINEERING领域共发表了15 328篇相关文献,以绝对优势位居第一,占比达到65.836%。MATERIALS SCIENCE和PHYSICS领域发文量占比分别为47.685%、27.824%, 表明增材制造的研究领域主要集中在工程、材料和物理性能方面,符合目前发展的研究趋势。其中,材料领域的发展会让增材制造的材料有更大的选择自由度,满足工程应用领域对3D打印件的复合多功能需求。
图 Figure7(Fig.Figure7)
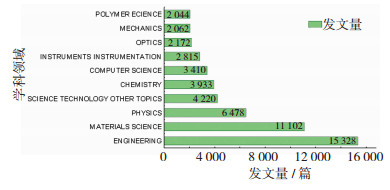
为了更好地了解增材制造领域的研究方向和发展状况,从23 282篇相关文献中选出405篇高被引论文,从高被引论文作者发文数量的角度进行分析(图 8)。在图 8中,作者BASIT A W排名第一位,发表的高被引论文量占总分析论文的16.049%,GAISFORD S,GOYANES A位列第二、三位,是增材制造领域的权威专家,在增材制造领域具有影响力。在前十位高被引论文中(表 2),FRAXIER, WILLIAM E于2014年发表的“Metal additive manufacturing: a review”引用量高达2 034,位居第一,具有绝对的领先优势。从表 2中可以看到,高被引论文多集中发表在2012-2016年间,排名靠前的高被引论文多是对增材制造技术的回顾与展望,基础且全面,涉及具体课题的论文较少,表明目前对3D打印技术的研究多是基础研究。
图 Figure8(Fig.Figure8)

表2(Table 2)
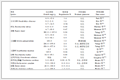
1 Metal additive manufacturing: a review Frazier, William E JOURNAL OF MATERIALS ENGINEERING AND PERFORMANCE 2014 2 034
2 Laser additive manufacturing of metallic components: materials, processes and mechanisms Gu D D, Meiners W, Wissenbach K INTERNATIONAL MATERIALS REVIEWS 2012 1 485
3 Additive manufacturing of metallic components-Process, structure and properties DebRoy T, Wei H L, Zuback J S PROGRESS IN MATERIALS SCIENCE 2018 1 347
4 Additive manufacturing (3D printing): a review of materials, methods, applications and challenges Ngo Tuan D, Kashani A, Imbalzano, Gabriele COMPOSITES PART B-ENGINEERING 2018 1 180
5 Additive manufacturing of metals Herzog Dirk, Seyda V, et al ACTA MATERIALIA 2016 1 173
6 3D printing of polymer matrix composites: a review and prospective Wang Xin, Jiang Man, Zhou Zuowan COMPOSITES PART B-ENGINEERING 2017 878
7 3D printing based on imaging data: review of medical applications Rengier F, Mehndiratta A, von Tengg-Kobligk H NTERNATIONAL JOURNAL OF COMPUTER ASSISTED RADIOLOGY AND SURGERY 2010 878
8 Continuous liquid interface production of 3D objects Tumbleston J R, Shirvanyants David, Ermoshkin Nikita AMER ASSOC ADVANCEMENT SCIENCE 2015 869
9 Bone tissue engineering using 3D printing Bose S, Vahabzadeh S, et al MATERIALS TODAY 2013 850
10 The status, challenges, and future of additive manufacturing in engineering Gao Wei, Zhang Yunbo, Ramanujan Devarajan COMPUTER-AIDED DESIGN 2015 846
表 2 2000~2021年间增材制造领域被引次数排名前10的论文Table 2 Top 10 papers cited in the field of additive manufacturing during 2000 and 2021
4.2 文献关键词分析在“web of science”核心合集,以2006~2021年为时间段,以标题“(additive manufacturing or AM)and(metal)”为检索条件,得到763篇相关论文,按照被引频次从高到底排序,利用CiteSpace软件对前500篇论文进行分析,得到图 9的突现词阶段变化特征反映发展趋势。图 9展示了金属增材制造研究过程在某个阶段出现的关键词,得到4个突现词。2014~2017年间,金属增材制造的关键词是“fabrication”、“deposition”,制造和沉积是当时的研究前沿; 2017~2018年间的关键词是“simulation”,表明对金属增材制造技术的仿真模拟研究较多,成为当时的研究前沿; 从2019年至今,高被引论文的关键词为“prediction”,强度达到3.07,表明对成型过程的实时预测加大了研究力度。实时观察预测会对成型过程的各种突发状况进行及时有效的处理,显著提高成形件质量。
图 Figure9(Fig.Figure9)
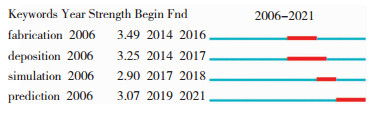
关键词是从期刊论文正文中提取出的单词或者术语,并且能以关键词表达出该文章的主旨大意。关键词出现的频次越高代表学者对其关注度越高。图 10关键词共现图谱显示,出现频率靠前的关键词有“microstructure”、“surface roughnes”、“additive manufacturing”、“3d printing”、“numercial modelling”、“aluminium alloys”、“yield”、“electron beam melting”、“binder jetting”,不难发现,最近十年的研究热点包括:机械性能研究,成形件质量评测,微结构研究,仿真模拟,成形材料,成型制造工艺。需要注意的是,增材制造研究的领域关联性不大(图 10,Density=0.015 5),呈现多方向研究趋势,没有形成统一的指导形式,需要不断迭代研究,建立标准化设计和制造体系,促进不同研究方向不断融合,实现跨领域,跨学科深入研究。
图 Figure10(Fig.Figure10)
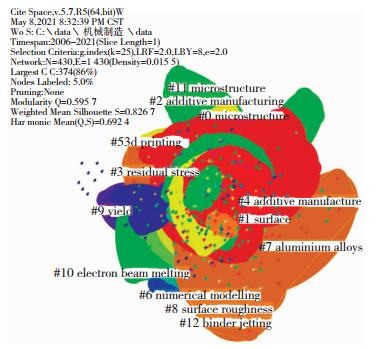
5 金属增材制造研究趋势金属增材制造技术发展迅速,通过对现存文献的分析[45-47],可得出如下结论。
5.1 金属增材制造技术材料的新扩展目前,大多数金属增材制造技术都是以能量束为热源,如激光束和电子束,在加工成形过程中,材料对能量的吸收率对成形质量有很大影响。大多数研究工作都集中在钛基、镍基和铁基合金粉末上,其中一些材料和工艺组合已经进入实际应用的成熟阶段,对激光能量具有高反射率的铝基合金激光增材制造面临重大挑战[48]。要对粉末材料制备及其化学、物理性能表征进行研究,包括预合金、铁、钛、铝、镍基粉末,适应功能要求的多样性。
5.2 金属增材制造技术制造功能梯度件和复杂多孔材料的新工艺利用加工过程的高度非平衡性质, 有利于制造具有独特微观结构和性质的材料。SLM基于液相烧结机制对粉末的处理[49-50],已经证明了加工多组分金属粉末和预合金粉末的可行性[14, 51]。通过部分熔化机制对钛和钽进行处理,形成复杂的多孔植入物,在医学应用方面有很高的潜力。通过改变激光功率和扫描速度改变粉末和激光的相互作用时间,形成具有不同孔隙率的多孔结构[52-55],以适应医学植入物重量尽可能轻同时确保适当的结构和机械特性的要求[56]。
5.3 金属增材制造技术加工数据库的完善金属增材制造技术最初因材料可选择性大,低成本和应用到各种领域的巨大潜力而发展起来的,分散式研究导致没有统一的评价标准和实践指南[57]。CAD设计3D模型采用嵌入原理[58],对于几何零件的保真度低,加之机器的分辨率不同,加工出的成型件表面光洁度和几何精度很难得到保证,要求精度高时,甚至会导致零件报废。应积累各种金属材料的合适的加工数据,结合粉末设计和制备的优化,实验确定相应的最佳增材制造工艺参数,建立材料工艺数据库,实现对工业应用通用粉末材料的增材制造处理的简单、精确和稳定的控制, 如王江等[59]采用机械混合法和搅拌蒸发法制备SiC复合粉末并利用激光选区烧结、碳化和渗硅反应处理成形SIC陶瓷零件来研究成形工艺对成形件的性能影响。
5.4 金属增材制造技术仿真模拟基于激光等高能光束的加工过程通常具有复杂的非平衡物理和化学冶金性质,对材料和工艺有很大的依赖性。粉末特性(如化学成分、颗粒形状、颗粒粒径及其分布、松散饱和度和粉末流动性)和加工参数(如激光类型、光斑尺寸、激光功率、扫描速度、扫描间距和层厚)都会对成形组件的质量产生影响。通常情况下,很难对使用金属增材制造技术工艺加工的某种材料进行显微结构特征(粒度、纹理等)以及由此产生的机械性能(强度、硬度、残余应力等)作出准确预测。为了对成形组件的残余应力和微观结构有一个详细的了解,需要做出大量实验,这是不现实的,因此需要建立模型模拟。现有的金属增材制造技术过程理论建模多集中在相对宏观的热场[60]、应力场[61]和体积收缩效应[62],很少涉及微观流体流动计算[63]。对非平衡熔融池内熔体的冶金热力学和动力学行为的理论研究特别重要,包括流体流动,晶核成核和生长,关键合金的熔化和混合行为,从而使微观结构能够根据组件的局部性能要求进行定制。
5.5 增减材智能制造一体化增材制造在成形方面具有速度快、机构易构性高、自动化程度高等优点,传统减材制造对零件精加工和表面处理如提高准确度、精密度和表面粗糙度方面具有优势。基于现有加工技术,结合不同工艺优势,开发了以增减材制造一体化为理念的复合加工快速成形系统,采用增材成形,减材加工,“先增后减,边增边减”的加工顺序,实现零件加工的一体化[64]。增减材复合制造需要适应不同材料不同加工工艺的要求,模块化的软硬件集成必不可少;高价值、高精度的零件加工需要实时监测,因此多类型高精度的检测技术是提高零件质量的必要因素;目前的制造控制方式多是开环控制,全闭环的加工过程控制能对过程实时调整,提高系统鲁棒性,实现高效高精加工[65]。
5.6 成分-结构-功能一体化增材制造的显著特点是金属的高冷却率[66]和高精炼性,这导致零件的微观结构发生变化[67],改变成形件的宏观性能。高凝固率显著增加了增材制造可用光谱的范围,使不可混溶或过饱和的合金组合物加工成为可能。如通过将铜和钨熔融于一体,可得到一种集铜高导电率和钨高熔点的新材料,提高宏观材料的物理和力学性能[68]。一种新思路是在原粉中加入添加剂,使其满足特定的加工或使用要求,如通过添加剂提高可加工性(流动性、润滑性,能量吸收率)或者功能特性(机械强度、电导率、磁导率)[69]。对零件轻量化和一体化的需求催生了功能梯度材料,功能梯度材料由两种及以上材料组合而成,包括金属、合金和金属基复合材料,集成了不同材料的物理、力学特性。由异质材料通过增材制造成形的形状复杂、微结构可控的复合功能金属零件具有多功能性特点,对满足航空航天、国防、汽车和生物医学工业的严苛使用要求具有重要意义。
6 金属增材制造技术展望金属增材制造过程中,材料经受反复的受热、熔化和快速凝固以及固态相变,对分析微观结构和机械性能带来了巨大的挑战。但金属增材制造技术发展迅速,各国研究机构都在加大力度投入大量资源进行科研攻关,在增材设备,制造工艺,参数优化,零件质量控制及后续处理等方面开展研究。金属增材制造技术能减少能源消耗和碳排放,对环境友好,但需要更深入的研究探索,需要一整套系统来合理评估金属增材制造技术的优势以及潜在的风险。金属增材制造技术目前作为传统制造工艺的补充,被公认为是未来成形方式方面最具发展潜力和发展前景的制造技术之一。加快对金属增材制造技术的科学研究,充分发挥增材制造技术的独特优势,将是提高国家的综合国力,加快高新技术发展的助推器。
参考文献
[1] KEICHER D. Beyond rapid prototyping to direct fabrication: forming metallic hardware directly from a CAD solid model[J]. Materials Technology, 1998, 13(1): 5-7. DOI:10.1080/10667857.1998.11752757
[2] 袁宏, 何戈宁, 李磊, 等. 3D打印技术在核电领域的发展应用情况综述[J]. 科技视界, 2020(17): 118-122.
YUAN Hong, HE Gening, LI Lei, et al. Development and application of 3D printing technology in nuclear power[J]. Science & TechnologyVision, 2020(17): 118-122. DOI:10.19694/j.cnki.issn2095-2457.2020.17.40
[3] 雷聪蕊, 葛正浩, 魏林林, 等. 3D打印模型切片及路径规划研究综述[J]. 计算机工程与应用, 2021, 57(3): 24-32.
LEI Congrui, GE Zhenghao, WEI Linlin, et al. A review of 3D printing model slice and path planning[J]. Computer Engineering and Applications, 2021, 57(3): 24-32. DOI:10.3778/j.issn.1002-8331.2009-0106
[4] KEICHER D M, MILLER W D, SMUGERESKY JE, et al. Laser engineered net shaping (LENSTM): beyond rapid prototyping to direct fabrication[C]//TMS Annual Meeting. Minerals, Metals & Materials Soc (TMS), 1998: 369-377.
[5] ATWOOD C, ENSZ M, GREENE D, et al. Laser engineered net shaping (LENS (TM)): a tool for direct fabrication of metal parts[C]//17th International Congress on Applications of Lasers and Elector-Optics, 1998: 16-19.
[6] GARY K L, ERIC SCHLIENGER. Practical considerations and capabilities for laser assisted direct metal deposition[J]. Materials & Design, 2000, 21(4): 417-423. DOI:10.1016/S0261-3069(99)00078-3
[7] KEICHER D M, SMUGERESKY J E. The laser forming of metallic components using particulatematerials[J]. JOM, 1997, 49(5): 51-54. DOI:10.1007/BF02914686
[8] BHUSHAN B, CASPERS M. An overview of additive manufacturing (3D printing) for microfabrication[J]. Microsystem Technologies, 2017, 23(4): 1117-1124. DOI:10.1007/s00542-017-3342-8
[9] WONG K F V, HERNANDEZ A. A review of additive manufacturing[J]. International Scholarly Research Notices, 2012, 2012: 208760. DOI:10.5402/2012/208760
[10] MOHAMMAD V, HERMANN S, SHOU F Y. A review on 3D micro-additive manufacturing technologies[J]. The International Journal of Advanced Manufacturing Technology, 2013, 67(5-8): 1721-1754. DOI:10.1007/s00170-012-4605-2
[11] CONNER B P, MANOGHARAN G P, MARTOF A N, et al. Making sense of 3-D printing: creating a map of additive manufacturing products and services[J]. Additive Manufacturing, 2014, 1-4: 64-76. DOI:10.1016/j.addma.2014.08.005
[12] WILLIAM E, FRAZIER. Metal additive manufacturing: a review[J]. Journal of Materials Engineering and Performance, 2014, 23(6): 1917-1928. DOI:10.1007/s11665-014-0958-z
[13] 王庭庭, 张元彬, 谢岳良. 丝材电弧增材制造技术研究现状及展望[J]. 电焊机, 2017, 47(8): 60-64.
WANG Tingting, ZHANG Yuanbing, XIE Yueliang. Research status and prospect of wire arc additive manufacturing technology[J]. Electric Welding Machine, 2017, 47(8): 60-64. DOI: CNKI:SUN:DHJI.0.2017-08-014
[14] WILLIAMS S W, MARTINA F, DI NG, et al. Wire plus arc additive manufacturing[J]. Materials Science and Technology: MST: A publication of the Institute of Metals, 2016, 32(7/8): 641-647. DOI:10.1179/1743284715Y.0000000073
[15] 许洋. 金属3D打印技术研究综述[J]. 中国金属通报, 2019(2): 104-105.
XU Yang. A review of metal 3D printing technology[J]. China Metal Bulletin, 2019(2): 104-105. DOI: CNKI:SUN:JSTB.0.2019-02-066
[16] 周成候, 李蝉, 吴王平, 等. 金属材料增材制造技术[J]. 金属加工(冷加工), 2016(S1): 879-883.
ZHOU Chenghou, LI Chan, WU Wangping, et al. Manufacturing technology for metal material augmentation[J]. Machinist Metal Cutting, 2016(S1): 879-883.
[17] JIA H L, SUN H, WANG H Z, et al. Scanning strategy in selective laser melting (SLM): a review[J]. The International Journal of Advanced Manufacturing Technology, 2021, 113(9-10): 2413-2435. DOI:10.1007/S00170-021-06810-3
[18] KUO Y L, KAMIGAICHI A, KAKEHI K. Characterization of Ni-based superalloy built by selective laser melting and electron beam melting[J]. Metallurgical and Materials Transactions A, 2018, 49(9): 3831-3837. DOI:10.1007/s11661-018-4769-y
[19] JIA Q, GU D. Selective laser melting additive manufacturing of Inconel 718 super alloy parts: densification, microstructure and properties[J]. Journal of Alloys and Compounds, Journal of Alloys and Compounds, 2014, 585: 713-721. DOI:10.1016/J.ENG.2017.05.011
[20] SING S L, WIRIA F E, YEONG W Y. Selective laser melting of titanium alloy with 50wt.% tantalum: effect of laser process parameters on part quality[J]. InternationalJournal of Refractory Metals and Hard Materials, 2018, 77: 120-127. DOI:10.1016/j.ijrmhm.2018.08.006
[21] 耿海滨, 熊江涛, 黄丹, 等. 丝材电弧增材制造技术研究现状与趋势[J]. 焊接, 2015(11): 17-21, 69.
GENG Haibin, XIONG Jiangtao, HUANG Dan, et al. Current situation and trend of manufacturing technology technology of wire arc material increasing[J]. Welding & Joining, 2015(11): 17-21, 69. DOI:10.3969/j.issn.1001-1382.2015.11.003
[22] 田彩兰, 陈济轮, 董鹏, 等. 国外电弧增材制造技术的研究现状及展望[J]. 航天制造技术, 2015(2): 57-60.
TIAN Cailan, CHEN Jilun, DONG Peng, et al. Research status and prospect of foreign arc additive manufacturing technology[J]. Aerospace Manufacturing Technology, 2015(2): 57-60.
[23] CILIA T, BERTETTA D, GUALENI P, et al. Additive manufacturing application to a ship propeller model for experimental activity in the cavitation tunnel[J]. Journal of Ship Production and Design, 2019, 35(4): 364-373. DOI:10.5957/JSPD.11170055
[24] CARSTEN S, CHRISTIAN S. Developments in titanium research and applications in germany[C]//14th World Conference on Titanium (Ti-2019), 2020, 321.
[25] KOLAMROUDI MK, ASMAEL M, LLKAN M, et al. Developments on electron beam melting (EBM) of Ti-6Al-4V: a review[J]. Transactions of the Indian Institute of Metals, 2021, 74: 783-790. DOI:10.1007/s12666-021-02230-9
[26] 郭超, 张平平, 林峰. 电子束选区熔化增材制造技术研究进展[J]. 工业技术创新, 2017, 4(4): 6-14.
GUO Chao, ZHANG Pingping, LIN Feng. Research progress of melting additive manufacturing technology in electron beam constituency[J]. Industrial Technology Innovation, 2017, 4(4): 6-14. DOI:10.14103/j.issn.2095-8412.2017.04.001
[27] LIU Z C, KIM H, LIU W W, et al. Influence of energy density on macro/micro structures and mechanical properties of as-deposited Inconel 718 parts fabricated by laser engineered net shaping[J]. Journal of Manufacturing Processes, 2019, 42: 96-105. DOI:10.1016/j.jmapro.2019.04.020
[28] CHEN H, YE L, HAN Y, et al. Additive manufacturing of W-Fe composites using laser metal deposition: microstructure, phase transformation, and mechanical properties[J]. Materials Science and Engineering: A, 2021, 811: 141036. DOI:10.1016/j.msea.2021.141036
[29] IZADI M, FARZANEH A, MOHAMMED M, et al. A review of laser engineered net shaping (LENS) build and process parameters of metallic parts[J]. Rapid Prototyping Journal, 2020, 26(6): 1059-1078. DOI:10.1108/RPJ-04-2018-0088
[30] CHEN D, WANG P, PAN R, et al. Characteristics of metal specimens formed by selective laser melting: a state-of-the-art review[J]. Journal of Materials Engineering and Performance, 2020(1): 1-28. DOI:10.1007/s11665-020-05323-6
[31] 杨强, 鲁中良, 黄福享, 等. 激光增材制造技术的研究现状及发展趋势[J]. 航空制造技术, 2016(12): 26-31.
YANG Qiang, LU Zhongliang, HUANG Fuxiang, et al. Research on status and development trend of laser additive manufacturing[J]. Aeronautical Manufacturing Technology, 2016(12): 26-31. DOI:10.16080/j.issn1671-833x.2016.12.026
[32] SUN H, CHU X, LUO C, et al. Selective laser melting for joining dissimilar materials: investigations of interfacial characteristics and in situ alloying[J]. Metallurgical and Materials Transactions A, 2021, 52(4): 1540-1550. DOI:10.1007/S11661-021-06178-9
[33] 陈南宇. 金属零件3D打印技术的应用研究[J]. 计算机产品与流通, 2020(10): 67.
CHEN Nanyu. Application of metal parts 3 D printing technology[J]. Computer Products and Circulation, 2020(10): 67. DOI: CNKI:SUN:WXXJ.0.2020-10-061
[34] 邹海平, 李上奎, 李博, 等. 3D打印用金属粉末的制备技术发展现状[J]. 中国金属通报, 2016(8): 88-89.
ZOU Haiping, LI Shangkui, LI Bo. Developmentstatus ofmetal powder preparation technology for 3D printing[J]. China Metal Bulletin, 2016(8): 88-89.
[35] CHEN G, ZHOU Q, ZHAO S Y, et al. A pore morphological study of gas-atomized Ti-6Al-4V powders by scanning electron microscopy and synchrotron X-ray computed tomography[J]. Powder Technology, 2018, 330: 425-430. DOI:10.1016/j.powtec.2018.02.053
[36] YIN J O, CHEN G, ZHAO S Y, et al. Microstructural characterization and properties of Ti-28Ta at.% powders produced by plasma rotating electrode process[J]. Journal of Alloys and Compounds, 2017, 713: 222-228. DOI:10.1016/j.jallcom.2017.04.195
[37] SUN P, FANG Z Z, XIA Y, et al. A novel method for production of spherical Ti-6Al-4V powder for additive manufacturing[J]. Powder Technology, 2016, 301: 331-335. DOI:10.1016/j.powtec.2016.06.022
[38] 欧阳鸿武, 陈欣, 余文焘, 等. 气雾化制粉技术发展历程及展望[J]. 粉末冶金技术, 2007, 25(1): 53-58, 63.
OUYANG Hongwu, CHEN Xin, YU Wentao, et al. Development history and prospect of aerosol pulverizationtechnology[J]. Powder Metallurgy Technology, 2007, 25(1): 53-58, 63. DOI:10.19591/j.cnki.cn11-1974/tf.2007.01.014
[39] 杨全占, 魏彦鹏, 高鹏, 等. 金属增材制造技术及其专用材料研究进展[J]. 材料导报, 2016, 30(S1): 107-111, 124.
YANG Zhanquan, WEI Yanpeng, GAO Peng, et al. Research progress of metal additive manufacturing technologies and related materials[J]. Materials Reports, 2016, 30(S1): 107-111, 124.
[40] 许德, 高华兵, 董涛, 等. 增材制造用金属粉末研究进展[J]. 中国有色金属学报, 2021, 31(2): 245-257.
XU De, GAO Huabing, DONG Tao, et al. Research progress of metal powder for additive manufacturing[J]. The Chinese Journal of Nonferrous Metals, 2021, 31(2): 245-257.
[41] MOMENI A, ABBASI S M. Effect of hot working on flow behavior of Ti-6Al-4V alloy in single phase and two phase regions[J]. Materials & Design, Materials & Design, 2010, 31(8): 3599-3604. DOI:10.1016/j.matdes.2010.01.060
[42] 王会杰, 崔照雯, 孙峰, 等. 激光选区熔化成形技术制备高温合金GH4169复杂构件[J]. 粉末冶金技术, 2016, 34(5): 368-372.
WANG Huijie, CUI Zhaowen, SUN Feng, et al. Superalloy GH4169 complicated components prepared by selective lasemelting forming technique[J]. Powder Metallurgy Technology, 2016, 34(5): 368-372. DOI:10.19591/j.cnki.cn11-1974/tf.2016.05.009
[43] LVDDECKE A, PANNITZ O, ZETZENER H, et al. Powder properties and flowability measurements of tailored nanocomposites for powder bed fusion applications[J]. Materials & Design, 2021(1-2): 109536. DOI:10.1016/J.MATDES.2021.109536
[44] KARUNAKARAN R, ORTGIES S, TAMAYOL A, et al. Additive manufacturing of magnesium alloys[J]. Bioactive Materials, 2020, 1(5): 44-54. DOI:10.1016/j.bioactmat.2019.12.004
[45] GU D D. Laser additive manufacturing of high-performance materials[M]. Springer, 2015: 15-71.
[46] ZHONG M, LIU W. Laser surface cladding: the state of the art and challenges[J]. ARCHIVE Proceedings of the Institution of Mechanical Engineers Part C Journal of Mechanical Engineering Science, 2010, 224(5): 1041-1060. DOI:10.1243/09544062JMES1782
[47] VRANCKEN B, THIJS L, KRUTH J P, et al. Heat treatment of Ti6Al4V produced by selective laser melting: microstructure and mechanical properties[J]. Journal of Alloys and Compounds, 2012, 541: 177-185. DOI:10.1016/j.jallcom.2012.07.022
[48] GU D D. Laser additive manufacturing of high-performance materials[M]. Spriger, 2015: 115-150.
[49] CHATTERJEE A N, KUMAR S, SAHA P, et al. An experimental design approach to selective laser sintering of low carbon steel-science direct[J]. Journal of Materials Processing Technology, 2003, 136(1-3): 151-157. DOI:10.1016/S0924-0136(03)00132-8
[50] DAS S, BEAMA J J, WOHLERT M, et al. Direct laser freeform fabrication of high performance metal components[J]. Rapid Prototyping Journal, 1998, 4(3): 112-117. DOI:10.1108/13552549810222939
[51] GU D D, SHEN YF. Influence of phosphorus element on direct laser sintering of multicomponent Cu-based metal powder[J]. Metallurgical and Materials Transactions B, 2006, 37(6): 967-977. DOI:10.1007/BF02735019
[52] BALLA V K, BODHAK S, BOSE S, et al. Porous tantalum structures for bone implants: fabrication, mechanical and in vitro biological properties[J]. Acta Biomaterialia, 2010, 6(8): 3349-3359. DOI:10.1016/j.actbio.2010.01.046
[53] BANDYOPADHYAY A, ESPANA F, BALLA V K, et al. Influence of porosity on mechanical properties and in vivo response of Ti6Al4V implants[J]. Acta Biomaterialia, 2010, 6(4): 1640-1648. DOI:10.1016/j.actbio.2009.11.011
[54] KRISHNA B V, BOSE S, BANDYOPADHYAYA. Low stiffness porous Ti structures for load-bearing implants[J]. Acta Biomaterialia, 2007, 3(6): 997-1006. DOI:10.1016/j.actbio.2007.03.008
[55] XUE W, KRISHNA B V, BANDYOPADHYAY A, et al. Processing and biocompatibility evaluation of laser processed porous titanium[J]. Acta Biomaterialia, 2007, 3(6): 1007-1018. DOI:10.1016/j.actbio.2007.05.009
[56] KRISHNA B V, XUE W, BOSE S, et al. Engineered porous metals for implants[J]. JOM, 2008, 60(5): 45-48. DOI:10.1007/s11837-008-0059-2
[57] WEI G, ZHANG Y B, DEVARAJAN RJ, et al. The status, challenges, and future of additive manufacturing in engineering[J]. Computer-Aided Design, 2015, 69: 65-89. DOI:10.1016/j.cad.2015.04.001
[58] NGO T D, KASHANI A, IMBALZANOG, et al. Additive manufacturing (3D printing): a review of materials, methods, applications and challenges[J]. Composites Part B: Engineering, 2018, 143: 172-196. DOI:10.1016/j.compositesb.2018.02.012
[59] 王江, 刘凯, 孙华君, 等. 激光增材制造用SiC粉末制备及成形工艺探索[J]. 材料科学与工艺, 2018, 26(2): 9-14.
WANG Jiang, LIU Kai, SUN Huajun, et al. Study on preparation and forming process of SiC powder for laser additimanufacturing[J]. Materials Science and Technology, 2018, 26(2): 9-14. DOI:10.1195/j.issn.1005-0299.20170092
[60] DAI K, VILLEGAS J, STONE Z, et al. Finite element modeling of the surface roughness of 5052 Al alloy subjected to a surface severe plastic deformation process[J]. Acta Materialia, 2004, 52(20): 5771-5782. DOI:10.1016/j.actamat.2004.08.031
[61] WANG L, FELICELLI S D, PRATT P. Residual stresses in LENS-deposited AISI 410 stainless steel plates[J]. Materials Science & Engineering A, 2008, 496(1): 234-241. DOI:10.1016/j.msea.2008.05.044
[62] DAI K, SHAWL. Finite element analysis of the effect of volume shrinkage during laser densification[J]. Acta Materialia, 2005, 53(18): 4743-4754. DOI:10.1016/j.actamat.2005.06.014
[63] QI H, MAZUMDER J, KI H. Numerical simulation of heat transfer and fluid flow in coaxial laser cladding process for direct metal deposition[J]. Journal of Applied Physics, 2006, 100(2): 024903. DOI:10.1063/1.2209807
[64] 董一巍, 赵奇, 李晓琳. 增减材复合加工的关键技术与发展[J]. 金属加工(冷加工), 2016(13): 7-12.
DONG Yiwei, ZHAO Qi, LI Xiaolin. Key technology and development of increase and decrease composite processing[J]. Metal Working(Metal Cutting), 2016(13): 7-12.
[65] 张宇, 吴天明, 唐鸿雁, 等. 多功能高速高效五轴金属增减材复合智能装备研制[J]. 内燃机与配件, 2018(3): 115-117.
ZHANG Yu, WU Tianming, TANG Hongyan, et al. Development of multi-function high-speed five-axis metal composite intelligent equipment[J]. Internal Combustion Engine & Parts, 2018(3): 115-117. DOI:10.19475/j.cnki.issn1674-957x.2018.03.054
[66] KHAIRALLAH S A, ANDERSON A T, RUBENCHIK A, et al. Laser powder-bed fusion additive manufacturing: physics of complex melt flow and formation mechanisms of pores, spatter, and denudation zones[J]. Acta Materialia, 2016, 108: 36-45. DOI:10.1016/j.actamat.2016.02.014
[67] KVRNSTEINER P, WILMS M B, WEISHEIT A, et al. High-strength damascus steel by additive manufacturing[J]. Nature, 2020, 582(7813): 515-519. DOI:10.1038/s41586-020-2409-3
[68] GU D, MA J, CHEN H, et al. Laser additive manufactured WC reinforced Fe-based composites with gradient reinforcement/matrix interface and enhanced performance[J]. Composite Structures, 2018, 192: 387-396. DOI:10.1016/j.compstruct.2018.03.008
[69] CARLOS D B, GU D D, SCHMIDT M, et al. On the selection and design of powder materials for laser additive manufacturing[J]. Materials & Design, 2021, 204: 109653. DOI:10.1016/j.matdes.2021.109653