刘明维1,2,曾丽琴1,2,余杰1,2,梁越1,2,王俊杰2,3,杨成渝1,2
(1.重庆交通大学 国家内河航道整治工程技术研究中心,重庆 400074; 2.水利水运工程教育部重点实验室(重庆交通大学),重庆 400074;3.重庆交通大学 重庆市高校水工建筑物健康诊断技术与设备工程研究中心,重庆 400074)
摘要:
为获得内河码头钢构件防腐涂层的损伤规律,通过物理模型试验研究含沙水流条件下钢构件防腐涂层的冲蚀特性,分析涂层损伤过程,提出适于内河码头钢构件涂层冲蚀损伤模型.首先,结合长江上游含沙水流冲蚀环境条件,确定冲蚀试验参数,制备涂覆环氧沥青涂层的钢构件,按照相似比尺缩放,模拟现场码头钢构件涂层受含沙水流冲蚀4个月的情况,观察冲蚀损伤后形貌,发现现场实测和室内试验呈现出相似的破坏过程和损伤规律.然后,开展钢构件防腐涂层冲蚀特性试验,重点研究含沙水流条件下防腐涂层在不同冲角、冲蚀时间、含沙量等条件下与冲蚀量的关系.涂层冲蚀量随冲角-45°~90°呈现“中间大,两边小”的趋势,涂层最大冲蚀量出现在40°冲角左右;缓增期涂层各冲角的厚度冲蚀量与冲蚀时间近似呈现线性相关;高含沙量条件下涂层的整体冲蚀量随流速增加近似呈指数增长.最后,基于钢构件防腐涂层冲蚀试验结果和现有冲蚀理论,改进了防腐涂层冲蚀损伤模型公式,利用此公式得出在大流速下涂层的临界冲角约为40°,与试验结果较吻合.研究表明:利用该冲蚀试验,可以获得内河码头钢构件防腐涂层的损伤规律以及冲蚀特性;利用改进的损伤模型可以有效地计量水工钢构件防腐涂层的损伤量,为研发新型防腐涂层提供理论依据.
关键词: 内河码头 钢构件 防腐涂层 冲蚀试验 损伤模型
DOI:10.11918/j.issn.0367-6234.201807166
分类号:TV47
文献标识码:A
基金项目:国家自然科学基金(51479014),重庆市社会民生科技创新(cstc2017shmsA30002);四川省交通厅(2018-B-04)
Erosion characteristics and damage model of anti-corrosion coating onsteel-structure in inland river wharf
LIU Mingwei1,2,ZENG Liqin1,2,YU Jie1,2,LIANG Yue1,2,WANG Junjie2,3,YANG Chengyu1,2
(1.National Inland Waterway Improvement Engineering Research Center, Chongqing Jiaotong University, Chongqing 400074, China; 2. Key Laboratory for Hydraulic and Waterway Engineering of Ministry of Education (Chongqing Jiaotong University), Chongqing 400074, China; 3. Engineering Research Center of Diagnosis Technology and Instruments of Hydro-Construction, Chongqing Jiaotong University, Chongqing 400074, China)
Abstract:
In order to obtain the damage rule of anti-corrosion coating on steel structures of inland river, the erosion characteristics of anti-corrosion coating on steel structures under the condition of sand flow were studied by physical model test, the process of coating damage was analyzed, and the erosion damage model for steel structures’ coatings in inland river wharf was proposed. First of all, combined with the environmental conditions of the sandy water flow in the upper reaches of the Yangtze River, the erosion test parameters were determined, and the steel structures coated with an epoxy asphalt coating was prepared. According to similar scaling, the coating of the steel structure of the on-site dock was simulated by the sandy water flow for 4 months. Through observing the morphology after erosion damage, it was found that the model test and the field coating erosion test showed similar failure processes and damage patterns. Then, the physical model test was carried out, which focused on the relationship between the corrosion resistance of steel structures under different conditions of angle of attack, erosion time, and sediment concentration with sandy water flow. The coating of the maximum eclipse appeared in 40° angle of attack, and coating erosion quantity with -45°~90° angle of attack showed the tendency of "between big and small on both sides. During slow increase period, there was a linear correlation between the thickness and the erosion time of each impact angle. Under the condition of high sand concentration, the overall erosion amount of the coating increased exponentially with the increase of velocity of flow. Finally, based on the corrosion test results of steel structures’ anti-corrosion coating and the existing erosion theory, the erosion damage model of anti-corrosion coating was improved. The critical angle of attack of the coating at high flow rate was about 40°, which was in good agreement with the test results. The research shows that the damage law and erosion characteristics of the anti-corrosion coating on the steel structures in inland river wharf can be obtained by using the erosion test. The damage model of the hydraulic steel structures’ anti-corrosion coating can be effectively measured by the improved damage model, which provides a theoretical basis for the development of new anti-corrosion coatings.
Key words: inland river wharf steel structures anti-corrosion coating erosion test damage model
刘明维, 曾丽琴, 余杰, 梁越, 王俊杰, 杨成渝. 内河码头钢构件防腐涂层冲蚀特性及损伤模型[J]. 哈尔滨工业大学学报, 2019, 51(10): 115-122. DOI: 10.11918/j.issn.0367-6234.201807166.

LIU Mingwei, ZENG Liqin, YU Jie, LIANG Yue, WANG Junjie, YANG Chengyu. Erosion characteristics and damage model of anti-corrosion coating on steel-structure in inland river wharf[J]. Journal of Harbin Institute of Technology, 2019, 51(10): 115-122. DOI: 10.11918/j.issn.0367-6234.201807166.

基金项目 国家自然科学基金(51479014), 重庆市社会民生科技创新(cstc2017shmsA30002);四川省交通厅(2018-B-04) 作者简介 刘明维(1972—), 男, 博士, 教授, 博士生导师 通信作者 刘明维, mingwei_liu@126.com 文章历史 收稿日期: 2018-07-23
Contents -->Abstract Full text Figures/Tables PDF
内河码头钢构件防腐涂层冲蚀特性及损伤模型
刘明维1,2


1. 重庆交通大学 国家内河航道整治工程技术研究中心, 重庆 400074;
2. 水利水运工程教育部重点实验室(重庆交通大学),重庆 400074;
3. 重庆交通大学 重庆市高校水工建筑物健康诊断技术与设备工程研究中心, 重庆 400074
收稿日期: 2018-07-23
基金项目: 国家自然科学基金(51479014), 重庆市社会民生科技创新(cstc2017shmsA30002);四川省交通厅(2018-B-04)
作者简介: 刘明维(1972—), 男, 博士, 教授, 博士生导师
通信作者: 刘明维, mingwei_liu@126.com
摘要: 为获得内河码头钢构件防腐涂层的损伤规律, 通过物理模型试验研究含沙水流条件下钢构件防腐涂层的冲蚀特性, 分析涂层损伤过程, 提出适于内河码头钢构件涂层冲蚀损伤模型.首先, 结合长江上游含沙水流冲蚀环境条件, 确定冲蚀试验参数, 制备涂覆环氧沥青涂层的钢构件, 按照相似比尺缩放, 模拟现场码头钢构件涂层受含沙水流冲蚀4个月的情况, 观察冲蚀损伤后形貌, 发现现场实测和室内试验呈现出相似的破坏过程和损伤规律.然后, 开展钢构件防腐涂层冲蚀特性试验, 重点研究含沙水流条件下防腐涂层在不同冲角、冲蚀时间、含沙量等条件下与冲蚀量的关系.涂层冲蚀量随冲角-45°~90°呈现“中间大, 两边小”的趋势, 涂层最大冲蚀量出现在40°冲角左右;缓增期涂层各冲角的厚度冲蚀量与冲蚀时间近似呈现线性相关;高含沙量条件下涂层的整体冲蚀量随流速增加近似呈指数增长.最后, 基于钢构件防腐涂层冲蚀试验结果和现有冲蚀理论, 改进了防腐涂层冲蚀损伤模型公式, 利用此公式得出在大流速下涂层的临界冲角约为40°, 与试验结果较吻合.研究表明:利用该冲蚀试验, 可以获得内河码头钢构件防腐涂层的损伤规律以及冲蚀特性;利用改进的损伤模型可以有效地计量水工钢构件防腐涂层的损伤量, 为研发新型防腐涂层提供理论依据.
关键词: 内河码头 钢构件 防腐涂层 冲蚀试验 损伤模型
Erosion characteristics and damage model of anti-corrosion coating on steel-structure in inland river wharf
LIU Mingwei1,2


1. National Inland Waterway Improvement Engineering Research Center, Chongqing Jiaotong University, Chongqing 400074, China;
2. Key Laboratory for Hydraulic and Waterway Engineering of Ministry of Education (Chongqing Jiaotong University), Chongqing 400074, China;
3. Engineering Research Center of Diagnosis Technology and Instruments of Hydro-Construction, Chongqing Jiaotong University, Chongqing 400074, China
Abstract: In order to obtain the damage rule of anti-corrosion coating on steel structures of inland river, the erosion characteristics of anti-corrosion coating on steel structures under the condition of sand flow were studied by physical model test, the process of coating damage was analyzed, and the erosion damage model for steel structures' coatings in inland river wharf was proposed. First of all, combined with the environmental conditions of the sandy water flow in the upper reaches of the Yangtze River, the erosion test parameters were determined, and the steel structures coated with an epoxy asphalt coating was prepared. According to similar scaling, the coating of the steel structure of the on-site dock was simulated by the sandy water flow for 4 months. Through observing the morphology after erosion damage, it was found that the model test and the field coating erosion test showed similar failure processes and damage patterns. Then, the physical model test was carried out, which focused on the relationship between the corrosion resistance of steel structures under different conditions of angle of attack, erosion time, and sediment concentration with sandy water flow. The coating of the maximum eclipse appeared in 40° angle of attack, and coating erosion quantity with -45°~90° angle of attack showed the tendency of "between big and small on both sides. During slow increase period, there was a linear correlation between the thickness and the erosion time of each impact angle. Under the condition of high sand concentration, the overall erosion amount of the coating increased exponentially with the increase of velocity of flow. Finally, based on the corrosion test results of steel structures' anti-corrosion coating and the existing erosion theory, the erosion damage model of anti-corrosion coating was improved. The critical angle of attack of the coating at high flow rate was about 40°, which was in good agreement with the test results. The research shows that the damage law and erosion characteristics of the anti-corrosion coating on the steel structures in inland river wharf can be obtained by using the erosion test. The damage model of the hydraulic steel structures' anti-corrosion coating can be effectively measured by the improved damage model, which provides a theoretical basis for the development of new anti-corrosion coatings.
Keywords: inland river wharf steel structures anti-corrosion coating erosion test damage model
由于存在浅覆盖层及深水施工等问题, 中国内河特别是长江上游框架码头下部结构多采用钢管混凝土嵌岩桩型式, 下部桩基及下层纵横撑均大量使用钢结构.据统计, 中国每年因金属腐蚀造成的直接经济损失高达数千亿元, 占GDP的1%~4%, 其中水环境腐蚀损失大于33%[1].因此, 内河港口水工钢构件的防腐问题越来越重要.
目前, 中国内河钢构件防腐设计主要参考海港工程钢结构防腐规范, 以涂层保护法为主.通过对重庆果园港等大型码头水工钢构件防腐情况的现场调研发现, 码头钢构件防腐涂层经水流冲刷1 a左右, 涂层出现大范围脱落, 导致钢结构裸露腐蚀, 强度降低, 直接影响内河水工钢构件的正常使用.内河大流速(>1 m/s)含沙水流快速冲蚀防腐涂层, 是港口工程维护保养中亟待解决的重大问题.
国、内外对水轮机、涡轮机等过流件在高速浑水下的冲蚀试验以及冲蚀理论进行了众多研究.黄细彬[2]通过自研的高速浑水循环系统对含沙高速掺气水流边界剪切力和脉动压强等参数的量测, 研究了水沙气三相流的紊动特性及其对过流边界的作用问题, 建立了磨蚀率预测、控制公式; 李浩平等[3]通过分析旋转喷射式磨蚀试验原理研制了水轮机冲蚀试验设备, 分析了国内主要电站水轮机的过机流速、泥沙含量及泥沙级配等指标影响; 郭源君[4]针对水轮机等过流件冲蚀, 提出了采用弹性涂层实现回避粒子接触的抗冲蚀设计理论; 马颖等[5]依据材料属性对几种脆性和塑性材料的冲蚀理论模型进行评价分析, 并探讨了粒子性能、环境因素和材料性质等因素对冲蚀的影响; 邓军等[6]通过研究含沙水流冲蚀指出, 冲角是影响冲蚀机理的主要因素, 当流速较大时, 以低冲角下的微切削破坏为主;当流速较小且泥沙粒径较大时, 以高冲角下的冲击变形为主; Hussainova等[7]通过扫面电镜观察磨痕形貌提出了切削、梨沟磨损理论; Tilly[8]提出二次冲蚀理论, 认为冲粒破碎后将会对材料表面产生再次冲蚀, 冲粒破坏能力正比于粒子动能和破碎程度; Evans[9]提出, 材料存在弹性变形区, 在连续荷载作用下, 中间裂纹从弹性区向下径向扩展, 当载荷超过中间裂纹的极限时, 材料内部产生残余应力导致裂纹横向扩展.
但是, 针对大流速含沙水流下防腐涂层冲蚀机理的成果较少, 水工钢构件防腐涂层冲蚀特性、涂层损伤机理等研究还不够深入.本文针对内河流速大、含沙量高的环境特点, 建立室内冲蚀模型试验, 重点研究含沙水流冲蚀下涂层表面冲蚀特性以及涂层损伤过程, 分析得到了涂层损伤规律, 建立了冲蚀损伤模型, 为研发新型防腐涂层提供理论依据.
1 冲蚀试验 1.1 冲蚀环境特性分析水流速度、冲蚀周期、含沙量是影响防腐涂层冲蚀的主要因素.结合长江上游含沙水流冲蚀环境条件, 确定冲蚀试验参数如下:
1) 水流速度.三峡水库回水变动区, 在汛期, 库区水位按145 m运行, 河段水流条件呈现天然航道状态.河流含沙量最大的6~9月, 过水流量变化在12 000 ~70 000 m3/s左右.当流量为12 000 m3/s时, 表面流速为0.5~2.0 m/s;流量为40 000 m3/s时, 表面流速为0.9~2.5 m/s.综合考虑, 本试验选择0.6~2.0 m/s流速范围作为冲蚀流速.
2) 冲蚀周期.根据长江上游主要水文站水文资料[10]可知, 三峡蓄水后, 长江输沙量及含沙量依然呈现季节性变化, 含有悬移质和推移质, 主要集中在汛期, 5~10月输沙量占全年的80%~90%以上.故本试验模拟现实条件下4个月(6~9月份)的冲蚀周期.
3) 含沙量.根据长江上游的寸滩水文站多年实测资料, 并考虑试验中设备加沙条件, 本试验以2006-2015年平均含沙量约0.45 kg/m3作为原型含沙量.试验中推移质选用中值粒径D50=1.5 mm的细沙石料, 悬移质选用中值粒径d50=220 μm的沙石粉, 见表 1.
表 1
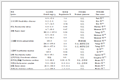
多年平均输沙量/107t 1.420
多年平均含沙量/(kg·m-3) 0.447
最大含沙量/(kg·m-3) 1.030
最小含沙量/(kg·m-3) 0.108
平均中值粒径/mm 0.027
表 1 重庆寸滩水文站2006—2015年含沙量特征值 Tab. 1 ChongqingCuntan hydrological station sediment concentration value from 2006 to 2015
1.2 冲蚀试验装置试验采用26.5 m×1.0 m×1.0 m多功能水槽系统(如图 1所示), 该系统基于变频技术的供回水系统控制, 可模拟多种形态的连续非恒定流;进口采用逆向式下出水稳态技术, 可以进行恒定流及非恒定流条件下的清水和浑水输沙实验、工程概化模型试验研究, 其最大供水能力300 L/s.
Fig. 1
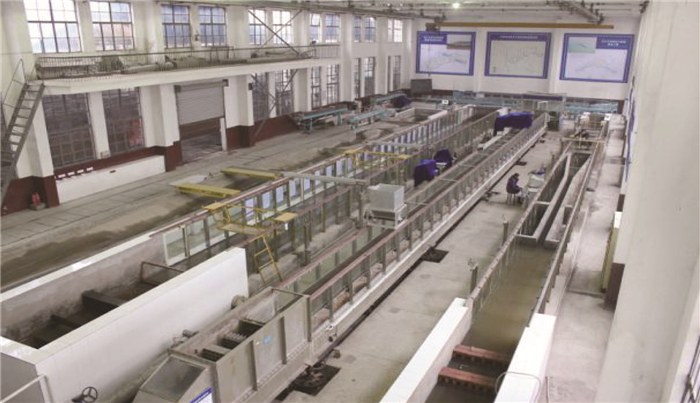
试验中的水流流场按重力相似准则考虑.根据实测数据, 果园码头桩间距为8 m, 单桩直径约2 m, 而试验水槽宽度为1 m.故单桩所受冲蚀水流影响范围按4倍桩径考虑, 拟定水槽水平比尺λl=8.
由于桩柱处于匀速流体中, 其绕流阻力分为两部分, 包括由于表面作用的压强阻力和由桩柱表面切应力引起的摩擦阻力.故模型桩需满足阻力相似准则, 单桩阻力F通常表示为
$\;F = {C_{\rm{d}}}\rho {u^2}A/2$
式中:Cd为单桩阻力系数;u为水流流速, m/s;ρ为流体密度, kg/m3;A为桩柱垂直于水流流向的投影面积, m2.将上式改写成阻力比尺为
${\lambda _F} = {\lambda _{{C_{\rm{d}}}}}{\lambda _A}\lambda _u^2$
按照相似比尺缩放后, 应保持原型与模型单桩阻力系数相等, 而实际上模型与原型雷诺数不同, 其阻力系数也不相同, 所以不能按重力比尺直接缩放制作模型桩, 应选择较细的模型桩进行代替.考虑果园港码头河流阻力系数为0.4[11], 室内模型试验阻力系数约为1.1, λvu=1, 故取桩径比尺λd=22.
码头现场涂层实测最大厚度约为1 mm, 按水平比尺λl=8进行缩放, 试验涂层涂覆厚度约为125 μm.涂层冲蚀主要受水流中泥沙颗粒影响, 其冲蚀过程遵从能量守恒原则.涂层冲蚀时间比尺λt根据单位时间内动能守恒原则计算如下:
$\begin{array}{*{20}{c}}{{I_p}/{I_m} = {\lambda _I}/{\lambda _t} \Rightarrow 1/{\lambda _t} = {\lambda _m}\lambda _u^2, }\\{{\lambda _t} = 8.}\end{array}$
式中:Ip、Im分别为原型和模型的单位动能; λm为原型和模型的泥沙颗粒质量比.故泥沙质量比尺取λm=1/8.试验模型比尺(原型:模型)见表 2.
表 2
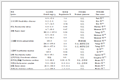
比尺符号 λl λd λu λm λt
数值 8 22 1 1/8 8
原型参数 0.50~1.85 0.45 2 880
模型参数 0.50~1.85 3.60 360
表 2 试验模型参数表 Tab. 2 Test modelparameters
本试验采用LS-501D型直读式旋桨流速仪测量模型桩前的顶冲流速, 以此流速值作为冲蚀流速.选取相邻两模型桩中靠近进水口侧的一根进行安装, 每根模型桩上安装4块涂层试件, 试验方案布置示意图如图 2所示.
Fig. 2
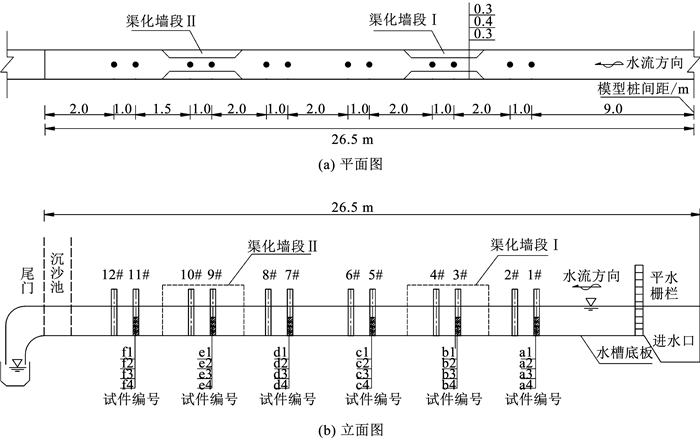
1.3 试件制备本试验选用与内河码头相同的环氧沥青涂层, 其由环氧树脂、煤焦沥青、溶剂固化剂等组成的双组份涂料.使用时将漆料(A组)和固化剂(B组)按一定比例混合搅匀并静置熟化0.5 h, 根据JTS153-3-2007《海港工程钢结构防腐蚀技术规范》规定, 采用人工刷涂.涂层表面损伤特征分析本次冲蚀试验, 标记迎水面冲角为90°, 顺时针依次为60°、45°、30°、0°及-45°(如图 3所示).
Fig. 3

利用相似比尺模拟了现场码头钢构件涂层4个月下含沙水流冲蚀情况.对比模型试验中涂层冲蚀的损伤形貌和码头涂层实测形貌, 发现了两者呈现出相似的损伤过程.图 4~6分别是试验和现场涂层在冲蚀初期、中期、后期的形貌.
Fig. 4
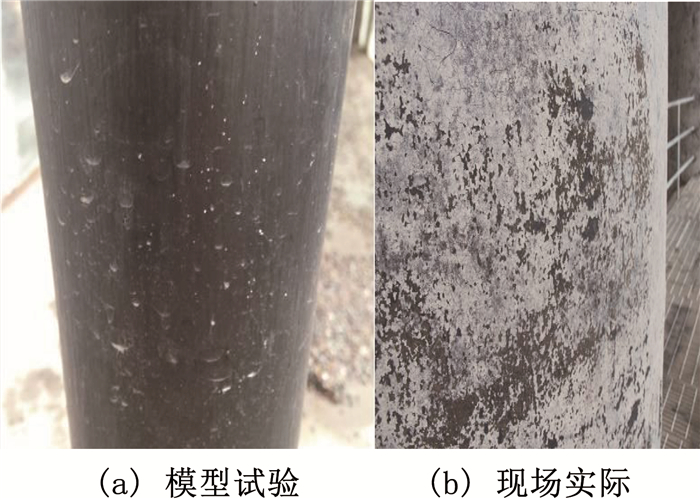
Fig. 5
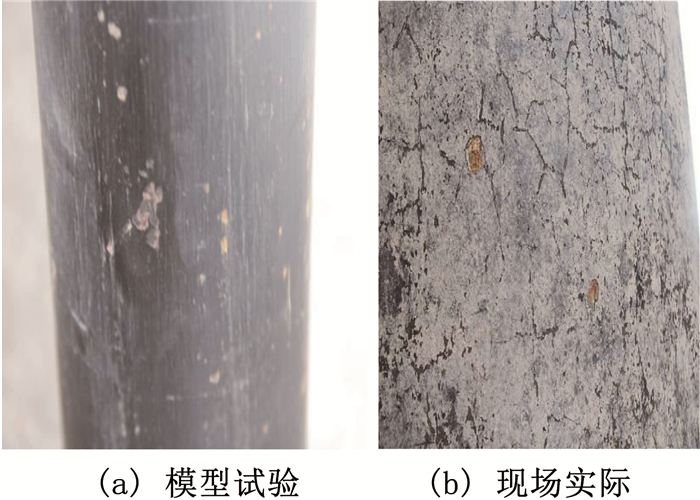
Fig. 6

初期涂层表面均出现明显的泥沙冲击和切削痕迹, 涂层表面有微裂纹萌生.中期涂层表面均出现明显较深的冲蚀坑, 部分钢管已裸露锈蚀, 涂层表面裂纹向层间和四周扩展.后期涂层已出现部分开裂、掀起, 大范围剥落, 导致钢管严重腐蚀.
泥沙颗粒的粒径和形状对涂层冲蚀程度有重要影响.一方面, 涂层表面的冲蚀损伤主要来自水流中泥沙颗粒作用, 球形或软颗粒造成的损伤极小;另一方面泥沙颗粒具有可碎性, 在冲角较大时颗粒可能会发生撞击破碎, 其碎屑将会对涂层凸起部分造成再次冲蚀.
粒径较小的泥沙颗粒惯性小, 易受水流方向的改变运动轨迹, 碰撞桩身次数较少, 大部分绕过桩身随下流运动, 不能对涂层表面造成较大凹坑或切痕;而粒径较大的颗粒则轨迹偏移有限, 碰撞频率较高, 并能造成明显的切削或冲击坑.
通过对室内试验和码头观测数据进行对比分析, 结果见表 3.
表 3
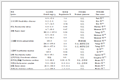
流速/(m·s-1) 含沙量/(kg·m-3) 冲蚀周期/h 破坏过程 损伤规律
室内试验 0.50~1.85 3.60 360 涂层冲蚀时期分为缓增期—加速期—减缓期 ①缓增期涂层微裂纹萌生;②加速期涂层裂纹向四周和涂层内部扩展;③减缓期涂层发生涂层剥落, 出现明显点蚀坑 涂层在45°冲蚀最大, 背水侧冲蚀最低
码头实测 0.8~1.8 0.45 6月~9月
(汛期) 涂层冲蚀时期分为前期—中期—后期 ①前期涂层表面发生细微裂痕;②中期涂层有明显冲蚀坑, 钢材裸露锈蚀;③后期涂层发生开裂、脱落 侧水面(45°~90°)涂层冲蚀损伤大, 钢管锈蚀较严重
表 3 室内试验和码头实测冲蚀损伤对比 Tab. 3 Ccomparison of model test and the field coating erosion
从表 3对比可以看出, 发现了现场实测和室内试验呈现出相似的破坏过程和损伤规律.
2 涂层冲蚀磨损测量以及评价每个冲蚀周期(30 h)结束后, 采用电子分析天平和MT600涂层测厚仪分别对涂层质量及各冲角的损失厚度进行检测, 每个测点数据测量5次取均值.通过各冲蚀条件下的涂层冲蚀量, 来反映桩身涂层在不同流速下的冲蚀量变化.
2.1 冲角根据大量实验研究[12~15], 典型的塑性材料最大冲蚀出现在冲角20°~30°之间, 脆性材料最大冲蚀在90°冲角左右, 其余材料一般表现出介于塑、脆性之间的冲蚀率变化. 图 7是涂层在含沙量3.6 kg/m3条件下冲蚀360 h后涂层厚度损失的变化.
Fig. 7
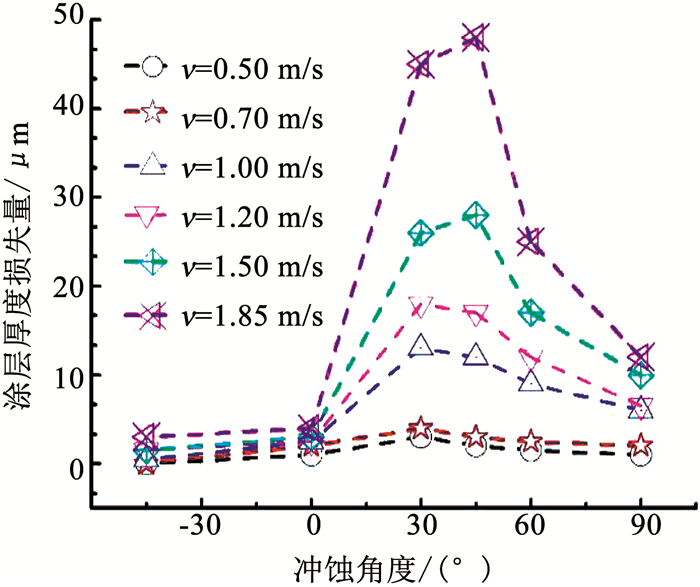
由图 7可知, 涂层在40°冲角的厚度冲蚀量最大, 并由40°向两边逐渐减小, 冲角小于40°时, 随着冲角增大, 涂层损失随之增大, 冲角大于40°时, 随着冲角增大, 涂层损失减小.这是由于含沙水流冲蚀涂层时, 受桩身绕流影响, 泥沙颗粒作用集中在15°~45°冲角范围.在不同流速下, 泥沙颗粒以低角度冲蚀居多, 其水平切应力占主导.同时, 泥沙颗粒硬度远大于涂层材料, 且多带有不规则棱角, 故进一步加强其切削作用, 导致涂层表面在低冲角下冲蚀严重.另外, 涂层在低角度冲蚀时, 涂层的抗冲蚀性主要受硬度影响, 而在高角度冲蚀时, 涂层的抗冲蚀性主要取决于其韧性.由于环氧沥青涂层属于延展性材料, 其硬度低而韧性高, 故其在低角度冲蚀的损失厚度要大于高角度.涂层最大冲蚀率出现在40°冲角左右, 整体呈现“中间大, 两边小”的趋势.
2.2 冲蚀时间涂层损伤量随时间的变化可以反映涂层冲蚀的动态过程.图 8、9分别是在1.00 m/s(低流速)、1.85 m/s(高流速)流速下涂层各冲角的厚度冲蚀量与时间的关系.
Fig. 8
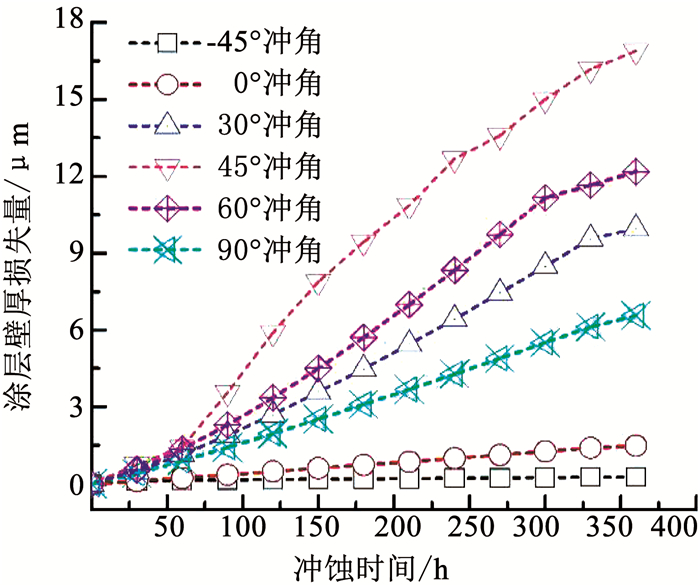
Fig. 9
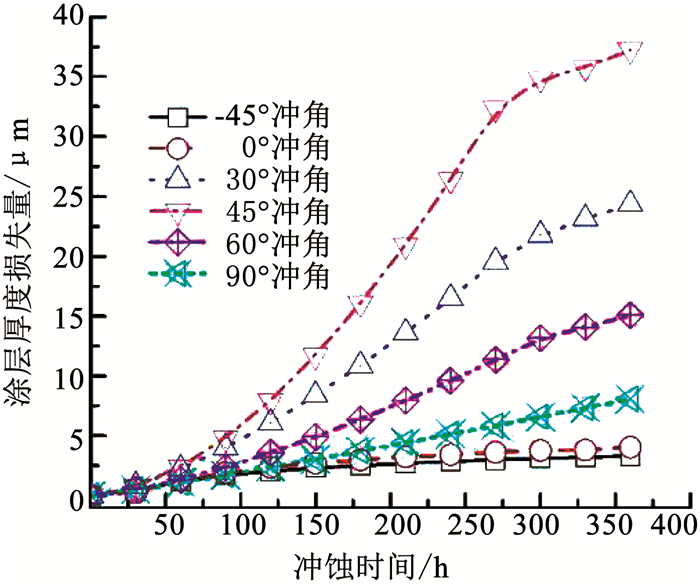
由图 8可知, 在低流速下, 涂层厚度冲蚀量表现为“缓增-加速”两阶段的变化, 其中以45°和30°冲角增长趋势最为明显, -45°和0°冲角变化趋势较为相似, 先缓慢增加, 然后趋于稳定, 且0°冲角下涂层厚度冲蚀量增长有限, 变化较为平缓.
由图 9可知, 不同流速下, 涂层在各正向冲角的厚度损失与冲蚀时间近似呈现线性相关.其冲蚀过程大致可分为3个阶段, 即缓增期—加速期—减缓期. 3个阶段的冲蚀特性如下:
1) 缓增期, 为冲蚀初期.涂层表面发生弹塑性变形, 伴随有微裂纹萌生, 表现出较长的“孕育期”.此时, 泥沙颗粒主要使涂层表面粗糙度增大, 造成材料损失较少;
2) 加速期, 涂层冲蚀率开始快速增长.随着低冲角下的切削作用和高冲角下的冲击作用相互促进, 造成涂层表面出现大量疲劳损伤;
3) 减缓期, 冲蚀率增速变缓.此时涂层表面已大范围破坏, 泥沙颗粒较难造成进一步损伤.
2.3 含沙量图 10是涂层在高含沙量(2.4~3.6 kg/m3)和低含沙量(0.4~0.8 kg/m3)两种条件下以不同流速冲蚀360 h后的涂层质量损失.
Fig. 10
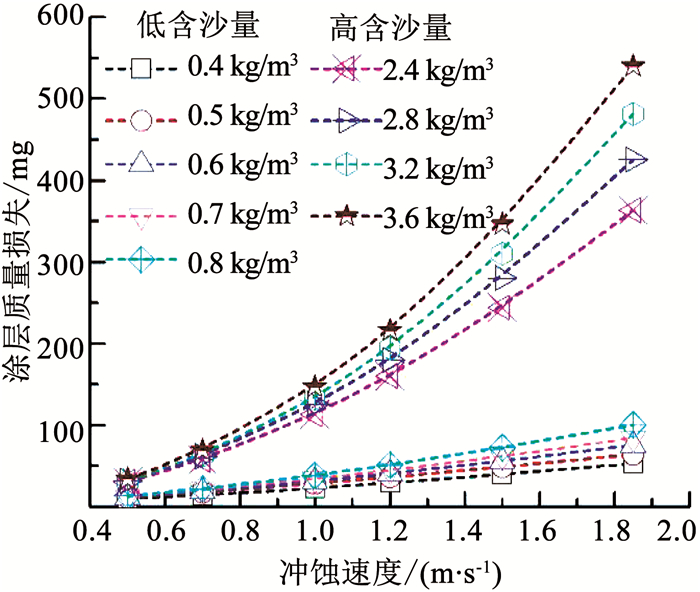
由图 10可知, 高含沙量条件下涂层的质量损失随流速增加而增大, 低含沙量条件下涂层质量损失经历较长平缓增长阶段.在低流速下, 涂层质量损失增加缓慢, 这是因为泥沙颗粒冲击涂层时动能较小, 对涂层冲击能量较弱, 而随着流速增加到某一阶段, 泥沙颗粒动能加大并且对涂层表面的撞击、切削次数增多, 导致涂层质量损失快速增长.水流中泥沙颗粒的增加, 将反复作用到涂层表面发生的塑性变形导致疲劳裂纹萌生, 同时伴随着外部颗粒冲击和切削作用的增加, 将使裂纹扩展, 导致涂层表面发生疲劳剥落, 从而冲蚀率快速增加.但含沙量与涂层冲蚀率并不呈线性相关, 这是由于含沙量增加, 其泥沙颗粒相互碰撞频率也增大, 导致沙粒能量损失, 冲蚀作用在一定程度上减弱.
3 冲蚀损伤模型分析由于泥沙颗粒受绕流影响, 均以一定冲角冲蚀涂层表面, 同时存在水平切削作用和竖向冲击作用.针对大流速含沙水流条件, 选用Bitter[16]提出改善的塑性材料冲蚀损伤公式进行计算.公式将涂层表面的冲蚀损伤量分解为变形损伤和切削损伤, 即
$\begin{array}{l}{W_t} = {W_d} + {W_c} = \\\left\{ \begin{array}{l}\frac{{{m_s}{{\left( {v\sin \;\alpha - {v_0}} \right)}^2}}}{{2\eta }} + \frac{{{m_s}{{(v\cos \;\alpha )}^2}\sin \;n\alpha }}{{2\psi }}, 0 < \alpha < {\alpha _0};\\\frac{{{m_s}{{\left( {v\sin \;\alpha - {v_0}} \right)}^2}}}{{2\eta }} + \frac{{{m_s}{{(v\cos \;\alpha )}^2}}}{{2\psi }}, {\alpha _0} < \alpha \le {\rm{ \mathsf{ π} }}/2.\end{array} \right.\end{array}$
式中:Wt为涂层总的冲蚀量; Wd为变形冲蚀磨损作用冲蚀量; Wc为切削磨损作用冲蚀量; ms为有效碰撞粒子的质量; n为水平回弹力因数; v为粒子冲击速度; v0为无冲蚀损伤的垂直临界速度; α0为最大冲蚀临界角, α0=nπ/2;η为变形冲蚀耗能系数; ψ为切削冲蚀耗能系数.
计算过程中, 由于试验条件限制, 无法直接测量出各自的切削磨损量和冲击变形量, 需要对该模型公式相关参数进行计算分析.为便于预估含沙水流条件下涂层冲蚀率, 本文将原有理论公式进行调整, 令Wt=DtρtS, ms=CsQs=CsvsS, 综合考虑, 在较低流速下, 经过足够的冲蚀时间后, 涂层也会发生冲蚀损伤, 确定最终计算式为
$\begin{array}{l}{D_t} = \\\left\{ {\begin{array}{*{20}{l}}{0.003\;6T\rho _t^{ - 1}{C_s}v_s^3\left[ {\frac{{{{\sin }^2}\alpha }}{{{\eta ^\prime }}} + \frac{{{{\cos }^2}\alpha \sin \;n\alpha }}{{{\psi ^\prime }}}} \right], 0 < \alpha < {\alpha _0};}\\{0.003\;6T\rho _t^{ - 1}{C_s}v_s^3\left[ {\frac{{{{\sin }^2}\alpha }}{{{\eta ^\prime }}} + \frac{{{{\cos }^2}\alpha }}{{{\psi ^\prime }}}} \right], {\alpha _0} < \alpha \le {\rm{ \mathsf{ π} }}/2.}\end{array}} \right.\end{array}$
式中:Dt为涂层厚度损伤量, μm;T为冲蚀时间, h;ρt为涂层材料密度, kg/m3, 取1.3×103 kg/m3;Cs为水流含沙量, kg/m3;n为水平回弹力因数;vs为水流流速, m/s;α0为最大冲蚀临界角, α0=nπ/2;α为水流流向角度;η′为变形冲蚀耗能系数, m2/s2;ψ′为切削冲蚀耗能系数, m2/s2;S为单位面积, m2;Qs为水流流量, m3/s.
对参数ψ、η、n、α0的具体计算步骤如下:
1) 从试验数据中选取v=1.85 m/s, T=270 h涂层厚度冲蚀量, 假定临界冲角30°<α0<60°, α=90°进行计算, 得出η=2.508×10-3 m2/s2;由α=60°下, Wt=Wd+Wc得出ψ=3.592×10-4 m2/s2;由α=30°, 计算出n=2.27, 即得出临界冲角α0=39.64°, 符合假定条件.
2) 再选取v=1.85 m/s, T=180、360 h的涂层厚度冲蚀量对上述计算参数进行验证, 其公式计算值和试验数据值拟合曲线对比如图 11(a)所示, 可知计算结果与试验数据基本符合.
Fig. 11
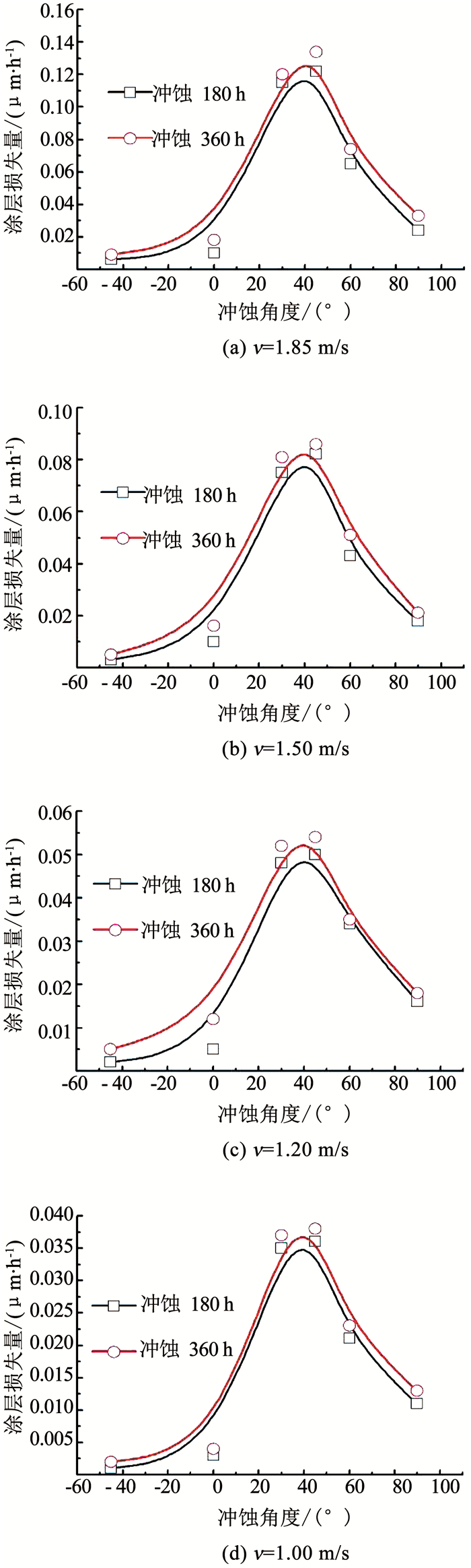
3) 重复步骤1)~2)计算3种流速条件下,即v=1.50、1.20、1.00 m/s的ψ、η、n、α0值.其结果如图 11及表 4所示.
表 4
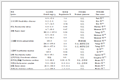
1.85 2.508 3.592 2.27 39.64
1.50 1.787 2.822 2.27 39.64
1.20 1.368 2.292 2.27 39.64
1.00 1.061 1.668 2.27 39.64
表 4 各流速条件下η、ψ、n、α0参数计算 Tab. 4 Calculation of parameters (η、ψ、n、α0) under diffent flow rates
目前认同的冲蚀速度与涂层冲蚀量规律为
$W = C{v^n}.$
式中:W为材料的冲蚀失质量;v为冲击速度;C、n分别为常数.大量实验研究表明[17], 塑性材料变幅较小, n=2.30~2.40, 脆性材料变幅较大, n=2.20~6.50, 而对于液固两相流冲蚀而言, 当冲角在20°~90°间时, n=1.62~2.12.根据改进的冲蚀损伤公式分析可知, 在不同流速下涂层的临界冲角为α0=40°, n=2.27, 与冲蚀理论结果基本一致.
切削冲蚀分量和总冲蚀量随冲角增大而增大, 并在临界冲角达到最大值, 随后逐渐减小;同时, η的变化幅度比ψ大, 变形冲蚀系数η相比切削冲蚀系数ψ对流速的变化更敏感.
4 结论1) 含沙量一定时, 在不同流速下, 涂层在40°冲角的厚度冲蚀量最大, 并由40°向两边逐渐减小, 涂层冲蚀量随冲角-45°~90°呈现“中间大, 两边小”的趋势.
2) 现场实测和室内试验呈现出相似的破坏过程和损伤规律, 冲蚀过程大致可分为3个阶段, 即缓增期、加速期和减缓期, 缓增期时, 涂层各冲角的厚度损失与冲蚀时间近似呈现线性相关.
3) 高含沙量条件下涂层的整体冲蚀量随流速增加近似呈指数增长, 低含沙量条件下涂层冲蚀量增长缓慢;含沙水流对涂层冲蚀主要表现为两方面, 一是泥沙颗粒反复作用, 引起涂层表面弹塑性疲劳变形累计及微裂纹萌生、扩展;二是腐蚀介质通过损伤裂隙渗透到防腐涂层, 并发生腐蚀反应, 导致涂层起泡、剥落.
4) 基于试验结果和现有冲蚀理论公式, 改进了冲蚀损伤公式.在大流速下涂层的临界冲角α0约为40°, 切削冲蚀分量和总冲蚀量随冲角增大而增大, 并在临界冲角达到最大值, 随后逐渐减小;同时, 变形冲蚀系数η相比切削冲蚀系数ψ对流速的变化更敏感.
参考文献
[1] 颜民, 黄桂桥. 中国水环境腐蚀试验站网工作回顾与展望[J]. 海洋科学, 2005, 29(7): 73.
YAN Min, HUANG Guiqiao. Review and expectation on national network for water environment corrosion test in China[J]. Marine Science, 2005, 29(7): 73. DOI:10.3969/j.issn.1000-3096.2005.07.018
[2] 黄细彬.高速含沙掺气水流及磨蚀机理的研究[D].南京: 河海大学, 2001
HUANG Xibin. Study on torbulent characteristics and abrasion mechanisms of high-velocity sediment-laden and aerated flow[D]. Nanjing: Hohai University, 2001 http://www.wanfangdata.com.cn/details/detail.do?_type=degree&id=Y430679
[3] 李浩平, 李峰, 卞雪, 等. 水轮机磨蚀试验设备的设计参数与总体设计[J]. 南水北调与水利科技, 2015, 13(6): 1124.
LI Haoping, LI Feng, BIAN Xue, et al. Design parameters and overall structure of turbine abrasion test equipment[J]. South-to-North Water Transfers and Water Science & Technology, 2015, 13(6): 1124. DOI:10.13476/j.cnki.nsbdqk.2015.06.022
[4] 郭源君.水机涡轮弹性涂层抗冲蚀理论及应用[D].辽宁: 辽宁工程技术大学, 2005
GUO Yuanjun. Anti-erosion theory on elastic coating of hydraulic turbine and its application[D]. Liaoning: Liaoning Technical University, 2005 http://www.wanfangdata.com.cn/details/detail.do?_type=degree&id=Y698082
[5] 马颖, 任峻, 李元东, 等. 冲蚀磨损研究的进展[J]. 兰州理工大学学报, 2005, 31(1): 21.
MA Ying, REN Jun, LI Yuandong, et al. Development of research on erosion of materials[J]. Journal of Lanzhou University of Technology, 2005, 31(1): 21. DOI:10.3969/j.issn.1673-5196.2005.01.006
[6] 邓军, 杨永全, 沈焕荣, 等. 水流含沙量对磨蚀的影响[J]. 泥沙研究, 2000(4): 65.
DENG Jun, YANG Yongquan, SHEN Huanrong, et al. The influence to abrasion of sediment concentration[J]. Journal of Sediment Research, 2000(4): 65. DOI:10.3321/j.issn:0468-155X.2000.04.015
[7] HUSSAINOVA I, JASIUK I, SARDELA M, et al. Micromechanical properties and erosive wear performance of chromium carbide based cermets[J]. Wear, 2009, 267(1): 152. DOI:10.1016/j.wear.2008.12.104
[8] TILLY G P. Erosion caused by impact of solid particles[J]. Treatise on Materials Science & Technology, 1979, 13(1): 287. DOI:10.1016/S0161-9160(13)70071-1
[9] EVANS A G. Abrasive wear of ceramics[J]. American Ceramic Society Bulletin, 1977, 56(3): 292.
[10] 陈野.长江中游水体颗粒磷与悬沙定量关系及其通量变化研究[D].武汉: 长江科学院, 2014
CHEN Ye. Research of quantitative relationship and flux changes between particle phosphorus and suspended sediment in middle reaches of Yangtze river[D]. Wuhan: Changjiang River Scientific Research Institute, 2014 http://cdmd.cnki.com.cn/Article/CDMD-82305-1014042434.htm
[11] 沈立龙.内河架空直立式码头桩柱水动力特性现场测试研究[D].重庆: 重庆交通大学, 2015
SHEN Lilong. Field testing study on pile hydrodynamic characters of inland river suspended vertical wharf[D]. Chongqing: Chongqing Jiaotong University, 2015 http://cdmd.cnki.com.cn/Article/CDMD-10618-1015328019.htm
[12] 董刚.材料冲蚀行为及机理研究[D].杭州: 浙江工业大学, 2004
DONG Gang. Study on the erosion wear mechanisms of several behaviors and materials of several materials[D]. Hangzhou: Zhejiang University of Technology, 2004 http://www.wanfangdata.com.cn/details/detail.do?_type=degree&id=Y587510
[13] FINNIE I. Erosion of surfaces by solid particles[J]. Wear, 1960, 3(2): 87. DOI:10.1016/0043-1648(60)90055-7
[14] WELLMAN R G, ALLEN C. The effects of angle of impact and material properties on the erosion rates of ceramics[J]. Wear, 1995, 186-187: 117. DOI:10.1016/0043-1648(95)07130-X
[15] FINNIE I, STEVICK G R, RIDGELY J R. The influence of impingement angle on the erosion of ductile metals by angular abrasive particles[J]. Wear, 1992, 152(1): 91. DOI:10.1016/0043-1648(92)90206-N
[16] BITTER J G A. A study of erosion phenomena[J]. Wear, 1963, 6(1): 5. DOI:10.1016/0043-1648(63)90003-6
[17] LEVY A V, CHIK P. The effects of erodent composition and shape on the erosion of steel[J]. Wear, 1983, 89(2): 151. DOI:10.1016/0043-1648(83)90240-5
[18] ARJI R, DWIVEDI D K, GUPTA S R. Sand slurry erosive wear of thermal sprayed coating of stellite[J]. Surface Engineering, 2007, 23(5): 391. DOI:10.1179/174329407X247145