薛克敏1,杨卫正1,代光旭2,李萍1
(1. 合肥工业大学 材料科学与工程学院, 合肥 230009; 2. 合肥工业大学 工业与装备技术研究院,合肥 230009)
摘要:
针对汽车双质量飞轮驱动齿盘外缘为原始板厚的3~5倍的特点,以SIMUFACT软件分析为手段,对双质量飞轮驱动齿盘多道次旋压增厚成形工艺进行研究.基于旋压增厚成形工艺的理论分析,设计出多道次旋压增厚模具并建立了旋压增厚成形有限元模型.以第1道次旋压增厚成形为例,分析了成形过程中应力场分布及板坯的变形情况.同时在板坯表面设置4个测量点分析第1道次旋压增厚成形过程中金属的流动规律,从而总结出第2至5道次的旋压增厚成形规律.以旋轮进给速度、摩擦系数、芯模转速为自变量,进行三因素三水平正交试验,获得最大成形载荷、增厚程度数据.结合灰色理论对双质量飞轮驱动齿盘旋压增厚成形工艺参数进行了优化,在CDC-4S80旋压机上进行了试验,结果表明:在旋压增厚过程中板坯所受径向力最大、切向力次之、轴向力最小;较小的摩擦系数与旋轮进给速度有利于提高零件的成形质量;通过物理试验成功将板坯外缘由3 mm增厚到10.5 mm,验证了该成形方案与灰色系统理论优化的可行性.
关键词: 双质量飞轮驱动齿盘 旋压增厚成形 金属流动 增厚程度 灰色系统理论
DOI:10.11918/j.issn.0367-6234.201708098
分类号:TG306
文献标识码:A
基金项目:江苏省科技计划项目(BA2016047);江苏省南通市科技项目(GY22015008)
Study on spinning thickening forming process of double mass flywheel drive plate
XUE Kemin1,YANG Weizheng1,DAI Guangxu2,LI Ping1
(1.School of Material Science & Engineering, Hefei University of Technology, Hefei 230009, China; 2. Institute of Industry & Equipment Technology, Hefei University of Technology, Hefei 230009, China)
Abstract:
According to the rim of dual mass flywheel (DMFW) drive plate is 3~5 times thicker than the original thin plate, such formation of multi-steps spinning thickening forming process was investigated based on the SIMUFACT software. According to the analysis of spinning thickening deformation, the mould and the finite element model of spinning thickening forming were established. Taking the 1st step spinning thickening forming as an example, the stress field distribution and the deformation of the sheet metal during the forming process were analyzed. Meanwhile, 4 measuring points on the surface of the plate were used to analyze the metal flowing in the 1st step spinning thickening forming process, and such forming rules of the steps ranging from 2 to 5 were summarized. Taking the roller feed speed, friction factor and rotation rate as independent variables, Three factors and three levels orthogonal experiments were carried out to obtain the maximum forming load and thickening rate data. The grey system theory was used to optimize the process parameters of the spinning thickening forming of DMFW drive plate, Such experiments were conducting on the CDC-4S80 spinning machine. The results show that the radial force is the largest, the tangential force is the second, and the axial force is the smallest, in the process of spinning thickening forming, ; The smaller friction and the roller feed rate can improve the quality of forming parts. The rim of the plate was thickened from 3 mm to 10.5 mm by physical test, which verifies the feasibility of the forming process and the grey system theory.
Key words: DMFW drive plate spinning thickening forming metal flowing thickening rate grey system theory
薛克敏, 杨卫正, 代光旭, 李萍. 双质量飞轮驱动齿盘旋压增厚成形工艺研究[J]. 哈尔滨工业大学学报, 2018, 50(5): 145-151. DOI: 10.11918/j.issn.0367-6234.201708098.

XUE Kemin, YANG Weizheng, DAI Guangxu, LI Ping. Study on spinning thickening forming process of double mass flywheel drive plate[J]. Journal of Harbin Institute of Technology, 2018, 50(5): 145-151. DOI: 10.11918/j.issn.0367-6234.201708098.

基金项目 江苏省科技计划项目(BA2016047);江苏省南通市科技项目(GY22015008) 作者简介 薛克敏(1963—), 男, 教授, 博士生导师;
李萍(1973—), 女, 教授, 博士生导师 通信作者 李萍, li_ping@hfut.edu.cn 文章历史 收稿日期: 2017-08-25
Contents -->Abstract Full text Figures/Tables PDF
双质量飞轮驱动齿盘旋压增厚成形工艺研究
薛克敏1, 杨卫正1, 代光旭2, 李萍1


1. 合肥工业大学 材料科学与工程学院, 合肥 230009;
2. 合肥工业大学 工业与装备技术研究院,合肥 230009
收稿日期: 2017-08-25
基金项目: 江苏省科技计划项目(BA2016047);江苏省南通市科技项目(GY22015008)
作者简介: 薛克敏(1963—), 男, 教授, 博士生导师;
李萍(1973—), 女, 教授, 博士生导师
通信作者: 李萍, li_ping@hfut.edu.cn
摘要: 针对汽车双质量飞轮驱动齿盘外缘为原始板厚的3~5倍的特点,以SIMUFACT软件分析为手段,对双质量飞轮驱动齿盘多道次旋压增厚成形工艺进行研究.基于旋压增厚成形工艺的理论分析,设计出多道次旋压增厚模具并建立了旋压增厚成形有限元模型.以第1道次旋压增厚成形为例,分析了成形过程中应力场分布及板坯的变形情况.同时在板坯表面设置4个测量点分析第1道次旋压增厚成形过程中金属的流动规律,从而总结出第2至5道次的旋压增厚成形规律.以旋轮进给速度、摩擦系数、芯模转速为自变量,进行三因素三水平正交试验,获得最大成形载荷、增厚程度数据.结合灰色理论对双质量飞轮驱动齿盘旋压增厚成形工艺参数进行了优化,在CDC-4S80旋压机上进行了试验,结果表明:在旋压增厚过程中板坯所受径向力最大、切向力次之、轴向力最小;较小的摩擦系数与旋轮进给速度有利于提高零件的成形质量;通过物理试验成功将板坯外缘由3 mm增厚到10.5 mm,验证了该成形方案与灰色系统理论优化的可行性.
关键词: 双质量飞轮驱动齿盘 旋压增厚成形 金属流动 增厚程度 灰色系统理论
Study on spinning thickening forming process of double mass flywheel drive plate
XUE Kemin1, YANG Weizheng1, DAI Guangxu2, LI Ping1


1. School of Material Science & Engineering, Hefei University of Technology, Hefei 230009, China;
2. Institute of Industry & Equipment Technology, Hefei University of Technology, Hefei 230009, China
Abstract: According to the rim of dual mass flywheel (DMFW) drive plate is 3~5 times thicker than the original thin plate, such formation of multi-steps spinning thickening forming process was investigated based on the SIMUFACT software. According to the analysis of spinning thickening deformation, the mould and the finite element model of spinning thickening forming were established. Taking the 1st step spinning thickening forming as an example, the stress field distribution and the deformation of the sheet metal during the forming process were analyzed. Meanwhile, 4 measuring points on the surface of the plate were used to analyze the metal flowing in the 1st step spinning thickening forming process, and such forming rules of the steps ranging from 2 to 5 were summarized. Taking the roller feed speed, friction factor and rotation rate as independent variables, Three factors and three levels orthogonal experiments were carried out to obtain the maximum forming load and thickening rate data. The grey system theory was used to optimize the process parameters of the spinning thickening forming of DMFW drive plate, Such experiments were conducting on the CDC-4S80 spinning machine. The results show that the radial force is the largest, the tangential force is the second, and the axial force is the smallest, in the process of spinning thickening forming, ; The smaller friction and the roller feed rate can improve the quality of forming parts. The rim of the plate was thickened from 3 mm to 10.5 mm by physical test, which verifies the feasibility of the forming process and the grey system theory.
Key words: DMFW drive plate spinning thickening forming metal flowing thickening rate grey system theory
双质量飞轮驱动齿盘作为发动机中的关键部件,具有:将发动机作功行程的部分能量储存起来,以克服其他行程的阻力,使曲轴均匀旋转;通过安装在飞轮上的离合器,把发动机和汽车传动系统连接起来,便于发动机启动[1].所以零件的机械性能对发动机的整体性能及使用寿命有很大影响.
国内对双质量飞轮的研究主要集中在双质量飞轮结构设计与优化[2]来实现对双质量飞轮性能提升,但加工方式仍为铸造、拼焊.铸造生产的双质量飞轮驱动齿盘往往带有缩孔、缩松等缺陷[3],拼焊生产的双质量飞轮驱动齿盘,会造成焊接影响区化学成分不均影响其力学性能[4].为提高零件的材料利用率及力学性能本文提出旋压增厚工艺成形双质量飞轮驱动齿盘.旋压增厚这种板料近净成形新工艺主要有金俊松、王新云等[5-7]进行研究,文献[5]将板料由2.5 mm双侧旋压增厚到8.5 mm,并未对多道次旋压增厚成形过程进行分析.文献[6]将有限元模拟和试验相结合得出板坯单道次旋压增厚最优工艺参数组合.文献[7]设计一套板料局部加热装置,提高了板坯单道次增厚率.文献[6-7]只针对一道次旋压增厚成形工艺参数、增厚率及旋轮结构进行了优化,并未将其应用于多道次旋压增厚成形.本文通过有限元分析软件SIMUFACT对双质量飞轮驱动齿盘多道次旋压增厚成形过程进行有限元模拟,分析成形过程中金属变形情况及流动规律,总结进给速度、摩擦系数对成形影响规律,在正交试验的基础上优化得到双质量飞轮驱动齿盘成形的最优参数,并在旋压机上进行物理试验,将模拟结果与试验进行对比分析.
1 旋压增厚成形工艺分析 1.1 旋压增厚成形原理旋压增厚成形是将金属平板毛坯或预制毛坯卡紧在旋压机的芯模上,由主轴带动芯模和坯料旋转,利用特殊结构的旋压增厚轮对坯料施加压力,使之产生连续、逐点的塑性变形,从而获得平板外缘增厚状的回转体零件的塑性加工方法.
1.2 成形工艺分析图 1为某汽车用双质量飞轮驱动齿盘增厚处,该零件齿圈与辐板为整体成形,传统冲锻成形适用于厚板且成形过程中增厚处易失稳产生折叠[8-9].根据其外缘厚度为原始薄板厚度3~5倍的特点,制定出旋压增厚成形工艺方案.旋压增厚过程中工艺参数及模具几何尺寸匹配不当将导致:增厚处折叠产生裂纹;端面飞边过多降低材料利用率;模具局部产生裂纹降低模具使用寿命.
Figure 1
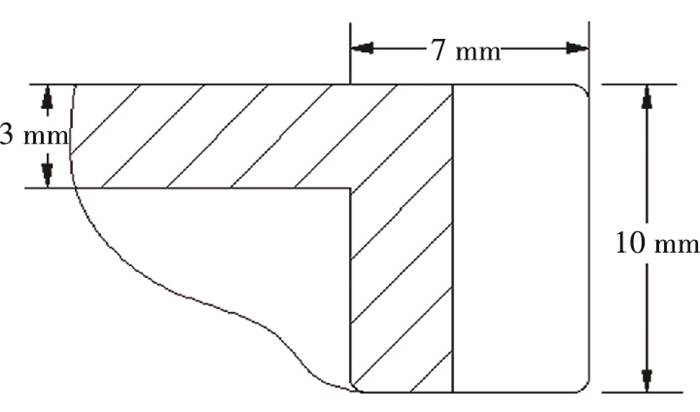
1.3 旋压增厚道次的确定在旋压增厚过程中,各道次增厚率λ(1.2≤λ≤1.4)[10]为
$\lambda = {t_{\rm{n}}}/{t_{{\rm{n}} - 1}}, \;\left( {n \ge 2} \right).$ (1)
式中: tn为第n道次板坯外缘厚度;tn-1为第(n-1)道次板坯外缘厚度.
板坯最终外缘厚度tn为
${t_{\rm{n}}} = {t_0} \times {\lambda ^{\rm{n}}}.$ (2)
式中t0为初始板坯厚度.
由于板坯初始厚度为3 mm,考虑端面加工余量确定外缘厚度为10.5 mm,带入式(1)和式(2)确定旋压次数n=ln3.5/ln(1.2~1.4)=4~7.经过多次模拟优化最终确定旋压次数为5次.
1.4 旋轮设计图 2为所用增厚轮局部, 该旋轮围绕圆柱体侧面开有一深度为h的轮槽,底部有一半径为r的圆弧面将上、下端面连接起来,此旋轮结构有助于金属向下流动,且坯料与旋轮之间接触面积逐渐增大,增加旋压稳定性,其中t为板坯所需增厚厚度、t0为原始板坯厚度、l为板坯所需增厚长度、h为轮槽深度、θ1为轮槽上倾角、θ2为轮槽下倾角.
Figure 2
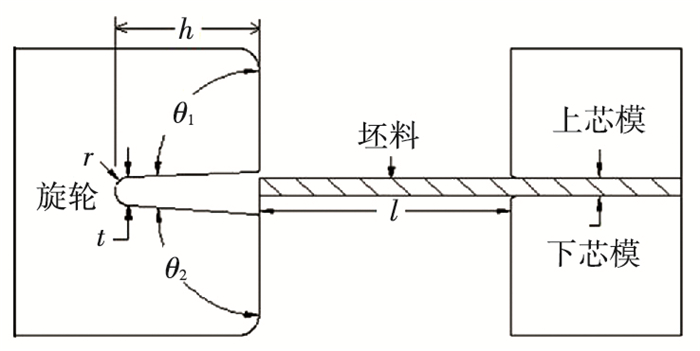
由原始板坯增厚处截面积和轮槽截面积相等可得出t、r、h、θ1、θ2、l、t0间的函数关系为
$\begin{array}{l}l \times {t_0} = \frac{1}{2}\left[{2t + \left( {r-h} \right)\left( {{\rm{cot}}\;{\theta _1} + {\rm{cot}}\;{\theta _2}} \right)} \right] \times \\\;\;\;\;\;\;\;\;\;\;\left( {h - r} \right) + \frac{1}{2}\pi {r^2} + \left( {t - 2r} \right)r.\end{array}$ (3)
将l=31 mm、t0=3 mm带入式(3),得
$\pi {r^2} + 2th - rt - {\left( {h - r} \right)^2}\left( {{\rm{cot}}{\theta _1} + {\rm{cot}}{\theta _2}} \right) = 186.$ (4)
在文献[5]中提出θ1=92°、θ2=93.5°为单道次旋压增厚过程中最优参数.本文选取θ1=92°、θ2=95°,将其带入式(4)得
$\begin{array}{l}0.122{h^2} + h\left( {2t - 0.244r} \right) + 0.122{r^2} + \pi {r^2} - \\\;\;\;\;\;\;\;\;\;\;\;\;\;\;\;\;\;\;\;\;\;\;\;\;rt - 186 = 0.\end{array}$ (5)
由于各道次增厚程度不同选取r=1 mm~3 mm,t值大小可由式(2)确定.
$令\;A = 2t - 0.244r, B = 0.122{r^2} + \pi {r^2} - rt - 186.$ (6)
将式(6)带入式(5)得
$h = \frac{{\sqrt {{A^2} - 0.488B} - A}}{{0.244}}.$ (7)
综上可求出各道次所需旋轮参数并结合有限元模拟结果多次优化见表 1.
表 1
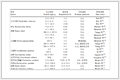
1 4.2 2.1 18.5 92° 95°
2 5.8 2.2 15 92° 95°
3 7.4 2 12.5 92° 95°
4 8.9 1.5 11 92° 95°
5 10.5 1 9 90° 94°
表 1 旋轮参数 Table 1 Roller parameters
2 数值模拟研究 2.1 有限元模型建立采用SIMUFACT有限元分析软件对板坯旋压增厚过程进行数值模拟.选取牌号为AISI-1008直径322 mm、厚度3 mm的圆形板坯,材料基本力学性能:屈服强度220 MPa,密度7.85 g/cm3,弹性模量210 GPa,泊松比0.3,硬化模量1 000 MPa[11].旋轮与板坯之间为库伦摩擦摩擦系数为0.05~0.3,旋轮进给速度为1~5 mm/s,芯模转速为250~500 r/min[12].板坯为变形体采用六面体网格划分,网格尺寸5.45 mm×0.57 mm×0.75 mm,网格总数约为30 000,板坯厚度方向为4层网格,旋轮及芯模为刚体无需网格划分,为提高运算效率,对模型简化见图 3.
Figure 3
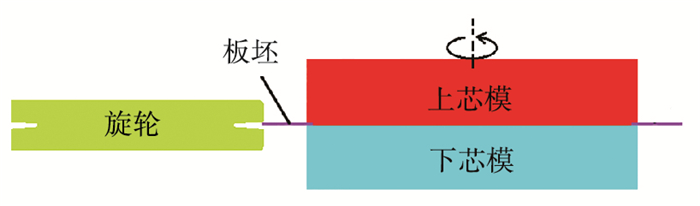
2.2 第1道次旋压增厚有限元模拟图 4为第1道次旋压增厚成形,在成形初期,板坯外缘紧贴轮槽上端面,随着旋轮径向进给板坯外缘逐渐旋弯,此时金属主要发生弹性变形;在成形中期,被旋弯的板坯外缘轴向逐渐增厚且无轴向飞边出现,此时金属发生塑性变形,该阶段等效应力值和变形区域越来越大,塑性变形区主要集中在板坯被增厚处;在成形末期,由于金属变形抗力的增大,且旋轮与芯模之间存在间隙,金属被轴向挤出形成小飞边,此时板坯与轮槽圆弧接触处等效应力值最大.
Figure 4
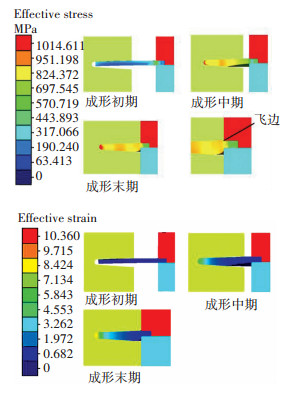
在板坯表面标记4个点见图 5,记录成形过程中标记点的金属流动见图 6,成形初期即金属弹性变形阶段,因为芯模转速是定值,所以4个点对应金属流速与距板坯中心距离成正比,此时4个点仍位于原标记位置;成形中期,板坯外缘金属被增厚发生塑性变形,此时点3和点4已脱离原标记位置,而点1和点2对应金属变形程度不大所以仍位于标记位置上;成形末期,随着金属变形结束,点1~点4对应金属变形程度由弱到强表现为点1~点4脱离原标记位置程度越来越大.
Figure 5
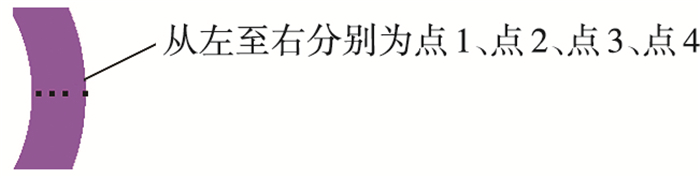
Figure 6
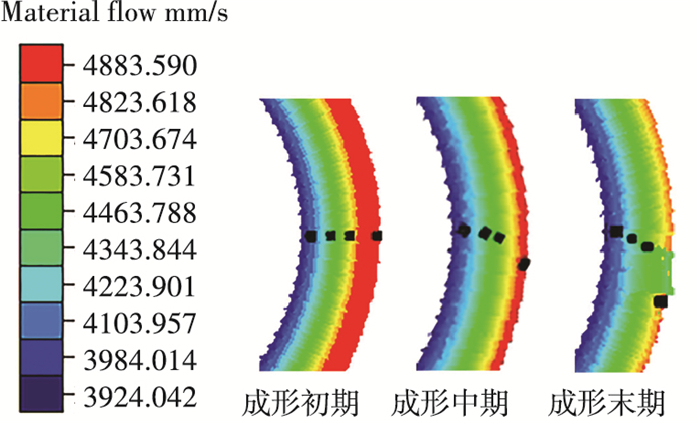
图 7为第1道次旋压增厚成形过程中各向载荷分布数据,从图 7可见:在整个成形中板坯受到径向力最大、切向力次之,轴向力最小,径向力最大值为160 kN,可见旋压增厚工艺所需成形力较小;9 s为板坯外缘刚接触旋轮圆弧底部开始增厚的临界时间点,9 s后随着板坯与轮槽接触面积增大,金属在旋轮约束作用下充填轮槽,导致变形抗力急剧上升径向载荷突变;切向载荷在9~18 s后出现负值归因于金属切向受力方向为所建x轴负向,轴向载荷在9~18 s出现“先负后正”现象,“负”载荷是由于9~16 s此时金属轴向压应力受力方向为z轴负向,“正”载荷是由于16~18 s金属在轴向拉应力作用下产生飞边其受力方向为z轴正向;在旋压增厚过程中,零件成形载荷以径向载荷为主,后续主要分析各工艺参数对径向载荷的影响.
Figure 7
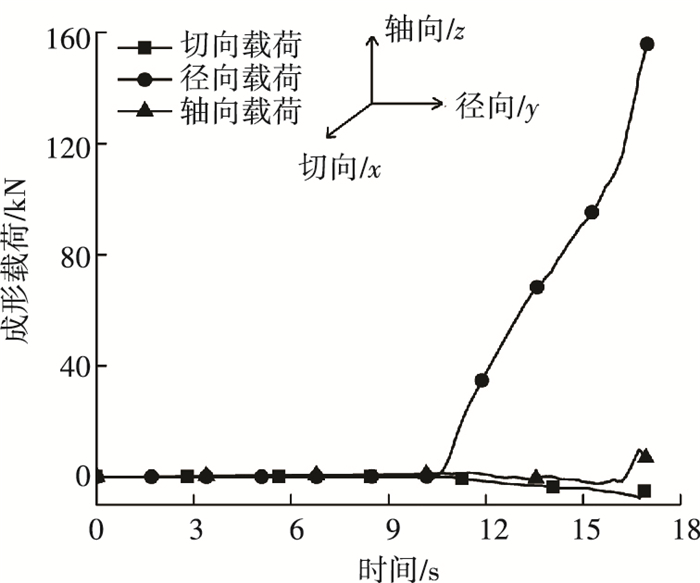
2.3 工艺参数对旋压增厚的影响根据实际经验及旋压手册[12]确定旋压增厚过程中旋轮进给速度1~5 mm/s,主轴转速250~500 r/min,摩擦系数0.05~0.3.
2.3.1 旋轮进给速度对第1道次旋压增厚的影响旋轮进给速度是工艺调试中最常用参数.分别模拟旋轮进给速度为1 mm/s、3 mm/s、5 mm/s时第1道次旋压增厚成形情况. 图 8为不同旋轮进给速度下的板坯应力场分布,从图 8可见轮槽与板坯接触为局部加载此处为应力集中区,在较低旋轮进给速度下,其余区域应力场分布较为均匀.随着进给速度的增大,应力集中区逐渐扩大,应力场分布变得不均匀,这说明旋轮进给速度对应力场分布的均匀性及应力集中区大小影响显著.
Figure 8
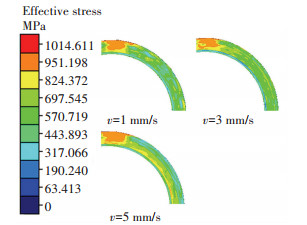
旋轮进给速度主要影响金属径向的流动速率,图 9为不同旋轮进给速度下的板坯飞边大小,从图 9可见旋轮进给速度越大,板坯与上芯模间飞边体积越大,较大的飞边会阻碍金属进入轮槽使板坯增厚不充分,影响零件质量. 图 10为不同旋轮进给速度下的径向成形载荷分布,从图 10可见随着旋轮进给速度的增大,径向成形载荷增大.
Figure 9
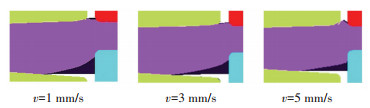
Figure 10
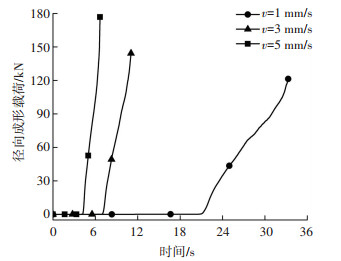
因此,较小的旋轮进给速度有利于保证金属变形的均匀性和降低成形载荷,提高零件质量.
2.3.2 摩擦条件对第1道次旋压增厚的影响旋压增厚过程中,由于板坯紧贴轮槽上端面必然产生较大摩擦.为考虑摩擦对成形的影响,分别模拟摩擦系数为0.05、0.10、0.20时旋压增厚成形情况. 图 11为不同摩擦系数下的板坯应力场分布,从图 11可见随摩擦系数的增大,应力集中区逐渐扩大,应力场分布变得不均匀.
Figure 11
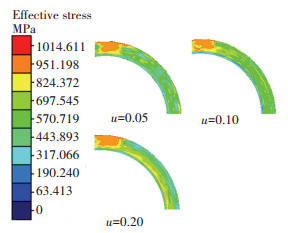
图 12为不同摩擦系数下板坯飞边大小,从图 12可见摩擦系数的增大也会增大成形过程中飞边的体积. 图 13为不同摩擦系数下径向成形载荷分布,从图 13可见由于摩擦系数增大阻碍了金属流动,增大零件的成形载荷.
Figure 12

Figure 13
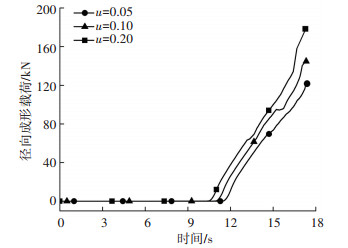
因此,在旋压过程中有必要加入液体润滑剂,这样不仅能减小板坯与旋轮之间的摩擦还能降低模具的表面温度.
2.4 第1道次旋压增厚成形多目标优化由以上分析可知板坯旋压增厚是一个复杂的成形过程,工艺参数选择对零件成形质量至关重要.
2.4.1 正交试验设计以旋轮进给速度、摩擦系数、主轴转速为自变量,以最大成形载荷和增厚程度为目标函数,安排三因素三水平正交试验表L9(34),建立正交试验方案.进行第1道次旋压增厚9次有限元模拟,正交试验自变量和目标函数结果见表 2.
表 2
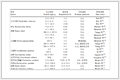
旋轮进给速度/
(mm·s-1) 摩擦系数 主轴转速/
(r·min-1) 最大载荷/
kN 增厚程度/%
1 1 0.05 250 147.1 100
2 1 0.1 300 151.3 100
3 1 0.2 350 160.4 99.8
4 3 0.05 300 192.5 99.5
5 3 0.1 350 202.2 99.1
6 3 0.2 250 248.3 98.5
7 5 0.05 350 215.4 99.3
8 5 0.1 250 221.5 99.2
9 5 0.2 300 249.1 98.6
表 2 三因素三水平正交试验表 Table 2 Orthogonal test table of three factors and three levels
2.4.2 灰色系统理论多目标优化基于灰色系统理论[13-15],关键是求出每个单目标与工艺参数之间的关联系数,以及考虑权重的目标函数的关联度,关联度最大值所对应的工艺参数为最优值.初始基准数据为X0{147.1, 98.5},将表 2数据带入式(8),得到目标函数灰色关联系数见表 3.在保证板坯成形质量良好的情况下,尽量降低零件最大成形载荷.本文认为最大载荷和增厚程度这两个目标函数权重相等,根据式(9)得到目标函数关联度见表 3.
$ \begin{array}{l}\xi \left( {{x_{\rm{i}}}\left( k \right), {x_0}\left( k \right)} \right) = \\\frac{{\mathop {{\rm{min}}}\limits_i \mathop {{\rm{min}}}\limits_k \left| {{x_{\rm{i}}}\left( k \right)- {x_0}\left( k \right)} \right| + \rho \mathop {{\rm{max}}}\limits_i \mathop {{\rm{max}}}\limits_j \left| {{x_{\rm{i}}}\left( k \right)- {x_0}\left( k \right)} \right|}}{{\left| {{x_{\rm{i}}}\left( k \right)- {x_0}\left( k \right)} \right| + \rho \mathop {{\rm{max}}}\limits_i \mathop {{\rm{max}}}\limits_j \left| {{x_{\rm{i}}}\left( k \right)- {x_0}\left( k \right)} \right|}}.\end{array} $ (8)
表 3
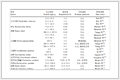
1 1 0.333 3 0.666 7
2 0.923 9 0.333 3 0.628 6
3 0.793 2 0.365 9 0.579 6
4 0.529 0.428 6 0.478 8
5 0.480 7 0.555 6 0.518 1
6 0.335 1 1 0.667 6
7 0.427 5 0.517 2 0.472 4
8 0.406 7 0.483 9 0.445 3
9 0.333 3 0.348 8 0.341 1
表 3 目标函数的灰色关联系数及灰色关联度 Table 3 Grey relational coefficient and grey relational grade of objective function
式中ρ为分辨系数,一般取0.5.
$\gamma ({X_{\rm{i}}}, {X_0}) = \frac{1}{n}\sum\limits_{k - 1}^n {{\lambda _{\rm{k}}}\xi \left( {{x_{\rm{i}}}\left( k \right), {x_0}\left( k \right)} \right)} .$ (9)
式中λk为权重,文中取0.5.
由灰色理论可知,关联度越大其对应目标系列越接近最优.计算各成形参数平均关联度见表 4.数据表明,对灰色关联度影响最大的参数是旋轮进给速度1 mm/s,摩擦系数0.05,主轴转速250 r/min.为一组最优工艺参数.
表 4
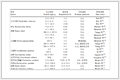
1 0.625
旋轮进给速度(mm/s) 3 0.554 8
5 0.419 6
0.05 0.539 3
摩擦系数 0.1 0.530 7
0.2 0.529 4
250 0.593 2
主轴转速(r/min) 300 0.482 8
350 0.523 4
表 4 自变量对目标函数的平均关联度 Table 4 Average correlation of independent variable to objective function
2.4.3 多目标优化模拟验证由于各道次旋压增厚成形金属变形情况及流动规律基本一致,所以在确定第1道次最优参数后可继续进行第2~5道次优化模拟,从图 14可见第1~5道次成形效果良好,达到了所制定的外缘厚度要求,各道次成形结束后板坯上端面会产生少量飞边,这种飞边一般是无法避免的,对零件的整体性能基本无影响.各道次成形载荷见图 15,最大径向成形载荷约为240 kN.
Figure 14
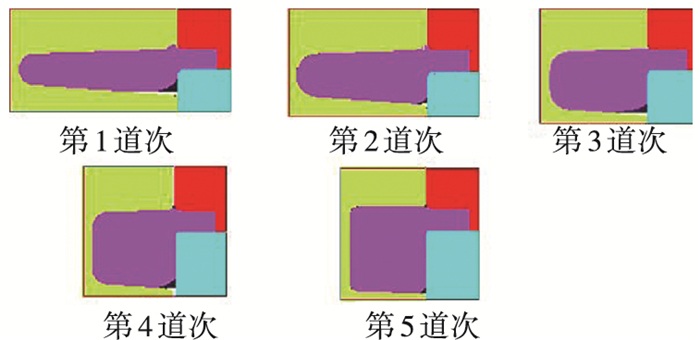
Figure 15
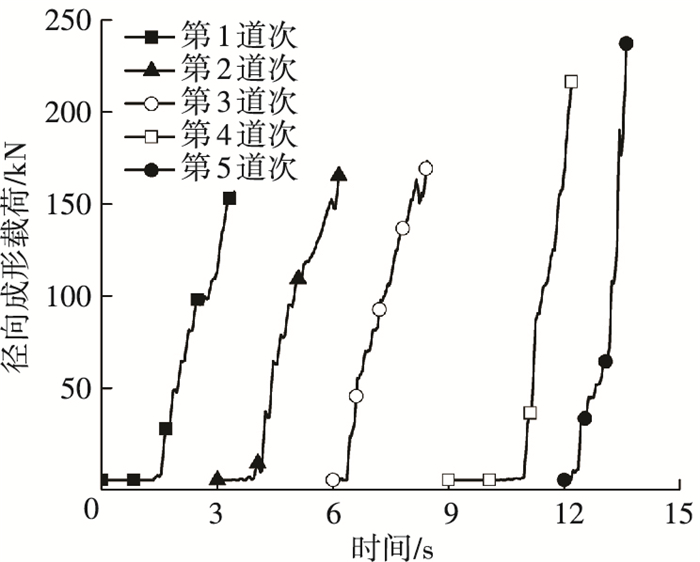
3 试验研究 3.1 试验验证双质量飞轮驱动齿盘旋压增厚试验是在CDC-4S80多工位旋压机上进行,所用圆形板坯尺寸为322 mm×3 mm、旋轮进给速度为1 mm/s、摩擦系数0.05、主轴转速250 r/min,旋轮尺寸与表 1完全一致. 图 16(a)是初始板坯经过5道次旋压增厚试验图,图 16(b)是5道次板坯增厚处剖切图,从图 16可见各道次成形质量良好,外缘厚度达到所设计要求.试验与优化模拟结果基本一致,最终经精车及切齿零件见图 17.
Figure 16
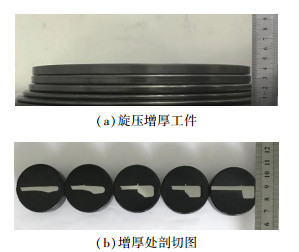
Figure 17
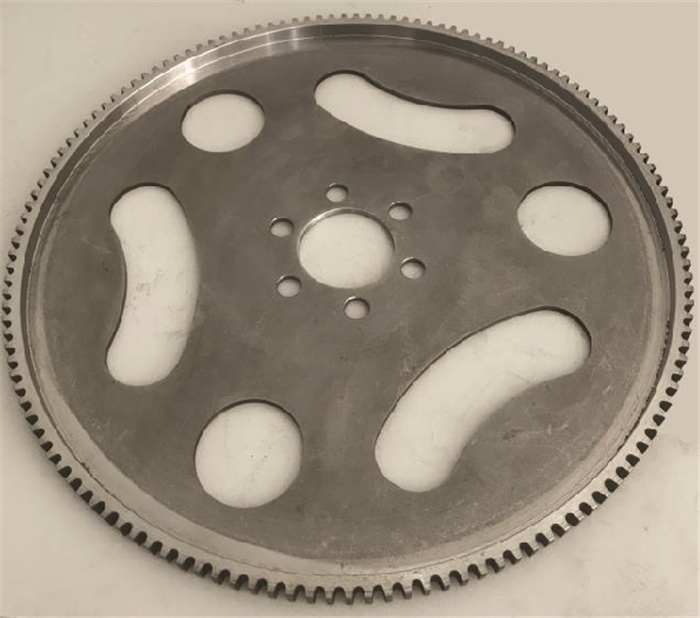
4 结论1) 板坯旋压增厚过程由三个阶段组成:第一阶段为板坯外缘刚接触轮槽底部发生金属的弹性变形;第二阶段紧接第一阶段为板坯外缘逐渐增厚发生金属的塑性变形;第三阶段为成形将要结束,板坯上端面飞边产生阶段.整个成形过程中金属所受径向力最大、切向力次之、轴向力最小.
2) 弹性变形阶段标记点主要以金属周向流动为主,各相对位置保持不变;塑性变形阶段外侧点金属产生剧烈的径向流动,而内侧点仍为金属的周向流动,表现为外侧点脱离标记位置;当成形将要结束时,内侧点到外侧点累积金属变形程度增加,表现为内侧点到外侧点脱离原标记位置的程度增加.
3) 分析不同工艺参数对旋压增厚过程的影响可知:较小的旋轮进给速度和摩擦系数有利于保证板坯变形的均匀性、降低成形载荷和减小飞边体积,提高零件成形质量.
4) 基于灰色系统理论,通过关联系数和关联度计算,获得多目标优化成形工艺参数最佳组合即旋轮进给速度为1 mm/s、摩擦系数0.05、主轴转速250 r/min,结合试验将板坯由3 mm增厚3.5倍至10.5 mm,验证了灰色关联度优化方法的可行性.
参考文献
[1]廖任伟. 汽车发动机挠性飞轮设计与制造工艺和试验研究[D]. 重庆: 重庆大学, 2014.
LIAO Renwei. Automobile engine flexible flywheel design and manufacturing technology and research for experimental[D]. Chongqing: Chongqing University, 2014.http://cdmd.cnki.com.cn/Article/CDMD-10611-1014043542.htm
[2]严正峰. 双质量飞轮设计与制造的关键技术研究[D]. 武汉: 武汉理工大学, 2009.
YAN Zhengfeng. Research on the key technology of dual mass flywheel design and manufacturing[D]. Wuhan: Wuhan University of Technology, 2009.http://cdmd.cnki.com.cn/Article/CDMD-10497-2010063989.htm
[3]陈春蕾. 铝合金飞轮壳的低压铸造模具设计及铸造工艺仿真[D]. 山东: 山东大学, 2014.
CHEN Chunlei. Low pressure die casting mold design casting process simulation of the aluminum alloy flywheel housing[D]. Shandong: Shandong University, 2014.http://cdmd.cnki.com.cn/Article/CDMD-10422-1014307477.htm
[4]杨战中. 飞轮齿圈的焊接工艺[J].工艺材料, 1996, 2: 25-27.
YANG Zhanzhong. Welding process of flywheel gear ring[J].Process and Material, 1996, 2: 25-27.
[5]金俊松, 夏巨谌, 王新云, 等. 板料旋压增厚新工艺[C]//第十二届全国塑性工程年会论文集. 北京: 中国机械工程塑性工程学会, 2011: 56-58.
JIN Junsong, XIA Juchen, WANG Xinyun, et al. New process of sheet spinning thickening[C]//The Proceedings of the 12th National Plastic Engineering Annual Conference. Beijing: Chinese Society for Technology of Plasticty, 2011: 56-58.
[6]李兰. 薄幅厚轮缘盘形件单工步旋压成形工艺研究[D]. 武汉: 华中科技大学, 2015.
LI Lan. Study of a single-step spinning process for disk-like parts with thickened rims[D]. Wuhan: Huazhong University of Science &Technology, 2015.http://cdmd.cnki.com.cn/Article/CDMD-10487-1015905551.htm
[7]胡运展, 金俊松, 王新云, 等. 盘形件局部加热旋压增厚过程设计[J].塑性工程学报, 2014, 24(1): 9-14.
HU Yunzhan, JIN Junsong, WANG Xinyun, et al. Process design for local heating rotary thickening of disc-like blanks[J].Journal of Plasticity Engineering, 2014, 24(1): 9-14.DOI: 10.3969/j.issn.1007-2012.2017.01.002
[8]王新云, 夏巨谌, 陈志明, 等. 板冲锻成形新工艺及其在轿车飞轮盘加工中的应用[J].塑性工程学报, 2008, 15(4): 180-184.
WANG Xinyun, XIA Juchen, CHEN Zhiming, et al. Application of a new sheet stamping-forging hybrid technology in the forming of flying wheel panel of car[J].Journal of Plasticity Engineering, 2008, 15(4): 180-184.
[9]WANG Z G, HIRASAWA K H, YOSHIKAWA Y, et al. Forming of light-weight gear wheel by plate forging[J].CIRP Annals-Manufacturing Technology, 2016, 65(1): 293-296.DOI: 10.1016/j.cirp.2016.04.134
[10]薛克敏. 一种薄底厚外缘的盘类零件的成形方法. 中国专利: 201310421324. 8[ P]. 2013.
XUE Kemin. Forming method of disk type parts with thin bottom and thick outer edge. Chinese Patent: 201310421324. 8[P]. 2013.
[11]谢瑞, 丁方强, 李萍, 等. 皮带轮圆筒形凸台多道次拉深成形工艺研究[J].精密成形工程, 2016, 8(4): 60-64.
XIE Rui, DING Fangqiang, LI Ping, et al. Multi-stage deep drawing process of cylindrical boss of pulley[J].Journal of Netshape Forming Engineering, 2016, 8(4): 60-64.DOI: 10.3969/j.issn.1674-6457.2016.04.011
[12]王成和, 刘克璋, 周路. 旋压技术[M]. 1版. 福州: 福建科学技术出版社, 2007: 709-721.
WANG Chenhe, LIU Kezhang, ZHOU Lu. Spinning technology[M]. The 1st edition. Fuzhou: Fujian Science and Technology Press, 2007: 709-721.
[13]田野, 薛克敏, 孙大智, 等. 涡旋盘背压成形工艺研究[J].机械工程学报, 2015, 51(16): 143-149.
TIAN Ye, XUE Kemin, SUN Dazhi, et al. Study on backpressure forming process of scroll[J].Journal of Mechanical Engineering, 2015, 51(16): 143-149.DOI: 10.3901/JME.2015.16.143
[14]孔炎, 薛克敏, 李萍, 等. 基于正交试验和灰色系统理论的高强钢厚板折弯优化成形模拟及实验[J].塑性工程学报, 2014, 24(5): 11-14.
KONG Yan, XUE Kemin, LI Ping, et al. Optimized simulation and experiment on high-strength thick steel plate bending based on orthogonal test and grey system theory[J].Journal of Plasticity Engineering, 2014, 24(5): 11-14.DOI: 10.3969/j.issn.1007-2012.2014.05.003
[15]陈龙, 黄璞, 王炯, 等. 基于正交试验和灰色系统理论的拼焊板前纵梁成形优化[J].塑性工程学报, 2012, 19(4): 1-5.
CHEN Long, HUANG Pu, WANG Jiong, et al. Optimization of tailor-welded front longitudinal forming based on orthogonal experiment and grey system theory[J].Journal of Plasticity Engineering, 2012, 19(4): 1-5.DOI: 10.3969/j.issn.1007-2012.2012.04.001