

东北大学 冶金学院, 辽宁 沈阳 110819
收稿日期:2021-05-24
基金项目:国家自然科学基金资助项目(52104324,52171031);中央高校基本科研业务费专项资金资助项目(N2025020)。
作者简介:黄雪驰(1990-), 男, 山东潍坊人, 东北大学讲师;
李宝宽(1963-), 男, 辽宁辽阳人, 东北大学教授,博士生导师。
摘要:为降低电渣钢锭中的总wO, 建立了预测界面传质速率的同步反应热-动力学模型, 对电渣重熔过程的氧传递行为与电磁-流动-传热-传质进行耦合分析, 并提出钢液中wO的控制方法.结果表明, 随重熔过程的进行, 熔渣中wFeO和钢液中wO均升高, 呈现重熔前期“脱氧”、后期“增氧”的现象, 渣池-电极端部和渣池-金属熔滴界面是wO升高的主要位置.当电流为1 200~1 800 A时, 熔炼相同长度电极时的钢液中wO从82.4×10-6降低到70.6×10-6; 采用惰性气体保护, 使钢液中wO从78.7×10-6降低到15.3×10-6; 使用70% CaF2+30% Al2O3渣系控制钢液中wO的效果最佳, 低wAl2O3的渣系有利于降低钢液中wO.
关键词:电渣重熔wOwFeO传质热力学平衡数学模型
Prediction and Control of Oxygen Content in Steel During Electroslag Remelting Process
HUANG Xue-chi


School of Metallurgy, Northeastern University, Shenyang 110819, China
Corresponding author: HUANG Xue-chi, E-mail: huangxuechi@163.com.
Abstract: In order to reduce the total wO in electroslag remelting(ESR)ingots, a thermo-kinetic model of simultaneous reaction is established to predict the interface mass transfer rate. The oxygen transfer behavior in ESR process coupled with electromagnetic-flow-heat-mass transfer was analyzed, and the control methods for wO of molten steel were proposed. The results show that with the progress of the remelting process, both the wFeO of the molten slag and the wO of the molten steel increase, showing the phenomenon of "deoxidation" in the early stage of remelting and "reoxidation" in the later stage. The slag pool-electrode end and slag pool-metal droplet interface are the main locations where the wO increases. As the current increases from 1200~1800 A, the wO decreases from 82.4 ×10-6 to 70.6 ×10-6. The implementation of inert gas protection can decrease the wO from 78.7 ×10-6 to 15.3 ×10-6. Using 70% CaF2+30% Al2O3 slag system to control wO of molten steel has the best effect. The slag system with low wAl2O3 is beneficial to reduce the wO of molten steel.
Key words: electroslag remeltingwOwFeOmass transferthermodynamic equilibriummathematical model
电渣重熔(electroslag remelting, ESR)是制备高端特殊钢及合金材料的特种冶炼工艺, 其利用电流通过熔渣产生的电阻热熔化自耗电极, 电极金属逐滴穿过渣池得到精炼, 形成金属熔池并在水冷结晶器中顺序凝固成铸锭[1].ESR制得的钢和合金纯度高、组织致密、成分均匀, 广泛应用于航空航天、能源、石油化工等重要领域[2].
ESR过程通常是开放式的精炼过程, 暴露在空气中的熔渣和电极发生氧化, 进而污染钢液.当电极中wO较小时, 甚至出现钢锭增氧的现象[3].氧化物夹杂作为氧在固体钢中的主要存在形式, 易引起裂纹和应力集中, 严重影响电渣锭的质量和性能[4].钢中总wO的控制始终是各国冶金工作者研究的热点问题[5].实验研究证实, 自耗电极、重熔气氛和熔渣成分都会影响钢锭总wO, 熔渣中wFeO决定了渣金间氧的迁移行为[6-7].受制于结晶器内高温、强电的严苛环境, 实验方法不仅耗时耗力, 信息十分有限, 同时难以分析流动、传热等多物理场对溶质扩散与相间化学反应的影响.在这种情况下, 数值模拟方法以其成本低廉、实施便捷、可视化等优点广泛应用于电渣冶金过程的基础研究与参数优化[8-10].
为进一步降低电渣钢中总wO, 将ESR过程的氧传递行为与电磁-流动-传热-传质多物理场进行耦合分析: 通过电极材料的高温氧化增重实验, 定量计算电极表面氧化引起熔渣中wFeO增加; 基于钢液、熔渣和空气间的界面反应热力学平衡和传质动力学理论, 提出预测界面传质速率的同步反应热-动力学模型, 揭示氧传递行为的内在机理和钢液中wO的变化规律, 从改变重熔电流、采用惰性气体保护、改变渣系组成等方面提出钢液中wO的控制方法.
1 数学模型基于有限体积法求解ESR过程中多场耦合的物理化学与宏观传输现象[11-12], 对所用数学框架和建模考量进行简述.
1.1 电磁-热-流-溶质多场耦合模型1) VOF(volume of fluid)方法: 计算区域包含互不相融的熔渣、钢液和空气三相, 基于几何重构方案追踪任意两相界面, 体积分数α和混合相的物性参数分别为
![]() | (1) |
![]() | (2) |
2) 电磁现象: 交流电磁场采用电势法进行求解, 获得时均电磁力与焦耳热密度, 并作为源项分别加入动量和能量方程[13]:
![]() | (3) |
3) 多相流动: 熔体流动由连续性方程和纳维-斯托克斯方程描述, 热浮力和电磁力为主要驱动力.采用重整化群k-ε模型描述结晶器内的弱湍流流动, 并结合增强壁面函数捕捉近壁面流动[14].
![]() | (4) |
![]() | (5) |
4) 传热: 采用焓形式的能量守恒方程计算ESR体系内的热量传递:
![]() | (6) |
5) 溶质传输: 钢液、熔渣和空气中每种组分均存在对流和扩散, 且其总量能够通过相界面化学反应增加或减少, 从而建立相应的溶质传输方程:
![]() | (7) |
1.2 同步反应热-动力学模型1.2.1 传质源项在多相共存的ESR体系中不仅包含界面化学反应和越过反应界面的传质过程, 还涉及反应物和反应产物的扩散过程.ESR过程中熔体的温度超过2 000 K, 在高温下化学反应速率极快, 普遍认为组分的扩散过程是决定传质过程的限制性环节[15].基于这一共识, 建立了氧传递过程中关键组分在钢液、熔渣和空气间迁移的传输表达式.
根据薄膜理论, 在熔渣-金属界面, 组分i的传质速率源项Si为[16]
![]() | (8) |
同理, 在熔渣-空气界面, 组分i的传质速率分别为[16]
![]() | (9) |
![]() | (10) |
1.2.2 热力学平衡以CaF2+Al2O3二元渣系为例, 考虑了O, Si, Mn, Al和Fe五种元素, 钢液、熔渣和空气间的氧传递行为如图 1所示.
图 1(Fig. 1)
![]() | 图 1 电渣重熔过程氧传递行为示意图Fig.1 Schematic diagram of oxygen transfer behavior in ESR process |
1) 熔渣-金属界面: 熔渣中的Fe2O3被还原, FeO的分解引起钢液中wO上升, 同时钢液中合金元素发生氧化, 这些氧化还原反应及热力学平衡常数如下:
![]() | (11) |
![]() | (12) |
![]() | (13) |
![]() | (14) |
![]() | (15) |
联合式(8)及式(11)~式(15), 各组分的界面分配比均可表示为钢中氧活度的函数, 进而得到各组分的传质速率, 其中aO*是唯一的未知量.基于质量守恒原理, 建立熔渣-金属界面FeO的物质守恒方程, 使该界面的传质模型封闭:
![]() | (16) |
2) 熔渣-空气界面: 熔渣中的FeO被空气氧化, 引起wFe2O3上升, 其氧化反应及热力学平衡常数为
![]() | (17) |
![]() | (18) |
1.3 数值处理ESR体系的计算域及边界如图 2所示.电流从电极流至底水箱形成供电回路, 电极端部设置零电势, 底水箱施加符合集肤效应的电势梯度.在电极端部, 电极金属受热完全熔化, 且具有30 K过热度.采用综合换热系数描述熔体-结晶器间的复杂传热, 并假定底部边界为无回流的凝固前沿.
图 2(Fig. 2)
![]() | 图 2 计算区域及边界Fig.2 Computational domain and boundaries |
电极端部设置为质量流量入口, 指定钢液中每种组分的初始质量分数, 该值与电极材质相同.假定电极中的原始氧均以氧化物夹杂的形式存在, 在电极熔化过程中不能分解, 同时在精炼过程被彻底去除.基于这一合理假设, 钢液中wO的初值为0.在与渣池接触的电极侧面同样设置为质量流量入口, 电极表面氧化层发生熔化, 假定其为100% FeO的熔渣.
几何模型及工艺参数见表 1.电极金属为304不锈钢, 其化学成分(质量分数,%)为: C 0.052, Mn 1.28, Si 0.41, Ni 8.85, Cr 17.78, Al 0.001 4, O 0.005 6.熔渣的成分(质量分数,%)为: CaF2 69.9, Al2O3 29.9, FeO 0.2.详细物性参数参考文献[11, 14].借助Fluent商业软件对各控制方程进行离散和迭代计算.使用C语言自主编译电磁场的控制方程和传质模型, 并与动量、能量和组分方程耦合.
表 1(Table 1)
![]()
| 表 1 几何模型及工艺参数 Table 1 Geometric model and process parameters |
2 电极氧化增重实验由图 1可知, 电极表面氧化层熔化也会影响熔渣中wFeO, 通过电极氧化增重实验进行定量预测.采用热重分析仪对电极材料进行恒温氧化实验, 设置4组典型的氧化温度, 分别为900, 1 000, 1 100, 1 200 ℃.实验流程为: 升温阶段以100 mL/min的流量通入氩气, 钢样以25 ℃/min的速率加热到预热温度, 然后以100 mL/min的流量通入空气, 并在预设温度保温100 min, 随后以25 ℃/min的速率降至室温.
不同温度下的热重分析如图 3所示, 不同温度下钢样的单位面积增重不断增大, 但增加速率不断减小, 氧化曲线近似抛物线.根据Kofstad理论, 金属的高温氧化动力学表达式为
![]() | (19) |
![]() | 图 3 不同温度下的热重分析曲线Fig.3 Thermogravimetric curves at different temperatures |
式中: ΔW为单位面积增重; Kp为氧化速率常数, 并满足Arrhenius定律:
![]() | (20) |
对式(20)两边取对数, 并将预设温度及相应氧化速率常数代入, 可拟合出lnKp与1/T之间的线性关系, 如图 4所示.计算得到钢样的激活能为256.14 kJ/mol, 并得到氧化速率常数随温度的变化关系.
图 4(Fig. 4)
![]() | 图 4 氧化速率常数的对数与温度倒数之间的线性关系Fig.4 Linear relationship between logarithm of oxidation rate constant and reciprocal of temperature |
假定自耗电极表面温度呈轴向分布, 离渣池越近电极表面温度越高:
![]() | (21) |
当温度低于450 ℃时, 电极表面氧化十分缓慢, 可以忽略.由式(21)计算得到从电极端部到温度为450 ℃位置的距离为1.475 m.假定电极表面可分解为若干个微小等温单元, 那么每个等温单元从初始时刻到进入渣池的ΔWi2为
![]() | (22) |

将式(20)和式(21)代入式(22)可得:
![]() | (23) |
![]() | (24) |
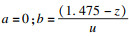
本文中的重熔速率约为0.011 kg/s, 计算得到每个微小等温单元的氧化增重约为10.37 mg/cm2.电极表面氧化层进入渣池的质量流量为
![]() | (25) |
计算得到单位长度电极表面的氧化增重所产生的FeO与熔渣的质量比为
![]() | (26) |
图 5(Fig. 5)
![]() | 图 5 模型计算值与实测值对比Fig.5 Comparison of model calculated and measured values (a)—渣池温度;(b)—钢液中wO. |
3.2 磁流体流动与温度分布电流为1 500 A时, ESR过程电流路径和焦耳热密度分布如图 6所示.各相间存在清晰的相界面(图中红线), 熔化金属向内汇聚形成熔滴, 然后逐滴滴落.焦耳热主要在电阻率较高的渣池中产生, 交流电的集肤效应使高焦耳热密度区域集中在靠近电极端部的渣池上层.电流倾向于流经电导率较大的金属熔滴, 大量电流从熔滴端部流出, 使熔滴尖端周围的熔渣同样产生大量焦耳热.
图 6(Fig. 6)
![]() | 图 6 电流1 500 A时的电流路径和焦耳热密度分布Fig.6 Current path and Joule heat density distribution under current of 1 500 A |
ESR过程的温度分布是影响精炼反应热力学平衡的关键, 如图 7所示.受电磁场和流动的影响, 高温区域主要位于靠近电极端部外侧的渣池上层; 由于部分热量用于预热和熔化电极, 电极下方熔渣的温度较低, 呈抛物线形分布; 水冷结晶器持续带走大量热量, 使紧靠其内壁面的熔渣温度迅速降低; 被高温渣池覆盖的金属熔池具有一定的过热度, 能够在轴向上形成一段未发生凝固的全液相区域.
图 7(Fig. 7)
![]() | 图 7 电流1 500 A时的温度分布Fig.7 Temperature distribution under current of 1 500 A |
电流1 500 A时ESR过程的流场特征如图 8所示, 流场能够显著影响组分的扩散过程.在熔滴剪切应力和向心电磁力的作用下, 渣池中心区域的熔渣向下流动, 在渣池上层形成了由外向内的强度较大的涡流; 结晶器的冷却作用使局部热浮力减小, 引起近壁面熔渣的下沉流动.金属熔池中的流动较弱, 驱动力主要为熔渣剪切应力和热浮力.
图 8(Fig. 8)
![]() | 图 8 电流1 500 A时的流场特征Fig.8 Flow field characteristics under current of 1 500 A |
3.3 氧传递行为在同步反应热-动力学模型中, 任意组分在相界面处的传质速率都可由已知的传质系数、氧的界面平衡活度和组分的局部质量分数计算.电流为1 500 A时, 氧的界面平衡活度aO*的分布如图 9所示, 其由界面反应[Si]-(SiO2), [Mn]-(MnO), [Al]-(Al2O3), [O]-(FeO), (FeO)-(Fe2O3)和(FeO)-O2(g)的热力学平衡共同决定, 还受温度、组分的质量分数和传质系数等多种动力学因素的影响.可知, 在渣池-电极端部(SEI)界面, aO*分布较均匀; 在渣池-金属熔滴(SDI)界面, 随高度的降低, 钢液温度升高, aO*增大; 在渣池-金属熔池(SPI)界面, aO*沿径向向外减小.当钢液中wO小于aO*所对应的wO时, 熔渣向钢液传氧, 引起钢液中wO升高, 反之, 钢液向熔渣传氧, 引起钢液中wO降低.
图 9(Fig. 9)
![]() | 图 9 电流1 500 A时氧的界面平衡活度分布Fig.9 Interfacial equilibrium activity of oxygen under current of 1 500 A (a)—渣池-空气界面、渣池-金属熔滴界面;(b)—渣池-金属熔池界面.. |
电流为1 500 A时, 各组分的界面传质速率分布如图 10所示.可知, 氧的传质速率SO为正值, 说明在熔渣-金属界面, 熔渣向钢液传氧.SEI界面和SDI界面的SO比SPI界面大2个数量级, 原因在于前两个界面的传质系数和比表面积较大.因此, SEI界面和SDI界面是影响熔渣-金属界面氧传递过程的主要位置, SO的最大值位于电极端部外侧和金属熔滴尖端.
图 10(Fig. 10)
![]() | 图 10 电流1 500 A时各组分的界面传质速率分布Fig.10 Interfacial mass transfer rate distribution of various components under current of 1 500 A (a)—[O]; (b)—(FeO); (c)—(Fe2O3); (d)—[Si]; (e)—[Mn]; (f)—[Al]. |
由图 10b和10c可知, 在渣池-空气(SAI)界面, FeO被氧化生成Fe2O3, 体现为FeO消耗(负值)、Fe2O3生成(正值); 在SEI界面和SDI界面, 同时存在合金元素的氧化反应和Fe2O3的还原反应, 而合金元素氧化引起的FeO消耗量大于Fe2O3还原引起的FeO生成量, 体现为FeO消耗(负值)、Fe2O3消耗(负值).然而, 熔渣中wFeO随熔炼进程不断升高, 说明空气直接氧化熔渣不足以引起熔渣中wFeO上升, 熔渣中FeO的主要来源是电极表面的高温氧化.
由图 10d和10e可知, 在熔渣-金属界面, Si和Mn发生氧化烧损(负值), 主要发生在SEI界面和SDI界面.由于所用渣系中wAl2O3较高, 少量的Al被吸收进钢液中, 引起钢液wAl的升高, 如图 10f所示.温度较低时, Al2O3难以分解, 因而温度较高且反应比表面积较大的SDI界面是钢液增Al的主要位置.
图 11为金属熔滴形成和滴落过程中钢液wO的演变, 这一典型周期持续约1.35 s.根据前文假设, 在熔滴形成初期, 刚熔化的电极金属中的wO较小.在图 11a中, 由于比表面积大、反应时间长, 紧靠SEI界面的钢液中wO率先升高.较高wO的钢液沿金属液膜表面向内汇聚, 使电极尖端的钢液具有更高的wO.随电极持续熔化, 熔滴加速形成, 可观察到明显的浓度梯度, 如图 11b所示.在重力和表面张力的作用下, 不断长大的熔滴呈向下滴落的趋势, 此时熔滴中的wO明显上升, 如图 11c所示.下落的熔滴并没有直接脱离电极端部, 而是形成了细长的“颈部”, 如图 11d所示.“颈部”位置的钢液与熔渣接触更加充分, 此处的wO迅速升高.SPI界面氧的传质速率较小, 但由于接触面积大、时间长, 仍使金属熔池中的wO略高于金属熔滴.
图 11(Fig. 11)
![]() | 图 11 电流1 500 A时钢液中wO随时间的变化Fig.11 Change of wO in liquid steel with time under current of 1 500 A (a)—700.88 s; (b)—701.43 s; (c)—701.64 s; (d)—701.73 s; (e)—701.80 s; (f)—701.92 s. |
由于金属熔池具有较高的湍流扩散强度, 因而熔滴在落入金属熔池后, 不同wO很快混合均匀, 如图 11e所示.在重力作用下, 与熔滴脱离的“颈部”继续发生断裂, 部分回弹并融入电极端部金属液膜中, 这种回弹使电极端部金属液膜中的wO受SEI界面和SDI界面传质过程的共同影响, 剩余的小尺寸熔滴则落入金属熔池中, 如图 11f所示.
电流为1 500 A时, 渣池中FeO分布如图 12所示.可知, 电极表面氧化层在浸入渣池后发生溶解, 引起电极端部外侧的wFeO显著上升, 在内侧涡旋流动的牵引下, FeO向电极下方的渣池中心区域扩散, 并与低wFeO的熔渣混合.在SEI界面和SDI界面, FeO参与氧化反应被消耗, 界面附近的wFeO降低; 在SPI界面, FeO的传质速率很小, 界面附近没有明显的变化; 在SAI界面, FeO被空气氧化, 使界面附近的wFeO降低, 在结晶器冷却作用下, 低wFeO的熔渣向下流动.
图 12(Fig. 12)
![]() | 图 12 1 500 A时渣池中wFeO的分布Fig.12 Distribution of wFeO in slag pool under current of 1 500 A |
3.4 钢液wO的控制基于上述分析, 从以下方向控制钢液中wO: 改变重熔电流, 采用惰性气体保护, 改变渣系组成.
3.4.1 改变重熔电流不同电流下, 熔渣中wFeO随时间的变化如图 13所示.随重熔过程的进行, 空气持续氧化电极表面和渣池表面, 使熔渣中wFeO持续升高, 但增长率呈减小趋势.根据前述的电极氧化动力学计算方法, 当电流从1200 A增大到1800 A时, 电极熔化速率提高, 单位时间(h)内电极表面氧化增重所产生的FeO占熔渣的质量分数从1.904% 增大到2.352%, 而单位长度(m)的电极表面氧化增重所产生的FeO占熔渣的质量分数从1.010% 减小到0.819%.因此, 重熔时间相同时, 熔渣中的wFeO随电流的增大而增加; 重熔电极长度相同时, 熔渣中的wFeO随着电流的增大而降低.
图 13(Fig. 13)
![]() | 图 13 不同电流下熔渣中wFeOs随时间的变化Fig.13 Changes of wFeOs in molten slag with time under different currents |
不同电流下, 钢液中的wO随时间的变化如图 14所示.可知, 钢液中的wO呈与熔渣wFeO相同的变化趋势, 对比电极原始wO, 呈现重熔前期“脱氧”、后期“增氧”的现象.在生产中, 通常将钢锭的最高wO作为评价钢锭洁净度的指标.以熔炼30 min为例, 当电流分别为1 200, 1 500和1 800 A时, 钢液中wO分别为71.39×10-6, 78.72×10-6和94.08×10-6, 说明钢液中wO随电流的增大而增加.在实际生产中, 每炉次生产的电渣锭质量是恒定的, 而不同电参数所需的熔炼时间并不一致, 因此, 以相同时间尺度分析电流对钢液中wO的影响是片面的.应以熔炼相同长度电极为基准, 以熔炼1 m电极为例, 当电流分别为1 200, 1 500和1 800 A时, 钢液中的最终wO分别为82.37×10-6, 78.72×10-6和70.64×10-6, 即钢液中wO随电流的增大而降低, 这种变化是增大的传质速率与减小的熔炼时间之间的竞争导致的.因此, 适当提高电流, 不仅有利于提高生产率, 还能够获得wO更低的钢锭.
图 14(Fig. 14)
![]() | 图 14 不同电流下钢液中wO随时间的变化Fig.14 Changes of wO in liquid steel with time under different currents |
3.4.2 采用惰性气体保护在空气和惰性气体保护下, 熔渣中wFeO随时间的变化如图 15所示, 单位时间内电极表面氧化增重所产生的FeO为0, 使熔渣中wFeO大幅降低.随重熔过程的进行, 惰性气体保护条件下的wFeO先小幅上升, 随后在较低处趋于稳定, 这主要是FeO-Al2O3反应平衡引起的.
图 15(Fig. 15)
![]() | 图 15 不同重熔气氛下熔渣中wFeO随时间的变化Fig.15 Changes of wFeO in molten slag with time under different remelting atmospheres |
在空气和惰性气体保护条件下, 钢液wO随时间的变化如图 16所示.随重熔过程的进行, 在惰性气体保护下, 钢液wO小幅升高后逐渐趋于平缓.以熔炼30 min为例, 在空气和惰性气体保护条件下, 钢液中的wO分别为78.72×10-6和15.26×10-6, 说明惰性气体保护条件下钢液wO得到明显控制, 整个重熔过程呈现“脱氧”特征.惰性气体保护只能抑制钢液增氧, 不能起到进一步降低钢液wO的作用.
图 16(Fig. 16)
![]() | 图 16 不同重熔气氛下钢液中wO随时间的变化Fig.16 Changes of wO in liquid steel with time under different remelting atmospheres |
3.4.3 改变渣系组成不同渣系下, 熔渣中wFeO随时间的变化如图 17所示.三种渣系分别为70% CaF2+30% Al2O3, 40% CaF2+30% Al2O3+30% CaO和50% CaF2+25% Al2O3+25% CaO.熔炼30 min时, 三种渣系中的wFeO分别为0.809%, 0.751% 和0.776%.在wAl2O3不变的情况下, 提高熔渣中wCaO能够增大熔渣中FeO的活度, 加快钢液中合金元素的氧化, 增加了FeO的损耗.在维持熔渣中wAl2O3∶ wCaO=1∶ 1的前提下, 降低熔渣中wAl2O3能够减小熔渣中FeO的活度, 减缓钢液中合金元素的氧化, 降低了FeO的损耗.
图 17(Fig. 17)
![]() | 图 17 不同渣系组成下熔渣中wFeO随时间的变化Fig.17 Changes of wFeO in molten slag with time under different slag compositions |
不同渣系下, 钢液wO随时间的变化如图 18所示.当熔炼30 min时, 三种渣系对应的钢液中wO分别为78.72×10-6, 98.25×10-6和90.50×10-6.在熔渣中wAl2O3不变时, 提高熔渣中wCaO能够使钢液wO显著升高, 不利于控制钢液wO.在维持熔渣中wAl2O3∶ wCaO=1∶ 1不变的前提下, 降低熔渣中wAl2O3使钢液wO降低, 有利于控制钢液wO.使用70% CaF2+30% Al2O3渣系控制钢液wO的效果最佳, 且低wAl2O3的渣系有利于降低钢液中的wO.
图 18(Fig. 18)
![]() | 图 18 不同渣系组成下钢液中wO随时间的变化Fig.18 Changes of wO in liquid steel with time under different slag compositions |
4 结论1) 熔渣中FeO的主要来源是电极表面的高温氧化, 电极氧化增重产生FeO的质量流量为10.769 mg/s, 单位长度电极表面氧化增重可使熔渣中wFeO上升0.943%.
2) 随着熔炼过程的进行, 熔渣中wFeO和钢液中的wO均升高, 呈重熔前期脱氧、后期增氧的现象.wO升高主要发生在SEI和SDI界面.
3) 1 200 ~1 800 A时, 电极氧化引起的wFeO从1.010% 降低至0.819%, 使熔炼相同长度电极时钢液中wO从82.37×10-6降低到70.64×10-6, 适当提高重熔电流, 有利于提高生产率,获得wO更低的钢锭.
4) 重熔过程中采用惰性气体保护, 可杜绝熔渣中wFeO的增加, 使钢液中wO从78.72×10-6降低到15.26×10-6.
5) 当熔渣中wAl2O3不变时, 提高wCaO不利于脱氧.当熔渣中wAl2O3∶ wCaO=1∶ 1时, 降低wAl2O3有利于脱氧.
参考文献
[1] | 李宝宽, 王强. 基于数值模拟的电渣重熔理论与技术[M]. 北京: 科学出版社, 2016: 1-2. (Li Bao-kuan, Wang Qiang. Theory and technology of electroslag remelting based on numerical simulation[M]. Beijing: Science Press, 2016: 1-2.) |
[2] | Kharicha A, Karimi-Sibaki E, Wu M, et al. Review on modeling and simulation of electroslag remelting[J]. Steel Research International, 2018, 89(sup1): 1-20. |
[3] | Chang L Z, Shi X F, Cong J Q. Study on mechanism of oxygen increase and countermeasure to control oxygen content during electroslag remelting process[J]. Ironmaking & Steelmaking, 2014, 41(3): 182-186. |
[4] | Zhang L F, Thomas B G. State of the art in the control of inclusions during steel ingot casting[J]. Metallurgical and Materials Transactions B, 2006, 37B: 733-761. |
[5] | Shi C B. Deoxidation of electroslag remelting(ESR)—a review[J]. ISIJ International, 2020, 60(6): 1083-1096. DOI:10.2355/isijinternational.ISIJINT-2019-661 |
[6] | 周德光, 徐卫国, 王平, 等. 轴承钢电渣重熔过程中氧的控制及作用研究[J]. 钢铁, 1998, 33(3): 13-17. (Zhou De-guang, Xu Wei-guo, Wang Ping, et al. Control and behavior of oxygen during electroslag remelting of bearing steel[J]. Iron and Steel, 1998, 33(3): 13-17.) |
[7] | Shi C B, Chen X C, Guo H J, et al. Assessment of oxygen control and its effect on inclusion characteristics during electroslag remelting of die steel[J]. Steel Research International, 2012, 83(5): 472-486. DOI:10.1002/srin.201100200 |
[8] | Ludwig A, Kharicha A, Wu M. Modeling of multiscale and multiphase phenomena in materials processing[J]. Metallurgical and Materials Transactions B, 2014, 45B: 36-43. |
[9] | Hernandez-Morales B, Mitchell A. Review of mathematical models of fluid flow, heat transfer, and mass transfer in electroslag remelting process[J]. Ironmaking & Steelmaking, 1999, 26(6): 423-438. |
[10] | Wang Q, He Z, Li G Q, et al. Numerical investigation of desulfurization behavior in electroslag remelting process[J]. International Journal of Heat and Mass Transfer, 2017, 104: 943-951. DOI:10.1016/j.ijheatmasstransfer.2016.09.022 |
[11] | Huang X C, Li B K, Liu Z Q, et al. Three-dimensional mathematical model of oxygen transport behavior in electroslag remelting process[J]. Metallurgical and Materials Transactions B, 2018, 49B: 709-722. |
[12] | Huang X C, Li B K, Liu Z Q, et al. Modeling of fluid flow, heat transfer and inclusion removal in electroslag remelting process with a rotating electrode[J]. International Journal of Heat and Mass Transfer, 2020, 163: 120473. DOI:10.1016/j.ijheatmasstransfer.2020.120473 |
[13] | Karimi-Sibaki E, Kharicha A, Bohacek J, et al. A dynamic mesh-based approach to model melting and shape of an ESR electrode[J]. Metallurgical and Materials Transactions B, 2015, 46B: 2049-2061. |
[14] | Wang Q, Zhao R J, Fafard M, et al. Three-dimensional magnetohydrodynamic two-phase flow and heat transfer analysis in electroslag remelting process[J]. Applied Thermal Engineering, 2015, 80: 178-186. DOI:10.1016/j.applthermaleng.2014.12.075 |
[15] | Fraser M E. Mass transfer aspects of A.C. electroslag remelting[D]. Vancouver: University of British Columbia, 1974: 8-10. |
[16] | Lou W T, Zhu M Y. Numerical simulation of desulfurization behavior in gas stirred systems based on computation fluid dynamics-simultaneous reaction model(CFD-SRM)coupled model[J]. Metallurgical and Materials Transactions B, 2014, 45B: 1706-1722. |
[17] | Lamont J C, Scott D S. An eddy cell model of mass transfer into the surface of a turbulent liquid[J]. AIChE Journal, 1970, 16(4): 513-519. DOI:10.1002/aic.690160403 |