翟文杰,高博
(哈尔滨工业大学 机电工程学院, 哈尔滨 150001)
摘要:
为了解决传统SiC化学机械抛光(CMP)加工效率低的问题,针对单晶SiC表面抛光质量和材料去除率指标,综述了应用传统碱性抛光液、混合磨粒抛光液及含强氧化剂抛光液对单晶SiC进行化学机械抛光的研究现状;为了提高SiC-CMP的化学和机械两方面作用,对SiC-CMP催化辅助增效技术、SiC电化学机械抛光(ECMP)技术、固结磨料抛光、光催化辅助抛光等增效新技术进行了系统综述;对SiC-CMP及其增效技术进行了分析、讨论,指出了当前的研究难点,展望了进一步提高单晶SiC抛光效率的研究方向.
关键词: 碳化硅(SiC) 化学机械抛光(CMP) 电化学机械抛光(ECMP) 催化辅助 固结磨粒抛光
DOI:10.11918/j.issn.0367-6234.201803130
分类号:TU375.2
文献标识码:A
基金项目:国家自然科学基金(51475119)
Research progress of chemical mechanical polishing and its efficiency-enhancement technology for single crystal silicon carbide
ZHAI Wenjie,GAO Bo
(School of Mechatronics Engineering, Harbin Institute of Technology, Harbin 150001, China)
Abstract:
Chemical mechanical polishing (CMP), now regarded as the only method to obtain whole-wafer planarization and super-smooth surface without sub-surface defects, is usually employed as the final processing method for silicon carbide (SiC) wafer, but the processing efficiency of conventional SiC-CMP is too low to fulfill the current requirement. Aiming at surface quality and material removal rate (MRR) of polished single crystal SiC wafer, the current state of SiC-CMP research is discussed and categorized by CMP using different slurries, e.g. conventional alkaline colloidal silica base slurry, mixed abrasives slurry and slurries with strong oxidizers, respectively. Then from the viewpoint of improving the mechanical role, as well as the chemical one of CMP, the existing efficiency-enhancement methods of SiC-CMP, including the catalyst assisted polishing, electrochemical-mechanical polishing (ECMP), fixed abrasive polishing, and photo-catalyst assisted polishing are extensively reviewed and discussed. Analyses and discussions are conducted from the reviewed researches of SiC-CMP and its related efficiency-enhancement methods, the difficulties and future direction for further improvement on polishing MRR of single crystal SiC are proposed.
Key words: silicon carbide (SiC) chemical mechanical polishing (CMP) electrochemical-mechanical polishing (ECMP) catalyst assisted polishing fixed abrasive polishing
翟文杰, 高博. 单晶SiC的化学机械抛光及其增效技术研究进展[J]. 哈尔滨工业大学学报, 2018, 50(7): 1-10. DOI: 10.11918/j.issn.0367-6234.201803130.

ZHAI Wenjie, GAO Bo. Research progress of chemical mechanical polishing and its efficiency-enhancement technology for single crystal silicon carbide[J]. Journal of Harbin Institute of Technology, 2018, 50(7): 1-10. DOI: 10.11918/j.issn.0367-6234.201803130.

基金项目 国家自然科学基金(51475119) 作者简介 翟文杰(1964—),男,教授,博士生导师 通信作者 翟文杰,zhaiwenjie@hit.edu.cn 文章历史 收稿日期: 2018-03-23
Contents -->Abstract Full text Figures/Tables PDF
单晶SiC的化学机械抛光及其增效技术研究进展
翟文杰


哈尔滨工业大学 机电工程学院, 哈尔滨 150001
收稿日期: 2018-03-23
基金项目: 国家自然科学基金(51475119)
作者简介: 翟文杰(1964—),男,教授,博士生导师
通信作者: 翟文杰,zhaiwenjie@hit.edu.cn
摘要: 为了解决传统SiC化学机械抛光(CMP)加工效率低的问题,针对单晶SiC表面抛光质量和材料去除率指标,综述了应用传统碱性抛光液、混合磨粒抛光液及含强氧化剂抛光液对单晶SiC进行化学机械抛光的研究现状;为了提高SiC-CMP的化学和机械两方面作用,对SiC-CMP催化辅助增效技术、SiC电化学机械抛光(ECMP)技术、固结磨料抛光、光催化辅助抛光等增效新技术进行了系统综述;对SiC-CMP及其增效技术进行了分析、讨论,指出了当前的研究难点,展望了进一步提高单晶SiC抛光效率的研究方向.
关键词: 碳化硅(SiC) 化学机械抛光(CMP) 电化学机械抛光(ECMP) 催化辅助 固结磨粒抛光
Research progress of chemical mechanical polishing and its efficiency-enhancement technology for single crystal silicon carbide
ZHAI Wenjie


School of Mechatronics Engineering, Harbin Institute of Technology, Harbin 150001, China
Abstract: Chemical mechanical polishing (CMP), now regarded as the only method to obtain whole-wafer planarization and super-smooth surface without sub-surface defects, is usually employed as the final processing method for silicon carbide (SiC) wafer, but the processing efficiency of conventional SiC-CMP is too low to fulfill the current requirement. Aiming at surface quality and material removal rate (MRR) of polished single crystal SiC wafer, the current state of SiC-CMP research is discussed and categorized by CMP using different slurries, e.g. conventional alkaline colloidal silica base slurry, mixed abrasives slurry and slurries with strong oxidizers, respectively. Then from the viewpoint of improving the mechanical role, as well as the chemical one of CMP, the existing efficiency-enhancement methods of SiC-CMP, including the catalyst assisted polishing, electrochemical-mechanical polishing (ECMP), fixed abrasive polishing, and photo-catalyst assisted polishing are extensively reviewed and discussed. Analyses and discussions are conducted from the reviewed researches of SiC-CMP and its related efficiency-enhancement methods, the difficulties and future direction for further improvement on polishing MRR of single crystal SiC are proposed.
Key words: silicon carbide (SiC) chemical mechanical polishing (CMP) electrochemical-mechanical polishing (ECMP) catalyst assisted polishing fixed abrasive polishing
单晶SiC作为第3代半导体材料,与传统半导体材料相比,具有高热导率、高临界击穿电场、高饱和电子漂移速率、高键合能和宽禁带等特点,是高频、高温、大功率、抗辐照电子器件及传感器件的优选材料,也是制造大尺寸、超高亮度白光、蓝光二极管和激光二极管的理想衬底材料,在航空、航天探测、核能开发、雷达、通信领域具有重要应用.随着光电、微机电系统以及信息技术的迅速发展,对相关器件所应用的单晶SiC衬底的表面加工精度和表面质量提出了亚纳米制造精度和无亚表层缺陷的超光滑表面制造要求[1-3].
大直径单晶SiC的高效率、高精度、低成本加工是单晶SiC衬底制备技术的关键和发展方向.但单晶SiC硬度高,脆性大,化学惰性强,一般经锯切后的晶片必须由粗、细金刚石磨粒逐级研磨后,再通过粗、精抛光才能获得无亚表层缺陷的超光滑表面.而由于化学机械抛光(Chemical Mechanical Polishing, CMP)是目前唯一能够实现全局平坦化的加工方法,常作为单晶SiC晶片的最终加工工序[2-3],但传统SiC-CMP的材料去除率很低.
化学机械抛光过程如图 1所示.化学机械抛光就是使试件与抛光垫在抛光液(由固体磨粒、氧化剂和液体介质等组成)中保持一定压力并相对运动.其本质是在摩擦条件下利用抛光液中的氧化剂与试件表面产生化学反应形成更易于被抛光液中的磨粒机械去除的软质层.
Figure 1
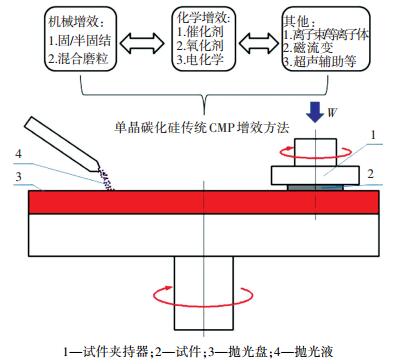
在化学机械抛光过程中,影响表面化学反应层结构、性质的因素很多,包括晶片加工前的微观表面性质、表面形貌和结构状态、抛光压力、转速、抛光液、磨粒、抛光垫特性及温度等.化学机械抛光通常采用含软质磨粒的抛光液及聚氨酯抛光垫,通过协同试件与液体界面的化学作用及嵌在抛光垫上的磨粒与试件的机械作用实现材料去除;因此其去除机制为力学与化学耦合作用[4].
优质的SiC-CMP在于既要保证加工质量又要提高效率以降低成本.而控制SiC表面化学反应层(SiO2层)的形成和去除过程,是实现SiC-CMP高效加工的关键[4].
本文从图 1所示的机械作用和化学作用两方面,对SiC-CMP及其主要增效技术的研究进展进行综述.机械增效方面,主要对采用含有软硬混合磨粒抛光液的SiC-CMP和利用固结/半固结磨粒抛光盘的增效技术进行了综述.化学增效方面,综述了采用强氧化剂基于化学反应动力学的SiC-CMP;采用具有催化性质的颗粒或抛光盘,基于催化反应机理的SiC-CMP增效技术;以及利用电化学反应机理来提高化学反应速率的电化学机械抛光增效技术.
1 单晶SiC-CMP技术研究进展 1.1 传统碱性抛光液的SiC-CMP研究 1.1.1 碱性SiO2抛光液采用胶体SiO2碱性抛光液对SiC-Si面进行化学机械抛光,可获得Ra < 0.5 nm、甚至0.1 nm的原子级光滑无缺陷表面.但材料去除率很低[3, 5-6],即使是在添加含H2O2氧化剂的抛光液中抛光,材料去除率一般也只能达到0.1 μm/h左右[7-9].
1997年,美国凯斯西储大学的Zhou等[10]通过提高含纳米SiO2(60~70 nm)碱性抛光液的温度和pH来增强化学机械抛光的化学作用,获得了光滑低缺陷表面(RMS为0.5 nm),但其材料去除率 < 0.2 μm/h.研究结果表明,化学机械抛光氧化反应速率和温度之间遵循Arrhenius关系,材料去除率取决于SiC层的氧化反应速率和磨粒的机械去除速率的平衡. 2007年,山东大学晶体材料重点实验室的Chen等[11]进行了类似的研究,通过提高介质温度和优选其他工艺参数,获得Ra为0.178 nm的超光滑表面,但没有给出材料去除率.
2001年,美国空军研究实验室的Neslen等[12]系统研究了4H-SiC-CMP中抛光液温度、pH、压力及转速对材料去除率的影响.发现在不同工况下的材料去除率在0.01~0.25 μm/h,压力和转速增大均使材料去除率增加,但转速对材料去除率的影响更大,而抛光液温度和pH对材料去除率的影响不大.
2013年,清华大学摩擦学重点实验室的Pan等[8]发现在含SiO2的碱性抛光液中添加适量H2O2(质量分数为6%)有助于提高材料去除率并获得低缺陷表面;但H2O2浓度过低或过高,会因反应层的形成与去除难以达到平衡而导致表面凹坑等缺陷. Pan等[8]还对比了KOH和单乙醇胺两种碱液的作用效果,发现添加单乙醇胺的材料去除率和抛光质量均不如KOH,认为单乙醇胺中的疏水基团使生成的氢氧根不能在SiC表面充分吸附和反应.清华大学摩擦学重点实验室的Zhou等[13-14]进一步研究发现,材料去除率和SiC抛光面的偏轴角有关,因为不同偏轴角晶面的抛光会导致原子台阶密度及台阶边缘活性原子数目不同.在H2O2和磨料联合作用下SiC更易沿台阶边缘发生化学反应.
1.1.2 混合磨粒抛光液2004年,美国宾夕法尼亚州立大学的Heydemann等[15]应用含SiO2和0.1 μm金刚石混合颗粒的抛光液抛光6H-SiC,得到Ra为0.55 nm的表面,材料去除率为0.6 μm/h;在混合磨粒抛光液中加入氧化剂NaClO后,抛光效果进一步提升,材料去除率为0.92 μm/h,Ra为0.52 nm.
2006年,Kuo等[16]用化学改性的胶状SiO2与特殊处理的纳米金刚石构成的复合抛光液对SiC进行抛光.发现化学添加剂是通过提高SiC与抛光液的化学作用使SiC的抛光质量和材料去除率得到提高;添加金刚石磨粒是通过其机械作用和添加剂的化学作用的协同效应,不仅可以提高SiC的材料去除率,而且其亚表面损伤程度也大大降低.
2009年,Lee等[17]等用H2O2、胶体SiO2和金刚石磨粒(25 nm)组成的碱性抛光液对6H-SiC进行化学机械抛光,得到10 μm×10 μm范围内Ra为0.077 2 nm的表面,材料去除率为0.15 μm/h. An等[18]在上述抛光液中添加氧化剂NaClO后,材料去除率可进一步增大.
2010年,韩国国立大学机械工程研究生院的Lee等[19]用含有SiO2的碱性抛光液浸泡SiC,并对SiC进行了表面XPS分析、AFM刮擦和纳米压痕测试,对混合磨料化学机械抛光的作用机理进行了分析.认为混合磨料中金刚石既有机械去除SiC的作用,也有在SiC表面产生压力促进表面和化学液发生反应的作用,而胶体SiO2的作用是去除化学反应层形成光滑表面. 2009年,Lee等[20]采用混合纳米SiO2(120 nm)和金刚石(50 nm,25 g/L)的抛光液对6H-SiC进行化学机械抛光,获得了Ra为0.27 nm的表面,但材料去除率 < 0.32 μm/h;增大金刚石颗粒浓度(35 g/L)可提高材料去除率到0.55 μm/h(Ra为0.37 nm).
SiC-CMP的材料去除率取决于SiC表面的化学反应速率,但要求SiC与抛光液的化学作用和磨粒机械作用匹配.也有研究者在抛光液中添加金刚石、SiC和Al2O3等惰性磨粒,来增强化学机械抛光的机械去除作用,但表面质量和材料去除率不高.
1.2 含强氧化剂抛光液的SiC-CMP 1.2.1 H2O2氧化剂为提高SiC-CMP的材料去除率,许多人对抛光液中氧化剂的作用进行了研究. 1999—2000年,美国史蒂文斯理工学院的Zhu等[21]与Muratov等[22]基于摩擦化学原理,分别用不含磨粒的H2O2、CrO3及KMnO4对多晶SiC进行了摩擦化学研抛.结果表明,氧化剂的存在可提高材料去除率;使用氮化硅或铸铁研磨盘,在质量分数为3%的CrO3或H2O2中抛光SiC,均获得了Ra < 几个nm的高质量表面(其中使用铸铁研磨盘在质量分数为3%的CrO3溶液下获得的表面质量最好,Ra < 1 nm,材料去除率为0.2~0.4 μm/h),而KMnO4的反应活性过强,对SiC晶界有明显的腐蚀作用.
H2O2氧化剂广泛应用于化学机械抛光的抛光液中[7-9, 15, 18-19]. 2014年,美国克拉克森大学的Lagudu等[23]采用不同pH的H2O2+SiO2抛光液对α-SiC进行化学机械抛光,比较了抛光液中所添加的钾盐分散剂浓度对材料去除率的影响.在质量分数为10%的SiO2+1.47 mol/L的H2O2+50 mmol/L的KNO3抛光液(pH为8)中,获得RMS为0.48 nm,材料去除率为2.1 μm/h;KNO3浓度增大至100 mmol/L时,材料去除率增至3.2 μm/h.
2013年,印度国家物理实验室的Singh等[24]研制了一种基于摩擦化学原理的含有金刚石磨料和强氧化剂的研磨液,对CVD-SiC抛光的材料去除率达到14~16 μm/h,而且表面粗糙度<0.2 nm.
1.2.2 KMnO4氧化剂2002年,美国路易斯威尔大学的Fu等[25]研究表明,酸性介质中Al2O3磨粒对SiC几乎没有去除作用,但在含Al2O3磨粒的酸性抛光液中适度添加KMnO4,可显著提高材料去除率,并改善抛光质量. 2015年,山东大学晶体材料国家重点实验室的Liang等[26]发现,用含KMnO4和Al2O3磨粒的抛光液在相同条件下抛光SiC-C面的材料去除率>硅面的去除率,用质量分数为0.3%的KMnO4抛光液抛光SiC-Si面,材料去除率为0.5 μm/h(Ra为0.094 6 nm);用质量分数为0.1%的KMnO4抛光液抛光C面,材料去除率为2.81 μm/h(Ra为0.24 nm).但KMnO4浓度过大则会造成SiC表面腐蚀损伤.
鉴于KMnO4的强氧化性,许多学者研究了KMnO4对单晶SiC的抛光效果. 2012年,Yin等[27]研究了抛光液pH、KMnO4浓度对SiC的Si面和C面材料去除率的影响,发现使用0.1 mol/L的KMnO4可提高材料去除率;pH为6时,C面材料去除率为1.019 μm/h,pH为3时,达到1.695 μm/h;pH为7时,在开放的空气氛围下, Si面材料去除率可达0.915 μm/h. 2013年,Kurokawa等[28]对含MnO2的抛光液进行研究,发现增大抛光环境中氧气浓度和气压可提高SiC的材料去除率,再添加KMnO4可进一步提高SiC的材料去除率. 2014年,哈尔滨工业大学的杨文航等[29]通过改变刻划时间、载荷、溶液浓度和pH等条件,并结合单晶SiC表面和针尖形貌,研究了SiC在KMnO4氧化性体系中微观去除的力学和化学综合作用及其对材料去除率的影响规律.
2014年,美国克拉克森大学的Lagudu等[30]研究了不同pH下的KMnO4(50 mmol/L)+质量分数为10%的SiO2抛光液对α-SiC抛光的影响规律,比较了在抛光液中添加硫酸铜分散剂对SiC材料去除率的影响.发现过渡金属化合物会显著提高SiC的材料去除率,pH为6时,在上述抛光液中添加2 mmol/L的CuSO4可使材料去除率由无CuSO4时的1.8 μm/h增至3.7 μm/h.
2015—2017年,江南大学机械工程学院的Chen等[31-32]对比了CeO2和SiO2在含KMnO4的抛光液中抛光6H-SiC-Si面的效果,发现质量分数为2%的CeO2+0.05 mol/L的KMnO4(pH为2)的材料去除率为1.089 μm/h(Ra为0.11 nm),优于质量分数为6%的SiO2+0.05 mol/L的KMnO4(pH为6)的抛光结果(材料去除率为0.185 μm/h,Ra为0.254 nm).酸性环境下含CeO2与KMnO4的抛光液中的摩擦系数和材料去除率更大,归因于CeO2易与SiC表面氧化生成化学齿,导致CeO2磨粒在晶片表面发生较强粘附. 2015年,日本大阪大学的Deng等[33]应用质量分数为1%的CeO2溶液(pH为8.53)对SiC进行了化学机械抛光,着重研究了SiC抛光表面的原子级台阶结构型式和抛光过程中化学作用与机械作用的相互关系。
就磨粒而言,CeO2广泛用于硅系材料的抛光,其硬度与SiO2相当,但具有独特的Ce4+、Ce3+变价特性.利用CeO2磨料的氧化还原能力有助于化学机械抛光过程中SiC表面的氧化.作为抛光介质中的磨粒,Cr2O3、Fe3O4也具有与CeO2类似的变价反应或摩擦催化特性,但因Cr2O3具有较强化学毒性,目前应用不多.
2 单晶SiC-CMP增效技术研究进展 2.1 催化辅助SiC-CMP增效技术研究 2.1.1 铂金属催化剂为进一步提高SiC抛光效率,还可构建催化反应来促进SiC的氧化.由于单纯的化学刻蚀难以保证SiC表面的平整化,2006年,日本大坂大学的Hara等[34]提出了催化盘辅助刻蚀(catalyst referred etching, CARE)技术.催化盘辅助刻蚀,是在无磨料条件下,利用金属催化剂加快SiC化学溶解,同时将金属作为抛光盘平滑抛光SiC. 2007—2011年,日本大阪大学的Arima等[35-36]采用金属催化剂铂(Pt)盘在无磨粒HF溶液中对SiC进行低压(0.02 MPa)抛光,基于无电子氧化机理在SiC表面凸峰处形成SiO2,再经HF溶解去除,实现了单晶SiC原子级平整加工,但材料去除率只有0.1~0.2 μm/h.
2012年,日本大阪大学的Okamoto等[37]在无磨粒+Pt抛光盘+HF的基础上,通过增加转速及压力来提高化学反应速率,得到Ra为0.060 nm的超光滑SiC表面,但材料去除率提高不多,仅为0.23 μm/h. 2013年,日本大阪大学的Sano等[38]采用开槽抛光盘,以利于抛光液与试件的接触,可进一步提高转速及压力,材料去除率提高到0.492 μm/h.而且发现了羟基自由基·OH对抛光的辅助作用.
2.1.2 铁及其氧化物催化剂2005年,台湾国立科技大学的Lin等[39]使用不同金属抛光盘,分别在水和丙酮溶液中对α-SiC摩擦化学抛光,发现用铁或不锈钢盘在水溶液中的抛光效果较好, 材料去除率为60 nm/h,Ra为3.51 nm.分析表明SiC研抛过程中产生的Fe2O3起到催化作用,降低了摩擦化学反应的活化能和阈值温度.
2009年—2012年,日本熊本大学的Kubota等[40-41]利用催化性的铁制抛光盘,将微米铁粉加入H2O2中,对SiC进行抛光.以较高压力研抛4H-SiC-C面,获得了光滑(Ra为0.5 nm)无亚表层缺陷的表面,材料去除率接近1.0 μm/h.
2014年,清华大学摩擦学国家重点实验室的Zhou等[42]通过试验发现,在H2O2碱性溶液中加入纳米Fe时的去除率(120 nm/h)高于添加纳米Pt的(100 nm/h),分析认为Fe催化可产生更多能氧化SiC的·OH,而Pt催化则使H2O2过多的分解为H2O和O2.用纳米Fe作为催化剂对6H-SiC-Si面进行化学机械抛光,获得了Ra为0.05 nm的表面.
2010年,Yagi等[43]在0.01 mol/L的FeSO4+质量分数为30%的H2O2溶液中,用铁盘在0.06 MPa压力下进行化学机械抛光,基于Fe2+和H2O2反应(Fenton反应),分解产生了强氧化性的·OH,促进表面氧化生成易于去除的SiO2.尽管获得了原子级光滑的表面形貌,但SiC-Si面的材料去除率 < 30 nm/h(但SiC-C面的材料去除率接近1.0 μm/h).
2017年,广东工业大学的徐少平等[44]通过用质量分数为2.5%的催化剂+粒度为W0.5质量分数0.5%的金刚石+质量分数为10%的H2O2研究了催化剂对SiC-C面抛光的影响.发现铁及其氧化物的催化效果依次为Fe3O4>FeO>Fe>Fe2O3. Fe2+的浓度是决定抛光速率的重要因素,催化剂电离出Fe2+的能力越强,抛光液中Fe2+浓度越高,反应越快,抛光效果越好, 最佳材料去除率为17.2 mg/h,Ra为2.5 nm. 2017年,广东工业大学的阎秋生等[45]利用芬顿试剂抛光液,研究了Fe3O4和H2O2浓度、pH及温度对SiC-C面抛光的影响,在质量分数为1.25%的Fe3O4+质量分数为15%的H2O2+pH为7+41 ℃条件下获得最优结果, 材料去除率为12.0 mg/h,Ra为2.0~2.5 nm.
2014年,中国电子科技集团公司第四十六研究所的高飞等[46]在抛光液中加入催化剂,借助软磨料对4H-SiC-Si面进行化学机械抛光,获得Ra为0.065 2 nm原子级光滑表面.催化剂可提高材料去除率,当氧化剂为硝酸时材料去除率最高约为0.387 μm/h,但该研究没有说明是何种催化剂.
2.2 SiC电化学机械平坦化技术 2.2.1 电化学刻蚀尽管单晶SiC在一般条件下难以与强酸、强碱反应,但在HF或KOH等介质中却易进行电化学刻蚀. 2007年—2009年,荷兰乌得勒支大学的Dorp等[47]与Van Drop等[48]对单晶SiC电化学刻蚀性能及表面评价进行了研究. 2004年,台湾交通大学电子研究所的Chang等[49]研究发现,6H-SiC电化学的刻蚀速率为几十个μm/h(取决于刻蚀电流),但表面粗糙度较大. 2009年,美国宾夕法尼亚州立大学的Ke等[50]在稀释的HF溶液中对p-4H-SiC的电化学刻蚀效果和条件进行了系统研究,发现控制电流较控制电压更利于获得高质量表面(硅面的抛光质量优于碳面).通过研究电流密度、HF浓度、刻蚀时间对刻蚀效果的影响,得到硅面刻蚀效果(材料去除率为40 μm/h,RMS为1.9 nm)最优工艺条件为50 mA/cm2+质量分数为1%的HF+30 min,而在该条件下对碳面刻蚀,虽然材料去除率稍大,但表面变得粗糙(RMS为6.8 nm,高于初始值3.1 nm).上述研究均是在盘电极静止不动条件下对SiC的刻蚀,并不是抛光.但说明可以利用SiC电化学反应原理提高加工效率.
2.2.2 电化学机械抛光用电解质作抛光液, 将试件的电化学腐蚀和低压力化学机械抛光技术相结合对试件进行平整化的技术称为电化学机械抛光(ECMP)技术.近年来,随着45纳米Cu互连芯片平整化要求,对金属的电化学机械抛光进行了较多的研究,但目前关于SiC-ECMP的研究,国内外的研究均非常有限.
2004年,美国伦斯勒理工学院的Li等[51]应用电化学机械抛光原理,用含SiO2+KNO3+H2O2的抛光液,对单晶SiC进行了电化学机械抛光.结果表明,较低的阳极电流可获得较好的表面质量,但材料去除率和化学机械抛光相差不大;增大阳极电流可提高材料去除率,但过高的电流会导致表面粗糙多孔的形成.发现阳极电流为1 mA/cm2时,抛光质量较好(RMS为0.2 nm),但材料去除率 < 0.2 μm/h.为避免在SiC表面留下划痕,应将电化学腐蚀作用和机械去除作用协同、高效地结合起来以获得光滑无损伤的SiC表面.通过将阳极氧化和磨粒机械去除以“电化学氧化+机械去除”两步法的方式循环进行,可高效获得优质SiC表面.
2014年,意大利米兰理工大学的Ballarin等[52]以HF溶液为电解质对n-SiC进行了电解抛光,研究了HF浓度、电流密度、抛光时间对抛光效果的影响,最终得到最优参数为10 mA/cm2+质量分数为1%的HF+30 min,RMS由17.3 nm降到8.3 nm.并发现当电流密度较小(1~2 mA/cm2)时,Ra较好,但材料去除率较低;电流密度过大,表面质量变差. HF浓度过小,反应不明显,Ra和材料去除率均不理想;HF浓度过大,造成过度腐蚀,Ra明显增大;蚀刻时间过长会导致多孔形成,抛光质量降低.
2015年,日本大阪大学的Deng等[53]用含质量分数为2.5%的CeO2颗粒(平均粒径190 nm)的碱性(pH为9.24)抛光液,对单晶SiC-Si面进行电化学机械抛光,结果表明,阳极氧化可明显降低SiC表面硬度,以利于机械去除;对经化学机械抛光的SiC进行电化学机械抛光,基于氧化生长模型估算,材料去除率约为0.42 μm/h;对经机械抛光处理的SiC进行电化学机械抛光,其材料去除率可达3.62 μm/h,30 min的电化学机械抛光,即可获得光滑无划痕(RMS为0.23 nm)的表面.说明经机械抛光的SiC比经化学机械抛光的SiC更易被氧化,更适合电化学机械抛光. 2016年,中国人民解放军理工大学的Shen等[54]以H2O2、HCl和H2O的混合溶液作为电解质,用三电极系统对4H-SiC施加9.8 V电势,进行电化学氧化,估算得到电化学氧化速率可达20 μm/h;在含质量分数为0.1%的CeO2颗粒的抛光液中,对SiC施加9.8 V电势进行了1 h的同步氧化抛光,获得RMS为0.89 nm的光滑表面,但没有给出实际的材料去除率.
2016年,日本近畿大学机械工程系的Murata等[55]在不锈钢盘(阴极)和SiC(阳极)间使用自制的CeO2/聚氨酯(PU)(最佳质量比为2.5)核壳颗粒对单晶SiC-Si面进行电化学机械抛光,其过程包括SiC的电化学氧化和壳核颗粒机械去除氧化物.发现施加持续电压时,表面易产生划痕(Ra为6.61 nm),施加周期性偏压可获得光滑表面(Ra为0.51 nm);基于法拉第电解理论获得最优电解条件为E=10 V,Ton:Toff=2.5 min:7.5 min,在该条件下计算出SiC的材料去除率为3.70 μm/h,接近相同条件下CeO2/PU核壳颗粒去除SiO2速率(材料去除率为3.82 μm/h).该方法不使用抛光垫,所使用的CeO2/PU核壳颗粒可重复使用,寿命长,成本低.
综上所述,为提高单晶SiC-CMP的材料去除率,一方面可以通过电化学作用来提高化学机械抛光的化学反应速率(但应注意避免试件过度腐蚀);另一方面还需提供与之相配的表层腐蚀产物的机械去除方法.
2.3 固结磨料抛光与游离磨粒(三体磨损)相比,固结磨料(二体磨损)的研抛可控性好,能高效获得超精密研抛表面,同时可节省加工时间和成本. 2015年,台湾国立勤益科技大学的Tsai等[56]研制了固结金刚石磨粒的抛光垫,在含Al2O3自由磨粒和KMnO4的抛光液中对单晶SiC进行抛光.结果表明,嵌入纳米金刚石磨粒的抛光垫可高效获得无缺陷光滑表面, 材料去除率为1.3 μm/h,Ra < 0.5 nm. 2016年,台湾国立勤益科技大学的Ho等[57]研制了固结Fe粉和Al2O3磨粒的抛光垫,在质量分数为20%的H2O2(HCl调pH至4)中对单晶SiC进行抛光,在最佳磨粒比例(质量分数为1%的Fe+质量分数为3%的Al2O3)下,可得到材料去除率为0.74 μm/h,Ra为0.159 nm.
由于固结磨粒抛光在高接触压力下容易在试件表面产生划痕和亚层损伤,近年来华侨大学的硬脆材料先进加工技术与装备研究团队提出半固结磨粒抛光方法[58-61]。2015年,Lu等[58]用溶胶-凝胶法把金刚石磨粒半固结在弹性抛光垫上,抛光SiC并获得Ra为0.59 nm的无划痕纳米级光滑表面,但其材料去除率比同粒度游离磨粒抛光低一个数量级. 2017年Lu等[59]采用电泳沉积技术将超细金刚石和聚酯沉积、烧结在钢盘上制备出20 μm厚的抛光垫,用该抛光垫以蒸馏水作冷却剂对SiC-Si面抛光1 h,Ra由90 nm降至4.3 nm.
Luo等[60-61]对比研究了半固结磨粒抛光和固结磨粒抛光的机理.结果表明,柔性抛光垫可使不同粒度磨粒的出刃高度相同,有助于实现SiC表面的平整化,也便于采用较大的固结磨粒以避免超细磨料的聚结现象.但磨粒过大,材料去除尺度>几十nm时,SiC为脆性去除。采用40 μm的金刚石磨粒进行固结,在塑性去除域加工,获得Ra为5.1 nm的纳米级光滑表面,材料去除率为0.16 μm/h。
2.4 SiC的光催化辅助抛光2003年,日本熊本大学的Ishikawa等[62]发现,室温下TiO2作为光催化剂可产生强氧化性的·OH,促使SiC分解为CO2和SiO2,尽管分解速率很低,但TiO2光催化处理可得到无亚表层损伤的纳米级表面. 2012年,日本九州大学的Ohnishi等[63]在碱性SiO2抛光液中添加质量分数为0.3%的TiO2(粒径0.3 μm),发现紫外线照射可提高SiC的抛光质量,但材料去除率 < 0.06 μm/h.
2016年,清华大学的Li等[64]在传统胶体SiO2抛光液中添加经紫外线修饰的碳纳米管-TiO2复合催化剂颗粒,在室温下对4H-SiC-Si面进行抛光,通过试验得到Ra为0.043 nm的原子级光滑表面,材料去除率为0.126 μm/h. 2017年,华侨大学的Lu等[65]研制TiO2包覆金刚石的复合磨粒,在紫外线照射下,对6H-SiC进行了机械抛光(以水作为冷却剂).对比试验发现,TiO2与金刚石复合磨粒的材料去除率约0.115 μm/h,约为单纯金刚石磨粒的2倍(0.061 μm/h),表面质量得到提高(Ra为0.915 nm).分析认为紫外线照射TiO2的光催化效应提高了·OH的生成速率,加快了SiC表面的氧化速度.
2017年,沈阳工业大学的Yuan等[66]通过配方优化,研制了含有TiO2+H2O2+SiO2磨粒的抛光液(pH为2),在紫外线照射下对初抛后的4H-SiC-Si面进行光催化辅助抛光,以材料去除率为0.95 μm/h的高去除率获得了较光滑的SiC表面(Ra为0.35 nm),表明通过优化光催化辅助抛光液的配方,可以对SiC实现高效抛光.
综上所述,SiC-CMP典型增效技术如表 1所示(若未注明均指对SiC-Si面的抛光).
表 1
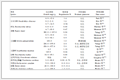
材料去除率/(μm·h-1) Ra/nm
混合磨粒 游离SiO2+游离金刚石(35 g/L) 0.550 0.370 材料去除率和Ra均得到改善(与SiO2单独作磨粒相比)[17];
固结磨粒 固结金刚石磨粒+游离Al2O3+KMnO4 1.300 < 0.500 材料去除率是采用聚氨酯抛光垫的2.5倍[56];
固结Fe磨粒+Al2O3磨粒的抛光垫+H2O2(pH为4) 0.740 0.159 比传统化学机械抛光的材料去除率高73%[57];
强氧化剂增效 CeO2磨粒+KMnO4(pH为2) 1.089 0.110 KMnO4在酸性环境下有助于材料去除率提高;添加CeO2优于添加SiO2[31];
催化增效 铁制抛光盘+铁粉+H2O2 接近1.000* 0.500 *去除率是针对SiC-C面的,针对Si面的要小得多[40];
电化学机械抛光 游离CeO2+30 min(pH为9.24)+持续电流 3.620** RMS 0.23 **去除率是针对经机械抛光的SiC-ECMP[53];
CeO2/PU核壳颗粒+周期偏压(Ton:Toff=2.5 min:7.5 min) 3.700 0.510 未用抛光垫,CeO2/PU核壳质量比为2.5,E=10 V[55];
光催化辅助 TiO2+H2O2+SiO2磨粒 0.950 0.350 材料去除率在类似研究中很高,值得关注[66];
表 1 SiC-CMP典型增效技术比较 Table 1 Comparison of typical high-efficient polishing methods
2.5 其他抛光增效技术在提高化学作用方面,高温氢蚀可以高效刻蚀SiC,但难以达到晶片的全局平整化要求,而且加工表面存在内应力,易产生后续外延膜缺陷.同时,该技术需要造价高、结构复杂的装置.日本大阪大学的Yamamura等[67]和Deng等[68]用等离子体辅助以及热氧化等手段使SiC表面生成SiO2后,再结合化学机械抛光或“固结磨粒”抛光,可获得原子级光滑、无内应力的单晶SiC表面.但该技术的材料去除率 < 0.1 μm/h,且需要复杂的等离子体生成和辐照装置,工艺操作性差.
在提高磨粒的机械作用方面,除了固结磨粒抛光之外,哈尔滨工业大学翟文杰课题组应用磁流变液的磨粒聚集效应[69],以及超声振动的机械强化去除(冲击、空蚀、摩擦)作用[70]对SiC晶片的高效抛光进行了研究.结果表明,机械去除作用不能过度增强,应结合SiC脆塑性转变阈值来指导实施,以保证加工表面质量.
3 结论与展望本文综述了SiC-CMP的研究现状,特别以SiC-CMP的材料去除率和表面质量为指标,比较和论述了SiC催化辅助抛光、SiC-ECMP、固结磨料抛光、光催化辅助抛光等增效新技术的研究进展,得到如下结论:
1) 采用胶体SiO2碱性抛光液的SiC-CMP可获得原子级光滑无缺陷表面,但材料去除率最大只能达到0.1~0.2 μm/h.
2) 在含SiO2、Al2O3或CeO2磨粒的抛光液中加入H2O2或KMnO4氧化剂,可提高SiC-CMP的材料去除率,若进一步添加适当分散剂可使SiC-Si面的材料去除率达到μm/h级.
3) 混合磨粒抛光和固结磨料抛光主要提高化学机械抛光的机械去除作用,必须结合抛光液的氧化作用才能使SiC-CMP的材料去除率达到μm/h级.
4) SiC电化学机械抛光中氧化物生成速率可达数十μm/h,远大于对应的机械去除速率.为高效获得优质的SiC表面,可采用“二步法”或采用优化周期性偏压的电化学机械抛光.
5) 无磨粒Pt催化盘辅助化学机械抛光受压力和转速的限制,材料去除率只能接近0.5 μm/h.基于铁系催化剂的芬顿反应可提高SiC-C面化学机械抛光的材料去除率,而对硅面的材料去除率影响不大.
6) 结合抛光液中H2O2氧化剂和TiO2催化功能磨粒,辅以紫外线的光催化效应可使SiC-Si面的材料去除率接近μm/h级.
为提升SiC的抛光效率和质量,应综合利用SiC氧化理论及电化学、催化化学等方法提高SiC氧化速率,同时还要提供与SiC氧化速率相匹配的氧化层机械去除速率(混合磨粒、固结磨粒抛光和超声辅助是其主要实现技术).目前,采用施加周期性电压的电化学机械抛光以及采用催化金属盘或催化磨粒的催化(光催化)辅助抛光是化学增效的两种主流方法. SiC-CMP的催化、电化学增效机理研究和材料去除率模型建立(定量研究)是目前亟待解决的难点.结合化学和机械两方面增效的复合技术,如,集磁流变-催化复合抛光、超声-电化学机械抛光、超声-催化盘辅助抛光、固结磨粒-超声-催化抛光等,是未来SiC高效抛光的发展方向.
参考文献
[1] 肖强, 李言, 李淑娟. SiC单晶片化学机械抛光超精密加工技术现状与趋势[J]. 宇航材料工艺, 2010, 40(1): 9-13.
XIAO Qiang, LI Yan, LI Shujuan. Situation and development trends of CMP for SiC monocrystal slice[J]. Aerospace Materials & Technology, 2010, 40(1): 9-13.
[2] 李娟, 陈秀芳, 马德营, 等. SiC单晶片的超精密加工[J]. 功能材料, 2006, 37(1): 70-72.
LI Juan, CHEN Xiufang, MA Deying, et al. High-prcesion processing of silicon carbide[J]. Journal of Functional Materials, 2006, 37(1): 70-72.
[3] AIDA H, DOI T, TAKEDA H, et al. Ultraprecision CMP for sapphire, GaN, and SiC for advanced optoelectronics materials[J]. Current Applied Physics, 2012, 12(9): S41-S46. DOI:10.1016/j.cap.2012.02.016
[4] 甘阳, 张飞虎. 单晶碳化硅和蓝宝石基片化学机械抛光的表面反应层形成机制的研究进展[J]. 科学通报, 2016, 61(36): 3930-3939.
GAN Yang, ZHANG Feihu. Review on formation mechanism of chemical reaction layer during chemical mechanical polishing of monocrystalline SiC and sapphire substrates[J]. Chinese Science Bulletin, 2016, 61(36): 3930-3939. DOI:10.1360/N972015-01415
[5] CHEN Xiufang, XU Xiangang, HU Xiaobo, et al. Anisotropy of chemical mechanical polishing in silicon carbide substrates[J]. Materials Science & Engineering B, 2007, 142(1): 28-30. DOI:10.1016/j.mseb.2007.06.015
[6] KATO T, WADA K, HOZOMI E, et al. High throughput SiC wafer polishing with good surface morphology[J]. Materials Science Forum, 2007, 556/557: 753-756. DOI:10.4028/www.scientific.net/MSF.556-557
[7] NITTA H, ISOBE A, PARK J H, et al. Research on reaction method of high removal rate chemical mechanical polishing slurry for 4H-SiC substrate[J]. Japanese Journal of Applied Physics, 2011, 50(4): 046501-046501. DOI:10.1143/JJAP.50.046501
[8] PAN G S, ZHOU Y, LUO G, et al. Chemical mechanical polishing (CMP) of on-axis Si-face 6H-SiC wafer for obtaining atomically flat defect-free surface[J]. Journal of Materials Science Materials in Electronics, 2013, 24(12): 5040-5047. DOI:10.1007/s10854-013-1519-1
[9] ZHANG Peng, FENG Xianying, YANG Jingfang. Research on a processing model of CMP 6H-SiC (0001) single crystal wafer[J]. Journal of Semiconductors, 2014, 35(9): 166-170. DOI:10.1088/1674-4926/35/9/096002
[10] ZHOU L, AUDURIER V, PIROUZ P, et al. Chemical mechanical polishing of silicon carbide[J]. Electrochem Soc, 1997, 144(6): L161-163. DOI:10.1149/1.1837711
[11] CHEN Xiufang, XU Xiangang, LI Juan, et al. Surface polishing of 6H-SiC substrates[J]. Journal of Materials Science & Technology, 2007, 23(3): 430-432.
[12] NESLEN C L, MITCHEL W C, HENGEHOLD R L. Effects of process parameter variations on the removal rate in chemical mechanical polishing of 4H-SiC[J]. Journal of Electronic Materials, 2001, 30(10): 1271-1275. DOI:10.1007/s11664-001-0111-2
[13] ZHOU Yan, PAN Guoshun, SHI Xiaolei, et al. Effects of ultra-smooth surface atomic step morphology on chemical mechanical polishing (CMP) performances of sapphire and SiC wafers[J]. Tribology International, 2015, 87: 145-150. DOI:10.1016/j.triboint.2015.02.013
[14] ZHOU Yan, PAN Guoshun, SHI Xiaolei, et al. XPS, UV-vis spectroscopy and AFM studies on removal mechanisms of Si-face SiC wafer chemical mechanical polishing (CMP)[J]. Applied Surface Science, 2014, 316(1): 643-648. DOI:10.1016/j.apsusc.2014.08.011
[15] HEYDEMANN V D, EVERSON W J, GAMBLE R D, et al. Chemi-mechanical polishing of on-axis semi-insulating SiC substrates[J]. Materials Science Forum, 2004, 457-460: 805-808. DOI:10.4028/www.scientific.net/MSF.457-460.805
[16] KUO P, CURRIER I. Augmented CMP techniques for silicon carbide[C]// Silicon Carbide and Related Materials 2005. Switzerland: Trans Tech Publications, 2006: 1099-1102. DOI: https://doi.org/10.4028/www.scientific.net/MSF.527-529.1099.
[17] LEE G S, HWANG H H, SON C H, et al. The effect of slurry composition and flatness on sub-surface damage and removal in chemical mechanical polishing of 6H-SiC[C]// Silicon Carbide and Related Materials 2008. Barcelona: Trans Tech Publications, 2009: 605-608. DOI: https://doi.org/10.4028/www.scientific.net/MSF.615-617.605.
[18] AN J H, LEE G S, LEE W J, et al. Effect of process parameters on material removal rate in chemical mechanical polishing of 6H-SiC (0001)[C]// Silicon Carbide and Related Materials 2007. Otsu: Trans Tech Publications, 2008: 831-834. DOI: 10.4028/www.scientific.net/MSF.600-603.831.
[19] LEE H S, KIM D I, AN J H, et al. Hybrid polishing mechanism of single crystal SiC using mixed abrasive slurry (MAS)[J]. CIRP Annals-Manufacturing Technology, 2010, 59(1): 333-336. DOI:10.1016/j.cirp.2010.03.114
[20] LEE H S, JEONG H. Chemical and mechanical balance in polishing of electronic materials for defect-free surfaces[J]. CIRP Annals-Manufacturing Technology, 2009, 58(1): 485-490. DOI:10.1016/j.cirp.2009.03.115
[21] ZHU Z, FISCHER T E, MURATOV V A. Tribochemical polishing of silicon carbide in oxidant solution[J]. Wear, 1999, 225-2259(4): 848-856. DOI:10.1016/S0043-1648(98)00392-5
[22] MURATOV V A, FISCHER T E. Tribochemical Polishing[J]. Annual Review of Materials Science, 2000, 30(30): 27-51.
[23] LAGUDU U R K, ISONO S, KRISHNAN S, et al. Role of ionic strength in chemical mechanical polishing of silicon carbide using silica slurries[J]. Colloids & Surfaces A: Physicochemical & Engineering Aspects, 2014, 445: 119-127. DOI:10.1016/j.colsurfa.2014.01.038
[24] SINGH R K, ARJUNAN A C, KANNAN B, et al. Novel reactive chemical mechanical polishing technology for fabrication of SiC mirrors[J]. Proceedings of SPIE-The International Society for Optical Engineering, 2013, 8837(43): 88370H-88370H. DOI:10.1117/12.2024765
[25] FU X A, ZORMAN C A, MEHREGANY M. Chemical mechanical polishing of cubic silicon carbide films grown on Si (100) wafers[J]. Journal of the Electrochemical Society, 2002, 149(12): G643-G647. DOI:10.1149/1.1517285
[26] LIANG Qingrui, HU Xiaobo, CHEN Xiufang, et al. Chemical mechanical polishing of 4H-SiC with strong oxidizing slurry[J]. Journal of Synthetic Crystals, 2015, 44(7): 1741-1747.
[27] YIN T, DOI T, KUROKAWA S, et al. The effects of strong oxidizing slurry and processing atmosphere on double-sided CMP of SiC wafer[J]. Advanced Materials Research, 2012, 591-593(25): 1131-1134. DOI:10.4028/www.scientific.net/AMR.591-593.1131
[28] KUROKAWA S, DOIT, OHNISHI O, et al. Characteristics in SiC-CMP using MnO2 slurry with strong oxidant under different atmospheric conditions[C]// Materials Research Society Spring Meeting. San Francisco: Materials Research Society, 2013: 39-47. DOI: 10.1557/opl.2013.903.
[29] 杨文航. SiC单晶化学机械抛光过程中的化学作用研究[D]. 哈尔滨: 哈尔滨工业大学, 2014.
YANG Wenhang. Study on polishing chemistry during chemical mechanical polishing of SiC single crystals[D]. Harbin: Dissertation of Master of Harbin Institute of Technology, 2014.
[30] LAGUDU U R K, BABU S V. Effect of transition metal compounds on amorphous SiC removal rates[J]. Journal of Solid State Science and Technology, 2014, 6(3): 219-225. DOI:10.1149/2.021406jss
[31] CHEN Guomei, NI Zifeng, XU Laijun, et al. Performance of colloidal silica and ceria based slurries on CMP of Si-face 6H-SiC substrates[J]. Applied Surface Science, 2015, 359: 664-668. DOI:10.1016/j.apsusc.2015.10.158
[32] CHEN Guomei, NI Zifeng, BAI Yanwen, et al. The role of interactions between abrasive particles and substrate surface in chemical-mechanical planarization of Si-face 6H-SiC[J]. RSC Advances, 2017, 7(28): 16938-16952. DOI:10.1039/c6ra27508g
[33] DENG H, ENDO K, YAMAMURA K. Competition between surface modification and abrasive polishing: a method of controlling the surface atomic structure of 4H-SiC (0001)[J]. Scientific Reports, 2015, 8947(5): 1-6. DOI:10.1038/srep08947
[34] HARA H, SANO Y, MIMURA H, et al. Novel abrasive-free planarization of 4H-SiC (0001) using catalyst[J]. Journal of Electronic Materials, 2006, 35(8): L11-L14. DOI:10.1007/s11664-006-0218-6
[35] ARIMA K, HARA H, MURATA J, et al. Atomic-scale flattening of SiC surfaces by electroless chemical etching in HF solution with Pt catalyst[J]. Applied Physics Letters, 2007, 90(20): 202106-202106. DOI:10.1063/1.2739084
[36] ARIMA K, ENDO K, YAMAUCHI K, et al. Mechanism of atomic-scale passivation and flattening of semiconductor surfaces by wet-chemical preparations[J]. Journal of Physics Condensed Matter, 2011, 23(39): 394202. DOI:10.1088/0953-8984/23/39/394202
[37] OKAMOTO T, SANO Y, TACHIBANA K, et al. Improvement of removal rate in abrasive-free planarization of 4H-SiC substrates using catalytic platinum and hydrofluoric acid[J]. Japanese Journal of Applied Physics, 2012, 51(4): 046501-046501. DOI:10.1143/JJAP.51.046501
[38] SANO Y, ARIMA Z K, YAMAUCHI K. Planarization of SiC and GaN wafers using polishing technique utilizing catalyst surface reaction[J]. Journal of Solid State Science and Technology, 2013, 8(2): N3028-N3035. DOI:10.1149/2.007308jss
[39] LIN Y C, KAO C H. A study on surface polishing of SiC with a tribochemical reaction mechanism[J]. International Journal of Advanced Manufacturing Technology, 2005, 25(1/2): 33-40. DOI:10.1007/s00170-003-1873-x
[40] KUBOTA A, YAGI K, MURATA J, et al. A study on a surface preparation method for single-crystal SiC using a Fe catalyst[J]. Journal of Electronic Materials, 2009, 38(1): 159-163. DOI:10.1007/s11664-008-0583-4
[41] KUBOTA A, YOSHIMURA M, FUKUYAMA S, et al. Planarization of C-face 4H-SiC substrate using Fe particles and hydrogen peroxide solution[J]. Precision Engineering, 2012, 36(1): 137-140. DOI:10.1016/j.precisioneng.2011.09.003
[42] ZHOU Yan, PAN Guoshun, SHI Xiaolei, et al. Chemical mechanical planarization (CMP) of on-axis Si-face SiC wafer using catalyst nanoparticles in slurry[J]. Surface & Coatings Technology, 2014, 251(1): 48-55. DOI:10.1016/j.surfcoat.2014.03.044
[43] YAGI K, MURATA J, KUBOTA A, et al. Catalyst-referred etching of 4H-SiC substrate utilizing hydroxyl radicals generated from hydrogen peroxide molecules[J]. Surface & Interface Analysis, 2010, 40(6/7): 998-1001. DOI:10.1002/sia.2804
[44] 徐少平, 路家斌, 阎秋生, 等. 单晶SiC化学机械抛光液的固相催化剂研究[J]. 机械工程学报, 2017, 53(21): 167-173.
XU Shaoping, LU Jiabin, YAN Qiusheng, et al. Solid catalysts based on Fenton reaction for SiC wafer in chemical mechanical polishing[J]. Journal of Mechanical Engineering, 2017, 53(21): 167-173. DOI:10.3901/JME.2017.21.167
[45] 阎秋生, 徐少平, 路家斌, 等. 单晶SiC化学机械抛光液化学反应参数研究[J]. 机械设计与制造, 2017(9): 98-100.
YAN Qiusheng, XU Shaoping, LU Jiabin, et al. Study on chemical reaction parameters of CMP solution for single-crystal SiC[J]. Machinery Design & Manufacture, 2017(9): 98-100. DOI:10.19356/j.cnki.1001-3997.2017.09.026
[46] 高飞, 徐永宽, 程红娟, 等. 4H-SiC (0001)硅面原子级平整抛光方法[J]. 微纳电子技术, 2014, 51(9): 610-614.
GAO Fei, XU Yongkuan, CHENG Hongjuan, et al. Atomic-scale flattening polishing method of 4H-SiC (0001) Si face[J]. Micronanoelectronic Technology, 2014, 51(9): 610-614. DOI:10.13250/j.cnki.wndz.2014.09.011
[47] DORP D H V, SATTLER J J H B, OTTER J H D, et al. Electrochemistry of anodic etching of 4H and 6H-SiC in fluoride solution of pH 3[J]. Electrochimica Acta, 2009, 54(26): 6269-6275. DOI:10.1016/j.electacta.2009.05.086
[48] VAN DORP D H, WEYHER J L, KELLY J J. Anodic etching of SiC in alkaline solutions[J]. Journal of Micromechanics & Microengineering, 2007, 17(4): 50-55. DOI:10.1088/0960-1317/17/4/S04
[49] CHANG W H. Micromachining of p-type 6H-SiC by electrochemical etching[J]. Sensors & Actuators A Physical, 2004, 112(1): 36-43. DOI:10.1016/j.sna.2003.09.046
[50] KE Y, YAN F, DEVATY R P, et al. Surface polishing by electrochemical etching of p-type 4H SiC[J]. Journal of Applied Physics, 2009, 106(6): 259. DOI:10.1063/1.3212541
[51] LI C, BHAT I B, WANG R J, et al. Electro-chemical mechanical polishing of silicon carbide[J]. Journal of Electronic Materials, 2004, 33(5): 481-486. DOI:10.1007/s11664-004-0207-6
[52] BALLARIN N, CARRARO C, MABOUDIAN R, et al. Electro-polishing of n-type 3C-polycrystalline silicon carbide[J]. Electro-chemistry Communications, 2014, 40(3): 17-19. DOI:10.1016/j.elecom.2013.12.018
[53] DENG H, HOSOYA K, IMANISHI Y, et al. Electro-chemical mechanical polishing of single-crystal SiC using CeO2 slurry[J]. Electrochemistry Communications, 2015, 52: 5-8. DOI:10.1016/j.elecom.2015.01.002
[54] SHEN Xinmin, TU Qunzhang, DENG Hui, et al. Comparative analysis on surface property in anodic oxidation polishing of reaction-sintered silicon carbide and single-crystal 4H silicon carbide[J]. Applied Physics A, 2016, 122(4): 354. DOI:10.1007/s00339-016-9896-y
[55] MURATA J, YODOGAWA K, BAN K. Polishing-pad-free electrochemical mechanical polishing of single-crystalline SiC surfaces using polyurethane-CeO2 core-shell particles[J]. International Journal of Machine Tools & Manufacture, 2016, 114: 1-7. DOI:10.1016/j.ijmachtools.2016.11.007
[56] TSAI M Y, WANG S M, TSAI C C, et al. Investigation of increased removal rate during polishing of single-crystal silicon carbide[J]. International Journal of Advanced Manufacturing Technology, 2015, 80(9/10/11/12): 1511-1520. DOI:10.1007/s00170-015-7023-4
[57] HO J K, HUANG C Y, TSAI M Y, et al. Investigation of polishing pads impregnated with Fe and Al2O3 particles for single-crystal silicon carbide wafers[J]. Applied Sciences, 2016, 6(3): 89. DOI:10.3390/app6030089
[58] LU Jing, LI Yang, XU Xipeng. The effects of abrasive yielding on the polishing of SiC wafers using a semi-fixed flexible pad[J]. Journal of Engineering Manufacture, 2015, 229(1): 170-177. DOI:10.1177/0954405414563556
[59] LU J, LUO Q F, MAO X Y, et al. Fabrication of a resin-bonded ultra-fine diamond abrasive polishing tool by electrophoretic co-deposition for SiC processing[J]. Precision Engineering, 2017, 47: 353-361. DOI:10.1016/j.precisioneng.2016.09.009
[60] LUO Qiufa, LU Jing, XU Xipeng. Study on the processing characteristics of SiC and sapphire substrates polished by semi-fixed and fixed abrasive tools[J]. Tribology International, 2016, 104: 191-203. DOI:10.1016/j.triboint.2016.09.003
[61] LUO Qiufa, LU Jing, XU Xipeng. A comparative study on the material removal mechanisms of 6H-SiC polished by semi-fixed and fixed diamond abrasive tools[J]. Wear, 2016, 350-351: 99-106. DOI:10.1016/j.wear.2016.01.014
[62] ISHIKAWA Y, MATSUMOTO Y, NISHIDA Y, et al. Surface treatment of silicon carbide using TiO2 (Ⅳ) photocatalyst[J]. Journal of the American Chemical Society, 2003, 125(21): 6558-6562. DOI:10.1021/ja020359i
[63] OHNISHI O, DOI T, KUROKAWA S, et al. Effects of atmosphere and ultraviolet light irradiation on chemical mechanical polishing characteristics of SiC wafers[J]. Japanese Journal of Applied Phy-sics, 2012, 51(51): 4403-4408. DOI:10.1143/JJAP.51.05EF05
[64] LI Xu, PAN Guoshun, ZOU Chunli, et al. Planarization of SiC using a novel catalyst (UV-modified TiO2) to improve its MRR[C]// 2016 International Conference on Planarization/CMP Technology. Beijing: Chemical Mechanical Planarization Users Group-China, 2016: 37-41.
[65] LU Jing, WANG Yaguang, LUO Qiufa, et al. Photocatalysis assisting the mechanical polishing of a single-crystal SiC wafer utilizing an anatase TiO2-coated diamond abrasive[J]. Precision Engineering, 2017(49): 235-242. DOI:10.1016/j.precisioneng.2017.02.011
[66] YUAN Zewei, HE Yan, SUN Xingwei, et al. UV-TiO2 photocatalysis-assisted chemical mechanical polishing 4H-SiC wafer[J]. Materials & Manufacturing Processes, 2017, 33(11): 1214-1222. DOI:10.1080/10426914.2017.1364855
[67] YAMAMURA K, TAKIGUCHI T, UEDA M, et al. Plasma assisted polishing of single crystal SiC for obtaining atomically flat strain-free surface[J]. CIRP Annals-Manufacturing Technology, 2011, 60(1): 571-574. DOI:10.1016/j.cirp.2011.03.072
[68] DENG Hui, ENDO K, YAMAMURA K. Atomic-scale planarization of 4H-SiC (0001) by combination of thermal oxidation and abrasive polishing[J]. Applied Physics Letters, 2013, 103(11): 111603-111606. DOI:10.1063/1.4821068
[69] 王翱翔. 单晶碳化硅磁场辅助电化学机械研抛实验与机理研究[D]. 哈尔滨: 哈尔滨工业大学, 2017.
WANG Aoxiang. The experiment and mechanism study on magnetic field assisted electrochemical mechanic polishing of single crystal silicon carbide[D]. Harbin: Dissertation of Master of Harbin Institute of Technology, 2017.
[70] 孙丙镇. 碳化硅超声-电化学抛光仿真与研抛实验研究[D]. 哈尔滨: 哈尔滨工业大学, 2016.
SUN Bingzhen. Simulation and experimental study on ultrasonic-electrochemical polishing of silicon carbide[D]. Harbin: Dissertation of Master of Harbin Institute of Technology, 2016.