陈源, 姜梦, 陈曦, 马生翀, 姜楠, 雷正龙, 陈彦宾
(先进焊接与连接国家重点实验室(哈尔滨工业大学),哈尔滨 150001)
摘要:
增材制造作为实现三维结构快速成形的技术,广泛用于航空航天、汽车交通等领域。当前,激光熔丝增材制造多依托于传统的激光焊接设备,采用旁轴送丝方式,在增材过程中,需调整激光头方向保证送丝和焊接头行进的相对方位,增大了复杂构件增材制造系统控制难度,损失了加工自由度。随着激光加工设备和技术的发展,近年来出现了一种可以解决上述问题的光丝同轴激光熔丝增材制造技术。由于此项技术刚刚起步,为了更好的理解光丝同轴激光熔丝增材制造技术的特性,本文从技术分类及原理、加工制造特性、成形精度控制以及增材件的组织性能等方面,论述了光丝同轴激光增材制造取得的研究进展,对比分析了光丝同轴技术与旁轴激光熔丝技术的差异性,阐述了用于光丝同轴技术的两种成形精度方法及特点,分析了光丝同轴增材件的组织与性能;最后,指出了光丝同轴技术未来的发展趋势。
关键词: 增材制造 激光熔丝 光丝同轴 工艺特性 成形质量
DOI:10.11951/j.issn.1005-0299.20210207
分类号:TG456.7
文献标识码:A
基金项目:国家科技重大专项(2019-VII-0004-0144).
Research progress of coaxial laser wire additive manufacturing
CHEN Yuan, JIANG Meng, CHEN Xi, MA Shengchong, JIANG Nan, LEI Zhenglong, CHEN Yanbin
(State Key Laboratory of Advanced Welding and Joining (Harbin Institute of Technology), Harbin 150001, China)
Abstract:
Additive manufacturing is widely applied in aerospace and automobile industries due to its ability to realize rapid prototyping of three-dimensional structures. The current wire-based laser additive manufacturing mostly relies on the traditional laser welding equipment with a lateral wire feeding method. However, in additive manufacturing with lateral wire feeding, it is necessary to adjust the direction of laser processing head to ensurea fixed relative position between wire and processing head, resulting in a significant increase in complexity of system control and obvious loss of processing freedom. With the development of laser processing equipment and technology, a novel process of coaxial laser wire additive manufacturing has emerged with the potential to solve the aforementioned problem. Since the process is just getting started, in order to better understand the characteristics of coaxial laser wire additive manufacturing, the research progress of coaxial laser wire additive manufacturing was summarized from the perspectives of implementation principle, processing characteristics, precision control, and microstructure and properties of additive manufactured components. The differences between laser wire additive manufacturing with coaxial wire and lateral wire feeding were analyzed. Two precision control methods for coaxial laser wire additive manufacturing and their characteristics were demonstrated. The microstructure and properties of components made by coaxial laser wire additive manufacturing were analyzed. In the end, the further research trend for coaxial laser wire additive manufacturing was put forward.
Key words: additive manufacturing wire-based laser metal deposition coaxial laser and wire process characteristics forming quality
陈源, 姜梦, 陈曦, 马生翀, 姜楠, 雷正龙, 陈彦宾. 光丝同轴激光增材制造研究进展[J]. 材料科学与工艺, 2022, 30(2): 16-27. DOI: 10.11951/j.issn.1005-0299.20210207.

CHEN Yuan, JIANG Meng, CHEN Xi, MA Shengchong, JIANG Nan, LEI Zhenglong, CHEN Yanbin. Research progress of coaxial laser wire additive manufacturing[J]. Materials Science and Technology, 2022, 30(2): 16-27. DOI: 10.11951/j.issn.1005-0299.20210207.

基金项目 国家科技重大专项(2019-Ⅶ-0004-0144) 通信作者 姜梦,E-mail:mengjiang@hit.edu.cn
陈曦,E-mail:chenxi_hit2016@hit.edu.cn
雷正龙,E-mail:leizhenglong@hit.edu.cn
陈彦宾,E-mail:chenyanbin@hit.edu.cn 作者简介 陈源(1992—),男,博士研究生;
雷正龙(1977—),男,教授,博士生导师;
陈彦宾(1962—),男,教授,博士生导师 文章历史 收稿日期: 2021-09-06 网络出版日期: 2021-11-27
Contents Abstract Full text Figures/Tables PDF
光丝同轴激光增材制造研究进展
陈源, 姜梦








先进焊接与连接国家重点实验室(哈尔滨工业大学),哈尔滨 150001
收稿日期: 2021-09-06
基金项目: 国家科技重大专项(2019-Ⅶ-0004-0144)
作者简介: 陈源(1992—),男,博士研究生;
雷正龙(1977—),男,教授,博士生导师;
陈彦宾(1962—),男,教授,博士生导师.
通信作者: 姜梦,E-mail:mengjiang@hit.edu.cn;
陈曦,E-mail:chenxi_hit2016@hit.edu.cn;
雷正龙,E-mail:leizhenglong@hit.edu.cn;
陈彦宾,E-mail:chenyanbin@hit.edu.cn.
摘要: 增材制造作为实现三维结构快速成形的技术,广泛用于航空航天、汽车交通等领域。当前,激光熔丝增材制造多依托于传统的激光焊接设备,采用旁轴送丝方式, 在增材过程中,需调整激光头方向保证送丝和焊接头行进的相对方位,增大了复杂构件增材制造系统控制难度,损失了加工自由度。随着激光加工设备和技术的发展,近年来出现了一种可以解决上述问题的光丝同轴激光熔丝增材制造技术。由于此项技术刚刚起步,为了更好的理解光丝同轴激光熔丝增材制造技术的特性,本文从技术分类及原理、加工制造特性、成形精度控制以及增材件的组织性能等方面,论述了光丝同轴激光增材制造取得的研究进展,对比分析了光丝同轴技术与旁轴激光熔丝技术的差异性,阐述了用于光丝同轴技术的两种成形精度方法及特点,分析了光丝同轴增材件的组织与性能;最后,指出了光丝同轴技术未来的发展趋势。
关键词: 增材制造 激光熔丝 光丝同轴 工艺特性 成形质量
Research progress of coaxial laser wire additive manufacturing
CHEN Yuan, JIANG Meng








State Key Laboratory of Advanced Welding and Joining (Harbin Institute of Technology), Harbin 150001, China
Abstract: Additive manufacturing is widely applied in aerospace and automobile industries due to its ability to realize rapid prototyping of three-dimensional structures. The current wire-based laser additive manufacturing mostly relies on the traditional laser welding equipment with a lateral wire feeding method. However, in additive manufacturing with lateral wire feeding, it is necessary to adjust the direction of laser processing head to ensurea fixed relative position between wire and processing head, resulting in a significant increase in complexity of system control and obvious loss of processing freedom. With the development of laser processing equipment and technology, a novel process of coaxial laser wire additive manufacturing has emerged with the potential to solve the aforementioned problem. Since the process is just getting started, in order to better understand the characteristics of coaxial laser wire additive manufacturing, the research progress of coaxial laser wire additive manufacturing was summarized from the perspectives of implementation principle, processing characteristics, precision control, and microstructure and properties of additive manufactured components. The differences between laser wire additive manufacturing with coaxial wire and lateral wire feeding were analyzed. Two precision control methods for coaxial laser wire additive manufacturing and their characteristics were demonstrated. The microstructure and properties of components made by coaxial laser wire additive manufacturing were analyzed. In the end, the further research trend for coaxial laser wire additive manufacturing was put forward.
Keywords: additive manufacturing wire-based laser metal deposition coaxial laser and wire process characteristics forming quality
增材制造是一种基于三维模型对材料进行逐层堆积的快速成形技术。近年来,增材制造一直是全球性的研究热点[1]。2011年美国在“先进制造伙伴”计划中率先提出增材制造,随后,德国和中国在相应的国家战略计划中也均将增材制造列为推进制造业发展的重要技术(德国工业4.0战略计划和中国制造2025)。增材制造凭借其加工灵活度高、生产周期短、易于数字化控制等优点,广泛用于航空航天、汽车交通、航空发动机等[2-3]。
根据填充材料的不同,增材制造可以分为熔粉增材和熔丝增材,如表 1所示。相比于熔粉增材制造,熔丝增材制造具有高沉积速率、低加工成本和低气孔缺陷倾向的优势,适用于大尺寸件的增材[4-5],但由于熔丝增材成形精度差,难以精确控制,使其商业化受到限制。熔丝增材制造按照热源可以分为:电弧熔丝、激光熔丝和电子束熔丝。电弧熔丝具备较大熔覆效率和较低成本,但成形精度较低,需要进行大工作量的机械加工处理。电子束熔丝具备较高熔覆效率和成形质量,但成本较高。激光熔丝具备兼顾成本、熔覆效率和成形质量的前景。
表1(Table 1)
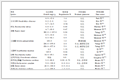
电弧熔丝增材 丝材 1 000~3 000 5~15 0.2~2.8 简单 短 110~1 100 低 需要机械加工 需要机械加工
电子束熔丝增材 丝材 500~2 000 1~10 0.1~2.0 适中 中 110~1 100 高 1.0~1.5 8~15
激光粉末床增材 粉末 50~1 000 10~1 000 - 复杂 长 360~2 500 高 0.04~0.2 7~20
激光送粉增材 粉末 100~3 000 5~20 0.1~1.0 复杂 长 360~2 500 中 0.5~1.0 4~10
激光熔丝增材 丝材 500~3 000 5~25 0.1~2.0 适中 中 110~1 100 中 1.0~1.5 10~25
表 1 不同增材制造的种类及特点[2, 6, 12-14]Table 1 Types and characteristics of different additive manufacturing [2, 6, 12-14]
目前,激光熔丝增材制造多采用旁轴送丝增材,其加工平台易于搭建,但由于送丝具有方向性,丝材受热不均匀,难于满足熔覆层尺寸和性能在各方向的一致性,且旁轴送丝增材的光、丝耦合性差,对光丝相对位置要求颇为严格。当成形路径复杂多变时,将增大旁轴送丝增材的成形控制系统的复杂性[6-7]。为解决旁轴送丝加工自由度受限制的问题,电弧熔丝采用同轴送丝进给方式,实现复杂构件成形[8-9],电子束熔丝利用同轴送丝进给方式,获得性能更优良、组织形态更均一的增材件[10-11],同轴送丝是解决上述问题的最佳方案。相比电弧和电子束热源,激光热源具有其特殊性,可以借助光束整形技术,较为容易地实现光丝同轴的熔丝增材制造方式。近几年,随着商用光丝同轴激光头的出现,越来越多的学者开始研究光丝同轴激光增材制造,如表 2所示。
表2(Table 2)
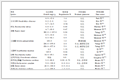
Henri等[15] 坦佩雷理工大学(芬兰) 2012 Fraunhofer同轴头 低碳钢 IN625(1.0 mm) 工艺分析
Nowotny等[16] 弗劳恩霍夫IWS(德国) 2013 Fraunhofer同轴头 IN718 IN718(0.6 mm) 加工成形
Wu等[17] 苏州大学(中国) 2013 苏大自研同轴头 45#钢 304钢(0.6 mm) 成形控制
Gu等[18] 苏州大学(中国) 2014 苏大自研同轴头 X X 工艺分析
Kuznetsov等[19] 卢布尔雅那大学(斯洛文尼亚) 2014 X X 镍丝(0.25, 0.6 mm) 熔滴过渡
Ding等[20] 重庆绿色智能技术研究所(中国) 2016 自研设备 TC4 5356Al(0.4 mm), TC4(0.4 mm) 热过程分析
Pajukoski等[21] 坦佩雷理工大学(芬兰) 2016 Fraunhofer同轴头 低碳钢 IN625(1.0 mm), 双相钢(1.2 mm) 热丝增材
Motta等[22] 米兰理工大学(意大利) 2018 Precitec同轴头 316不锈钢 308不锈钢(1 mm) 熔丝行为及工艺分析
Shakhverdova等[23] 弗劳恩霍夫IWS(德国) 2018 Fraunhofer同轴头 无 无 设备研究
Shi等[24] 苏州大学(中国) 2018 苏大自研同轴头 304不锈钢 304不锈钢(0.5 mm) 成形分析
Du等[25] 重庆大学(中国) 2019 自研设备 TC4 TC4(0.4 mm) 工艺分析
Garmendia等[26] 工业研究中心(西班牙) 2019 Fraunhofer同轴头 316不锈钢 316不锈钢(0.8 mm) 成形控制
Kelbassa等[27] 弗劳恩霍夫ILT(德国) 2019 ILT自研同轴头 IN718, TC4 IN718(0.8 mm), TC4(0.8 mm) 工艺分析
Churruca等[28] 工业研究中心(西班牙) 2020 Fraunhofer同轴头 TC4 TC4 同轴送丝送粉对比分析
Silzea等[29] 劳西茨应用技术大学(德国) 2020 X TC4 TC4(1 mm) 组织分析
Becker等[30] 斯图加特大学(德国) 2021 Precitec同轴头 6082Al 5356Al(1 mm) 成形控制
Cazaubon等[31] 波尔多大学(法国) 2021 Precitec同轴头 TC4 TC4(1.2 mm) 工艺分析
Ji等[32] 苏州大学(中国) 2021 苏大自研同轴头 304不锈钢 304不锈钢(0.8 mm) 工艺分析
表 2 光丝同轴激光增材制造的研究概况Table 2 Research progress of coaxial laser wire additive manufacturing
1 光丝同轴的实现方式及原理光丝同轴技术,是利用不同的分光技术,通过改变激光束与金属丝的耦合方式,使得丝材居中并垂直于加工表面,保证激光光束与金属丝中心线同轴的光丝耦合技术。目前国内外的报道中,光丝同轴增材制造的实现方式主要包括以下3种类型:1)分三光束光内同轴技术;2)多光束集成光内同轴技术;3)分环形光束光内同轴技术。
1.1 分三光束光内同轴技术分三光束光内同轴送丝技术原理如图 1(a)所示。单激光束通过三棱镜将被分成周向均匀分布的三激光束,形成三光束中空区域,金属丝通过导丝管进入该区域,实现金属丝与三光束同轴分布,聚焦镜将三光束聚焦到工件表面。如图 1(d)所示,在基板上形成周向均匀分布的三光束,且三光束能量分布均匀。其中,苏州大学[24, 33-34]和德国Fraunhofer IWS[16, 21, 23, 26]均采用此光丝同轴技术,如图 1(g)。分三光束光内同轴的光路简单,易于实现,但光丝同轴头体积较大,光路不易调整,且光丝同轴头的丝管送丝有一定的弯曲弧度,在一定程度下影响了送出丝材与激光束的同轴度,无法保证丝材完全垂直于基板送进。
图 Figure1(Fig.Figure1)
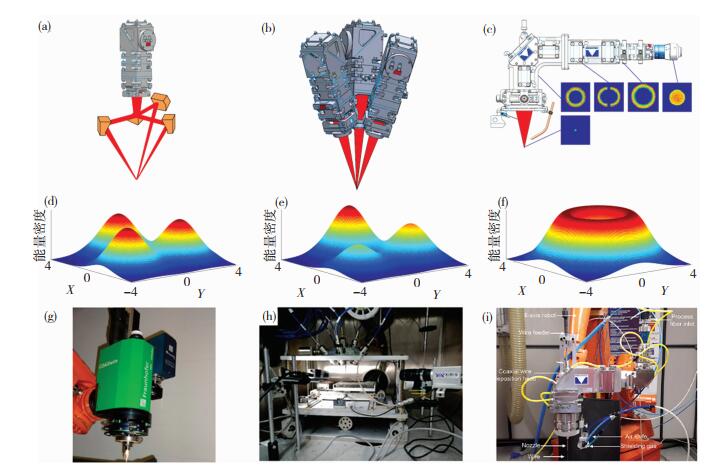
1.2 多光束集成光内同轴技术多光束集成光内同轴送丝技术原理如图 1(b)所示。激光头固定在工作平台上方且采用环列式排布,保证各路激光与竖直方向夹角相等,多路激光组成的环列式激光热源聚焦到工件表面,如图 1(e)所示,在工件表面形成周向均匀分布的多光束,且各光束能量均匀分布。多光束集成光内同轴可通过调节各路激光与竖直方向夹角和激光功率而改变环列式激光热源的能量分布,但该方法对激光头的装配要求颇为严格。运用此光丝同轴技术的有重庆大学[25, 35-36],如图 1(h)所示。
1.3 分环形光束光内同轴技术分环形光束光内同轴技术原理如图 1(c)所示。单激光束通过锥透镜形成环形光束,随后,环形光束通过棱镜将其分成两个半环形光束,分开的两个半环形光束有利于金属丝通过导丝管沿轴向进入工作区域,而后,两个半环形光束通过另一个棱镜重新连接成环形光束,并经过聚焦透镜最终在工件表面形成尺寸为2~4 mm的环形光斑。如图 1(f)所示,在工件表面形成环形激光热源,能量集中于距圆心2~4 mm的环状带处,热源能量随着距环状带距离的增加而降低。华中科技大学[37]和德国Precitec公司[22]均采用此方法制造光丝同轴激光头,见图 1(i)。分环形光束光内同轴能够实现丝材均匀受热和丝材垂直于加工表面送进,实现真正意义上的360度方向加工,但其光路复杂、灵活性较差、光丝耦合严格,且该结构设计容易造成镜片损坏。
2 光丝同轴激光增材制造工艺特性光丝同轴激光增材制造由于特殊的光丝耦合方式,其熔丝行为和增材制造工艺特性都具有特殊性。
2.1 光丝同轴增材技术熔丝行为旁轴激光熔丝增材受制于光丝相互作用关系[38],为了使激光能量在金属丝表面分布更均匀,通常采用较小的送丝角度(如金属丝与基板表面夹角为30°[39])进行激光熔丝增材,而小角度旁轴送丝增材使得其存在方向性和局限性。光丝同轴增材技术在确保金属丝均匀受热的前提下,实现金属丝垂直于基板的送丝机制。
光丝同轴增材熔丝行为主要采用液桥过渡,通过稳定的液桥过渡,能够获得尺寸良好的熔道。如图 2(a)所示,金属丝沿轴向竖直向下进给,在激光热源和激光头运动的共同作用下,金属丝在激光单道多层增材制造的不同层(第1层,第8层,第16层,第24层)均能实现稳定的液桥过渡,从而获得尺寸稳定的增材件。当激光能量过高且送丝速度小时,易形成滴状缺陷,如图 2(b)所示,在t0时刻,熔化过程从工件表面上方的金属丝开始,形成金属液滴,由于激光束光斑尺寸大于金属丝,剩余激光束达到工件表面形成熔池;当金属丝不断进给时(t=256和864 ms),金属丝末端的熔滴不断长大,熔滴最大直径超过3.3 mm,更多的激光束照射在金属熔滴上,使工件表面熔化量减少。
图 Figure2(Fig.Figure2)
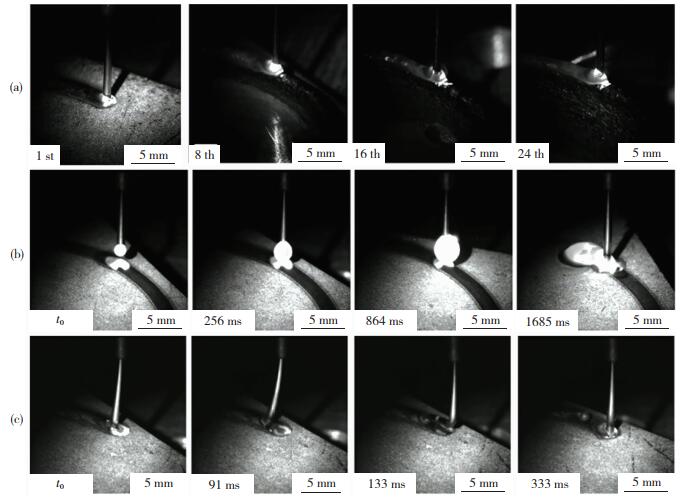
经过约1.6 s,金属熔滴才滴落至工件表面,形成一滩尺寸不均的液态金属。当激光能量较低时,其不足以充分熔化金属丝,且工件表面的熔池尺寸受到限制,如图 2(c)所示,在t0时刻,未熔化的金属丝与工件表面接触,随着金属丝不断进给(t=91 ms),金属丝受挤压弯曲,偏离熔化区域,导致金属沉积存在不连续。
光丝同轴增材多采用液桥过渡形成尺寸稳定的沉积层,而在特殊要求下,光丝同轴增材也存在滴状过渡形式。斯洛文尼亚Kuznetsov等[19]利用脉冲激光实现光丝同轴激光的滴状加工,适用于需要确定尺寸和准确位置的沉积液滴领域。
2.2 工艺参数对成形质量的影响合适的工艺参数设定能够有效避免增材过程中缺陷的产生,同时,也直接影响着增材件的尺寸形貌、组织及性能。因此,掌握光丝同轴增材技术的工艺特性是对这种新型加工方式开展研究的基础。光丝同轴增材技术主要工艺参数有离焦量、激光功率、扫描速度、送丝速度、层间抬高量以及层间冷却时间,本文将对不同的工艺特性做具体阐述。
2.2.1 离焦量区别于旁轴送丝激光增材技术,光丝同轴激光增材技术对离焦量的变化更为灵敏,即离焦量的工艺窗口窄,这与光丝同轴激光的工作原理相关。苏州大学傅戈雁等[32]研究了离焦量对分三光束光内同轴技术的影响,发现仅当离焦量在-1.5~-2.5 mm的范围内时才能形成光滑连续的熔覆道。同样,意大利Demir等[22]也发现分环形光内同轴技术的离焦量工艺窗口窄。如图 3所示,仅在离焦量(f)为-6 mm附近才能够获得稳定光滑的熔覆道;当离焦量为-7 mm时,环形激光光斑孔径过大,不足以充分熔化丝材,形成锯齿状熔道;而当离焦量为-5 mm时,环形激光光斑孔径过小,激光能量集中于丝材上,导致丝材迅速熔化成熔滴并不断长大,最终形成不连续的滴状熔道。
图 Figure3(Fig.Figure3)
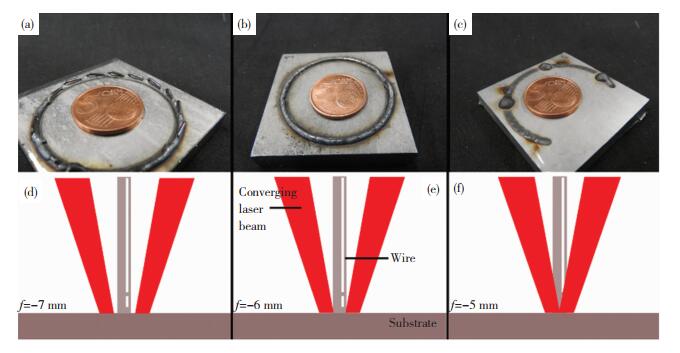
2.2.2 激光功率、扫描速度、送丝速度激光功率、扫描速度和送丝速度是影响增材制造沉积层尺寸和形状的主要工艺参数。由图 4可知,激光功率、扫描速度、送丝速度的变化将会影响熔道的熔宽、熔高和熔道的横截面积。为更好地分析熔丝工艺参数对熔覆道尺寸的影响,引入宽高比(熔宽与熔高的比值)和稀释率(基板熔化区域与整个熔化区域的比值)这两个评价熔覆道质量的重要指标[40]。激光功率决定着光源能量输入大小,其主要影响熔道的稀释率,随着激光功率的增大,激光光斑的能量密度增大,熔道的熔宽和熔深增大,进而使熔道的稀释率增大;扫描速度对熔道的熔宽比影响较大,随着扫描速度的增加,熔道的宽度减小,熔高下降,但熔高下降更明显,即宽高比增大[41];相对于其他参数,送丝速度对熔高影响更显著,送丝速度的增加提高了金属丝的供给量,从而使得熔高增加[36]。
图 Figure4(Fig.Figure4)
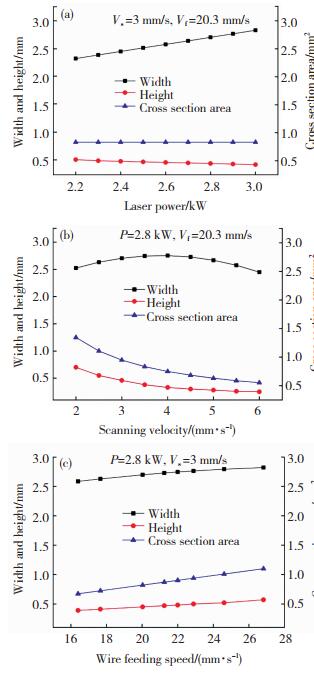
2.2.3 层间抬高量及冷却时间层间抬高量和层间冷却时间是影响多层多道沉积质量的两个重要参数。重庆大学Du等[25]采用0.4 mm钛合金金属丝研究了不同抬高量对光丝同轴增材件的影响。如图 5所示,当层间抬高量为0.24或0.26 mm时,薄壁件上部不平整,且薄壁件侧壁存在毛刺和未熔化的金属丝;当抬高量为0.28 mm时,可获得表面连续光滑的薄壁件;当抬高量为0.30 mm时,过大的抬高量可能导致沉积层间存在间隙,随着增材层数的增加易在薄壁增材件中形成缺陷。
图 Figure5(Fig.Figure5)
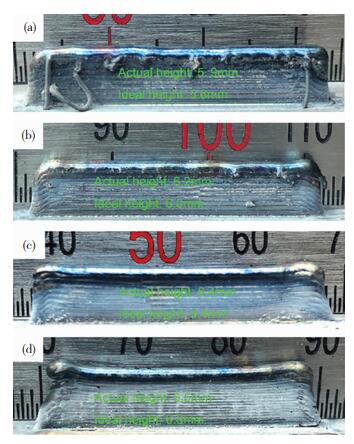
随着增材层数的增加,工件常存在热积累的问题,调整层间冷却时间是减缓热积累的重要方法。德国Silze等[29]研究了不同层间冷却时间(1,5,10,20 s)对钛合金增材组织的影响,研究发现随着层间冷却时间的增加,柱状β晶由860 μm(宽)×7370 μm(长)减小至450 μm×5390 μm,且板条α厚度由1.8 μm减小至1.5 μm。
2.3 光丝同轴增材制造的成形精度控制方法对于薄壁件或块体的光丝同轴增材制造,准确控制加工件的成形精度和尺寸,既有利于提高工件的成形质量和性能,又最大程度地减少了后续加工的工作量。前文已说明工艺参数,如离焦量、激光功率、扫描速度等对成形的影响,而工件的成形精度控制往往需要多因素的耦合调控。本部分将阐述目前国内外在成形精度的控制方法方面的研究。
2.3.1 同步监测优化技术通过对逐层制造过程的实时监控,能够及时发现过程中的问题并做相应调整,有利于高质量成形件生成。基于此,同步监测优化技术采用三维结构光扫描仪获取实时加工尺寸,对比实际尺寸与理论尺寸的差异而调整工艺参数,以期最终获得目标尺寸工件[30, 42-43]。西班牙Garmendia等[26]利用同步监测优化技术实现在高低不平面上的稳定尺寸增材。如图 6(a)所示,在开始增材之前,工件表面存在着左侧高右侧低的台阶缺陷,通过同步监测获得工件的高度尺寸,如图 6(c)所示,在工件左侧使用较快的扫描速度,在工件右侧采用较慢的扫描速度,因此,工件左侧高度增长变缓,而工件右侧高度增材迅速,见图 6(d),两侧的高度差逐渐减小,当增材到第12层时,台阶缺陷已完全消失,形成尺寸均匀的块体工件,如图 6(b)所示。
图 Figure6(Fig.Figure6)
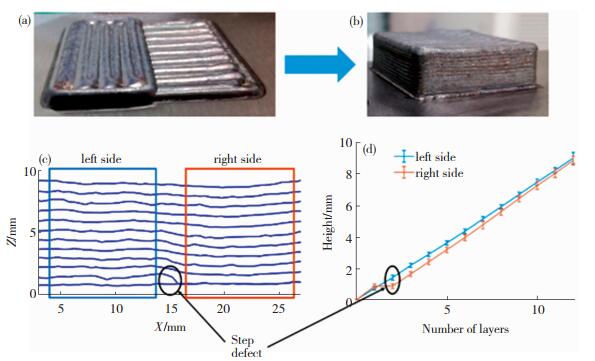
2.3.2 数学模型计算法同步监测优化技术虽然能够精确地控制增材件尺寸精度,但其需要复杂的监测设备和反馈条件系统,价格高昂且操作较复杂。在激光熔覆过程中,许多因素影响熔覆道的尺寸特征,其中送丝速度、扫描速度、激光功率、丝材半径是影响熔覆层形貌尺寸的主要工艺参数。数学模型计算法是依据与熔覆层相关的理论基础,建立数学模型,从而获得主要工艺参数与熔覆层的定量关系。采用数学模型计算法能够在较低成本和较小实验量的情况下快速获得增材件尺寸,适用于高效低精度获取工件尺寸的领域。
如图 7所示,Q1为熔化金属丝所需要吸收的能量,包括金属丝温度升高的能量和熔化潜热,其中,m为金属丝质量,C为比热容,ΔT为金属丝由室温到熔点的温度差,ΔHm为熔化潜热;Q2为激光作用于金属丝上的能量,其中,γw为反射系数,P为激光功率;根据能量守恒,即可获得熔覆层质量m的关系式;同时,熔覆层质量与金属丝熔化量相等,即获得另一熔覆层质量m的关系式,其中,rw为金属丝半径,vf为送丝速度,t为加热时间;根据质量守恒即可获得熔覆层横截面积S与送丝速度vf和扫描速度vs的关系式。并且,结合熔覆层的几何关系,即能获得熔覆层横截面积S和熔高H与熔宽W和圆弧半径R的关系式。通过该数学模型能够巧妙的将增材工艺参数(送丝速度、扫描速度、激光功率、金属丝半径)与熔覆层形貌尺寸参数(熔高、熔宽、熔覆层横截面积)建立定量的关系,为获得目标尺寸的增材制造提供了理论基础。
图 Figure7(Fig.Figure7)
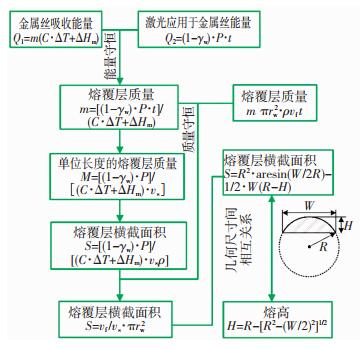
2.4 光丝同轴增材制造典型构件如图 8所示,光丝同轴增材制造因其良好的光丝耦合性、加工适应性、高加工自由度等优势,可成功实现多种典型构件加工,例如圆筒形薄壁件和方形薄壁件,也可制造不同变曲率构件,例如涡轮叶片、进气管、倾斜圆筒形薄壁件以及扭曲薄壁件。光丝同轴设备靠近加工表面处往往只有垂直于加工表面送进的细小导丝管,使得光丝同轴加工能在狭小空间的环境中正常运行。
图 Figure8(Fig.Figure8)
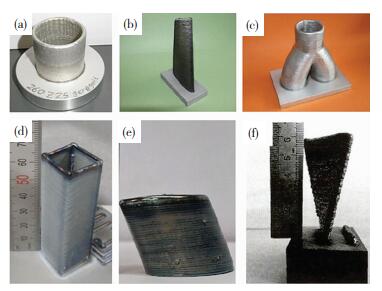
2.5 激光熔丝增材制造组织性能研究激光熔丝增材制造的成形件微观组织种类、形态和尺寸对其性能具有重要影响,本部分将阐述目前学者们利用光丝同轴技术获得的增材件的组织与性能方面的结果。
2.5.1 显微组织分析利用光丝同轴增材技术制备的308不锈钢在靠近基材处为细小的组织,而在增材件中部区域呈现柱状晶,且柱状晶方向与增材生长方向相同[22],在增材件的顶部,由于直接暴露在空气中形成的快速冷却,增材组织较为细小[18]。
光丝同轴激光增材的钛合金组织多以β柱状晶组成,其晶内为网篮状组织。粗大柱状晶的形成与增材过程中热积累有关,在下一层增材过程中,会部分熔化上一层熔覆道,对应位置的柱状晶吸热继续向上长大。重庆大学杜发瑞[48]的研究发现:TC4单道多层薄壁件不同区域的组织存在差异,薄壁件下层是由中央的粗大β晶粒和两侧针状α′组成的集束魏氏组织;薄壁件中部为细小的网篮组织;薄壁件上层区域是相互垂直的针状α′形成的块状组织αm和两侧的集束状针状α′。如图 9所示,西班牙Madarieta等[28]的研究发现,TC4多道多层块体以网篮组织和α集束为主,因为网篮组织中交织的α板条有最小的有效滑动长度,理想的增材件组织为更多的网篮组织和更少的α集束。由于增材钛合金过程中的热作用,在薄壁件的中下部常存在层带组织,平行的层带内是粗大的魏氏组织[49]。
图 Figure9(Fig.Figure9)
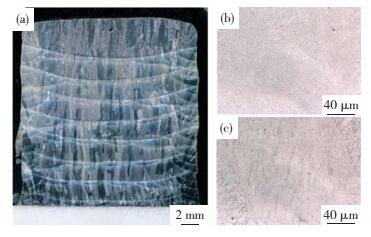
当激光能量不足以完全熔化上一层顶部的等轴晶时(激光功率偏低且送丝速度过大时),增材件柱状晶难以实现外延生长,后一层组织以上一层顶部的等轴晶为形核质点长大,最终形成粗大的等轴晶[47]。
区别于旁轴送丝激光增材制造,光丝同轴激光增材技术拥有更小的温度梯度G(Temperature Gradient)和更大的冷却速度R(Solidification Rate),结合凝固组织与G/R关系,增材件更易形成等轴组织。与光丝同轴激光增材技术类似的电子束丝材同轴增材技术已证实同轴技术有助于等轴组织形成[11],但其具体的机理还有待研究。本研究团队正致力于探索光丝同轴激光增材制造对G/R的影响变化,以期揭示该技术对组织的影响规律。
2.5.2 性能分析粉末增材制造易产生气孔缺陷,当气孔率大于0.7%时,增材件的韧性受到明显的损害[50-51]。光丝同轴增材制造在合适的制造工艺下,能够有效避免气孔缺陷的产生。
光丝同轴技术增材不同材料存在成形精度差异。德国Kelbassa等[27]研究了不同材料光丝同轴增材块体的表面粗糙度,研究发现,IN718合金块体沿熔道方向和垂直于熔道方向的粗糙度分别约为1.5 μm和7.5~20.7 μm,而TC4钛合金沿熔道和垂直熔道方向粗糙度分别为1.7~9.3 μm和29.6~36.3 μm。意大利Motta等[22]利用光丝同轴技术增材308不锈钢,如图 10所示,获得致密度高于99.9%的高质量增材件,在稳定沉积情况下,其表面质量(Ra=10.0~12.8 μm)能达到熔粉增材件表面质量(Ra=10~90 μm)的水平[52-53]。
图 Figure10(Fig.Figure10)
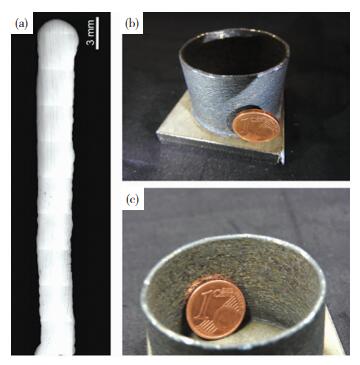
光丝同轴的薄壁增材件显微硬度随着层高的增加,呈现先减小后升高的趋势,TC4钛合金薄壁件的显微硬度在340~385HV[27, 48]。而旁轴熔丝TC4合金增材件显微硬度随着层高的增加而增加,显微硬度在332~392HV[13]。
光丝同轴的钛合金增材件屈服强度为949~999 MPa,抗拉强度为1 007~1 060 MPa,延伸率为7.5%~9.7%[29],如图 11所示,使用光丝同轴技术的增材制造的增材件抗拉强度略高于旁轴激光熔丝增材件。熔丝增材件在不同方向均存在着性能差异,通常,垂直于增材方向的延伸率高平行于增材方向的25%~33%,而抗拉强度近似相等[54-55]。
图 Figure11(Fig.Figure11)
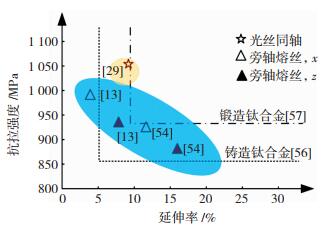
3 展望近年来,随着激光加工装备和技术的发展,出现了一种突破传统熔丝增材局限的光丝同轴激光熔丝增材技术,并逐渐受到国内外学者的关注。本文总结了国内外实现光丝同轴技术的3种技术原理,系统归纳了光丝同轴技术的加工特性,并论述了光丝同轴增材件的显微组织及性能。一项材料加工技术的发展涉及到热物理机制、工艺特性和加工装备等多方面,光丝同轴激光熔丝技术目前尚有很多技术问题有待进一步解决,具体包括以下几个方面。
1) 进一步研究光丝同轴条件下的焊丝与激光相互作用机理及其焊接熔池的熔化、流动和凝固行为,阐明气孔、未熔合等缺陷的形成机理。
2) 对于工件的晶粒粗大、性能各向异性、残余应力大等问题,应进一步开展工艺参数对光丝同轴增材质量和性能的系统研究,并建立工艺- 热过程- 组织- 性能的相关性,实现组织性能调控。
3) 加强光丝同轴增材过程监测研究,实现对焊丝熔化过程和熔池行为进行多方位、多信号监控,并反馈控制工艺,提高加工制造精度。
4) 设计并制造用于激光熔丝增材制造的专用焊丝,将光丝同轴熔丝增材与直径更小、挺直度更好和成分更多样的焊丝结合,充分发挥光丝同轴熔丝精度高特点,并从冶金角度调节增材制造的组织性能。
5) 研制新型的光丝同轴增材制造加工头,提升加工头的功能性、灵活性和稳定性,使其能在更小、复杂的工况条件下长时间、安全、稳定运行,并进一步降低其制造成本。
6) 推动光丝同轴增材制造技术在典型产品的应用,全面分析其制造成本、制造质量,组织性能基础数据和服役效果。
参考文献
[1] MOSALLANEJAD M H, NIROUMAND B, AVERSA A, et al. In-situ alloying in laser-based additive manufacturing processes: a critical review[J]. Journal of Alloys and Compounds, 2021, 872: 159567. DOI:10.1016/j.jallcom.2021.159567
[2] DEBROY T, WEI H L, ZUBACK J S, et al. Additive manufacturing of metallic components-process, structure and properties[J]. Progress in Materials Science, 2018, 92: 112-224. DOI:10.1016/j.pmatsci.2017.10.001
[3] YUSUF S M, CUTLER S, GAO N. Review: The impact of metal additive manufacturing on the aerospace industry[J]. Metals, 2019, 9: 1286. DOI:10.3390/met9121286
[4] ZHOU Y H, LI W P, WANG D W, et al. Selective laser melting enabled additive manufacturing of Ti-22Al-25Nb intermetallic: excellent combination of strength and ductility, and unique microstructural features associated[J]. Acta Materialia, 2019, 173: 117-129. DOI:10.1016/j.actamat.2019.05.008
[5] ZHU Y Y, TANG H B, LI Z, et al. Solidification behavior and grain morphology of laser additive manufacturing titanium alloys[J]. Journal of Alloys and Compounds, 2019, 777: 712-716. DOI:10.1016/j.jallcom.2018.11.055
[6] DING D, PAN Z, CUIURI D, et al. Wire-feed additive manufacturing of metal components: technologies, developments and future interests[J]. The International Journal of Advanced Manufacturing Technology, 2015, 81: 465-481. DOI:10.1007/s00170-015-7077-3
[7] CHAURASIA M, SINHA M K. Investigations on process parameters of wire arc additive manufacturing (WAAM): a review[J]. Advances in Manufacturing and Industrial Engineering, 2021, 74: 845-853. DOI:10.1007/978-981-15-8542-5_74
[8] ELMER J W, GIBBS G, CARPENTER J S, et al. Wire-based additive manufacturing of stainless steel components[J]. Welding Journal, 2020, 99: 8-24. DOI:10.29391/2020.99.002
[9] WANG Yangfan, CHEN Xizhang, SU Chuanchu. Microstructure and mechanical properties of Inconel 625 fabricated by wire-arc additive manufacturing[J]. Surface and Coatings Technology, 2019, 374: 116-123. DOI:10.1016/j.surfcoat.2019.05.079
[10] KOVALCHUK D, IVASISHIN O, SAVVAKIN D. Microstructure and properties of 3D Ti-6Al-4V articles produced with advanced co-axial electron beam & wire additive manufacturing technology [C]// The 14th World Conference on Titanium. MATEC Web of Conferences, 2020, 321: 03014. DOI: 10.1051/matecconf/202032103014
[11] ZHANG J, YANG Y, CAO S, et al. Fine equiaxed β grains and superior tensile property in Ti-6Al-4V alloy deposited by coaxial electron beam wire feeding additive manufacturing[J]. Acta Metallurgica Sinica, 2020, 33: 1311-1320. DOI:10.1007/s40195-020-01073-5
[12] KEIST J S, PALMER T A. Role of geometry on properties of additively manufactured Ti-6Al-4V structures fabricated using laser based directed energy deposition[J]. Materials & Design, 2016, 106: 482-494. DOI:10.1016/j.matdes.2016.05.045
[13] BAUFELD B, BRANDL E, BIEST O V D. Wire based additive layer manufacturing: comparison of microstructure and mechanical properties of Ti-6Al-4V components fabricated by laser-beam deposition and shaped metal deposition[J]. Journal of Materials Processing Technology, 2011, 211: 1146-1158. DOI:10.1016/j.jmatprotec.2011.01.018
[14] KHAIRALLAH S A, ANDERSON A T, RUBENCHIK A, et al. Laser powder-bed fusion additive manufacturing: Physics of complex melt flow and formation mechanisms of pores, spatter, and denudation zones[J]. Acta Materialia, 2016, 108: 36-45. DOI:10.1016/j.actamat.2016.02.014
[15] HENRI P, JONNE N, SEBASTIAN T, et al. Laser cladding with coaxial wire feeding [C]//Proc of the 31st International Congress on Applications of Lasers and Electro-Optics. Anaheim, CA: 2012, 1196-1201. DOI: 10.2351/1.5062408
[16] NOWOTNY S, THIEME S, ALBERT D, et al. Generative manufacturing and repair of metal parts through direct laser deposition using wire material [C]// IFIP International Federation for Information Processing, 2013, 411: 185-189. DOI: 10.1007/978-3-642-41329-2_20
[17] WU M J, SHI S H, FU G Y, et al. Process parameters control of deposition of hollow cylindrical part with internal wire feeding through a hollow laser beam[J]. Applied Mechanics and Materials, 2013, 419: 305-309. DOI:10.4028/www.scientific.net/AMM.419.305
[18] GU C X, SHI S H, FU G Y. Study on the thin wall′s accumulation of inside-laser powder and wire synchronization feeding[J]. Applied Mechanics and Materials, 2014, 574: 358-362. DOI:10.4028/www.scientific.net/AMM.574.358
[19] KUZNETSOV A, JEROMEN A, GOVEKAR E. Droplet detachment regimes in annular laser beam droplet generation from a metal wire[J]. CIRP Annals, 2014, 63: 225-228. DOI:10.1016/j.cirp.2014.03.051
[20] DING X P, LI H M, WANG G Y, et al. Application of infrared thermography for laser metal-wire additive manufacturing in vacuum[J]. Infrared Physics & Technology, 2017, 81: 166-169. DOI:10.1016/j.infrared.2016.12.017
[21] PAJUKOSKI H, NAKKI J, THIEME S, et al. High performance corrosion resistant coatings by novel coaxial cold-and hot-wire laser cladding methods[J]. Journal of Laser Applications, 2016, 28: 012011. DOI:10.2351/1.4936988
[22] MOTTA M, DEMIR A G, PREVITALI B. High-speed imaging and process characterization of coaxial laser metal wire deposition[J]. Additive Manufacturing, 2018, 22: 497-507. DOI:10.1016/j.addma.2018.05.043
[23] SHAKHVERDOVA I, NOWOTNY S, THIEME S, et al. Coaxial laser wire deposition[J]. Journal of Physics: Conference Series, 2018, 1109: 012026. DOI:10.1088/1742-6596/1109/1/012026
[24] SHI J, ZHU P, FU G, et al. Geometry characteristics modeling and process optimization in coaxial laser inside wire cladding[J]. Optics & Laser Technology, 2018, 101: 341-348. DOI:10.1016/j.optlastec.2017.10.035
[25] DU F, ZHU J, DING X, et al. Dimensional characteristics of Ti-6Al-4V thin-walled parts prepared by wire-based multi-laser additive manufacturing in vacuum[J]. Rapid Prototyping Journal, 2019, 25: 849-856. DOI:10.1108/rpj-08-2018-0207
[26] GARMENDIA I, PUJANA J, LAMIKIZ A, et al. Development of an intra-layer adaptive toolpath generation control procedure in the laser metal wire deposition process[J]. Materials, 2019, 12: 352. DOI:10.3390/ma12030352
[27] KELBASSA J, GASSER A, BREMER J, et al. Equipment and process windows for laser metal deposition with coaxial wire feeding[J]. Journal of Laser Applications, 2019, 31: 022320. DOI:10.2351/1.5096112
[28] CHURRUCAM M, ARRIZABALAGA J L, HEREDIA I, et al. Comparative study of laser metal deposition (LMD) of coaxial wire and powder in the manufacture of Ti-6Al-4V structures[J]. Dyna, 2020, 95: 376-379. DOI:10.6036/9378
[29] SILZE F, SCHNICK M, SIZOVA I, et al. Laser metal deposition of Ti-6Al-4V with a direct diode laser set-up and coaxial material feed[J]. Procedia Manufacturing, 2020, 47: 1154-1158. DOI:10.1016/j.promfg.2020.04.156
[30] BECKER D, BOLEY S, EISSELER R, et al. Influence of a closed-loop controlled laser metal wire deposition process of S Al 5356 on the quality of manufactured parts before and after subsequent machining[J]. Production Engineering, 2021, 15: 489-507. DOI:10.1007/s11740-021-01030-w
[31] CAZAUBON V, AKLE A A, FISCHER X. A parametric study of additive manufacturing process: TA6V laser wire metal deposition [C]// Advances on Mechanics, Design Engineering and Manufacturing Ⅲ, 2021: 15-20. DOI: 10.1007/978-3-030-70566-4_4
[32] JI S, LIU F, SHI T, et al. Effects of defocus distance on three-beam laser internal coaxial wire cladding[J]. Chinese Journal of Mechanical Engineering, 2021, 34: 45. DOI:10.1186/s10033-021-00560-9
[33] 吉绍山, 刘凡, 傅戈雁, 等. 三光束光内同轴送丝激光熔覆成形新方法研究[J]. 表面技术, 2019, 48(4): 285-293.
JI Shaoshan, LIU Fan, FU Geyan, et al. New forming method of coaxial wire feeding inside three beams laser cladding[J]. Surface Technology, 2019, 48(4): 285-293. DOI:10.16490/j.cnki.issn.1001-3660.2019.04.040
[34] 张吉平. 三光束光内送丝熔覆实体堆积成形工艺研究[D]. 苏州: 苏州大学, 2020.
ZHANG Jiping. Research on solid forming process of three-beam inside-laser wire feeding cladding [D]. Suzhou: Soochow University, 2020.
[35] 朱进前. 环列式多激光束熔丝增材制造工艺特性研究[D]. 重庆: 重庆大学, 2018.
ZHU Jinqian. Study on the process characteristics of circular multi-laser melting wire additive manufacturing [D]. Chongqing: Chongqing University, 2018.
[36] 李慧敏. 激光熔丝增材制造工艺特性研究[D]. 重庆: 重庆大学, 2017.
LI Huimin. Study on the process characteristics of wire based laser additive manufacturing [D]. Chongqing: Chongqing University, 2017.
[37] 许翔. 激光送丝熔敷成形技术的基础及应用研究[D]. 武汉: 华中科技大学, 2018.
XU Xiang. Research on mechanism and application of laser cladding forming with wire [D]. Wuhan: Huazhong University of Science & Technology, 2018.
[38] LEE C M, WOO W S, BAEK J T, et al. Laser and arc manufacturing processes: a review[J]. International Journal of Precision Engineering and Manufacturing, 2016, 17: 973-985. DOI:10.1007/s12541-016-0119-4
[39] SCHULZ M, KLOCKE F, RIEPE J, et al. Process optimization of wire-based laser metal deposition of titanium[J]. Journal of Engineering for Gas Turbines and Power, 2019, 141. DOI:10.1115/1.4041167
[40] 战金明, 梁志刚, 黄进钰, 等. TC4钛合金表面单道激光熔覆工艺研究[J]. 应用激光, 2020, 40(6): 955-961.
ZHAN Jinming, LIANG Zhigang, HUANG Jinyu, et al. Study on the single laser cladding process on TC4 titanium alloy surface[J]. Applied Laser, 2020, 40(6): 955-961. DOI:10.14128/j.cnki.al.20204006.955
[41] 张吉平, 石世宏, 蒋伟伟, 等. 三光束光内送丝激光熔覆温度场仿真分析与工艺优化[J]. 中国激光, 2019, 46(10): 122-129.
ZHANG Jiping, SHI Shihong, JIANG Weiwei, et al. Simulation analysis of temperature field and process optimization of laser cladding based on internal wire feeding of three beams[J]. Chinese Journal of Lasers, 2019, 46(10): 122-129. DOI:10.3788/CJL201946.1002004
[42] HERALIC A, CHRISTIANSSON A K, OTTOSSON M, et al. Increased stability in laser metal wire deposition through feedback from optical measurements[J]. Optics and Lasers in Engineering, 2010, 48: 478-485. DOI:10.1016/j.optlaseng.2009.08.012
[43] HERALIC A, CHRISTIANSSON A K, LENNARTSON B. Height control of laser metal-wire deposition based on iterative learning control and 3D scanning[J]. Optics and Lasers in Engineering, 2012, 50: 1230-1241. DOI:10.1016/j.optlaseng.2012.03.016
[44] HERALICA. Monitoring and control of robotized laser metal-wire deposition [D]. Sweden: Chalmers University of Technology, 2012.
[45] SOMASHEKARAM A, SURYAKUMAR S. Studies on dissimilar twin-wire weld-deposition for additive manufacturing applications[J]. Transactions of the Indian Institute of Metals, 2017, 70: 2123-2135. DOI:10.1007/s12666-016-1032-3
[46] 蒋伟伟, 傅戈雁, 张吉平, 等. 三分光束光内同轴送丝熔覆层几何形貌预测[J]. 红外与激光工程, 2020, 49(3): 300-308.
JIANG Weiwei, FU Geyan, ZHANG Jiping, et al. Prediction of geometrical shape of coaxial wire feeding cladding in three-beam[J]. Infrared and Laser Engineering, 2020, 49(3): 300-308. DOI:10.3788/IRLA202049.0305005
[47] 杨广楠. 316L不锈钢和TC4钛合金光内送丝增材制造工艺研究[D]. 北京: 北京理工大学, 2016.
YANG Guangnan. Study on inside-beam wire feeding process of additive manufacturing about 316L stainless steel and TC4 titanium alloy [D]. Beijing: Beijing Institute of Technology, 2016.
[48] 杜发瑞. 真空环境下钛合金激光熔丝增材制造成形工艺研究[D]. 重庆: 重庆大学, 2019.
DU Farui. Study on the process characteristics of titanium alloy laser wire additive manufacturing in vacuum [D]. Chongqing: Chongqing University, 2019.
[49] 章敏. 送粉式和送丝式的钛合金激光增材制造特性研究[D]. 哈尔滨: 哈尔滨工业大学, 2013.
ZHANG Min. Research on laser additive manufacturing characteristics of titanium alloy with powder and wire [D]. Harbin: Harbin Institute of Technology, 2013.
[50] PLESSIS A, YADROITSAVA I, YADROITSEV I. Effects of defects on mechanical properties in metal additive manufacturing: a review focusing on X-ray tomography insights[J]. Materials & Design, 2020, 187: 108385. DOI:10.1016/j.matdes.2019.108385
[51] VOISIN T, CALTA N P, KHAIRALLAH S A, et al. Defects-dictated tensile properties of selective laser melted Ti-6Al-4V[J]. Materials & Design, 2018, 158: 113-126. DOI:10.1016/j.matdes.2018.08.004
[52] GU D D, MEINERS W, WISSENBACH K, et al. Laser additive manufacturing of metallic components: materials, processes and mechanisms[J]. International Materials Reviews, 2013, 57: 133-164. DOI:10.1179/1743280411y.0000000014
[53] VAYRE B, VIGNAT F, VILLENEUVEF. Metallic additive manufacturing: state-of-the-art review and prospects[J]. Mechanics & Industry, 2012, 13: 89-96. DOI:10.1051/meca/2012003
[54] KERFELDT P, ANTTI M L, PEDERSON R. Influence of microstructure on mechanical properties of laser metal wire-deposited Ti-6Al-4V[J]. Materials Science and Engineering: A, 2016, 674: 428-437. DOI:10.1016/j.msea.2016.07.038
[55] 陈刚, 路新, 章林, 等. 钛及钛合金粉末制备与近净成形研究进展[J]. 材料科学与工艺, 2020, 28(3): 98-108.
CHENG Gang, LU Xin, ZHANG Lin, et al. Research progress in powder production and near-net-shape manufacturing of titanium and its alloys[J]. Materials Science and Technology, 2020, 28(3): 98-108. DOI:10.11951/j.issn.1005-0299.20200041
[56] SAE Aerospace. Castings, structural investment, titanium alloy 6Al-4V, hot isostatically pressed: AMS 4992B[S]. USA: SAE International, 2014.
[57] SAE Aerospace. Titanium alloy bars, wire, forgings, rings, and drawn shapes 6Al4V, annealed: AMS 4928S [S]. USA: SAE International, 2011.