
ADVANCES IN KEY MECHANICAL PARAMETERS FOR RELIABILITY ASSESSMENT OF HIGH-SPEED TRAIN BEARINGS 1)
Wang Xi
通讯作者: 2)王曦, 教授, 主要研究方向: 车辆结构可靠性及优化. E-mail:wangxi@bjtu.edu.cn
收稿日期:2020-06-19接受日期:2020-09-17网络出版日期:2021-12-31
基金资助: |
Received:2020-06-19Accepted:2020-09-17Online:2021-12-31
作者简介 About authors

摘要
轴承是高速列车牵引传动和轮轴系统的关键零部件. 受列车运行过程中电机转矩、齿轮啮合以及轮轨随机激励的影响,轴承可能发生疲劳破坏, 严重影响高速列车的行车安全.我国特有的复杂运用条件对轴承部件的疲劳性能提出了更高的要求,而轴承疲劳可靠性的基础理论和关键技术是我国轴承正向设计研发中的薄弱环节.可靠性评估方面的相关研究在解决轴承可靠性研究的瓶颈问题中起到了承上启下的关键作用.高速列车轴承可靠性评估手段与技术旨在获得使用环境中轴承可靠性评估的关键力学参量,并以此推动复杂激励下轴承疲劳可靠性理论研究. 因此,需要哪些关键力学参量并且在复杂的实际使用环境下如何去获取这些力学参量是进行高速列车轴承可靠性评估的关键所在.本文首先概述了高速列车轴承所处的复杂使用环境及运用中的主要失效模式,并据此分析了高速列车轴承可靠性评估所需的关键力学参量,强调了轴承内部滚滑行为和载荷分布在可靠性评估和轴承状态监测中的重要作用,之后从计算模型和测试技术等方面系统阐述了针对这两个关键力学参量的研究进展.最后提出了在高速列车轴承可靠性评估关键力学参量特征及测试技术研究中值得关注的若干问题.
关键词:
Abstract
Bearing is the key component of the traction transmission and wheelset systems of high-speed train. It is possible to experience fatigue damage or failure under the influence of traction motor torque, gear meshing and random wheel-rail excitation during the train operation, which seriously threatens the operation safety of high-speed train. The special complex service conditions of high-speed trains in China require higher fatigue performance and reliability for bearing components, however, the fundamental theory and key technology of fatigue performance and reliability are the weak links in the forward design and development of bearing in China. The research on bearing reliability assessment plays a significant connecting role in solving the bottleneck problem of bearing reliability research. The method and technology of reliability assessment for high-speed train bearings aim to obtain the key mechanical parameters for bearing reliability assessment in service environment, and further to promote the fundamental theory research on bearing fatigue performance and reliability under complex internal and external excitations. Therefore, the key is to identify what mechanical parameters are required for reliability assessment of high-speed train bearings and how to obtain them in such a complex service environment. In this article, the complex service environment and main failure modes of high-speed train bearings during the train operation are firstly reviewed. Then, the key mechanical parameters required for the reliability assessment of high-speed train bearings are proposed and analyzed, in which the important roles of internal rolling-sliding behavior and load distribution on bearing reliability assessment and condition monitoring are emphasized. From the aspects of calculation methods and measurement technologies, the advances to obtain those two key mechanical parameters (i.e. the rolling-sliding behavior and load distribution in bearings) are systematically reviewed. Finally, several open problems in the research of reliability assessment of high-speed train bearing are addressed for future studies.
Keywords:
PDF (23547KB)元数据多维度评价相关文章导出EndNote|Ris|Bibtex收藏本文
本文引用格式
王曦, 侯宇, 孙守光, 李强, 任尊松. 高速列车轴承可靠性评估关键力学参量研究进展 1). 力学学报[J], 2021, 53(1): 19-34 DOI:10.6052/0459-1879-20-200
Wang Xi, Hou Yu, Sun Shouguang, Li Qiang, Ren Zunsong.
引言
通过引进、消化、吸收和再创新, 我国在高速列车系统集成技术、转向架技术、车体技术和制造技术等方面已处于世界先进水平,具备研发当今最先进的高速列车并规模化制造大部分子系统的能力. 在"复兴号"中国标准动车组平台上,我国实现了车轮、车轴、齿轮箱、制动盘等轮轴系统核心部件的国产化. 然而,作为高速列车关键基础零部件之一的轴承, 其核心技术目前我国尚不完全掌握.图1展示了高速列车牵引传动系统中轴承的种类和布置情况. 如图1所示, 包括轴箱轴承、齿轮箱轴承以及牵引电机轴承在内的滚动轴承是高速列车牵引传动系统的关键基础零部件.高速列车高性能滚动轴承的自主设计理论及制造技术, 直接体现了国家高端制造的能力和水平[1]. 目前,全国高速铁路里程将达到3万千米以上, 高速列车保有量超过3000组标准列,关键轴承使用量达到30万套以上. 然而,高速列车轴箱轴承、齿轮箱轴承和牵引电机轴承全部依赖进口,主要由德国FAG、瑞典SKF和日本NTN等国外知名供应商垄断[2].轴承为寿命管理部件, 需定期更换, 如无国产化替代, 一旦被国外封锁"卡脖子",高铁列车将无法正常运行, 严重影响国民经济的健康高效发展和产业安全,我国急需开展高速列车轴承部件的自主化研究.
我国高速列车轴承目前要求的轴承寿命为240万千米, 检修周期为120万千米,但有些装配在我国CRH2和CRH3型高速列车的进口轴承在运行60~90万千米后即出现由疲劳引起滚道剥离的现象[3].这些故障的连锁反应增大了维修的工作量, 干扰列车运用和检修的正常秩序, 严重时甚至威胁列车运行安全. 对于进口轴承"水土不服"的问题说明轴承结构在实际线路环境中的承载、动力学行为以及润滑特性比现有设计工况中的情况要复杂恶劣得多.究其根本原因, 是我国高速列车运用条件极为复杂,表现为列车运用密度高、持续运行时间和运行里程长、隧道众多、路谱载荷丰富,我国特有的高速列车运用条件对轴承部件的疲劳性能提出了更高的要求.
图1
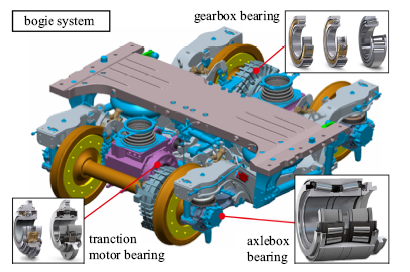
图1高速列车牵引传动系统轴承示意图
Fig.1Schematic diagram of bearings in high-speed train traction system
轴承涉及材料、力学、摩擦学、润滑等基础研究和交叉学科,是设计、制造、材料、检验等一系列关键技术自主创新能力的集中体现.国外多个著名轴承供应商积累了大量轴承实验和运用数据,但文献和技术资料高度保密, 我国在该领域的研究尚处于攻关阶段.国内洛轴和瓦轴等专业轴承制造企业联合国内高校和研究所对高速列车轴箱轴承进行了试制和试验,在轴承材料制备、结构设计与分析、高精度制造、台架试验考核等方面积累了一定经验.但是, 国内对高速列车轴承设计技术、制造技术、综合评估技术尚未开展系统性研究,正向设计体系不完整.轴承可靠性的基础理论和关键技术是我国轴承正向设计研发中的薄弱环节.目前在可靠性设计层面缺乏对轴承使用环境的深入分析,在可靠性评估层面仍需加强试验研究手段和测试技术,在可靠性理论层面缺乏复杂激励下滚动接触疲劳理论的应用指导,这些成为制约我国高速列车轴承自主化研究的瓶颈问题. 其中,高速列车轴承可靠性评估手段与技术旨在获得使用环境中轴承可靠性评估的关键力学参量,并以此推动复杂激励下轴承疲劳可靠性理论研究. 因此,可靠性评估层面的相关研究在解决轴承可靠性研究的瓶颈问题中起到了承上启下的关键作用.
本文首先对高速列车轴承在复杂使用环境中的典型失效模式进行总结概述,进一步分析导致高速列车发生这些典型失效的直接原因,从而论述在这样的运用情况下进行轴承可靠性评估需要关注轴承内部滚滑行为和载荷分布等关键力学参量.之后对轴承滚滑行为和载荷分布两个方面的研究进展进行综述.最后对高速列车轴承可靠性评估层面的研究进行总结与展望.
1 高速列车轴承典型失效模式
国际标准化组织(ISO)提出一种对轴承损坏和失效进行分类的方法(ISO 15243)[4]. 基于滚动元件接触表面和其他功能表面上可见的特征, 该标准识别6个主要的故障模式及与其造成的持续损坏子模式,并确定了每种故障类型涉及的机制. 按照这一标准, SKF公司在其铁路技术手册中统计了国外运营中实际发生的高速列车轴箱轴承和齿轮箱轴承损伤及破坏,对相应的损伤原因进行了分析, 并分别给出了损伤失效分析矩阵[5-6].其中, SKF给出的轴箱轴承损伤失效分析矩阵参见SKF铁路技术手册第一卷135页[5],本文中表1引用了SKF铁路技术手册第二卷中齿轮箱轴承的损伤失效分析矩阵[6].由于运行工况、环境因素、润滑条件、装配操作等原因, 轴箱轴承和齿轮箱轴承主要失效模式大体相同,均是表面材料的疲劳剥离、接触面的摩擦磨损以及疲劳裂纹. 同时, SKF还对这些轴承失效最常发生的部位进行了统计, 发现外圈滚道是最频繁发生损伤失效的部位[6].Table 1
Table 1Damage and failure matrix of high-speed train bearings[6]
![]() |
新窗口打开|下载CSV
相较于国外, 我国有着特有的高速列车运行工况, 我国高速列车运行环境更加复杂恶劣. 具体表现为:(1)列车运用密度高、持续运行时间和运行里程长. 以京广高铁为例, 京广高铁总里程超过2000 km, 每趟高铁列车要持续高速运行8 h以上; (2)线路条件复杂多样. 我国幅员辽阔, 一条高速铁路线可能穿过平原、丘陵、山区等众多地形, 同时线路隧道桥梁众多,这些多样的线路条件都给高速列车带来了复杂的外部激扰; (3)列车运行环境温差大. 冬季南北地区温差可能超过50$^\circ$C. 在这样复杂的运行环境中, 随着高速列车速度的不断提高, 来自轮轨相互作用产生的激扰频率范围已显著高于普通轨道机车车辆,如果考虑列车使用过程中轮对踏面的多边形磨耗、擦伤以及扁疤等变化, 将会使来自轮轨的激励更加复杂.这些因素的共同作用势必导致高速列车轴承部件的使用环境变得非常恶劣, 从而引起轴承的损伤及早期失效[3].通过对国内各型高铁轴箱轴承检修统计分析发现, 损伤部位及损伤形式多种多样,其中发生频率最高的损伤形式为轴承外圈滚道材料的剥离[7]. 图2中给出了一些高铁轴箱轴承外圈滚道材料剥离失效的典型案例. 这种外圈材料的疲劳剥离均集中发生在外圈滚道的轴承承载区. 承载区范围的外圈滚道持续不断的承受交变应力及冲击载荷,这使得外圈承载区成为了疲劳剥离的高发区域.
总的来说, 影响高速列车轴承可靠性的轴承损伤主要有两种形式:以摩擦磨损为主的损伤, 以及以疲劳裂纹、剥落为主的破坏,而运行工况、环境因素、润滑条件等都会不同程度的影响高速列车轴承可靠性.为避免轴承运行过程中发生损伤失效, 需要实时掌握轴承运行状态,利用可靠性相关关键力学参量进行使用轴承的可靠性验证与评估.
图2
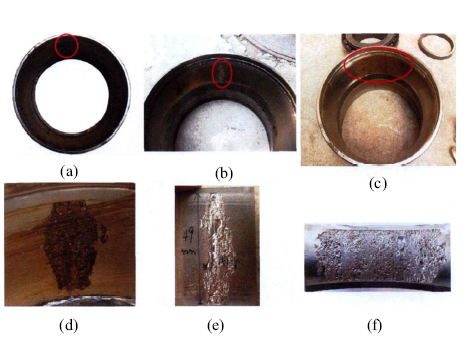
图2高铁轴箱轴承外圈材料的剥离.
(a)(c)(e)外圈失效试样.(b)(d)(f)分别为(a)(c)(e)红圈位置放大图[7]
Fig.2Spalling in outer ring of high-speed train axle-box bearings.
(a)(c)(e) Outer ring failure specimens, (b)(d)(f) Magnified view of red circle region in (a)(c)(e) respectively[7]
2 轴承可靠性评估关键力学参量
为了揭示复杂使用条件和轴承寿命之间的关系,需要获取一些关键力学参量来对高速列车轴承进行性能评估和寿命预测,以此推动复杂激励下轴承疲劳可靠性理论研究.一套完整的滚动轴承包括内外圈、滚动体和保持架,而这些部件之间的接触行为和相互作用力是轴承运转过程中的关键力学参量. 因此,造成高速列车轴承滚道磨损和疲劳剥落的直接原因可以分别追溯到轴承内部部件间的滚滑行为[8-10]和滚动接触载荷[11-13].一方面轴承内部的磨损是由于一定条件下轴承内部的打滑行为造成的, 另一方面,轴承内部变化的载荷及其分布是影响轴承疲劳可靠性的重要参数,交变的径向载荷及切向载荷不仅会对轴承的滚动接触疲劳性能造成影响[14],其中由滑动摩擦引起的切向载荷还会加剧轴承内部的磨损[15].打滑作为轴承内部的异常运动, 经常出现于轻载高速的工况下[16-17].在轻载高速的情况下, 轴承内部滚子无法实现运动学上纯滚动时的行星运动,从而出现保持架及滚子的打滑. 高速列车牵引电机最大转速可以达到6000 r/min,使得输入端轴承工作在轻载高速环境中. 而轴箱轴承虽然承受载荷较大,但由于外部激扰的原因, 在转动过程中也存在打滑现象,同时外部激扰的加强会增大轴箱轴承的打滑程度[18].打滑不仅加速滚动轴承的磨损, 破坏滚动轴承的旋转精度,还将导致滚动轴承及润滑油温度剧增[19], 局部高温破坏润滑油膜,导致滚动轴承寿命的缩短. 由于打滑对滚动轴承的工作性能影响的严重性,滚动轴承的打滑问题得到了轴承行业的高度重视, 已成为该领域的关键共性科学问题,如何预测、检测、减轻或消除打滑对轴承性能的影响成为高精度、长寿命轴承研发的技术瓶颈.
轴承内部的载荷分布是轴承最重要的运行参数之一[20].向心轴承内部的载荷包括径向载荷及切向载荷.其中径向载荷分布在轴承的径向刚度[21-23], 承载能力[24-25],疲劳寿命[26-28], 振动和动力学特征[29-30]等方面扮演着重要的角色. 同时,由于轴承内部的疲劳剥落或裂纹多发生在承载区最中间的外圈内滚道上[7],了解这一位置的接触载荷变化对可靠性评估和疲劳寿命预测有着重要意义.然而轴承内部径向载荷的计算与测试均存在一定困难. 理论计算方面,首先轴承内部的滚动体以不同的方式参与到载荷传递中,每个滚动体承受的载荷是不均匀的;其次轴承内部游隙及外加载荷与载荷分布之间存在复杂的关系[31-32].这些都使得在计算轴承内部径向载荷分布时要考虑大量因素. 载荷测试方面,受配合量影响的径向游隙以及随时间变化的动态外加载荷给轴承内部的载荷分布带来了很大的不确定性[32].此外轴承在位运行环境的空间限制[25,33]、轴承压装引起的预加载荷[26]以及实际测试中通常不允许对轴承进行较大改造的限制条件, 这些都增加了轴承内部径向载荷分布测试的难度.直接测量轴承内部单个滚动体与滚道之间的切向载荷通常也是非常困难的,但它与滚动体与滚道之间的总的摩擦力或摩擦力矩有关. 综上所述,研究并检测轴承运行过程中滚滑行为及载荷分布特性对轴承性能评估和寿命预测具有重要的科学价值和实际工程意义.
3 轴承内部滚滑行为研究
滚动轴承内部的运动关系比较复杂, 滚动体既要绕自身轴线旋转,又要绕轴承轴线公转; 在滚动的同时, 沿滚道还伴随着一定的滑动. 目前,滚动轴承的运动学分析广泛采用假设滚动体与内外圈之间均为纯滚动的简单运动学关系假设,来计算保持架转速和滚动体自转转速, 但这种假设只适用于低速重载情况[34].对于轴承滚子打滑的运动行为研究,Jones[35]提出的套圈控制理论在早期的轴承设计中得到相对简单且广泛应用.该理论假定滚动体在一个套圈滚道上无自旋运动仅发生纯滚动,采用拟静力学方法建立滚动体的力学平衡方程组.套圈控制理论一般适用于摩擦系数足够大的高速轴承[16],20世纪60年代高速轴承几乎都依此方法进行设计.之后Walters[36]假定滚动体的运动是稳定不变的,以此建立滚动体的运动微分方程, 提出了滚动体的动力学分析方法.但由于滚动轴承运转过程中载荷和转速的变化导致滚动体接触角和离心力的改变,使得滚动体运动稳定不变的假设不适用于承受外加激励的滚动轴承的动态过程[37].此后, 随着考虑影响因素的增多, 轴承滚滑行为特征的研究得到逐渐完善.Harris[34]采用拟静力学法建立了高速滚子轴承的打滑预测模型,研究了轴承载荷、转速以及滚动体数目对滚动轴承打滑的影响,这里他综合考虑滚动体受到的与内外圈之间的摩擦力、接触力、滚动体所受的离心力以及流体阻力等因素.Gupta[37]采用动力学分析方法建立了止推角接触轴承中球的6自由度运动微分方程,考虑了弹流润滑的影响, 研究了球的瞬态运动行为,实现了润滑状态下轴承的打滑仿真.Hirano[38]通过实验研究了轴向载荷下角接触球轴承球的运动及打滑发生的条件.试验通过测量磁化球的磁通量的改变来进行,结果表明当轴向载荷和离心力之比小于10时, 轴承内部将发生打滑.Liao等[39-41]通过对球轴承进行几何分析和力平衡分析,同时考虑离心力的影响, 获得了球的接触力和接触角,然后利用Hirano法则[38]研究了球轴承在径向和轴向载荷同时作用下的打滑行为.Boness[42]研究了影响轴承内部保持架和滚动体滑动的因素,并提出了用于防止高速角接触球轴承中滚动体和保持架打滑所需的最小轴向载荷的经验公式.Ghaisas等[43]为仿真所有滚动体的运动, 提出了圆柱滚子轴承6自由度模型,研究了内圈转速的变化、不对中、滚子大小和保持架的不对称性对保持架运动的影响.结果表明, 在轻载高速情况下,保持架的不稳定性是滚子与内、外圈间隙及滚子与保持架兜孔间隙的函数.Wang等[44]发展了一套动态模型,研究了角接触球轴承轴向载荷、转动速度等对轴承内部滚子打滑的影响,并讨论了打滑状态下轴承内部滚动体和滚道接触力的变化. 李军宁等[8,19,45]进行了一系列实验,研究了不同滑差率下打滑引起的温升效应以及接触面温度变化对打滑行为的影响.涂文兵等[17,46]提出了滚动体咬入轴承承载区的动力学模型,并讨论了打滑状态对轴承运行振动噪声的影响.
针高速列车轴箱轴承, 查浩等[18]在车辆与轨道耦合动力学模型基础上,考虑轴承与列车耦合运动关系,建立了6自由度滚子和6自由度保持架的双列圆锥滚子轴承模型,研究了高速动车组轴箱轴承在有无轨道激扰的情况下内部动态打滑情况.其模型如图3所示. 在车速300 km/h, 轨道随机激扰采用实测的"京津谱"激扰时,
轴箱轴承保持架打滑情况如图4所示. 结果表明, 不论是否有外加轨道激扰,
图3
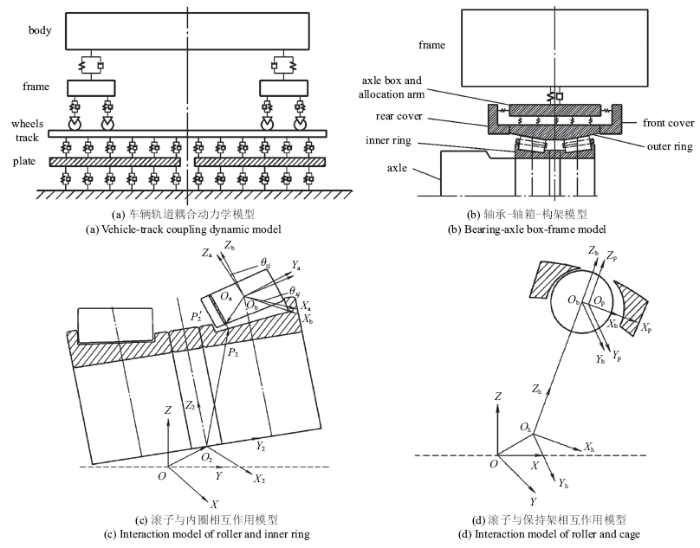
图3包含轴箱轴承的车辆-轨道系统动力学模型[18]
Fig.3Vehicle-track system dynamic model including the axle box bearing[18]
图4
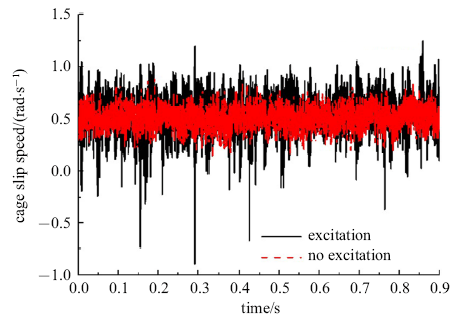
图4有无轨道激扰情况下轴箱轴承保持架打滑速度对比[18]
Fig.4Comparison of cage slip speed of axle box bearing with or without track excitation[18]
轴承在高速运行时内部都存在一定的打滑现象. 另一方面, 在轨道激扰条件下,保持架打滑速度的均值略大于无激扰条件下保持架打滑速度的均值,且动态变化幅度上前者明显大于后者, 说明激励会使轴承内部发生更严重的打滑现象.
在滚滑行为检测方面,之前的研究采用的方法按照直接测量的物理量的不同可以分为三类,即电磁传感器法、光学传感器法和振动传感器法.Boness[47]利用磁传感器和电子脉冲计数器来监测保持架和滚子转速,进而得到轴承内部保持架及滚动体的滚滑状态.O'Brien等[48]通过带有磁性拾取器的保持架铆钉来获得保持架速度,从而进行滚滑行为表征. Qu等[49]运用改进的磁巴克豪森噪声技术,提出了一种用于检测轴承钢滑动损伤的无损检测方法.Ford等[50]通过记录轴和保持架上的逆向反射标记的脉冲,用光学方法测量轴和保持架的速度并计算得到保持架打滑率.Selvaraj等[51]在研究轴承内部保持架及滚动体打滑影响因素时,使用了3个由光电传感器和光栅盘组成速度传感器来分别获得内圈,保持架和滚子的速度. Prashad[52]为检测轴承内部缺陷,测量了轴承的加速度信号, 并使用信号的频率表征保持架滑移,研究了保持架打滑对缺陷检测的影响.Markho等[53]应用激光多普勒仪测量了保持架和滚子速度.Han等[54]在保持架上黏贴反射板,并使用激光转速计确定保持架转速以及保持架滑动.Li等[55]搭建了轴承部件打滑损伤检测试验台,通过对加速度信号进行快速傅里叶变换和离散小波变换,分析了径向载荷、温度分布、打滑率等因素对滚子滚道打滑损伤的影响.
尽管上述方法和实验系统可以有效地用于检测保持架打滑并探究其影响因素,但由于这些方法大都需要对轴承本身进行一定改造或者对传感器的布置空间有较大要求,这些方法都仅适用于实验室环境中.目前研究及工程应用中缺乏对实际使用中轴承的滚滑行为进行有效监控的方法,这也是高速列车轴承在位测试技术发展的关键问题.
针对上述问题, 提出了一种基于应变响应检测的轴承滚滑行为在位检测方法,这种方法通过在轴承外圈表面引入一个槽口并在槽口处粘贴应变片来获取轴承运行时的打滑情况.同时设计了原理性实验对这一方法的有效性进行了验证[56].图5(a)和图5(b)展示了实验用的圆柱滚子轴承试样及轴承外圈开槽情况.实验中的轴承试验台被设计为能够同时测量圆柱滚子轴承外圈的应变以及轴和保持架的转速,如图5(c)所示. 保持架打滑不仅可以由速度信号进行表征,也可以由应变信号进行表征. 而在轴承使用状态下,应变信号比轴承内部部件的转速信号更容易获取.实验中基于应变信号获得的打滑率与基于速度信号获得的打滑率呈现很好的一致性(如图5(d)所示),这也证明了提出的基于应变响应的轴承内部滚滑行为检测方法的可行性.由于这种轴承滚滑行为在位检测方法还是需对轴承或轴承座进行微小改造,该方法在实际轴承使用环境中的应用效果还有待进一步研究和验证.
图5
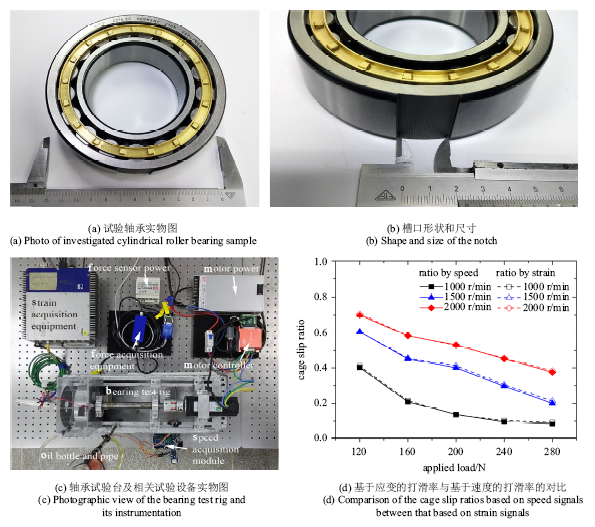
图5基于应变响应的保持架打滑检测方法
Fig.5Method for detecting the cage slip based on the strain response
4 轴承内部载荷分布研究
4.1 径向载荷
4.1.1 计算方法在轴承内部载荷分布计算方法方面, Stribeck[57]的工作被认为是最早的研究.以Hertz接触理论为基础, Stribeck[57]在1901年建立了轴承静力学模型,给出了游隙为零且承受单一径向载荷的球轴承以及向心滚子轴承的最大滚子负载和径向外载荷之间的关系.由于径向间隙为零, 轴承的载荷区大小范围为$\pi $. 基于这个假设,Stribeck推导出一个计算滚动体上最大载荷的方程.Sj$\ddot{o}$ vall[58]提出了一种积分方法来计算载荷分布.在Sj$\ddot{o}$ vall的研究中, 基于在载荷区域中存在大量具有极小直径的滚动元件的假设,用于计算载荷分布的表达式中的总和被积分代替. 这个积分被称为Sj$\ddot{o}$ vall积分.Sj$\ddot{o}$ vall指出,这一积分受轴承接触类型以及径向游隙与内圈径向跳动位移之比的影响.为了确定随上述比例变化的积分值, Sj$\ddot{o}$ vall将椭圆积分的变量引入到计算中.以Sj$\ddot{o}$ vall积分为基础,Harris[20]发展了一个适用于任何游隙情况的轴承内部载荷分布计算综合模型.在这个模型中, Harris提出了载荷分布因子的概念,同时利用数值方法对Sj$\ddot{o}$ vall积分的值进行了调整并在后来的研究中被广泛采用[59-60].Oswald等[32]、Houpert[61]和田荣[62]各自利用多项式及分段函数对
Sjov$\ddot{a}$ ll积分进行了拟合, 简化了轴承内部载荷分布积分的计算方法.Tomovi$\acute{c}$[31,63]定义了一个用于衡量边界外部径向载荷的系数,以确定参与外部载荷传递的滚动体数量.Ren等[64]提出了不需要计算接触刚度的载荷分布计算模型. 在此模型中,仅使用轴承的变形和几何参数就可以确定径向载荷分布.Aschenbrenner等[65]提出了一种可以考虑轴承几何尺寸偏差及其统计参数的圆柱滚子轴承径向载荷分布和滚动体径向偏移的计算方法.魏延刚等[66]比较了离散法、积分法和有限元法这3种方法在轴承内部载荷分布计算方面的优劣性.Chen等[67]研究了滚子尺寸偏大对圆柱滚子轴承内部载荷分布的影响,分别考虑了1个滚子偏大、多个滚子偏大和全部滚子偏大的情况,发现仅1个滚子偏大时, 轴承内部载荷分布的改变最明显.Zhou等[68]建立了一种载荷分布计算模型,用于研究滚动体尺寸的微小差异对轴承内部载荷分布的影响,其结果表明轴承内部滚动体较小的尺寸差异会对明显改变轴承内部载荷分布.
尽管所有方法都能够计算径向载荷分布,但是这些方法大多数都有各自特定的应用条件. 例如,在Stribeck的方程[57]中假定载荷区为$\pi$并固定,这意味着Stribeck的方法不适用于非零游隙轴承的计算. Tomovi$\acute{c}$[31,63]和Ren等[64]提出的离散模型不能用于获得承荷区的角度范围.在这些径向载荷分布的所有计算方法中, 由于适用范围广,由Sj$\ddot{o}$ vall提出并由Harris改进了的径向载荷分布积分得到了研究者们的广泛认可与使用.但是, 使用现有的径向载荷分布积分值来计算载荷分布仍存在一些问题. 首先,在通过Sj$\ddot{o}$ vall积分的原始值或改进值获得的载荷分布结果中,所计算的各滚动体载荷的垂直分量之和与外部径向载荷不完全相等[20].这表明通过现有的径向载荷分布积分值来计算径向载荷分布是不准确的,并且初始误差将引入基于载荷分布的一系列相关计算中. 其次,当载荷分布系数大于0且小于0.1时,之前的研究没有给出径向载荷分布积分的值或计算积分的方法,这表明积分方法不适用于承载区较小的情况. 而同时,承载区较小时的载荷分布对于确定滚动体的打滑行为[17]和轴承疲劳寿命[27]来说很重要.
上述计算方法都可以较好地获得轴承内部的静态载荷分布,也可以用于高速列车轴承静载状态下的载荷分布求解.而针对轴承内部动态载荷分布情况,尤其是对高速列车轴承这样复杂使用环境中的承受内外系统激励的轴承来说,动力学模型则是解决轴承内部动态载荷及其分布计算的有效方法.Petersen等[21-22]和Sawalhi等[69-70]将轴承当作质量–弹簧–阻尼系统处理,通过非线性多体动力学模型计算得出了轴承内部的动态载荷分布.Singh等[71]建立了复杂的显式动力学有限元模型,用来计算轴承内部的动态接触力. 针对高速列车轴箱轴承系统,考虑高速列车轴箱轴承复杂的使用环境,查浩等[72]基于包含轴箱轴承的车辆-轨道动力学模型(如图3所示),研究了轨道激扰和不同列车运行速度下滚子滚道接触载荷特征. 研究结果表明,轨道激扰对承载区内的载荷分布影响不大,但是会使非承载区内滚子与外圈滚道发生接触,从而增大非承载区内的分布载荷(如图6(a)所示).另外对外圈受到的接触载荷最大的区域进行研究发现, 随着速度的增大,轨道激扰造成的振动越大, 滚子滚道接触载荷数据波动越大(如图6(b)所示).基于考虑轴承的车辆轨道耦和动力学模型的载荷分布结果,查浩等[73]还对高速列车轴箱轴承运行过程中的累计损伤进行了计算, 对轴承运行疲劳寿命进行了预测.
图6
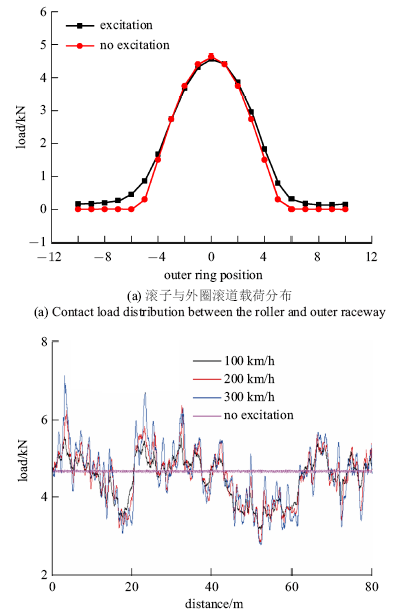
图6轨道激扰和运行速度对轴箱轴承内部载荷分布和动态接触载荷的影响[72]
Fig.6Effect of track excitation and running speed and on load distribution and dynamic contact load of axle box bearing[72]
4.2.2 测试技术
在轴承内部载荷分布测试方法方面, 20世纪80年代,Frayer等[74]发明了一种使用延性线插入件测量轴承载荷分布的方法.这种方法可以通过直接测量变形来获得圆柱或圆锥滚子轴承内部载荷分布. 之后,Bailey等[75]采用这种方法获得圆锥滚子轴承的载荷分布,并通过修改圆锥滚子轴承外圈几何形貌进一步优化了这种分布. 近年来,一些研究者利用不同类型的传感器研究了滚动轴承内部载荷分配问题[26,33,76-78].Monahan等[78]将压电薄膜传感器布置在轴承、轴承支撑结构,或者机械连接到轴承的单独部件上以监控轴承的性能.这个发明可以检测由压力波引起的轴承或支撑结构的弹性变形,并进一步预测滚子轴承的失效. Kwapisz等[77]开发了一种应变式的仪表轴承, 用于测量轴承支撑的力,可以获得随双列球轴承中的角位置变化的外圈载荷.Nagatomo等[26]提出了一种仅使用一个应变片就能获得轴承内部动态载荷分布的方法.他在轴承内圈内表面引入一个凹槽,并将光纤应变传感器布置在轴承内圈的凹槽内表面. 随着轴承的旋转,光纤应变传感器可以检测到变化的应变信号,检测到的应变信号在轴承每转中是不同的,这是因为在槽口位置处滚子通过内滚道的方位角位置在每个内圈转动周期内通常是不相同的.然后, 内圈每转一圈测量的叠加应变波的包络正好是轴承承载区内应变的分布.当轴承座的形状和载荷支撑方法变化时, 通过这种方式可以获得不同的载荷分布,从而证实了轴承寿命受负载分布的显着影响.Marconnet等[33]提出将电容探头放在轴承外圈内部,以确定轴承在外圈上传递的载荷. 对于一个16滚子的圆柱滚子轴承,他在外圈中等间距加工了16个电容探针外壳,使得电容探针有足够的空间形成具有可变间距的电容器.当负载通过滚子传递到外圈时, 由负载引起的变形改变了电容器的电容,从而导致测量电压的变化. 因此,可以通过电压测试以及电压和力之间的关系来识别分布在每个滚子上的载荷.但对比实际实验获得的载荷分布和理论载荷分布可以发现,Marconnet等的方法获得的载荷分布和相同工况下轴承的理论载荷分布差别较大,这可能是由于Marconnet等没有完整考虑各个测点处电压和载荷传递关系所导致的.Liu等[76]建立了单列四点接触式回转支承轴承的有限元模型,以研究轴承中的载荷分布, 并在静态加载条件下进行了实验验证了有限元结果.实验中应变传感器安装在内圈的内圆周上以获得载荷分布.
然而,现有的方法和设备都是在实验室而不是轴承的实际运行环境中设计、开发和使用的,更不可能直接用于高速列车轴承的载荷测试, 这是由下面几个原因造成的:(1)几乎所有轴承都必须进行不同程度的改造, 以便为传感器创造足够的空间,这些改造主要是引入外圈或内圈,而这种改造会一定程度上改变轴承内部的载荷分布情况;(2)现有的测试方法大多关注轴承内部静态载荷分布的情况,很少有研究关注轴承外滚道承载区某特定位置的动态载荷变化,而外滚道承载区这种动态载荷的变化恰恰是导致轴承疲劳剥离的重要因素.
针对上述问题, 为获得实际使用状态下的高速列车轴箱轴承承受的动态载荷,刘德昆等[79-80]提出了一种间接获得轴箱轴承径向及轴向载荷的测试方法.该方法基于轴箱弹簧及转臂载荷测试技术,将轴箱轴承所受的轴向载荷用转臂载荷来近似, 而径向载荷可近似由下式表达
式中, $F_{r} $为轴箱轴承所受径向力; $F_{s} $为轴箱弹簧作用载荷; $F_{t}$为牵引制动载荷; $F_{z}$为转臂效应载荷, 是转臂受到轴向载荷作用导致轴承偏转产生的. 实际测试中利用应变片传感器化的轴箱轴承及转臂如图7所示. 实际测试前, 先利用试验台对测力传感器进行标定, 得到相应的应变-载荷转换系数,之后就可以根据实测的应变信号转换得到轴箱弹簧和转臂所受的各种载荷. 利用这种方法, 对动车组动力转向架轴箱进行线路实测,获取了典型线路段弹簧和转臂的载荷时间历程, 并以测试载荷为基础对轴箱轴承使用可靠性进行了评估.这种测试方法虽然获得了实际使用环境中轴箱轴承的载荷, 但由于这种载荷是通过间接的形式获取的, 其准确度会受到一定程度的影响,使其无法准确描述运转过程中轴承内部的载荷分布.
为实现实际使用环境中轴承载荷的准确获取,又提出了一种通过检测外圈外表面的应变响应的轴承内部载荷分布直接测试方法.为了获得不同滚动体上不均匀的载荷分布, 必须测量通过每个滚子传递的载荷. 为此,一系列凹槽被引入到轴承座的内表面, 如图8(a)所示, 为应变片提供了足够的空间,从而实现检测轴承外圈的应变信号. 由于存在槽口, 外圈的相应部分可以视为梁结构.根据梁理论, 每当有一个滚子在凹槽位置上滚动时,就会在外圈的外表
图7
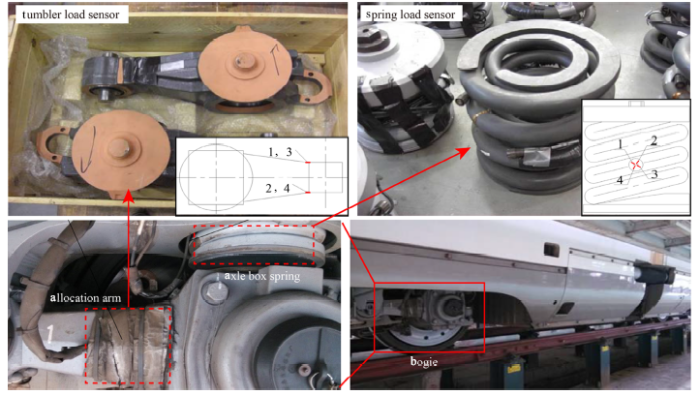
图7线路测试中的轴箱弹簧及转臂传感器[79]
Fig.7Axle box spring load sensor and tumbler load sensor for the track test[79]
图8
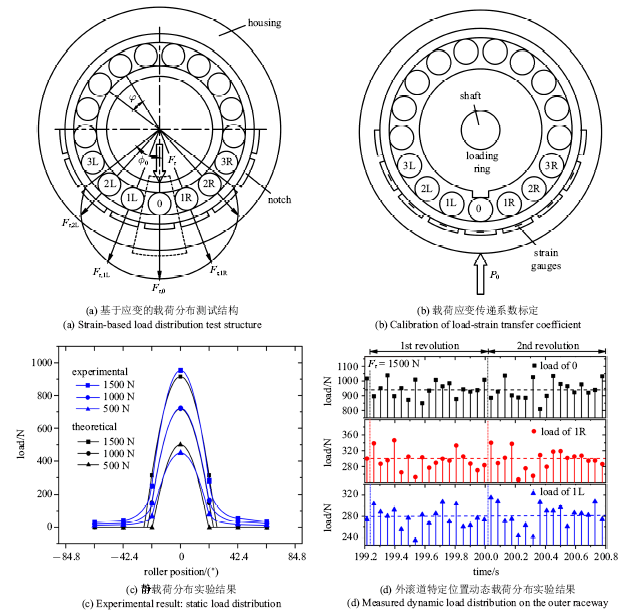
图8基于应变的载荷分布测试方法示意图及实验测试结果
Fig.8Schematic diagram and experimental results of the bearing load distribution measurement method based on the strain response
面产生应变响应. 在图8(a)所示的状态下, 测得的应变与载荷分布之间的关系可以借助一个刚度矩阵来表示
式中$\alpha $和$\beta $代表诸如0, 1R, 1L, 2R, 2L等的滚子编号. $\varepsilon_{\alpha }$是测试得到的应变分布, $F_{\beta }$为滚动体上的载荷分布, $k_{\alpha -\beta } $代表仅由滚子位置$\beta$处的单位载荷在滚子位置$\alpha$处造成的应变值,这个由载荷到应变的转换系数可以通过图8(b)所示的使用特制加载轴的标定实验来获取.这样只要测试得到了轴承外圈的应变分布并得到了刚度矩阵,轴承内部的载荷分布就可以按照式(3)计算得到
这种对轴承座的改造方式不会改变轴承内部的载荷分布,能够准确地获取圆柱滚子轴承的静态和动态载荷分布, 而无需对轴承本身进行修改.原理验证性实验测得的轴承内部静态和动态载荷分布结果分别如图8(c)和图8(d)所示.由试验轴承座测得的静载荷分布与理论结果吻合良好, 这证明了该方法的有效性.此外, 实验获得了轴承旋转过程中施加在外滚道加载区域中特定位置的实时交变载荷.接触力的动态变化可归因于由于滚子之间的差异而导致的滚子与外滚道之间接触刚度的变化.所提出的方法为滚动轴承的结构健康监测提供了有效的途径.
4.2 摩擦力矩
4.2.1 计算方法在轴承内部摩擦力矩计算方法方面, 国外各大轴承厂商都发展了自己的计算方法.Timken公司的Houpert解释了如何计算滚珠轴承和圆锥滚子轴承的轴承扭矩[81],并基于该计算方法, 进行轴承扭矩的比较, 用于指导在不同应用环境中选择最佳轴承.而且, Houpert已经开发了一种数值计算方法和一种名为SYSx的数值工具[82].他认为轴承内部摩擦力矩可分为弹流滚动阻力、曲率效应、弹性阻力和自旋效应四部分,并提出了每一部分的计算方法.Timken工程手册[83]分别给出了各种轴承内部摩擦力矩的计算方法,手册中认为不同类型的轴承内部摩擦力矩的组成有所差别.NSK轴承手册[84]中认为轴承内部的动态扭矩由两部分组成: 载荷项和速度项,并分别给出了载荷项和速度项的计算公式.SKF[85]为了准确计算滚动轴承中的总摩擦力矩,考虑了以下来源及其摩擦学影响:(1)滚动摩擦力矩和高速饥饿和入口剪切加热的最终影响;(2)滑动摩擦力矩及其对润滑质量的影响; (3)密封件的摩擦力矩; (4)拖曳损失, 搅动,飞溅等的摩擦力矩.Koyo公司的Matsuyama[86]针对圆锥滚子轴承提出了一个计算内部摩擦力矩的无量纲公式,定义了无量纲速度、材料及载荷参数. 此外,还有许多****针对不同工况下的不同轴承内部的摩擦力矩提出了相应地计算方法.Aihara[87]推导了轴向载荷作用下的圆锥滚子轴承内部摩擦力矩的计算公式.Aihara认为圆锥滚子轴承内部摩擦力矩由四部分组成: (1)滚子与滚道之间的滚动摩擦;(2)滚子端部与内圈挡边的滑动摩擦; (3)滚子与保持架之间的滑动摩擦;(4)由润滑油黏度引起的拖拽力.Kanatsu等[88]考虑了聚合物润滑剂及轴向载荷作用下的深沟球轴承内部摩擦力矩的计算方法.Balyakin等[89]推导了考虑内圈偏心的滚动轴承内部摩擦力矩计算公式,并讨论了轴承内圈偏心对内部摩擦力矩的影响.
总的来说, 虽然上述方法都能获得一定条件下特定轴承的内部摩擦力矩,但是在滚动轴承内部摩擦力矩计算方面还有些问题没有解决:(1)上述大多方法的推导相对独立, 对于同一工况下的同一种轴承,不同的方法得到的结果不尽相同;(2)现有方法基本上都是针对轴承纯滚动情况下提出的,目前还没有一套针对轴承打滑状态下的内部摩擦力矩的完整计算方法.
4.2.2 测试技术
在轴承内摩擦力矩测试方面, Matsuyama等[86]建立了一个试验台,它可以分别测量圆锥滚子轴承中滚道接触和挡边接触产生的摩擦力矩. 其中,挡边与内圈分离, 以获得由应变仪给出的纯挡边接触中的摩擦力矩, 根据平衡力矩法从载荷传感器给出总摩擦力矩.来自Timken公司的Gradu[90]比较了圆锥滚动轴承和浮动球轴承的摩擦力矩.通过测试台测量扭矩, 用于由Timken建立的轴承效率测量体系.Biyiklioglu等[91-92]开发了一种新的试验装置和方法,用于动态载荷下轴颈轴承的摩擦力测量.测试装置的机械系统和测量单元设计用于确定轴颈和轴承系统在不同速度,载荷和润滑条件下的动态载荷下的摩擦性能. 为了测量滚动轴承的摩擦力矩,Cousseau等[93-94]使用了改进的四球机,其中四球布置由滚动轴承组件代替. 该机器经过改造, 仅适用于轴向加载的滚动轴承.实验得到了不同类型润滑脂的推力球轴承的摩擦力矩,证明了润滑剂对摩擦力矩的影响.Hammami等[95]使用上述相同的测试机器给出了圆柱推力轴承和圆锥滚子轴承的扭矩测量.Mihaela等[96]使用CETR UMT2摩擦仪测试了混合润滑工况下推力球轴承内部摩擦力矩,讨论了不同转速、不同润滑条件对推力球轴承内部摩擦力矩的影响,并将实验数据与模型计算结果进行了对比.Popescu等[97]开发了一种实验方法,以确定在干摩擦条件和非常低的轴向载荷下运行的改进型角接触球轴承中的摩擦扭矩.上述研究工作大多是针对推力轴承或承受轴向载荷的轴承开展的摩擦力矩测试,对于承受径向载荷的轴承内部摩擦力矩测试来说,由于径向载荷通常通过接触的方式来施加, 这会对测试轴承引入干扰力矩,从而影响扭矩的测试. 为了解决这一问题,Bouyer等[98]利用静压轴承代替了径向载荷施加时的机械接触来进行外加载荷传递,从而利用扭矩计和轴承套圈相连, 实现了径向载荷下的轴承内部摩擦力矩的测试.此外, Kim等[99]基于平衡力矩原理提出了测量微型轴承摩擦系数的线张力法,并设计了如图9所示的实验装置. 实验中线材绕过轴承套圈并固定在适当的位置,配重在线材的一端连接, 以向轴承施加径向载荷, 而重量传感器在另一端连接.当电机带动主轴沿逆时针方向旋转时, 轴承会产生摩擦力,并且砝码会向钢丝施加初始张力. 根据平衡力矩原理,重量传感器的数值变化与轴承套圈外径的乘积就是轴承内部的摩擦力矩.陈会航等[100]在Kim等[99]提出的线张力法的基础上做了改进,用两个力传感器代替了原方法中的配重和重量传感器,从而实现了径向外加载荷下对正常尺寸大小向心滚动轴承的摩擦力矩测试.陶润等[101]设计了一套用于测量径向载荷下小型轴承摩擦力矩的实验装置,并利用这套装置对某乘用车发动机传动系统中典型滚动轴承在不同径向力和转速下的摩擦力矩进行了测量.针对更大尺寸的轴承, Wittenberghe等[102]开发了一种新的测试装置,以研究大型复合轴颈轴承在往复运动和静态或动态载荷下的摩擦学行为.这种新的测试装置可以仅测量测试轴承的摩擦力矩,而不会受到主轴支承轴承的任何干扰.
图9
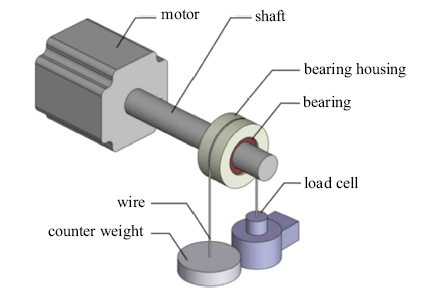
图9基于平衡力矩法的径向轴承摩擦力矩测试装置[99]
Fig.9Bearing friction torque testing device based on balanced torque method[99]
总的来说, 虽然现有的测试方法都能在一定条件下获得轴承内部的摩擦力或摩擦力矩,但现有的测试很少关注轴承内部摩擦力的分布情况,没办法准确获得轴承内外圈滚道上某点的摩擦力分布和变化情况.而作为评估轴承可靠性的关键力学参量之一,轴承内部摩擦力的分布即滚道某点的切向载荷的准确获取是能否对轴承可靠性进行准确评估的关键所在.另外, 由于实际使用环境空间的限制,现有的轴承内部摩擦力矩测试方法局限于实验室测试,针对高速列车轴承这种复杂使用环境中的轴承的摩擦力矩的测试手段还有待开发.
5 结论与展望
高速列车轴承可靠性评估作为高速列车轴承正向设计中承上启下的关键部分,旨在借助一些测试技术获得复杂使用环境中轴承可靠性评估的关键力学参量,并以此推动复杂激励下轴承疲劳可靠性理论研究. 其中,针对轴承可靠性评估所需关键力学参量特征和获取方法的研究对于评估高速列车轴承可靠性、检测轴承运行状态来说十分重要.本文从概述我国高速列车轴承复杂的使用环境及运用中的主要失效模式出发,分析了高速列车轴承可靠性评估所需的关键力学参量,强调了轴承内部滚滑行为和载荷分布这些关键力学参量在评估轴承寿命、进行轴承运行状态检测方面的重要意义.回顾了目前为止轴承内部滚滑行为和载荷分布相关的研究工作,重点总结了这些关键力学参量获取方法方面的研究进展.但是由于高速列车轴承使用环境的限制,尽管目前已经在轴承关键力学参量测试技术方面取得了一定成果,但这些成果大多还局限于实验室条件下的轴承力学参量测试,关于实际使用环境中的轴承可靠性评估关键力学参量特征和测试手段的研究仍需大力发展.
具体来说,针对轴承内部滚滑行为和载荷分布等高速列车轴承可靠性评估关键力学参量的研究还需在以下几方面大力加强:
(1) 结合高速列车轴承使用环境结构特征,开发适用于轴承使用状态的滚滑行为和载荷分布检测方法.
(2) 发展轴承滚道动态径向载荷与切向载荷分布测试与检测技术,实现轴承滚道失效高危位置交变载荷的实时测试, 从而实现轴承疲劳可靠性评估.
(3) 由于线路条件复杂多变, 载荷激励耦合作用,需要利用实验室台架实验分别研究内、外激励对轴承性能的影响规律.
参考文献 原文顺序
文献年度倒序
文中引用次数倒序
被引期刊影响因子
[本文引用: 1]
[本文引用: 1]
[本文引用: 1]
[本文引用: 1]
[本文引用: 2]
[本文引用: 2]
[本文引用: 1]
[本文引用: 2]
[本文引用: 5]
[本文引用: 4]
[本文引用: 4]
[本文引用: 2]
[本文引用: 1]
[本文引用: 1]
[本文引用: 1]
[本文引用: 1]
[本文引用: 1]
[本文引用: 2]
[本文引用: 3]
[本文引用: 6]
[本文引用: 6]
[本文引用: 2]
[本文引用: 3]
[本文引用: 2]
[本文引用: 1]
[本文引用: 1]
[本文引用: 1]
[本文引用: 2]
[本文引用: 4]
[本文引用: 1]
[本文引用: 1]
[本文引用: 1]
[本文引用: 1]
[本文引用: 3]
[本文引用: 3]
[本文引用: 3]
[本文引用: 2]
[本文引用: 1]
[本文引用: 1]
[本文引用: 2]
[本文引用: 2]
[本文引用: 1]
[本文引用: 1]
[本文引用: 1]
[本文引用: 1]
[本文引用: 1]
[本文引用: 1]
[本文引用: 1]
[本文引用: 1]
[本文引用: 1]
[本文引用: 1]
[本文引用: 1]
[本文引用: 1]
[本文引用: 1]
[本文引用: 1]
[本文引用: 1]
[本文引用: 1]
[本文引用: 1]
[本文引用: 1]
[本文引用: 1]
[本文引用: 3]
[本文引用: 1]
[本文引用: 1]
[本文引用: 1]
[本文引用: 1]
[本文引用: 1]
[本文引用: 1]
[本文引用: 2]
[本文引用: 2]
[本文引用: 1]
[本文引用: 1]
[本文引用: 1]
[本文引用: 1]
[本文引用: 1]
[本文引用: 1]
[本文引用: 1]
[本文引用: 1]
[本文引用: 3]
[本文引用: 1]
[本文引用: 1]
[本文引用: 1]
[本文引用: 1]
[本文引用: 2]
[本文引用: 1]
[本文引用: 2]
[本文引用: 3]
[本文引用: 3]
[本文引用: 1]
[本文引用: 1]
[本文引用: 1]
[本文引用: 1]
[本文引用: 1]
[本文引用: 1]
[本文引用: 1]
[本文引用: 2]
[本文引用: 1]
[本文引用: 1]
[本文引用: 1]
[本文引用: 1]
[本文引用: 1]
[本文引用: 1]
[本文引用: 1]
[本文引用: 1]
[本文引用: 1]
[本文引用: 1]
[本文引用: 1]
[本文引用: 1]
[本文引用: 4]
[本文引用: 1]
[本文引用: 1]
[本文引用: 1]
[本文引用: 1]
[本文引用: 1]