殷华英
(承德石油高等专科学校 计算机与信息工程系,河北 承德 067000)
摘要:
针对阀体传统制造工艺效率低、锻件性能差、成本高等问题,本文提出采用先进的多向模锻工艺进行阀体制造,并以一种不等径四通阀体为典型对象,结合Deform-3D数值分析进行工艺研究。首先,根据不等径四通阀体的结构特征,确定了分模面,并依此设计了两种锻件图;其次,根据锻件图设计了3种不同的多向模锻结构,并分别确定了模具的加载形式;最后,基于Deform-3D进行了建模分析,对比了3种模具结构下阀体的成形过程、等效应变、成形载荷等。研究表明:当阀体锻件连皮位于中部,且上凸模结构采用组合式凸模结构,下凸模为动模时,模拟获得的阀体锻件充填饱满,质量良好,无缺陷,此时模具受载更小,且成形时间短,利于提高生产效率。基于本文的分析结果进行了四通阀体的试制,获得的阀体表面成形完整,法兰质量良好,内部流线均匀连续,充分说明采用多向模锻工艺进行阀体的制造是可行的。
关键词: 四通阀体 多向模锻 模具结构 模具加载形式 等效应变 成形载荷
DOI:10.11951/j.issn.1005-0299.20210314
分类号:TG316.3
文献标识码:A
基金项目:河北省自然科学基金资助项目(E2016411008).
Multi-directional die forging process for four-way valve body based on finite element simulation
YIN Huaying
(Department of Computer and Information Engineering, Chengde Petroleum College, Chengde 067000, China)
Abstract:
In view of the problems of low efficiency, poor forging performance, and high cost of traditional manufacturing process for valve body, an advanced multi-directional die forging process was proposed. A four-way valve body which has unequal diameter was taken as the typical object, and the process was studied combined with Deform-3D numerical analysis. Firstly, on the basis of the structural characteristics of the four-way valve body, the parting surface was determined and two forging drawings were designed accordingly. Secondly, three different multi-directional die forging structures were designed according to the forging drawings, and the loading forms of the dies were determined respectively. Finally, modeling analysis was carried out based on Deform-3D, and the forming process, equivalent strain, and forming load of the valve body under three die structures were compared. Results show that when the connecting skin of the valve body forging located in the middle, the upper punch structure was the combined punch structure, and the lower punch was the moving die, the simulated valve body forging was fully filled with good quality and no defects. The die was less loaded with short forming time, which was conducive to improving the production efficiency. Based on the analysis results, the trial production of four-way valve body was carried out. The obtained valve body has complete surface forming, good flange quality, and uniform and continuous internal streamline, which demonstrates that the multi-directional die forging process is feasible for manufacturing valve bodies.
Key words: four-way valve body multi-directional die forging die structure loading form of the die equivalent strain forming load
殷华英. 基于有限元模拟的四通阀体多向模锻工艺研究[J]. 材料科学与工艺, 2022, 30(2): 81-90. DOI: 10.11951/j.issn.1005-0299.20210314.

YIN Huaying. Multi-directional die forging process for four-way valve body based on finite element simulation[J]. Materials Science and Technology, 2022, 30(2): 81-90. DOI: 10.11951/j.issn.1005-0299.20210314.

基金项目 河北省自然科学基金资助项目(E2016411008) 通信作者 殷华英,E-mail:yicheng9194@outlook.com 作者简介 殷华英(1976—),男,硕士,讲师 文章历史 收稿日期: 2021-12-03 网络出版日期: 2022-03-22
Contents Abstract Full text Figures/Tables PDF
基于有限元模拟的四通阀体多向模锻工艺研究
殷华英


承德石油高等专科学校 计算机与信息工程系,河北 承德 067000
收稿日期: 2021-12-03
基金项目: 河北省自然科学基金资助项目(E2016411008)
作者简介: 殷华英(1976—),男,硕士,讲师.
通信作者: 殷华英,E-mail:yicheng9194@outlook.com.
摘要: 针对阀体传统制造工艺效率低、锻件性能差、成本高等问题,本文提出采用先进的多向模锻工艺进行阀体制造,并以一种不等径四通阀体为典型对象,结合Deform-3D数值分析进行工艺研究。首先,根据不等径四通阀体的结构特征,确定了分模面,并依此设计了两种锻件图;其次,根据锻件图设计了3种不同的多向模锻结构,并分别确定了模具的加载形式;最后,基于Deform-3D进行了建模分析,对比了3种模具结构下阀体的成形过程、等效应变、成形载荷等。研究表明:当阀体锻件连皮位于中部,且上凸模结构采用组合式凸模结构,下凸模为动模时,模拟获得的阀体锻件充填饱满,质量良好,无缺陷,此时模具受载更小,且成形时间短,利于提高生产效率。基于本文的分析结果进行了四通阀体的试制,获得的阀体表面成形完整,法兰质量良好,内部流线均匀连续,充分说明采用多向模锻工艺进行阀体的制造是可行的。
关键词: 四通阀体 多向模锻 模具结构 模具加载形式 等效应变 成形载荷
Multi-directional die forging process for four-way valve body based on finite element simulation
YIN Huaying


Department of Computer and Information Engineering, Chengde Petroleum College, Chengde 067000, China
Abstract: In view of the problems of low efficiency, poor forging performance, and high cost of traditional manufacturing process for valve body, an advanced multi-directional die forging process was proposed. A four-way valve body which has unequal diameter was taken as the typical object, and the process was studied combined with Deform-3D numerical analysis. Firstly, on the basis of the structural characteristics of the four-way valve body, the parting surface was determined and two forging drawings were designed accordingly. Secondly, three different multi-directional die forging structures were designed according to the forging drawings, and the loading forms of the dies were determined respectively. Finally, modeling analysis was carried out based on Deform-3D, and the forming process, equivalent strain, and forming load of the valve body under three die structures were compared. Results show that when the connecting skin of the valve body forging located in the middle, the upper punch structure was the combined punch structure, and the lower punch was the moving die, the simulated valve body forging was fully filled with good quality and no defects. The die was less loaded with short forming time, which was conducive to improving the production efficiency. Based on the analysis results, the trial production of four-way valve body was carried out. The obtained valve body has complete surface forming, good flange quality, and uniform and continuous internal streamline, which demonstrates that the multi-directional die forging process is feasible for manufacturing valve bodies.
Keywords: four-way valve body multi-directional die forging die structure loading form of the die equivalent strain forming load
阀门是控制流体流动的重要零部件,在人类的日常生活,普通工业、石油业、航天领域、军工领域等都有着极其广泛的应用[1-3]。阀体是阀门中承载压力的主要零件,其质量和性能直接由制造工艺决定,其中使用最普遍的是传统的铸造工艺和普通模锻工艺。铸造工艺工序多,过程长,而普通模锻工艺后续需要机加工孔道,二者效率均较低。同时,阀体铸件晶粒大、组织疏松间隙大[4],而普通模锻件机加工后连续的组织被切断且外露易腐蚀[5],因此,两种工艺都会影响阀体的性能,仅适用于压力较小、环境良好的场合;对于尺寸较大的阀体,通常采用锻、焊结合的方式生产[6],但对焊缝的要求极高,导致制造成本较高。为解决上述难题,本文提出采用更为先进的多向模锻技术应用于阀体的制造,该技术对各类阀体的适用性好,既能保证生产效率,也可满足性能、生产成本等多方面的要求,因此该研究具有一定的工程意义。
多向模锻是指从多个方向对坯料进行挤压,利用紧闭的模腔获得与成品件尺寸相近的一种加工方法[7-8],其具有以下优点[9-10]:生产效率高;可成形形状不规则、不对称、带法兰、多孔的复杂锻件;可按需要设计多个分模面;后续机加工量小,通常仅需切除通孔连皮,材料成本低;锻件晶粒细小,组织连续,流线好,耐腐蚀;可实现较大的变形量。由文献可知,国内虽然已存在较多的应用案例,如姜雪鹏等[11]采用多向模锻生产T型三通阀,采用数值模拟技术对成形过程中的变形力进行了研究,实现了锻造力的可预测,并结合物理实验进行了对比验证;王波等[12]运用Deform-3D软件对等径四通阀体的多向模锻工艺进行了优化,确定了最佳的水平和垂直冲头加载方式,并通过模锻试验论证了可行性;任运来等[13]针对高温高压阀体提出了多向模锻工艺,并结合有限元模拟研究了4种不同模具动作顺序对载荷和模具温度的影响,最终确定了适合的工艺并获得了成形质量较好的阀体锻件;刘东帅[14]对液压阀体的多向模锻工艺展开了研究,分析了冲头不同进给速率对阀体质量的影响并取得了良好的效果。但目前的研究多数是针对结构较为简单或等径的阀体,而对应用于结构复杂的不等径阀体的研究报道较少,故本文以某种不等径四通阀体为研究对象,对其多向模锻新工艺进行开发,以取代落后的传统生产工艺,进而提高生产效率和锻件质量。本文选取的阀体模型如图 1所示,内部存在4个通道,其中3个通道端面存在法兰,阀体垂直孔道外径尺寸不一,其成形难点如下:1)阀体水平和垂直方向截面不一,且变化大,成形难度大;2)阀体上下结构不对称,水平孔道和垂直孔道尺寸不一致,导致成形不一致,使得材料变形量、流速等不同,因此,不易确定各凸模的加载方式,增大了阀体成形质量的不确定性;3)阀体一次成形,变形量大,水平孔道端面法兰不易填充饱满;4)需要较大的成形力,对锻造设备和模具寿命要求高;5)成形过程受温度影响较大。因此,本文运用Deform-3D软件进行模拟以协助分析[15],研究了不同模具结构及模具加载形式对阀体锻件质量及模具载荷的影响,确定了理想的锻造工艺,并根据模拟分析结果进行了阀体锻造试验,获得了符合质量要求的阀体。
图 Figure1(Fig.Figure1)
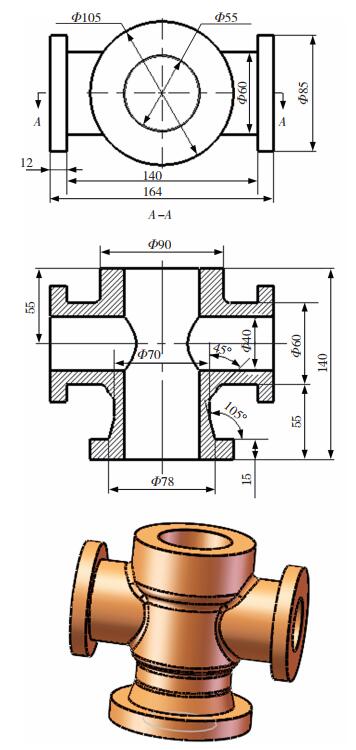
1 多向模锻工艺设计根据阀体的结构特征,设计的两种锻件图如图 2所示。
图 Figure2(Fig.Figure2)
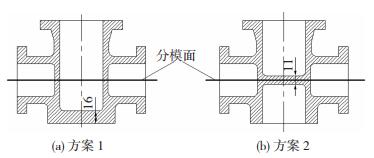
选取最大投影面为分模面,即采用水平分模。坯料采用圆形棒料,并使用垂直放置,这是由于:1)若使用水平放置,由于水平通道直径较小,根据锻造前后体积不变原则,计算可知坯料的高径比高达3.6,在镦粗时容易引起弯曲变形,而采用垂直放置,因垂直通道直径较大,坯料高径比为2.27,小于镦粗极限[16];2)方便棒料的定位。由于水平通道和垂直通道无法直接挤出,因此,两种方案均设置有连皮,厚度需计算合理,连皮厚度太小,会造成各方向凸模碰撞,而厚度太大,则会加大加工量,且造成材料浪费。两种方案的不同之处在于方案1的垂直方向连皮位于底部(图 2(a)),而方案2位于中部(图 2(b))。由于连皮厚度不一致,因此坯料长度不同。
针对方案1设计了图 3(a)和(b)两种多向模锻结构,成形流程基本相同,放入坯料后,上凹模下行完成合模,各凸模按顺序挤压完成成形,然后各凸模及上凹模复位,由下凸模顶出取件。区别在于,结构1中上凸模为组合凸模,而下凸模全程不参与挤压运动,仅起到顶杆作用,而结构2中上凸模为单凸模,下凸模在某个时刻参与挤压运动,与上凸模相向挤压,同时在脱模时起顶杆的作用。针对方案2设计了图 3(c)所示模具结构,其成形流程与前两种结构相似,同时综合了前两种结构的特点,上凸模采用组合凸模,且下凸模参与挤压运动。以下运用Deform-3D软件对3种不同模具结构形式的阀体成形过程分别进行模拟,并对其可行性进行分析。
图 Figure3(Fig.Figure3)
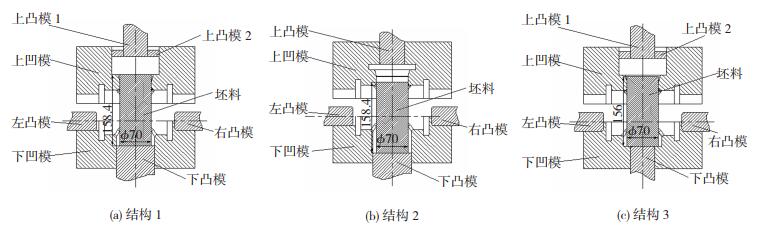
2 有限元建模与分析2.1 有限元模型的建立利用Solidworks三维造型软件完成上述3种模具结构的建模,由于模型关于xoz面和yoz面对称,为简化计算以及方便后续观察,以xoz面为对称面,取模型的二分之一为研究对象,同时将上凹模、下凹模直接装配为合模状态,并将3组模型依次导入Deform-3D中进行计算。坯料均设为塑性体,材料为25号钢,由于圆棒料在锻前需中频感应加热,故设置初始温度为1 050 ℃,通过高温压缩试验,获得的25号钢不同温度及不同应变率下的真实应力-应变曲线如图 4所示。
图 Figure4(Fig.Figure4)
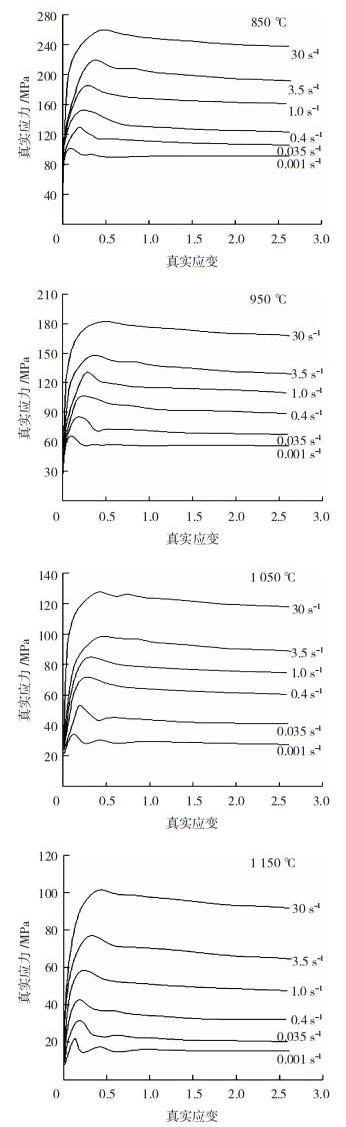
模具均设为刚体,材料为H13钢,为保护模具,需预热,故设置初始温度为420 ℃。坯料和模具均通过四面体网格划分,坯料划分网格数为80 000个,模具均划分网格数为32 000个,坯料、模具之间的传热因数为8 W/(m2 ·℃),摩擦因数为0.3[17]。设备采用液压机,3种模具结构,各凸模的加载方式均按照图 5在Deform-3D中设置,图中左凸模和右凸模为同一条直线,但加载方向相反。
图 Figure5(Fig.Figure5)
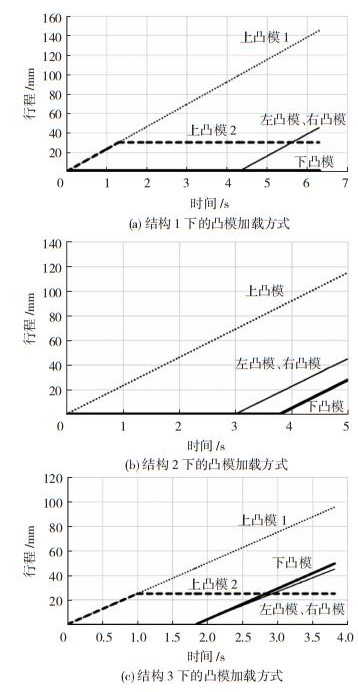
例如,以结构3模具形式为例,有限元建模结果见图 6所示,按照图 5(c),上凸模1和上凸模2以25 mm/s向下恒定挤压1 s后,上凸模1继续同速恒定挤压至成形结束,而上凸模2停止;左凸模和右凸模在成形开始1.82 s后,以22.5 mm/s分别向右、向左相对恒定挤压至成形结束;下凸模在成形开始1.84 s后以25 mm/s向上恒定挤压至成形结束。
图 Figure6(Fig.Figure6)
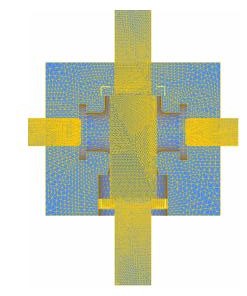
2.2 成形结果分析结构1模具形式阀体的成形过程和材料流动情况如图 7(a)、图 8(a)所示。棒料在上凸模1、2共同作用下得到镦粗,上部法兰得到预成形;随后,上凸模2到达终点,上凸模1持续向下挤压成形垂直孔道,遭到下凸模的限制后,大量金属分别向左、右两端聚集,同时左、右凸模开始运动成形水平孔道,促进了金属向难填充的左、右法兰流动,但由于受到上凸模1的持续挤压作用,使得阀体下端填充较快,并在端面形成大量毛刺,同时由于上端金属流失过快,径向填充阻力大,使得左、右法兰上部出现充不足的现象,而下部填充完整。
图 Figure7(Fig.Figure7)
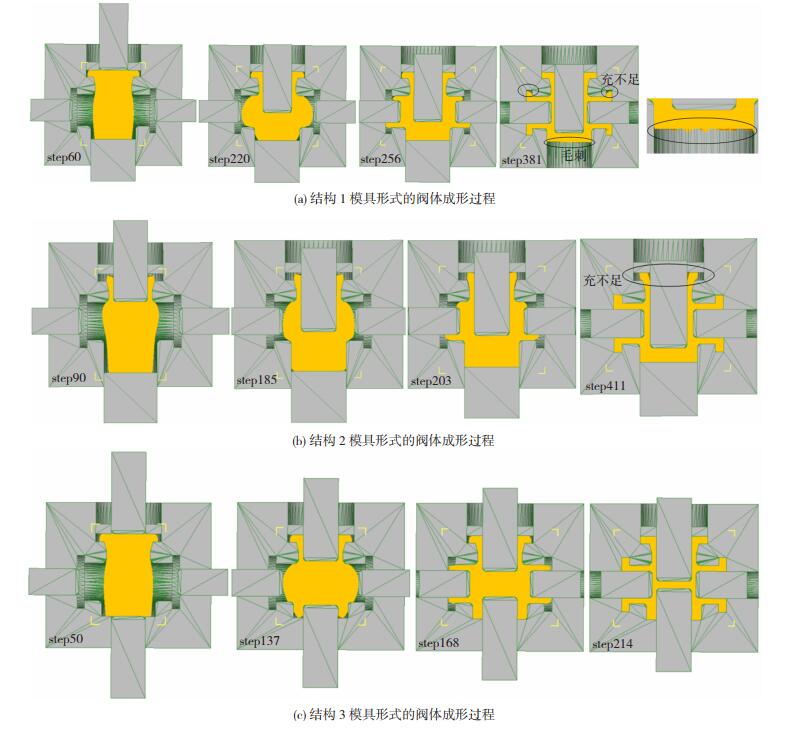
图 Figure8(Fig.Figure8)
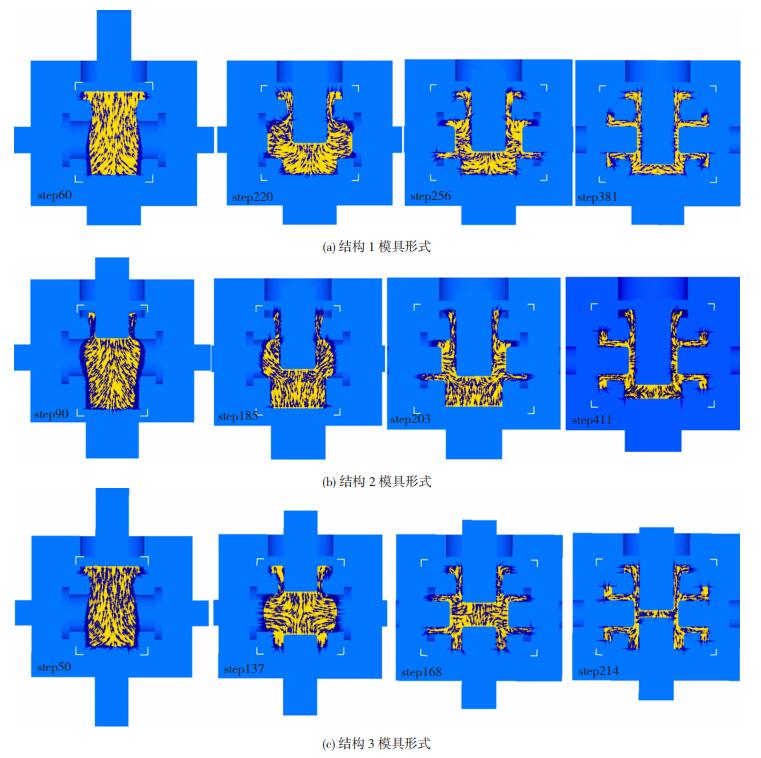
结构2模具形式阀体的成形过程和材料流动情况如图 7(b)、图 8(b)所示。前期没有对上部法兰进行预成形,其余过程与结构1模具形式时相似,上凸模优先向下挤压成形垂直孔道,坯料主要变形为镦粗,金属仍以向左右流动为主;随后左、右凸模开始运动成形水平通孔道,同时下凸模开始向上挤压,与上凸模相对挤压,促进金属向难填充的左、右法兰流动。虽然左、右法兰上、下部填充速度不一致,但最终均充填饱满,使采用结构1模具形式出现的法兰充不满问题得到解决,然而, 由于未对上部法兰进行预成形,顶部金属受上凸模挤压后流失过多,尽管受到下凸模作用,部分金属转而向上流动,但由于阻力过大,因此仍出现了上部法兰充不足的现象。
结构3模具形式阀体的成形过程和材料流动情况如图 7(c)、图 8(c)所示。采用该结构形式,不仅对上部法兰进行了预成形,同时采用上、下双凸模挤压,既能保证上部法兰填充完整,又保证了左、右法兰的填充完整,其次由于采用双凸模挤压,成形时间更短,对生产效率的提高起到一定的作用。仿真结果表明,只有结构3模具形式能够获得成形完整的四通阀体锻件。
2.3 等效应变分析对锻后阀体进行等效应变分析可以判断成形过程中变形的剧烈程度[18],其次在一定程度上,根据锻后阀体等效应变分布的均匀性可以判断成形件的质量。3种模具结构下的等效应变分布如图 9所示。
图 Figure9(Fig.Figure9)
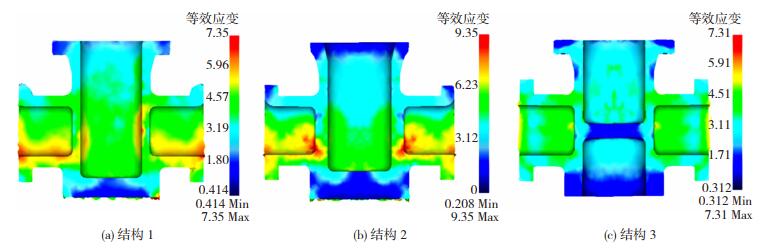
由图 9可以看到,采用结构2模具形式时,最大等效应变值最大,其次是结构1模具形式,最小的是结构3模具形式。结构1模具形式和结构2模具形式,由于连皮位于底部,金属材料较多的向下方流动,其次左、右两端金属聚集较多,使得成形左、右孔道时,偏下部变形剧烈;而结构3模具形式的连皮位于中部,金属由两端向中间聚集,更方便金属向左、右两端流动,变形更合理。同时,从等效应变分布的均匀性可以明显看出,采用结构3模具形式时,分布更好,更利于保证最终阀体的成形质量。
2.4 最大成形载荷分析采用结构2模具形式时,由于上凸模为单凸模,因此为方便比较,在结构1模具形式和结构3模具形式中取同样成形上端孔道的上凸模1进行比较。根据数值分析结果,对3种模具结构的最大成形载荷进行了统计与制图,结果见图 10。从图 10可以比较直观地看出,采用结构3模具形式时,各模具最大成形载荷均小于另外两种模具结构。由图 3的3种模具结构图可以看出,各模具的有效工作面积基本相同,因此,载荷越小越利于减小模具的单位受力,更利于模具的使用,延长模具的寿命。
图 Figure10(Fig.Figure10)
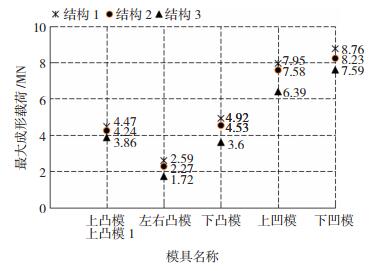
2.5 阀体锻后温度分布分析图 11为3种模具结构下阀体锻后的温度分布图,可以看到,采用结构1和结构2模具形式时,各部位温度分布情况基本相似。由于连皮位于底部,材料主要向下端集中,阀体上孔道最先成形,经热传递散热更多,因此,孔内温度较低;其次,坯料最先得到镦粗后与上、下凹模内壁接触较早,因此垂直孔道表面温度要低于水平孔道表面温度。
图 Figure11(Fig.Figure11)
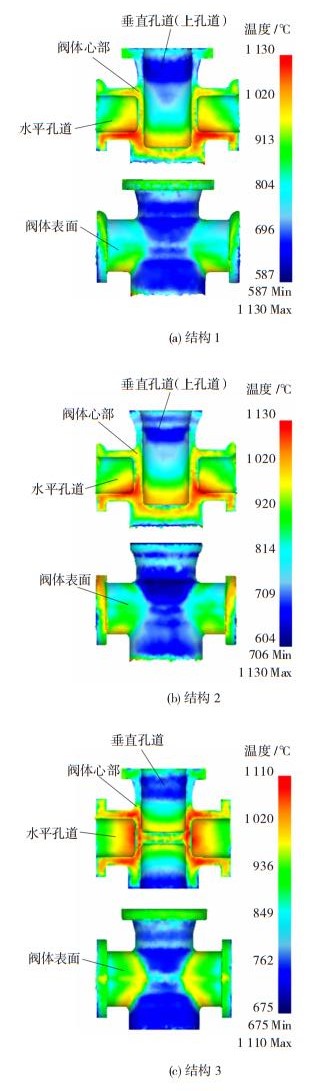
图中结构1和结构2模具形式的阀体,最高温度均为1 130 ℃,主要位于阀体偏下端心部,且温度高于锻件坯料初始温度1 050 ℃,原因在于材料集中在下端,受三向挤压后,金属变形剧烈,塑性功产生的温升显著,并且中间心部不与凸凹模直接接触,因此温降速度慢。
综上认为,由于材料较多向下聚集,导致阀体上、下两端温差过大,水平孔道心部及表面上下端温度分布不均匀,冷却时易产生较大的应力,引起裂纹。
采用结构3模具形式时,由于连皮位于中部,材料向中间聚集,因此,可以有效避免阀体上、下两端温度温差过大,以及水平孔道心部及表面上下端温度分布不均匀的现象。阀体上、下部温度低于左右部温度,是由于上、下部成形早,后续基本不发生变形,因此,出现上下部内孔及端面温度均较低的情况,左、右部温度较高也利于最终的金属流动,确保了左、右法兰的填充完整。总体分析可知,采用结构3的模具形式,锻后阀体温度分布更为均匀,更符合成形原理; 其次,成形时间相对另外两种结构要短,因此热量流失少,阀体最低温度为675 ℃,高于另外两种结构,而阀体最高温度为1 100 ℃,低于另外两种结构,显然整体温差更小,更有利于避免因冷却不均而造成冷却裂纹的产生,因此,采用结构3模具形式时更有利于提高阀体的成形质量。
3 阀体试制及结果通过Deform-3D进行的模拟及分析可知,该四通阀体多向模锻结构,采用结构3模具形式时,不仅能够获得填充完整的四通阀体,对阀体质量的提高也有一定的作用,同时可以降低阀体模具的受载,提高模具寿命。其次,根据模拟确定了各模具的动作顺序及规律。采用多向模锻液压机进行阀体试制(图 12(a)),上下合模,棒料垂直放置,通过中频感应炉加热设备将棒料加热至1 050 ℃ (图 12(b)),棒料尺寸为Φ70 mm×156 mm。模具预热至约420 ℃,锻前喷涂水基石墨乳润滑液。最终获得的不等径四通阀体成形情况如图 12(c)所示,可以看到,阀体成形饱满,3个法兰质量较好,无充满不足问题。阀体切开截面图如图 12(d)所示,可以看到,金属流线均匀分布,不存在折叠缺陷,4个孔道成形情况较好,与有限元模拟结果基本一致。连皮切除后,最终阀体件截面图如图 12(e)所示。
图 Figure12(Fig.Figure12)
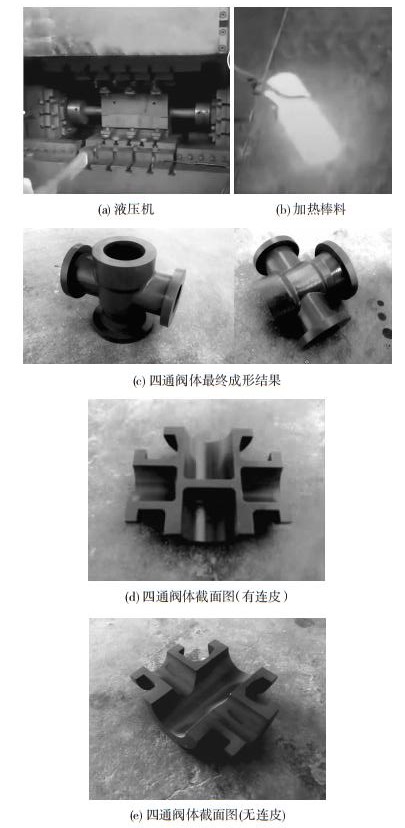
4 结论1) 采用Deform-3D对不等径四通阀体的多向模锻工艺进行了研究,比较了两种锻件结构,结果表明,连皮位于中部时,能够获得填充完整的阀体,同时模具受载更小,阀体锻后温度分布更均匀,而连皮位于底部时,阀体会出现充不足缺陷。
2) 利用Deform-3D的协助分析,获得了四通阀体的最佳多向模锻结构,确定了各模具的动作顺序及规律,同时可知,合理地制定模具加载方式能够有效改善金属的流动情况,避免折叠、充不足等缺陷的产生,从而最大程度地提高锻件的成形质量,并可有效改善各模具的受载情况,利于减小模具的单位受力,有效延长模具的使用寿命。
3) 通过对四通阀体的试制,获得了质量较好的锻件,充分表明采用多向模锻工艺进行阀体的制造是可行的,本文的阀体多向模锻的有限元建模及分析结果正确可靠,对同类零件的多向模锻工艺的研究能够起到一定的指导作用。
参考文献
[1] 石尚, 董洪波, 唐予松, 等. 2A12铝合金截止阀阀体成形过程模拟研究[J]. 塑性工程学报, 2019, 26(4): 48-54.
SHI Shang, DONG Hongbo, TANG Yusong, et al. Simulation study on forming process of 2A12 aluminum alloy stop valve body[J]. Journal of Plasticity Engineering, 2019, 26(4): 48-54. DOI:10.3969/j.issn.1007-2012.2019.04.007
[2] 江荣忠, 王志录, 张元东, 等. 石油阀体锻造工艺与模具设计[J]. 热加工工艺, 2018, 47(9): 128 -130, 134.
JIANG Rongzhong, WANG Zhilu, ZHANG Yuandong, et al. Forging process and die design of petroleum valve bodies[J]. Hot Working Technology, 2018, 47(9): 128 -130, 134. DOI:10.14158/j.cnki.1001-3814.2018.09.033
[3] 刘光辉, 刘华, 王涛, 等. 仪表阀体多向可控精密成形工艺[J]. 锻压技术, 2020, 45(3): 8-13.
LIU Guanghui, LIU Hua, WANG Tao, et al. Multi-directional controllable precision forming for instrument valve body[J]. Forging & Stamping Technology, 2020, 45(3): 8-13. DOI:10.13330/j.issn.1000-3940.2020.03.002
[4] 杨建, 曹峤, 宋帮鹍, 等. 一种高磅级阀体的铸造缺陷分析与工艺优化[J]. 铸造工程, 2021, 45(2): 61-63.
YANG Jian, CAO Qiao, SONG Bangkun, et al. Foundry defect analysis and process optimization of high pound class valve body[J]. Foundry Engineering, 2021, 45(2): 61-63. DOI: 1673-3320(2021)02-0061-03
[5] 顾文俊. 空排止回阀阀体多向模锻工艺研究[D]. 合肥: 合肥工业大学, 2019.
GU Wenjun. Research on multidirectional forging process for check valve body[D]. Hefei : Hefei University of Technology, 2019.
[6] 胡红磊. 水平带法兰阀体多向模锻工艺研究[D]. 秦皇岛: 燕山大学, 2015.
HU Honglei. Study on multiple-ram forging process of level flanged valve[D]. Qinhuangdao: Yanshan University, 2015.
[7] ITO Y, HOSHI N, HAYAKAWA T, et al. Mechanical properties and biological responses of ultrafine-grained pure titanium fabricated by multi-directional forging[J]. Materials Science and Engineering, 2019, 245: 30-36. DOI:10.1016/j.mseb.2019.05.002
[8] ZHAO J, DENG Y, ZHANG J, et al. Effect of temperature and strain rate on the grain structure during the multidirectional forging of the Al-Zn-Mg-Cu alloy[J]. Materials Science and Engineering, 2019, 756: 119-128. DOI:10.1016/j.msea.2019.04.033
[9] ZHANG R, LI Z, SHENG X, et al. Grain refinement and mechanical properties improvements in a high strength Cu-Ni-Si alloy during multidirectional forging[J]. Fusion Engineering and Design, 2020, 159(147): 111766. DOI:10.1016/j.fusengdes.2020.111766
[10] NOURI S, KAZEMINEZHAD M, SHADKAM A. Flow stress of 2024 aluminum alloy during multi-directional forging process and natural aging after plastic deformation[J]. Materials Chemistry and Physics, 2020, 254(5): 123446. DOI:10.1016/j.matchemphys.2020.123446
[11] 姜雪鹏, 潘晴, 李毅波, 等. T型三通多向模锻过程变形力预测方法[J]. 塑性工程学报, 2021, 28(5): 113-125.
JIANG Xuepeng, PAN Qing, LI Yibo, et al. Deformation force prediction method of tee valve inmulti-directional die forging process[J]. Journal of Plasticity Engineering, 2021, 28(5): 113-125. DOI:10.3969/j.issn.1007-2012.2021.05.013
[12] 王波, 张加正. 四通阀体热锻成形CAE分析及工艺优化[J]. 锻压技术, 2021, 46(5): 7-11.
WANG Bo, ZHANG Jiazheng. CAE analysis and process optimization on hot forging for four-way valve body[J]. Forging & Stamping Technology, 2021, 46(5): 7-11. DOI:10.13330/j.issn.1000-3940.2021.05.002
[13] 任运来, 李明权, 任杰, 等. 高温高压阀体的多向模锻技术研究[J]. 重型机械, 2015(5): 1-5.
REN Yunlai, LI Mingquan, REN Jie, et al. Study on multi-ram forging technology of high temperature high pressure valve body[J]. Heavy Machinery, 2015(5): 1-5. DOI:10.13551/j.cnki.zxjxqk.2015.05.001
[14] 刘东帅. 冲头速率对多向模锻液压阀体质量的影响[J]. 热加工工艺, 2020, 49(9): 92-94, 102.
LIU Dongshuai. Effect of punch rate on quality of hydraulic valve body formed by multi-direction die forging[J]. Hot Working Technology, 2020, 49(9): 92-94, 102. DOI:10.14158/j.cnki.1001-3814.20183364
[15] YIN J, HU R. Closed-die forging process of copper alloy valve body: finite element simulation and experiments[J]. Journal of Materials Research and Technology, 2020, 10(1): 1339-1347. DOI:10.1016/j.jmrt.2020.12.087
[16] 姚文俊, 陈松. 汽车法兰轴结构件塑性成形工艺分析及改进[J]. 锻压技术, 2020, 45(11): 7-12.
YAO Wenjun, CHEN Song. Analysis and improvement on plastic forming process for structure part of automobile flange shaft[J]. Forging & Stamping Technology, 2020, 45(11): 7-12. DOI:10.13330/j.issn.1000-3940.2020.11.002
[17] 张红颖, 刘颖, 刘晓芹. 等径三通多向加载挤压成形模拟研究[J]. 大型铸锻件, 2013(3): 23-27.
ZHANG Hongying, LIU Ying, LIU Xiaoqing. Simulation research on extrusion forming with multi-direction load of equal-diameter tee joint[J]. Heavy Casting and Forging, 2013(3): 23-27. DOI:10.14147/j.cnki.51-1396/tg.2013.03.005
[18] 陈凌翔, 李月超. 汽车六角球头冷锻工艺优化与数值仿真[J]. 材料科学与工艺, 2020, 28(5): 75-82.
CHEN Lingxiang, LI Yuechao. Optimization and numerical simulation of cold forging process for automobile hexagonal ball head[J]. Materials Science and Technology, 2020, 28(5): 75-82. DOI:10.11951/j.issn.1005-0299.20190227