1)PVDF瞬时催化及油水分离膜。针对复杂体系的油水分离问题,以机械性能和热稳定性能优异的聚偏氟乙烯(PVDF)为基膜,制备得到具有微纳米多级组装结构的PVDF-AuNPs微反应器分离膜。首先利用聚多巴胺作为膜表面“功能涂层”,对PVDF基膜进行初步修饰,然后将AuNPs微球通过动态过滤的方法负载到PVDF的指状孔内,形成微反应器。所得膜能够对含有硝基苯酚的水包油复杂体系,实现瞬时的硝基苯酚催化降解和油水分离。该方法对于将油水分离膜应用于实际含油废水处理,起到了重要的推动作用。相关工作已经发表于Chemical Engineering Journal, 2018, 334,579,王建强副研究员和吴紫阳为共同第一作者,刘富研究员为通讯作者。
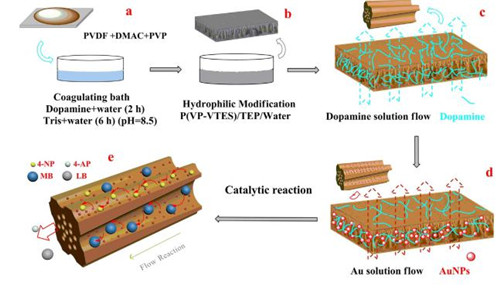
图1 PVDF指状催化反应器的制备过程
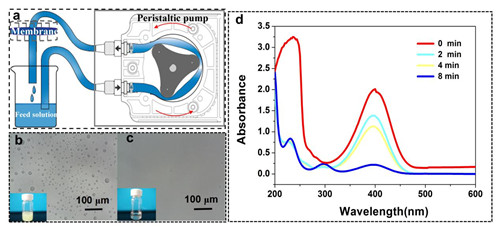
图2 PVDF膜油水分离及催化性能
2)具有超稳定刚性浸润表面的柔性PVDF油水分离膜。针对通常聚合物微孔膜的表面微纳结构不稳定、在化学腐蚀及物理损伤下易蠕变及衰减的问题,通过仿生植物根系固定土壤模型,利用微孔PVDF膜表面的微纳结构限域固定TiO2纳米粒子,制备了具有刚性界面TiO2界面的柔性PVDF微孔膜。所得膜具有优异的稳定性,能够抵抗极端物理损伤(液压、手指擦拭、液氮淬火后砂纸磨擦)、高温和苛刻的化学腐蚀(强酸、强碱、强氧化剂次氯酸钠),并且能够连续有效分离含有表面活性剂的油包水乳液。在错流模式下,通过负载超亲水纳米TiO2粒子制备的PVDF膜,可实现水包油乳液的连续分离(通量达1700

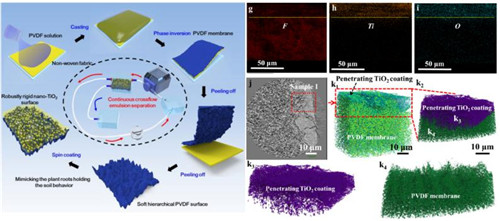
图3 超浸润刚性界面PVDF膜的制备过程
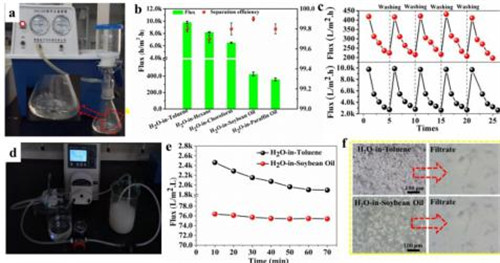
图4 刚性界面PVDF膜油水分离性能
3)超大通量静电纺丝PVDF油水分离膜。除了油水废液的复杂性和膜界面稳定性的制约,油水分离膜往往也受限于膜的低通量和易污染性。针对该问题,团队采用静电纺丝技术,通过将静电纺丝和静电喷涂相结合,制备得到了具有超高通量的PVDF纳米纤维油水分离膜,具有独特的微米级纤维及纳米级微球复合的结构。将该膜应用于高粘度的十甲基环五硅氧烷包水体系时,渗透系数高达88166±652

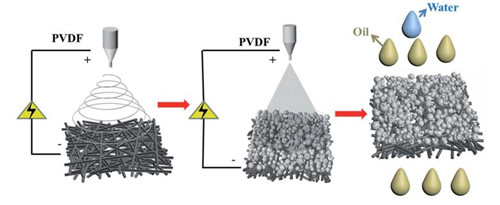
图5 超高通量PVDF纳米纤维油水分离膜的制备过程

图6 纳米纤维PVDF膜油水分离性能
上述系列研究工作受到了国家重点研发计划(2017YFB0309600)、国家自然科学基金(5161101025、51475449、51703233)、中科院青促会(2014258)和宁波市创新团队(2014B81004)等项目的资助支持。
(高分子事业部 王建强)