Baogang Zhang1,Lin Lyu1,Ming Liu2,Guanglei Li1,Pengli Yuan1
(1.Laboratory of Building Environment and New Energy Resources, Faculty of Infrastructure Engineering, Dalian University of Technology, Dalian 116024, Liaoning, China;2.School of Architecture and Fine Art, Dalian University of Technology, Dalian 116024, Liaoning, China)
Abstract:
Nowadays, people still rely on traditional heating methods in rural areas of northern China, such as Kang (bed-stoves) and burning caves in cold winter. Field measurements of indoor environment were carried out in several rural houses with burning-cave-coil-Kang coupling heating system in northern China. The results show that this system is able to realize the graded use of internal energy of burning cave. The temperature of supply pipe water ranged from 30 ℃ to 50 ℃ which met the demands in 74.7% of time. The surface temperature of Kang maintained at above 25 ℃. Compared with traditional burning cave, using burning-cave-coil-Kang coupled with heating system has a higher thermal efficiency of 48.9%, which is 8.32% higher than the traditional one.
Key words: burning cave pipe coil Kang coupled heating system thermal performance
DOI:10.11916/j.issn.1005-9113.17108
Clc Number:TU832.1
Fund:
Baogang Zhang, Lin Lyu, Ming Liu, Guanglei Li, Pengli Yuan. Burning Cave-Pipe Coil-Kang Coupled Heating System Research[J]. Journal of Harbin Institute of Technology (New Series), 2018, 25(4): 56-64. DOI: 10.11916/j.issn.1005-9113.17108.

Fund Sponsored by the National Natural Science Foundation of China (Grant No. 51178075) and the Fundamental Research Funds for the Central Universities (Grant No. DUT17RW118) Corresponding author Ming Liu, E-mail: liumingyitj@163.com Article history Received: 2017-09-11
Contents Abstract Full text Figures/Tables PDF
Burning Cave-Pipe Coil-Kang Coupled Heating System Research
Baogang Zhang1, Lin Lyu1, Ming Liu2


1. Laboratory of Building Environment and New Energy Resources, Faculty of Infrastructure Engineering, Dalian University of Technology, Dalian 116024, Liaoning, China;
2. School of Architecture and Fine Art, Dalian University of Technology, Dalian 116024, Liaoning, China
Received: 2017-09-11
Fund: Sponsored by the National Natural Science Foundation of China (Grant No. 51178075) and the Fundamental Research Funds for the Central Universities (Grant No. DUT17RW118)
Corresponding author: Ming Liu, E-mail: liumingyitj@163.com
Abstract: Nowadays, people still rely on traditional heating methods in rural areas of northern China, such as Kang (bed-stoves) and burning caves in cold winter. Field measurements of indoor environment were carried out in several rural houses with burning-cave-coil-Kang coupling heating system in northern China. The results show that this system is able to realize the graded use of internal energy of burning cave. The temperature of supply pipe water ranged from 30 ℃ to 50 ℃ which met the demands in 74.7% of time. The surface temperature of Kang maintained at above 25 ℃. Compared with traditional burning cave, using burning-cave-coil-Kang coupled with heating system has a higher thermal efficiency of 48.9%, which is 8.32% higher than the traditional one.
Key words: burning cave pipe coil Kang coupled heating system thermal performance
1 Introduction In rural areas of north China, over 50% farmers use Kang heating. Kang has the function of health care, especially to the elderly with backache and arthrists. For hundreds of years, northern farmers have been accustomed to Kang lifestyle. However, scholars found that traditional oven-Kang system had the problems of local overheating, uneven temperature distribution on surfaces of Kangs, and unstable indoor temperature between day and night etc. Therefore, burning cave heating came out. It can not only provide continuous heat but also make optimal use of biomass energy. The Refs.[1-6] illustrated that thermal efficiency of traditional burning cave was low. Relative scholars led a series of methods to improve through the issues in the study[7-15]. However, the above research for improvement ignored the Kang lifestyle of northern farmers. It is necessary to introduce an effective heating mode which can ensure the heating-comfort performance of Kang surface and reduce the energy waste at the same time.
The paper proposed an improved burning-cave- pipe coil-Kang coupled heating system, as shown in Fig. 1. It makes optimal use of the energy of internal fuel smoldering combustion: the first part is based on the temperature of burning cave cover plate to heat the indoor air by radiation and convection heat transfer. The other part is based on the radiation heat transfer of the burning cave coil to heat the supply pipe. With the aid of a circulating pump, the hot water heat is introduced into the Kang coil, increasing the temperature of Kang surface. Field measurements and theoretical analysis were also conducted to verify the performance.
Figure 1
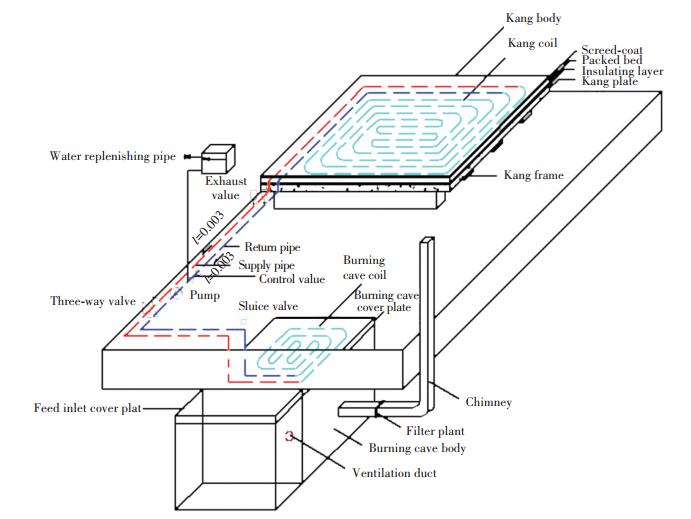
2 Experiment and Methods 2.1 Experiment Table To discuss the thermal performance of the coupled heating system, a house integrated with an optimized burning cave and Kang has been built in Fuxin of northern China as shown in Fig. 2. The system is composed of a burning cave, burning cave coils, a Kang, Kang coil and a pipe system. The diameter of burning cave coil is 32 mm, linked at right angles in a diminishing concentric spiral, as shown in Fig. 3. The burning cave coils are designed 150 mm below the burning cover plate, as shown in Fig. 4. The water in the coils is filtered. Water hardness < 450 mg/L and 6.5 < pH < 9.
Figure 2

Figure 3
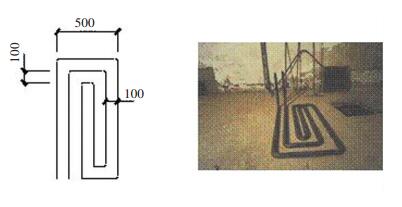
Figure 4
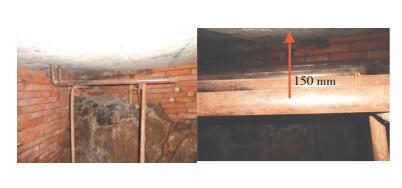
The diameter of Kang coil is 15 mm and made of cross linked polyethylene. The Kang coil takes form and shape as shown in Fig. 5. The structure of Kang body is shown in Fig. 6 and the materials of each layer are shown in Table 1.
Figure 5
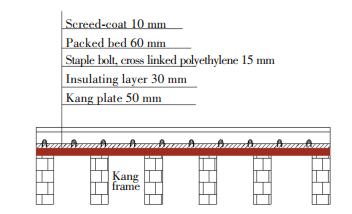
Figure 6
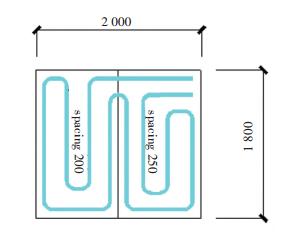
表 1
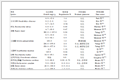
material Thickness
(mm) Density
(kg/m3) Thermal
conductivity (W/m·K) Specific heat
(kJ/kg·K)
Kang plate 50 1 560 0.490 0.754
EPS 30 20 0.047 1 470
Clay sand inclusion 60 1 460 1.303 1.968
Cement mortar 10 1 800 0.930 1.050
Table 1 Kang body structural materials and their physical property parameter values
The model of pump is LRS25-6. The volume of expansion tank is 10 L. The diameter of pipe is 32 mm, as shown in Fig. 7. According to the calculation, the speed of system water is 32 kg/h, and the quantity is 7.65 L. Based on the above parameters, the selected pump model is LRS25-6, the maximum lift of water pump is 6 m, and the maximum flow is 50 L/min, as shown in Fig. 6. The volume of the expansion tank is 10 L, as shown in Fig. 8.
Figure 7
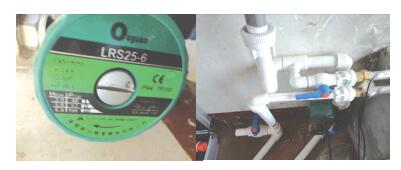
Figure 8
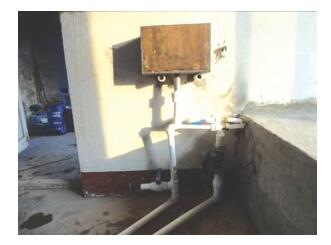
2.2 Experiment Condition The experimental table is 2 200 mm×1 900 mm×1 200 mm(length×width×height). The fuel filled in the burning cave is cob. After filling the fuel, we put dry twigs on the surface of the fuel to ignite. The height and weight of the fuel are 550 mm and 220 kg respectively. The low calorific value of the fuel is 13 129.82 kJ/kg. The running time is from October 29, 2014 to November 6, 2014, exactly in heating period.
The main test parameters of the experiment include indoor and outdoor temperature and humidity, Kang surface temperature, the temperature of supply and return pipe, the temperature of enclosure structure, burning cave temperature, flue gas temperature, burning cave floor surface temperature, above Kang air temperature, above burning cave floor air temperature, indoor air temperature and indoor air quality, as shown in Table 2.
表 2
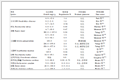
accuracyAppearance
oftest
instrument
Thetemperature
of Kang surface,
burning cave floor,
supply and return
pipe and enclosure
structureJTNT-A±0.5℃
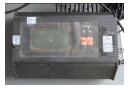
Burning cave and
flue gas temperaturK type
thermocouple+
Changhui
SWP-ASR color
paperless
recorder0.5%FS
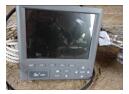
Indoor and
outdoor
temperature and
humidityTesto DE±0.5℃;
±3%RH

Indoor CO2
concentratioCO2 automatic
recorder±50×10-6

Table 2 Information of the test instrument
The measuring points of indoor temperature and relative humidity were arranged in the indoor center 1.5 m above the ground and the test interval is 10 min. The measuring points of burning cave floor air temperature are arranged at a distance of 0.8 m from the burning cave floor. Specific measuring point arrangement is shown in Fig. 9.
Figure 9
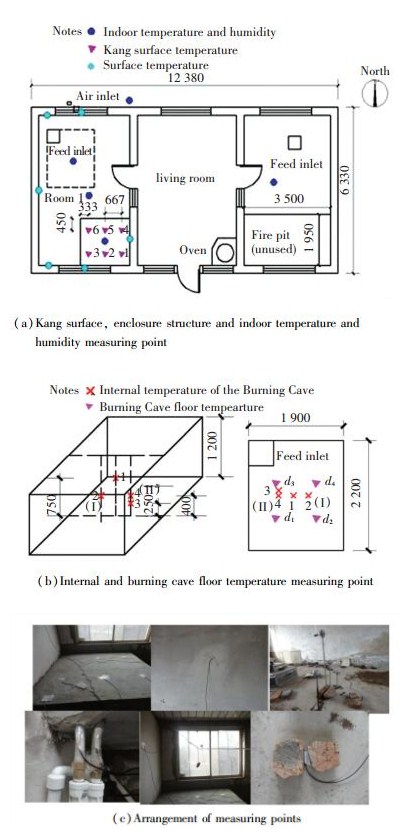
3 Results and Analysis 3.1 Thermal Performance Analysis of Burning Cave As shown in Fig. 10, during the smoldering process, the temperature of burning cave floor fluctuated dramatically. At the initial stage, it climbed to the peak value 61.5 ℃ which exceeded the temperature of human body. When the water pump started to work on October 30, 2014, 4 PM the temperature was in a downtrend. Generally speaking, the pump started to work, so as to take part of the heat of the burning cave into the Kang body, so that the heat of the burning cave floor was reduced, and the excess heat can be used in steps.
Figure 10
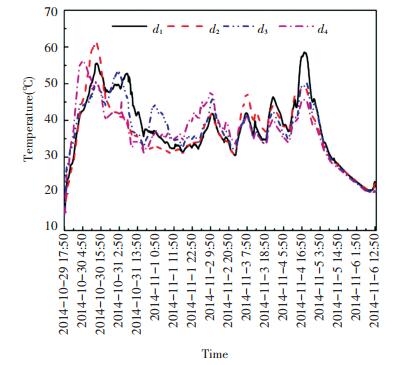
Known from the analysis, when internal burning cave temperature declined, the temperature of burning cave floor dropped rapidly after slight respond time. In addition, the burning cave floor temperature was not only related to burning cave internal heat source temperature, but also related to the structure of the burning cave cover plate. The structural layer of burning cave cover plate was shown in Table 3.
表 3
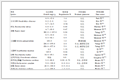
material Thickness
(mm) Density
(kg/m3) Thermal
conductivity
(W/m·K) Specific
heat
(kJ/kg·K)
Concrete slab 30 1 930 0.790 0.837
Filling(Clay sand
inclusion) 60 1 460 1.303 1.968
Cement mortar 10 1 800 0.930 1.050
Table 3 Construction materials of burning cave floor and their physical property parameter values
Using the heat capacity calculation method[16], experimental burning cave floor heat capacity was 239.76 kJ/(m2·K), which is less than the floor construction capacity 462.6 kJ/ (m2·K). Therefore this burning cave floor was easy to be affected by heat source, which should be built based on reasonable structure design to meet the needs of personnel activities.
3.2 Analysis of Heat Transfer Characteristics of Pipe The heated water was transported under the action of the water pump, and the temperature of Kang supply pipe ranged from 21 ℃ to 46.3 ℃ as shown in Fig. 11. The maximum difference between temperature of supply and return pipe was 8.6 ℃. As shown in Fig. 12, the Kang coil temperature ranged from 30 ℃ to 50 ℃ accounted for 74.7% in line with the relevant norms. Thus the excess heat of the burning cave was able to meet the temperature of the Kang coils. What's more it ensured comfort Kang surface in terms of temperature.
Figure 11
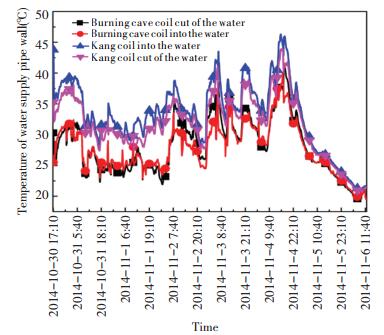
Figure 12
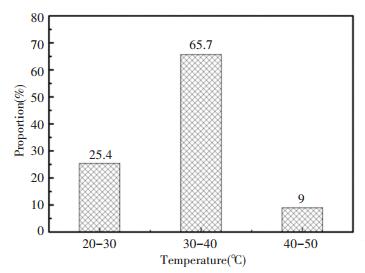
3.3 Thermal Characteristics of Kang Body In order to study whether the system can meet the requirements of thermal comfort, the experiment used a quilt with a thickness of 30 mm to simulate the working condition at night as shown in Fig. 13. In the early stage, the temperature of spot 4 and spot 5 were higher than other spots. The reason is these two spots simulated the conditions of night and the quilt is used for heat preservation of the part of the Kang surface to keep 25 ℃. What's more, the highest temperature was 34 ℃ which satisfied the human body thermal comfort requirements. It solves the problem that the traditional Kang system overheats more than 40 ℃.
Figure 13
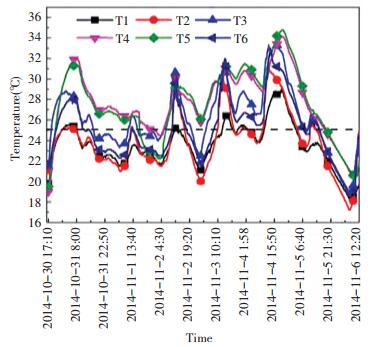
A measuring point without a quilt such as spot 3 and spot 6 was higher than the one of spot 1 and spot 2. Combined with Fig. 4 and Fig. 9(a), the reason is that the human foot coil spacing was set to 200 mm and the human head coil spacing was set to 250 mm which met the law ′warm feet and cool roof ′. This system avoids the farmers repeat packing multifarious every day, but also guarantees the Kang surface temperature to satisfy the human body thermal comfort of sleep at night, to improve the indoor thermal instability caused by intermittent heating.
3.4 The Analysis of Heating Effect 3.4.1 Temperature variation of enclosure structure The Fig. 14 gives the information about enclosure structure temperature changing rule. Excluding outside window it basically keeps enclosure structure temperature more than 15 ℃. As is known to all, sensible temperature was closely related to the temperature of enclosure structure. From Fig. 14 we can see that the burning-cave-pipe coil-Kang coupled heating system can effectively guarantee the enclosure structure radiation temperature averaged 23.1 ℃, which effectively improve the average body temperature and indoor thermal comfort.
Figure 14
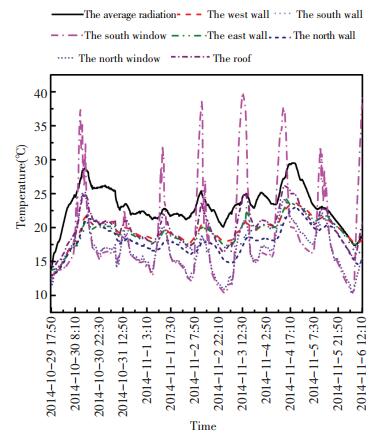
The Fig. 15 shows the temperature of the room equipped with burning-cave-pipe coil-Kang coupled heating system is 6.5 ℃, higher than rooms without heating and 3.5 ℃ higher than the only Kang heating room. From November 2, 2014, 19:50 to November 3, 2014, 6:30, outdoor air temperature ranged -2.4 ℃ to 0.6 ℃ meanwhile indoor air temperature ranged 18.4 ℃ to 20.4 ℃. Therefore, in cold winter, this system ensures the indoor temperature.
Figure 15
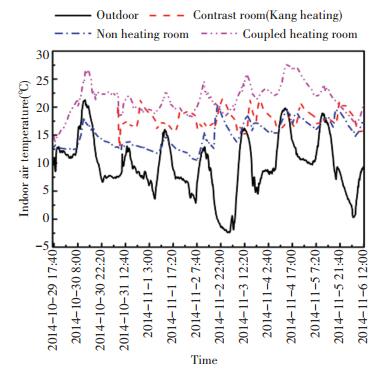
3.4.2 Burning cave floor heat output The corresponding convection and radiation heat transfer calculation methods were used to analyze the change of burning cave floor heat output. The Fig. 16 illustrates that the floor radiation heat transfer is greater than the convection heat transfer. The total heat of burning cave floor output ranged from 16.87 W/m2 to 360.5 W/m2, the average heat flux was 178.44 W/m2 and the total heat output was relatively large. According to the burning cave floor temperature analysis, the floor heat capacity was small, this leads to excess heat directly into the room and cannot be stored in the floor, resulting in a larger indoor thermal environment fluctuations.
Figure 16
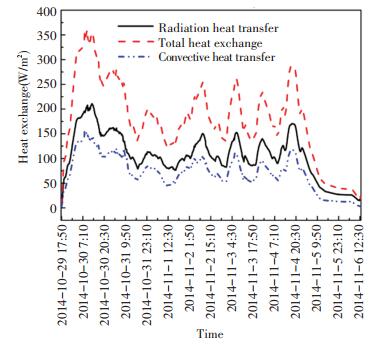
3.4.3 Kang surface heat output Fig. 17 shows the surface of the Kang at different times to provide heat for the room, in the initial stage of the system, Kang surface heat loss was negative value, indicating that the Kang surface temperature was less than air temperature, cannot provide heat for the room. With fuel smoldering and releasing heat, the temperature of the water putting into the Kang body gradually raised, which manifested as heat dissipation.
Figure 17
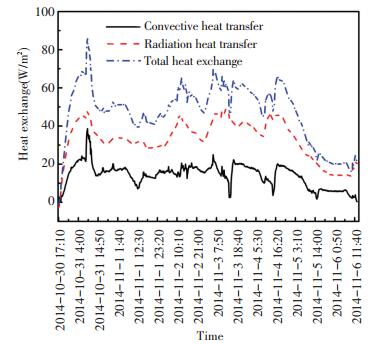
According to Fig. 17, the average total heat transfer of Kang surface was 47.36 W/m2 and the maximum heat transfer was 86.27 W/m2. In rural areas of northern China, the building enclosure structure usually adopts 240 mm or 370 mm brick wall and the building thermal load is large. Obviously, the only Kang heating cannot fully meet the needs of rural traditional architecture, thus, burning-cave-pipe coil-Kang coupled heating system is necessary.
On the basis of building indoor thermal load calculation method, using the analysis of the burning cave floor and the Kang heat output and the outdoor heating calculation temperature, the indoor air temperature in Liaoyang can be achieved. The average heat output of burning cave floor and Kang surface was 225.8 W/m2. It was calculated that this system under the condition of the outdoor heating calculation temperature can provide 14.5 ℃ for indoor air temperature which meets the northern winter indoor thermal comfort temperature 12-16 ℃.
3.4.4 Pipe heat distribution According to the use of hot water heat, we can get the information about the heat carried out by hot water pipes, including Kang surface heat and part of heat loss of return pipe. The heat loss includes the convection heat transfer between pipe and indoor air and radiation heat transfer between the pipe and building enclosure structure. The experimental correlations of convection heat transfer between pipe and air are as follows[17-20]:
$Q = \pi dL\varepsilon \sigma \left( {T_s^4-T_w^4} \right)$
where d represents pipe outside diameter (m); L is pipeline length (m); Ts represents pipe surface temperature (℃); Tw is retaining structure wall temperature (℃)
According to the above method and Fig. 18, the pipe average heat loss is 31.72 W, which accounts for 15.7% of the total heat of return pipe. The heat loss proportion is not obvious. However, if set the pipes in other non-heating room, it will lead to large heat loss, Kang surface temperature cannot meet the requirements in the winter.
Figure 18
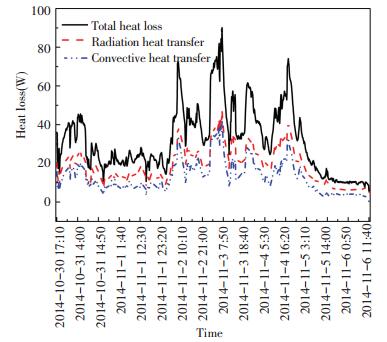
3.4.5 System heat distribution Fig. 19 shows the distribution of heat supplied by burning cave. It illustrates that burning cave floor heat in the process of fuel burning is a large proportion, the floor heat release have fallen sharply at the end of the combustion, but is larger than Kang surface heat release.
Figure 19
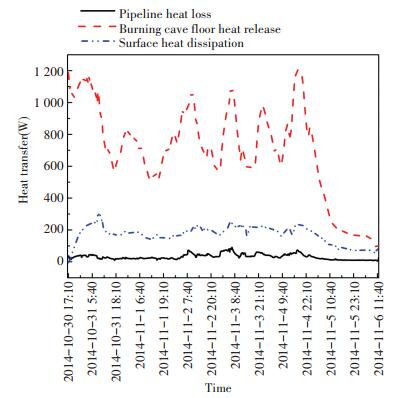
Fig. 20 gives the information about the proportions of outward heat distribution inside the burning cave. The maximum proportion of the effective heat provided by burning cave is the floor heat release from indoor environment which is 78.14%. Meanwhile, the water heated by the burning cave represented 18.36%. Therefore, radiant floor heating has a high heat utilization rate. On the contrast, the heat utilization of pipe system is low which provides less heat for indoor environment.
Figure 20
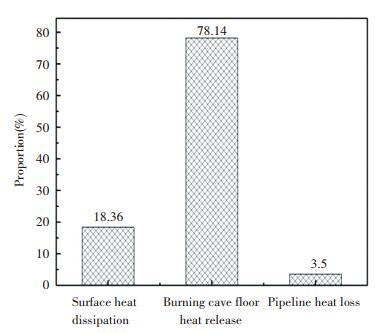
3.4.6 Integrated thermal efficiency According to the calculation method of the thermal efficiency of the above mentioned, it is applied to the comprehensive thermal efficiency of the burning-cave-pipe coil-Kang coupled heating system, the calculation formula is:
$\eta = \frac{{{Q_{{\text{eff}}}}}}{{{Q_z}}} = \frac{{{Q_{{\text{bur}}}} + {Q_{{\text{kang}}}}}}{{{Q_z}}} = \frac{{{Q_{{\text{bur}}}} + {Q_{{\text{kang}}}}}}{{v \cdot {Q_J}}}$
where η is Burning-cave-coil-Kang coupled heating system comprehensive thermal efficiency (%); Qeff: Effective use of heat (W); Qbur: Burning cave floor effective heat (W); Qkang: Kang surface effective heat release (W); v: Smoldering combustion rate (kg/s); QJ: low calorific value of corn cob fuel (kJ/kg).
Based on burning cave floor heat output and Kang surface heat release, the highest comprehensive thermal efficiency of burning-cave-coil-Kang coupled heating system is 48.9%, comparing with the traditional burning cave increased by 8.32%. Therefore, it can be used to make full use of the heat in the burning cave to heat the Kang surface so as to provide heat for the room.
4 Conclusions The paper is based on the completedburning-cave-coil-Kang coupled heating system, using the performance data to analyze the heat distribution and performance. The main conclusions are as follows:
1) Smoldering combustion duration is about 216 h. The average speed of smoldering combustion is 0.25 mm/h. Combustion flue gas temperature is stable inside burning cave: because of thin burning cave floor layer, the heat storage capacity of the floor is weak and the burning cave floor even over 40 ℃ in parts.
2) The temperature of supply pipe which enters the Kang coil ranges from 21 ℃ to 46.3 ℃, the largest temperature difference of supply and return pipe is 8.6 ℃. 74.7% of Kang coil supply temperature meets standard requirements.
3) The night working conditions test spots with aquilt stay above 25 ℃ and the highest temperature is 34 ℃ which satisfys the human body thermal comfort range. It avoids overheating more than 40 ℃ in the traditional Kang system.
4) Indoor floor heat release accounts for 78.14% of the effective heat of burning cave. The water heated by the burning cave represented 18.37%. The comprehensive thermal efficiency of burning-cave-coil-Kang coupled heating system is as high as 48.9%, comparing with the traditional burning cave increased by 8.32%.
References
[1] Tian Weizhi. The Research of Heating Methods Based on Fire Pit. Dalian: Dalian University of Technology, 2011. (

[2] Zhang Xueyan, Chen Bin. A simplified calculation method for predicting the thermal performance of a burning cave in rural houses of Northern China. Energy and Buildings, 2016, 117: 208-215. DOI:10.1016/j.enbuild.2016.02.035 (

[3] Tian Weizhi, Chen Bin, Zhang Xueyan, et al. Study on winter thermal performances of northern rural burning cave heating system. Chinese Renewable Energy Society Annual Conference Proceedings 2011. Beijing, 2011(9): 846-849. (

[4] Tian W Z, Chen B, Zhang X Y, et al. Study on technology utilization of burning cave for heating in rural houses in cold areas in China. Journal of Central South University (Science and Technology)(Suppl. Issues), 2012, 4(43): 180-186. (in Chinese) (

[5] Zhuang Z, Li Y G, Chen B, et al. Chinese kang as a domestic heating system in rural northern China-A review. Energy and Buildings, 2009, 41(1): 111-119. DOI:10.1016/j.enbuild.2008.07.013 (

[6] Zhang Xueyan, Chen Bin, Tian Weizhi. Pool-experimental study of hot water heating system based on the combustion of biomass. Acta Energiae Solaris Sinica, 2013(9): 1667-1672. (

[7] Zhang X Y, Chen B, Zhao J R, et al. Optimization of thermal performance in a Chinese traditional heating system-Burning cave. Energy and Buildings, 2014, 68(Part A): 423-431. DOI:10.1016/j.enbuild.2013.09.031 (

[8] Zhang Xueyan, Chen Bin. Analysis on the heat transfer process of the burning cave-A traditional heating system in rural houses of northern China. Procedia Engineering, 2016, 146: 459-465. DOI:10.1016/j.proeng.2016.06.429 (

[9] Yuan Pengli, Wang Zongshan, Lin Duanmu, et al. Study on the heating methods of rural residential building in different thermal zones in Northern China. Procedia Engineering, 2016, 146: 604-611. DOI:10.1016/j.proeng.2016.06.411 (

[10] Lin Duanmu, Yuan Pengli, Wang Zongshan, et al. Heat transfer model of hot-wall Kang based on the non-uniform Kang surface temperature in Chinese rural residences. Building Simulation, 2017, 10(2): 145-163. DOI:10.1007/s12273-016-0325-0 (

[11] Wang Shengcheng, Zhou Fubao, Kang Jianhong, et al. A heat transfer model of high-temperature nitrogen injection into a methane drainage borehole. Journal of Natural Gas Science and Engineering, 2015, 24: 449-456. DOI:10.1016/j.jngse.2015.04.013 (

[12] Yang Ming, Yang Xudong, Wang Zhifeng, et al. Thermal analysis of a new solar kang system. Energy and Buildings, 2014, 75: 531-537. DOI:10.1016/j.enbuild.2014.02.047 (

[13] Zhang Xueyan, Chen Bin, Fan Xinying. Different fuel types and heating approaches impact on the indoor air quality of rural houses in northern China. Procedia Engineering, 2015, 121: 493-500. DOI:10.1016/j.proeng.2015.08.1097 (

[14] Zhao K, Liu X H, Jiang Y. Dynamic performance of water-based radiant floors during start-up and high-intensity solar radiation. Solar Energy, 2014, 101: 232-244. DOI:10.1016/j.solener.2013.12.033 (

[15] Zhang Baogang, Fan Xinying, Liu Ming, et al. Experimental study of the burning-cave hot water soil heating system in solar greenhouse. Renewable Energy, 2016, 87(Part 3): 1113-1120. DOI:10.1016/j.renene.2015.08.020 (

[16] China Academy of Building Research, JGJ142-2004. Radiant Floor Heating Technology Procedures. Beijing: China Building Industry Press, 2004. (

[17] Shieh S S, Chang Y H, Jang S S, et al. Statistical key variable analysis and model-based control for the improvement of thermal efficiency of a multi-fuel boiler. Fuel, 2010, 89(5): 1141-1149. DOI:10.1016/j.fuel.2009.07.001 (

[18] Bergman T L, Lavine A S, Incropera F P. Fundamentals of Heat and Mass Transfer. seventh ed. . Hoboken: John Wiley and Sons, Inc., 2011. 380-885. (

[19] Zhang X M, Ren Z P, Mei F M. Heat Transfer. Fourth ed. . Beijing: China Building Industry Press, 2001. (in Chinese) (

[20] Rohsenow W M, Hartnett J R, Cho Y I. Hand Book of Heat Transfer. Third ed. . New York: McGraw-Hill, 1998. 230. (
