贾晨1,2,邵永松1,2,郭兰慧1,2,李建伟1,2
(1.结构工程灾变与控制教育部重点实验室(哈尔滨工业大学),哈尔滨 150090; 2.土木工程智能防灾减灾工业和信息化部重点实验室(哈尔滨工业大学),哈尔滨 150090)
摘要:
腐蚀是钢结构面临的一大耐久性问题,而大气腐蚀是最常见、造成腐蚀损失最大的一类腐蚀.多年来,国内外学者通过在役结构的原位测试、大气暴露试验、室内加速试验、电化学测试等手段对各种钢材的大气腐蚀进程进行了大量研究,对不同环境中的钢材腐蚀机理进行了分析,并提出钢材的腐蚀模型.本文从典型腐蚀性大气环境中建筑结构用钢的腐蚀机理、钢材的腐蚀失重时变模型和钢材表面的蚀坑发展和分布规律等三方面论述了建筑结构用钢的大气腐蚀模型的研究现状和进展.
关键词: 钢结构 大气腐蚀 腐蚀机理 时变模型 蚀坑分布
DOI:10.11918/201905174
分类号:TU391
文献标识码:A
基金项目:国家自然科学基金(51778185)
A review of atmospheric corrosion models of building structural steel
JIA Chen1,2,SHAO Yongsong1,2,GUO Lanhui1,2,LI Jianwei1,2
(1.Key Lab of Structures Dynamic Behavior and Control (Harbin Institute of Technology), Ministry of Education, Harbin 150090, China; 2.Key Lab of Smart Prevention and Mitigation of Civil Engineering Disasters (Harbin Institute of Technology), Ministry of Industry and Information Technology, Harbin 150090, China)
Abstract:
Corrosion is a major durability problem for steel structures, and atmospheric corrosion is the most common corrosion that causes the greatest loss. Over the years, researchers have studied the atmospheric corrosion process of various kinds of steel through in-situ test of in-service steel structures, atmospheric exposure test, accelerated corrosion test, electrochemical test, and other methods. The corrosion mechanism of steel in different environments were analyzed and corrosion models were put forward. In this paper, the research status and progress of atmospheric corrosion models of structural steel are discussed from three aspects: corrosion mechanism of steel in typical corrosive atmosphere, time-dependent model of corrosion loss of steel, and pitting depth development and distribution of steel surface.
Key words: steel structure atmospheric corrosion corrosion mechanism time-dependent model pitting distribution
贾晨, 邵永松, 郭兰慧, 李建伟. 建筑结构用钢的大气腐蚀模型研究综述[J]. 哈尔滨工业大学学报, 2020, 52(8): 1-9. DOI: 10.11918/201905174.

JIA Chen, SHAO Yongsong, GUO Lanhui, LI Jianwei. A review of atmospheric corrosion models of building structural steel[J]. Journal of Harbin Institute of Technology, 2020, 52(8): 1-9. DOI: 10.11918/201905174.

基金项目 国家自然科学基金(51778185) 作者简介 贾晨(1993—),女,博士研究生;
邵永松(1964—),男,教授,博士生导师;
郭兰慧(1978—),男,教授,博士生导师 通信作者 邵永松,shaoyongsong@hit.edu.cn 文章历史 收稿日期: 2019-05-24
Abstract Full text Figures/Tables PDF
建筑结构用钢的大气腐蚀模型研究综述
贾晨1,2, 邵永松1,2


1. 结构工程灾变与控制教育部重点实验室(哈尔滨工业大学), 哈尔滨 150090;
2. 土木工程智能防灾减灾工业和信息化部重点实验室(哈尔滨工业大学), 哈尔滨 150090
收稿日期: 2019-05-24
基金项目: 国家自然科学基金(51778185)
作者简介: 贾晨(1993—),女,博士研究生; 邵永松(1964—),男,教授,博士生导师; 郭兰慧(1978—),男,教授,博士生导师
通信作者: 邵永松,shaoyongsong@hit.edu.cn
摘要: 腐蚀是钢结构面临的一大耐久性问题,而大气腐蚀是最常见、造成腐蚀损失最大的一类腐蚀.多年来,国内外学者通过在役结构的原位测试、大气暴露试验、室内加速试验、电化学测试等手段对各种钢材的大气腐蚀进程进行了大量研究,对不同环境中的钢材腐蚀机理进行了分析,并提出钢材的腐蚀模型.本文从典型腐蚀性大气环境中建筑结构用钢的腐蚀机理、钢材的腐蚀失重时变模型和钢材表面的蚀坑发展和分布规律等三方面论述了建筑结构用钢的大气腐蚀模型的研究现状和进展.
关键词: 钢结构 大气腐蚀 腐蚀机理 时变模型 蚀坑分布
A review of atmospheric corrosion models of building structural steel
JIA Chen1,2, SHAO Yongsong1,2


1. Key Lab of Structures Dynamic Behavior and Control (Harbin Institute of Technology), Ministry of Education, Harbin 150090, China;
2. Key Lab of Smart Prevention and Mitigation of Civil Engineering Disasters
Abstract: Corrosion is a major durability problem for steel structures, and atmospheric corrosion is the most common corrosion that causes the greatest loss. Over the years, researchers have studied the atmospheric corrosion process of various kinds of steel through in-situ test of in-service steel structures, atmospheric exposure test, accelerated corrosion test, electrochemical test, and other methods. The corrosion mechanism of steel in different environments were analyzed and corrosion models were put forward. In this paper, the research status and progress of atmospheric corrosion models of structural steel are discussed from three aspects: corrosion mechanism of steel in typical corrosive atmosphere, time-dependent model of corrosion loss of steel, and pitting depth development and distribution of steel surface.
Keywords: steel structure atmospheric corrosion corrosion mechanism time-dependent model pitting distribution
在建筑钢结构中,最常用的钢材为低碳钢和低合金钢.当建筑钢结构长期处于恶劣的环境中时,由于钢材自身的金属化学属性,极易与空气中的腐蚀介质发生电化学腐蚀.在不同环境中,腐蚀的机理和产物有所差别,进而腐蚀的时变规律也会有所不同.虽然一般情况下建筑钢结构在初建时会进行一定的防腐处理,但随着时间的推移,防腐层会从一些薄弱部位(如螺栓孔、构件根部等)开始失效,基体钢材发生腐蚀[1],造成严重的后果.由腐蚀造成的直接经济损失高达国民生产总值的3%~5%,而间接损失更加严重,因腐蚀引起的事故中也时常会发生人员伤亡[2-3].在腐蚀所造成的经济损失中,大气腐蚀体量最大,每年因此而损失的钢材约占总损失量的50%以上[4].
腐蚀分为均匀腐蚀和局部腐蚀,而局部腐蚀又分为点蚀、缝隙腐蚀、晶间腐蚀等[5-6].在大气环境中,均匀腐蚀和点蚀是建筑结构用钢最常见的腐蚀类型,而且往往同时发生[7-10].随着腐蚀时间的推移,两种腐蚀类型会分别造成板件厚度损失和钢板表面蚀坑的分布(图 1).实际钢结构工程应用中,往往只考虑均匀腐蚀造成的截面损失而引起的构件承载力退化[1].但应当指出,由蚀坑所引起的应力不均匀分布和应力集中效应会造成结构延性的降低[11-14].可以看出,研究建筑结构用钢在大气环境下的腐蚀进程是研究腐蚀作用下钢材力学性能退化规律的基础,基于此,才能进一步进行腐蚀环境中建筑钢结构的性能预测及其剩余寿命的评定[15-16].因而,总结大气腐蚀后蚀坑的随机分布规律特点可以为进一步的大气腐蚀后钢结构工作性能研究提供参考.
Fig. 1
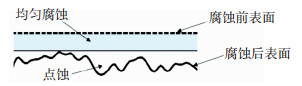
腐蚀是一个逐渐进行且相对漫长的过程,完成这一过程并得到腐蚀产物是进行腐蚀机理研究和腐蚀后钢材性能研究的基础.除对在役结构进行研究外,腐蚀试验是最重要的研究手段.腐蚀试验主要分为两类,一类是自然环境下的大气腐蚀暴露试验,另一类是模拟加速腐蚀试验.自然环境下的大气腐蚀暴露试验是指直接将已知参数的试件暴露于大气环境中,这种试验手段能真实地反映出材料在试验所在地的腐蚀情况,试验结果可靠性强,也是用于研究金属材料大气腐蚀过程的基础,但是试验周期太长,少则几年,多则数十年[17-20].模拟加速腐蚀试验是指人为设定腐蚀性较强的环境,对材料进行腐蚀,优点在于试验周期短,对区域没有严格要求,模拟加速腐蚀试验往往在室内或特定的试验仪器中进行.近年来,人们针对不同的环境特征提出了多种模拟加速腐蚀试验方法[21-22],如酸试验、湿热试验、浸泡试验、盐雾试验、多因子循环复合试验等,其中,浸泡试验和盐雾试验应用最为广泛.为了进一步采用加速试验的结果预测实际腐蚀进程,学者们采用灰色理论对加速腐蚀试验与暴露试验的相关性进行了大量研究,结果表明,在海洋大气腐蚀环境下,人工加速模拟早期和后期相关性都较好,而在工业大气环境下,早期相关性较好,后期相关性逐渐变差[23-25].根据上述总结,可以根据不同的试验目的和试验条件选择相应的研究方法.
目前,国内外学者针对海洋环境中如海洋平台用钢、船只用钢等钢材的腐蚀规律进行了广泛研究和总结,但建筑结构用钢与其不同,主要面临的是大气腐蚀问题,其中最典型的腐蚀性大气环境即为海洋大气环境(如海滨城市)和工业大气环境(如工业厂房).本文针对建筑结构用钢在典型大气腐蚀环境中的腐蚀机理、腐蚀的时变规律以及蚀坑的发展和分布规律等方面的研究进展进行总结和分析,以期为进一步研究腐蚀性大气环境下钢结构长期工作性能提供参考.
1 建筑结构用钢的大气腐蚀机理研究钢材腐蚀机理,是钢材防腐工作的基础,同时,了解腐蚀过程,也有助于深入理解腐蚀对钢材性能造成影响的原因.进行腐蚀机理研究时,往往对不同腐蚀时间的锈层进行分析,采用SEM、XRD、Raman谱等手段[26-30],得到锈层结构和腐蚀产物的成分,以推断腐蚀过程中发生的化学反应.
1.1 大气腐蚀的主要环境因素大气腐蚀的基本过程为:由于钢材表面的毛细管作用、吸附作用或凝聚作用,导致空气中的水分在钢材表面形成薄液膜,同时,可溶性的腐蚀介质溶于薄液膜中,使得钢材发生电化学腐蚀,基体铁单质不断发生阳极溶解,生成中间腐蚀产物,经过进一步反应,形成最终腐蚀产物.影响钢材大气腐蚀的环境因素比较复杂,其中的主要因素包括大气的湿度、温度、腐蚀性组分等[26-30].
大气相对湿度主要是通过影响薄液膜形成而影响钢材腐蚀速率.当大气相对湿度低于某一临界值RHc时,难以形成有效的薄液膜,因而钢材腐蚀速率很低.当大气相对湿度超过该临界值时(RHc~100%),会形成有利于腐蚀电化学反应顺利进行的薄液膜,随着相对湿度增加,腐蚀速率急剧升高[31-32]. RHc与钢材表面的状态相关,例如,当大气中的一些具有吸附性的固体颗粒附着在钢材表面时,RHc减小[33-34].由此可见,较高的大气相对湿度是钢材大气腐蚀的基本条件.此外,干湿交替的大气环境对钢材的影响本质是薄液膜厚度的变化过程.在薄液膜环境下,钢材的腐蚀是一个氧去极化的过程,而液膜在干燥过程中变薄有利于氧的传递,水分减少的同时也增加了电解质浓度,从而加速腐蚀,当水分减少至超过某一临界值时,腐蚀速率又逐渐降低[33-34].
大气温度从两方面对钢材腐蚀速率产生影响.一方面,根据范特霍夫规则[35-36],在反应温度不是很高时,温度每上升10 ℃,反应速率提高2~4倍.因此,大气温度升高造成钢材腐蚀过程的电化学反应速率加快[37],腐蚀加剧.另一方面,随着大气温度升高,O2的溶解度逐渐降低(图 2),进而影响阴极的氧去极化反应,此外,SO2等气体的溶解度也会随着温度变化而改变,对腐蚀进程也会造成影响.应该指出,当大气温度不高于60 ℃时,升温导致电化学反应速率加快占主导地位,因此,整体而言钢材的腐蚀速率随着温度的升高而增大.温度、湿度对腐蚀加剧作用具有耦合效应,湿热试验正是借此实现对腐蚀的加速[37].此外,昼夜温差也会影响薄液膜的形成,夜间大气温度降低,水蒸气冷凝,在钢材表面结露,同时,O2、SO2等气体的溶解度升高,会加快腐蚀进程[38].
Fig. 2
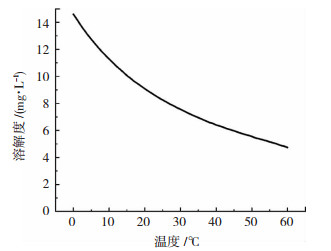
GB/T 15957—1995《大气环境腐蚀性分类》中主要根据大气中的组分将大气环境划分为乡村大气、城市大气、工业大气和海洋大气等四种类型[39],其中,工业大气与海洋大气是典型的腐蚀性大气环境,对钢材的腐蚀性较强,因而研究较多.工业大气对建筑结构用钢造成腐蚀的主要因素是大气中的SO2等腐蚀性气体,这些酸性物质溶于钢材表面薄液膜,使溶液pH降低,进而造成钢材的腐蚀加剧[40].在海洋大气中,浓度较高的Cl-是造成钢材腐蚀的主导因素,大量的Cl-溶解在钢材表面的薄液膜中,大大地增强了溶液的导电性,极化反应加剧,随着Cl-浓度升高,腐蚀速率增大[41-42].
1.2 建筑结构用钢的工业大气腐蚀机理在以SO2主导的工业大气环境中[43],钢材的工业大气腐蚀机理见图 3.SO2易溶于水,钢材表面的薄液膜会吸附大气中的SO2,生成H2SO3,并进一步氧化为H2SO4[44],薄液膜中的溶液呈酸性.同时,在薄液膜中钢材的基体铁单质发生阳极溶解,阴极既会发生吸氧反应生成不稳定的腐蚀产物Fe(OH)2,也会发生一定程度的析氢反应[45-46].在酸性的薄液膜中,Fe(OH)2会被溶解,进一步生成腐蚀产物FeSO4·xH2 O,而FeSO4·xH2O被进一步氧化为α-FeOOH和γ-FeOOH,此过程同时会生成H2SO4,形成了特有的酸的循环反应机制[47].随着腐蚀不断进行,γ-FeOOH会转化为α-FeOOH和Fe3O4.
Fig. 3
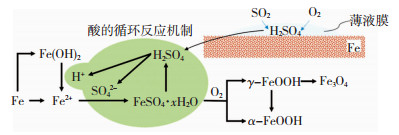
1.3 建筑结构用钢的海洋大气腐蚀机理在以NaCl主导的海洋大气环境中,钢材的海洋大气腐蚀机理见图 4,该过程主要分为两个阶段.NaCl具有很强的吸湿性,当附着在钢材表面时,会极大地促进薄液膜的形成,进而促使腐蚀的电化学反应迅速发生[48].在第一阶段,钢材基体Fe发生阳极溶解,阴极发生吸氧反应并生成Fe(OH)2,Fe(OH)2附着在钢材表面形成一层不稳定的腐蚀产物膜.第二阶段,Fe(OH)2会被进一步缓慢氧化,形成α-FeOOH和γ-FeOOH,同时Cl-发挥作用,生成γ-Fe2O3.与工业大气腐蚀相似,随着腐蚀的进行,γ-FeOOH会转化为α-FeOOH和Fe3O4[49],不同的是,在Cl-的作用下,γ-FeOOH还会转化为β-FeOOH,由于β-FeOOH的存在,导致Cl-通过锈层抵达钢材表面,进一步促进腐蚀.因此,可看出,γ-Fe2O3和β-FeOOH是以Cl-主导的海洋大气环境中特有的腐蚀产物.
Fig. 4
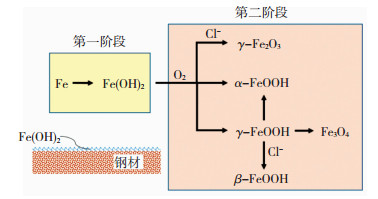
2 钢材的大气腐蚀失重时变规律腐蚀会造成钢材基体金属的损失,因此,常采用失重法(式(1)),通过计算腐蚀前后钢材质量变化来定量评定腐蚀情况.
${\eta _t} = \frac{{{m_0} - {m_t}}}{{{m_0}}} \times 100\% , $ (1)
式中:ηt为腐蚀t时间后试件的失重率,mt为腐蚀t时间并完全清除腐蚀产物后试件的质量,m0为腐蚀前试件的初始质量.
一方面,由失重曲线可直观看出某腐蚀时间时的质量损失.另一方面,由失重曲线的斜率可以得到腐蚀速率的变化情况.应当指出,很多时候会通过简单的数学计算将质量损失转化为厚度损失[50].失重法由于操作简单、数据直观、适用性强等特点受到广泛应用[51].基于失重法,学者们提出了不同的腐蚀时变模型,主要包括简单模型和分段模型两大类(有防腐层时,仅考虑防腐层失效,腐蚀开始发生后的情况).简单模型(图 5(a)~(d))包括线性模型、幂模型、对数模型、指数模型等,分段模型(图 5(e)~(f))主要包括非线性-线性模型和双峰模型.
Fig. 5
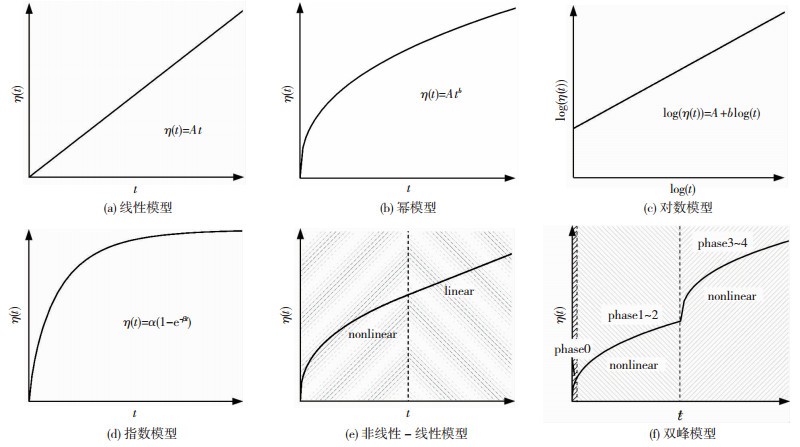
线性模型(图 5(a))是最简单、最粗略的腐蚀时变模型[52-54],仅有一个模型参数A,即为腐蚀速率.一般根据某段时间的腐蚀量与时间的比值来确定腐蚀速率A.线性模型不考虑腐蚀速率随腐蚀时间的变化,即模型中的腐蚀速率A仅仅代表这一时间段内的平均腐蚀速率.而实际上随着腐蚀时间的增长,由于腐蚀产物的影响,腐蚀速率是不断变化的,这一点从其他模型中也可以看出.
幂模型(图 5(b))是目前最常用的非线性腐蚀时变模型[52, 54-59],有两个模型参数,其中A表示初始腐蚀速率,b反映了随着腐蚀的进行腐蚀速率的变化趋势.当b=1时,即为线性模型.实际情况下,对于建筑结构用钢材,b < 1且范围在0.4~0.8,这意味着腐蚀速率逐渐减小.根据Tammann[60]的理论,金属的腐蚀速率是由氧气穿过锈层到达金属表面的速率控制的,因而锈层越厚,氧气越难以到达金属表面,腐蚀速率越小.因此,幂模型中的参数b < 1反映了腐蚀产物对基体钢材的保护作用.作为最广泛使用的一种腐蚀时变模型,幂模型依然存在一些问题.在进行长期腐蚀数据的拟合时,效果可能不佳[61-64],拟合参数会有较大扰动.例如,若对一组腐蚀时间长达8 a的数据进行分析,仅拟合前6 a的数据所得的参数与拟合8 a的数据所得的参数可能相差较大.这个现象主要是由于腐蚀失重数据的随机性和离散性导致的.对数模型(图 5(c))实际上是幂模型的变异形式,即将幂模型在对数坐标系中呈现[65],这样一来,模型为直线.与幂模型不同的是,实际应用中,先对腐蚀数据与时间取对数,再进行线性拟合,得到对数模型的拟合参数A和b,而非直接采用原始数据进行非线性拟合.这样做法的优点是会在一定程度上减小数据的变异性.
指数模型(图 5(d))最初是根据船只的腐蚀情况提出的[66-68],但也被应用于结构钢材的大气腐蚀[28, 68-70].该模型也考虑了腐蚀产物对基体钢材的保护作用,但与幂模型的最大区别在于,指数模型认为,随着腐蚀的进行,如果对腐蚀产物不加扰动,随着腐蚀时间增长,腐蚀速率最终会趋于零,腐蚀停止,且最终的腐蚀量为α.应当指出的是,指数模型的原始数据是基于船只的长期腐蚀数据,这些数据中包含了多种不可控变量的影响,不完全满足统计要求[1, 15].例如,船只的航路不唯一,因而经历的环境也不确定,会进一步影响腐蚀机理从而影响腐蚀失重数据.此外,与金属铝的致密氧化膜不同,根据建筑结构用钢的腐蚀机理,腐蚀产物对基体的保护作用有限,并不能形成一层十分致密的氧化膜而使得腐蚀停止,而且目前未见有直观表明腐蚀会停止的现有文献或者观测数据,因此,指数模型对长期腐蚀的有效性还有待进一步讨论[1, 15].
非线性-线性模型(图 5(e))将腐蚀描述两个阶段[71-74],第一阶段即为腐蚀前期,腐蚀失重为非线性增长,可采用幂模型[71-73]或指数模型[75]来拟合,第二阶段即为腐蚀后期,腐蚀失重呈线性增长,两个阶段的临界腐蚀时间约为8 a[75].
双峰模型(图 5(f))根据不同的腐蚀机制,将长期腐蚀分为两个阶段[76-81].实际上钢材的腐蚀速率是由阴极反应速率控制的,腐蚀机理的不同也都是阴极反应不同造成的.第一阶段中包含腐蚀的萌生时期以及阴极发生吸氧反应时期,这一阶段氧气可以通过薄液膜或不太厚的锈层渗透至基体钢材表面.第二阶段为阴极析氢反应时期,此阶段中由于腐蚀时间长、锈层太厚导致氧气无法顺利渗透,造成了钢材表面的缺氧环境,无法发生吸氧腐蚀.两个阶段的临界时间与环境温度、薄液膜厚度、溶解氧浓度等因素相关.目前多项研究表明,双峰模型适用于多种金属在多种环境下的腐蚀规律[81-86].
3 钢材腐蚀表面蚀坑发展及分布规律如前文所述,钢材发生大气腐蚀时,板件厚度均匀减小的同时,会出现随机分布的蚀坑,蚀坑的发展主要包含萌生-深度发展-横向发展三个过程.在铸造成型过程中,钢材表面及内部会存在一些缺陷,加之钢材的多相性,会引起多处产生局部微弱的电势差,从而导致蚀坑的萌生[87-89].蚀坑萌生后,首先向深度方向发展,腐蚀产物最初在坑口附近产生和堆积[8, 88-89].随着腐蚀的发展,蚀坑深度增加,腐蚀产物逐渐覆盖在坑口上形成产物膜,一方面氧气渗透至坑底的路径增长,另一方面,腐蚀产物阻碍氧气的渗透,二者共同导致了坑底的缺氧环境,析氢反应逐渐代替吸氧反应.坑内氢气逐渐增多,气压增大,会导致坑口覆盖的腐蚀产物薄膜破裂,氢气得以逸出蚀坑[88, 91].但腐蚀产物不断增多,无论是氧气的向内渗透还是氢气的向外逸出都愈加困难,坑底的反应逐渐停止,蚀坑不再向深度方向发展[91-92].然而,由于坑内较低的pH,此时蚀坑会沿横向发展,直径扩大,最终相邻的蚀坑互相连接形成更大的蚀坑,甚至形成一片腐蚀低洼[93].在腐蚀低洼上,又会形成新的蚀坑,进一步发展[94].
钢材表面的腐蚀形貌往往可以通过光学显微镜[70],扫描电镜(SEM)[26],激光共聚焦显微镜(CLSM)[26]和三维形貌仪[27-29]等仪器设备进行观测,并提取蚀坑参数,结合图像处理技术[30, 95],对腐蚀数据进行分析.在腐蚀表面形貌的众多参数中,人们最关注的往往是蚀坑深度.对于蚀坑深度而言,一方面与腐蚀失重相似,是随腐蚀时间变化的函数,另一方面,蚀坑在钢材表面的分布具有显著的随机性特征[96],因此,蚀坑深度的时变规律与随机分布规律受到广泛研究.应当指出的是,经历长期腐蚀后,蚀坑深度的频率分布为双峰分布[97],这是因为此时钢材表面蚀坑可分为稳态蚀坑和亚稳态蚀坑两种类型[9],其中稳态蚀坑往往深而大,频率分布呈正态分布或I型极值分布(Gumbel分布),亚稳态蚀坑浅而小,往往在腐蚀初期迅速萌生但不再进一步发展,其频率分布呈指数分布[88].
描述钢材蚀坑深度(最大蚀坑深度、平均蚀坑深度)的时变规律最常用的是幂模型[52, 73, 98-101](图 5(b)),指数模型[28](图 5(d))有时也被采用.此外,根据蚀坑发展的机制,学者[15, 102-103]提出了更为复杂的台阶式时变模型(图 6).每一级“台阶”都包含了单独蚀坑的发展以及相邻蚀坑相互连接形成腐蚀低洼的信息,而每上一级“台阶”,也就意味着在腐蚀低洼中新蚀坑重新萌生和发展的过程.
Fig. 6
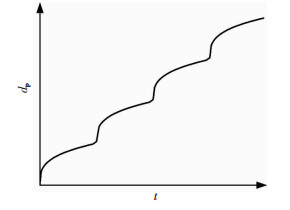
蚀坑会造成钢材的应力集中,而深度最大的深坑往往还会导致结构的最终失效[96, 104-105],因此,研究蚀坑最大深度的随机分布模型是建立腐蚀导致的结构失效模型的重要基础.20世纪50年代,极值分析开始被用于研究蚀坑深度的随机分布规律[106]且一直沿用至今.大量研究表明,最大蚀坑深度服从Gumbel分布[106-118]或Frechet分布[97],但是,对于同一组腐蚀数据,如果用来预测结构失效,则采用Frechet分布更为安全保守(例如,根据Gumbel分布和Frechet分布,某钢板腐蚀4 a后,蚀坑穿透的概率分别为2%和4%[97]).
极值分布又称广义极值分布,概率密度函数如式(2)所示,根据k的大小可分为I型极值分布(Gumbel分布,k=0)、II型极值分布(Frechet分布,k < 0)和III型极值分布(Weibull分布,k>0).进行极值分析时最常见的手段是标准极值坐标图法[97, 109, 111-113, 117-118],该方法可以分为三步进行.第一步,求出每个独立样本中的最大蚀坑深度di;第二步,将di升序排列,并将其转化为标准极值变量wi;第三步,分别以蚀坑深度d和标准极值变量w为横纵坐标作图,如果数据服从极值分布,则在相应的坐标图中为直线.Gumbel标准极值变量[117-118]的计算方法如式(3)~(5)所示,其中,u、α为分布参数,μd、σd分别为蚀坑深度数据的均值和标准差.进行极值分析时,除了采用标准极值坐标图法,还可以采用假设检验法[114-116],即假设最大蚀坑深度d数据服从极值分布,计算其实际的累计概率分布曲线(CDF),并与理论CDF进行对比,从而判断假设是否成立.
${\begin{array}{*{20}{c}}{f(x|k, \mu , \sigma ) = }\\{\left( {\frac{1}{\sigma }} \right)\exp \left( { - {{\left( {1 + k\frac{{x - \mu }}{\sigma }} \right)}^{ - \frac{1}{k}}}} \right){{\left( {1 + k\frac{{x - \mu }}{\sigma }} \right)}^{ - 1 - \frac{1}{k}}}, }\end{array}}$ (2)
${w_i} = \left( {{d_i} - u} \right)\alpha , $ (3)
${\mu _d} = u + \frac{{1.139\;6}}{\alpha }, $ (4)
${\sigma _d} = \frac{{0.408\;25{\rm{ \mathsf{ π} }}}}{\alpha }.$ (5)
4 结论1) 建筑结构用钢的大气腐蚀主要发生于腐蚀性较强的工业大气环境和海洋大气环境中,两种环境中钢材腐蚀机理不尽相同,但无论哪种环境,空气湿度和温度都是影响腐蚀的重要因素.工业大气腐蚀的突出特点是由于SO2而引起的酸的循环再生机制,海洋大气腐蚀的特点是由于存在高浓度的Cl-而生成特有的腐蚀产物γ-Fe2O3和β-FeOOH.
2) 腐蚀失重是最常用的腐蚀损失指标,其时变规律可以采用线性模型、幂模型、指数模型、分段模型等数学模型来描述,而每一个模型都是根据特有的腐蚀过程提出的.其中双峰模型最符合钢材的长期腐蚀,且适用于多种环境下的腐蚀.
3) 在钢材的腐蚀过程中,均匀腐蚀和点蚀是一起发生的,点蚀所引起的蚀坑分布具有鲜明的随机性.蚀坑深度是人们最关注的蚀坑参数,其时变规律的趋势往往与失重规律类似,常用幂模型来描述.最大蚀坑深度的随机分布规律往往通过极值分析来进行研究,结果表明,一般情况下,最大蚀坑深度服从广义极值分布(Gumbel分布或Frechat分布).
参考文献
[1] MELCHERS R E. Progress in developing realistic corrosion models[J]. Structure and Infrastructure Engineering, 2018, 14(7): 843.
[2] 侯保荣, 张盾, 王鹏. 海洋腐蚀防护的现状与未来[J]. 中国科学院院刊, 2016, 31(12): 1326.
HOU Baorong, ZHANG Dun, WANG Peng. Current situation and future of marine corrosion protection[J]. Bulletin of Chinese Academy of Sciences, 2016, 31(12): 1326.
[3] 侯保荣. 献身腐蚀防护事业降服"吃金属的老虎"——专访中国工程院院士侯保荣[J]. 表面工程与再制造, 2016, 16(3): 2.
HOU Baorong. Dedicated to corrosion protection, subdue the "tiger that eats metal"—an interview with Hou Baorong, an academician of Chinese Academy of Engineering[J]. Surface Engineering and Remanufacturing, 2016, 16(3): 2.
[4] 何建新.热带海洋大气环境下碳钢大气腐蚀行为规律特征[D].北京: 机械科学研究总院, 2008
HE Jianxin. Study on the carbon steel corrosion at tropic seashore atmosphere[D]. Beijing: China Academy of Machinery Science and Technology, 2008
[5] JONES D A. Principles and prevention of corrosion[M]. Upper Saddle River, NJ: Prentice Hall, 1996: 207.
[6] HARRO H M, PORT R D. The nalco guide to cooling water system failure analysis[M]. New York, NY: McGraw-Hill, 1993: 28.
[7] MELCHERS R E, CHERNOV B B. Corrosion loss of mild steel in high temperature hard freshwater[J]. Corrosion Science, 2010, 52(2): 449.
[8] BUTLER G, STRETTON P, BEYNON J G. Initiation and growth of pits on high-purity iron and its alloys with chromium and copper in neutral chloride solutions[J]. British Corrosion Journal, 1972, 7(4): 168.
[9] BURSTEIN G, PISTORIUS T. The nucleation and growth of corrosion pits on stainless steel[J]. Corrosion Science, 1993, 35(1): 57.
[10] BRASHER D M. Stability of the oxide film on metals in relation to inhibition of corrosion of mild steel in presence of aggressive anions[J]. British Corrosion Journal, 1967, 2(3): 95.
[11] 余冬冬.酸性大气环境锈损钢框架节点抗震性能试验及理论研究[D].西安: 西安建筑科技大学, 2017
YU Dongdong. Experimental and theoretical analysis on seismic behavior of corroded steel frame joints in acidic atmosphere[D]. Xi'an: Xi'an University of Architecture and Technology, 2017
[12] 徐善华, 张宗星, 苏超, 等. 中性盐雾环境锈蚀H型钢柱抗震性能试验研究[J]. 建筑结构学报, 2019, 40(1): 49.
XU Shanhua, ZHANG Zongxing, SU Chao, et al. Experimental study on seismic behavior of corroded H-shaped steel columns under neutral salt spray environment[J]. Journal of Building Structures, 2019, 40(1): 49.
[13] NAKAI T, MATSUSHITA H, YAMAMOTO N, et al. Effect of pitting corrosion on local strength of hold frames of bulk carriers (1st report)[J]. Marine Structures, 2004, 17(5): 403.
[14] WANG Renhua, SHENOI R A. Experimental and numerical study on ultimate strength of steel tubular members with pitting corrosion damage[J]. Marine Structures, 2019, 64: 124.
[15] MELCHERS R E. Predicting long-term corrosion of metal alloys in physical infrastructure[J]. npj Materials Degradation, 2019, 3(4): 1.
[16] FRANGOPOL D M, TSOMPANAKIS Y. Maintenance and safety of aging infrastructure[M]. Boca Raton, FL: CRC Press, 2014: 32.
[17] 王振尧, 于国才, 韩薇. 钢的大气暴露腐蚀与室内模拟加速腐蚀的相关性[J]. 腐蚀科学与防护技术, 2004, 16(2): 70.
WANG Zhenyao, YU Guocai, HAN Wei. Investigation on interrelation of indoor accelerated corrosion and atmospheric exposure corrosion of steels[J]. Corrosion Science and Protection Technology, 2004, 16(2): 70.
[18] FABIS P, BROWN C, ROCKETT T, et al. An infrared and Raman spectroscopy study of the corrosion products on carbon steel and weathering steel[J]. Oxidation of Metals, 1981, 16(5): 399.
[19] JEANNIN M, CALONNEC D, SABOT R, et al. Role of a clay sediment deposit on the passivity of carbon steel in 0.1 mol·dm-3 NaHCO3 solutions[J]. Electrochimica Acta, 2011, 56(3): 1466
[20] CHEN Anna, CAO Fahe, LIAO Xiaoning, et al. Study of pitting corrosion on mild steel during wet-dry cycles by electrochemical noise analysis based on chaos theory[J]. Corrosion Science, 2013, 66: 183.
[21] 党丽华.模拟典型海洋大气环境中Q235钢初期腐蚀特征研究[D].天津: 天津大学, 2014
DANG Lihua. The initial corrosion characteristic research of Q235 steel in simulated typical marine atmospheric environment[D]. Tianjin: TianjinUniversity, 2014
[22] LEBOZEC N, BLANDIN N, THIERRY D. Accelerated corrosion tests in the automotive industry: a comparison of the performance towards cosmetic corrosion[J]. Materials and Corrosion, 2008, 59(11): 889.
[23] 王海涛, 韩恩厚, 柯伟. 碳钢、低合金钢大气腐蚀的灰色模型预测及灰色关联分析[J]. 腐蚀科学与防护技术, 2006, 18(4): 278.
WANG Haitao, HAN Enhou, KE Wei. Gray model and gray relation analysis for atmospheric corrosion of carbon steel and low alloy steel[J]. Corrosion Science and Protection Technology, 2006, 18(4): 278.
[24] ROBERGE P R, KLASSEN R D, HABERECHT P W. Atmospheric corrosivity modeling—a review[J]. Materials and Design, 2002, 23(3): 321.
[25] 王秀静, 陈克勤, 张炬, 等. 金属大气暴露与模拟加速腐蚀结果相关性探讨[J]. 装备环境工程, 2012(1): 94.
WANG Xiujing, CHEN Keqin, ZHANG Ju, et al. Investigation on correlation of atmospheric exposure test and accelerated corrosion test of metals[J]. Equipment Environmental Engineering, 2012(1): 94.
[26] TIAN Huiyun, WANG Xin, CUI Zhongyu, et al. Electrochemical corrosion, hydrogen permeation and stress corrosion cracking behavior of E690 steel in thiosulfate-containing artificial seawater[J]. Corrosion Science, 2018, 144: 145.
[27] CHEN Jie, DIAO Bo, HE Jingling, et al. Equivalent surface defect model for fatigue life prediction of steel reinforcing bars with pitting corrosion[J]. International Journal of Fatigue, 2018, 110: 153.
[28] XU Shanhua, WANG Hao, LI Anbang, et al. Effects of corrosion on surface characterization and mechanical properties of butt-welded joints[J]. Journal of Constructional Steel Research, 2016, 126: 50.
[29] KAINUMA S, JEONG Y S, AHN J H. Investigation on the stress concentration effect at the corroded surface achieved by atmospheric exposure test[J]. Materials Science and Engineering A, 2014, 602: 89.
[30] LYU Shengli, MU Quanxu, GAO Xiaosheng, et al. Influence of morphology of corrosion on fracture initiation in an aluminum alloy[J]. Materials and Design, 2013, 45: 96.
[31] 董杰, 董俊华, 韩恩厚, 等. 低碳钢在模拟酸雨大气条件下的锈蚀演化[J]. 腐蚀科学与防护技术, 2009, 21(1): 1.
DONG Jie, DONG Junhua, HAN Enhou, et al. Rusting evolvement of mild steel under wet/dry cyclic condition with pH 4 NaHSO3 solution[J]. Corrosion Science and Protection Technology, 2009, 21(1): 1.
[32] SUZUMURA K, NAKAMURA S I. Environmental factors affecting corrosion of galvanized steel wires[J]. Journal of Materials in Civil Engineering, 2004, 16(1): 1.
[33] 唐子龙, 李超, 李辉. NaCl液膜下碳钢腐蚀速率及其与环境因素的关联性[J]. 中国腐蚀与防护学报, 2010, 30(1): 67.
TANG Zilong, LI Chao, LI Hui. Corrosion rate of carbon steel under liquid layer containing Cl-and its correlation with environment control factors[J]. Journal of Chinese Society for Corrosion and Protection, 2010, 30(1): 67.
[34] AUWAL S T, RAMESH S, YUSOF F, et al. A review on laser beam welding of copper alloys[J]. International Journal of Advanced Manufacturing Technology, 2018, 96: 475.
[35] 焦让杰. 关于范特霍夫规则的讨论[J]. 北京林业大学学报, 1987(4): 81.
JIAO Rangjie. Discussion of Vant Hoff rule[J]. Journal of Beijing Forestry University, 1987(4): 81.
[36] 张映明. 与范特霍夫规则相关的两个问题[J]. 化学教学, 2014(4): 74.
ZHANG Yingming. Two problems related to Vant Hoff rule[J]. Education in Chemistry, 2014(4): 74.
[37] 黎学明, 陈大华, 陈建文, 等. 模拟酸雨溶液中温度对桥梁索缆镀锌钢丝腐蚀行为影响[J]. 腐蚀科学与防护技术, 2010, 22(1): 14.
LI Xueming, CHEN Dahua, CHEN Jianwen, et al. Effect of temperature on corrosion behavior of galvanized steel bridge wires in simulated acid rain[J]. Corrosion Science and Protection Technology, 2010, 22(1): 14.
[38] 李晓刚. 金属大气腐蚀初期行为与机理[M]. 北京: 科学出版社, 2009: 56.
LI Xiaogang. Initial behavior and mechanism of metal atmospheric corrosion[M]. Beijing: CSPM, 2009: 56.
[39] 王玲, 牟献良, 朱蕾, 等. 大气环境腐蚀性分类分级研究综述[J]. 装备环境工程, 2010, 7(6): 24.
WANG Ling, MU Xianliang, ZHU Lei, et al. Review of atmospheric corrosivity classification[J]. Equipment Environmental Engineering, 2010, 7(6): 24.
[40] 屈庆, 严川伟, 张蕾, 等. NaCl和SO2在A3钢初期大气腐蚀中的协同效应[J]. 金属学报, 2002, 38(10): 1062.
QU Qing, YAN Chuanwei, ZHANG Lei, et al. Synergism of NaCl and SO2 in the initial atmospheric corrosion of A3 steel[J]. Acta Metallurgica Sinica, 2002, 38(10): 1062.
[41] DAWSON J L, FERREIRA M G S. Electrochemical studies of the pitting of austenitic stainless steel[J]. Corrosion Science, 1986, 26(12): 1009.
[42] CORVO F, MINOTAS J, DELGADO J, et al. Changes in atmospheric corrosion rate caused by chloride ions depending on rain regime[J]. Corrosion Science, 2005, 47(4): 883.
[43] ROZENFELD I L. Atmospheric corrosion of metals[M]. Houston, TX: National Association of Corrosion Engineers, 1972: 15.
[44] 刘月娥, 林翠, 赵晴. 碳钢在SO2大气环境中的腐蚀行为[J]. 中国腐蚀与防护学报, 2010, 30(1): 51.
LIU Yue'e, LIN Cui, ZHAO Qing. Corrosion behavior of mild steel in atmosphere containing SO2[J]. Journal of Chinese Society for Corrosion and Protection, 2010, 30(1): 51.
[45] 姚伟达, 孔学云, 刘禹铭, 等. 油气田开发中H2S对钢材腐蚀因素分析与预防[J]. 石化技术, 2016, 23(3): 255.
YAO Weida, KONG Xueyun, LIU Yuming, et al. Analysis and prevention of steel corrosion by H2S in oil and gas field development[J]. Petrochemical Industry Technology, 2016, 23(3): 255.
[46] HAAGENRUD S, OTTAR B. Long range transport of air pollutants and corrosion effects[C]//Proceedings of the 7th Scandinavian Corrosion Congress. Trondheim, Norway: National Academy of Sciences, 1975: 102
[47] 赵婷婷, 徐善华, 孔正义, 等. 碳钢人工加速腐蚀试验研究[J]. 水利与建筑工程学报, 2010, 8(2): 13.
ZHAO Tingting, XU Shanhua, KONG Zhengyi, et al. Study on accelerated corrosion tests of carbon steel[J]. Journal of Water Resources and Architectural Engineering, 2010, 8(2): 13.
[48] 周常蓉, 朱卫华. 海洋环境下钢结构的腐蚀机理[J]. 科协论坛, 2008(9): 59.
ZHOU Changrong, ZHU Weihua. Corrosion mechanism of steel structures in marine environment[J]. Science and Technology Association Forum, 2008(9): 59.
[49] 董杰, 董俊华, 韩恩厚, 等. 低碳钢带锈电极的腐蚀行为[J]. 腐蚀科学与防护技术, 2006, 18(6): 414.
DONG Jie, DONG Junhua, HAN Enhou, et al. Corrosion behavior of rusted mild steel under means of wet/dry alternate conditions[J]. Corrosion Science and Protection Technology, 2006, 18(6): 414.
[50] 苏铁军, 曹发, 杨帆, 等. 滴定法与失重法测定碳钢腐蚀速率的比较研究[J]. 中国无机分析化学, 2018, 8(1): 29.
SU Tiejun, CAO Fa, YANG Fan, et al. A comparative study of corrosion rate measurement using titration and weight loss methods[J]. Chinese Journal of Inorganic Analytical Chemistry, 2018, 8(1): 29.
[51] 侯迪, 罗永峰.钢结构腐蚀问题研究进展[C]//绿色建筑与钢结构技术论坛论文集.兰州: 工业建筑, 2017: 141
HOU Di, LUO Yongfeng. Research progress on corrosion of steel structures[C]//Proceedings of Technical Forum on Green Building and Steel Structure. Lanzhou: Industrial Construction, 2017: 141
[52] ENGLEHARDT G, MACDONALD D D. Deterministic prediction of pit depth distribution[J]. Corrosion, 1998, 54(6): 469.
[53] KREYSA G, ECKERMANN R. DECHEMA corrosion handbook[M]. New York, NY: VCH, 1992: 85.
[54] FELIU S, MORCILLO M, FELIU S, J r. The prediction of atmospheric corrosion from meteorological and pollution parameters—Ⅱ. Long-term forecasts[J]. Corrosion Science, 1993, 34(3): 415.
[55] MELCHERS R E. Modelling of marine immersion corrosion for copper-bearing steels[J]. Corrosion Science, 2003, 45(10): 2307.
[56] TIDBLAD J, MIKHAILOV A A, KUCERA V. Application of a model for prediction of atmospheric corrosion in tropical environments[C]//Proceedings of Marine Corrosion in Tropical Environments. West Conshohocken, PA: ASTM, 2000: 3
[57] DEAN S W, REISER D B. Analysis of long-term atmospheric corrosion results from ISO CORRAG program[C]//Proceedings of Outdoor Atmospheric Corrosion. West Conshohocken, PA: ASTM, 2002: 16
[58] ALCáNTARA J, FUENTE D, CHICO B, et al. Marine atmospheric corrosion of carbon steel: a review[J]. Materials, 2017, 10(4): 406.
[59] LEYGRAF C, WALLINDER I O, TIDBLAD J, et al. Atmospheric corrosion[M]. 2nd ed. Hoboken: John Wiley & Sons, 2016: 88.
[60] TAMMANN G. Lehrbuch der metallographie[M]. Leipzig: Leopold Voss, 1923: 12.
[61] SOUTHWELL C R, FORGESON B W, ALEXANDER A L. Corrosion of metals in tropical environments (part 2—atmospheric corrosion of ten structural steels)[J]. Corrosion, 1958, 14(9): 55.
[62] SCHUMACHER M. Seawater corrosion handbook[M]. Park Ridge, NJ: Noyes Data Corp, 1979: 16.
[63] BEHRENS D. DECHEMA corrosion handbook: corrosive agents and their interaction with materials[M]. Frankfurt am Main: DECHEMA VCH, 1987: 28.
[64] HOU Wentai, LIANG Caifeng. Atmospheric corrosion prediction of steels[J]. Corrosion, 2004, 60(3): 313.
[65] MORCILLO M, SIMANCAS J, FELIU S. Long-term atmospheric corrosion in Spain: results after 13-16 years of exposure and comparison with worldwide data[C]//Proceedings of Atmospheric Corrosion. West Conshohocken, PA: ASTM, 1995: 195
[66] SOARES C G, GARBATOV Y, ZAYED A, et al. Non-linear corrosion model for immersed steel plates accounting for environmental factors[C]//Proceedings of 2005 SNAME Maritime Technology Conference & Expo and Ship Production Symposium. Houston, TX: The Society of Naval Architects and Marine Engineers, 2005: 306
[67] SOARES C G, GARBATOV Y. Reliability of maintained, corrosion protected plates subjected to non-linear corrosion and compressive loads[J]. Marine Structures, 1999, 12(6): 425.
[68] PANAYOTOVA M, GARBATOV Y, SOARES C G. Factor influencing atmospheric corrosion and corrosion in closed spaces of marine steel structures[C]//Proceedings of the International Conference on Marine Science and Technology. Varna: University of Mining and Geology, 2004: 286
[69] QIN Shengping, CUI Weicheng. Effect of corrosion models on the time-dependent reliability of steel plated elements[J]. Marine Structures, 2003, 16(1): 15.
[70] JIA Chen, SHAO Yongsong, GUO Lanhui, et al. Incipient corrosion behavior and mechanical properties of low-alloy steel in simulated industrial atmosphere[J]. Construction and Building Materials, 2018, 187: 1242.
[71] MCCUEN R H, ALBRECHT P. Composite modeling of atmospheric corrosion penetration data[C]//Proceedings of Application of Accelerated Corrosion Tests to Service Life Prediction of Materials. Miami, FL: ASTM, 1992: 65
[72] ALBRECHT P, HALL T T. Atmospheric corrosion resistance of structural steels[J]. Journal of Materials in Civil Engineering, 2003, 15(1): 2.
[73] SCHUMACHER M. Seawater corrosion handbook[M]. Park Ridge, NJ: Noyes Data Corp, 1979: 38.
[74] PAIK J K, MELCHERS R E. Condition assessment of aged structures[M]. Cambridge: Woodhead Publishing, 2008: 77.
[75] MIKHAILOVSKⅡ Y N, STREKALOV P V, AGAFONOV V V. A model of atmospheric corrosion of metals allowing for meteorological and aerochemical characteristics[J]. Prot Metarials, 1980, 16(4): 308.
[76] MELCHERS R E. Modeling of marine immersion corrosion for mild and low-alloy steels—part 2: uncertainty estimation[J]. Corrosion, 2003, 59(4): 335.
[77] MELCHERS R E. Mathematical modelling of the diffusion controlled phase in marine immersion corrosion of mild steel[J]. Corrosion Science, 2003, 45(5): 923.
[78] MELCHERS R E. Modeling of marine immersion corrosion for mild and low-alloy steels—part 1: phenomenological model[J]. Corrosion, 2003, 59(4): 319.
[79] MELCHERS R E, WELLS T. Models for the anaerobic phases of marine immersion corrosion[J]. Corrosion Science, 2006, 48(7): 1791.
[80] PAIK J K, MELCHERS R E. Condition assessment of aged structures[M]. Cambridge: Woodhead Publishing, 2008: 85.
[81] MELCHERS R E. The transition from marine immersion to coastal atmospheric corrosion for structural steels[J]. Corrosion, 2007, 63(6): 500.
[82] MELCHERS R E. Long-term corrosion of cast irons and steel in marine and atmospheric environments[J]. Corrosion Science, 2013, 68: 186.
[83] MELCHERS R E. Bi-modal trends in the long-term corrosion of copper and high copper alloys[J]. Corrosion Science, 2015, 95: 51.
[84] MELCHERS R E. Bi-modal trend in the long-term corrosion of aluminium alloys[J]. Corrosion Science, 2014, 82: 239.
[85] PETERSEN R B, MELCHERS R E. Long term corrosion of buried cast iron pipes in native soil[C]//Proceedings of the Annual Conference of the Australasian Corrosion Association 2014: Corrosion and Prevention 2014. Darwin: Australasian Corrosion Association, 2014: 28
[86] PETERSEN R B, MELCHERS R E. The bi-modal corrosion behaviour of ferrous metals buried in soil[C]//Proceedings of the Annual Conference of the Australasian Corrosion Association 2015: Corrosion and Prevention 2015. Adelaide: Australasian Corrosion Association, 2015: 15
[87] FORGESON B W, SOUTHWELL C R, ALEXANDER A L. Corrosion of metals in tropical environments(part 1—five non-ferrous metals and a structural steel)[J]. Corrosion, 1958, 14(2): 33.
[88] SZKLARSKA S Z. Pitting corrosion of aluminum[J]. Corrosion Science, 1999, 41(9): 1743.
[89] FRANKEL G S. Pitting corrosion of metals: a review of the critical factors[J]. Journal of the Electrochemical Society, 1998, 145(6): 2186.
[90] GALVELE J R. Transport processes and the mechanism of pitting of metals[J]. Journal of the Electrochemical Society, 1976, 123(4): 464.
[91] WRANGLEN G. Pitting and sulphide inclusions in steel[J]. Corrosion Science, 1974, 14(5): 331.
[92] MERCER A D, LUMBARD E A. Corrosion of mild steel in water[J]. British Corrosion Journal, 1995, 30(1): 43.
[93] PHULL B S, PIKUL S J, KAIN R M. Seawater corrosivity around the world: results from five years of testing[C]//Proceedings of Corrosion testing in natural waters: second volume. West Conshohocken, PA: ASTM, 1997: 34
[94] JEFFREY R, MELCHERS R E. The changing topography of corroding mild steel surfaces in seawater[J]. Corrosion Science, 2007, 49(5): 2270.
[95] XU Yang, LI Hui, LI Shunlong, et al. 3-D modelling and statistical properties of surface pits of corroded wire based on image processing technique[J]. Corrosion Science, 2016, 111: 275.
[96] CARPEN L, HAKKARAINEN A, SARPOLA M, et al. Localized corrosion risk of stainless steels under evaporative conditions[C]//Proceedings of Corrosion 2007. Nashville, TN: NACE International, 2007: 197
[97] MELCHERS R E. Extreme value statistics and long-term marine pitting corrosion of steel[J]. Probabilistic Engineering Mechanics, 2008, 23(4): 482.
[98] FUENTE D D L, OTERO H E, MORCILLO M. Studies of long-term weathering of aluminium in the atmosphere[J]. Corrosion Science, 2007, 49(7): 3134.
[99] MELCHERS R E. Pitting corrosion of mild steel in marine immersion environment—part 1: maximum pit depth[J]. Corrosion, 2004, 60(9): 824.
[100] VELAZQUEZ J C, CALEYO F, VALOR A, et al. Predictive model for pitting corrosion in buried oil and gas pipelines[J]. Corrosion, 2009, 65(5): 332.
[101] ALAMILLA J L, ESPINOSA-MEDINA M A, SOSA E. Modelling steel corrosion damage in soil environment[J]. Corrosion Science, 2009, 51(11): 2628.
[102] MELCHERS R E. A review of trends for corrosion loss and pit depth in longer-term exposures[J]. Corrosion and Materials Degradation, 2018, 1(1): 42.
[103] MELCHERS R E, AHAMMED M. Maximum pit depth variability in water injection pipelines[C]//Proceedings of the 28th International Ocean and Polar Engineering Conference. International Society of Offshore and Polar Engineers. Sapporo: ISOPE, 2018: 40
[104] DARMAWAN M. Pitting corrosion model for reinforced concrete structures in a chloride environment[J]. Magazine of Concrete Research, 2010, 62(2): 91.
[105] CHAVES I A, MELCHERS R E. Extreme value analysis for assessing structural reliability of welded offshore steel structures[J]. Structural Safety, 2014, 50: 9.
[106] AZIZ P M. Application of the statistical theory of extreme values to the analysis of maximum pit depth data for aluminum[J]. Corrosion, 1956, 12(10): 35.
[107] VALOR A, RIVAS D, CALEYO F, et al. Discussion: statistical characterization of pitting corrosion—part 1: data analysis and part 2: probabilistic modeling for maximum pit depth[J]. Corrosion, 2007, 63(2): 107.
[108] MELCHERS R E. Reply to discussion: statistical characterization of pitting corrosion—part 1: data analysis and part 2: probabilistic modeling for maximum pit depth[J]. Corrosion, 2007, 63(2): 112.
[109] KLEINER Y, RAJANI B, KRYS D. Performance of ductile iron pipes I: characterization of external corrosion patterns[J]. Journal of Infrastructure Systems, 2013, 19(1): 108.
[110] SHEIKH A K, BOAH J K, HANSEN D A. Statistical modeling of pitting corrosion and pipeline reliability[J]. Corrosion, 1990, 46(3): 190.
[111] LAYCOCK P J, SCARF P A. Exceedances, extremes, extrapolation and order statistics for pits, pitting and other localized corrosion phenomena[J]. Corrosion Science, 1993, 35(1/2/3/4): 135.
[112] LEADBETTER M R, LINDGREN G, ROOTZEN H. Extremes and related properties of random sequences and processes[M]. New York: Springer, 2012: 267.
[113] SCARF P A, LAYCOCK P J. Applications of extreme value theory in corrosion engineering[J]. Journal of Research of the National Institute of Standards and Technology, 1994, 99(4): 313.
[114] CASTILLO E. Extreme value theory in engineering[M]. San Diego: Elsevier, 2012: 183.
[115] CASTILLO E, GALAMBOS J, SARABIA J M. Extreme value theory[M]. New York: Springer, 1989: 181.
[116] GALAMBOS J. Extreme value theory and applications[M]. Boston: Springer, 1994: 1.
[117] ASADI Z S, MELCHERS R E. Extreme value statistics for pitting corrosion of old underground cast iron pipes[J]. Reliability Engineering and System Safety, 2017, 162: 64.
[118] ASADI Z S, MELCHERS R E. Clustering of corrosion pit depths for buried cast iron pipes[J]. Corrosion Science, 2018, 140: 92.