Junchao Li, Yanyan Zang,Wei Wang
(College of Material Science and Engineering, Chongqing University, Chongqing 400044, China)
Abstract:
The mismatch of elasticity modulus has limited the application of titanium alloys in medical implants, and porous structures have been proved effective to deal with this problem. However, the manufacturing of porous structures has been restricted from conventional technologies. In this study, selective laser melting (SLM) technology was employed to produce a set of Ti-6Al-4V porous samples based on cubic lattices with varying size of strut width from 200 μm to 600 μm. Then the compression tests were conducted to analyze the influence of the strut width on the elasticity modulus and the ultimate strength. The result shows both of them increases linearly with the growth of strut width or with the decrease of porosity, and the elasticity modulus of porous parts is largely reduced and actually meets the requirement of clinical application. Additionally, a finite element model was established to verify the un-uniform stress distribution of porous parts. It reveals that fractures always initially occur at the vertical struts along the force direction which suffer from the main deformation.
Key words: selective laser melting Ti-6Al-4V porous structures elastic modulus stress
DOI:10.11916/j.issn.1005-9113.2016.02.007
Clc Number:TP29
Fund:
Li Junchao, Zang Yanyan, Wang Wei. Elastic Modulus and Stress Analysis of Porous Titanium Parts Fabricated by Selective Laser Melting[J]. Journal of Harbin Institute of Technology, 2016, 23(2): 46-50. DOI: 10.11916/j.issn.1005-9113.2016.02.007.

Fund the National High Technology Research and Development Program of China (Grant No.2015AA042501) Corresponding author E-mail:ljchust@163.com Article history Received: Dec 25, 2014
Contents Abstract Full text Figures/Tables PDF
Elastic Modulus and Stress Analysis of Porous Titanium Parts Fabricated by Selective Laser Melting
Li Junchao


College of Material Science and Engineering, Chongqing University, Chongqing 400044, China
Received: Dec 25, 2014
fund: the National High Technology Research and Development Program of China (Grant No.2015AA042501)
Corresponding author: E-mail:ljchust@163.com
Abstract: The mismatch of elasticity modulus has limited the application of titanium alloys in medical implants, and porous structures have been proved effective to deal with this problem. However, the manufacturing of porous structures has been restricted from conventional technologies. In this study, selective laser melting (SLM) technology was employed to produce a set of Ti-6Al-4V porous samples based on cubic lattices with varying size of strut width from 200 μm to 600 μm. Then the compression tests were conducted to analyze the influence of the strut width on the elasticity modulus and the ultimate strength. The result shows both of them increases linearly with the growth of strut width or with the decrease of porosity, and the elasticity modulus of porous parts is largely reduced and actually meets the requirement of clinical application. Additionally, a finite element model was established to verify the un-uniform stress distribution of porous parts. It reveals that fractures always initially occur at the vertical struts along the force direction which suffer from the main deformation.
Key words: selective laser melting Ti-6Al-4V porous structures elastic modulus stress
1 IntroductionTitanium and its alloys are often used as hard tissue substitutes in artificial bones due to their excellent properties such as biocompatibility and corrosion resistance [1]. However, the mismatch of elasticity modulus is one of the main reasons of failures of clinical bone implants [2]. The Young’s modulus of natural bones is expected to be less than 30 GPa while it is more than 100 GPa as for titanium alloys. This mismatch would reduce the stress transferred to the adjoining bones. This phenomenon, always called ‘stress shielding’, would result in undesirable bone resorption. Additionally, as the implants assume the main force, muscles and bones around the implants would not exercise, and thus the bone tissue thickness would be decreased[3]. Further, the capability for bone healing is another concern of bone implants, which requires a cell population with mechanical stability facilitating bone formation and fracture healing [4].
Porous titanium parts have been examined in attempts to tackle these two problems [5]. Porous structures with pores ranging from 150 μm to 500 μm are thought to be optimal for bone formation [6]. And some porous titanium structures have been designed and proved ideal for bone in-growth applications[7].Despite these achievements, the manufacturing of porous structures has still been limited by production techniques[8].Selective laser melting (SLM), an layer-based additive manufacturing process, enables the formation of complex shaped parts without any special tooling and allows the production of fine porous structures with pores from 200 μm to 500 μm [9]. A sketch of the SLM process is shown in Fig. 1. A thin powder layer with a certain thickness is deposited firstly on a base plate and then leveled by a roller. The fiber laser, going through the optical and scan system, melts the pre-deposited powder layer in the light of a specific pattern defined by computer. After this layer is melted, the build platform moves down by a layer thickness and a new powder layer is paved and afterwards scanned. The process repeats until the final geometry is finished.
Some researches on porous structures processed by SLM have been conducted so far. Sallica-Leva et al.[10]found that the energy input is closely related to the dimensional accuracy and the mechanical properties of porous parts. Yan et al.[11] investigated the influence of unit cell size on the manufacturability and compression properties of the final lattice structures. Stamp et al.[12]adopted a ‘beam overlap’ technology to manufacture porous structures with controlled porosity in pure titanium. Stok et al.[13] designed two kinds of strut width to produce porous titanium scaffolds which facilitates the bone formation for treated bone defects and provides adequate mechanical supports. Habijan et al.[14]showed that dense and porous samples are satisfying carriers for human mesenchymal stem cells which are a promising cell type for regeneration of critical bones. Kujala et al.[15] evaluated the effect of porosity on the osteointegration of nickel-titanium implants in rat bone. Smith et al.[16] established finite element models to predict the compressive response of lattice structures based on two simple architectures.
Figure 1

From what have been mentioned, it is believed that SLM is a promising technology which is able to produce fine porous structures for improving bone formation. However, most attentions were paid on the manufacturing method of porous structures or the compression properties of the final porous parts. Few studies about elasticity modulus of a porous titanium part have been carried out. Thus, in this study, based on a cubic unit, the influence of strut width on the elastic modulus as well as the ultimate strength was researched. Additionally, a finite element model was developed to analyze the stress distribution of porous structures.
2 Materials and Methods2.1 MaterialsThe powder used for this study is pre-alloyed Ti-6Al-4V powder with a particle size normally below 30 μm.
Table 1 lists the chemical composition of Ti-6Al-4V powder, and Fig. 2 shows the SEM image of Ti-6Al-4V powder obtained by gas atomization, which presents a spherical morphology.
表 1
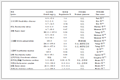
5.5-6.53.5-4.5<2000×10-6<500×10-6<800×10-6<120×10-6<2500×10-6Balance
Table 1 Chemical composition of Ti-6Al-4V(Wt)%
Figure 2
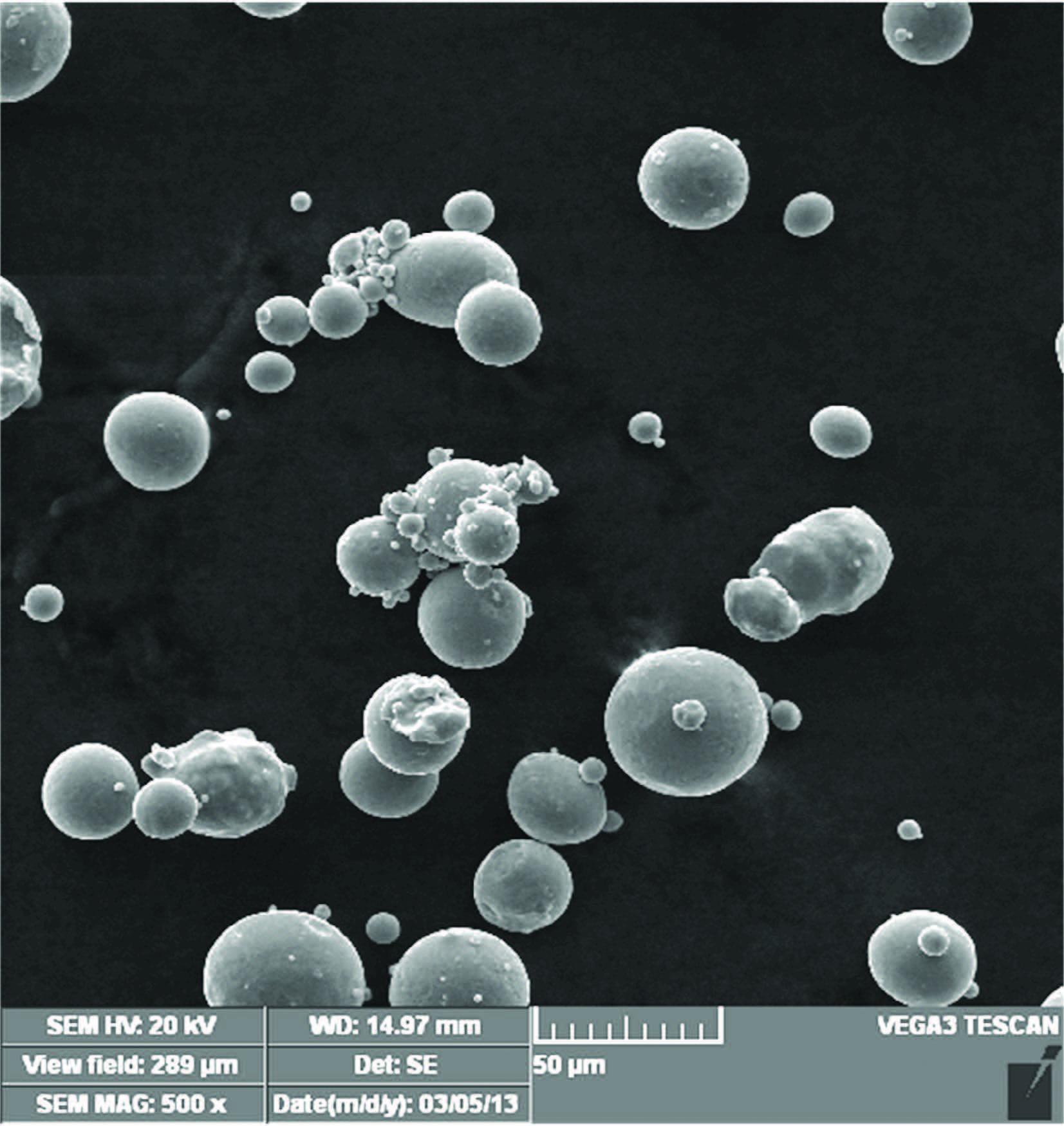
2.2 Sample ManufactureA cubic unit lattice was designed as shown in Fig. 3. The side length of square pores is kept as 500 μm, and the strut width varies from 200 μm to 600 μm with the interval of 100 μm. In this way, five kinds of porous samples with the dimension of 10 mm*10 mm*15 mm were manufactured by EOS M280, a commercial SLM workstation with the laser beam diameter being close to 100 μm. Since the powder is fully melted during the process, it is essential to keep the manufactured parts from oxidation. Therefore, argon atmosphere of 0.1% O2 or less is assured.
Figure 3
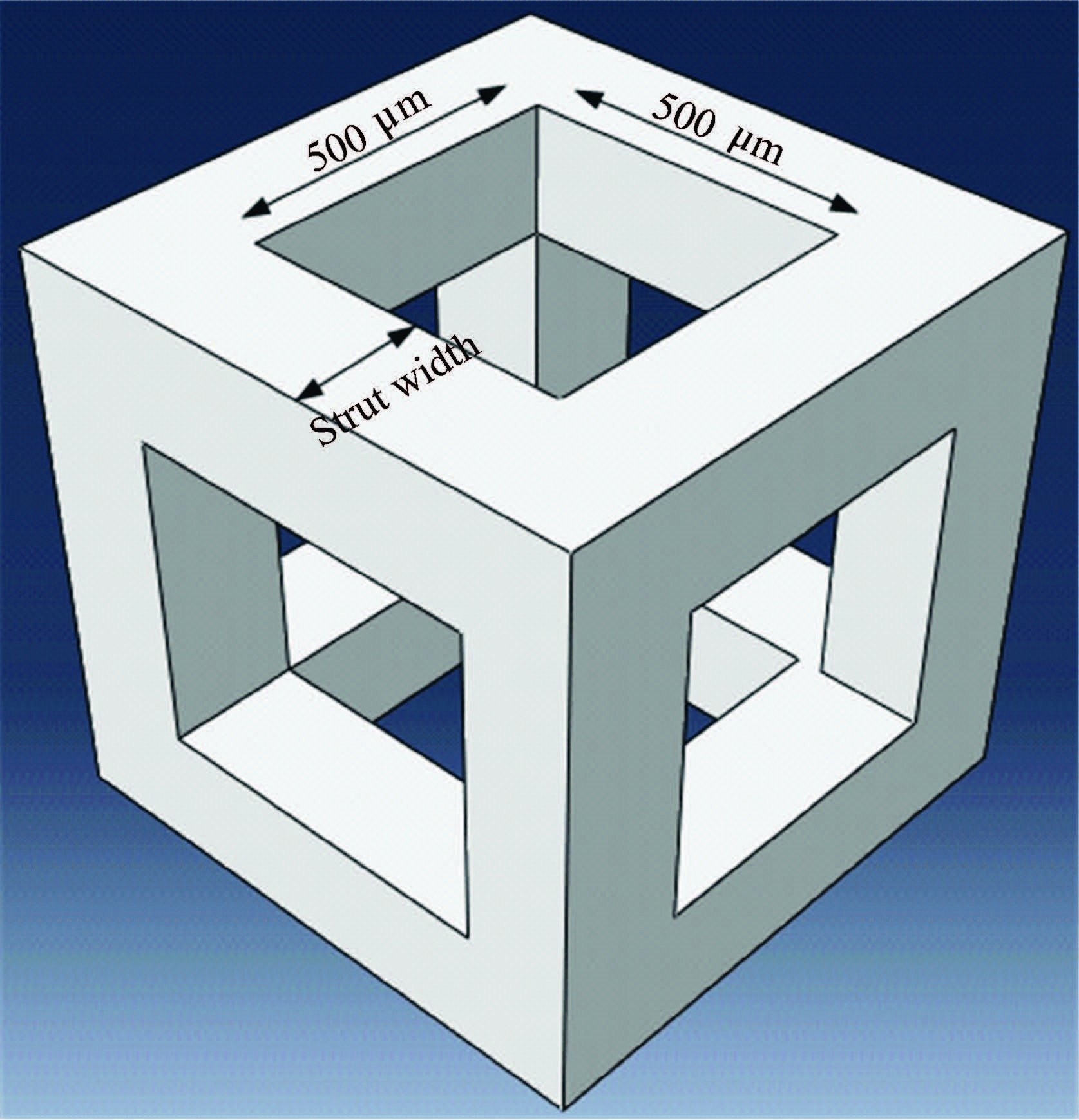
The quality of SLM fabricated parts largely depends on a few factors such as material property, system performance and process parameters [17]. Of the process parameters, laser power P, scan speed V, hatch spacing HS and layer thickness t are the most important. These four parameters determine the energy density Ev, the energy supplied by the laser beam to a volumetric unit of powder material. Energy density Ev is an experimental quantity that has a significant impact on part density. The relation between Ev and the four main process parameters can be described using the following expression[10]:
${{E}_{\upsilon }}=\frac{P}{HS\times V\times t}$ (1)
According to this equation, the energy density Ev will be enhanced by increasing laser power and decreasing scan speed or/and hatching space. This will largely contribute to full melting of materials. Table 2 shows the manufacturing parameters for all the experiments in this study. The values of these parameters are strongly recommended by EOS Company and have been proved reasonable for processing TC4 parts. After processing, the melted parts were removed from base plate by wire cutting, and compression tests of all the samples were conducted with a universal material testing machine (CMT5105) at room temperature. During the tests, lubricants were used to reduce the effect of friction. Thus, the experimental values of load for each sample could be achieved.
表 2
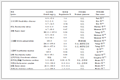
1701 250200, 300, 400, 500, 60030100
Table 2 Manufacturing parameters in this study
3 Results and Discussion3.1 Compression Loads at Different Strut WidthsFig. 4 shows the SLM fabricated porous parts, which are generally fine despite that there are a few acceptable adhering particles at local areas. The lattice structures with varying strut widths were manufactured successfully, verifying the capability of SLM technology to process porous parts. For each strut width, two same samples were processed and then compressed on the testing machine to obtain the average experimental data. A set of load-displacement curves with different strut widths were plotted in Fig. 5. As it is shown, the load increases linearly with the increase of displacement in the beginning as the material suffers from elastic deformation. Then, when the plastic deformation occurs, it tends towards stability to reach the maximum value. It should also be noted that the larger the strut width the larger maximum load is.
Figure 4
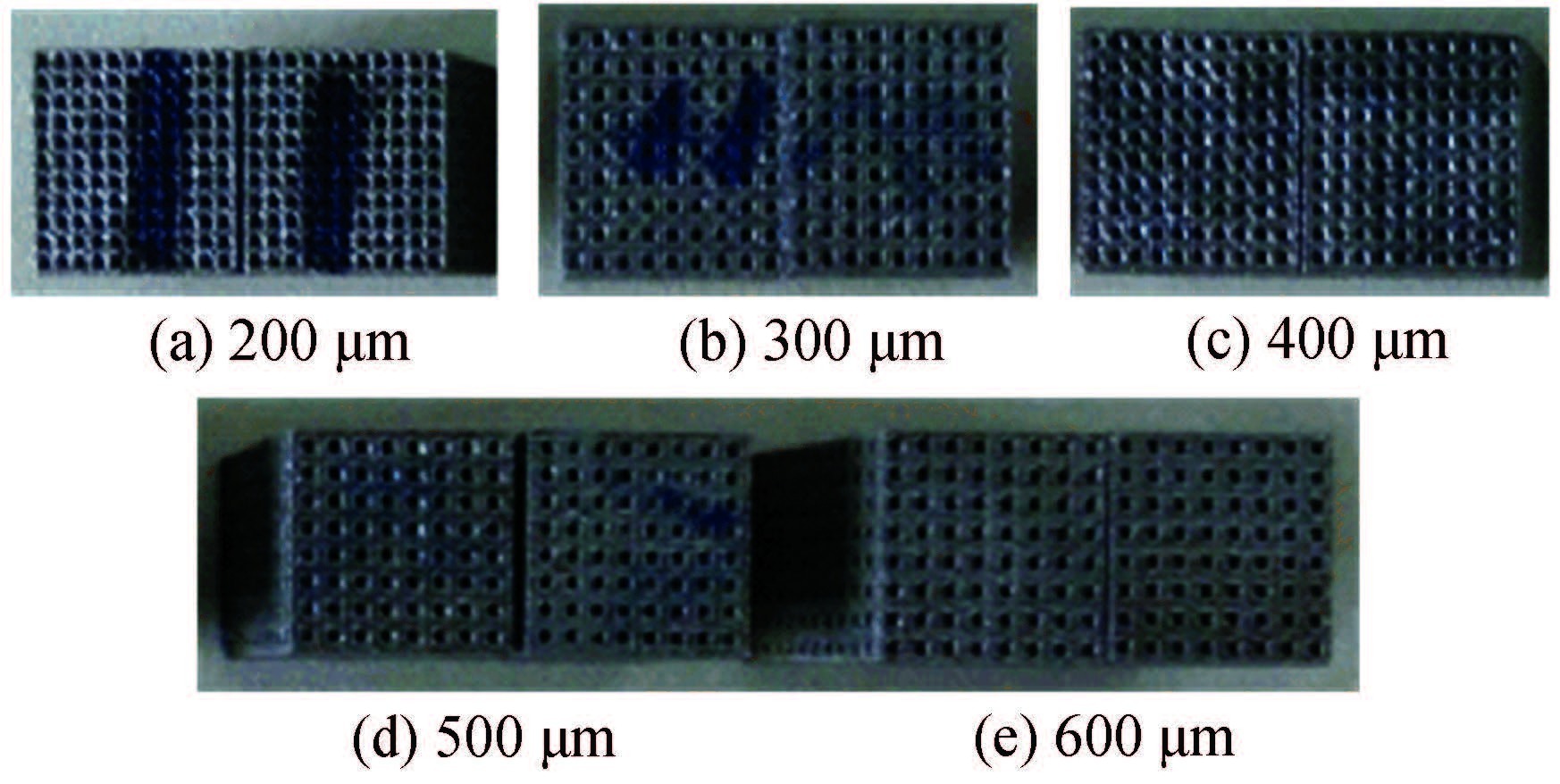
Figure 5
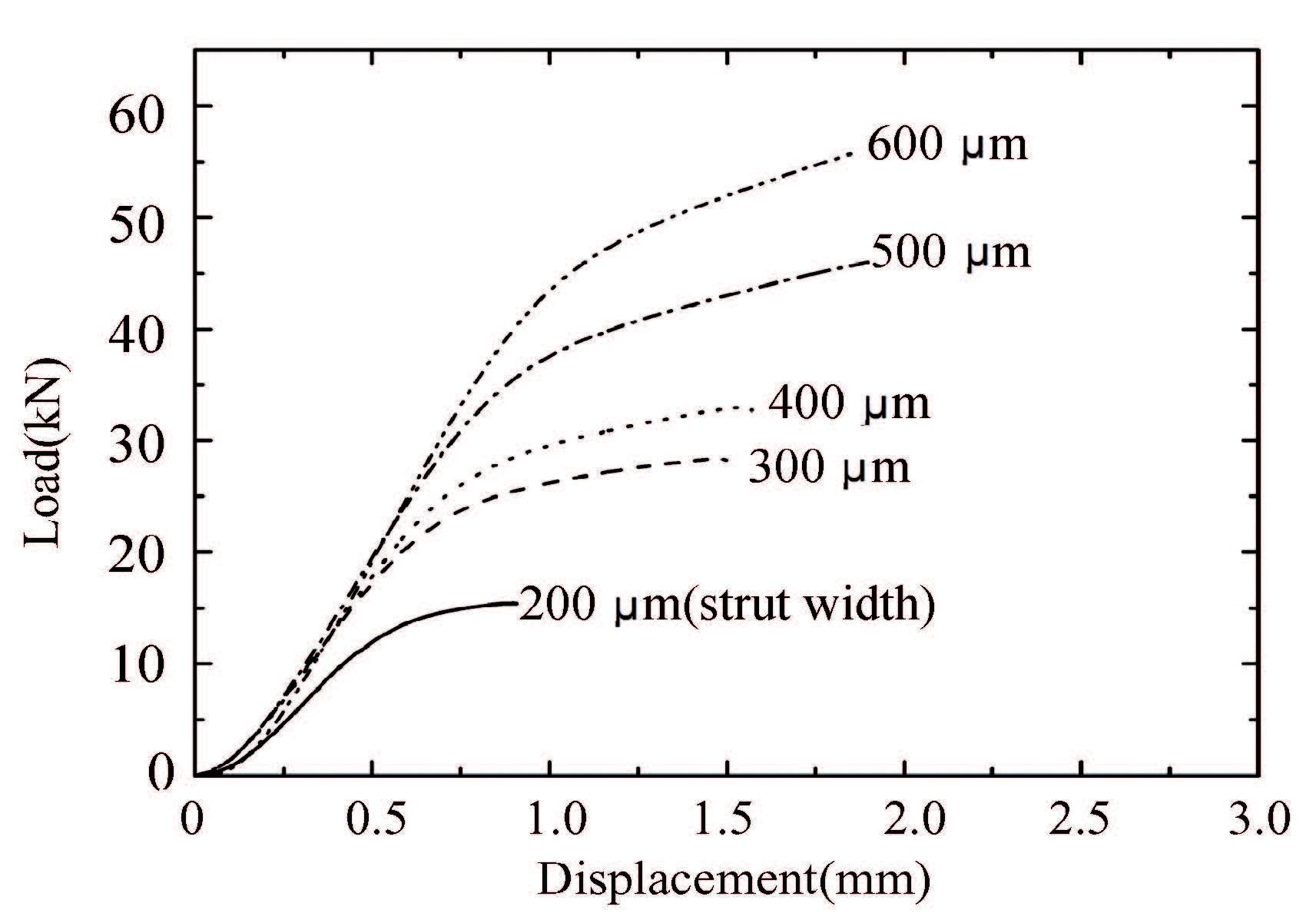
3.2 Elastic Modulus of Porous PartsAs mentioned before, although titanium and alloys are applicable to artificial bone transplants for their satisfying biocompatibility, the application has largely been restricted because of the mismatch of elastic modulus between the titanium implants and natural bones. Fig. 6 presents the stress-strain curves of samples with different strut widths by processing the experimental load data of compression tests. It shows that the ultimate strength grows evidently as the strut width increases, exhibiting a similar trend with that of the maximum load as shown in Fig. 5.
Figure 6
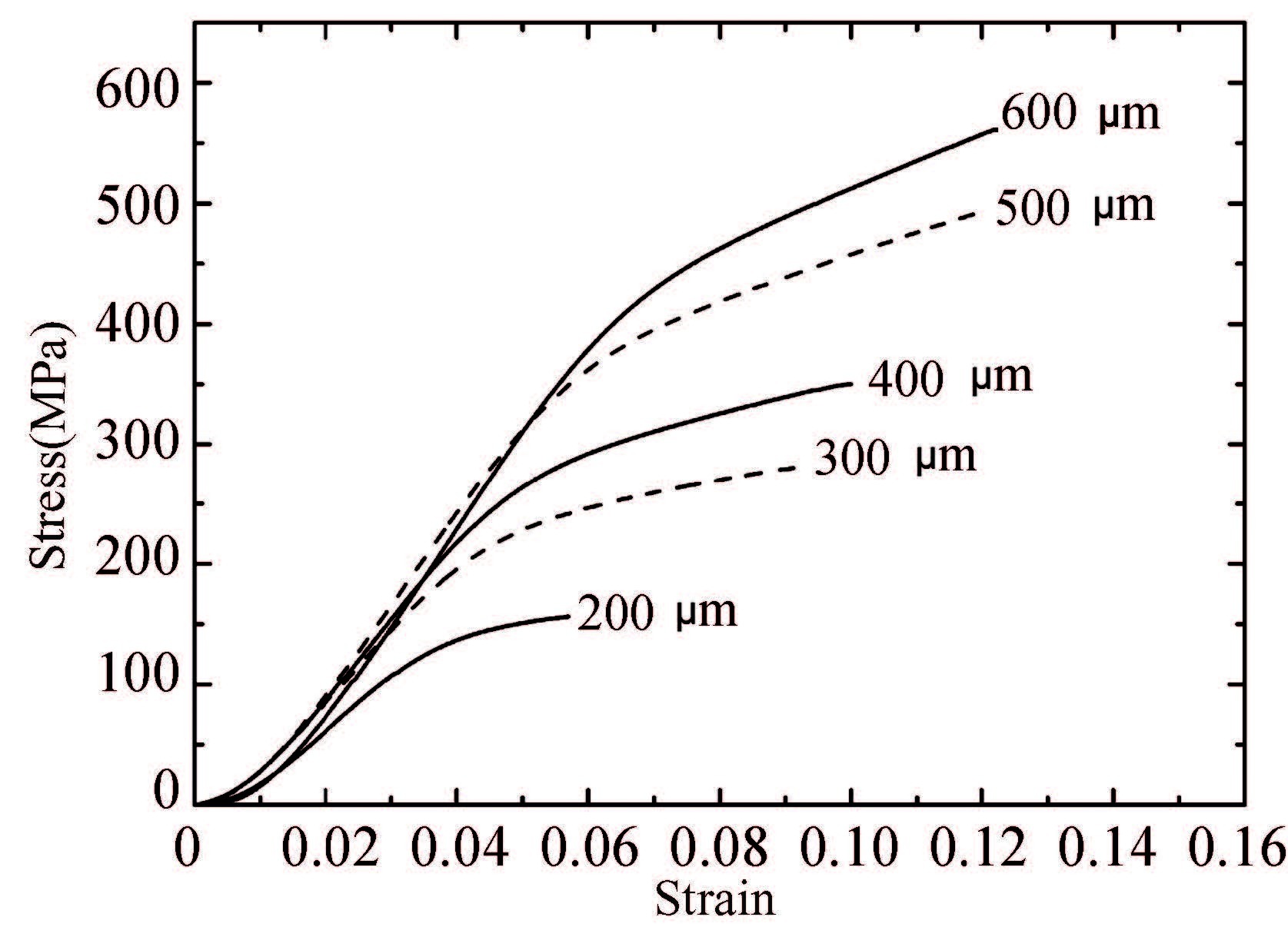
From fitting the linear part of each curve in Fig. 6, the elastic modulus can be calculated. Fig. 7 presents the elastic modulus and the ultimate strength of titanium porous parts versus the strut width. As porosity is often linked to a porous part, the porosity for each porous part is also represented. It should be noted that both the elastic modulus and the ultimate strength of porous parts processed by SLM can be largely reduced considering that the elastic modulus of titanium materials is normally more than 100 GPa and the ultimate strength is generally over 1200 MPa. It is therefore proved that the existence of pores has a significant effect on the mechanical properties of titanium parts. According to the compression tests by Duchemin [18], the elastic modulus of natural bones is expected to be in the range of 4.4 to 19.8 GPa, and the average ultimate strength is around 111 MPa. Thus, all the values of elastic modulus for porous parts in this study meet the requirements of natural bones. However, although all the values of the ultimate strength are drastically decreased, they are still much larger than 111 MPa except when the strut width is equal to 200 μm. Additionally, both the elastic modulus and the ultimate strength present an approximately linear relation with the porosity and strut width.
Figure 7

3.3 Stress Distribution AnalysisThe experimental stress-strain curves in Fig. 6 were obtained by compression tests viewing the test samples as a whole. As there are so many square pores in the part, it is impossible to have a uniform stress distribution.Thus, in order to conduct stress analysis of porous parts, a finite element method (FEM) model based on ABAQUS platform was established.A simplified cubic lattice with strut width of 400 μm and the side length of 2.7 mm was adopted to reduce the simulation time. In the FEM model, the part was meshed with tetrahedral elements with type of C3D10.And the displacement boundary condition was created to simulate the compression process: the sample’s bottom surface was fixed and the upper surface was pushed to move down by 0.2 mm. With reference to Fig. 6, this would result in a strain value of 0.072 in general and the corresponding stress is about 300 MPa. However, according to the simulation result as shown in Fig. 8, only the horizontal struts which are perpendicular to the force direction have a similar stress distribution. The slight difference between them may be attributed from a reduced model.The vertical struts along the force direction suffer from the main deformation, and the stress of vertical struts has almost reached the natural ultimate strength of titanium materials because the actual force bearing area is largely reduced.Thus, the porous parts would initially fail at the areas of vertical struts, which is in accordance with the experimental results as the ruptures always happen at the same place as shown in Fig. 8.
Figure 8

4 Conclusions1) A set of porous parts, based on cubic lattices with different strut widths from 200 μm to 600 μm, are successfully manufactured by selective laser melting.
2) Both the elasticity modulus and the ultimate strength have a nearly linear increase with the growth of strut width or with the decrease of porosity of the designed lattice. And the elasticity modulus of porous parts is largely lowered down to a range of 4.49 GPa to 8.2 GPa which matches the requirements of natural bones. It is also verified that the elasticity modulus of porous titanium parts can be adjusted by different porous structures.
3) The simulation results show that the stress value of the horizontal struts perpendicular to the external force direction is close to the experimental value, but the vertical struts along the force direction which undertake the main deformation have a much larger stress value and always fail at first.
References
[1]Liu X, Chu P K. Surface modification of titanium alloys and related materials for medical applications.Materials Science and Engineering,2004, 47: 49-121.(

[2]Niinomi M. Recent research and development in titanium alloys for biomedical applications and healthcare goods.Science and Technology of Advanced Materials,2003, 4(5): 445-454.(

[3]Karachalios T, Tsatsaronis C, Efraimis G. The long-term clinical relevance of calcar atrophy caused by stress shielding in total hip arthroplasty: a 10-year, prospective, randomized study.Journal of Arthroplasty,2004, 19(4): 469-475.(

[4]Giannoudis P V, Einhorn T A, Marsh D. Fracture healing: the diamond concept.Injury,2007, 38(4): 3-6.(

[5]Taddei E B, Henriques V A R, Silva C R M, et al. Production of new titanium alloy for orthopedic implants.Materials Science and Engineering,2004, 24(5): 683-697.(

[6]Blokhuis T J, Termaat M F, den Boer F C. Properties of calcium phosphate ceramics in relation to their in vivo behavior.Journal of Trauma-Injury, Infection, and Critical Care,2000, 48(1): 179-186.(

[7]Mullen L, Stamp R C, Brooks W K. Selective laser melting: a regular unit cell approach for the manufacture of porous, titanium, bone in-growth constructs, suitable for orthopedic applications.Journal of Biomedical Materials Research Part B: Applied Biomaterials,2009, 89(2): 325-334.(

[8]Murr L E, Gaytan S M, Medina F. Next-generation biomedical implants using additive manufacturing of complex, cellular and functional mesh arrays.Philosophical Transactions of the Royal Society A: Mathematical, Physical and Engineering Sciences,2010, 368(1917): 1999-2032.(

[9]Hollander D A, Wirtz T. Structural mechanical and in vitro characterization of individually structured Ti-6Al-4V produced by direct laser forming.Biomaterials,2006, 27(7): 955-963.(

[10]Sallica-Leva E, Jardini A L. Microstructure and mechanical behavior of porous Ti-6Al-4V parts obtained by selective laser melting.Journal of the Mechanical Behavior of Biomedical Materials,2013, 26: 98-108.(

[11]Yan Chunze, Hao Liang. Evaluations of cellular lattice structures manufactured using selective laser melting.International Journal of Machine Tools & Manufacture,2012, 62: 32-38.(

[12]Stamp R, Fox P, Jones E. The development of a scanning strategy for the manufacture of porous biomaterials by selective laser melting.Journal of Materials Science: Materials in Medicine,2009, 20(9): 1839-1848.(

[13]Van der Stok J, Van der Jagt O P, Amin Yavari S, et al. Selective laser melting-produced porous titanium scaffolds regenerate bone in critical size cortical bone defects.Journal of Orthopaedic Research,2013, 31(5): 792-799.(

[14]Habijan T, Haberland C. The biocompatibility of dense and porous Nickel-Titanium produced by selective laser melting.Materials Science and Engineering :C,2013, 33(1): 419-426.(

[15]Kujala S, Ryhnen J, Danilov A, et al. Effect of porosity on the Osseo integration and bone ingrowth of a weight-bearing nickel-titanium bone graft substitute.Biomaterials,2003, 24(25): 4691-4697.(

[16]Smith M, Guan Z. Finite element modeling of the compressive response of lattice structures manufactured using the selective laser melting technique.International Journal of Mechanical Sciences,2012, 67: 28-41.(

[17]Yadroitsev I, Bertrand Ph, Smurov I. Parametric analysis of the selective laser melting process.Applied Surface Science,2007, 253(19): 8064-8069.(

[18]Duchemin L, Bousson V. Prediction of mechanical properties of cortical bone by quantitative computed tomography.Medical Engineering & Physics,2008, 30(3): 321-328.(
