阎峰云1,2, 张芳芳1, 李小红1, 王振1, 赵永生1
(1.省部共建有色金属先进加工与再利用国家重点实验室(兰州理工大学),兰州730050;2.甘肃省有色金属及复合材料工程技术研究中心,兰州730050)
摘要:
Mn+1AXn(简称MAX)为一种三元层状材料,当其作为金属基复合材料的增强项时,可使复合材料具有优异的力学性能和摩擦学性能,拓展了金属基复合材料的种类和应用范围。本文对MAX相的应用与性能进行了介绍,总结了MAX相增强金属基复合材料的界面对复合材料导电性和力学性能的影响,并对MAX增强金属基复合材料的摩擦学行为进行了综述,同时总结了MAX相作为增强相在协同摩擦、单相摩擦和高温摩擦中的磨损机理。最后对MAX相未来研究方向进行了展望。
关键词: 金属-非金属复合材料 Mn+1AXn相 界面 摩擦性能 导电性
DOI:10.11951/j.issn.1005-0299.20190163
分类号:TB333
文献标识码:A
基金项目:
The application and research status of MAX reinforced metal matrix composites
YAN Fengyun1,2, ZHANG Fangfang1, LI Xiaohong1, WANG Zhen1, ZHAO Yongsheng1
(1. State Key Laboratory of Advanced Processing and Recycling of Nonferrous Metals(Lanzhou University of Technology), Lanzhou 730050, China; 2. Gansu Nonferrous and Composite Materials Engineering Technology Research Center, Lanzhou 730050, China) [HJ1.7mm]
Abstract:
The Mn+1AXn (referred to as MAX) is a ternary layered material. MAX can be introduced into metallic materials as a strengthening phase to form metal-based composite materials. These composites exhibit excellent mechanical properties and tribological properties, thereby laying a theoretical basis for extending their applications. Here, the application and its performance of MAX phase are introduced. The interface effect on conductivity and mechanical properties of MAX phase reinforce metal matrix composites is summarized. The tribological behaviors of MAX reinforced metal matrix composites are overviewed. Meanwhile, the wear mechanism of the MAX phase as a reinforcing phase in synergistic friction, single phase friction, and high temperature friction is elaborated. Finally, the outlook of MAX phase in future research prospected is described.
Key words: metal-nonmetal composite Mn+1AXn phase interface tribology electrical conductivity
阎峰云, 张芳芳, 李小红, 王振, 赵永生. MAX相增强金属基复合材料的研究现状及应用[J]. 材料科学与工艺, 2020, 28(6): 88-96. DOI: 10.11951/j.issn.1005-0299.20190163.

YAN Fengyun, ZHANG Fangfang, LI Xiaohong, WANG Zhen, ZHAO Yongsheng. The application and research status of MAX reinforced metal matrix composites[J]. Materials Science and Technology, 2020, 28(6): 88-96. DOI: 10.11951/j.issn.1005-0299.20190163.

通信作者 阎峰云,E-mail:yanfy@lut.cn 作者简介 阎峰云(1962—),男,教授 文章历史 收稿日期: 2019-06-20 网络出版日期: 2020-03-23
Contents Abstract Full text Figures/Tables PDF
MAX相增强金属基复合材料的研究现状及应用
阎峰云1,2


1. 省部共建有色金属先进加工与再利用国家重点实验室(兰州理工大学),兰州730050;
2. 甘肃省有色金属及复合材料工程技术研究中心,兰州730050
收稿日期: 2019-06-20; 网络出版日期: 2020-03-23
作者简介: 阎峰云(1962—),男,教授.
通信作者: 阎峰云,E-mail:yanfy@lut.cn.
摘要: Mn+1AXn(简称MAX)为一种三元层状材料,当其作为金属基复合材料的增强项时,可使复合材料具有优异的力学性能和摩擦学性能,拓展了金属基复合材料的种类和应用范围。本文对MAX相的应用与性能进行了介绍,总结了MAX相增强金属基复合材料的界面对复合材料导电性和力学性能的影响,并对MAX增强金属基复合材料的摩擦学行为进行了综述,同时总结了MAX相作为增强相在协同摩擦、单相摩擦和高温摩擦中的磨损机理。最后对MAX相未来研究方向进行了展望。
关键词: 金属-非金属复合材料 Mn+1AXn相 界面 摩擦性能 导电性
The application and research status of MAX reinforced metal matrix composites
YAN Fengyun1,2


1. State Key Laboratory of Advanced Processing and Recycling of Nonferrous Metals (Lanzhou University of Technology), Lanzhou 730050, China;
2. Gansu Nonferrous and Composite Materials Engineering Technology Research Center, Lanzhou 730050, China
Abstract: The Mn+1AXn (referred to as MAX) is a ternary layered material. MAX can be introduced into metallic materials as a strengthening phase to form metal-based composite materials. These composites exhibit excellent mechanical properties and tribological properties, thereby laying a theoretical basis for extending their applications. Here, the application and its performance of MAX phase are introduced. The interface effect on conductivity and mechanical properties of MAX phase reinforce metal matrix composites is summarized. The tribological behaviors of MAX reinforced metal matrix composites are overviewed. Meanwhile, the wear mechanism of the MAX phase as a reinforcing phase in synergistic friction, single phase friction, and high temperature friction is elaborated. Finally, the outlook of MAX phase in future research prospected is described.
Keywords: metal-nonmetal composite Mn+1AXn phase interface tribology electrical conductivity
Mn+1AXn相(简称MAX)是一种三元层状化合物,其中M为过渡族金属元素,A为主族元素,X为碳、氮元素,其结构如图 1所示,M原子和A原子之间的结合为弱共价键,MX化合物则为M-X共价键和MX离子键混合组成。与石墨、MoS2的层状之间的范德华力不同,MAX的键合强度明显强于范德华力,故润滑性能与石墨、MoS2等不同[1-4]。MAX兼具金属和陶瓷的优异性能,如导电导热性好、高的弹性模量及高温强度、抗热震性和损伤容限、抗氧化、耐腐蚀、自润滑等。同时,张兴旺等人[5]研究发现,Ti3SiC2/铜基复合材料在高速高温摩擦实验中摩擦系数呈现稳定性,这表明Ti3SiC2具有优于片状石墨的高温抗氧化性能,说明MAX作为增强相有很大优势。MAX/金属基复合材料受制备温度的影响较大,温度较高时MAX相易分解,可改善界面结合性,导电性略有下降,且MAX相适当分解可使复合材料具有优异的综合性能。综上可以看出,制备温度对界面处的反应和MAX相分解的研究尤为重要。
图 Figure1(Fig.Figure1)
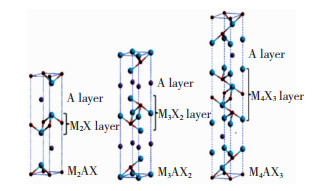
MAX相的应用与其自身的性质有很大关系,学者们在研究MAX相陶瓷时发现其在自愈合性,高温抗氧化性,导电性,自润滑性方面表现很突出。2011年,Gupta等[7]针对MAX相、MAX/Ag在室温及高温下的摩擦行为进行了研究,并提出了4种摩擦膜形成机理。但目前针对MAX协同增强时所起的作用方面研究较少,为此,本文将对MAX相的一些优异性能进行综述,并归纳总结了MAX/金属基复合材料的制备及力学性能和摩擦学方面的研究,最后对MAX相未来研究方向进行了展望。
1 MAX相特性的研究现状1.1 自愈合性能自愈合性能可以保护材料免受各种损伤,Ti3SiC2和Ti3AlC2的自愈合作用,与它们含有的主族元素和过渡族金属元素均有很大关系。Ti3SiC2/NAB (Cu-4.5Ni-9Al-4.2Fe-3.5V-1.2Mn)通过Ti3SiC2的分解和氧化实现了金属自愈合,改善了摩擦性能,裂纹的恢复率约为72.5%~76.5%[8]。其主要的裂纹恢复机制为重复的微动磨损导致少量的Ti3SiC2流向裂纹,由摩擦热形成的SiO2、TiO2、Al2O3及剪切应力和摩擦化学反应等因素促进了裂纹的恢复。Ti3SiC2自愈合性能也可应用于涂层中改善摩擦性能,在NAB基体等离子喷涂Ti3SiC2,由于Ti3SiC2选择性氧化使得裂纹愈合,耐磨性提高,摩擦氧化物使得摩擦系数降低[9]。Ti3AlC2经1 100 ℃高温氧化2 h后,在裂纹处形成了初生α-Al2O3、TiO2(图 2)。压痕处模量和硬度略高于原始基体Ti3AlC2,且由于Al的优先氧化,在裂纹表面形成了厚度小于1 μm的α-Al2O3[10]。
图 Figure2(Fig.Figure2)
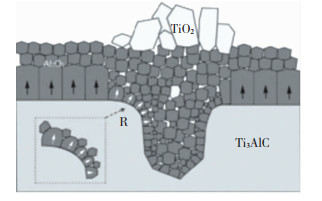
1.2 抗氧化性能Sarkar[11]等人发现Ti3SiC2氧化温度为900 ℃,由于在动态微动条件下,摩擦接触处的摩擦能对反应有驱动作用,室温下Ti3SiC2和TiC在微动磨损下也可氧化形成TiO2和SiO2。Ti3SiC2中的TiC可能导致抗氧化能力下降,从而形成剪切强度较低的TiO2相,起到润滑作用[12]。Ti3SiC2的循环氧化动力学曲线(图 3)呈抛物线型,氧化速率低于TiC,Ti3SiC2经循环氧化形成了一种双氧化层,其中外层为完整致密的TiO2,内层为TiO2与SiO2混合物,内部氧化层的裂缝以钛向外扩散,氧向内扩散为路径,增加了外部氧化层的生长速率[13]。
图 Figure3(Fig.Figure3)
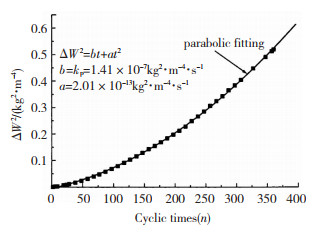
在渗碳条件下对Ti3Al合金进行表面处理,可以形成一层Ti3AlC2保护层[14]。Ti2AlC、Ti3AlC2和Cr2AlC均能形成致密且有保护性的Al2O3层。Ti2AlC作为高温结构材料,原材料成本相对较低,密度低,具有优异的抗氧化性(不受热循环的影响)和裂纹愈合能力[15-16, 3]。由于形成了Al2O3保护层,Ti2AlC在1 350 ℃可承受高达10 000次的热循环。Ti2AlC与Ti3AlC2相比,Al的浓度更高,增加了Al在基体/氧化物界面的活性,进而增加了形成氧化铝层的可能性; Ti2AlC和Al2O3的热膨胀匹配性好,能够减少热残余应力和散裂倾向; 而Cr2AlC形成的氧化物在热循环过程中会脱落。但由于Ti3AlC2和Ti2AlC陶瓷较差的抗熔融硫酸盐热腐蚀性能和Cr2AlC在高温腐蚀过程中较差的结构稳定性,限制了它们在恶劣高温环境中的应用[17]。
1.3 摩擦学方面研究Ti3AlC2陶瓷在不同真空度下表现出不同的摩擦学行为[18]。在真空度为5.0~2.0×104 Pa的情况下,由于其自身的润滑性能,磨损没有形成Ti-C-O氧化膜,润滑机理和石墨吸收潮湿的空气相似,摩擦系数(fc)低至0.2时几乎没有磨损。在真空度低于0.1 Pa时没有自润滑性,磨损严重。在空气中,fc从0.2升到0.7则与氧有很大的关系。因此,可以看出Ti3AlC2作为固体润滑材料比较适用于近太空环境中。
Xu等[19]通过强磁场校准方法得到了3个不同方向的Ti3AlC2的预制体,然后经放电等离子烧结(SPS)制备成型,其结构如图 4所示,研究发现,TTS((0001)平面)的摩擦系数与TSS-1(滑动方向平行于C轴)和TSS-2(滑动方向平行于C轴)相比最低。在载荷为9 N时,TSS-2的磨损率最小为1.51×10-3mm3/(N·m)。在载荷为1~9 N条件下,为最大限度提高其耐磨性提供了准则。
图 Figure4(Fig.Figure4)
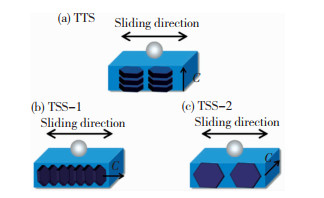
1.4 导电性研究目前MAX相的种类很多,制备纯度较高的Ti2SnC比较困难。Ti2SnC的键合性能具有各向异性,平行于基底平面导电性远高于C轴导电性[20]。不同学者测试的Ti2SnC电阻率并不相同,分别为0.07和0.22 μΩ·m,由于成分变化和微观结构中杂质相的存在,测量到的低电阻率是很难重复的[21-22]。
1.5 刻蚀MAX相的研究受二维石墨烯应用于润滑油添加剂的启发,薛茂权[23]发现MAX相层状纳米陶瓷粉经HF刻蚀后的纳米结构产物AlF3、TiC作为基础油的添加剂在摩擦方面有很好的效果。MAX也可作为制备碳化物衍生碳即氢储甲烷和超级电容器电极材料的前驱体,采用氯气在高温下刻蚀TiC、Ti3AlC2和Ti2SnC等从而得到新型多孔碳材料[24]。
由上述结果可以看出MAX的自愈合性及抗氧化性和摩擦方面的性能都与M-A-氧化物有很大关系。刻蚀MAX相与其层状结构有关联。MAX相的研究为其作为复合材料增强相奠定了基础,并可能在复合材料中发挥出新的作用。
2 MAX/金属基的制备及性能制备温度对MAX/金属基复合材料界面处的结合有很大影响。制备工艺的核心集中在温度对界面润湿性的影响、表面镀铜处理以及其他工艺因素对性能的影响等。MAX增强金属基复合材料主要制备方法有热压烧结、放电等离子烧结(SPS)、无压浸渗烧法、温压法、原位合成法(放热弥散法(XDTM)、反应喷射沉积法(RSD))等。表 1列出了不同制备工艺的优缺点。
表1(Table 1)
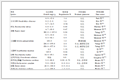
1 热压烧结 加热加压同时进行,温度控制精度高,可以减少金属与增强相的反应,致密度高。 生产周期长,效率低,生产成本高 [33-34]
2 SPS(放电等离子烧结) 升温速度快、烧结时间短,生产效率高。节能环保。可控制烧结气氛。 微区放电过热,金属熔化相易与MAX相反应,生成的物相不易控制,成形压力有限。 [30, 35]
3 温压+轧制法 温压制坯可提高生产效率,减小金属与MAX相反应。坯料再轧制提高制件的致密度,组织均匀。 生产周期长,高体积分数MAX的复合材料成形受限。 [36]
4 无压浸渗法 可形成增强体MAX和基体合金互为连续的复合材料结构,材料强度高,适合高体积分数的复合材料制备。 从陶瓷预制坯到浸渗,整个流程长。浸渗时间长,MAX相与基体合金易发生反应。 [37-38]
5 搅熔铸造法 生产成本低,生产效率高,颗粒分布均匀,可用于MAX相原位增强金属基复合材料。 增强相与基体合金密度差较大时偏析严重。只适合增强体质量分数在15%以下的复合材料。 [39]
6 原位合成法 XDTM:由高温下MAX相中A原子脱溶制备得到,增强相与基体的相容性好,界面结合强度高。RSD:颗粒分布均匀,晶粒细化,界面结合良好。 XDTM:工艺流程长,反应过程的影响因素多。RSD:生产成本高,不能形成致密的块体材料。 [44]
表 1 MAX/金属基复合材料制备方法优缺点对比Table 1 The comparison of pros and cons of MAX/metal matrix composite preparation methods
2.1 制备温度对复合材料界面及性能的影响研究界面处的反应对制备温度的控制有重要作用。Lu等人[25]采用座滴法研究了Ti3SiC2/Cu体系在真空下的润湿行为,研究发现,当温度从1 089 ℃增加到1 270 ℃,铜和Ti3SiC2之间的接触角从95°变为15°。在界面形成了由铜、TiCx、Ti3SiC2和CuxSiy组成的混合过渡区,这种界面层的形成有助于提高系统的润湿性。另外,添加Ti元素会抑制Cu的扩散,Si元素会阻止Ti3SiC2的分解,均不利于体系的润湿[26]。
Zhou等人[27]发现铜与Ti3SiC2的反应温度在900 ℃以上,当Ti3SiC2含量较低或温度低于1 000 ℃时,形成了Cu(Si)固溶体和TiCx,当Ti3SiC2含量较高且反应温度较高时,则形成了Cu5Si、Cu15Si4、(Cu, Si)η′等固溶体和TiCx。另外,制备温度控制在900 ℃以下时可得到纯度高的复合材料。Tungwai等人[28]通过温压成型和SPS烧结制备了Ti3SiC2/Cu复合材料,发现在800 ℃及以上时,Ti3SiC2分解成TiC或其他碳化物和TiSi2。如果纯度是主要研究因素,制备温度应限制在750 ℃及以下。而事实上900 ℃以上高温条件下制备的Ti3SiC2/Cu的机械性能和密度均得到显著提高。王帅等人[4]发现制备Ti2AlC/Cu复合材料的最佳温度为800 ℃,随着温度升高会出现Al从Ti2AlC中脱溶的现象。Al与TiCx之间的弱结合使得高于该温度时Ti2AlC易于分解,同时MAX相的分解还受环境中C或其氧化物的影响[29]。
Liu等人[30]考察用SPS法制备Ti3SiC2/Al-Si复合材料时发现,在低温520 ℃及以下烧结可以避免Ti3SiC2与基体铝的界面反应,试样硬度随Ti3SiC2含量的增加呈线性增加。10%Ti3SiC2/Al-20Si的力学性能最好,维氏硬度可达125.4 HV,摩擦系数为0.42。Zhang等人[31]在850 ℃时制备了强导电性的10vol.%Ti3AlC2/Cu复合材料,其拉伸强度为285 MPa,导电率为58% IACS,该复合材料的强化是通过界面层Ti3AlC2中Al的部分脱溶形成TiCx和Cu(Al)实现的。采用先在850 ℃预压实,而后在1 000 ℃热压制备高强度的10vol.%TiCx/Cu复合材料,进而使其拉伸强度达到356 MPa,导电率达到19% IACS,其中高模量的TiCx和大量的孪晶结构起到增强基体的作用。结果表明,
亚化学计量的Ti3AlxC2(x < 1)存在时其导电性下降不明显。吴进怡等人[32]在850 ℃热压烧结30 min制备Ti2SnC/Cu复合材料,结果表明,由于Sn向铜基体的扩散,虽然无TiCx生成,但5vol.%Ti2SnC/Cu的电阻率仍为纯铜的1.5倍。随后通过放热弥散法,即将上述块体在950 ℃退火4 h利用Sn从Ti2SnC中脱溶制备得到高强度TiCx/Cu复合材料。
综上可以看出烧结温度对界面的结合有很大影响,与铜复合的MAX相在低温下导电性较好,适度的分解对导电率影响不大,高制备温度可以得到高强度复合材料。通过控制烧结温度可以得到性能不同的复合材料。
2.2 镀铜对复合材料性能的影响Dudina等人[35]通过SPS制备Ti3SiC2/Cu时发现,如果在SPS过程中铜基体部分熔化会出现Ti3SiC2的化学不稳定性并伴随着相变,则不利于Ti3SiC2/Cu的致密化。由于烧结过程体系的界面结合性不好,部分学者采用镀铜的方法来提高其性能。Zhou等人[40]研究发现当Ti3SiC2的体积含量较高时,在880 ℃时通过热压烧结较难实现Ti3SiC2/Cu复合材料的致密化,而镀层可防止Ti3SiC2颗粒的接触和团聚,使Ti3SiC2分布更均匀。由于致密度和微观结构的改善,Ti3SiC2/Cu复合材料的力学性能得到显著的强化,20vol.%Ti3SiC2镀铜前后复合材料的屈服强度分别为216.2和247.1 MPa,相对密度分别为96%和99%。
Fu等人[41]研究了850 ℃真空热压烧结Ti3SiC2/Al2O3复合增强铜基受电弓滑板(HRCPs),发现HRCPs的电阻率明显低于纯碳。增强相经过化学镀铜后可有效降低电子散射的影响,一定程度上提高了复合材料的导电性。HRCPs的摩擦学性能明显优于纯碳板,且随着增强相含量的增加而改善。其中含30wt.%Ti3SiC2、3wt.%纳米Al2O3的试样综合性能最优,硬度为112 HB,电阻率为0.16 μΩ·m,摩擦系数为0.408,磨损率为3.31×106 μm3。Zhang[42]采用SPS在900 ℃制备了Ti2AlN/Cu复合材料,研究发现,镀铜的Ti2AlN增强相与铜基体具有较强的结合性。加入7wt.%Ti2AlN时,Cu基复合材料的拉伸强度约为380 MPa,导电率约为61.5% IACS,得到明显提高。
综上所述,经过镀铜处理后的MAX相与金属复合之后,导电性、力学性能和摩擦学性能均得到明显提高。
2.3 其他因素对复合材料性能的影响除通过镀铜改善复合材料界面的润湿性或采用先进的制备工艺提高其综合性能外,也可通过具体的预处理、制备参数、后续轧制或纳米化处理等提高复合材料的综合性能。Lu等人[33]研究发现,30vol.%Ti3SiC2/Cu复合材料在930 ℃下热压烧结2 h,其相对密度为100%,而在1 250 ℃真空烧结1 h,其相对密度则为98.4%。在900 ℃时热压烧结,维氏硬度达到1 735 MPa,电阻和维氏硬度随着烧结温度的升高而降低,致密度呈上升趋势,维氏硬度的降低可能是温度升高发生Ti3SiC2脱溶,使得其体积分数变小所致。Ngai等人[36]采用温压法制备了5wt.%Ti3SiC2/Cu复合材料。为了提高密度,对烧结样品进行热轧处理,轧制变形量为30%、密度为8.28 g/cm3、硬度为1 060 MPa(HB)、极限抗拉强度288 MPa、电阻率为7.0×10-8 Ω·m、摩擦系数为0.17,适用于电刷材料。
Wang等人[43]发现球磨10 h后,铜和Ti3AlC2晶粒尺寸分别减小到12 nm和10 nm。将混合粉末通过热压烧结在950 ℃、25 MPa下保温1 h制得60vol.%Ti3AlC2/Cu(Al)复合材料。由于Cu(Al)固溶强化效果、晶粒尺寸效应和扭结带与大量韧窝的形成,复合材料具有较低的电阻率(0.32±0.01)×10-6 Ω·m和优越的极限抗压强度(1 242±24) MPa。Li等人[44]基于Ti3AlC2在高温下易分解的性质,以50wt.%Ti3AlC2-50wt.%Cu混合粉末为原料,采用大气等离子喷涂法制备了一种原位纳米复合涂层。在喷涂过程中,由于高温,Al从Ti3AlC2中脱溶,为铜扩散至Ti3AlC2提供了通道,形成了铜的空间网络结构。由亚微米厚的Cu层和纳米颗粒Cu(Al)、Ti4O5、TiO2和Al2TiO5组成的大量纳米相起到协同增强的作用。纳米复合涂层的断裂韧性高达9.4 MPa·m1/2,能量释放率仅为15.1 N/m。
2.4 MAX作为金属基复合材料添加相的摩擦性能研究由于石墨、MoS2强度低、耐温差,已经不能满足更高使用温度的需求,鉴于MAX相的结构特征,强度高,抗高温氧化性高及良好的摩擦性能,其将是一种良好的固体润滑材料。MAX相既可以单独起到改善基体摩擦性能的作用,也可以与石墨、MoS2起到协同润滑的作用,并能拓宽复合材料适用的磨损温度范围及使用工况。
2.4.1 MAX作为金属基复合材料单一添加相的摩擦性能研究Huang等人[37]采用浸渗烧结制备的50vol.%Ti3AlC2/Cu复合材料,在滑动速度为60 m/s,载荷为0.8 MPa时,摩擦系数低至0.13~0.15,磨损率约(3.4~6.0)×10-6 mm3/(N·m),摩擦表面形成由钛、铝、铜和铁氧化物组成的摩擦膜。Shi等人[45]采用原位SPS制备Ti3SiC2/NiAl自润滑复合材料,在Ti3SiC2含量为10wt.%时,摩擦系数最低为0.6,磨损率为5.45×10-5 mm3/(N·m),TiC起到增强作用,Ti3SiC2和C起到润滑作用,优异的摩擦性能可能与强度和润滑之间的平衡有关。Deng等人[46]发现通过SPS制备Ti3SiC2/M50自润滑复合材料,在Ti3SiC2含量为10wt.%、温度为25~450 ℃时,其摩擦系数为0.21~0.78,磨损率为(1.78~3.14)×10-6 mm3/(N·m)。350 ℃时其摩擦系数和磨损率最低,Ti3SiC2和致密的Ti-Si氧化物均匀分布在润滑层中,改善了MT10的抗摩耐磨性。虽然TiC颗粒作为增强相可增强MTX的强度[47]和耐磨性能[48],然而,TiC颗粒会阻碍氧化物的流动,阻止氧化保护层的形成,不利于MTX减小摩擦。
2.4.2 MAX作为金属基复合材料协同添加相的摩擦性能研究Xu等人[49]通过SPS在1 100 ℃保温10 min制备TiAl基自润滑复合材料,研究表明,MoS2、hBN和Ti3SiC2(MhT)的添加量为10wt.%的TiAl基复合材料磨损表面形成了由MoS2、hBN和Ti3SiC2组成的致密摩擦层,表现出最佳的摩擦学性能。润滑相Ti3SiC2在摩擦过程[50]中氧化形成了TiO2和SiO2,降低了与GCr15钢的接触并提供低抗剪强度。Shi等人[51]采用SPS制备了MoS2/Ti3SiC2/NiAl复合材料,发现400 ℃时5Ti3SiC2-5MoS2(wt.%)摩擦系数低至0.13,磨损率为4.5×10-5 mm3/(N·m),粘附在表面的摩擦氧化膜TiO2和SiO2具有显著的减摩效果。MoS2和Ti3SiC2分别在低温和高温起作用,从室温到800 ℃,MoS2和Ti3SiC2展现了优异的协同润滑作用。
Liu等人[52]采用真空热压烧结法制备Cu/Ti3SiC2/C/MWCNTs复合材料进行电摩擦。在最佳工作条件下,机械磨损是主要的磨损机理,包括粘着磨损、磨粒磨损、疲劳磨损和氧化磨损。在低剪切应力下,石墨和Ti3SiC2会以层状滑移[53]。随着切应力的增大,接触面温度升高,CNTs复合材料软化,塑性变形增大,抗剪强度降低。在循环应力的作用下,磨损表面易产生疲劳裂纹,从而导致大量材料的剥落。Zhai等人[54]通过SPS在1 200 ℃制备了Ti3SiC2/MoS2/TiAl自润滑复合材料(TMC),XRD结果表明,复合材料由基体相TiAl、增强相TiC和固体自润滑相(Ti2AlC-Ti3SiC2-MoS2-C)组成。当(Ti3SiC2-MoS2)的添加量为10wt.%时,TMC复合材料的摩擦学性能最优,其摩擦系数约为0.57,磨损率为4.22×10-4 mm3/(N·m)。磨损机理为磨粒磨损、氧化磨损和摩擦层,摩擦层可以降低磨损率。
铜石墨复合材料具有良好的耐热性、耐磨性和摩擦稳定性,是一种理想的摩擦材料。Jiang等人[55]发现,加入Ti3SiC2可以提高铜石墨合金材料的强度、硬度和耐磨性,而不影响其自润滑性和导电性。Cu/Ti3SiC2/C/graphene纳米复合材料的添加相在基体中分布均匀,Ti3SiC2热分解在界面生成硬脆相TiC和Cu9Si,使其力学性能得到极大提高,但TiC是一种高熔点硬脆相,具有高硬度,TiC和Cu9Si也会引起应力集中[56]。Lian等人[57]研究发现,氧化石墨烯和镀铜Ti3AlC2协同增强铜基复合材料具有低的摩擦系数和磨损率,优于两相单独增强。Ti3AlC2作为一种硬质相能够起到承受载荷的作用,在摩擦过程中,可避免塑性变形和犁沟作用对铜基体表面的破坏。避免粘着磨损和磨粒磨损,有利于形成氧化石墨烯润滑摩擦层。另一方面,氧化石墨烯结合Ti3AlC2发生摩擦氧化反应使磨损表面形成了紧密连续和低剪切强度的摩擦层,大大降低了剪切应力从表层至亚表层的传递。
综上所述,MAX相在协同摩擦、单相摩擦或高温摩擦中,其氧化物Al2O3、SiO2、TiO2起很大作用,低的摩擦系数与TiO2的抗剪切强度低有关,TiC主要起减磨作用,其层状结构与磨损机理之间的关系很模糊,为更清楚的了解磨损机理,可以进行该方面研究。
3 结语1) MAX相自身有很多特性,也可以起到改善金属材料性能的作用,但与金属基材料复合的过程中,其制备受到MAX相的分解、界面结合性较弱的限制,可考虑选择合适的制备温度,镀铜、颗粒纳米化处理或对复合材料进行轧制处理。
2) MAX在较高的制备温度下的分解降低了复合材料的导电率,但可起到增强金属基复合材料的作用,进而得到高强度的复合材料; 少量的分解对导电性无明显影响,缺位Mn+1AxXn(x <1)相增强金属基复合材料有望具有优异的综合性能,可根据需要选择合适的制备温度。
3) MAX相对摩擦性能改善主要与其氧化物有关,MAX相层状结构的润滑作用与其摩擦实验环境有很大关系,对于MAX相的层状结构与摩擦之间的关联性有待进一步的研究。
4) MAX相是一种良好的增强相,加之本身较好的导电性,MAX相增强金属基复合材料时既降低了金属材料导电性的下降幅度又起到润滑作用。在摩擦方面既可以取代石墨、MoS2单独增强,也可以协同增强。
5) 目前发现MAX相既可应用于涂层中,也可应用于电接触材料及太空中的固体自润滑材料等。未来的主要研究方向集中在加强基体金属与MAX的反应物相控制、加强对其在实际工况中摩擦磨损的应用研究、加强MAX相织构的方向性对金属基复合材料摩擦的影响规律研究等。
参考文献
[1] SUN Z M. Progress in research and development on MAX phases:a family of layered ternary compounds[J]. International Materials Science, 2011, 56: 143-166. DOI:10.1179/1743280410Y.0000000001
[2] 陈艳林, 祝亚希, 方奇, 等. Cu与三元层状化合物复合材料研究现状[J]. 硅酸盐通报, 2014, 33(1): 92-96.
CHEN Yanlin, ZHU Yaxi, FANG Qi, et al. Research progress of Cu and three dimensional layered composite materials[J]. Silicate bulletin, 2014, 33(1): 92-96. DOI:10.16552/j.cnki.issn1001-1625.2014.01.033
[3] RADOVIC M, BARSOUM M W. MAX phases: bridging the gap between metals and ceramics[J]. American Ceramic Society Bulletin, 2013, 92(3): 20-27. DOI:10.1111/jace.12096
[4] 王帅. Ti2AlC/Cu复合材料的制备表征及其摩擦磨损行为研究[D].哈尔滨: 哈尔滨工业大学, 2014.
WANG Shuai. Prepapation and characterization of Ti2AlC/Cu composite and research of its friction and wear behavior[D]. Harbin: Harbin Institute of Technology, 2014.
[5] 张兴旺, 孟凡爱, 刘佳玲, 等. Ti3SiC2替代石墨对铜基摩擦材料性能的影响[J]. 粉末冶金技术, 2014, 32(1): 36-42.
ZHANG Xingwang, MENG Fanai, LIU Jialing, et al. Effect of Ti3SiC2 replacing graphite on the properties of copper based friction materials[J]. Powder metallurgy, 2014, 32(1): 36-42. DOI:10.3969/j.issn.1001-3784.2014.01.007
[6] 王帅, 杨军. MAX相陶瓷摩擦学研究进展[J]. 摩擦学学报, 2018, 38(6): 120-131.
WANG Shuai, YANG Jun. Progress research on the tribology of MAX phase ceramics[J]. Journal of Tribology, 2018, 38(6): 120-131. DOI:10.16078/j.tribology.2018121
[7] GUPTA S, BARSOUM M W. On the tribology of the MAX phases and their composites during dry sliding: A review[J]. Wear, 2011, 271(9-10): 1878-1894. DOI:10.1016/j.wear.2011.01.043
[8] ZHAI W Z, LU W L, ZHANG P, et al. Wear-triggered self-healing behavior on the surface of nano-crystalline nickel aluminum bronze Ti3SiC2 composites[J]. Applied Surface Science, 2017, 436: 1038-1049. DOI:10.1016/j.apsusc.2017.12.138
[9] ZHOU M Z, LU W L, LIU X J, et al. Fretting wear properties of plasma-sprayed Ti3SiC2 coatings with oxidative crack-healing feature[J]. Tribology International, 2018, 118: 196-207. DOI:10.1016/j.triboint.2017.10.009
[10] TALLMAN D J, BABAK A, MICHEL W, et al. A critical review of the oxidation of Ti2AlC, Ti3AlC2 and Cr2AlC in Air[J]. Research Letters in Materials Science, 2013, 1(3): 1-11. DOI:10.1080/21663831.2013.806364
[11] SARKAR D, KUMAR BVM, BASU B. Understanding the fretting wear of Ti3SiC2[J]. J Eur Ceram Soc, 2006, 26(13): 2441-2452. DOI:10.1016/j.jeurceramsoc.2005.05.006
[12] REN S F, MENG J H, WANG J B, et al. Friction and wear of thermal oxidation-treated Ti3SiC2[J]. Tribol Lett, 2010, 37: 59-67. DOI:10.1007/s11249-009-9490-y
[13] LIU G M, LI M S, ZHANG Y M, et al. Cracking behavior of oxide scale formed on Ti3SiC2-based ceramic[J]. Materials Science and Engineering A, 2003, 360: 408-414. DOI:10.1016/s0921-5093(03)00500-8
[14] WANG X H, ZHOU Y C. Layered machinable and electrically conductive Ti2AlC and Ti3AlC2 ceramics: a review[J]. J Mater Sci Technol, 2010, 26(5): 385-416.
[15] SONG G M, PEI Y T, SLOOF W G, et al. Oxidation-induced crack healing in Ti3AlC2 ceramics[J]. Scripta Materialia, 2008, 58(1): 13-16. DOI:10.1016/j.scriptamat.2007.09.006
[16] BARSOUM M W, YAROSCHUK G, TYAGI S. Fabrication and characterization of M2SnC (M=Ti, Zr, Hf and Nb)[J]. Scripta Materialia, 1997, 37(10): 1583-1591. DOI:10.1016/S1359-6462(97)00288-1
[17] 刘智谋.新型四元MAX相(Cr2/3Ti1/3)3AlC2的合成、晶体结构表征及性能研究[D].沈阳: 中国科学院大学, 2015.
LIU Zhimou. Synthesis, crystal structure characterization and properties of a novel quaternary MAX phase (Cr2/3Ti1/3)3AlC2[D]. Shenyang: University of Chinese Academy of Sciences, 2015.
[18] MA J Q, HAO J Y, FU L C, et al. Intrinsic self-lubricity of layered Ti3AlC2 under certain vacuum environment[J]. Wear, 2013, 297(1-2): 824-828. DOI:10.1016/j.wear.2012.10.015
[19] XU L, ZHU D, SALVATORE, et al. Effect of texture microstructure on tribological properties of tailored Ti3AlC2 ceramic[J]. Journal of Advanced Ceramics, 2017, 6(2): 120-128. DOI:10.1007/s40145-017-0224-6
[20] ZHOU Y C, DONG H Y, YU B H. Development of two-dimensional titanium tin carbide (Ti2SnC) plates based on the electronic structure investigation[J]. Materials Research Innovations, 2000, 4(1): 36-41. DOI:10.1007/s100190000065
[21] BARSOUM. The Mn+1AXn phases: A new class of solid: thermodynamically stable nanolaminates[J]. Prog Solid State Chem, 2000, 28: 201-281. DOI:10.1016/S0079-6786(00)00006-6
[22] El-RAGHY T, CHAKRABORTY S, BARSOUM M W. Synthesis and characterization of Hf2PbC, Zr2PbC and M2SnC(M=Ti, Hf, Nb or Zr)[J]. Journal of the European Ceramic Society, 2000, 20(14): 2619-2625. DOI:10.1016/S0955-2219(00)00127-8
[23] 薛茂权. MAX相及其氢氟酸腐蚀产物制备与摩擦学行为研究[D].镇江: 江苏大学, 2014.
XUE Maoquan. Study on preparation and tribological behavior of MAX phase[D]. Zhenjiang: Jiangsu University, 2014.
[24] 贾进.碳化物衍生碳的制备及其气体存储性能的研究[D].焦作: 河南理工大学, 2015.
JIA Jin. Progress of preparation of carbide-derived carbon and application it gas storage[D]. Jiaozuo: Henan Polytechnic University, 2015.
[25] LU J R, ZHOU Y, ZHENG Y, et al. Interface structure and wetting behaviour of Cu/Ti3SiC2 system[J]. Advances in Applied Ceramics, 2015, 114(1): 39-44. DOI:10.1179/1743676114Y.0000000185
[26] 路金蓉, 周洋, 李海燕, 等. Cu/Ti3SiC2体系润湿性及润湿过程的研究[J]. 无机材料学报, 2014, 29(12): 1313-1319.
LU Jinrong, ZHOU Yang, LI Haiyan, et al. Wettability and wetting process in Cu/Ti3SiC2 system[J]. Journal of Inorganic Materials, 2014, 29(12): 1313-1319.
[27] ZHOU Y C, GU W L. Chemical reaction and stability of Ti3SiC2 in Cu during high-temperature processing of Cu/Ti3SiC2 composites[J]. Basic, 2004, 95(1): 50-57. DOI:10.3139/146.017911
[28] NGARI T L, ZHENG W, LI Y Y. Effect of sintering temperature on the preparation of Cu-Ti3SiC2 metal matrix composite[J]. Progress in Natural Science:Materials International, 2013, 23(1): 70-76. DOI:10.1016/j.pnsc.2013.01.011
[29] 盖建丽, 陈继新, 李美栓, 等. Ti3AlC2在含C环境下热处理制备Al2OC晶须[C]//第十八届全国高技术陶瓷学术年会摘要集.北京: 清华大学, 2014: 145.
GAI Jianli, CHEN Jixin, LI Meishuan, et al. Preparation of Al2OC whiskers by heat treatment of Ti3AlC2 in a C-containing environment[C]//The 18th National High-tech Ceramics Annual Conference Summary. Beijing: Tsinghua University, 2014: 145. DOI: http://ir.imr.ac.cn/handle/321006/73713
[30] LIU W Y, ZHANG J B, JIN Y M, et al. Microstructure and properties of Ti3SiC2/Al-Si composites synthesized by spark plasma sintering[J]. Mater Res Express, 2007, 11(4): 1-8. DOI:10.1088/2053-1591/aa98e6
[31] ZHANG J M, ZHOU Y C. Microstructure, mechanical, and electrical properties of Cu-Ti3AlC2 and in situ Cu-TiCx composites[J]. Mater, 2008, 23(4): 924-932. DOI:10.1557/JMR.2008.0126
[32] 吴进怡. 锡碳化钛增强铜基复合材料[M]. 北京: 冶金工业出版社, 2008: 25-43.
WU Jinyi. Tin-titanium carbide reinforced copper matrix composite[M]. Beijing: Metallurgical Industry Press, 2008: 25-43.
[33] LU J R, ZHOU Y, ZHENG Y, et al. Effects of sintering process on the properties of Ti3SiC2/Cu composite[J]. Key Engineering Materials, 2012, 512-515: 377-381. DOI:10.1080/10402004.2014.931499
[34] CAO H Q, QIAN Z Y, ZHANG L, et al. Tribological behavior of Cu matrix composites containing graphite and tungsten disulfide[J]. Tribology Transactions, 2014, 57(6): 1037-1043. DOI:10.1080/10402004.2014.931499
[35] DUDINA V, VYACHESLAV I, ALEXANDER G, et al. Ti3SiC2-Cu composites by mechanical milling and spark plasma sintering: possible microstructure formation scenarios[J]. Met Mater Int, 2013, 19(6): 1235-1241. DOI:10.1007/s12540-013-6015-x
[36] NGAI T, ZHENG J J, TAN W C, et al. Effect of rolling on a warm compacted Ti3SiC2 particulate reinforced Cu matrix composite[J]. Rare Metal Materials and Engineering, 2011, 40(S3): 056-058. DOI:10.1002/maco.201005741
[37] HUANG Z Y, ZHAI H X, AI M X. A new Ti3AlC2/Cu cermet exhibiting excellent tribological properties[J]. Key Engineering Materials, 2007, 336-338: 1436-1438. DOI:10.4028/www.scientific.net/kem.336-338.1436
[38] 梁胜国, 翟洪祥, 艾明星, 等. Cu-Ti3AlC2金属陶瓷的制备及性能研究[J]. 稀有金属材料与工程, 2007, 36(S1): 668-670.
LIANG Shengguo, ZHAI Hongxiang, AI Mingxing, et al. Fabrication and properties of Cu-Ti3AlC2 cermets[J]. Rare Metal Materials and Engineering, 2007, 36(S1): 668-670. DOI:10.3321/j.issn:1002-185x.2007.z1.189
[39] 刘文扬, 胡涛涛, 张炜, 等. Ti3SiC2/Al稀释重熔制备铝基复合材料[J]. 铸造, 2018, 495(2): 8-12.
LIU Wenyang, HU Taotao, ZHANG Wei, et al. Preparation of Al matrix composites by Ti3SiC2/Al dilution remelting[J]. Casting, 2018, 495(2): 8-12.
[40] ZHOU Y C, CHEN B, WANG X H, et al. Mechanical properties of Ti3SiC2 particulate reinforced copper prepared by hot pressing of copper coated Ti3SiC2 and copper powder[J]. Metal Science Journal, 2004, 20(5): 661-665. DOI:10.1179/026708304225016581
[41] FU X L, HU Y B, PENG G, et al. Effect of reinforcement content on the density, mechanical and tribological properties of Ti3SiC2/Al2O3 hybrid reinforced copper-matrix pantograph slide[J]. Science And Engineering of Composite Materials, 2017, 24(6): 807-815. DOI:10.1515/secm-2015-0290
[42] ZHANG D D, ZHAN Z J, GUO C H, et al. Preparation and properties of Cu matrix reinforced with Ti2AlN ceramic particles[J]. Key Engineering Materials, 2014, 602-603: 523-526. DOI:10.4028/www.scientific.net/KEM.602-603.523
[43] WANG W J, ZHAI H X, CHEN L L, et al. Sintering and properties of mechanical alloyed Ti3AlC2-Cu composites[J]. Materials Science & Engineering A, 2017, 685: 154-158. DOI:10.1016/j.msea.2017.01.003
[44] LI Q L, YUAN X H, XU H, et al. Microstructure and fracture toughness of in-situ nanocomposite coating by thermal spraying of Ti3AlC2/Cu powder[J]. Ceramics International, 2019, 45: 13119-13126. DOI:10.1016/j.ceramint.2019.03.246
[45] SHI X L, WANG M, ZHAI W Z, et al. Influence of Ti3SiC2 content on tribological properties of NiAl matrix self-lubricating composites[J]. Materials and Design, 2013, 45: 179-189. DOI:10.1016/j.matdes.2012.08.060
[46] DENG X B, SHI X L, LIU X Y, et al. Effect of Ti3SiC2 on tribological properties of M50 matrix self-lubricating composites from 25 to 450 ℃[J]. JMEPEG, 2017, 26: 4595-4604. DOI:10.1007/s11665-017-2908-z
[47] SHI X L, ZHAI W Z, XU Z S, et al. Synergetic lubricating effect of MoS2, and Ti3SiC2 on tribological properties of NiAl matrix self-lubricating composites over a wide temperature range[J]. Tribol Trans, 2014, 55(3): 93-103. DOI:10.1016/j.matdes.2013.09.072
[48] JEROME S, RAVISANKAR B, MAHATO P K, et al. Synthesis and evaluation of mechanical and high temperature tribological properties of in-situ Al-TiC composites[J]. Tribology International, 2010, 43(11): 2029-2036. DOI:10.1016/j.triboint.2010.05.007
[49] XU Z S, SHI X L, ZHANG Q X, et al. Effect of sliding speed and applied load on dry sliding tribological performance of TiAl matrix self-lubricating composites[J]. Tribology Letters, 2014, 55(3): 393-404. DOI:10.1007/s11249-014-0367-3
[50] BARSOUM M.W, El-RAGHY T, OGBUJI L. Oxidation of Ti3SiC2 in air[J]. J Electrochem Soc, 1997, 144: 2508-2516. DOI:10.1149/1.1837846
[51] SHI X L, ZHAI W Z, XU Z S, et al. Synergetic lubricating effect of MoS2 and Ti3SiC2 on tribological properties of NiAl matrix self-lubricating composites over a wide temperature range[J]. Materials & Design, 2014, 55: 93-103. DOI:10.1016/j.matdes.2013.09.072
[52] LIU W X, JIANG X S, SHAO Z Y, et al. Tribological behaviors of Cu/Ti3SiC2/C/MWCNTs composites with electric current journal of computational and theoretical[J]. Nanoscience, 2015, 12: 2664-2672. DOI:10.1166/jctn.2015.4160
[53] GUL H, UYSAL M, AKBULUT H, et al. Tribological behavior of copper/MWCNT nanocomposites produced by pulse electrodeposition[J]. Acta Physica Polonica A, 2014, 125: 254-256. DOI:10.12693/APhysPolA.125.254
[54] ZHAI W Z, SHI X L, WANG M, et al. Friction and wear properties of TiAl-Ti3SiC2-MoS2 composites prepared by spark plasma sintering[J]. Tribology Transactions, 2014, 57: 416-424. DOI:10.1080/10402004.2014.880539
[55] JIANG X S, LIU W X, LI Y J, et al. Microstructures and mechanical properties of Cu/Ti3SiC2/C/ graphene nanocomposites prepared by vacuum hotpressing sintering and hot isostatic pressing[J]. Composites Part B, 2017, 12: 1-32. DOI:10.1016/j.compositesb.2017.12.050
[56] JIANG X S, SONG T F, SHAO Z Y, et al. Synergetic effect of graphene and MWCNTs on microstructure and mechanical properties of Cu/Ti3SiC2/C nanocomposites[J]. Nanoscale Research Letters, 2017, 12(1): 1-12. DOI:10.1186/s11671-017-2378-0
[57] LIAN W Q, MAI Y J, WANG J, et al. Fabrication of graphene oxide-Ti3AlC2 synergistically reinforced copper matrix composites with enhanced tribological performance[J]. Ceramics International, 2019, 45: 18592-18598. DOI:10.1016/j.ceramint.2019.06.082