周康根1,
宁凌峰1,
彭长宏1,
何德文1
1.中南大学冶金与环境学院,长沙 410083
Stepwise leaching of valuable metals from red mud using hydrochloric acid
TENG Chunying1,,ZHOU Kanggen1,
NING Lingfeng1,
PENG Changhong1,
HE Dewen1
1.School of Metallurgy and Environment, Central South University, Changsha 410083, China
-->
摘要
HTML全文
图
参考文献
相关文章
施引文献
资源附件
访问统计
摘要:采用盐酸2段分级浸出工艺回收氧化铝赤泥中的有价金属元素。通过考察液固比、反应温度、反应时间及盐酸使用量对浸出率的影响,确定了2段浸出的实验工艺。结果表明:在盐酸用量为理论用量的40%、90 ℃液固比为7∶1、反应时间1 h的条件下,Ca的浸出率为96.2%,Na的浸出率为82.47%,Al的浸出率为42.87%,其他元素几乎不浸出,这是第1段浸出;在盐酸用量为理论量的130%、90 ℃、盐酸浓度8.8 mol·L-1的条件下,浸出1段酸浸渣,Fe的浸出率99.65%,Sc的浸出率88.76%,V的浸出率93.58%,其他稀土元素的浸出率均达到了70%左右,这是第2段浸出。
关键词: 赤泥/
盐酸浸出/
有价金属/
回收
Abstract:In our study, a two-step leaching method was developed for valuable metal recovery from red mud by hydrochloric acid. By investigating the effect of liquid to solid ratio, reaction temperature, reaction time and the amount of hydrochloric acid on the leaching efficiency, the two-step leaching program was established. During the first stage,the addition amount of hydrochloric acid was 40% of theoretical values, and the reaction temperature and time were 90 ℃ and 1 h, respectively, with liquid-solid ratio as 7∶1. The leaching efficiencies of Ca, Na and Al were 96.2%, 82.47% and 42.87%, respectively, and almost no other elements was leached at this stage. During the second stage, the amount of hydrochloric acid was 130% of theoretical values, the reaction time was 90 ℃, and the concentration of hydrochloric acid was 8.8 mol·L-1. The leaching residue from the first stage was further leached in this stage, and the leaching efficiencies of Fe, Sc, and V were 99.65%, 88.76% and 93.58%. Furthermore, the leaching efficiencies of all other rare earth elements were above 70%.
Key words:red mud/
hydrochloric acid leaching/
valuable metals/
recovery.

[1] | YANG Y, WANG X W, WANG M Y, et al.Recovery of iron from red mud by selective leach with oxalic acid[J].Hydrometallurgy,2015,157:239-245 |
[2] | AGATZINI-LEONARDOU S, OUSTADAKIS P, TSAKIRIDIS P E, et al.Titanium leaching from red mud by diluted sulfuric acid at atmospheric pressure[J].Journal of Hazardous Materials,2008,157(2/3):579-586 |
[3] | 王克勤,李生虎.氧化铝赤泥盐酸浸出回收钒的试验研究[J].稀有金属与硬质合金,2012(6):5-8 |
[4] | 王克勤,王皓,李生虎.盐酸浸出赤泥回收铝的研究[J].有色金属(冶炼部分),2012(7):16-18 |
[5] | PIETRZYK-SOKULSKA E, KULCZYCKA J.Impact of landfilling of red mud waste on local environment:The case of Górka[J].Gospodarka Surowcami Mineralnymi,2015,31(2):137-156 |
[6] | LIU Z B, LI H X.Metallurgical process for valuable elements recovery from red mud:A review[J].Hydrometallurgy,2015,155:29-43 |
[7] | BORRA C, BLANPAIN B, PONTIKES Y, et al.Recovery of rare earths and other valuable metals from bauxite residue (red mud):A review[J].Journal of Sustainable Metallurgy,2016,2(4):365-386 |
[8] | HUANG Y F, CHAI W C, HUI G H, et al.A perspective of stepwise utilisation of Bayer red mud: Step two-extracting and recovering Ti from Ti-enriched tailing with acid leaching and precipitate flotation[J].Journal of Hazardous Materials,2016,307:318-327 |
[9] | DAVRIS P, BALOMENOS E, PANIAS D, et al.Selective leaching of rare earth elements from bauxite residue (red mud), using a functionalized hydrophobic ionic liquid[J].Hydrometallurgy,2016,164:125-135 |
[10] | LI G H, LIU M X, RAO M J, et al.Stepwise extraction of valuable components from red mud based on reductive roasting with sodium salts[J].Journal of Hazardous Materials,2014,280:774-780 |
[11] | 刘奋照,王中慧,薛玫,等.赤泥利用及提炼钪综述[J].广东化工,2015,42(5):56-58 |
[12] | 王琪,姜林.硫酸浸出赤泥中铁、铝、钛的工艺研究[J].矿冶工程,2011,31(4):90-94 |
[13] | BORRA C R, BLANPAIN B, PONTIKES Y, et al.Smelting of bauxite residue (red mud) in view of iron and selective rare earths recovery[J].Journal of Sustainable Metallurgy,2016,2(1):28-37 |
[14] | BORRA C R, MERMANS J, BLANPAIN B, et al.Selective recovery of rare earths from bauxite residue by combination of sulfation, roasting and leaching[J].Minerals Engineering,2016,92:151-159 |
[15] | ABHILAS H, SINHA S, SINHA M K,et al.Extraction of lanthanum and cerium from Indian red mud[J].International Journal of Mineral Processing,2014,130:70-73 |
[16] | 李亮星.从赤泥中回收铁钛的工艺研究[D].赣州:江西理工大学,2009 |
[17] | BORRA C R, PONTIKES Y, BINNEMANS K, et al.Leaching of rare earths from bauxite residue (red mud)[J].Minerals Engineering,2015,76:20-27 |
[18] | 王克勤,于永波,王皓,等.赤泥盐酸浸出提取钪的试验研究[J].稀土,2010(1):95-98 |

Turn off MathJax -->
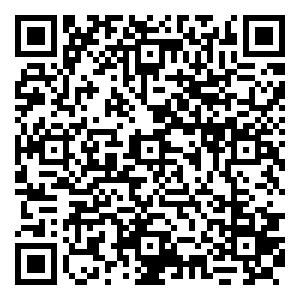
计量
文章访问数:1019
HTML全文浏览数:783
PDF下载数:311
施引文献:0
出版历程
刊出日期:2018-01-14
-->
盐酸分级浸出赤泥中有价金属元素
滕春英1,,周康根1,
宁凌峰1,
彭长宏1,
何德文1
1.中南大学冶金与环境学院,长沙 410083
基金项目:
关键词: 赤泥/
盐酸浸出/
有价金属/
回收
摘要:采用盐酸2段分级浸出工艺回收氧化铝赤泥中的有价金属元素。通过考察液固比、反应温度、反应时间及盐酸使用量对浸出率的影响,确定了2段浸出的实验工艺。结果表明:在盐酸用量为理论用量的40%、90 ℃液固比为7∶1、反应时间1 h的条件下,Ca的浸出率为96.2%,Na的浸出率为82.47%,Al的浸出率为42.87%,其他元素几乎不浸出,这是第1段浸出;在盐酸用量为理论量的130%、90 ℃、盐酸浓度8.8 mol·L-1的条件下,浸出1段酸浸渣,Fe的浸出率99.65%,Sc的浸出率88.76%,V的浸出率93.58%,其他稀土元素的浸出率均达到了70%左右,这是第2段浸出。
English Abstract
Stepwise leaching of valuable metals from red mud using hydrochloric acid
TENG Chunying1,,ZHOU Kanggen1,
NING Lingfeng1,
PENG Changhong1,
HE Dewen1
1.School of Metallurgy and Environment, Central South University, Changsha 410083, China
Keywords: red mud/
hydrochloric acid leaching/
valuable metals/
recovery
Abstract:In our study, a two-step leaching method was developed for valuable metal recovery from red mud by hydrochloric acid. By investigating the effect of liquid to solid ratio, reaction temperature, reaction time and the amount of hydrochloric acid on the leaching efficiency, the two-step leaching program was established. During the first stage,the addition amount of hydrochloric acid was 40% of theoretical values, and the reaction temperature and time were 90 ℃ and 1 h, respectively, with liquid-solid ratio as 7∶1. The leaching efficiencies of Ca, Na and Al were 96.2%, 82.47% and 42.87%, respectively, and almost no other elements was leached at this stage. During the second stage, the amount of hydrochloric acid was 130% of theoretical values, the reaction time was 90 ℃, and the concentration of hydrochloric acid was 8.8 mol·L-1. The leaching residue from the first stage was further leached in this stage, and the leaching efficiencies of Fe, Sc, and V were 99.65%, 88.76% and 93.58%. Furthermore, the leaching efficiencies of all other rare earth elements were above 70%.